Turbocharged engines are a double-edged sword. More power is readily available through more boost, but so is more disaster. So, when you even vaguely consider adding boost to an engine, you need to have a plan to at least monitor the other factors that will be affected by this additional air. Most notably, this means keeping an eye on how much fuel is getting mixed into that combustible fog being rammed into your cylinders.
The relationship between fuel and air in your engine is multifaceted. On one hand, you have something called the stoichiometric ratio, which is the relationship between air to fuel so that when combustion occurs, there is no leftover fuel or its catalyst (oxygen, in this case).
For typical gasoline, on Earth, where air is about 21% oxygen, that ratio is 14.7 parts air to 1 part fuel. Of course, different gasoline blends and elevations will affect this number slightly, but that’s the baseline.
But that 14.7:1 ratio doesn’t tell the whole story of max potential. See, while you may be burning all of the fuel at that ratio, there could be secondary effects that rob the engine of maximum power. Complete burning of the fuel means less atomized liquid fuel in the combustion chamber, which means less cooling of interior combustion surfaces, which means more energy lost as heat, for example.
Now, every engine is different, and most are going to make their maximum power at some ratio that is not the ideal 14.7:1. But this ratio is only attainable through dyno testing and precise monitoring of that air/fuel ratio. If you have a modern car, monitoring that ratio is usually as simple as slipping a connector on the OBD port and using some software or a hardware logger to read the data being sent to the onboard computer.
But our 1991 Toyota MR2 Turbo has no such modern accoutrements, and the factory oxygen sensor that sends exhaust data to the on-board computer is extremely low-resolution.
The solution is a proper wide-band oxygen sensor, which usually means the installation of an accompanying in-dash gauge or monitor to keep track of the numbers. But we found an easier solution that installs in minutes from Performance Electronics. The company’s PE-Wideband kit consists of a Bosch sensor, which connects to a Bluetooth-enabled controller that can be monitored via an app on your iOS or Android device. All it requires is a power and ground connection, so all the wiring can stay under your hood—or engine cover, in our case. The unit also has CAN inputs and outputs and a 0-5v output to connect it to dedicated gauges or your programmable ECU.
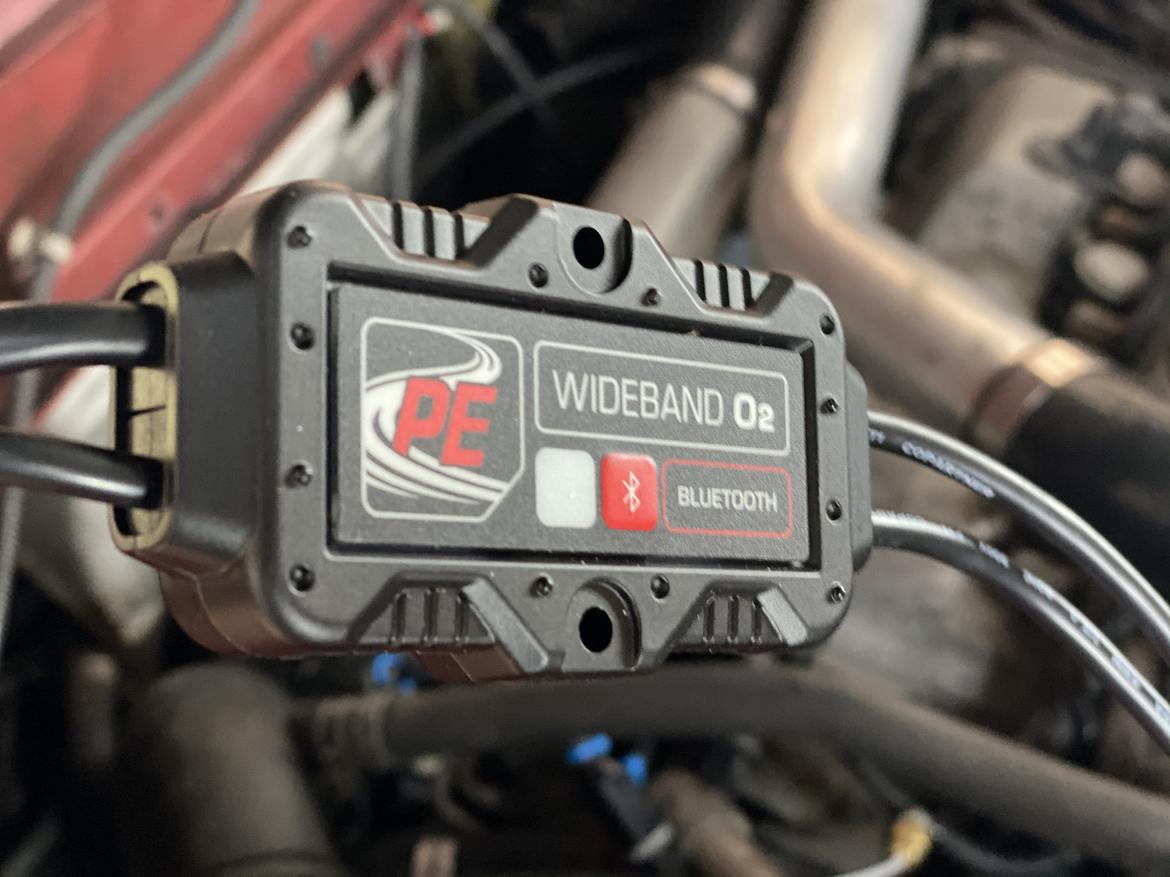
Installation on our MR2 was a snap, as we’d just installed a TCS downpipe that we had the foresight to order with an extra oxygen sensor bung already installed. We simply removed the plug, installed the new sensor, and plugged it into the unit. We were up and running within 30 minutes. The kit also comes with a mild-steel, weld-in bung if you don’t already have an available and willing bung hole. Stainless bungs are available as well.
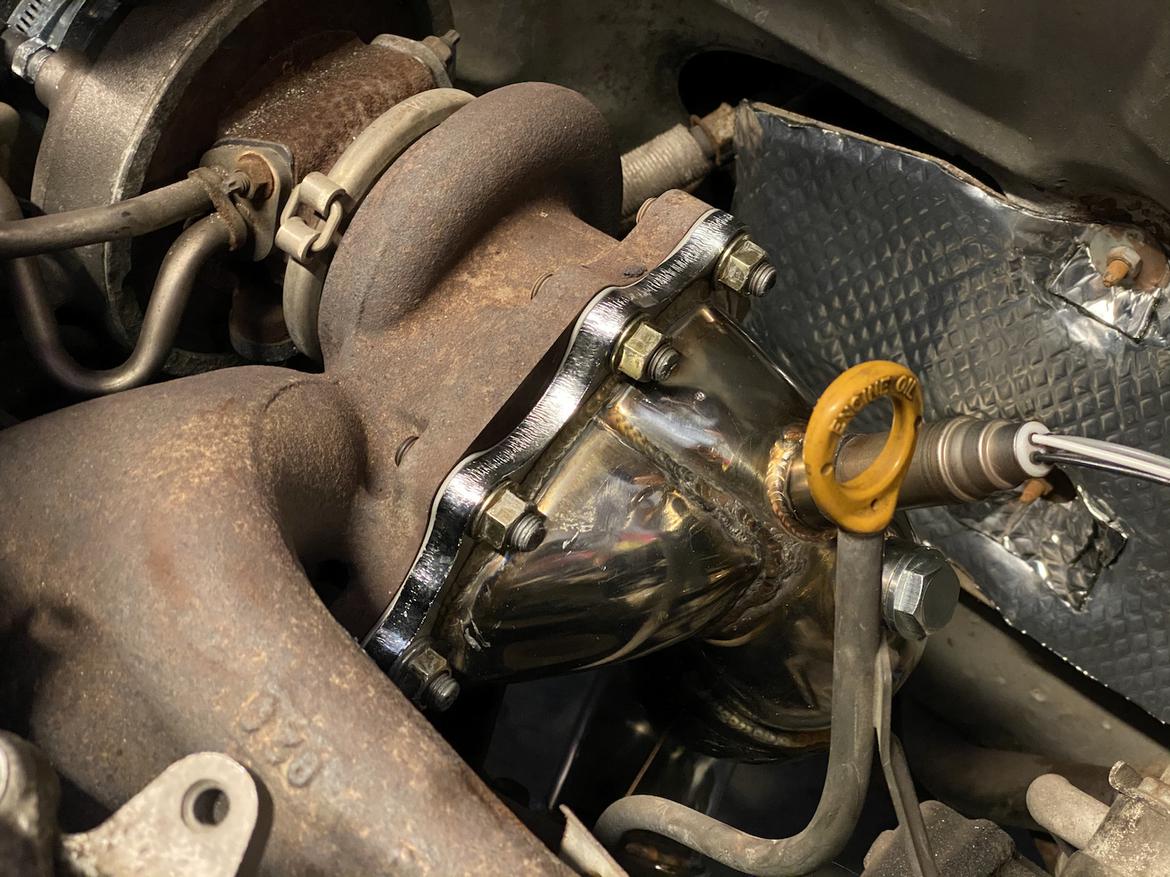
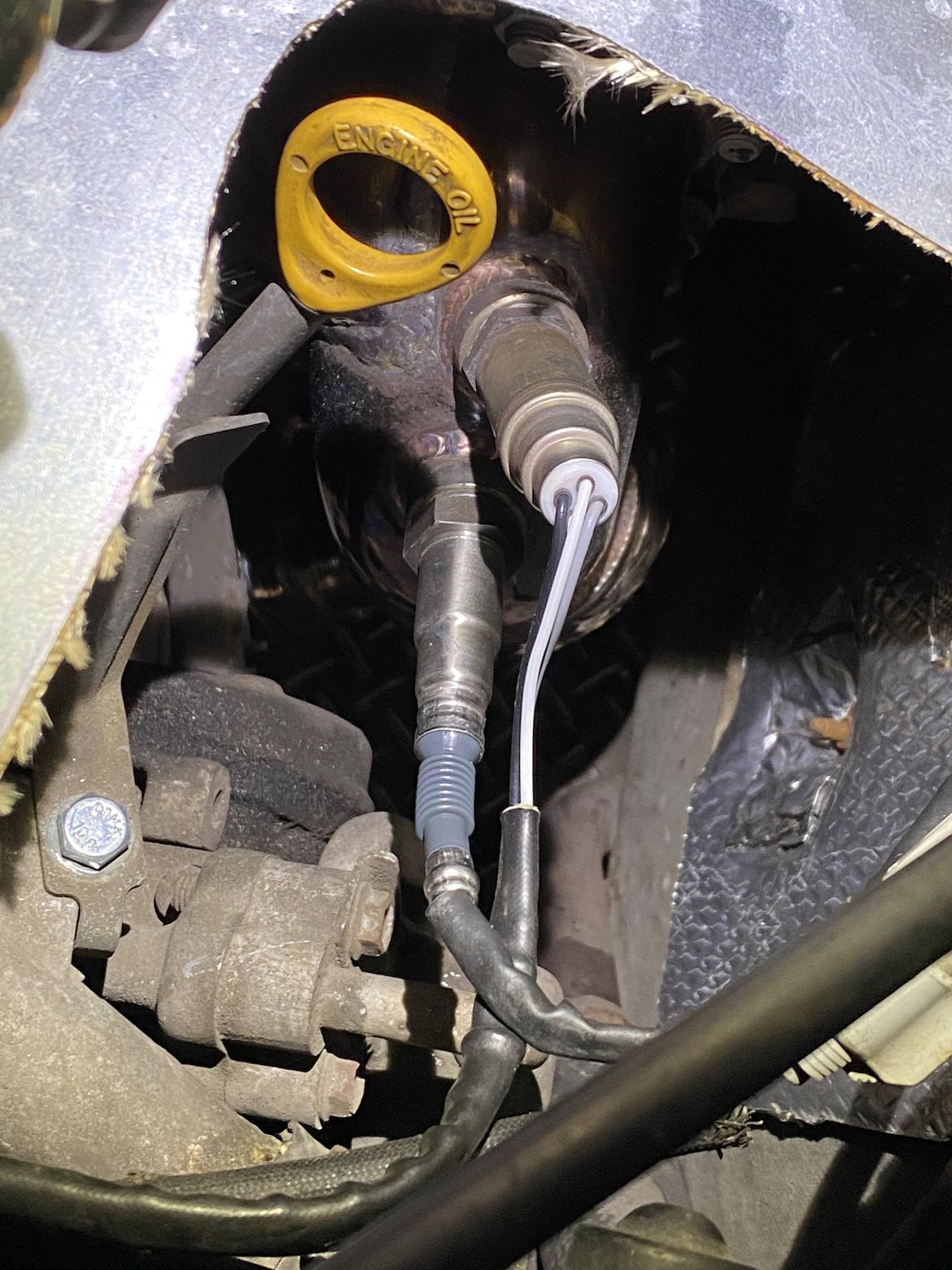
The app is easy to use, has real-time monitoring and some basic logging features, and reads AFR either as ratio or lambda. Typical AFR shows ideal as 14.7:1, with lower numbers—meaning more fuel per air mass—indicating a “rich” condition and higher numbers indicating a “lean” condition. Lambda expresses ideal stoichiometric ratio as 1, with readings lower than 1 indicating rich and higher than 1 indicating lean.
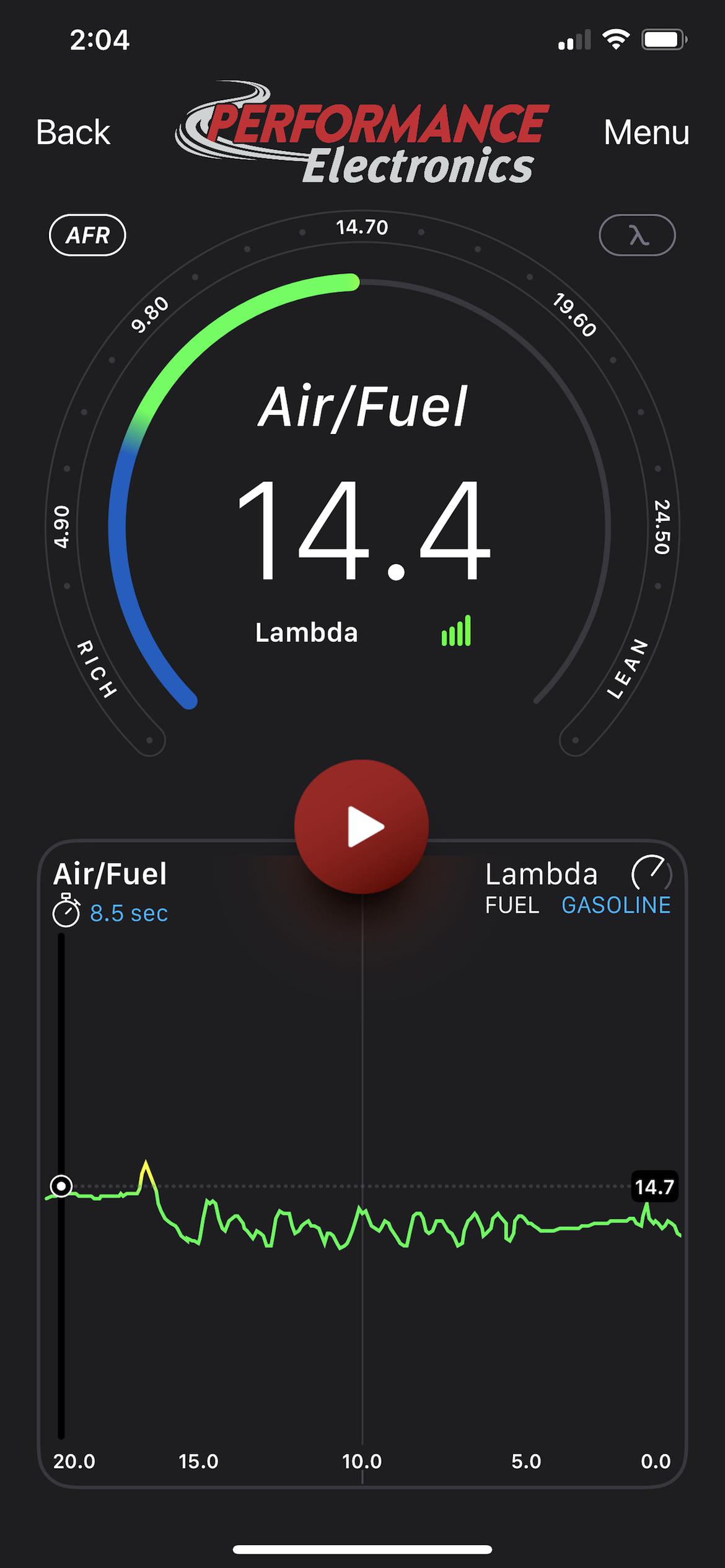
So, now that we can easily monitor our air/fuel ratio, what do we do about it? Well, first off, it’s good to know that our engine is properly metering fuel. At wide-open throttle, the on-board ECU richens the mixture to around 11:1, which means a lot of unburned fuel—but also a lot of safety margin for not producing excess heat or preignition, which can quickly kill an engine. As we add boost and unrestrict airflow, making sure the fuel mixture is within the safe zone will be additional insurance against premature disaster.
But if we ultimately want to make the most power that we can for a given configuration and boost level, we’ll need a way to precisely adjust that fuel mixture at various load levels. Unfortunately, unlike more modern ECUs, the MR2’s vintage computer is not easily reprogrammable. So if we ever want to get into precise fuel mixture tuning, we’ll need to install an aftermarket engine management computer.
More like this
Comments
I'm not a chemical engineer, but I do enjoy the science behind the scenes.
<< Complete burning of the fuel means less atomized liquid fuel in the combustion chamber, which means less cooling of interior combustion surfaces, which means more energy lost as heat, for example. >>
i don't follow this...
any heat not converted to pressure to push the piston down is a decrease in efficiency, yes? And any fuel not burned also decreases efficiency.
my "understanding " of rich mixtures under high load was to use the un burnt fuel as a coolant...absorbing heat...from the piston dome and exhaust valve....to prevent pre ignition and burnt valves.
Any thoughts?
and, I believe that a catalyst promotes or speeds up a chemical reaction, but is not consumed in the reaction...so oxygen would not qualify as a "catalyst", yes?
Bigben
HalfDork
6/5/24 12:40 a.m.
In reply to BimmerMaven :
Yep I agree. Oxygen is not a catalyst in the combustion process it is a reactant.
A rich mixture does lower combustion temp, partly due to the heat of vaporization of the excess fuel, but mostly because of the less hot combustion process of burning 2 HC + O2 = H2O & CO. A stoich mixture burns to CO2 which releases more heat & power.
In reply to BimmerMaven :
The rich mixture doesn't cool surfaces as much as it keeps the peak combustion temp down. Which then keeps surfaces less hot.
That being said, modern materials are almost magic- one of my last projects was to improve the CO emissions on a very boosted product. Which really means run less rich. Many modern engines can run a really long time at stoich under max boost, pushing exhaust temps past 1800F.
Displaying 1-4 of 4 commentsView all comments on the GRM forums
You'll need to log in to post.