I was hoping to avoid this; but I guess not: There's some issues with both the baero and occam's end plates articles, that might not be obvious to the lay-reader.
Firstly, I'm a little suspect of baero's data, based on this initial image:
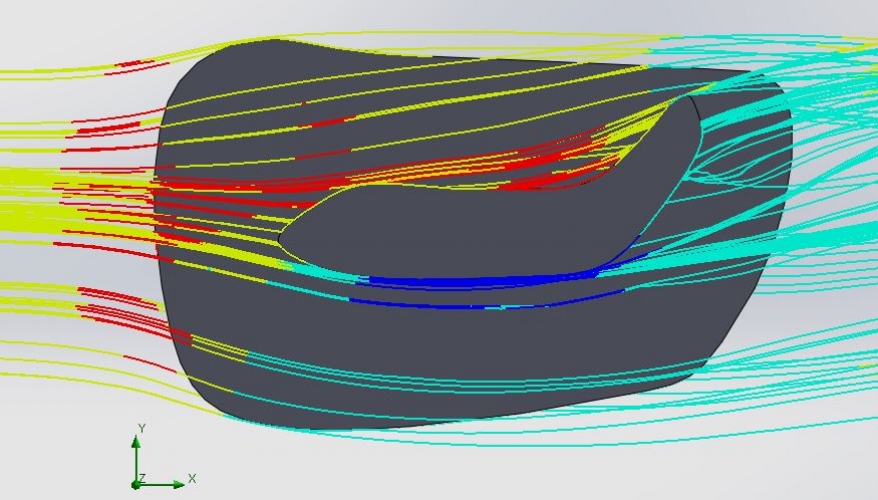
I have an APR GT500 foil profile I still need to digitize... but it definitely doesn't look like that. I suspect that overly small nose radius (and other issues with the leading edge foil shape) on that digital foil is creating some influence on the end-goal endplate design.
However, there's a more important misunderstanding that I feel is shared in both articles, and it's a fundamental misunderstanding of what the tip-vortex is, and how it's created/developed. The reason I bring that up, is because the tip-vortex is what any endplate/winglet is attempting to influence.
baere said:
We want the max pressure to be right on top of the airfoil and the min pressure right below it. This will create the maximum amount of downforce.
Mario-Occam said:
Given that information, and after looking at the preceding image, you might conclude that a good endplate should be shaped to exactly cover the high and low pressure regions of the wing. And from that, you might surmise that a good endplate for a 10” chord motorsports wing should extend 10” below the wing, and should have a lot of surface area concentrated at the front. And that’s how I see it as well. However, some end plates have most of the area towards the rear of the wing, and I can’t say I understand that.
Both of these authors see to think that the end plate needs to be biased forwards to cover the low pressure flow generated by the suction-side flow acceleration zone in the front ~30% of a foil. By implying that the endplate needs to cover this area, there's an implication in both articles that the high-pressure side of the flow can wrap directly around the tip without "going backwards", despite the wing traveling through the air forwards.
Mario's explanation is particularly problematic because he's using the chord to define the size of the endplate ("10inch chord wing should have a 10inch tall end plate"). It's unclear based on the article (and the report) if he's come to that conclusion because the low-pressure zone graphed is the same size as the chord of the pictured 2D foil... or if he's come to this conclusion because of some other influence.
The current Aerodynamicist/Aerospace Engineering understanding is that tip vortex is wrapping from the high-pressure to the low-pressure side while traversing longitudinally (i.e. backwards); and that's why the majority of winglets on an aircraft wings are bias the area towards the back portion of the low-pressure side of the wing:
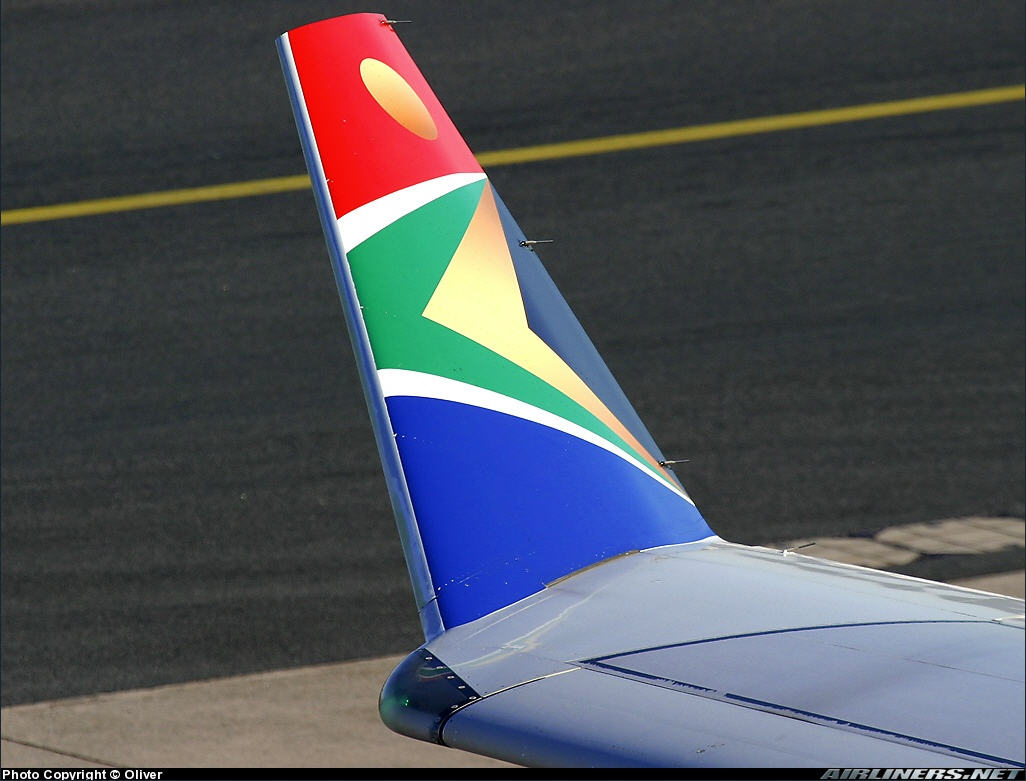
(https://airlineworld.files.wordpress.com/2008/10/south_african_winglet_close-up.jpg)
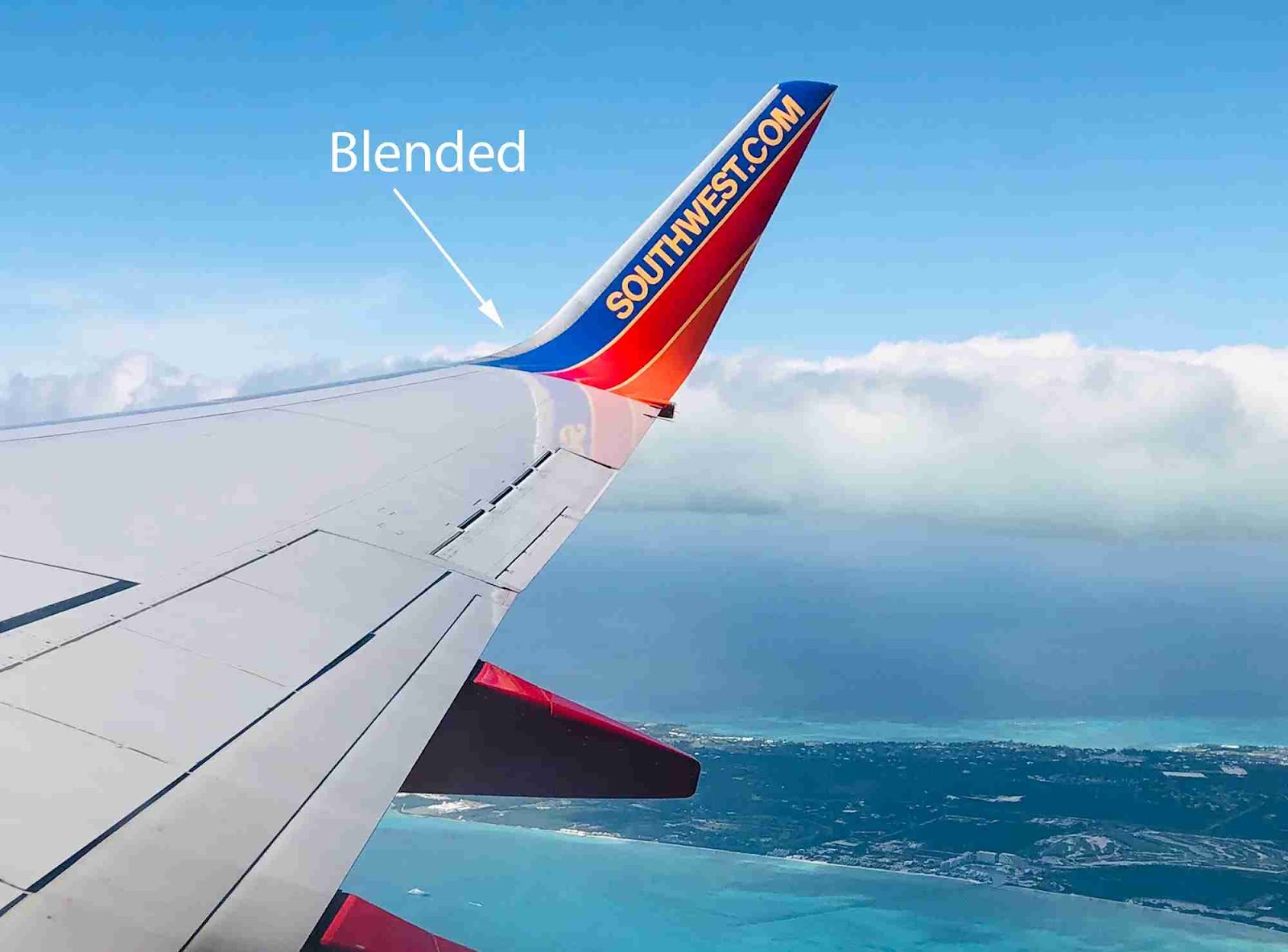
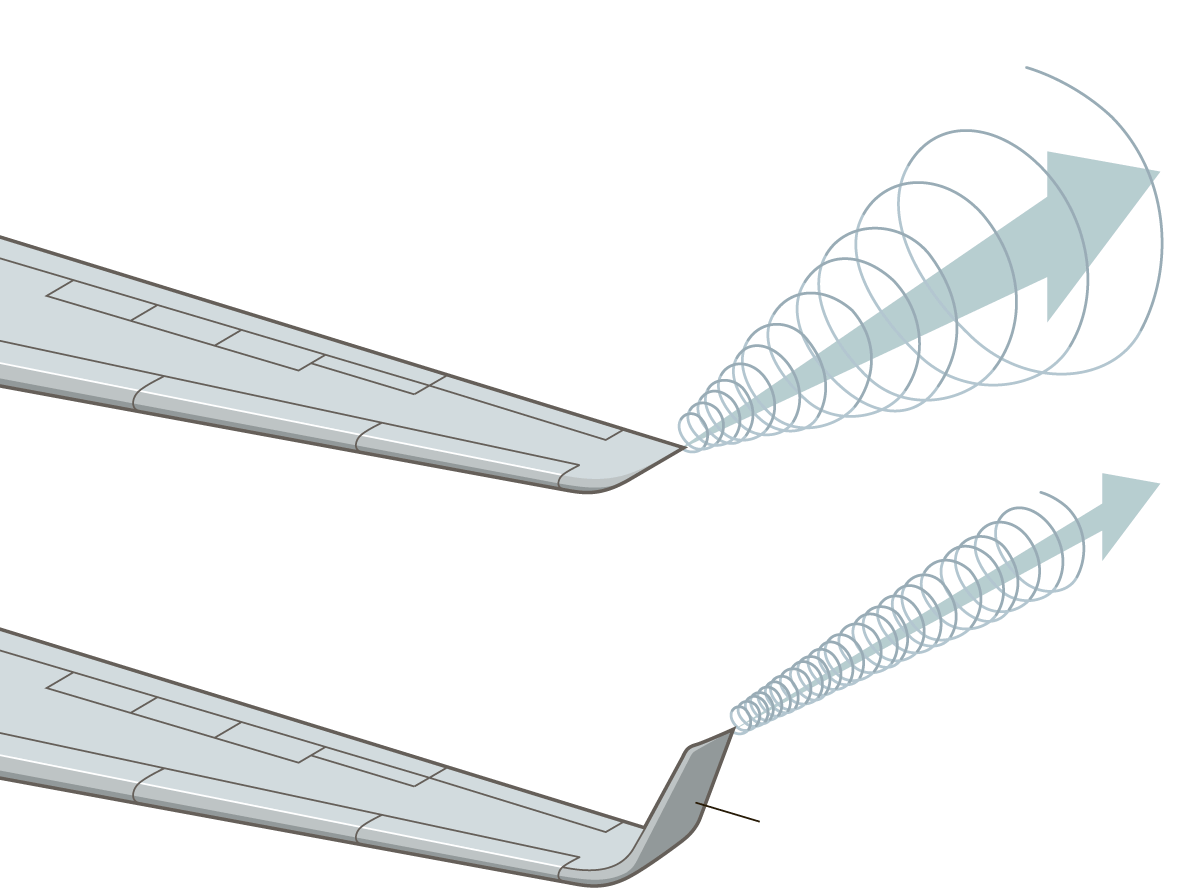
The broader picture though, is that the entirety of the high pressure across the span of the wing is attempting to wrap around to the entirety of the low pressure on the other side of the wing. The tip is resolving the entirety of of the pressure differential of the 3-dimensional finite-span wing. That's why one of the more commonly known regimes of flight is "Ground Effect", which is usually calculated as some percentage of the wingspan above the ground (although, there's a further band of ground effect that's calculated as a percentage of the chord above the ground {perhaps this is where Mario's confusion is coming from?}).
You don't have to take my word for it, you can calculate the efficiency benefit of an endplate via these formulas that are part of Katz's "New Directions in Race Car Aerodynamics" as cited by Mike Fuller on Mulsannes Corner. Which is in-line with what you can find in other places about end plates, which is that they generally have a similar benefit as extending the wing in span the same length as the winglet (this is an oversimplification).