I need to make a low profile wind deflector for my track car. It is a Lotus Seven clone with no windshield. The main purpose is to deflect wind and debris out of my face without causing weight or a lot of drag. I'm thinking 3/16 Lexan sheet will work but I have never worked or formed this stuff. Any tips?
If you want a complex curved shape, look into vacuuforming. You make a form, and put a heated lexan sheet over the top. A vacuum sucks it down over the form. Once it cools, you remove the form and trim it to shape.
There are tons of DIY videos on YouTube. Here's and example that fills in what I was talking about.
Not sure that would work too well with 3/16 thick!
If it isn't too complex, I just start at the middle and pop rivet it to whatever frame I'm using. I have done back windows and windshields this way many times.
If frameless, I think you need a large oven and a mold. Like the vacuum forming.
This rear window is not formed in any way, it's flexible enough to bend that far without cracking or any heat. That's 1/8" Lexan. It's been in place since 2007 with no signs of a problem.
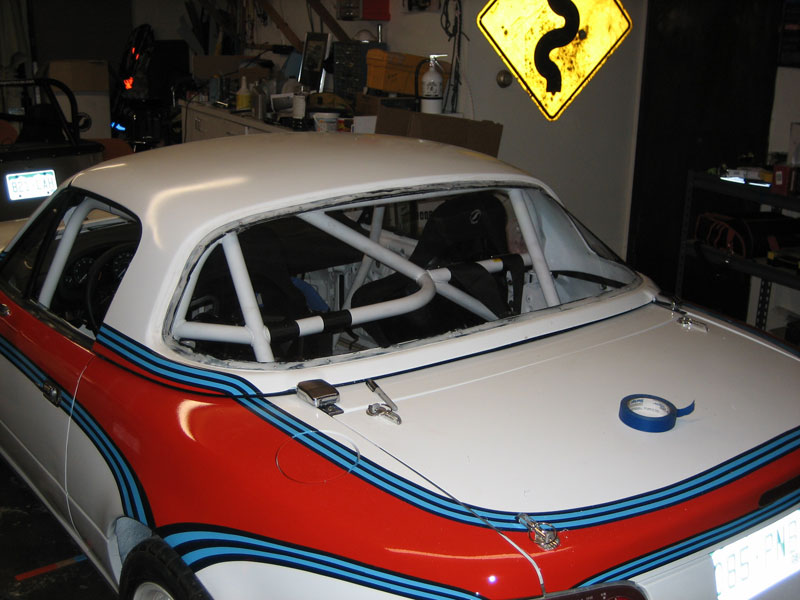
If I was doing a curved wind deflector with no upper frame, I'd make a lower frame (you need a mounting flange anyhow) with the desired curve and use heat to gradually shape it.
Are there companies that sell bubble windscreens already formed ?
Aircraft windshields in Los Alamitos , CA is who we had form some rear windows , not cheap
562-430-8108
I have no experience actualy forming lexan (polycarbonate) but thought I'd mention something I learned (some time back when thinking about making windows for vintage boats).
Evidently when bending, sometimes there are undesirable bubbles formed (in the material. at the bend). I learned this is caused by moisture and to avoid this it's important to heat for a long period of time prior to forming. Just something to look out for and/or look into.
HFmaxi
Reader
3/11/23 8:49 p.m.
I'm in the process of doing the same thing on my seven clone. Mine is being built to replace a standard windscreen for track days (ie support the wipers and lose the drag). Ended up sourcing "no break" polycarbonate from Grainger in a .171 thickness. It took a good bit of heat to get from solid to plastic and the transition happens either too slow or too quick. Make sure to support and clamp the piece in the right places to get the heat and bends where you want them. I still need to add the center support. It's possible it will be rebuilt a bit taller.
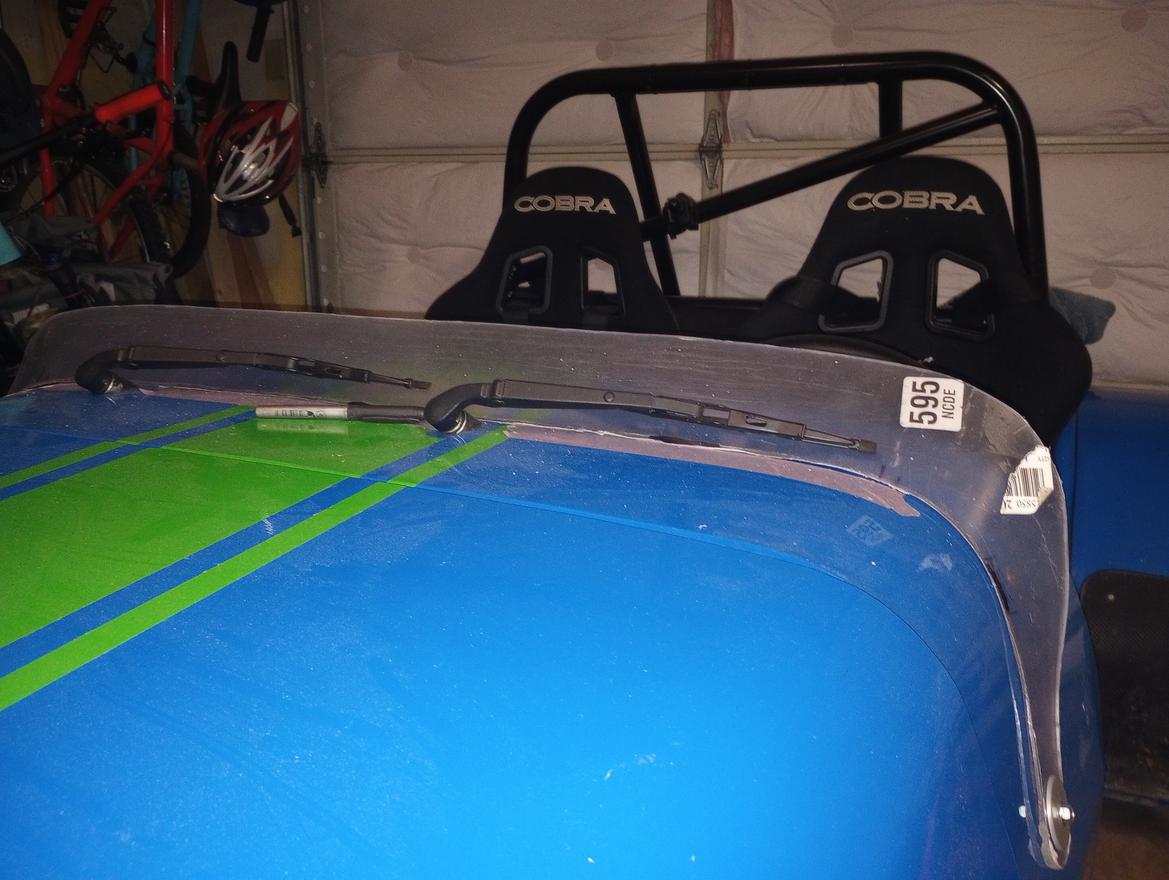
We have a polycarbonate sheet "heatbrake" at work. Similar to This one.
Worked ok, up to about 1/4" sheet. Definitely it needed water running through it to control the heat affected area. They claim you can run without, but we always got lots of bubbles in the plastic trying it that way.
These 2 videos from SuperFastMatt will take you through his trials and tribulations of forming compound curves with lexan/polycarb. It's mostly entertainment but there is some decent info in them as well.
https://www.youtube.com/watch?v=nJmANYGsMFM
https://www.youtube.com/watch?v=1E9TLWCLT2E
Some related talk elsewhere on the GRM site on the subject: Replacing a Glass Windshield With Plastic.
In reply to Marko159 :
Polycarbonate absorbs and retains moisture that causes the internal bubbles. Acrylic prolly does also, but the higher temps required to form Polycarbonate turn that moisture into steam. It is also extremely difficult to heat Polycarbonate evenly because it is formulated to remain stable under adverse conditions.
To drive out moisture, heat Polycarbonate sheets at elevated temperature for 3 days before forming.
Use acrylic in preference.
In reply to OzRaceFan :
It might be easier to form, but acrylic is the wrong material for a vehicle windshield because it cracks and shatters.
How high is an "elevated temperature" for drying polycarbonate?
Keith, you are correct in the case of windshield ... should not use acrylic.
However, majority of Historic racecar restorations are acrylic, fabricated by Aircraft Windshields Company, Los Angeles. I have 7 years experience at Sonoma Raceway.
Palsun OEM calls for 365*F for 10 hours prep. 365*F for sheet forming (not bending).
365*F is extremely hard to control in a workshop application.
Local heating will distort the sheet beyond useful.
Your "Martini Miata" application is the least troublesome route.
Handy Hint:
To avoid backside shattering when drilling plastic, grind a .050 flat spot on the cutting edge (parallel to the drill axis), and use no pressure.
This "scrapes" the plastic instead of the spiral flute "pulling" the drill bit thru uncontrollably.
Wind some electrical tape on that drill bit to quarantine it from metalworking drills.
OzRaceFan said:
To avoid backside shattering when drilling plastic, grind a .050 flat spot on the cutting edge (parallel to the drill axis), and use no pressure.
This "scrapes" the plastic instead of the spiral flute "pulling" the drill bit thru uncontrollably.
Wind some electrical tape on that drill bit to quarantine it from metalworking drills.
I had to read that a few times until it became clear to me that you are talking about grinding the drill bit cutting flute, not the plastic. Like Forrest Guhhump, sometimes I am not a smart man.
Do any of you guys have experience with using non-scratch film to protect the plastic in windshield applications?