So, I have an S10 Blazer rear end in my shop, with a custom Moser axle stuck in it. I'm running out of ideas here.
The Moser axles were supposed to be direct replacements for the GM axles, but with a custom flange that had a 4x100 bolt pattern and the correct diameter for fitting a Miata brake caliper. That part of everything worked perfectly. I got the custom axles because it was cheaper than modifying the stock ones.
Installing the axles, I had to tap the C-clips into place. I didn't think anything of this, I'd never dealt with this kind of axle before short of removing the stock part. Then I found I couldn't get the cross bar in. The "buttons" on the end of the axles were too long. I managed to get one C-clip out and measured the axle. When I called Moser with the details, the response was that the axles must have been made with the button from an 8.5 rear and not my 7.5. They quickly made up some replacements and shipped them right out.
But there's a problem. I cannot remove one of the C-clips. I can't get a pair of pliers on to it because of the placement of the ring gear - that's why I could get to the other side. I can't remove the ring gear because the pinion's in the way, and I can't remove the pinion without removing the differential. But the differential has an axle in it...
I've tried modifying pliers, but there just isn't enough room. I can't tap the C-clip off because there's that weird speed-based locking mechanism on the other side of the diff so it has nowhere to go. I don't need this differential anymore as I will be using the LSD unit out of my Camaro. I can use the R&P out of the Camaro as well, I guess. They're both the same ratio. Moser probably wants this axle back for a refund. Before I start cutting random things, any suggestions?
Original conversation: http://grassrootsmotorsports.com/forum/grm/shortening-a-solid-axle/5274/page1/ Knowing what I know now, it would have been a lot cheaper to simply buy the axles and shorten my Camaro housing. I haven't looked at the machining at the end of the Camaro axle, I'm thinking simply cutting down the tube and sticking a new seal in it would actually be quite simple.
P71
SuperDork
7/24/09 8:56 p.m.
Honestly Keith Moser axles are huge problem childs. My dad has two sets lying around the garage twisted like barbershop poles. Every drag racing shop I have ever dealt with has horror stories about them.
As for the c-clip, I always use a really strong magnet to suck the stupid things out. Unfortunately that sounds like not an option (unless you have a really badass magnet...). Try drilling the c-clip with a self-tapping screw and then yanking on that?
Shotgun? Am I the first to suggest Miata?
Seriously I have usualy used my Snap-on magnet that is on the flexible spring thingy. If that wont work Mercedes makes instrument cluster hooks. They are a small tempered wire hook about 6in long with a 3 to 4 mm right angle in the end. You should be able to make some very easily. I have used two to reach behind and pull the ends of Jesus clips before. I call them Jesus clips because thats the sound you make when you drop and loose one.
Freeze it with some liquid nitrogen, and hit it with a chisel. It falls into two pieces in theory.
If the axles that are in there are trash, you might be able to get a sawzall blade in enough to cut i, which would then allow you to remove the carrier, so you can then deal with what is left on a bench.
Loosen the carier caps and shift the diff toward the tight side the clip will slide out. Some thimes you need to shim behind the clips to get them tight too.
I loved my moser axle but i haer thing changed after Greg's passing.
44
Keith wrote:
So, I have an S10 Blazer rear end in my shop, with a custom Moser axle stuck in it. I'm running out of ideas here.
The Moser axles were supposed to be direct replacements for the GM axles, but with a custom flange that had a 4x100 bolt pattern and the correct diameter for fitting a Miata brake caliper
I almost had to stop reading there.
I agree with removing any side to side shims on the differential to try and buy space. I've also found that a dremel with the right bit can be the correct tool in these situation sometimes.
I third shifting the diff, pull the caps, remove the shims and use a pry bar to push the diff the way it needs to go. If it's still snug, try putting someone on the outside (wheel flange end) with a deadblow hammer. Turn the axle so the open side of the C clip is pointing up. One person pushes the diff the way you need to go, the other drives the axle further in with the deadblow hammer (or a brass hammer, or even a big hammer with a brass drift). Hopefully the C clip will shake out.
FWIW, I have never had to tap a C clip in. It's always been: pull the spider gear pin, push the axle in a bit further, the C clip then falls out of the 'recess' in the spider gear. Assembly is reverse yada yada.
I forgot to mention that the reason I had to tap the C clip on is because the groove on the axle has an ID that's 0.025" too large. In other words, the clip is a bit of a press fit. If I had previous experience with this sort of axle, that should have been a warning.
The problem is not that the axle won't move far enough side to side. The problem is that I simply can't get a good enough grip on the clip to pull it out. Thanks to the ring gear, there's a fairly small gap with which I can work, and all the stuff that's restricting my access will move side to side with the diff if I pull the shims.
I'm liking the liquid nitrogen idea. Right now, C clip demolition is looking like the best choice, and I hadn't figured out how to get a dremel tool in there. The Jesus clip hook might work if I can make one strong enough and get enough room behind the clip to make it work.
I've been very happy with Moser's service so far, and they nailed the dimensions of the custom outer flange perfectly. When I contacted them about the problem with the sizing, they sent out a pair of replacement axles immediately. If I'd known that having to tap that clip into place was a danger sign, everything would be cool. I didn't go with Moser for extra strength, but because it was the easiest and cheapest way to get what I needed. This axle I'm trying to remove is junk, but I think they want it back as part of the return process. Dunno if they'd be pleased to get it back in two pieces, but if I can find a way to get it out in two pieces that just might happen!
My mind only seems to work with pictures, so I'll try again, but after having looked at a random reference shot off the web.
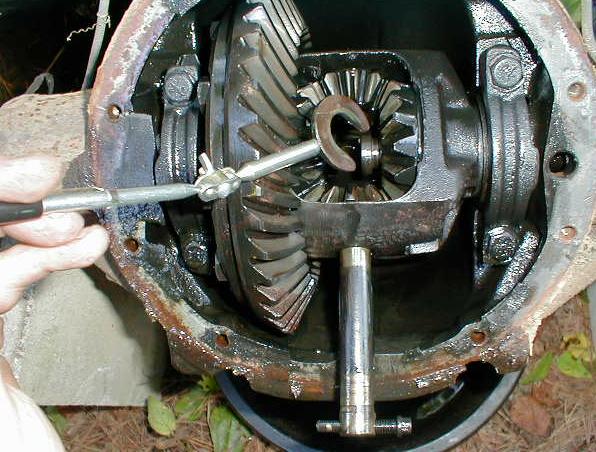
1) rotate the axle shaft so that the C-clip is oriented with the open end toward you
2) find a pickle fork, pair of chisels, or fab a custom tool to contact both ends of that c-clip
3) BFH
The problem with that is that the other side of the diff is occupied by a weird speed-sensitive locker setup (http://grassrootsmotorsports.com/forum/grm/is-this-a-limited-slip/10595/page1/) so the clip has nowhere to go. It would work on a normal open diff though.
Found a place in town that sells liquid nitrogen. 15 minutes after they closed :) I'll give that a try early next week.
Know any copier techs? We have steel spring-hooks that work well for popping off clips like that.
Simple Solution:
Call Moser, explain the issue, send the pics (or a link to this thread), see if they will simply let one of the axles slide.
Carter
Yeah, I might try that. They're a pretty useless axle to anyone else, really. But I still need to get it out, as it's currently occupying a location that needs to be occupied by one of the new axles!
Copier techs, eh? Hmm.
Or if you know a friendly doctor, particularly a dermatologist, he/she might be able to provide some liquid nitrogen from a private stash.
Can you fit a welding electrode in there?
Ground clamp to the outer axle flange.
Hold the electrode tip lightly onto the outer edge of the C-clip, flip the welder on for second or two until it melts and attaches, flip it off, let it cool for a few seconds, then yank the mess out.
Of course, if that doesn't work, you're really screwed.
Carter
Weld a slide hammer to it.
C-clip eliminators maybe?
umm no idea if these will work with your application but i just typed in "c-clip eliminators" on google and this was the first link. just to give you an idear....
edit GM 7.5
http://www.summitracing.com/search/Brand/Strange-Engineering/Product-Line/Strange-Safety-Hubs-C-Clip-Eliminators/Axle-Model/GM-7-5-in/?Ns=Rank|Asc&autoview=SKU
I win!
I always win.
P71's comment about drilling a hole and inserting a screw got me thinking. If I could drill a hole for a screw, what about a bigger hole so it cut the clip in half? So that's what I tried. I wasn't able to get the clip quite cut, but it weakened the clip enough so I could force the clip's arms a bit further apart. Now I was faced with a normal C clip extraction exercise. I just turned the differential upside down and it fell out
No damage to the axle either!
I'm not going to go to C clip eliminators. The main reason for those is to keep the wheel trapped in the case of a broken axle, and my rear disc brakes will do that for me.
Thanks to everyone for all the help and suggestions. I know now that C clips simply slip into place, they should never need help.
Keith.
Go to an office supply store grab a can of computer duster. turn it upside down and liquid comes out that freezing cold. we use it at times to get optics out of tooling that stuck after coating.
44
P71
SuperDork
7/26/09 8:13 p.m.
Woot! I was useful! 
Sounds like Moser has turned a corner in customer service since I last dealt with them years ago.