Schedule 80 steel pipe to 1/4"plate, because it's what I have lying around. .035 HF flux core wire, on my 170 amp Chicago electric, with no modifications. Cleaning done before welding was an 80 grit flap wheel and a grinding disc on my grinder just to get the millscale off and try to make it shiny.
This picture was my first try. Seriously, first time I've turned this welder on and tried to set a bead. Power setting 3 of 4, wire feed speed at 5 of 10. I went what I felt was a movement slow speed, pulled the weld towards me. I didn't make any letters or dot patterns or anything because I couldn't see very well, just pulled it along.
I don't think it's terrible, and it alone withstood a few whacks with a 3lb hammer.
This second picture I did a little bit later after "practicing" on just 1/4"plate. Wire speed 8.5, full power.

Obviously too much power for the steel pipe, I burned right through, but got one solid tack. I tried to angle myself better, and make little e's but couldn't tell I was burning through until I did.
So how did I do? I know there is a lot of room for improvement, and without cutting and etching we can't get a great analysis, but do they look alright(well the first one)?
This is going to be a grinder stand. On the other side of the tube is a piece of plate I welded on 10+ years ago, the last time I ever welded. It's pretty hideous, but it holds.
Turn up the heat and or slow down. Aim the wire at the plate and let it flow to the pipe. That will bring the plate up to temperature without blowing out the pipe.
Plate to pipe. Ok, I'll give that a try.
Is it normal to have scorch marks around the ground clamp? I feel like I should make it heavier.
If you are welding rusted metal, you will get some arcing around the ground clamp. If it doesn't settle down and stop arcing though, you will have a hard time keeping a steady arc.
Clean is good. For the best welds, clean everything down to shiny metal. Rust, scale, and paint, contaminate the welds, causing holes and voids, as that material flashes to gas.
I agree with Toyman. Furthermore, I can't be sure, but the splatter I see leads me to believe you should get closer. Most folks recommend 1/8" away. That seems insanely close to every rookie ever. We're talking almost touching the freaking weld.
To start, round pipe may be a little advanced. I'd suggest maybe 1/4" plates 1/16" to an 1/8 " apart. Just weld flat. If you can't break them apart with a hammer, you're getting somewhere. Doing "e" or "u" shapes, as you noted is important. You're trying to get almost to the point of burning through, but not so far that you actually do. Everything becomes liquid just long enough, but is busy solidifying before it falls apart because you are by that time in another spot. If that makes any sense.
After re-reading your first post, you said you couldn't see. If you can't see, you can't weld. You have to be able to watch the weld puddle. This is doubly true for flux welding, because there are two puddles and you have to be able to differentiate between them.
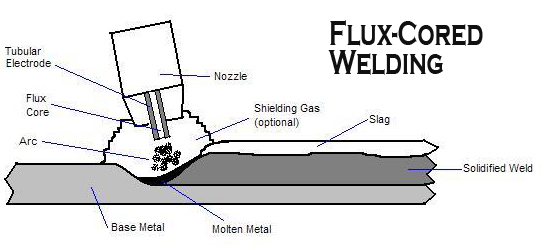
See the small amount of molten filler under the tip. That is what you have to watch. Watching the slag give you a cruddy looking weld. If I'm flux welding, I usually remove the nozzle for visibility. The metal puddle will be a slightly darker than the slag puddle. It will also snap forward as the weld progresses. You will move the tip, then a second later the puddle will jump forward, then move the tip again. Get a decent helmet and adjust it so you can see the entire weld.
With differing thicknesses you weave it and stay on the thick parts longer than the thin.
Start with just making beads on plate and move up from there, tubing is difficult.
I will reiterate what has been said above, but the most critical point is, You cannot weld if you cannot see the weld. Period. Welding is very much about managing the puddle.
First pic is way too little heat. Second is an obvious lack of vision, combined with the arc flowing to the pipe, not the plate.
Watch the puddle.
NOHOME
UltimaDork
6/22/17 6:49 p.m.
Lot more cleaning needed. Keep in mind that the backside of the weld needs ot be equally clean.
Forget that 80 grit, you want 40. Have at least 1" beyond the bead cleaned to shiny steel.
Toyman has it right. I would be welding that on the top setting of my Lincoln 185. I would start on the 1/4" and lead the puddle over to the tube and let it wick up the side.
I have no idea how people weld without an auto-darkeing mask. I usually have a light pointed right at the seam.
As mentioned, you need to learn to see the puddle if you are ever going to learn to weld. You ever see one of those hidden image pictures that looks like a bunch of dots until you stare at it long enough that the picture comes out of the background? Learning to weld is a bit like that. The puddle that you need to control is buried under a lot of flash and sizzle, but once you do see it for what it is, you will never have a problem seeing it again. Best to practice on the thick stuff on a high setting running straight beads until you learn to see and lead the bead.
I'd start practicing stringer beads only on the 1/4" plate. You'll weld cold and you'll see hot w/ speed and settings. Learn that first. You'll get to the two different thicknesses and joints in due time.
Grind the mill scale off much as possible but muriatic acid will clean the steel down to it's pores. Ten minute soak and rinse w/ water to neutralize. I know people don't like acid but it's an awesome weld prep/ cleaner on steel. There should be no doubts or excuses of not clean enough after that.
Well, the only steel I have at all is plate of varying thicknesses, so that helps. It's all just been exposed to the elements for ~13 years. Muriatic acid you say? I'll add it to my shopping list, with wire wheels for the grinder and some better flapper discs. Let it evaporate or clean it with something before welding?
I tried 40 grit on my belt sander, worked about as poorly as you'd expect. But I've seen the shinyness, it can be done.
When I said I couldn't see, let me clarify, it was due mostly to poor positioning. Sitting on the ground trying to keep the awkward tube up in the air to make the weld didn't leave me in a very good spot. Luckily, that tube is a decent enough height to run straight lines on a plate at. I really need to make or find a basic welding table I can stand comfortably over.
I do need more lighting than just the ceiling lights. And some magnetic clamps, but definitly a light that I can shine directly on the work piece, maybe even mount one to the helmet or the torch.
zooming in, not shiny enough. The gap on the right is from a piece of spatter finding my foot.
When I really zoomed in and started looking at these pictures, I can see a bit better where I'm just putting weld on top of metal vs where it's actually doing something.
At least I can spend most of tomorrow putting down beads, playing with settings, and grinding them off.
For gettign the rust off thicker stuff just lightly run over it with an angle grinder.
The second set looks better, but again, turn down the wire feed speed, and slow down. It's still looks to be on the cold side to me. There is a fine line between too fast and too slow.
That steel is pretty heavily rusted, it's going to take a bunch of heat to burn through the rust. Laying a pretty bead on that is going to be difficult without a 6011 rod and a lot of amps. Personally I'd hit it with a grinding disk on a angle grinder, and get it down to shiny steel.
Practice is your friend. Don't be afraid to twist the dials on the machine and see what happens.
If you are welding at a bad angle, listen as well as look. A bad weld sounds different than a good one. More than once I've laid down a pretty bead, that was nowhere near where it needed to be.
For getting the work up off the ground, a cheap set of saw horses and a piece plywood will work. I don't own a weld table. As much as I would like to, they are too ugly for the yard and too damn heavy to move often.
Keep up the good work.
NOHOME
UltimaDork
6/22/17 10:09 p.m.
When I have friends doing welding in my shop I often tweek the wire speed while they are welding in order to fine tune the setup for them. Try it: while running a long bead have a friend do minor adjustments to the wire feed so you get a feel for what feels
and sounds right.
Pulled this 3/8" plate outta the scrap bin at work. Most people wouldn't berkeley w/ it. Ya couldn't drag yur nail across it. This is the kinda stuff I learned to weld on because it was free.
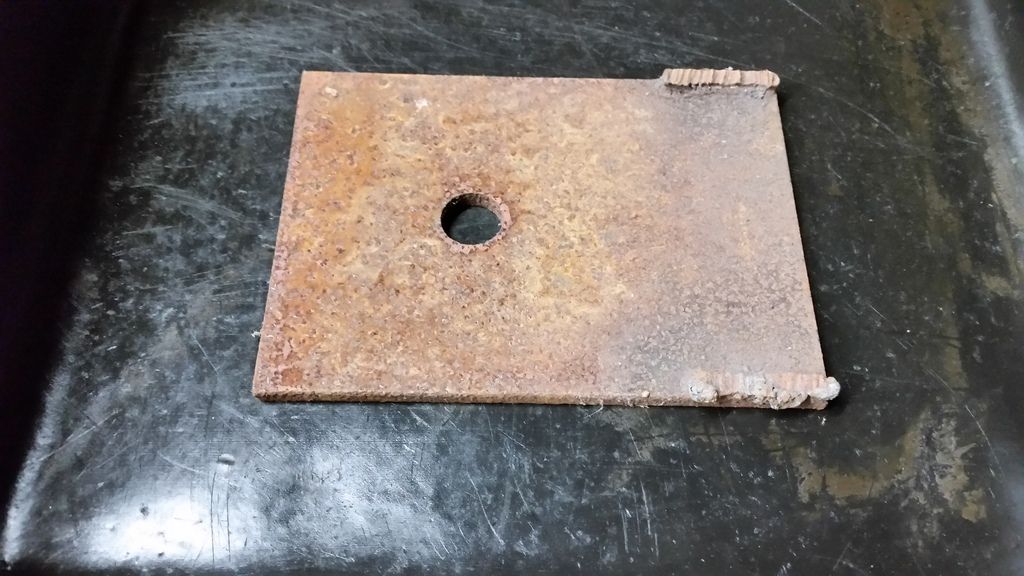
Sure, I could grind or wire wheel it down but soon learned muriatic acid would remove cadmium, galvanized, zinc as well as rust from steel w/ little effort.
Same plate, 3 beers worth or 1.5 hours later in layman's terms. Soaked in a plastic mortar pan w/ 1-2 quarts of acid, removed when 'bubbling' stopped, remove from pan and rinse w/ water to neutralize the acid. I wouldn't hesitate to TIG this now after a mild brush, yet alone MIG.

I doubt I could ever grind or wire wheel that plate this clean, pits are pretty deep. The residue is prolly red oxide of the day.
Not sayin' a new welder oughta do this but learning on clean steel is a plus, that at least takes dirty metal outta the equation. But yea, you wanna experience welding through dirt/ rust n such too.
Precautions need to be taken w/ using acid. It will kick yur frickin' ass big time.
Enough, I'll prolly post a separate thread on acid. Now back to yur regularly scheduled programming.
Everyone is giving you good advice, I have some more. Get a spool of Lincoln NR211 flux core wire, it is the best self shielding wire. Schedule 80 is thick walled pipe, grind a bevel on the pipe leaving a n 1/8" root face. clean the plate and pipe with a grinding wheel on an angle grinder. Because schedule 80 is thick it often needs to be preheated before welding 250-500 degrees is about right. Make sure that you are using a drag angle, If there is slag you drag. On the root pass try to use a stringer bead with little or no weaving motion. On the second pass weave and fill in the bevel. For more info look at Welding tips and tricks on you tube
Braden
With .035 NR211 wire 1/2"-5/8" is the suggested contact tip to workpiece length
I started off today cleaning up an endcap I had. The whole piece is 5/8" or so, and it's been acting as an anvil for me splitting wood for the smoker or beating things into shape.
It's shinier than the picture suggests.
I used these settings.
And wound up with beads looking like this. 
Grinding them off takes way longer than putting them down (duh!), but I think I'm getting better.
More patience, some wire speed fiddling with some tension adjustments, and things are looking better. I have to go get a bunch more grinding wheels and a wire wheel for the grinder, but I'm going to keep chipping away at it.
I did a few with blatantly wrong settings just to get an idea f what it looks and sounds like. The differences were very easy to see.
The bead is getting easier to see. Adjusted the helmet some, and put my face closer than I'd like to, but I was able to make out the leading edge from the slag bubble, I'm pretty sure.
I'm also trying to get someone more experienced to come over and play with the setting while I weld, like NoHome suggested, to really get dialed in, but I think things already look better than they did thursday.
This is still all with the Harbor Freight wire too. I haven't opened the spool of Lincoln yet, I suspect it will help too.
Are you using the harbor freight wire? Because i learned that good wire makes a lot of difference. And harbor freight flux core wire aint good wire.
Dusterbd13 wrote:
Are you using the harbor freight wire? Because i learned that good wire makes a lot of difference. And harbor freight flux core wire aint good wire.
For now, yes, its the HF. I do have a spool of lincoln 211MP flux core for when it runs out. I was originally just going to toss the HF wire when I brought the welder home, but after watching This comparison from weld.com I decided it was good enough to practice with.
From what I've seen, the big problem with HF wire is diameter consistancy throughout the spool. A couple .000" one way or the other throws off the tension, and then the wire speed. It's good enough to lay down and grind off again, but I won't be using it on my daughters wagon or anything important. When I get a gas tank, if I get a gas tank because I do everything outside, it will be lincoln solid wire only.
You have the smaller HF welder right, the 120v 90amp? Did you make it DCEN or is it still factory AC settings?
From my prepurchase research, I saw that as a suggestion from everyone from harbor freight reviewers to the guys on weldingweb.com
Looking better. Keep up the good work.
Get some thinner plate, like somewhere in the 16 gauge to 1/8" range so you can see what too hot looks/feels like.
In reply to RevRico:
Box stock except for wire. Works fine for what i use it for. Not nearly as nice as dad's lincoln with gas.
The "always on sale for $89" is the flux core im using.
I went out on a little adventure and picked up more grinding wheels and some wire wheels for the grinder. Damn are those night and day compared to the ones in my drill.
I also found some 1/8" I had from an old project, and sliced it down into 3-6" long pieces. Set the box up like the cheat sheet on the side says too, and made some ugly welds.
I'll spare you the big ugly beads on the flat that almost burned through, and show you this zoomed in cut corner that I did in "vertical up" inside and out.

Obviously I didn't etch it, just cut a corner weld in half with the portaband. For as downright ugly and terrible as the corner looked, cut opened and unetched, it doesn't look bad. I'm going to soak this piece in vinegar over night and see how it looks tomorrow. The portaband really didn't like cutting the weld, which may be important to know later.
I also think I'm going to move all this welding stuff over to my casting thread, "rev plays with metal" after today.
I still have a bunch of stuff to practice on, and god do I appreciate all the tips and help from everyone. I was trying to get a video for some more criticism, but my gopro isn't a big fan of these types of shots, so that failed.
Somethin' I was thinking about the other day while trying to describe how to weld decent to the new hire: Don't focus on laying wire IN, focus on melting the metal you're welding together, and adding wire to that weld puddle.
Everything else follows from that: getting the current right, the wire speed right, focusing more on the thicker/heavier piece when moving the puddle around, even tricky things like MIGing stainless or rusty mild steel exhaust, or worse, rusty stainless exhaust.