I finally got project frankenfiat up, running and weighed.
The bigger engine in the rear has the existing springs over loaded. I got corner weights today, with me in the car they are
Front Left 300 248 Front Right
Rear Left 578 558 Rear left
for a total weight of 1684, but a depressing 33% on the front tires.
The front is double a arms with coil overs, the rear is a trailing arm set up. I think the front should be fine.
The motion ratio of the rear is .6.
From here, what do I have to do to figure out what I need for a rear spring?
My thoughts are:
1. Jack up the rear for what I think would be the right spot for ride height.
-
Measure existing spring length at that height.
-
remove existing spring and measure total length.
Using this, I can find out how much spring compression I need to get to ride height, and therefore what spring rate I need.
Is this at all correct? if not, what steps do I need to do?
With this give me a good spring rate for trying to get this thing to turn?
Question 2. where in the total travel do I want to set the ride height?
I think Puhns or Smith has some numbers for this. Lots of people will use frequency.
As for the travel, I aim for about 2/3 compression 1/3 droop if possible.
I am a firm believer in the ride frequency analysis method, with deflection/roll analysis used to check for travel constraints. Basically, you need to select a ride frequency based on your performance targets. Want minimal body roll, tight response, but not a punishing ride? Aim for around 2Hz.
Here's a good primer: http://www.optimumg.com/docs/Springs&Dampers_Tech_Tip_1.pdf
Comfortable street car that feels tight? 1.5 Hz.
Autocross car? 2.5-3 Hz.
Road course car? 3-4 Hz. (not very streetable)
That's your average target rate, but you want different rates front and back to prevent harmonic pitching back and forth after bumps. I made a really detailed spreadsheet two years ago on this very problem, but it was compounded for a reverse-trike (World Solar Challenge Car). It worked out very well. I'll see if I have time to convert it for a four-wheeled car. We used Optimum K software for the FSAE cars.
Compression for ride height is easy. Figure out the distance from perch to perch when the car is at your desired ride height. Your spring's free length should be that length plus:
(weight on wheel) / (spring rate * (motion ratio)²)
The square on the motion ratio catches a lot of people out.
You really don't want to go stiffer in the rear so maybe a longer spring would level things out.
Until you get the handling figured out.
With that weight distribution, should be fun.
I tried the frequency method and the guidelines for targeted use end up being far too soft.By the time it was stiff enough I was up around 5.5hz.
Thanks warren,
When did you do the solar car?
I did one many years ago as a student
icaneat50eggs wrote:
Thanks warren,
When did you do the solar car?
I did one many years ago as a student
In reply to icaneat50eggs:
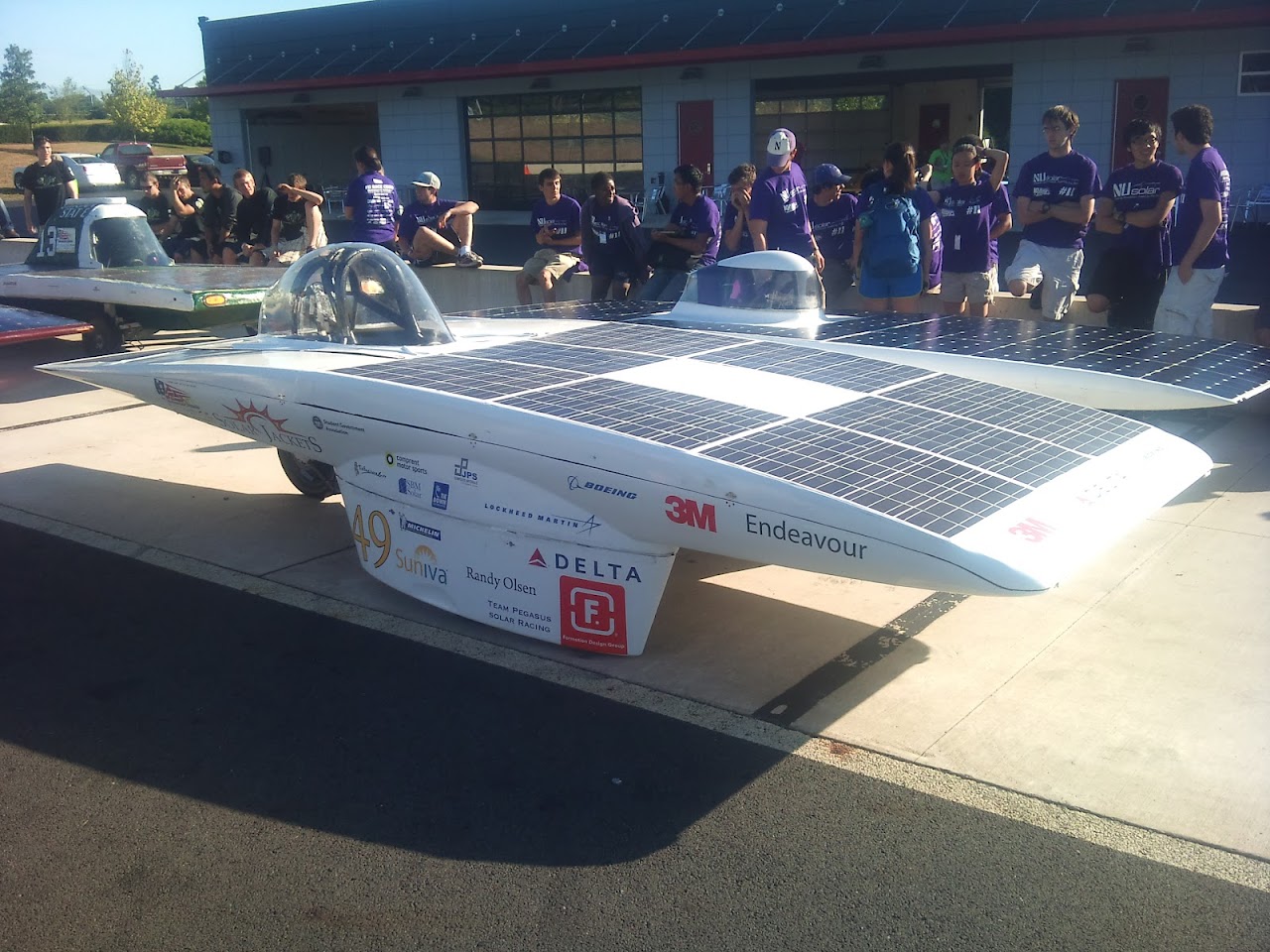
Way back in the old days (early 2012). I was mainly FSAE, but I stepped in on the Solar Team because they had no mechanical engineers and the car was pretty dangerous as-built (they used $4 radial-only ball bearings as wheel bearings, seriously). We went to the ASC (off year for WSC), but the BMS caught fire, and the array, and the motor controller...so we weren't able to compete. It passed mechanical and safety inspection, so I counted it as some sort of success.
I had the team push me down the parking lot hill at Monticello a few times, that thing handled really well as a $80k downhill car. 
They just got their new BMS working and will be driving the car at this year's ASC at the Circuit of the Americas.
https://docs.google.com/spreadsheet/pub?key=0AvUlKfewYcCNdHVXb01hdXdmYVlMMzY1WFo0NHdTQkE&output=html
Here's the spreadsheet I made to figure out the spring rates. The ride frequency was a bit higher than I'd like due to travel limitations, and will ball joints all around it will be tiring to drive long distances.
First, you want to find your ride height before you adjust corners and cross weights. Do you have driver's weight in as you are getting your weights? I would fill it with the minimum amount of fuel that you want, a driver in for driver's weight, then find get your ride height set.
Is that a roll cage of some sort? Holy cow if so have they hanged things since I did it in 96
Yes those weights included me
Okay, is there a target cross you are going for? What other spring rates do you have?
I have no clue what a good target cross weight would be. (see the learn me up there? it means I really know nothing) in the front I have a arms and coil overs, but I don't know what the spring rates up there are. I didn't really add any weight up there, so hopefully what is up there is good. If not I'll tackle that next. I have the front off right now anyway so i can pull the spring off and try to squish it and see if i can figure out the spring rates.
The spreadsheet is super cool, and appeals to my inner engineer geek. is there anyway to save it off of google docs so I can open it in excel and actually play with the numbers?
(I'm a geek, but i'm also old and not tech savvy)
icaneat50eggs wrote:
The spreadsheet is super cool, and appeals to my inner engineer geek. is there anyway to save it off of google docs so I can open it in excel and actually play with the numbers?
(I'm a geek, but i'm also old and not tech savvy)
Here it is in xlsx
Keep in mind it's for a single rear wheel and assumes a front-only roll couple. It was started in Google Docs, so sorry if it freaks out in Excel.
A little off topic, sorry!
But did you ever compete against the University of Michigan? We've don a lot of work for both their solar car and FSAE teams.
Way cool stuff!
Warren v wrote:
icaneat50eggs wrote:
Thanks warren,
When did you do the solar car?
I did one many years ago as a student
In reply to icaneat50eggs:
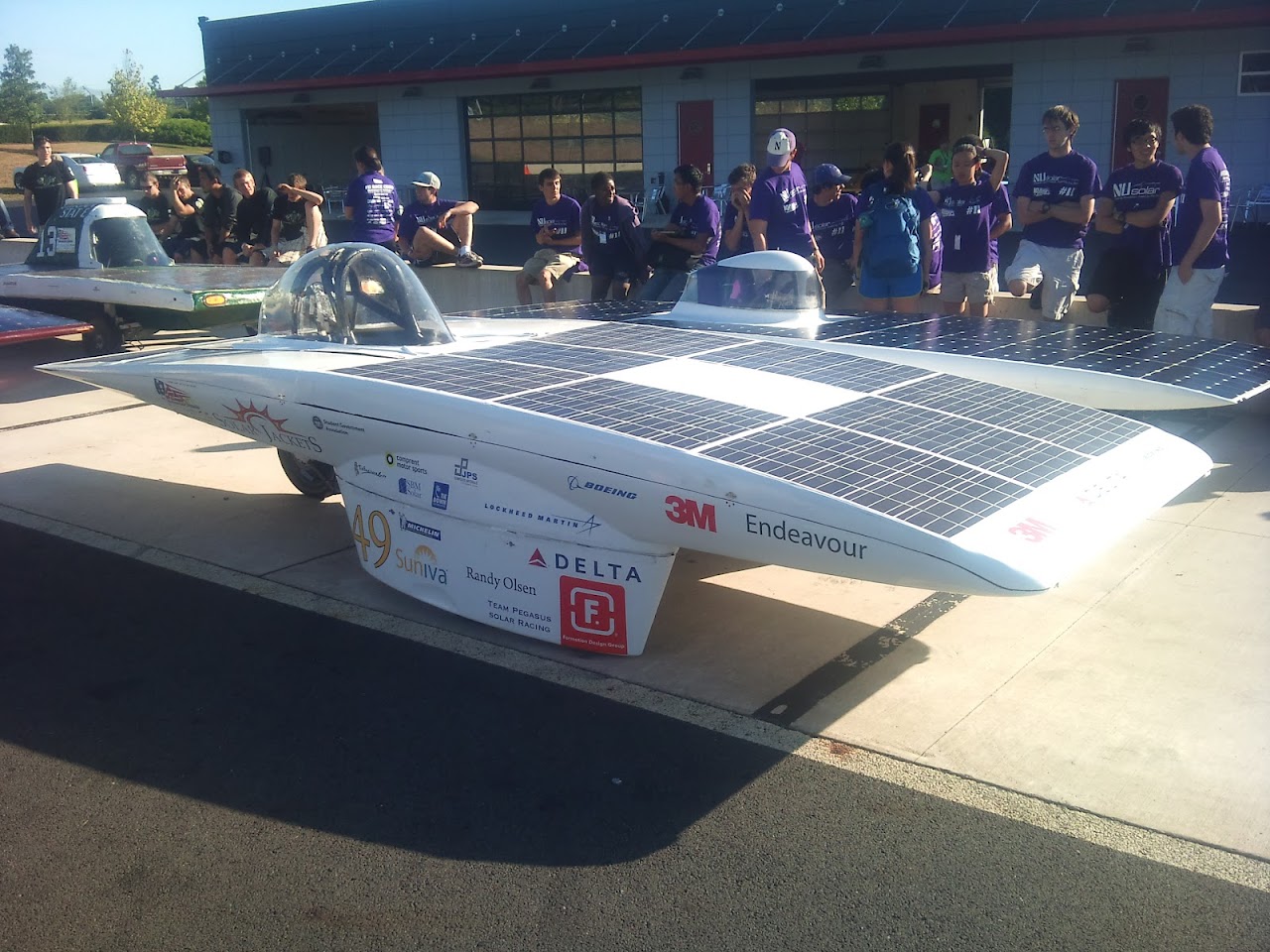
Way back in the old days (early 2012). I was mainly FSAE, but I stepped in on the Solar Team because they had no mechanical engineers and the car was pretty dangerous as-built (they used $4 radial-only ball bearings as wheel bearings, seriously). We went to the ASC (off year for WSC), but the BMS caught fire, and the array, and the motor controller...so we weren't able to compete. It passed mechanical and safety inspection, so I counted it as some sort of success.
I had the team push me down the parking lot hill at Monticello a few times, that thing handled really well as a $80k downhill car. 
They just got their new BMS working and will be driving the car at this year's ASC at the Circuit of the Americas.
https://docs.google.com/spreadsheet/pub?key=0AvUlKfewYcCNdHVXb01hdXdmYVlMMzY1WFo0NHdTQkE&output=html
Here's the spreadsheet I made to figure out the spring rates. The ride frequency was a bit higher than I'd like due to travel limitations, and will ball joints all around it will be tiring to drive long distances.
paranoid, you might want to edit your post. The quote tags got lost or something and it just reguritated my post. Yes, UofM had their E36 M3 together. Amazing team.
-Sorry OP for thoroughly hijacking your post.