8/16/22:
Last Week the Clutch Eyebolts Arrived in 2 days From Kentucky Clutch:

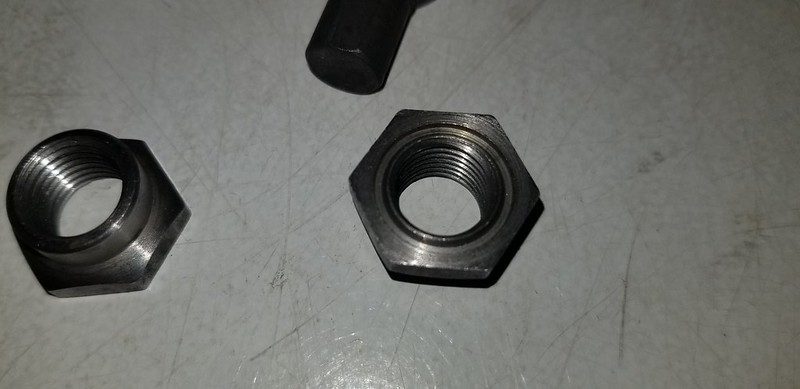
I hand Surfaced the Pressure Ring with a Diamond Stone as it was Not wrecked enough After say 8000 miles to warrant sending out to be blanchard ground.
The parts allowed me to put the pressure plate all back together, hopefully the Fingers will not fatigue, or crack etc. (fingers crossed) if It happens again I have one of the "Spec" Brand Fiero diaphragm Pressure Plates to try next, as they are a direct bolt in / replacement for a 9" slant 6 Borg and Beck Finger / Spring Style Pressure Plate.
Pressure Plate Reassembly:

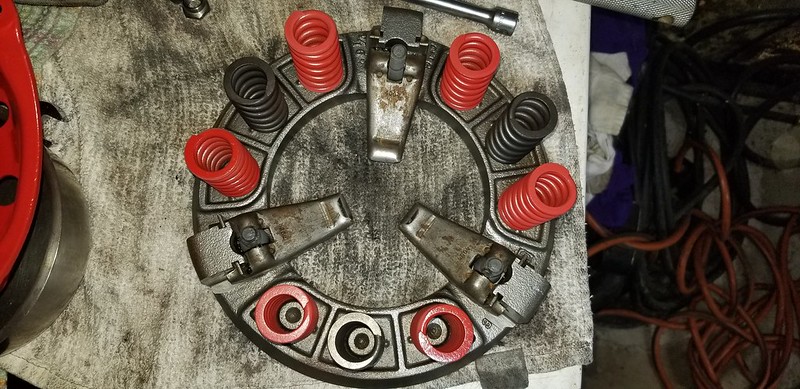


Every gearhead's household basement should have a 20 Ton Press next to the water heater, makes those pesky bearing and seal jobs at 1AM oh so convenient. :D :D

Push it all together with a somewhat close to proper thickness clutch disc, set the finger height, lock down or weld the nuts for the clutch eyebolts... call it good to go.

While I had the Pressure Plate and clutch disc removed from the flywheel I found the input bearing adapter to have dislodged from the back of the crank - I knew It was a light Press fit, but it was too light.
Fortunately It did not do any real damage, just was not supporting the input shaft correctly and was running against the clutch disc. I put it back in the proper place and used some Red Loctite 242 to hopefully hold it in place properly.
I figured this was a good time to make the switch to a hydraulic throwout bearing and get rid of the bulky clutch linkage, Z bar, clutch fork and other associated rods. I had already spent some considerable time reengineering the linkage and reinforcing the Z bar and other parts of the linkage to make it Skookum as Frig, but I was unhappy with how much flex there was in the dash with the clutch pedal pressed down, hopefully this will be better.
Because the Transmission is T5/Ford Parts are readily available and ubiquitous.. Not Something I am accustomed to with Slant 6's and Early Non B/E Body Mopars.
Hydraulic TOB - I used A Tilton 60-6104 - Literature says it's for a Diaphragm Pressure Plate, But it seems to work fine with the 3 Finger one as well. It has a little "finger stick" that replaces one of the input bearing retainer bolts.. this stick is used to keep the bearing body from spinning, some of the hydro TOB's I investigated just used the supply and feed lines for the anti rotation. - This method seemed like a better engineered idea to me.
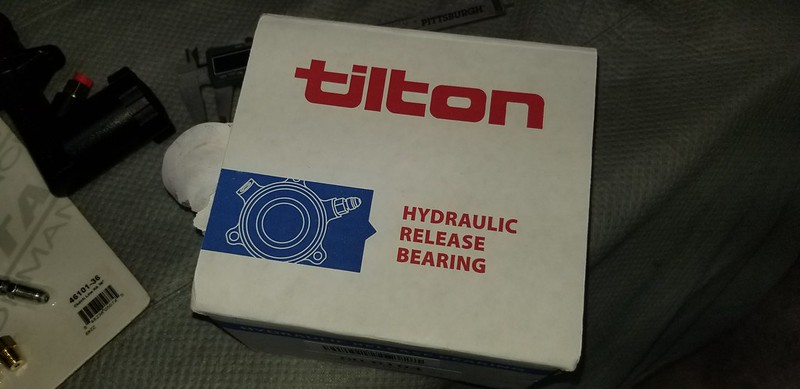

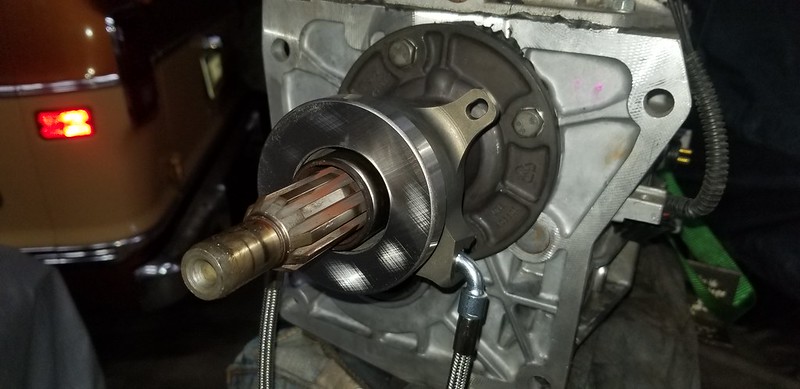

I am actuating it with a Wilwood GS Compact Master Cylinder 260-15098. They make these in a variety of bore sizes and intergal as well as remote reservoir versions.

Made up some quick mounts and firewall reinforcement plates from scrap metal.
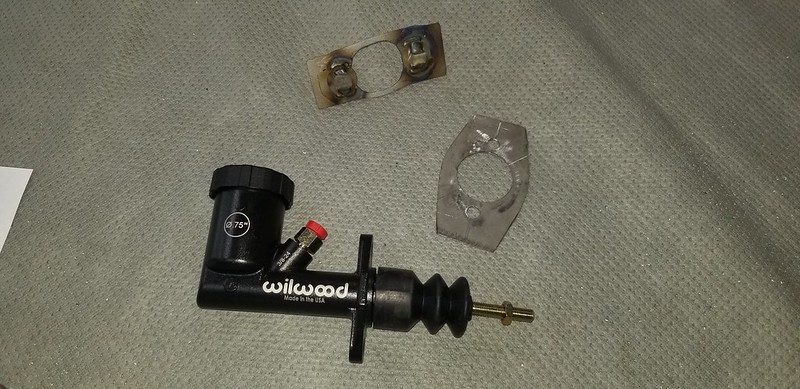
To get somewhat decent geometry to actuate the new clutch master I welded another actuator "nub" on the clutch pedal below the original one. If I ever need to revert back to the linkage and rod system I could do so without much trouble.
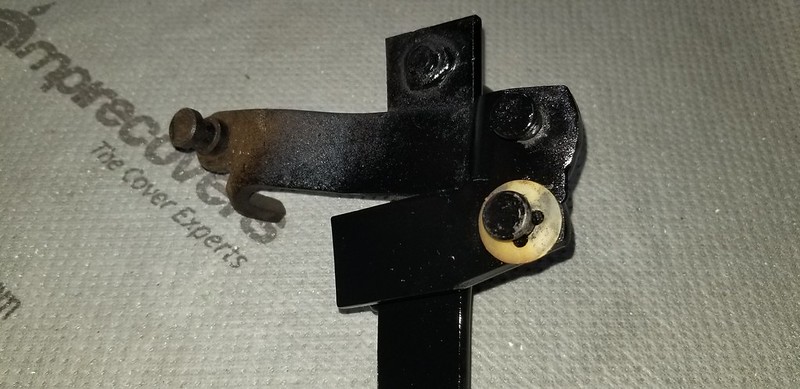

I had a helper at the shop help with a bit of the install.

Done, with a pedal stop added on the floor.

Clutch cylinder tucks in nicely next to the brake master, with just enough room to spin the cap off for fluid checks and fill.

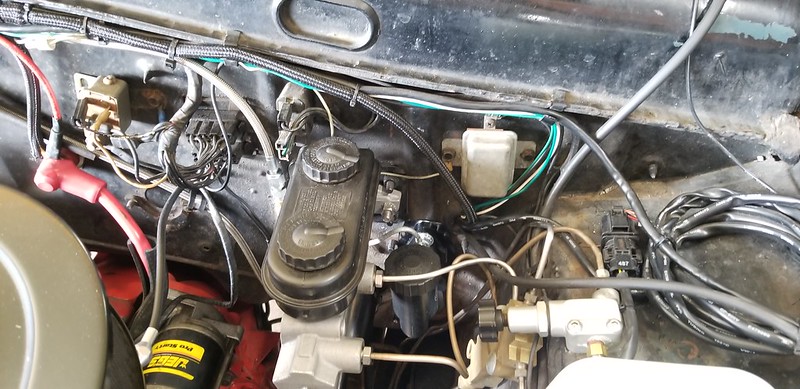
Since I had the Car on the Lift and the Trans out to Rebuild the Pressure Plate, I also Accomplished a few other things on my to do list for the car:
- Install the new Polyurethane Motor Mounts from www.polybushings.com
Old Mount on Right, Poly on Left. - The old Rubber Style Mount Was A Recent Parts store Replacement and Was already Moving around a bit.
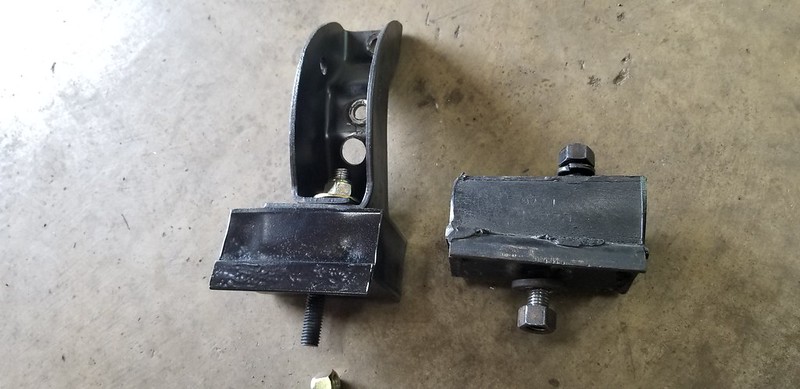
- Swap to a new steering box - front header needs to be removed to do this swap, and since it was out for the motor mount swap already, it made sense to do it now.

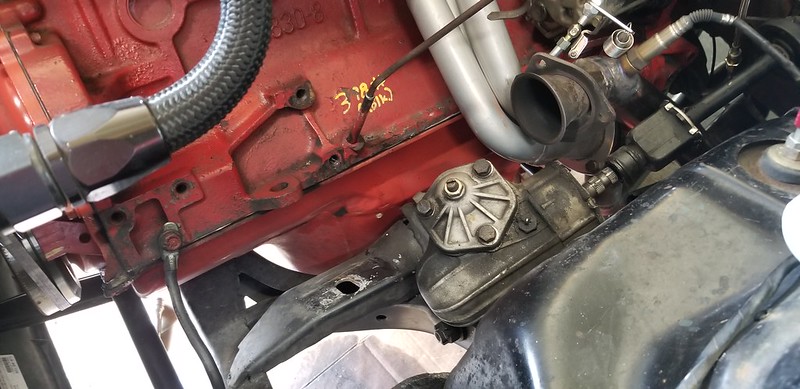
- And lastly, fix the god forsaken '60-'66 Mopar A Body Fuel Cap / Filler Neck Issue.
The left quarter panel on my car **had** nice paint on it until April 2022 when I took it to CMP, there it's a clockwise flow to the track layout meaning lots of repeated long / hard right turns.. Well on those right hand turns the gas sloshes back up the filler neck quite a bit, it ends up coming out of top of the filler neck and the cap can't hold it back, so it ate my paint away.

I have been thinking of a solution for a while, tried better / more / thicker gaskets on the cap, that failed, thought about relocating the filler inside the trunk, then I came up with this...
Get some 1.75" Inside Ø Fuel Hose... Continental 59211 will work..


And a 1 1/2" Ball Valve with 1 1/2" x 3" Pipe Nipples threaded on both ends.
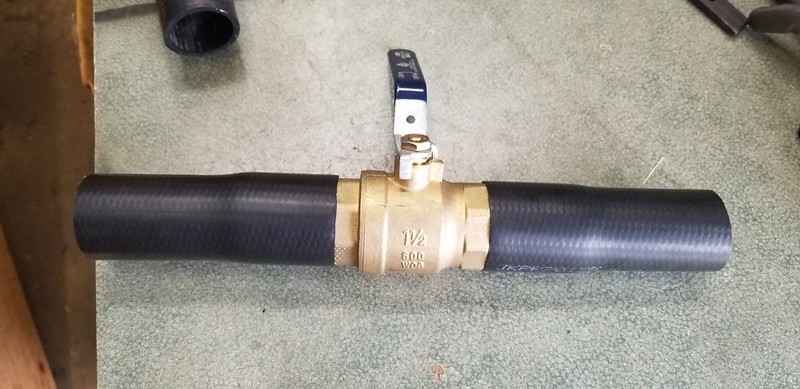
Cut out the appropriate amount of fuel filler neck:

Replace the Removed section with the valve.
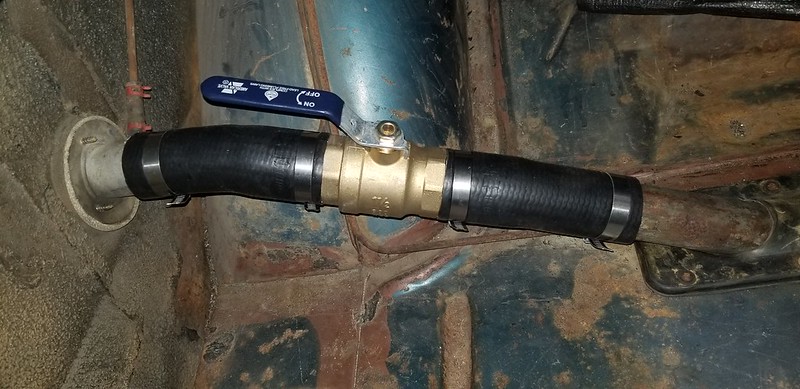

Close valve for track day, AutoX, or spirited mountain driving.

' Till Next Time!