“I’m finding that the older I get, it’s
not that I learn new things, it’s more
like I find out how much of what I
know is common knowledge.”
–Sam Lipsyte
We’ve owned our trusty 1997
BMW M3 for more than a decade,
and during that time we’ve learned
most of the E36 chassis’ common
problems. Fortunately, expertise
on the E36 M3 is abundant, with
answers to nearly every malady as
close as a Google search.
This online knowledge should be
the first resource in any troubleshooting
process; unfortunately, we
learned this the hard way.
BMW was our featured marque at
last year’s Speedfest at the Classic
Motorsports Mitty, and we used
the M3 as a chase car during the
weekend’s parade and touring laps.
Our task was simple: make sure that
everyone played by the rules.
We had noticed an occasional
rattling noise coming from the rear
suspension, but when we inspected
the car, nothing jumped out at us.
The noise wasn’t severe, or predictable,
so we chalked it up to worn
subframe and differential bushings
since the car was 18 years old,
sported 169,000 miles, and still had
the original bushings.
This is the point where we should
have consulted the interwebs–but didn’t.
At the end of the Mitty weekend,
we pointed the car south and
headed home. We were about 30
miles away from home when the source of the
rattle revealed itself–and left us stranded.
The rear differential on an
E36-chassis BMW is tied to its
subframe by just a single bolt. Over
time this bolt has a tendency to
back itself out, and if left unrepaired
will shear. Once the bolt breaks,
a violent vibration signals that the
differential is now free to move,
upsetting the driveshaft and differential
alignment. Fortunately ours
broke as we slowed for a gas stop;
we are still grateful it didn’t let go at
70 mph.
Once we had the BMW towed
home, we decided that it made
sense to not only change and
reinforce the diff bolt, but also to
freshen our subframe and differential
bushings. This is a major undertaking
because the entire subframe
needs to be removed. A lift would
be a necessity, and expertise would
come in handy, so we trailered the
car to Pompano Beach, Florida, when we
enlisted the help of Rennie Bryant,
owner of Redline BMW Performance.
We arrived at Rennie’s with all the
parts we thought we’d need, including
new bushings. Since our BMW
is predominantly a street car, solid
metal pieces would be too extreme;
instead we opted for more compliant
Delrin bushings for the subframe,
and slightly softer Powerflex
urethane bushings for the rear diff.
Our car sees significant track time,
so we went with Powerflex’s Black
Series bushings, which are a bit stiffer
than their standard poly units. Our
Delrin pieces were chosen because
we had previously installed Condor
Speed Shop’s Delrin bushings in our
rear control arms, and were very
happy with their performance; a bit
of stiffening for the rest of the rear
suspension seemed in order. The
Delrin and poly bushings would allow
much less deflection than the stock
rubber pieces, but wouldn’t be so stiff
as to transmit excessive noise, vibration
and harshness.
We pulled up to Redline BMW
early on Saturday morning, ready
to go. Redline BMW is an extremely
busy shop, and lift space is at a
premium, so we had to complete
the installation by Monday morning
in order to free up their valuable
space. At the time this seemed like
an easy proposition.
Once on the lift, the car needed
to be disassembled. This included
removing the exhaust, disassembling
the rear brakes–including the emergency
brake–and disconnecting the
driveshaft and rear suspension.
Now the hard part: Once the
mounting bolts were removed, the
subframe assembly was ready to
be released. Using a transmission
jack as support, and with Rennie’s
help, we carefully lowered the
assembly onto a nearby workbench.
This was done with care and deliberation,
as the subframe assembly
weighs nearly 200 pounds. Fortunately
neither of us sneezed, and
the subframe soon was resting
safely on the bench.
Once our subframe was out of
the car, we could easily inspect
the mounts that attach it to the
car’s unibody. We didn’t expect a
problem, since BMW reinforced
these mounting points on the M3
models. There have been rampant
internet rumors of subframe
mounting points ripping on the E36
chassis BMWs, and while this rarely
occurs, it always makes good sense
to inspect and evaluate. Fortunately,
our mounting points were
in perfect order.
Our next step was to remove the
old bushings from the subframe and
differential cover. We removed the
subframe bushings with the use of
a portable pneumatic press. Some
prefer to burn out the old bushings
and cut the remainder with a
reciprocating saw, but we prefer to
use a press. Once the old bushings
were out, our subframe was ready
for new ones.
This is where we ran into our first
big hurdle. The E36 M3’s rear subframe bushings
are slightly different than the
fronts: The rear bushing sleeves are
slightly wider to ease installation.
Unfortunately we received four rear
bushings and no fronts. We realize
that mistakes happen, especially
with parts that look so similar. But to
further compound our problems, we
cracked the differential cover while
attempting to remove our old bushings
on a hydraulic press.
It was now around 9 on Saturday
night, and things were looking
bleak. Somehow we needed to complete
this job by the end of the next
day, but there was a lot left to do.
Instead of pushing our weary minds
further, we settled in for a night of
fitful sleep.
Sunday morning found us still
doubting our odds of success.
We needed new bushings and a
replacement differential cover; we
also had to extract the remainder of
our broken differential bolt.
The bushing replacement was the
most daunting problem, as most of
the business world shuts down on
Sunday. Fortunately Rennie had a
solution: Redline BMW frequently
uses Condor Speed Shop bushings,
and Rennie just happened to have
the owner’s personal cell phone
number. A quick call to Carlos
Mendez solved our biggest obstacle:
Not only did he have the rear
subframe bushings that we needed,
he brought them over to Redline
personally and offered to help.
Rennie had one more trick up his
sleeve. He dove into the depths of
his shop and emerged a while later,
bloodied and greasy, with a replacement
differential cover in nearly
perfect shape. We heated the cover
using a propane torch and easily
pressed out the old bushings.
After a bit of cleaning, we installed
the Powerflex Black Series differential
bushings, which we sourced
through BimmerWorld. These
bushings would limit the movement
and deflection of our differential,
allowing for better launches, and
improved handling. Fortunately the
new bushings slid into place and fit perfectly.
Next on our list was the offending
differential bolt. To our amazement,
it was easily removed with the help
of a reverse-thread drill bit, leaving
our differential casing unharmed.
Now to make sure this problem
never happened again. Our solution
was Active Autowerke’s differential
support bracket. Installation
requires drilling two additional
holes into the subframe to secure
the beefy metal plate that sandwiches
the bracket and subframe
together for additional strength. The
Active Autowerke kit also comes
with a stronger differential bolt to
help eliminate the possibility of this
common failure.
As the sun set on Sunday, our
BMW was finally back together. It
had been a long and arduous process,
but the results were worth it.
The new bushings were a revelation,
as our M3’s rear end feels much
more planted than before. The car’s
cornering ability has been increased
exponentially with only minimal
drawbacks: Our ride is slightly less
compliant over sharp bumps, and
there is a slight gear whine audible
at certain engine speeds. Overall,
however, we’ve been thrilled with
the increase in performance and
improved feel of the now-rejuvenated
BMW.
If you are attempting this bushing replacement on your own, make sure you have a lift and an extra set of helping hands at your disposal. While this isn’t an expensive modification, it’s also not a one-person job. Fortunately it’s worth the effort.
Sources
Active Autowerke
activeautowerke.com
(305) 233-9300
BimmerWorld: Powerflex differential bushings
($144.99),
bimmerworld.com
(877) 639-9648
Condor Speed Shop: rear subframe bushings
($165)
condorspeedshop.com
Redline BMW Performance: tech help,
redlinebmwmini.com
(954) 783-7003
Comments
Hey! I’m finally going to be tackling this job on my m3 sometime within the next month or two, and I was thinking about going with this same setup, but I’m a little nervous after reading about some of the issues people have had by running bushings with different stiffness ratings in the rear. Have you had any issues with yours? What’s it like on the street? Thanks!
Turbine said:
Hey! I’m finally going to be tackling this job on my m3 sometime within the next month or two, and I was thinking about going with this same setup, but I’m a little nervous after reading about some of the issues people have had by running bushings with different stiffness ratings in the rear. Have you had any issues with yours? What’s it like on the street? Thanks!
I don't have an M3, but I somewhat recently rebuilt the entire rear subframe on my E34 touring. Now, I opted for Powerflex street (yellow) subframe bushings and OEM rubber for the differential and RTAB bushings, so it's not 100% comparable. I haven't noticed any negative effects of using harder bushing for subframe location in relation to their interaction with the rest of the rear bushings. I think a good rule of thumb is to keep parts of the same system a similar hardness. You don't want solid motor mounts with rubber transmission mounts, but I think its generally safe to run stiffer subframe bushings with softer differential bushings. Maybe someone with more experience will contradict me, but that's the assumption I work under and haven't had any bad results.
In reply to MTechnically :
Alright awesome! Thanks for the info
MTechnically said:You don't want solid motor mounts with rubber transmission mounts,
...Yes you do! Those mounts are 3 feet apart along the length of the car, across one of the main points of chassis twist and flex. If you don't have some give in the trans mounts, WHEN (not if) the chassis flexes and twists, it will stress the trans case and cause weird shifting at best and broken transmission cases at worst. The end of the transmission is not engineered to be a stressed member, the mounting point is just strong enough to hold the transmission off the ground and anything else is purely coincidental.
I have done this job in my home garage. It's do-able, but my advice to anyone is assume you'll be at it for a few days before it's all said and done. And always always go ahead and replace the BMW-specific mounting bolts that screw into the chassis before you re-mount the subframe. If they're old and you break one, the whole unit needs to come off the car to replace it.
Knurled. said:
MTechnically said:You don't want solid motor mounts with rubber transmission mounts,
...Yes you do! Those mounts are 3 feet apart along the length of the car, across one of the main points of chassis twist and flex. If you don't have some give in the trans mounts, WHEN (not if) the chassis flexes and twists, it will stress the trans case and cause weird shifting at best and broken transmission cases at worst. The end of the transmission is not engineered to be a stressed member, the mounting point is just strong enough to hold the transmission off the ground and anything else is purely coincidental.
Fair point. I hadn't thought about the forces at play in that specific example. I've always heard that you do want to be careful using mounts of wildly different stiffness within the same system, because you will wear softer bushings much more quickly. Maybe I was misinformed about that.
Nice work! This job is in my M3's future. Every other bushing on the car is original, and surprisingly not as horrible. The subframe bushings look like crap, though. I'll probably go with poly subframe bushings and OE diff bushing.
One of these days, the car will be off jackstands. It's been in hovercraft mode for months. Hopefully done by the Mitty, as an arbitrary goal. We'll miss the GRM crew this year.
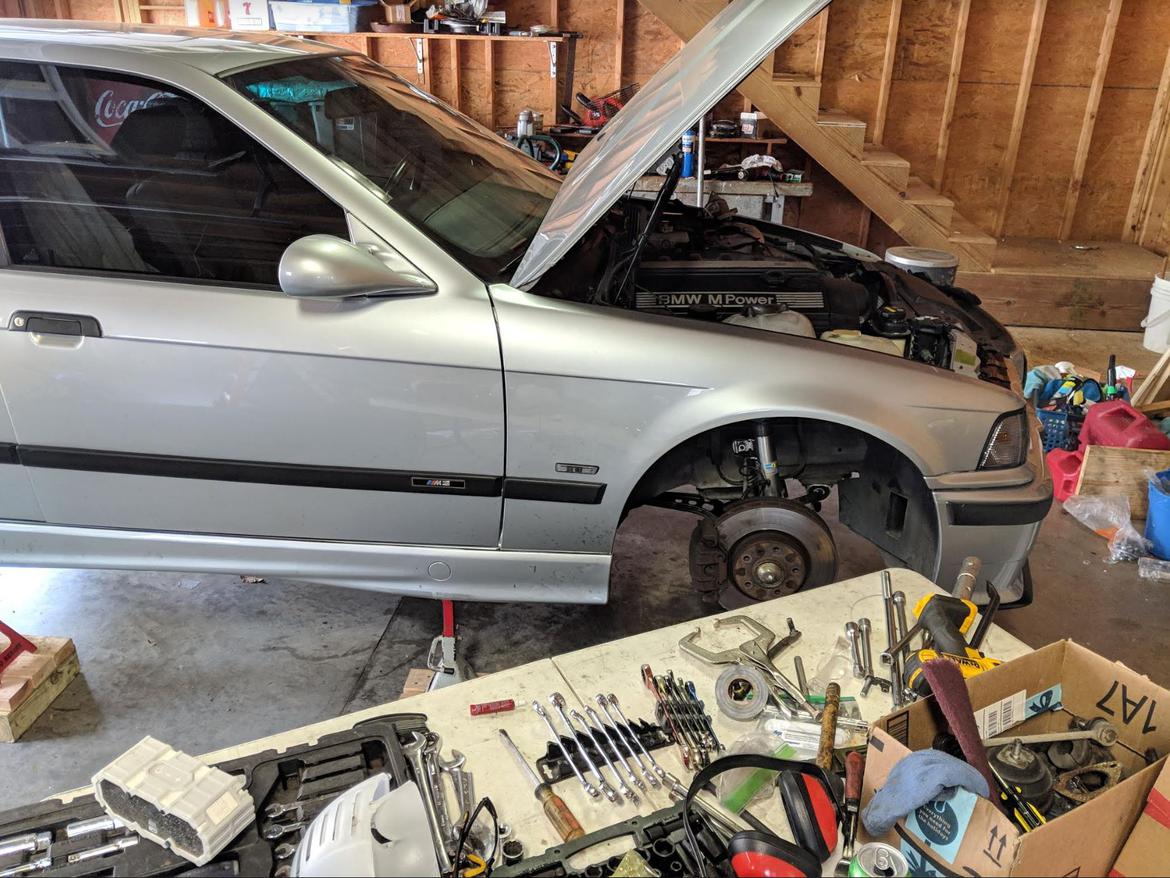
Displaying 1-7 of 7 commentsView all comments on the GRM forums
You'll need to log in to post.