So I've been making progress daily with my "one-hour a morning" routine (weekends being the exception). I'm absolutely thrilled to be making a go of this and have been trying my best not to make daily updates about not a whole lot of progress but I think I've got enough that I can post something. Here's how my first attempt at a "cut and patch" rust repair is going on my driver's side fender:
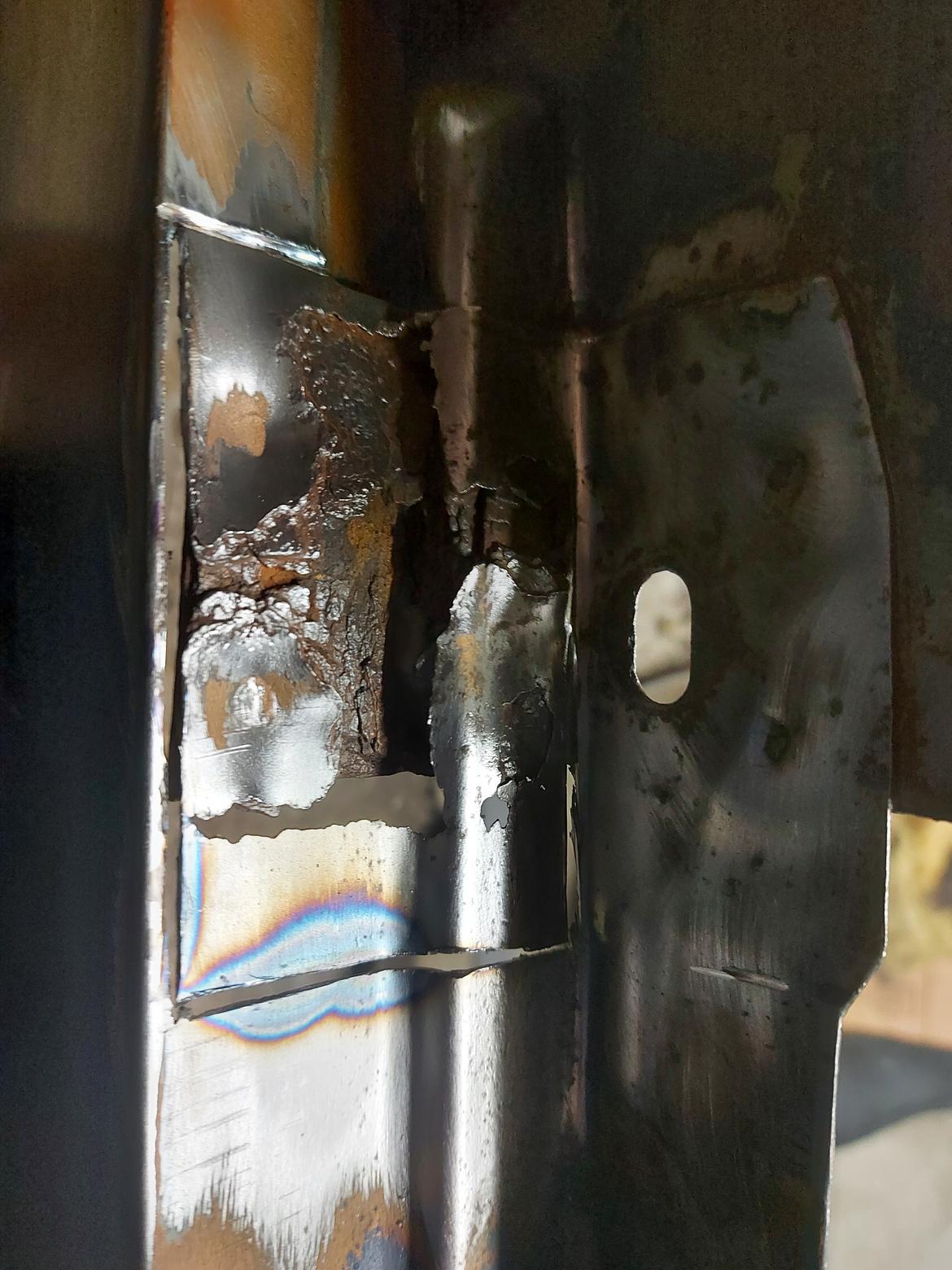
I used my "danger wheel" with the smallest possible remnants of my most used abrasive wheel to cut out as much as I could of the area. You can see that the rusty part is mostly held in by its spot welds, and I can start to see the panel underneath.
I started small with my drill sizes and worked my way up until I got to something that would do the job (I don't have a "spot weld bit" or a cutter, and with how things went so far I don't have any plans to order one unless someone suggests otherwise).
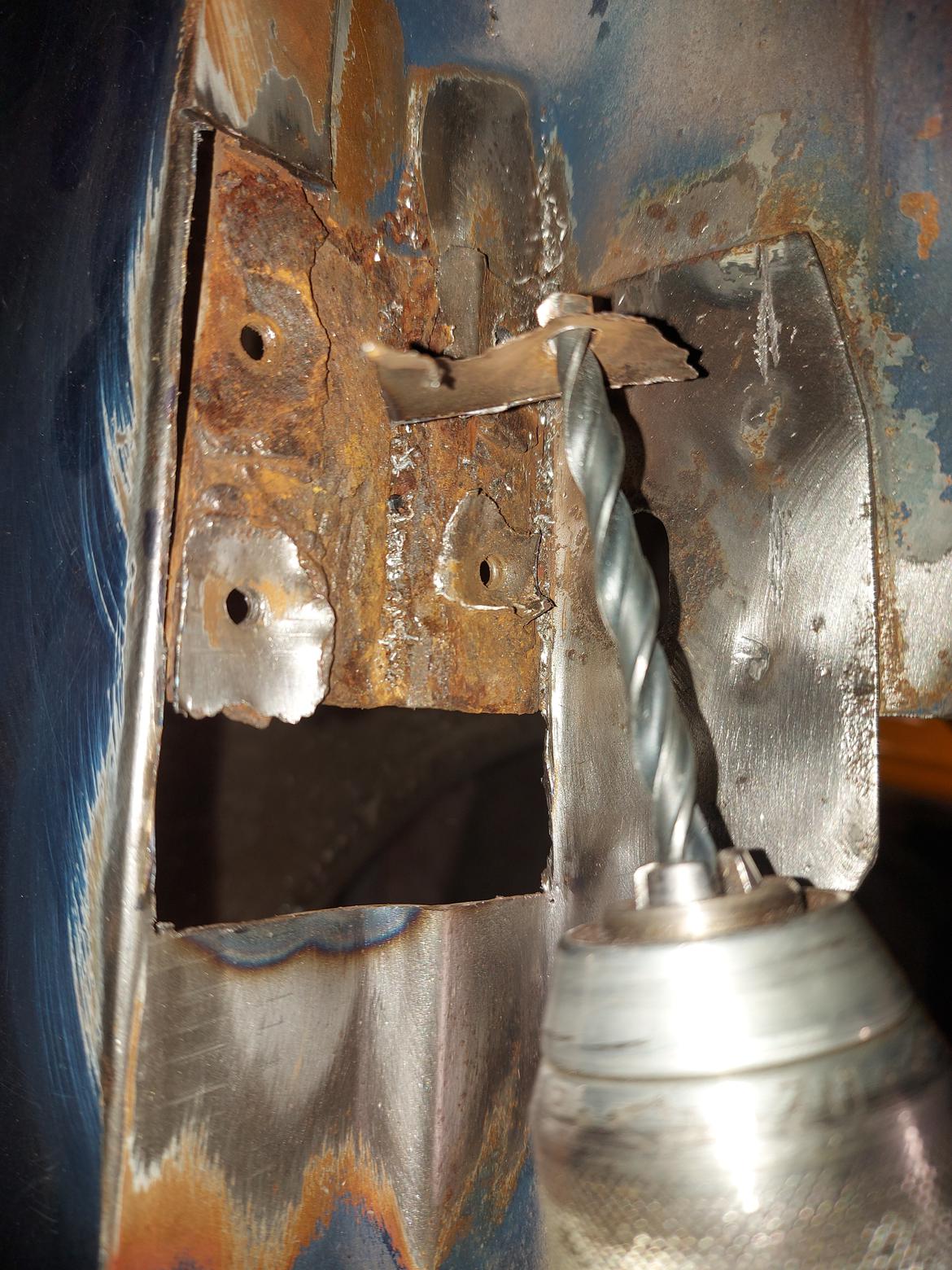
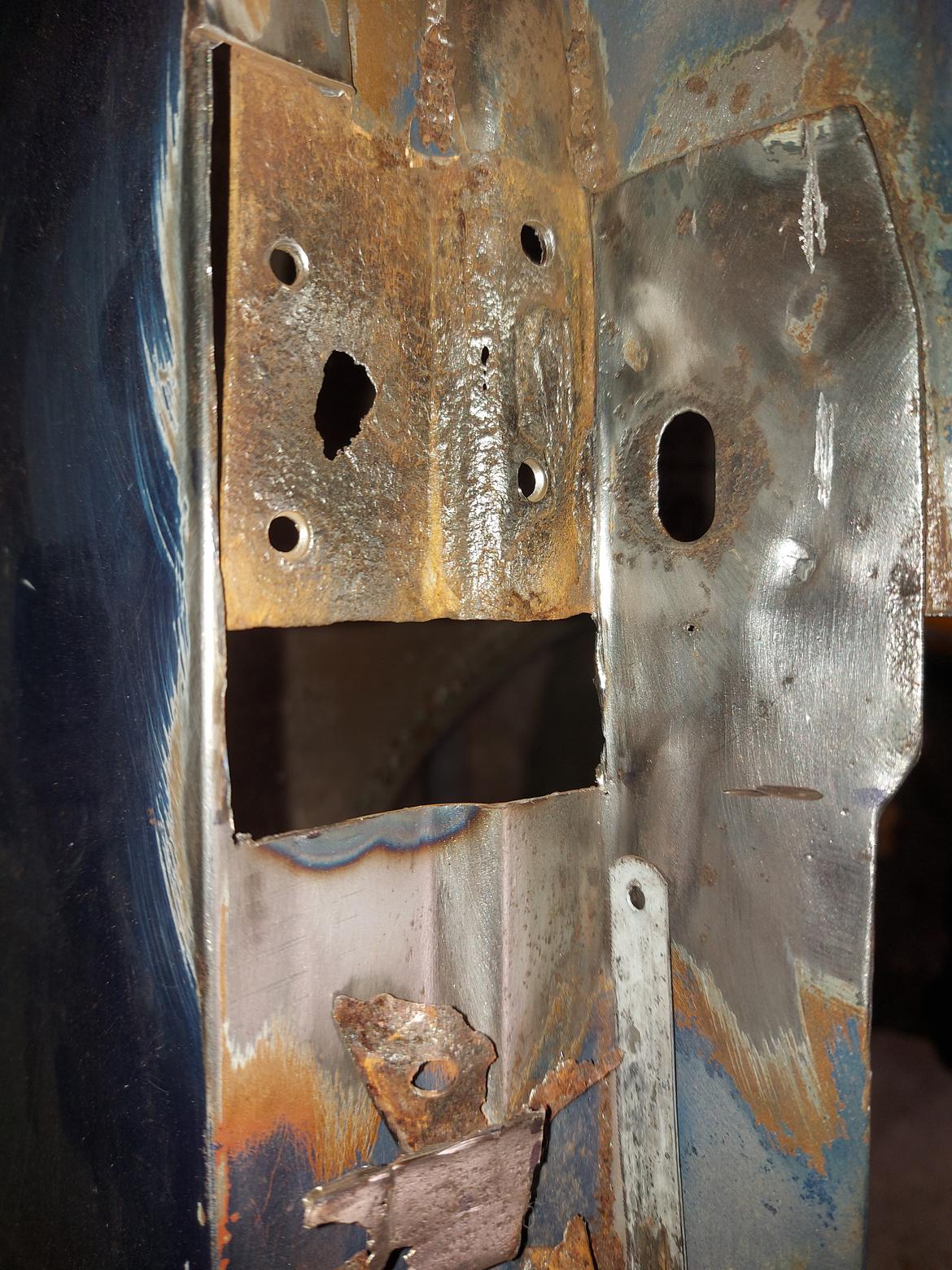
In the picture above the top layer is removed. If the two rust holes I saw through the under layer weren't enough for me to cut out what was underneath, the rust I found under the un-cut portions was (where that bolt hole meets with the fender). I tossed around a couple ideas to get at that bottom layer and drew out a few marker lines.
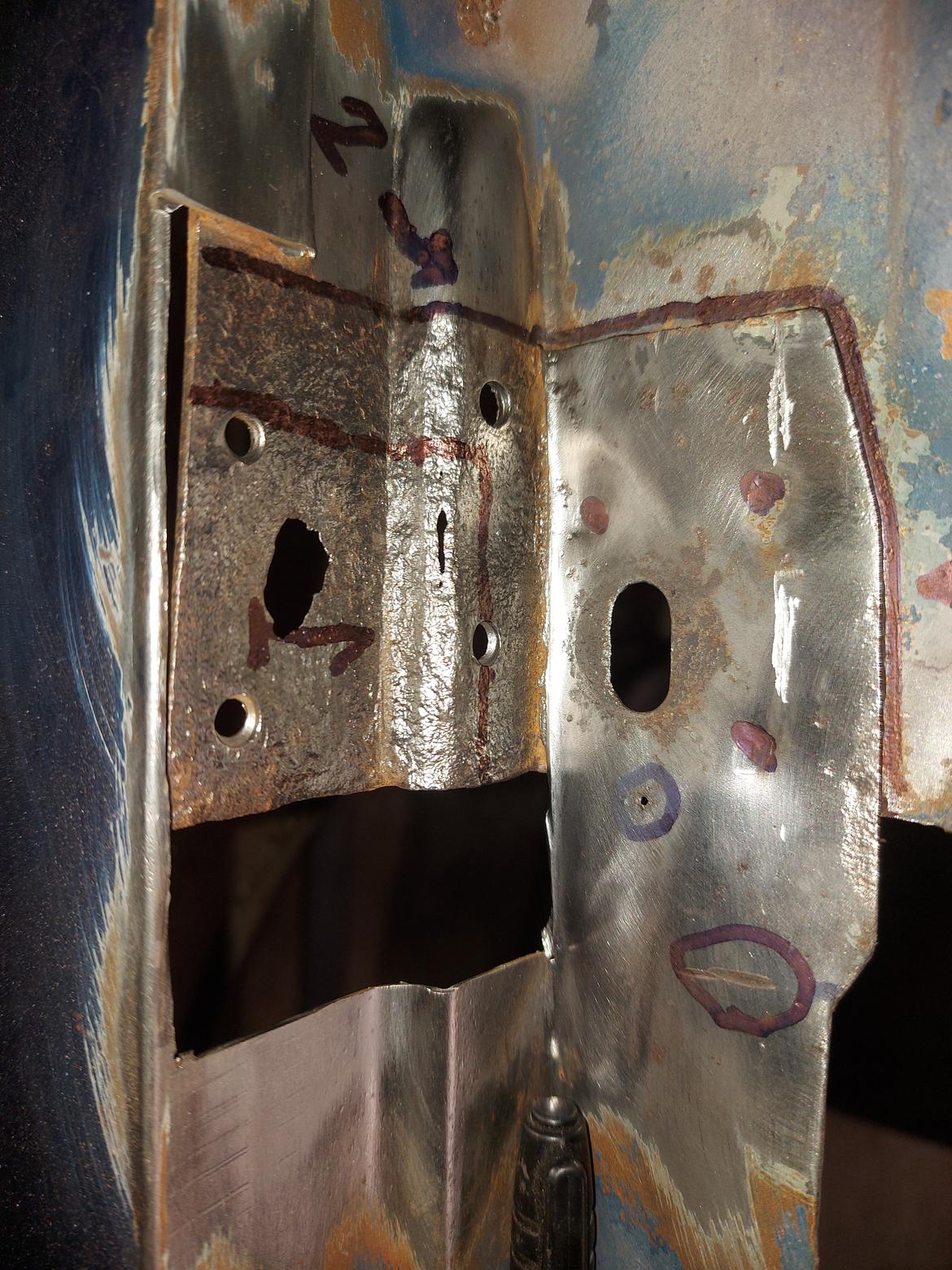
The line marked #1 was laid out and would get rid of the rust holes, but #2 also took care of the stuff underneath where the two panels met. Ultimately I decided I that I could probably pull off a #2 (poop reference intended) and went that direction
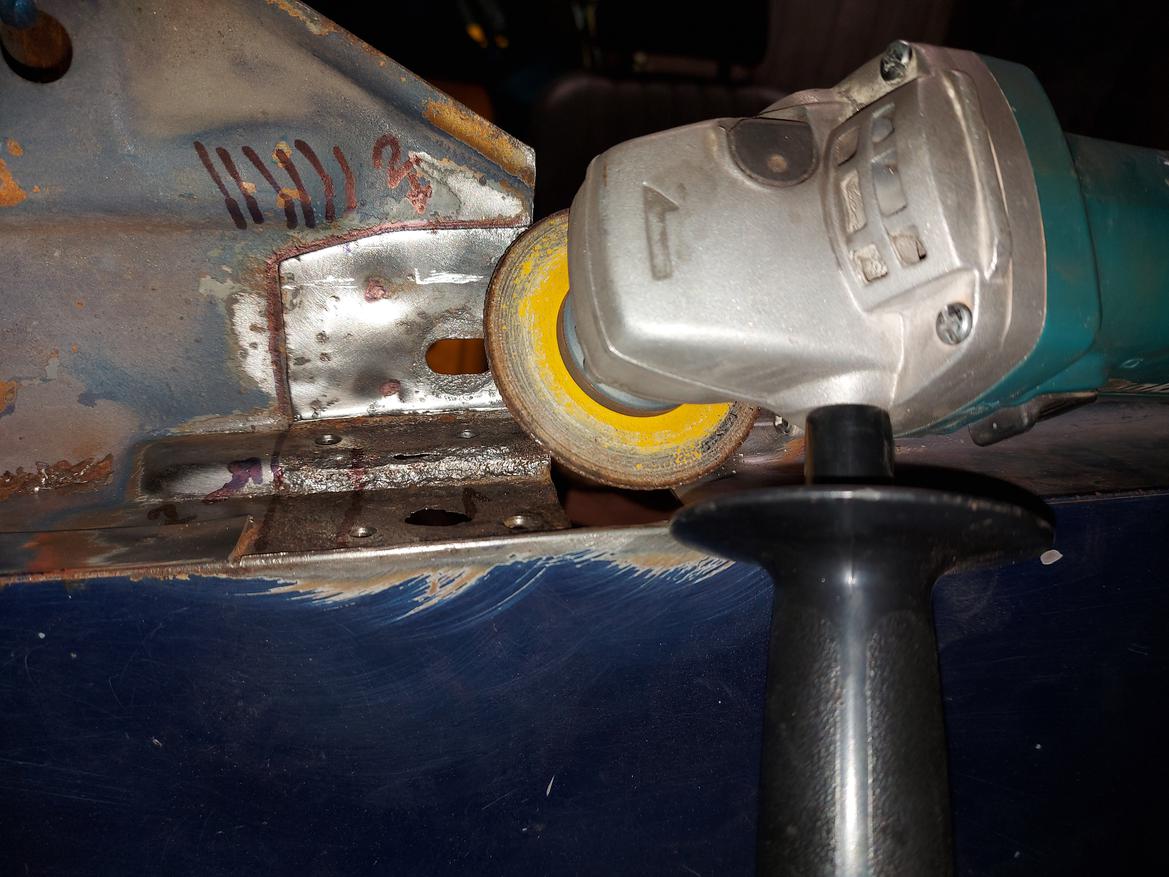
My goal was to get rid of the rust whilst avoiding that "bump" that I lined out with marker (above). I feel like I'm taking a leap here, and don't want to risk too much without a parachute. That bump looks like it'd be hard to duplicate.
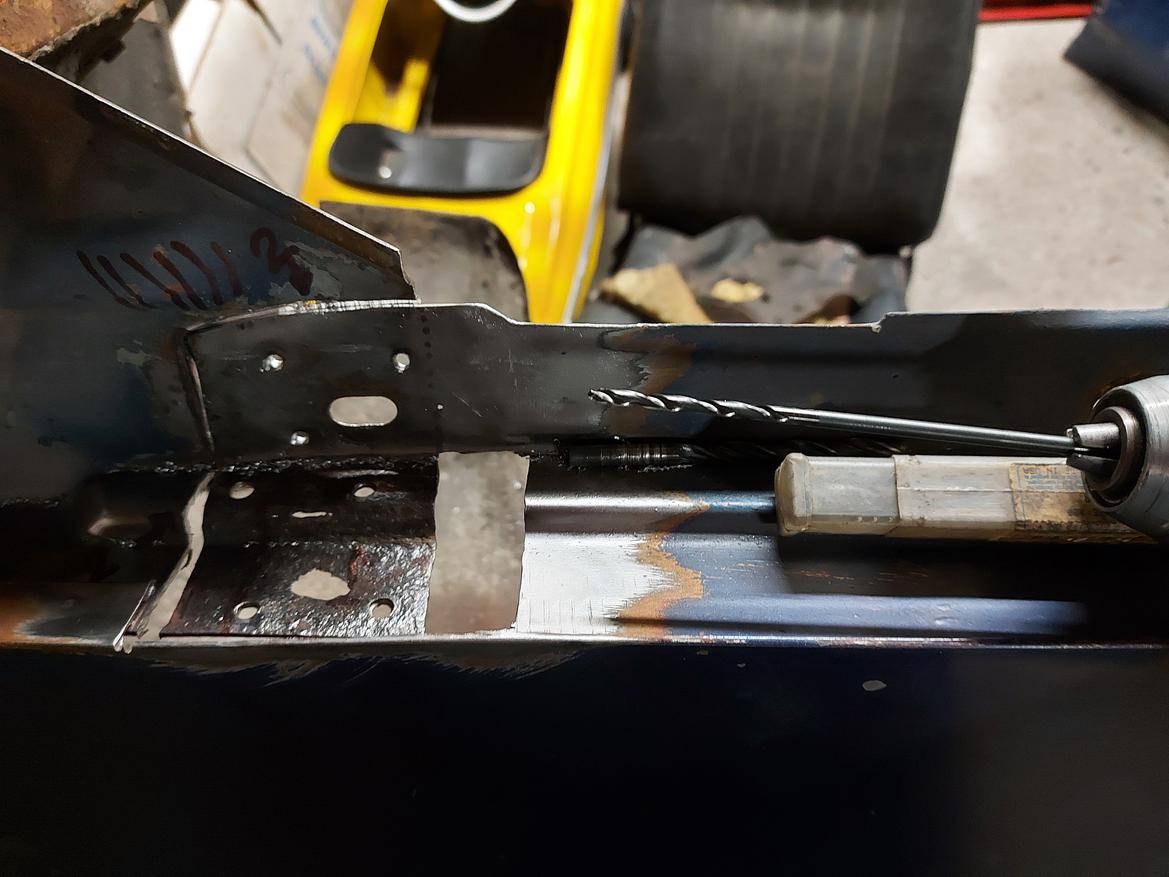
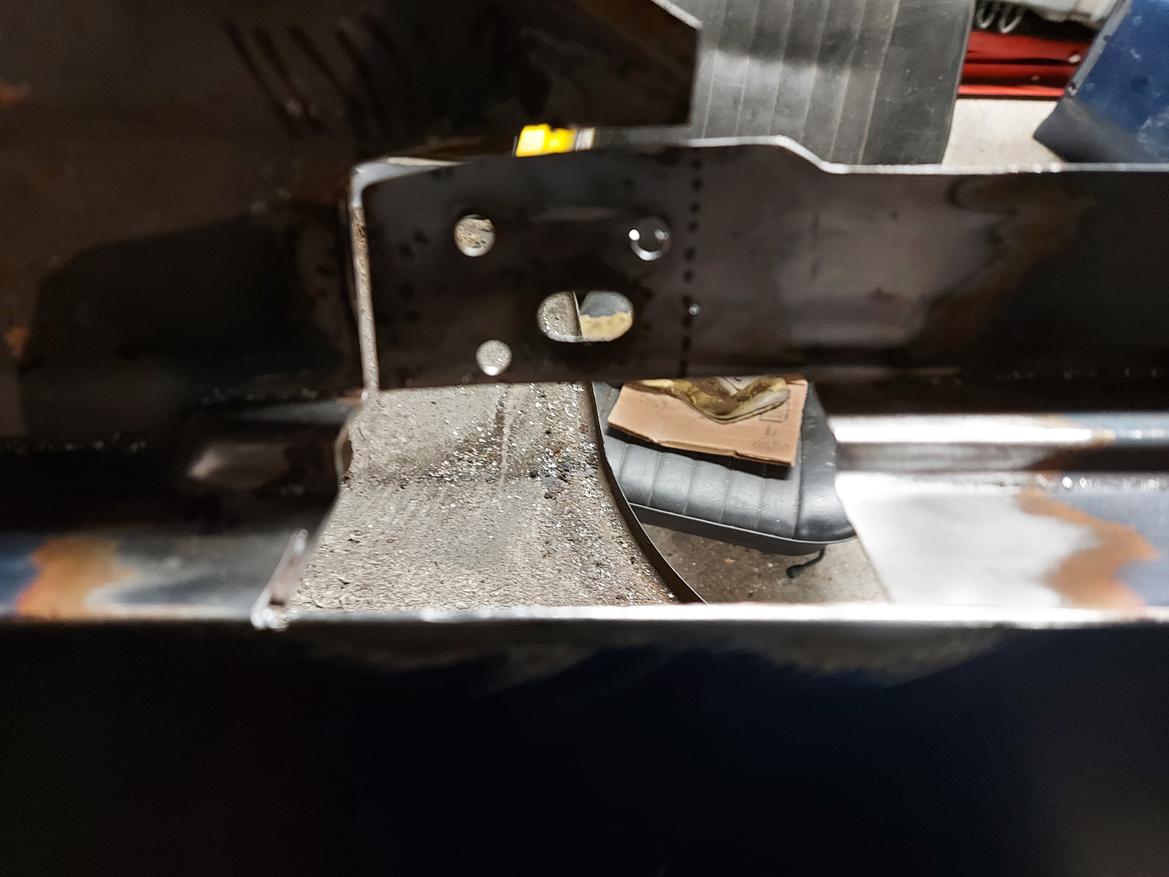
Spot welds out, and we've got the section removed! (yay).
About this time that hammer (and a few other things) I ordered back in December started to arrive.
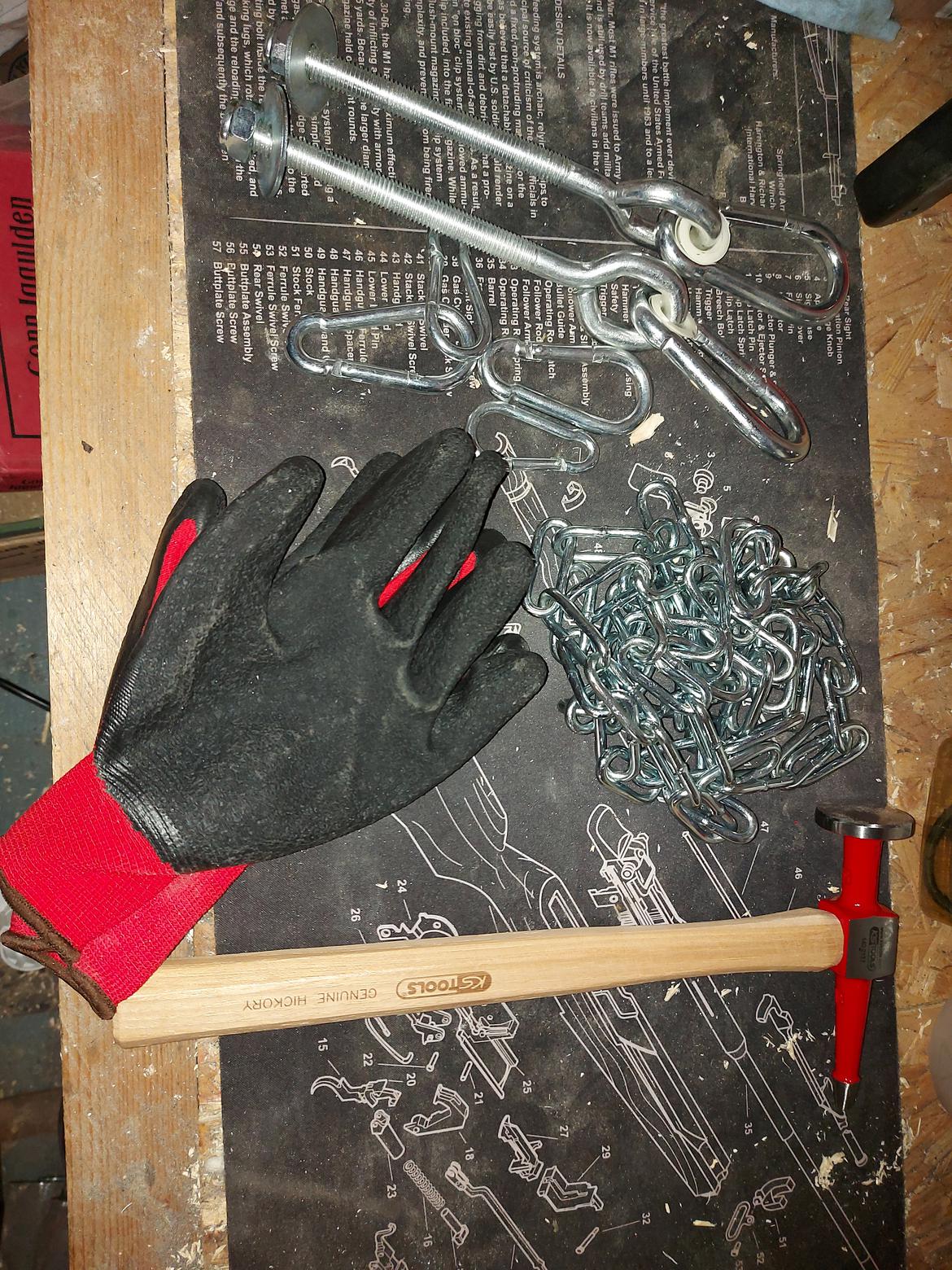
I had figured the ropes on my panel frame were going to be temporary so while I was picking up the hammer, I snagged a length of chain and some attaching hardware to upgrade things a bit.
Here's my "stage 1" upgrade to my panel frame:
(Cringe worthy "stage upgrade" reference intended)
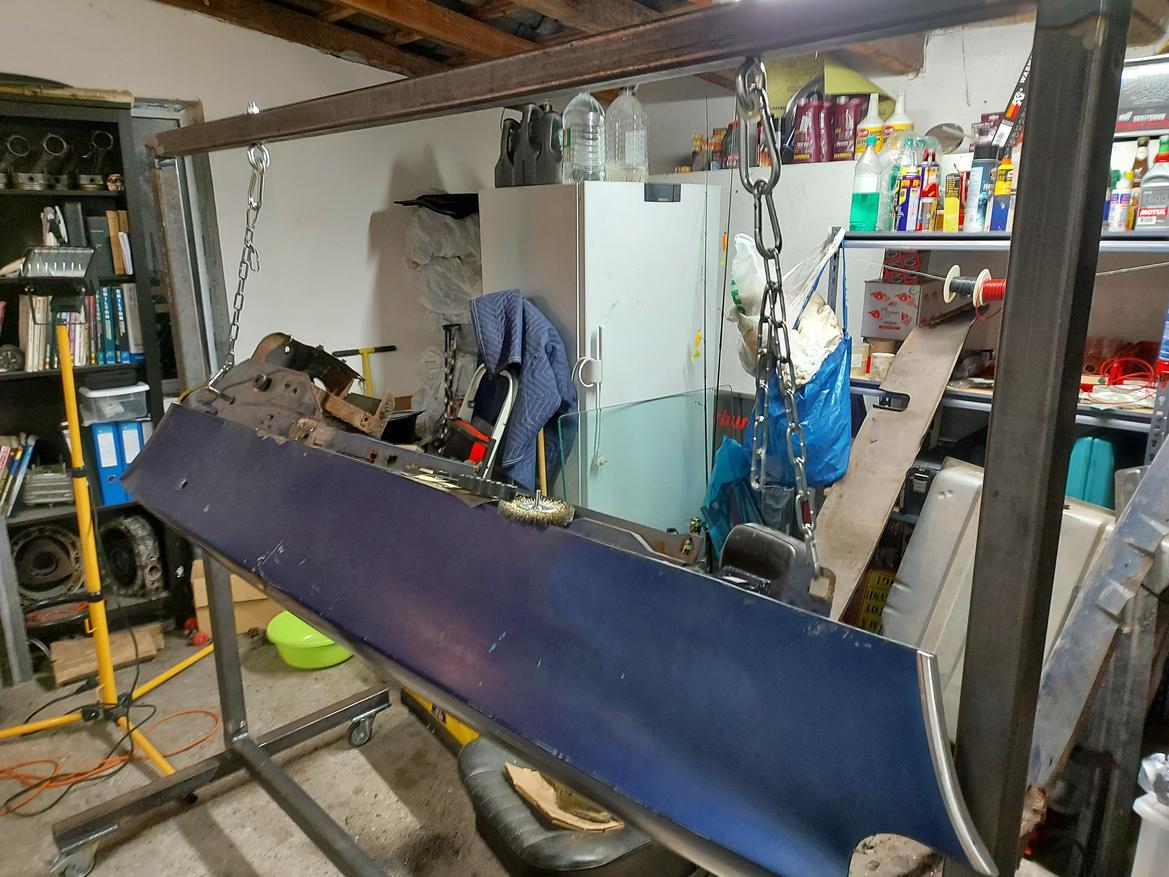
With everything cut out, I needed to find some material to make replacement bits. Unfortunately the benefit of working day-shift may be "guilt free garage time" but it also means I'm working at the office during the hours that the metal shop (singular) is open... Looking around inside the car and garage I found two bits of metal that could work as filler material:
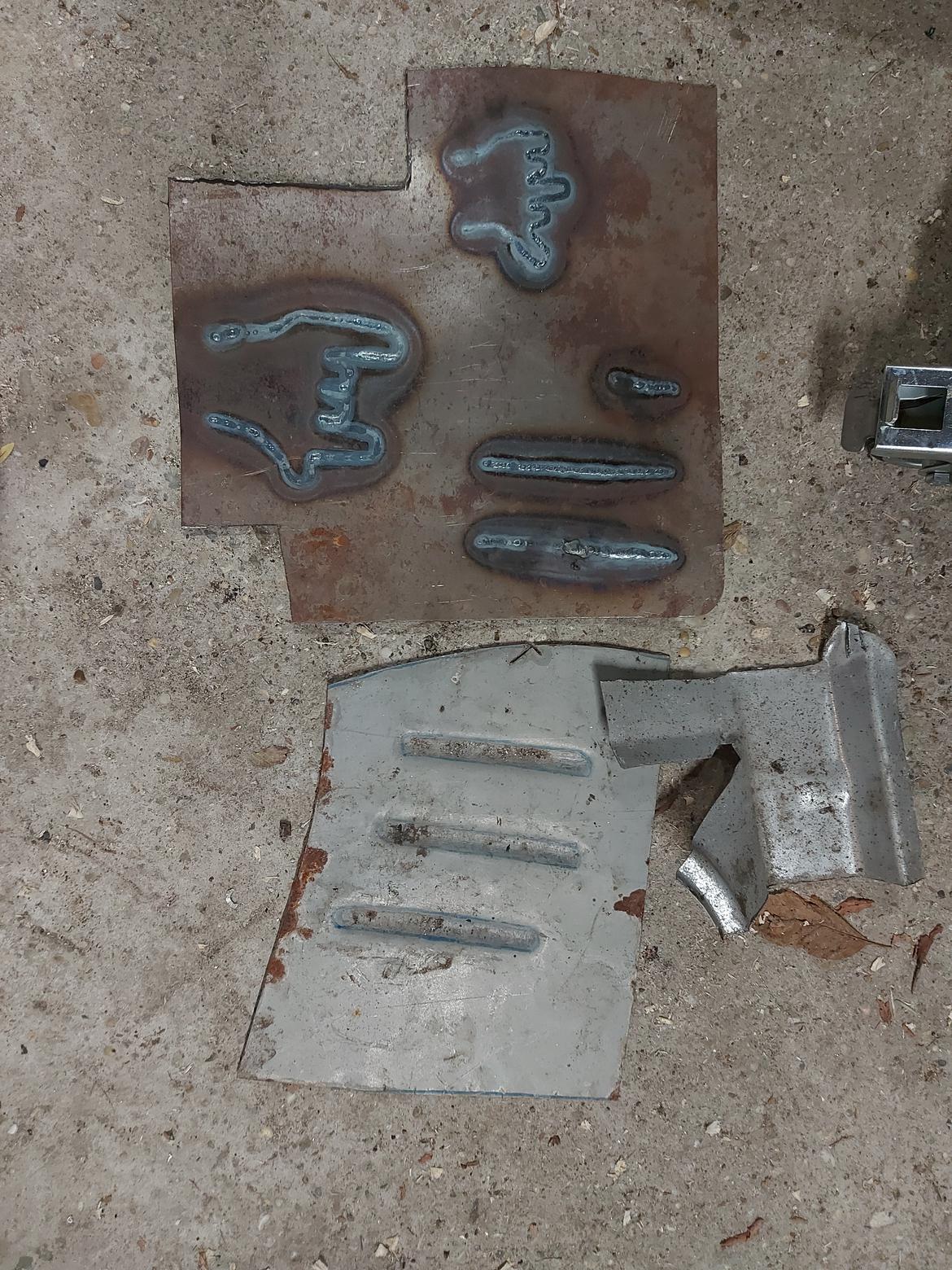
The top piece, funnily enough, was something I did very near this time of year in 2021 (so about 11 months ago?). This is when my hungover/quarantined butt got off his lazy rear and decided that 2021 was going to be the year that I laid a weld that I wasn't completely ashamed of. This random piece of flat stock had been in my inventory since Tacoma (circa 2016?) and I figured torch practice was something it was suited for. I started with the straight lines and immediately dipped my tungsten into the puddle. Things didn't get a whole lot better from there. You can kind of tell my mood at the time by what was drawn 
The bottom piece is something I found in the Charger. It looks to be intended for a floor repair but the way the dimples are hammered really has me bothered. I don't know whether I can do a better dimple job or not yet so I decide to play it safe and cut up the weld practice piece.
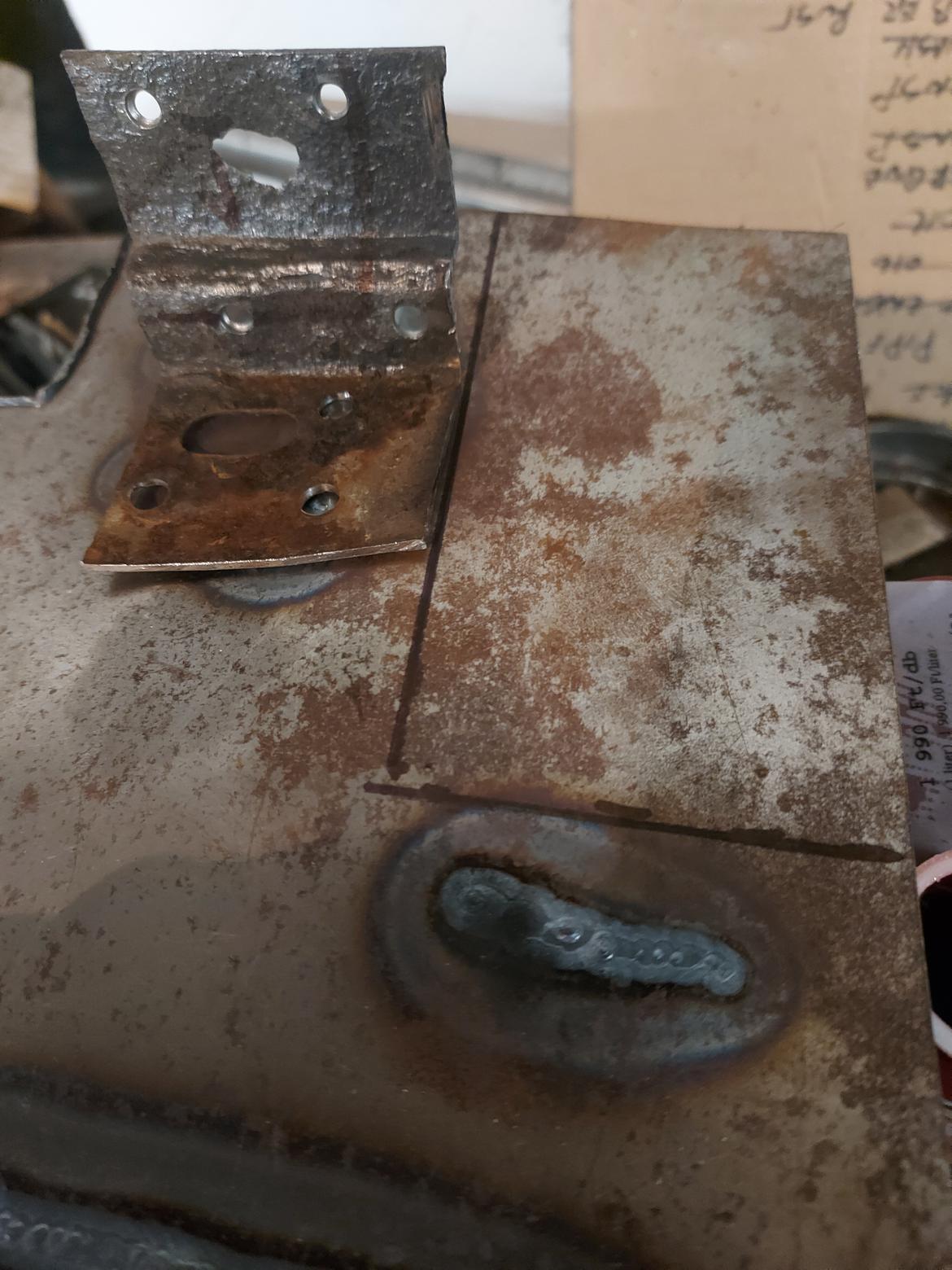
Also, in the spirit of "playing it safe", I gave myself plenty of material on all sides of the cut so I could mess up multiple times if needed 
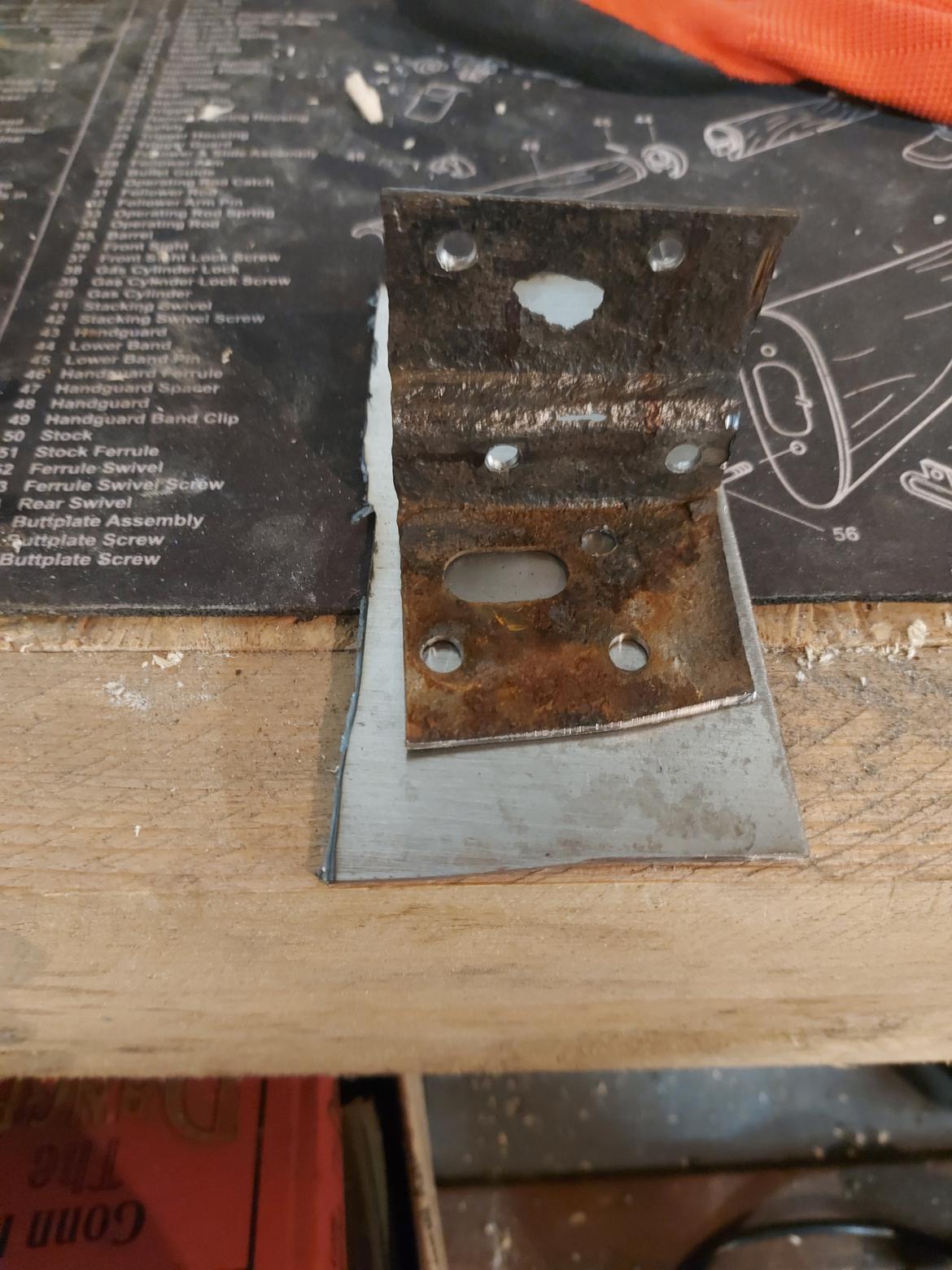
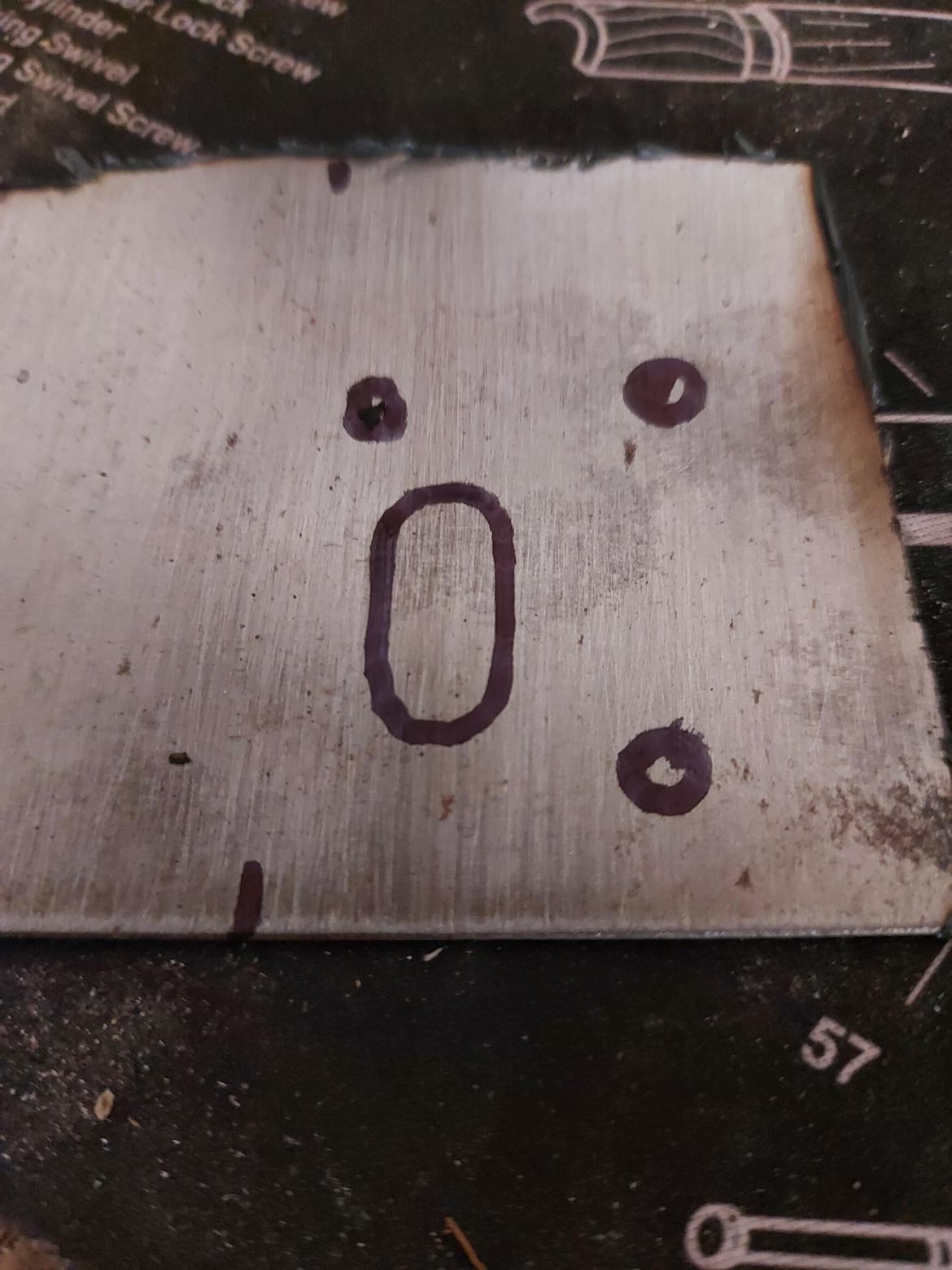
I don't own a finger brake, and bench-vice bends have never worked for me but I have an idea involving angle stock, flat bar stock, and lots of those clamps I bought back in December:
90-degree bend, here goes:
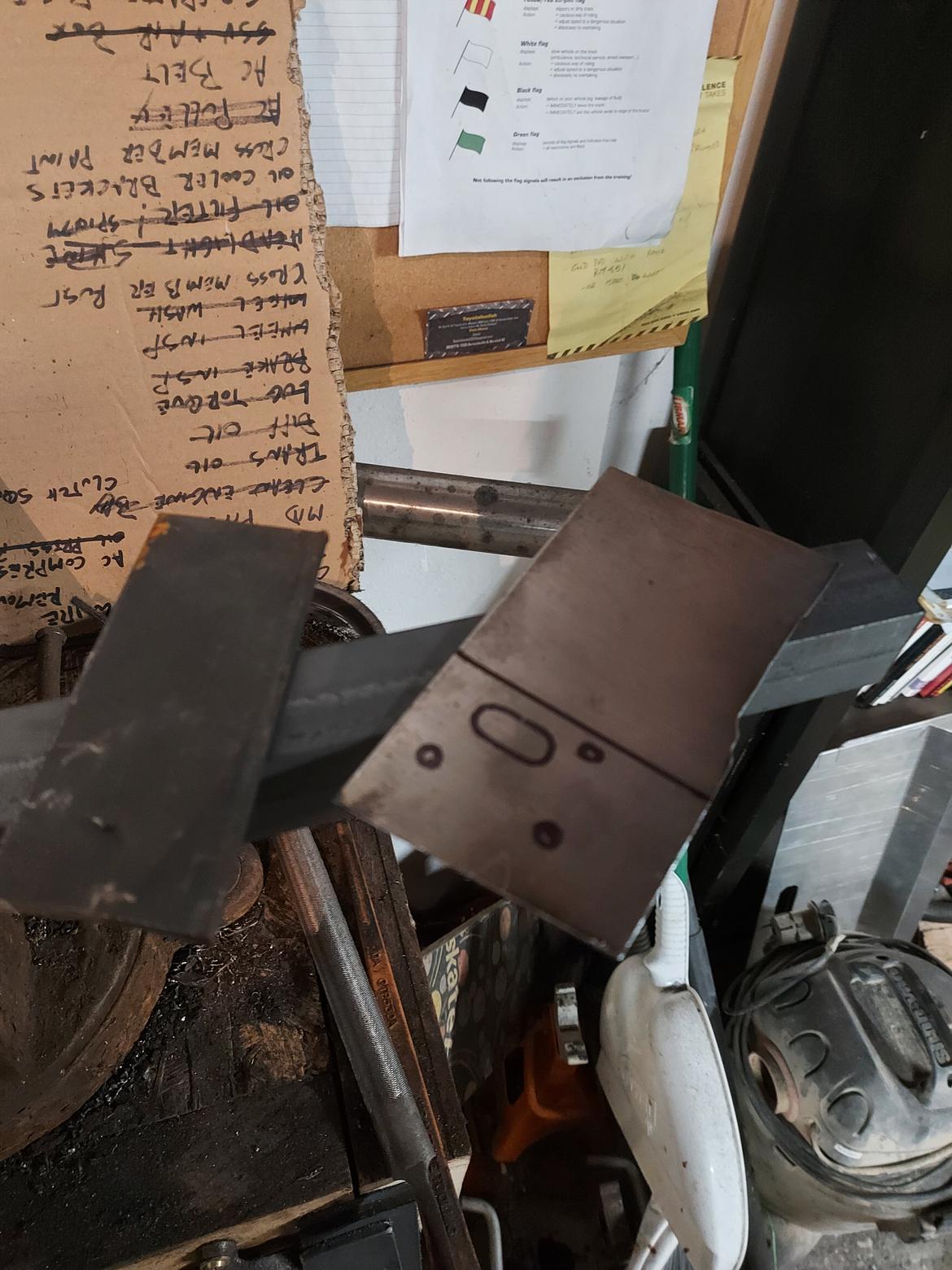
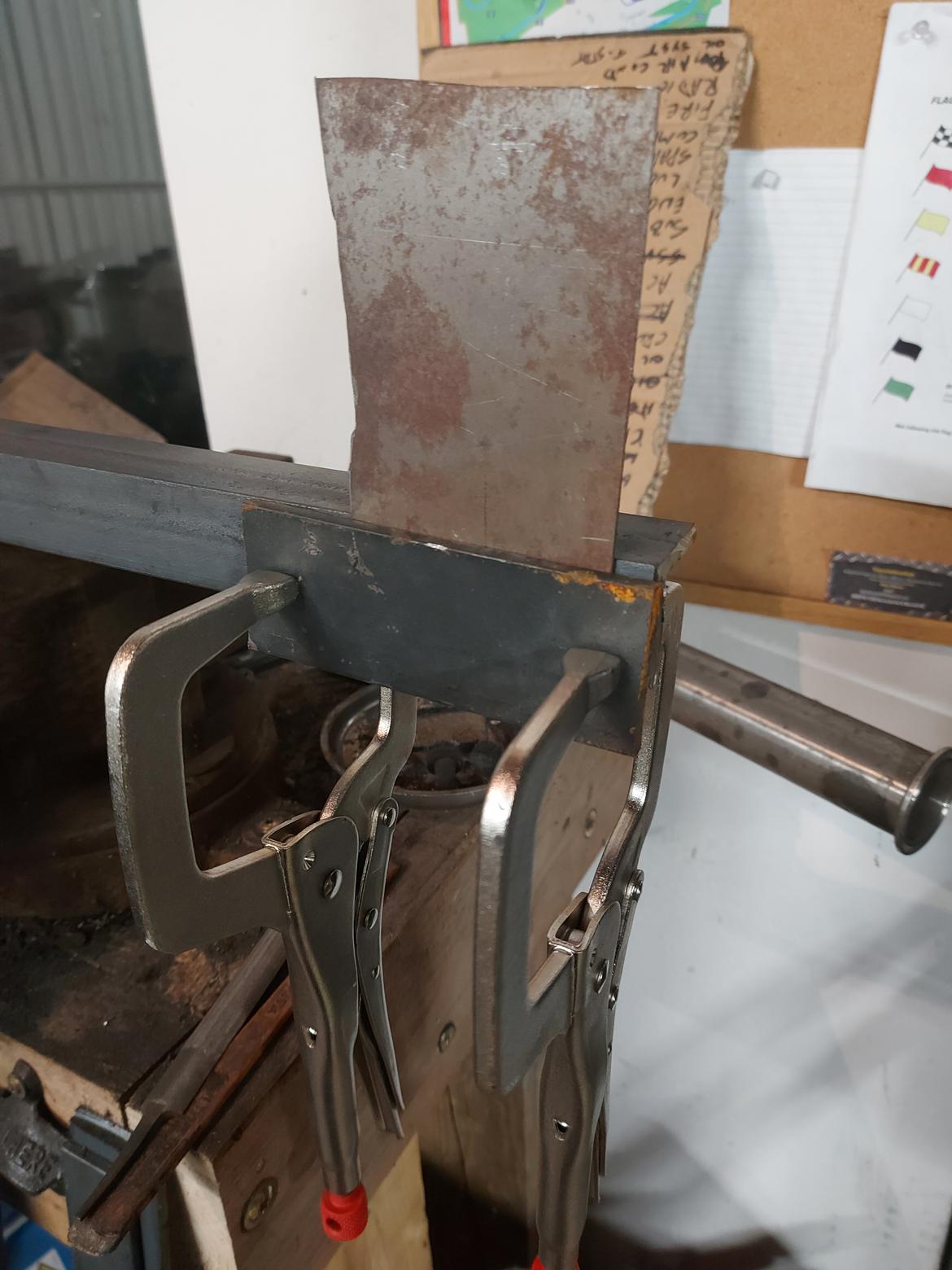
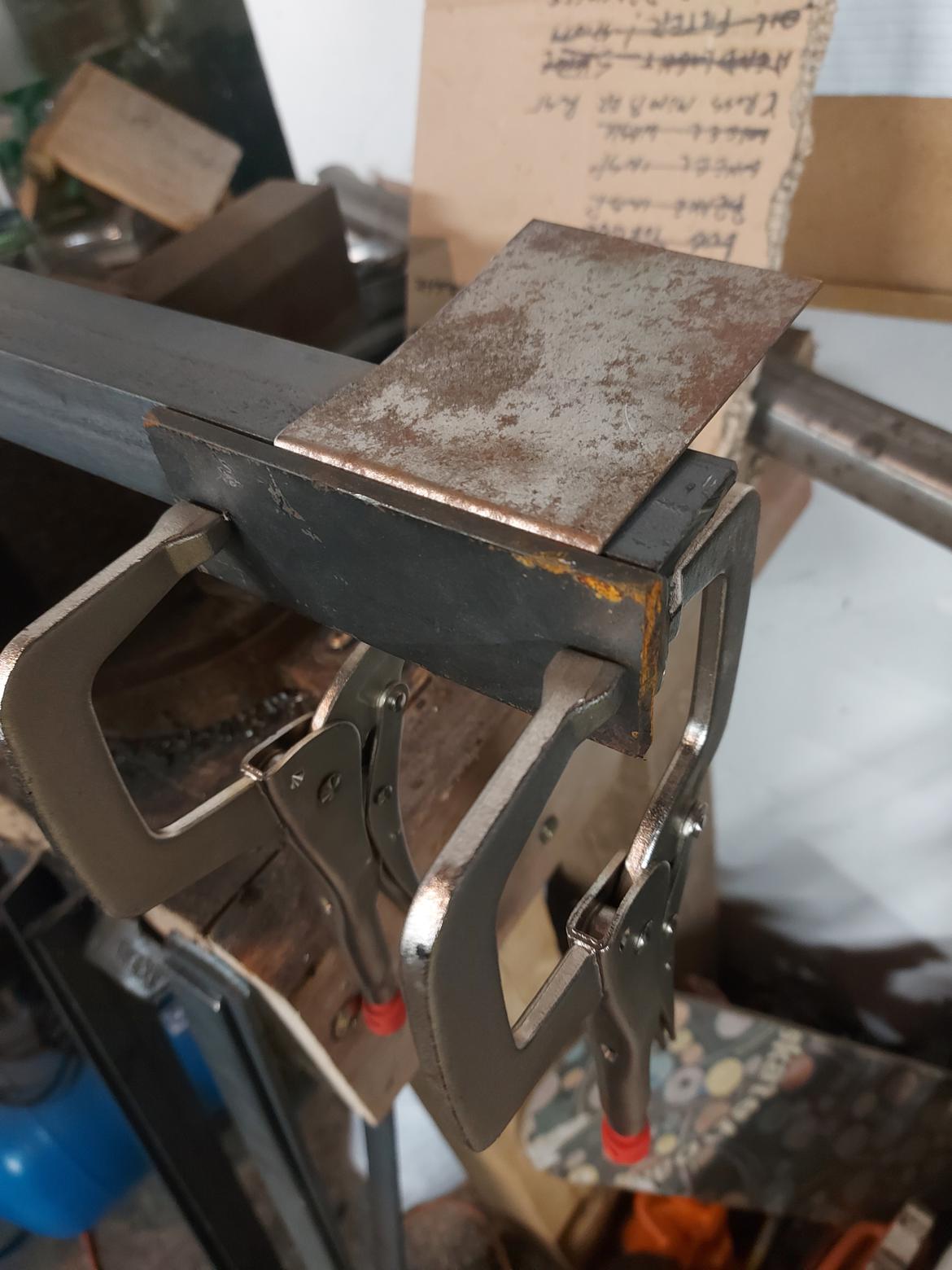
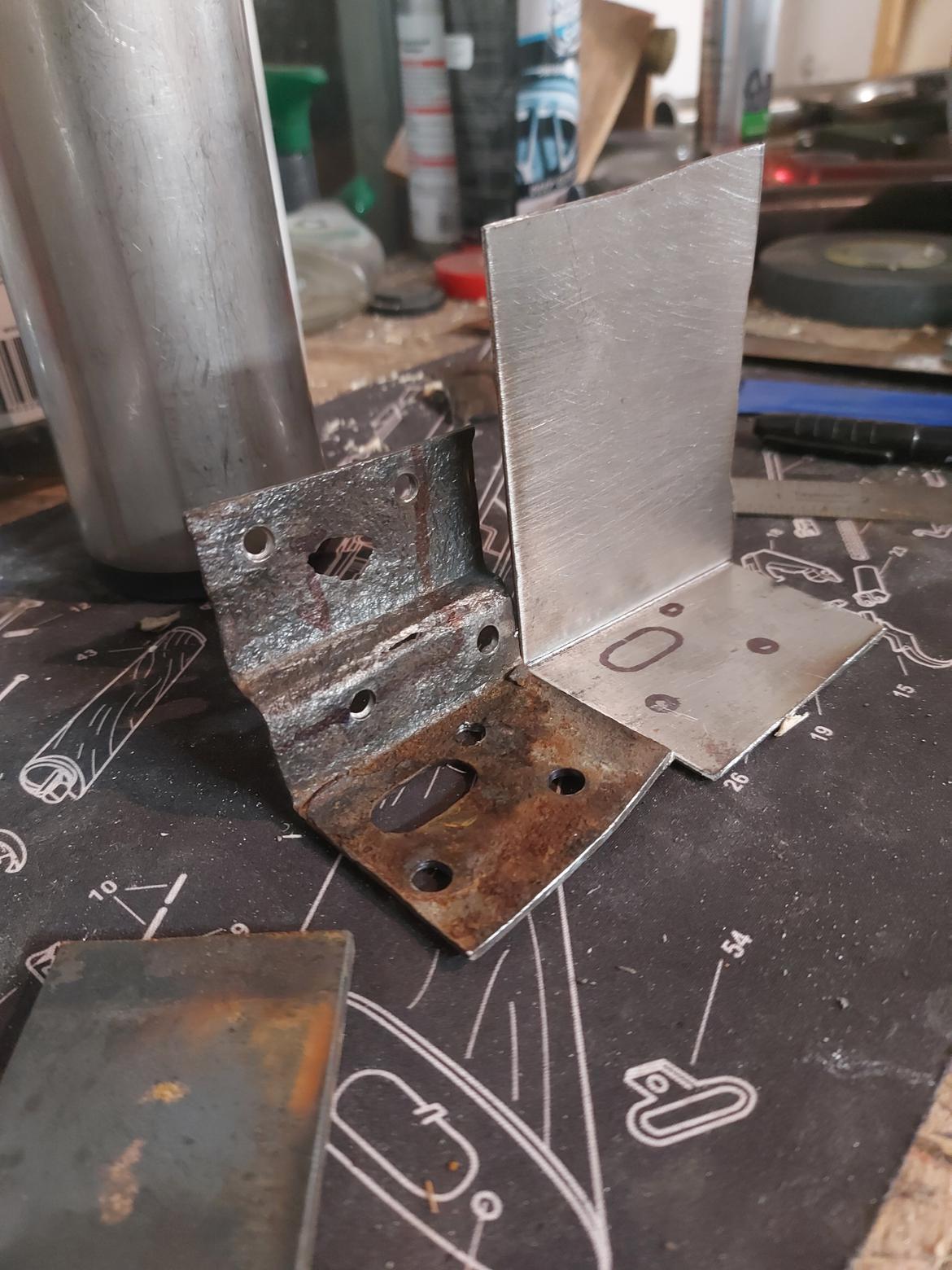
This had me unbelievably stoked
What you're seeing in the above is the final results of a Monday through Friday morning effort. The cleaning and cutting of the fender alone took me two days. Getting the metal cut out of the donor stock, and cutting the angle and bar stock was another day. I didn't get that bend made until mid-session Friday.
With the success of my 90-degree bend, I started some head scratching to finish the session. This mid-section joggle of this fender is going to be a bit difficult and I'm not quite sure how I'm going to do it yet. I toss around a few ideas but ultimately end Friday with the below being the best I could come up with:
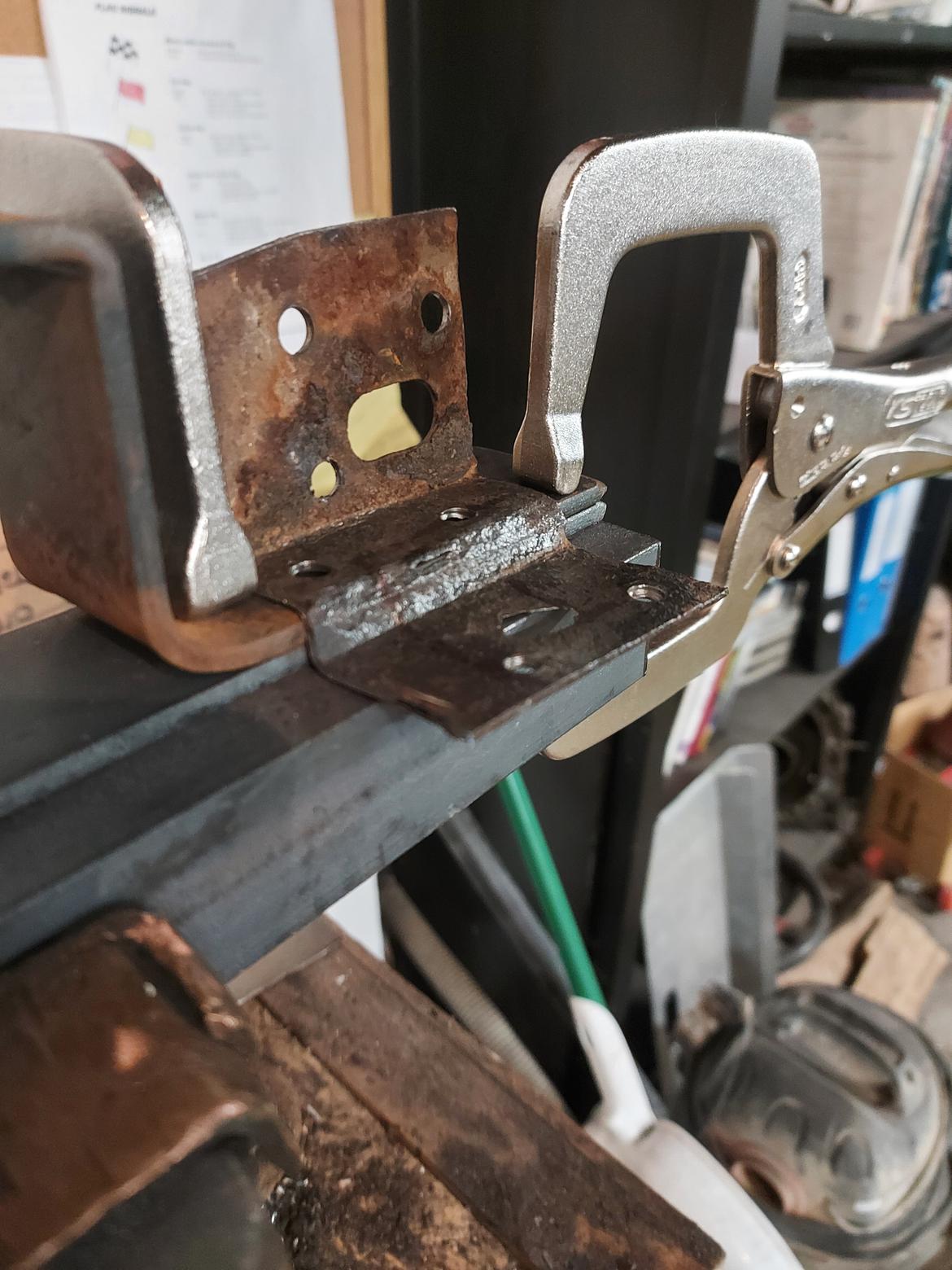
I figure if I can mount my donor stock in that sort of contraption, maybe I can use a chisel (or similar) to get that bend punched in there...
By Monday, I'm not so sure so I scrap the idea in favor of something a bit more simple. First I use square stock to allow my clamps to bite, and hammer out a rough 90:

Then I use multiple clamps to bite half-way on to that bend, to wack out the rest of the joggle with that rubber mallet. The bends aren't "sharp 90's" so I need a little "roundness" in them to look like the original.
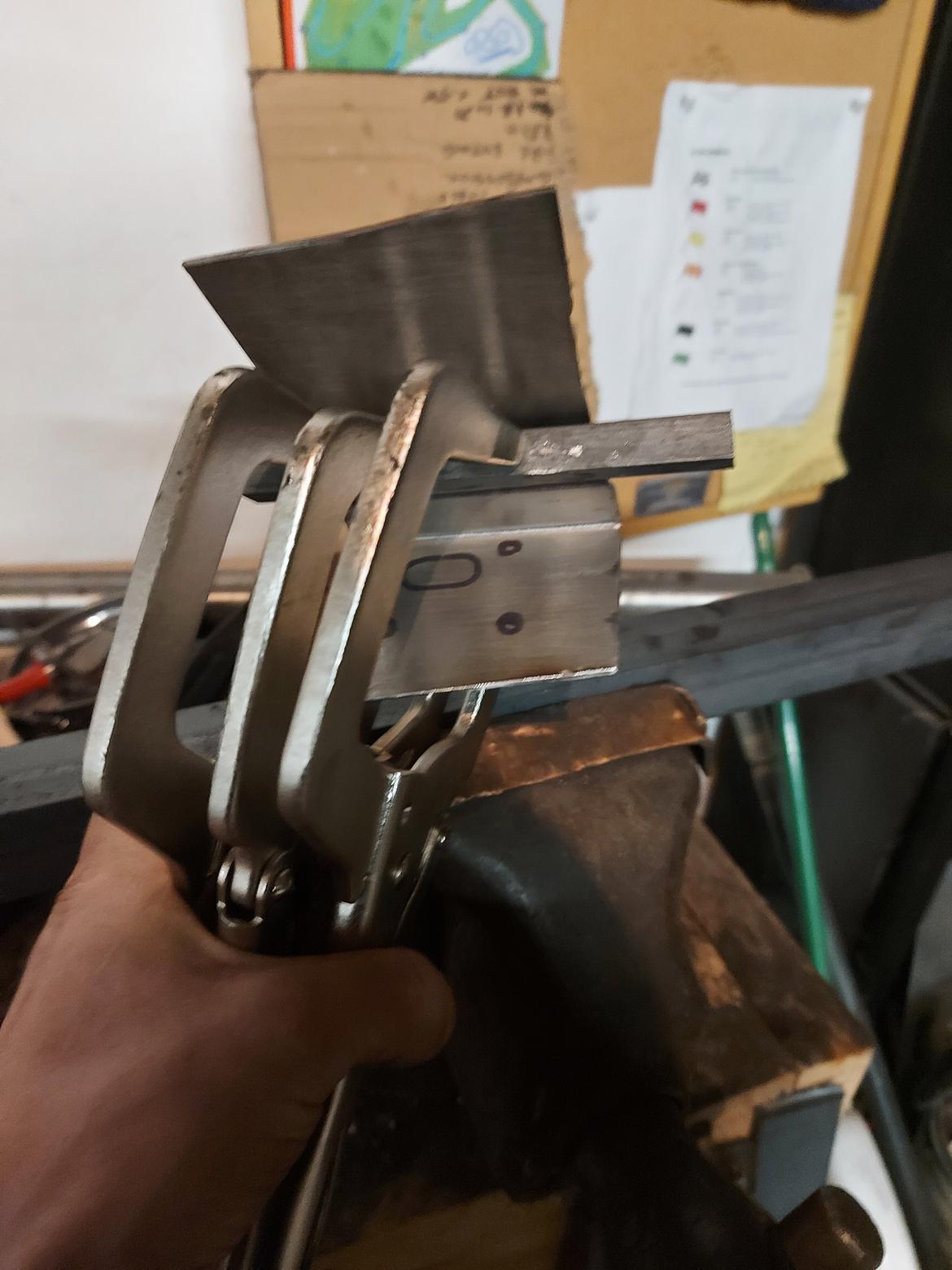
What comes out of my efforts looks like this:
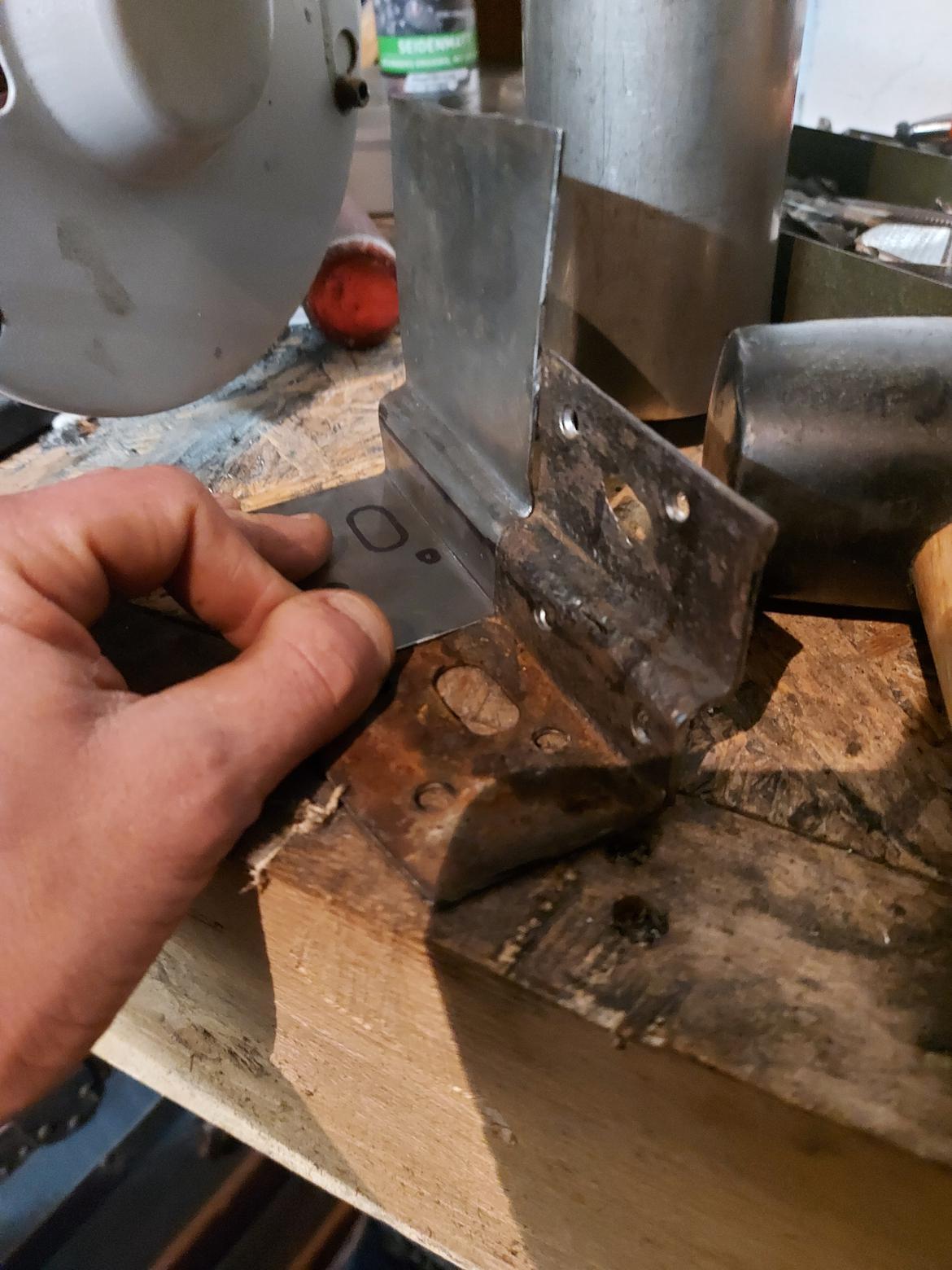
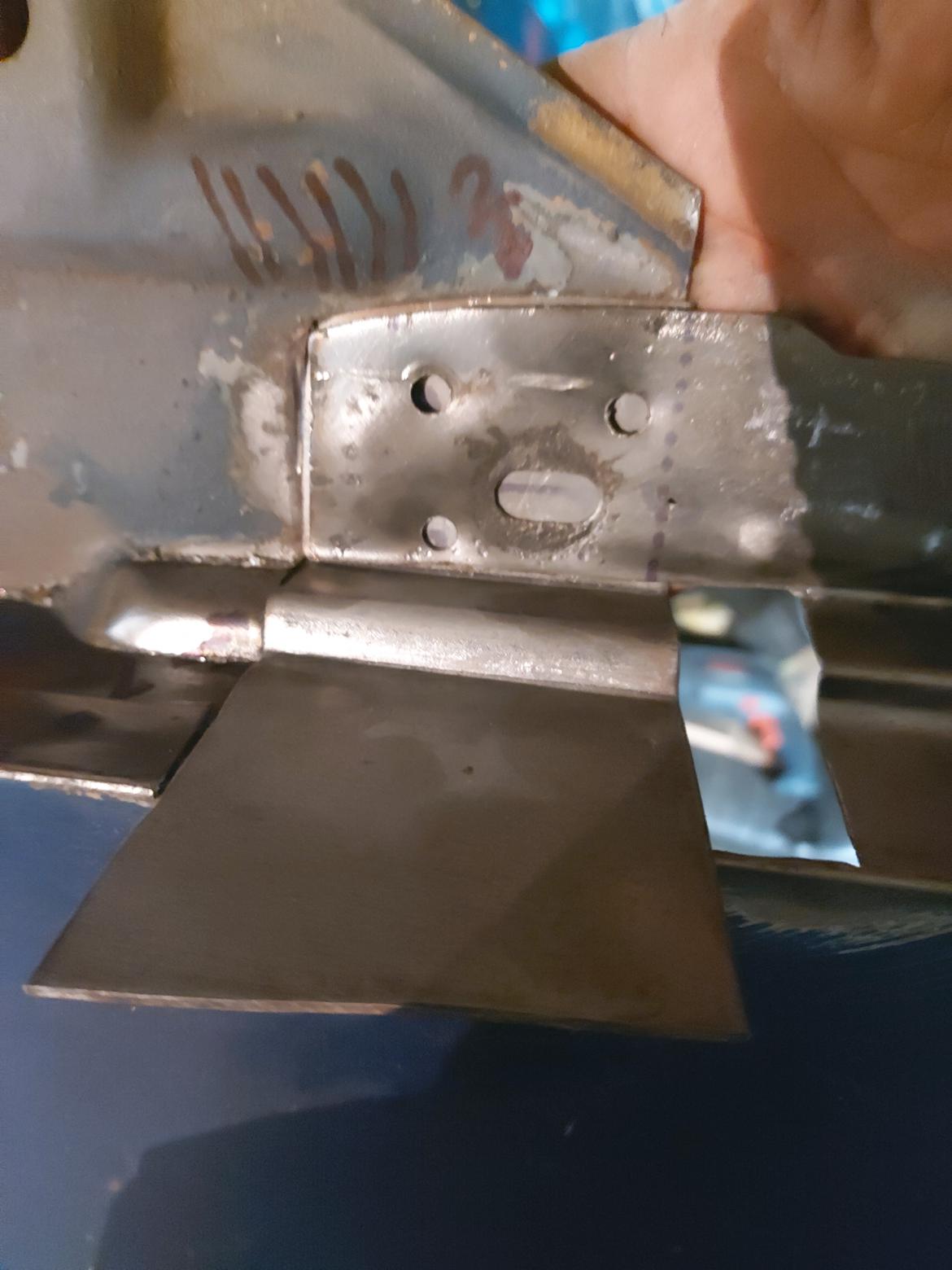
(Told you I left a lot of material on there for "goof up" room)
After that it was a lot (and I mean a LOT) of "back and forth" with the bench grinder to get things inside their footprint
Eventually we get to something that looks like this:
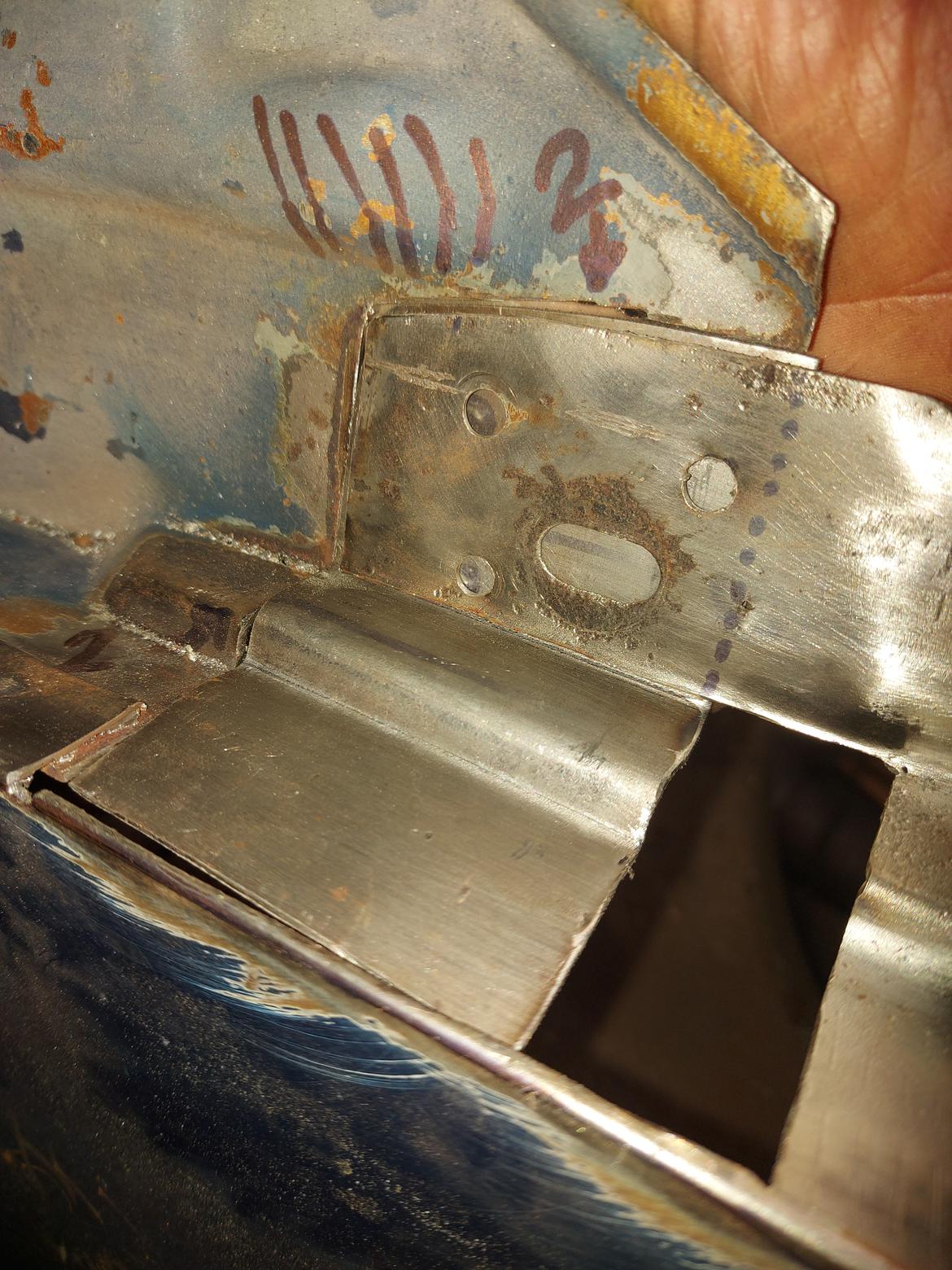

Old VS new there at the end. The bends aren't perfect, but hey! What do you expect when you're dealing with an idiot swinging a hammer? 
Next up is to hog out that mounting hole, and weld it into place! After that, I'll work on the top skin, slap some primer on it, and call it macaroni. Honestly though, this is a TON of fun, and I find myself completely consumed by it. It turns out that this is the exact creative outlet my darn brain needs and I find myself not only looking forward to my morning sessions every day, but unable to think about anything else afterwards. I REALLY hope the welding goes well and that this turns out as good as I hope it will.
100% good times.