Man, you guys are really delivering in this thread. This is EXACTLY the kind of feedback and insight I was hoping for….thank you. Lots of great callouts and things to consider in the design. I had started to respond yesterday, but the Internet ate my post – here’s a few additional pieces of info….
Size/Height –
The agreement with my sainted wife is that the outbuilding can’t be larger than the house, so my max square footage is 2,400. Although I have 5 acres, only about 2.25 is cleared and the lot is rectangular (330’ x 670’). I’m thinking of placing it approximately where the white box is below (ignore scale/size – it’s not remotely correct). There’s about 153’ from the house to the property line on that side, minus a 25’ mandatory setback from the line. Aside from the setback, there are no other zoning restrictions (height, front setback, size, etc)
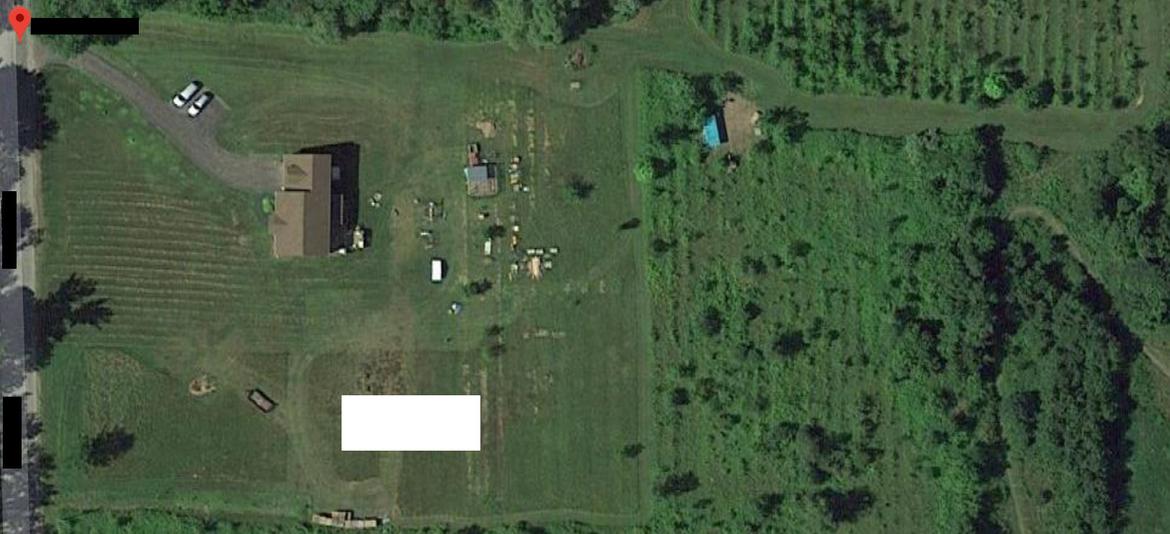
There’s also a 27’ pool to the side of the house that is not shown, so basically about 100’ of workable width. Keeping it towards the front/side of the lot makes for a shorter driveway, easier run for electric/plumbing, and I don’t have to trudge 400’ through knee-high snow to the barn. :)
On height, I was originally thinking 14’ on the chance that I someday get a 5th wheel trailer and want to pull it in there. Realistically (by the time that happens), it may end up heading South for the winter anyway. 12’ walls/doors would be fine for everything else I would work on in there.
Heating/Cooling –
Although I initially mentioned in-floor radiant heat as it’s supposed to be awesome, the reality is I think it will be more expensive and have a slower recovery time than I want. A few folks have mentioned radiant heat, which is what I have in my warehouse. That works GREAT, in that it warms up 1,250 sq/ft (with 16’ ceilings!) quickly and seems to be pretty cost efficient. I have one 40’ radiant tube down the length of the warehouse, but for the new shop, will want to look at BTUs once square footage is finalized. I think I’ve seen them with one burner and a long U-shaped radiant tube, or might do two separate units, one on each side lengthwise?
For insulation, any recommendations for a pole barn? I’ve seen spray foam as well as standard fiberglass batts used. For interior finishing (if it matters), I was thinking 4x8 sheets of particle board as the first course at the floor, then probably do metal panels above that for walls and ceiling.
The doors will be in the short end of the building facing the street, and I will probably put a 8’ roll-up door or double man door at the back corner, facing the house, for crossflow ventilation during the summer. One or two Big Ass Fans in the ceilings is probably a good idea.
Plumbing –
I have a septic system, and the junction box is about 18’ off the front of the house. The hope is that I can tie into that system, but not sure if that can be done to code. I’m really trying to avoid a separate system for one lousy bathroom. :) I’m also hoping to tap off of the house water to avoid a separate water utility charge. That said, having a sink, toilet, and shower in the barn will be important, as when I’m doing working on a project, I often look like I took a dive into a vat of grease and then rolled around in the dirt.
Electrical –
I’ll have a two-post lift, 220V welder, maybe a tire machine and balancer at some point, plus normal other stuff...drill press, bandsaw, etc. I’d like to do LED lights, with enough light to outshine the sun...need to do some research on these as far as style/type. Tapping off the house would require upgrading the house panel to 400A service (currently 200A), which I think can be done, but need to have RG&E out to inspect. I did want to run a separate conduit from the house with CAT6 to extend the network.
Floorplan/What’s Going In There –
There’s been a couple of mentions of segmented areas, which was exactly what I was thinking. General idea in my head is to take the rectangular building and divide into four general areas….back right corner is for the lift/longer term repair, front right corner is for movable projects or quick daily driver repairs), back left corner would be for vehicle storage, front left corner would be for….other stuff? Heavy duty shelving down the side walls for parts/supplies storage whereever there’s not floorstanding tools, probably using these.
The far back wall across left and right sides would be workbenches and toolboxes. Need to figure out where to put the bathroom, but if I can tap into the house septic system, then front left area would be the shortest run to the box. I’m going to spend some time with that floor planning tool that buzzboy suggested to see if there’s a chance this will all fit. 
Vehicles requiring indoor storage would include my road race Camaro, stage rally Honda, and a motorcycle (just one for now, but I’ve had up to 5 at one time). I’m missing an Answer...at some point, I think Mrs Rotaryracer and I will need a Miata (or Little British Car), so that will need indoor storage as well. I also have a single cab long box 4WD truck (with plow) and a crew cab long box DRW truck that I’d like to be able to pull in for maintenance during the winter…..ideally, I’d like to store the dually in the barn during the winter, but that’s not mission critical. I have a Subaru wagon I use for daily driver status and TSD/road rallies that will get serviced, but will not require storage. Finally, I have a 26’ enclosed trailer (probably 34’ overall length?) that I’d like to be able to back in on the left side of the barn for trailer work (rewiring, etc) and then pull right back out again.
All the lawn care/homeowner detrius will get moved to the two car garage attached to the house, so no need to store lawn tractors, etc. No woodworking equipment or other hobbies need to share space...sadly, I'm pretty laser focused on vehicular-related pursuits.
Thanks again all....