AS if I needed it, a huge oak tree decided to invade the shop from above. It caved in the roof but the car lift stopped it from taking out the walls, cars, tools or anything inside other than the lights. It acted like a roll bar for the building. No damage to the lift as it's big time steel.
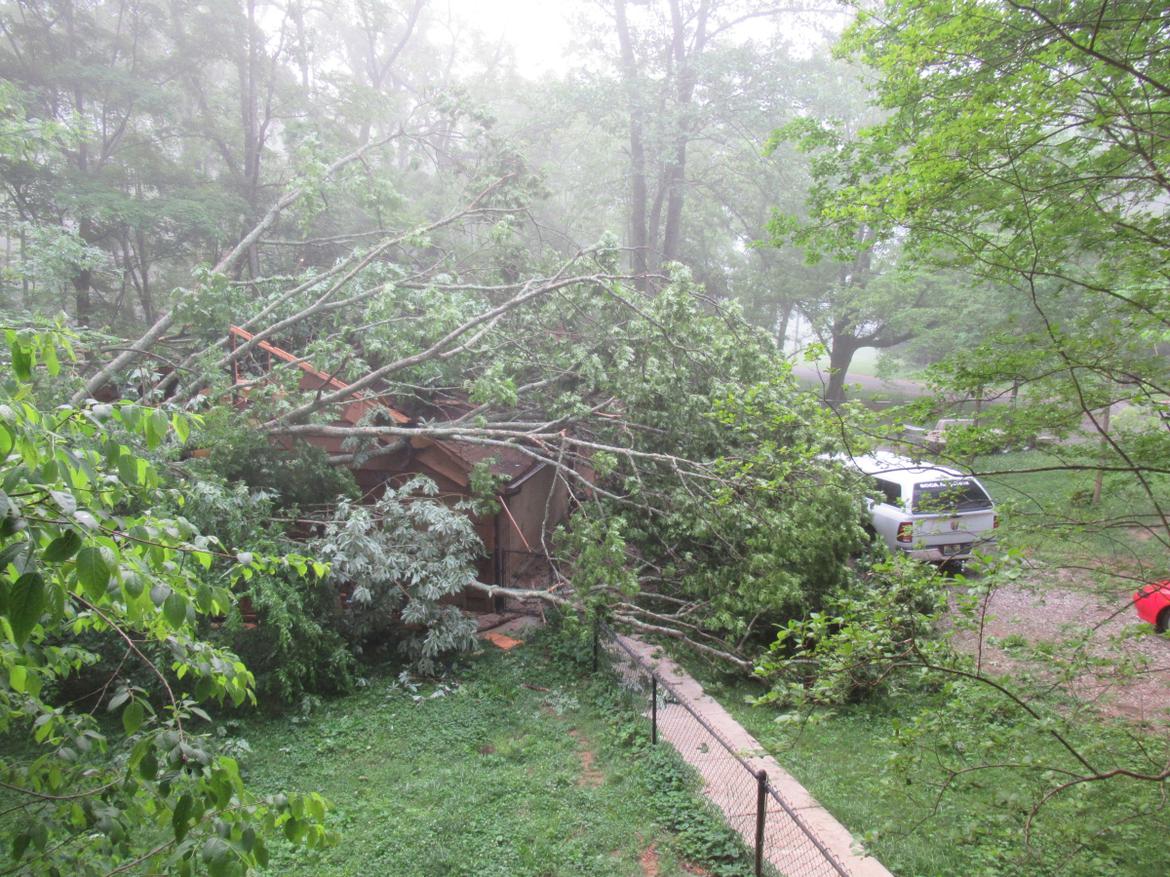
Insurance has been here. Between the tree guy and the Dudley Brothers construction, it should all be repaired and done in about a week. Meanwhile parts can be ordered and I can still do work mostly. Power is working.
man, bummer. A 80foot oak took out my backyard porch/deck and somehow didn't destroy my trailer parked next to it, so I feel your pain! Of course, thanks to insurance I ended up with a way better deck in the end. So, hopefully you'll end up with an even better shop!
RallyCaddy? Alabama? Is this Leon?
In reply to EvanB :
Yes it is.
The progress continues despite the interference.
The engine cradle has been powder coated and is installed (temporarily). First, it came with these channel brackets (on the right of the pic) that bolt where the original mounts were and they did not seem to spread the load out well. This is where having a Dynatorch CNC plasma come in handy (Shameless Plug). In just 2 minutes I had 3 new plates all within a couple thousanths.
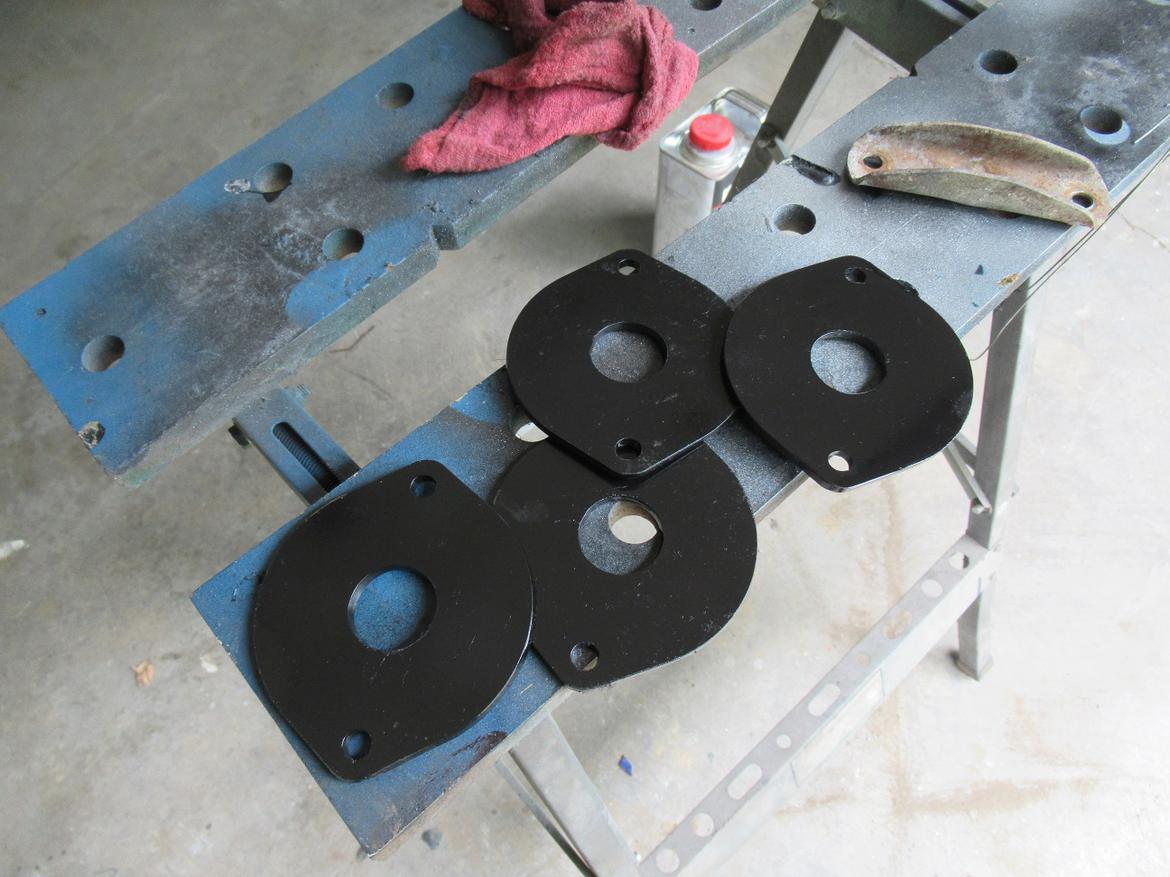
I used some universal motor mounts.
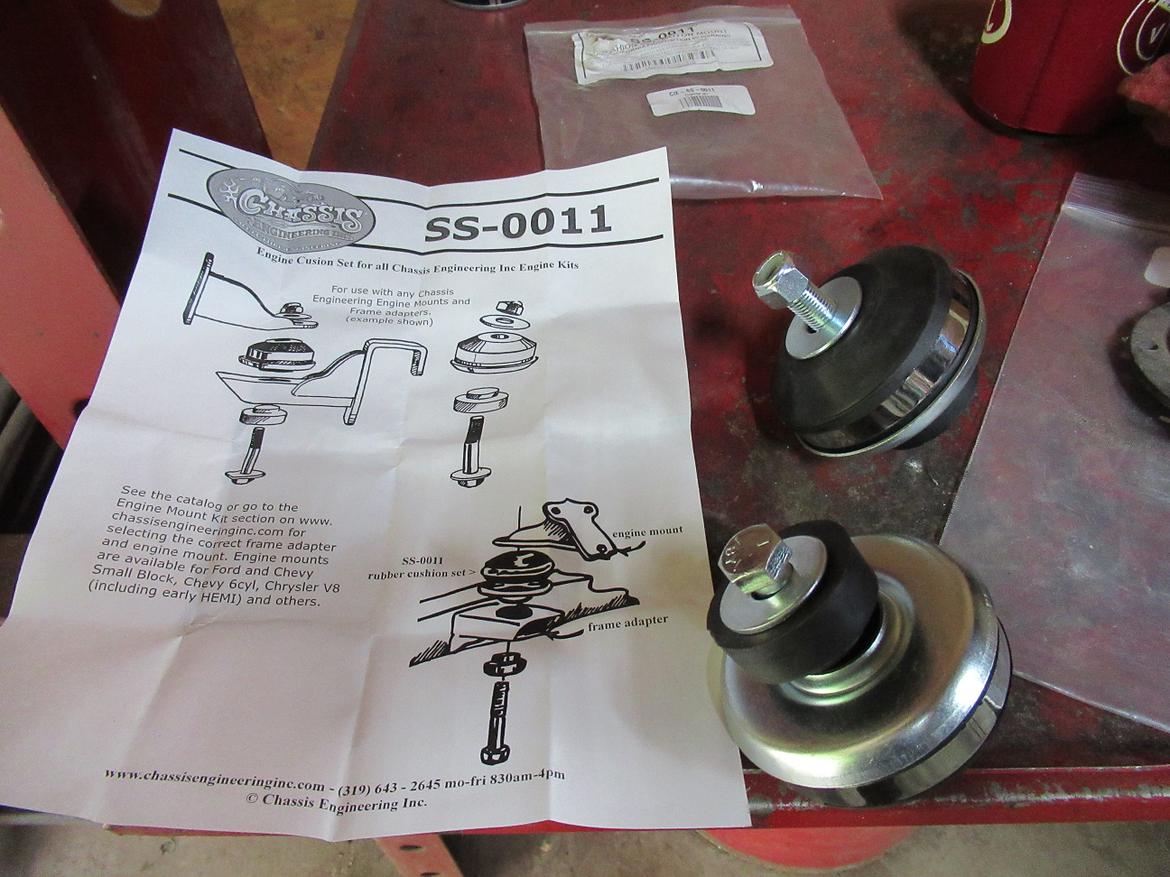
In short order the cradle was fitted.
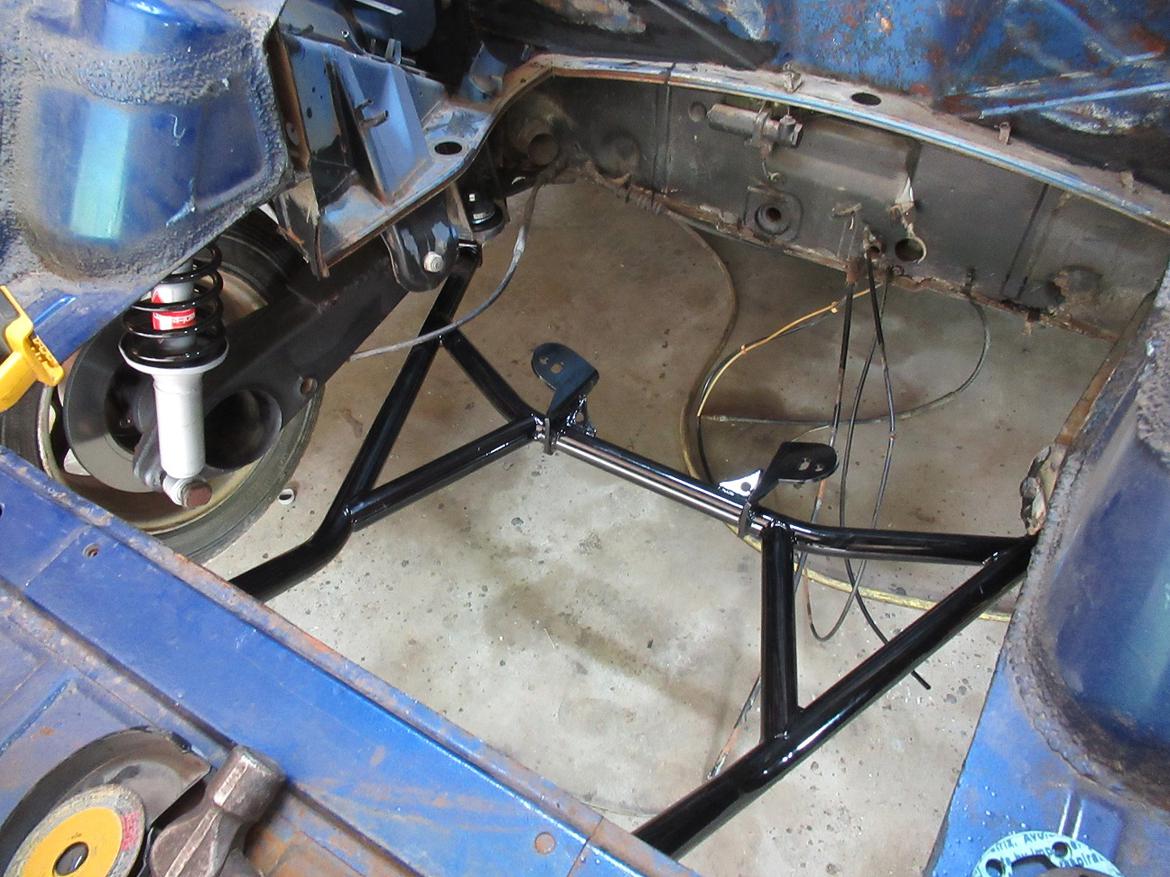
Here's a look at one of the mounts installed.
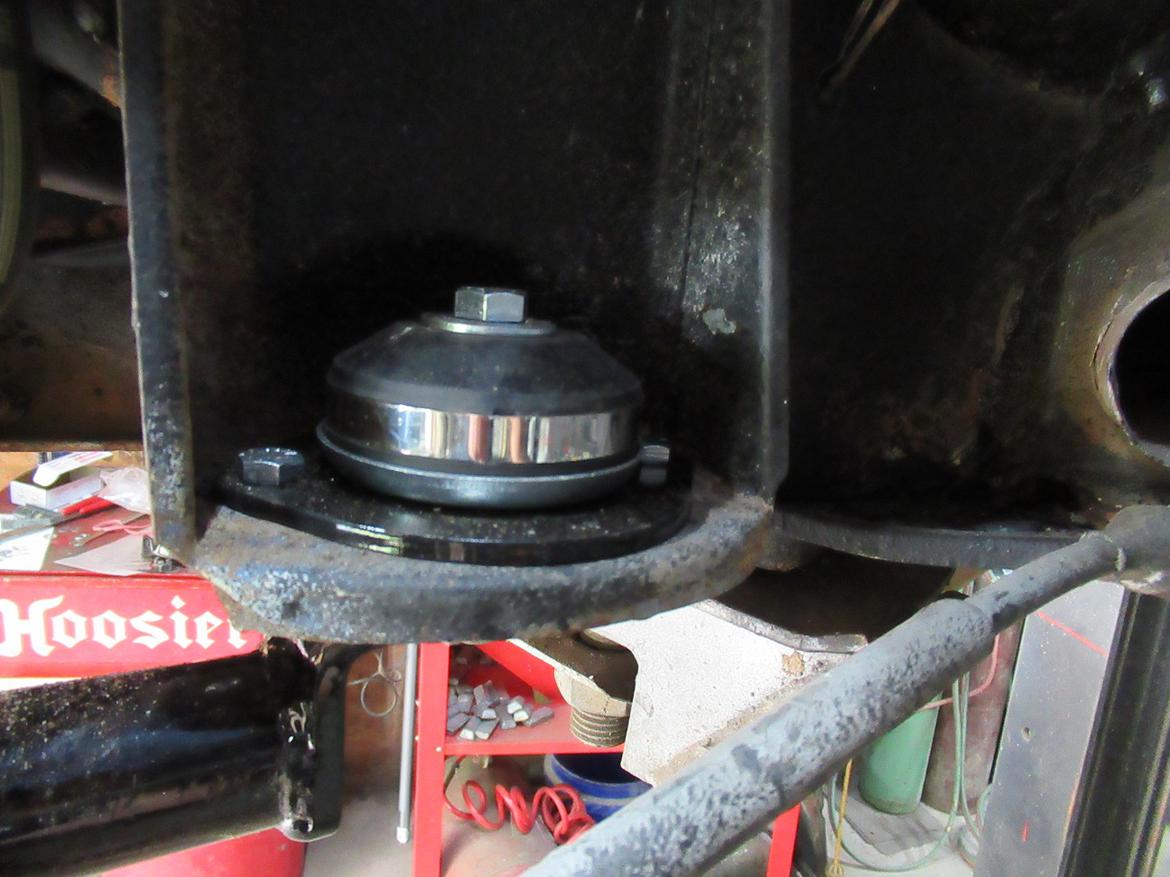
In reply to RallyCaddy :
Hopefully you can make it to our Ohio national event. I would love to see this thing in action.
This is awesome! I always liked the 914s.
As somone who hates 914-4 this thread is great to watch.
The seat is securely mounted and a set belt installed. I am waiting for the steering wheel release and s spring for the clutch pedal. Then brakes. This pic is before the seat was final installed but for fitup, here's a peek.
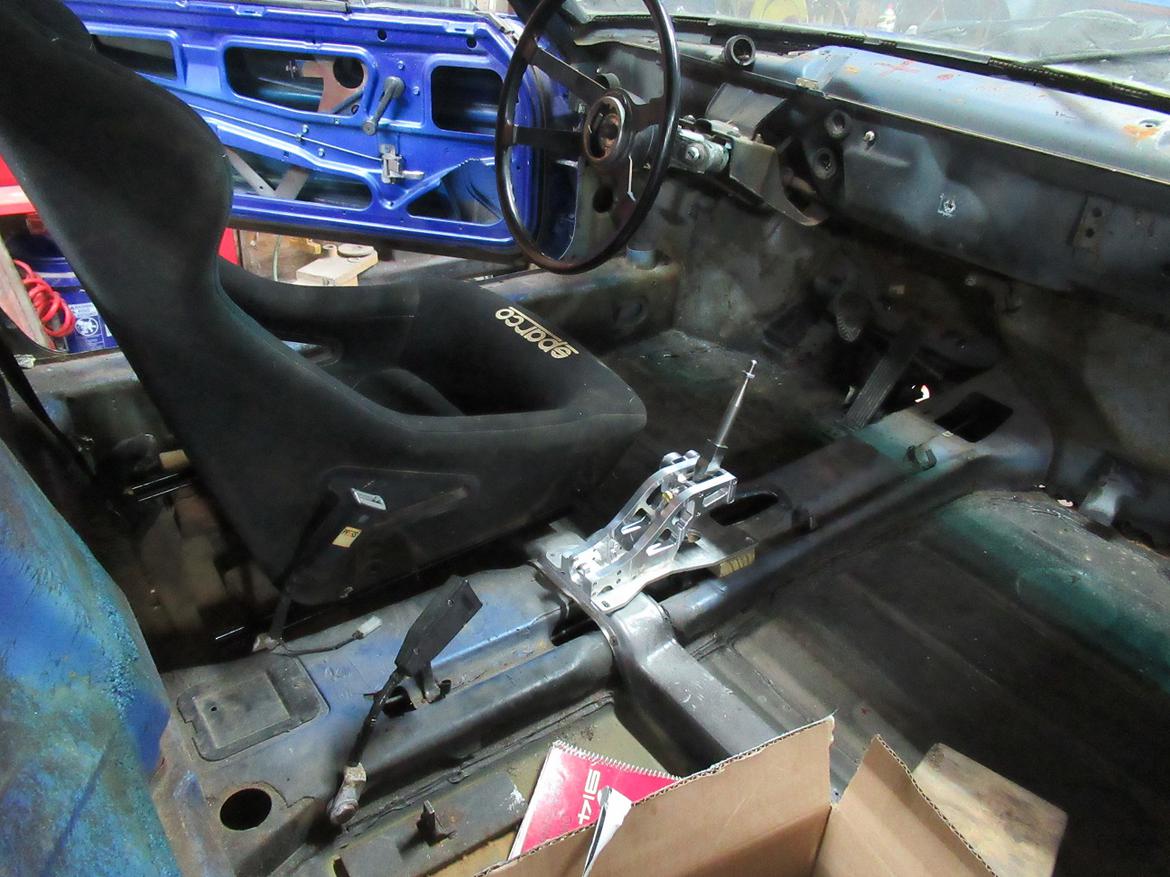
And for a teaser-
A hint at what is to come....
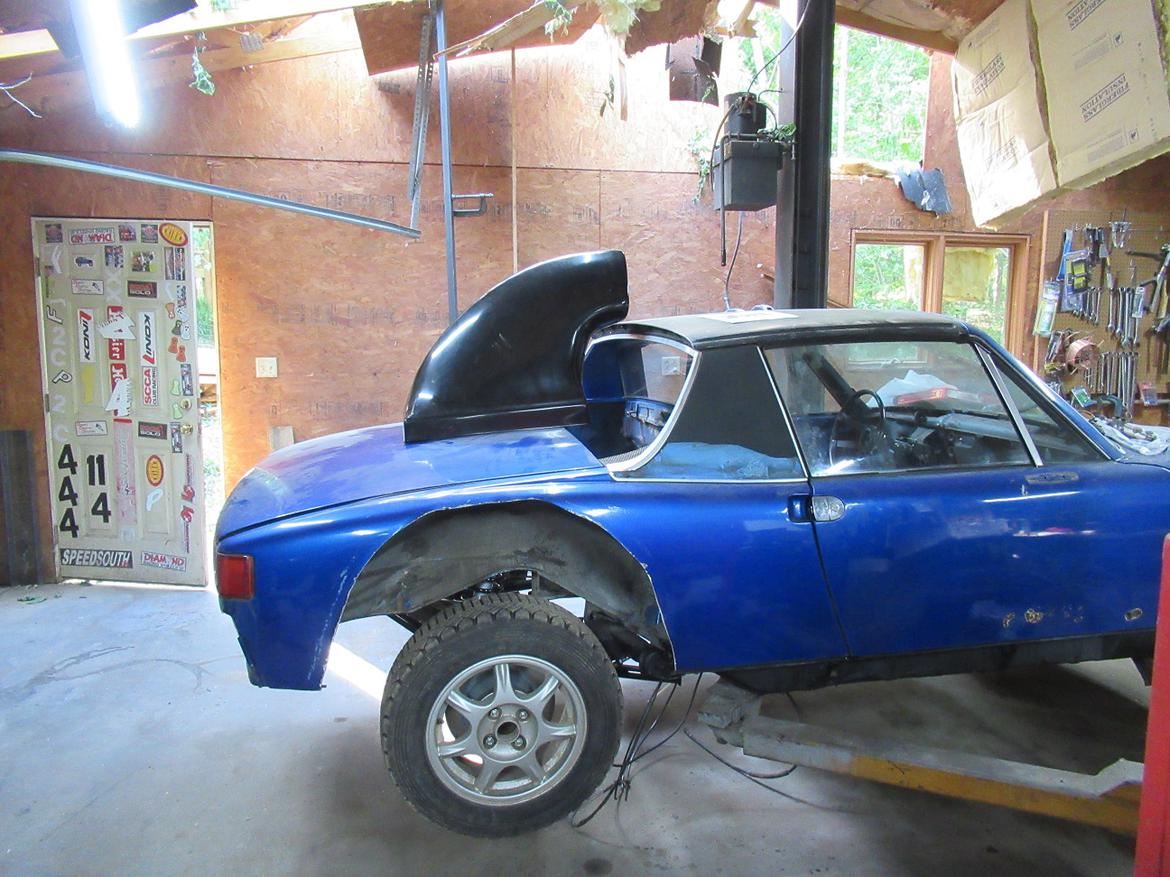
OK. BREAK TIME.
No more updates till next week. I am off to the Southern Ohio Forest Rally for some fun. I'll have parts here when I get back and it will be time to turn up the heat and really get this thing moving along.
The shop will be all fixed when I get back anyway. Insurance and construction crew are hard at it.
irish44j said:
RallyCaddy said:
The big push is to make Ohio but that's a really optomistic target.
If not, come to the DC region two-day double the last weekend of June (in W.Va.). If you want to find out how the car will stack up against some of the fastest MR cars/drivers in the nation, this is a good place to do it (I'm trying to get Vaughn Micchie to come down for it as well with his 924S). Our MR field for that event should be something like 20 cars (M3s, swapped e30s, a 944, 2zzz-swapped MR2s, Miatas, etc, . Hell, our back-markers are a BR-Z and a boosted Miata ;) There are only two out-of-towners who have been here and won in MR, that I recall - one is a national champion (John England, from Ohio), and Vaughn, who was 2nd at nats last year. So it would be a good test event (and expect something like 20 70-90 second runs over two days) if you want to shake it down and see how it can do.
Also, I want to see a 914 in action.
well E36 M3, now that I know who you are, I guess you know all these guys anyhow lol. What happened to the VW pickup?
Andy (Thomas) will be (un?)happy to see you in RWD though, since he's buidling a 2ZZZ MR2 at the moment for MR.
In reply to RallyCaddy :
I'll be around SOFR this weekend so I may see you there. If you happen to stick around we are having a rallycross on Sunday at the site where the national challenge will be in June in Chillicothe where the first day of SOFR is located. You are welcome to drive my Miata or I am sure there are a few other Ohio guys you know that would be happy to let you codrive.
UPDATE time. I'm having issues everywhere. The shop is repaired, I fractured my foot at the rally last week and parts problems. The brakes arrived but the rear rotors are not centered in the calipers.(?) The front brake hoses are too short. The Fiberglass hood and deck lid are actually OK so far. The wiring harness is delayed in transit and will not arrive till AFTER the holiday weekend. As usual, I planned to use that time to make serious progress. Then the transmission took 4 days to get to Florida from Alabama. They took another 3 days before looking at it and now the carrier bearings are not fitting the Quaife. Calls, and emails all around to find out what the problem is and how we can get it fixed asap. If the diff was machined wrong, we will have no chance of making the June race. I should have been installing the engine and trans now or at least over the weekend to make schedule. Having to sit out the weekend with only minimal progress will be a huge waste.
All of that sounds about standard for rush build. LOL (Not that I'm laughing at your misery.)
Where did you get those universal motor mounts? They look like candidates for replacing the weird fluidized mounts on the 2J's.
How did you break your foot?
Great build! Hope your foot heals fast and the shop gets done quickly, as I really NEED to see progress on this. Amazing
Ok first, I included the pic with the mount instructions and part number for ya'll. I got em from Summit.
The Aeromotive pump, filter and new rubber lines are installed up front. The tank is up by the cowl so it has nice gravity feed with pickup and return lines at the bottom of the tank.
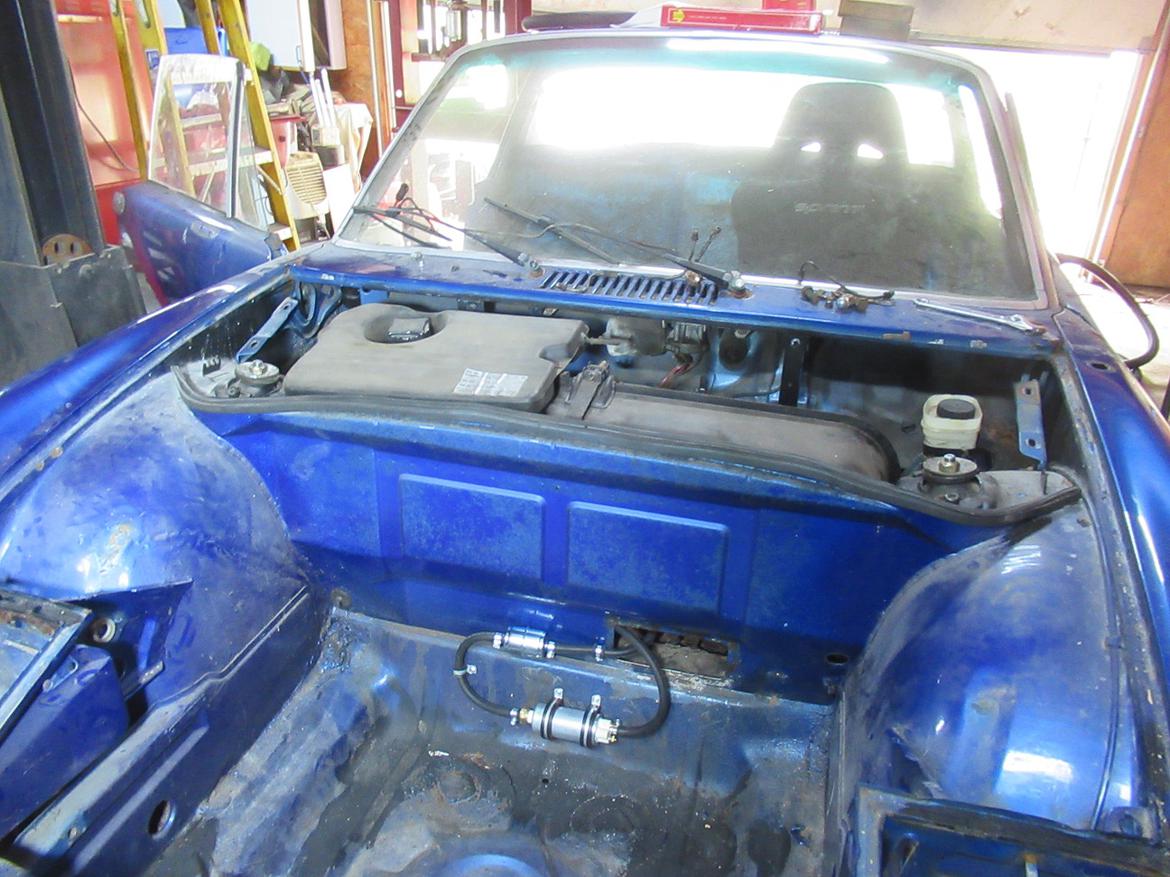
Next, the brake install. All new hoses and calipers. These were rebuilts from PMB performance. The fronts went on along with the new rotors without a hitch. The rears however had issues. The rotors were not centered in the caliper housings and lightly rubbed the back side of the rotor in the caliper. Offset to fix this needed to be 0.080". Why? I am not sure. The old ones didn't have the problem and with time short, I just needed a quick fix. Normally I would add machined spacers behind the caliper mounting points. In this case however, there was not 0.080" between the caliper and the control arm when installed. More like 0.050" so that would not fix it. The other, less desirable method is too add a spacer plate behind the rotor. It does need to be flat. Well, Dynatorch CNC to the rescue again. I had some 0.090" (close enough) aluminum plate. A few minutes later and I have some spacers.
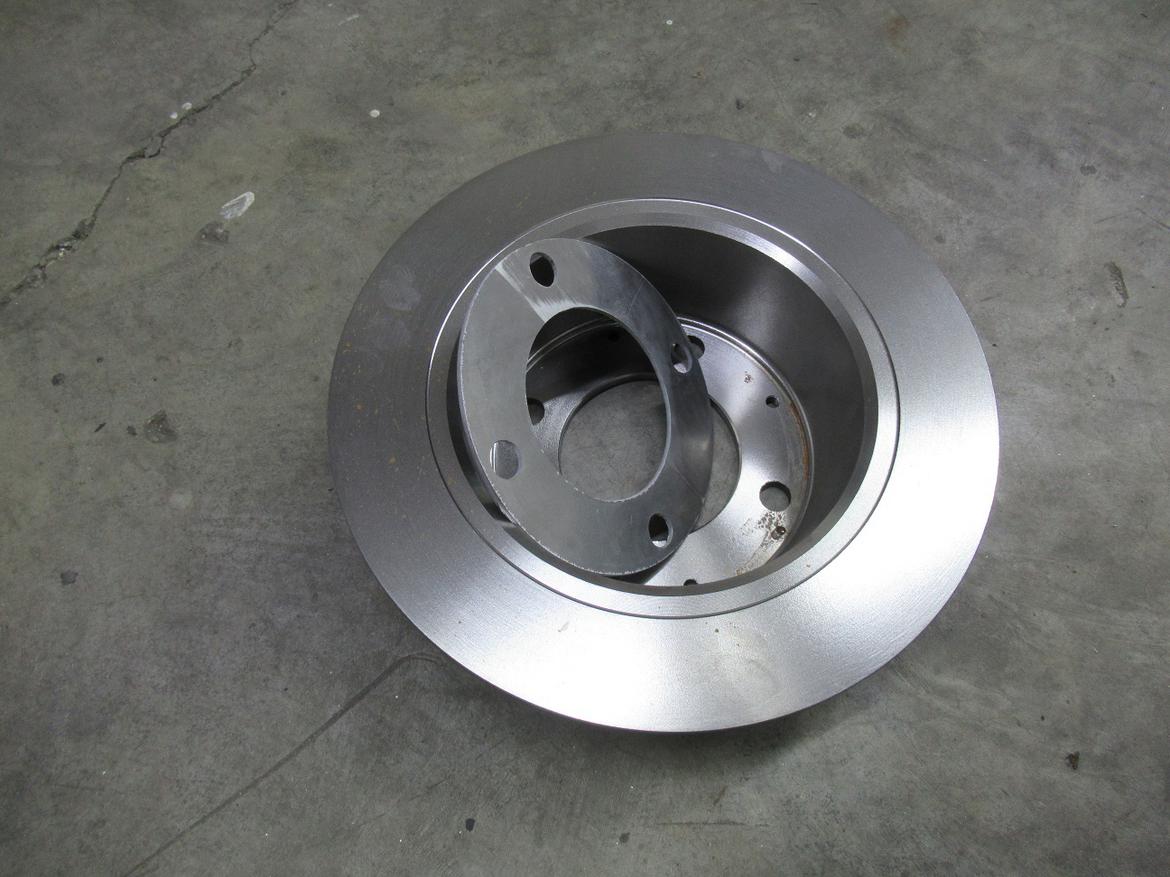
Now install, adjust and tighten it up and it looks like a go.
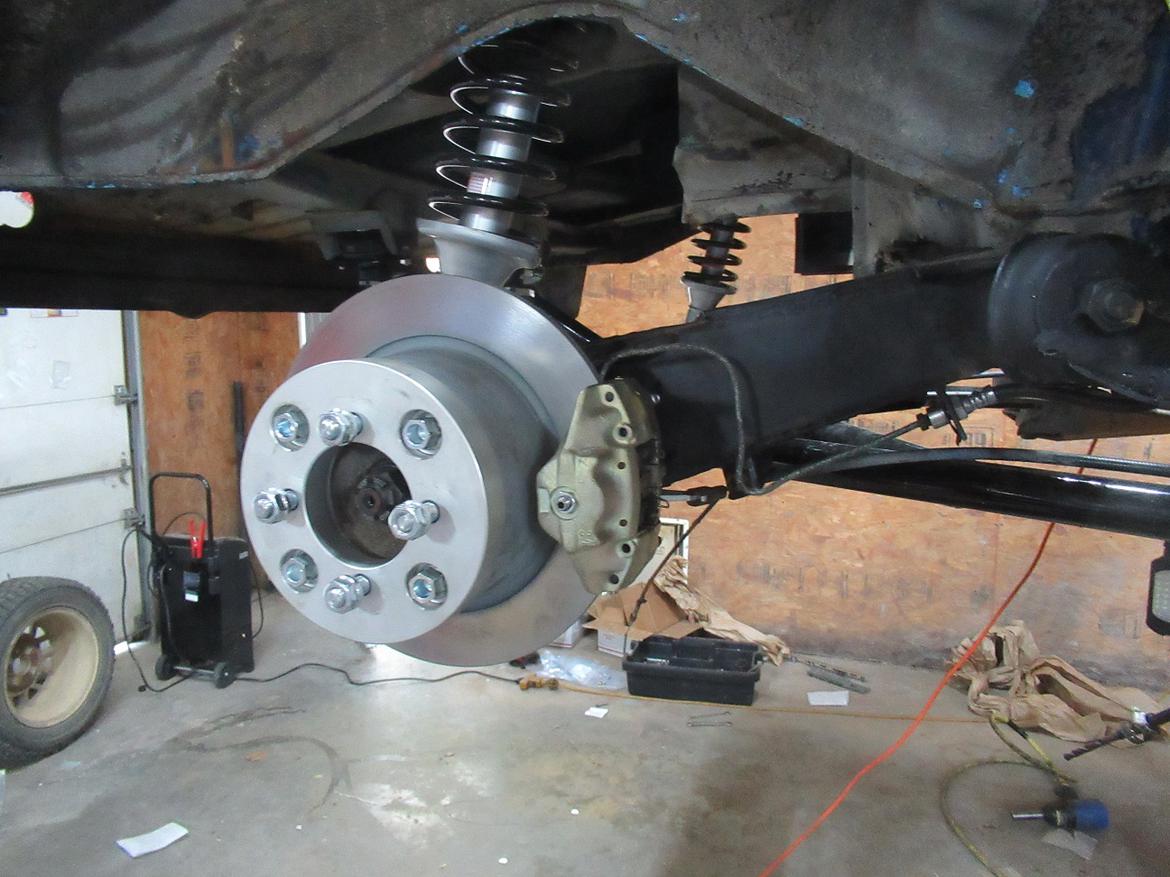
The rubber 4x4 wheel flares arrived all curled up tight. They need some sun to warm them up and let them uncoil. Snakes do that right?
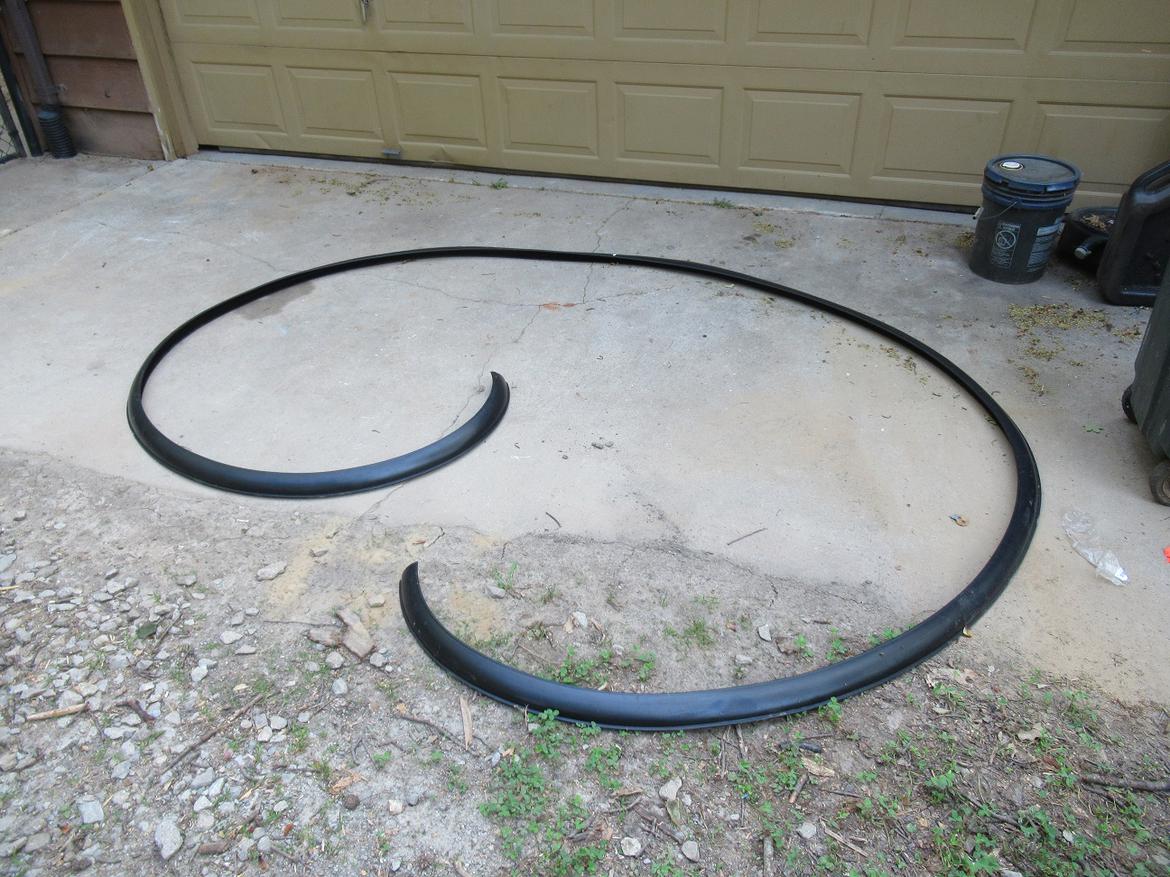
So for drama, the Quaife LSD and trans were shipped off almost 2 weeks ago. It took 4 days to get from Alabama to Florida. Grrr. Then 4 more days before they got into it only to find issues with carrier bearing sizes. So as it stands, the whole project is on the edge of disaster. Well, not making the June event anyway. I will know today if the bearing issue is resolved. With the holiday weekend, I really need to get the motor into the car this weekend. Without the trans, that cannot happen. So, if it gets the right bearings today, I will drive to Florida and get the trans tomorrow (8 hours each way). Then get to Persad parts Saturday to mate the motor and trans and get working on the install and half shafts this weekend, The wiring harness shipment is delayed till Tuesday.
If all that happens, then clutch, throttle and shifter install are next. After that, wiring, cooling and exhaust. Then cosmetics and some gauges.
Seat, lap belt, streering wheel with quick release, pedal set all installed.
I got a rebuild kt for the pedal assembly as all the plastic bushings were shot and the clutch was frozen in place. It's all nice and smooth now.
Just brake bleed left on that,
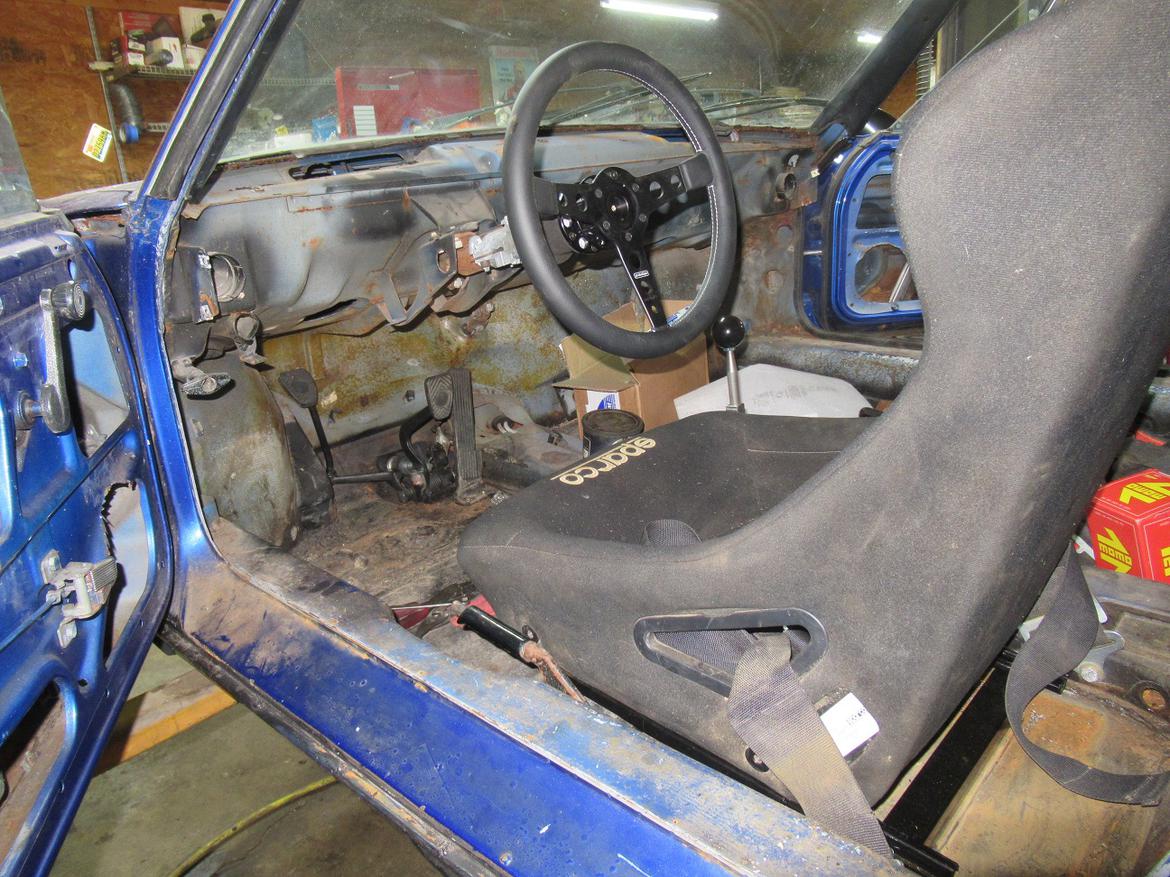
Oh, on the foot damage? I have perfected the foot twist technique while jumping out of the back of pickup trucks. Just land partially in a rut. 2nd time I did that so it's now a thing. Getting better slowly.
The shop is all rebuilt. We don't fool around here. The grass may take a while to grow back but the building is back. The tools and such have to go back in place this weekend.
Quick update. GOOD NEWS! The Guys found workable bearings. I'm headed to Florida to pick up the trans. No shiopping this time. I'll be back with it Friday PM and will get to put it all in this weekend.
So, after performing some lengthty searching, the guys at Dirty Racing Products in Florida located a set of bearings that fit the Quaife carrier that was cut undersize. They let me know they had the parts and that it would be ready Friday. Sit tight, I'm on my way. I left Thursday making it to mid Georgia that night and on to DRP about 9:30 Friday morning. They had it all done and loaded me up at 10. Then a marathon drive back to Alabama.
Friday morning, Saheed Persad met me at his shop to put things together. He had the engine long block ready with a new oil pan, upgraded pickup, new head studs and gaskets (just in case) and a new timing setup. We added the intake and all the other parts. A Fidanza light flywheel, clutch and new throw out along with the cable clutch fork. A Y pipe and other bolts and bits and we had the trans on and all loaded in the truck. So back at my place, here's the driveline waiting eagerly to get in it's new home.
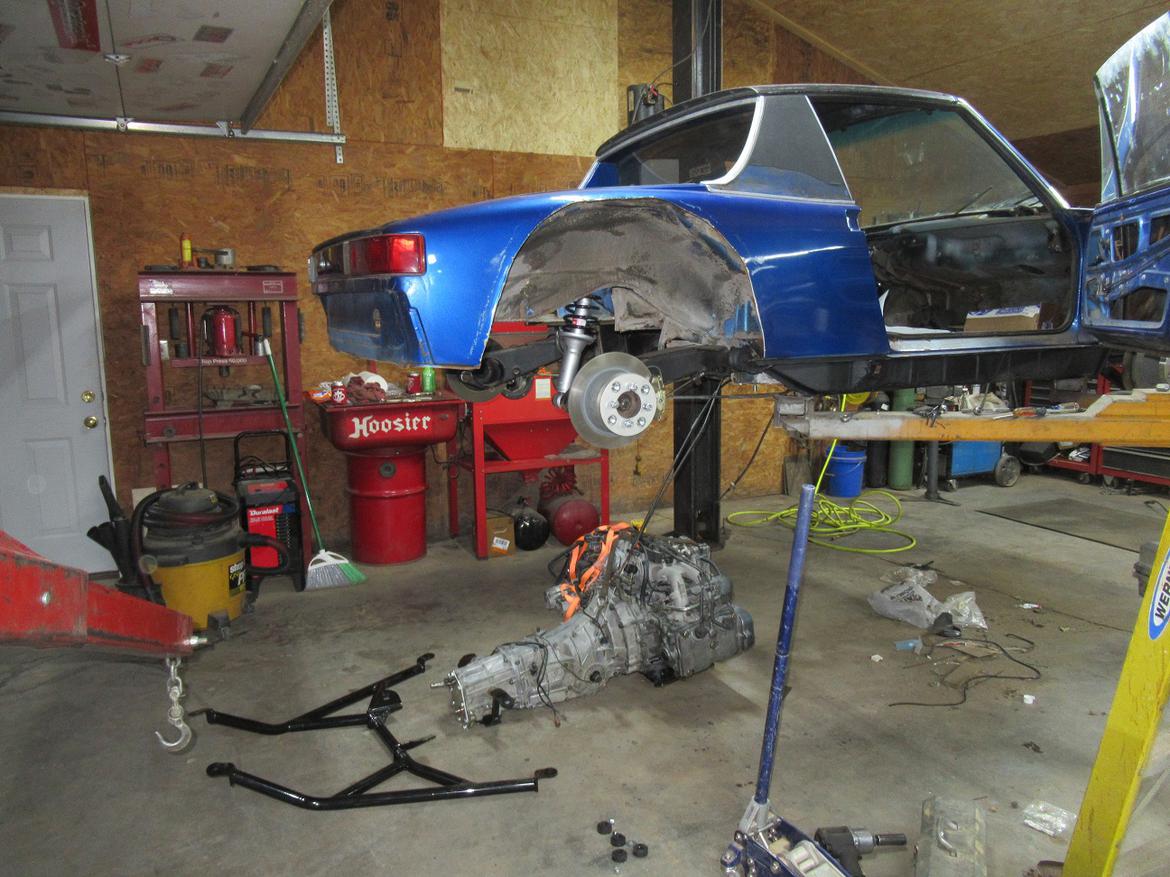
Then with some hoisting we're getting there.
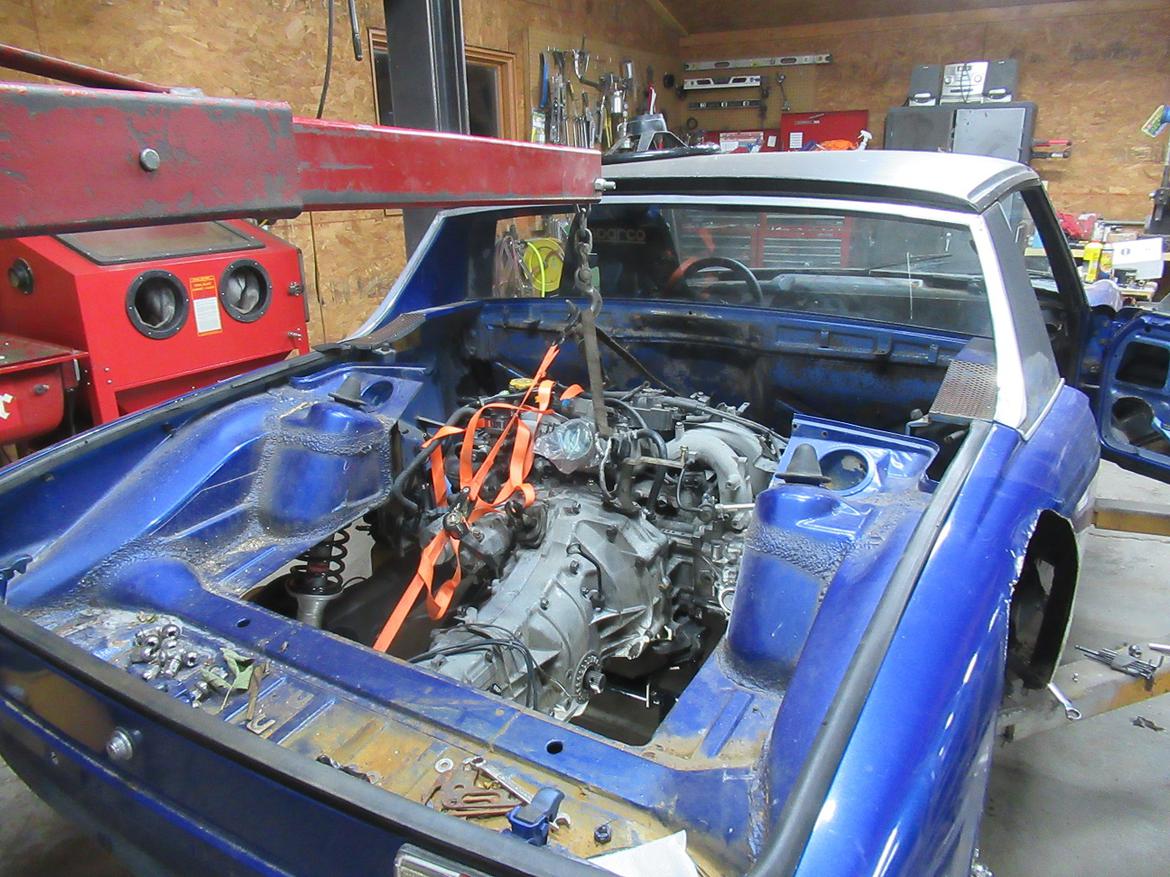
Some wrestling and some bolts and here we are. Man, look at all that room to work wround the motor. Best swap I've ever done. Usually there are things hitting things everywhere.
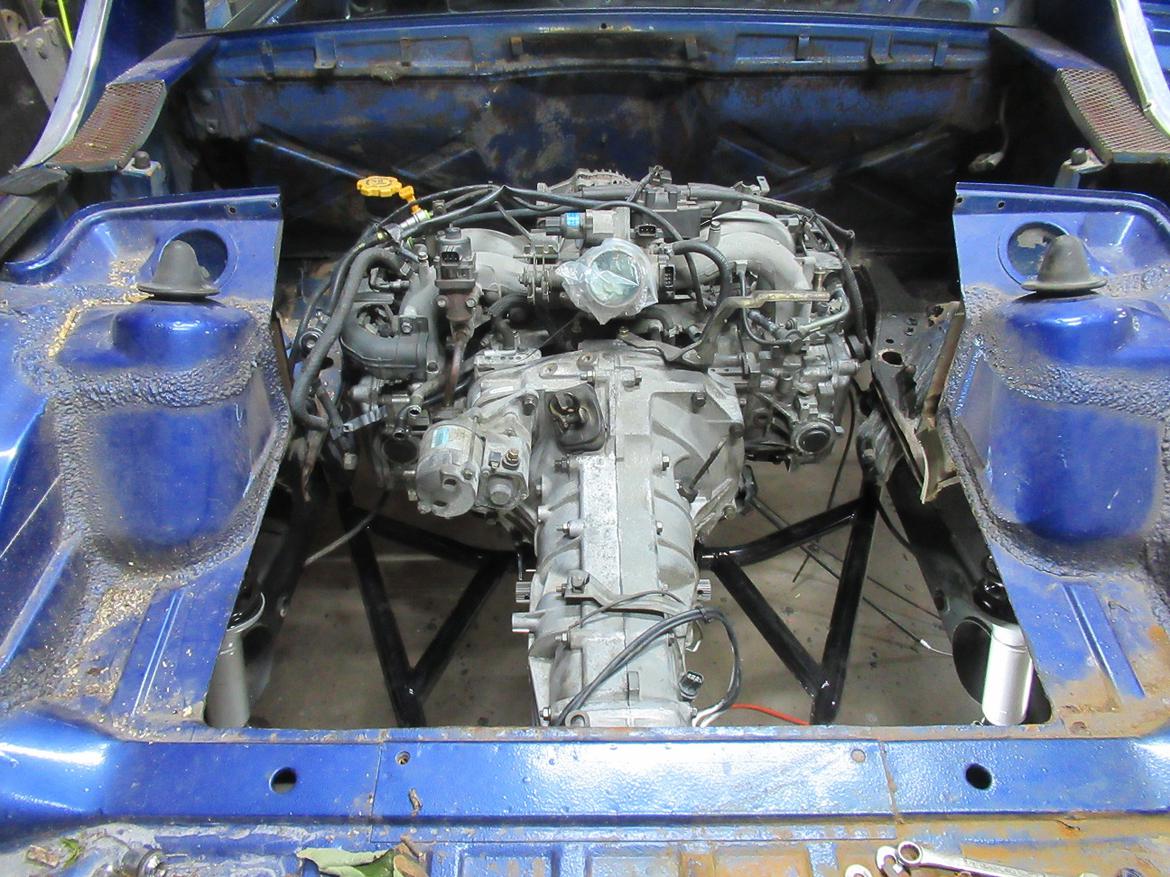
Even up front, lots of room. I was afraid the engine would tight against the firewall but not here.
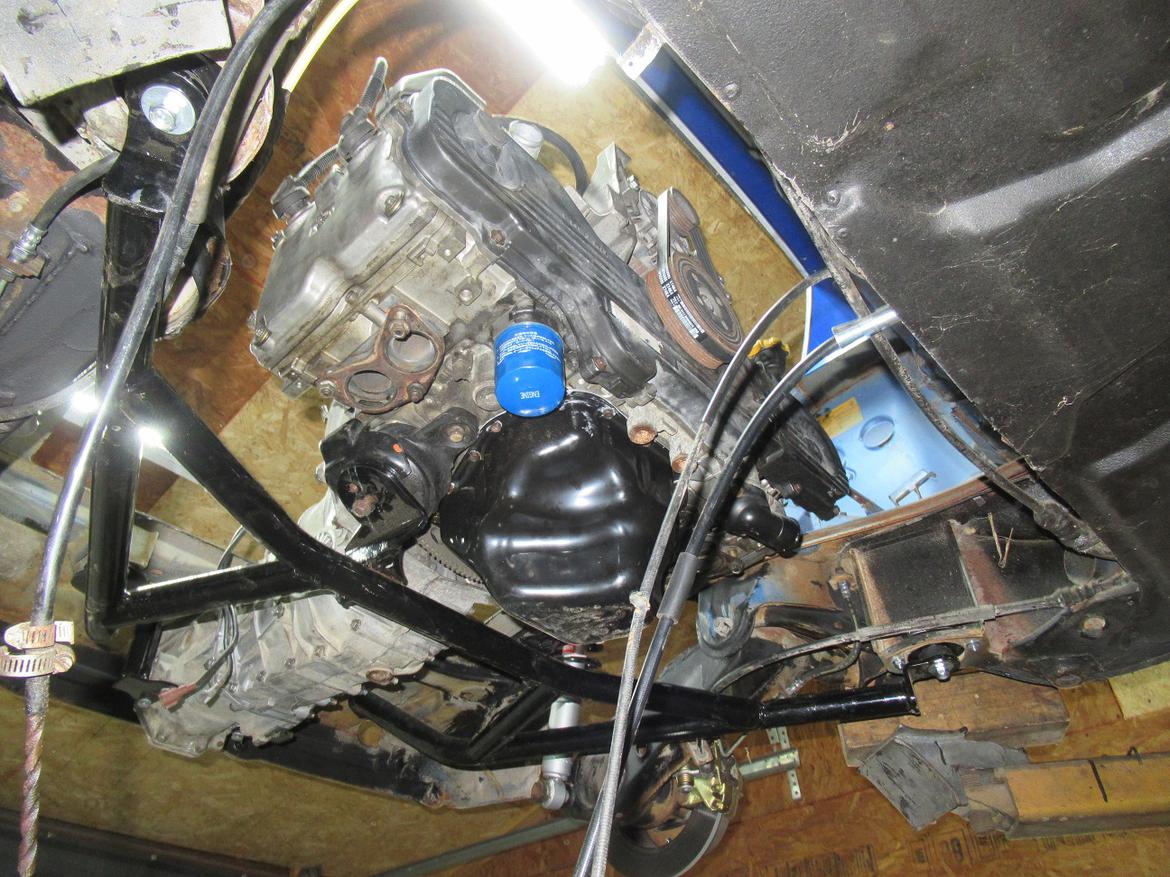
Next up. add some required bits. All the cables and other heat sensitive parts need to stay away from the exhaust. So lets look at the Y pipe and see what we have.
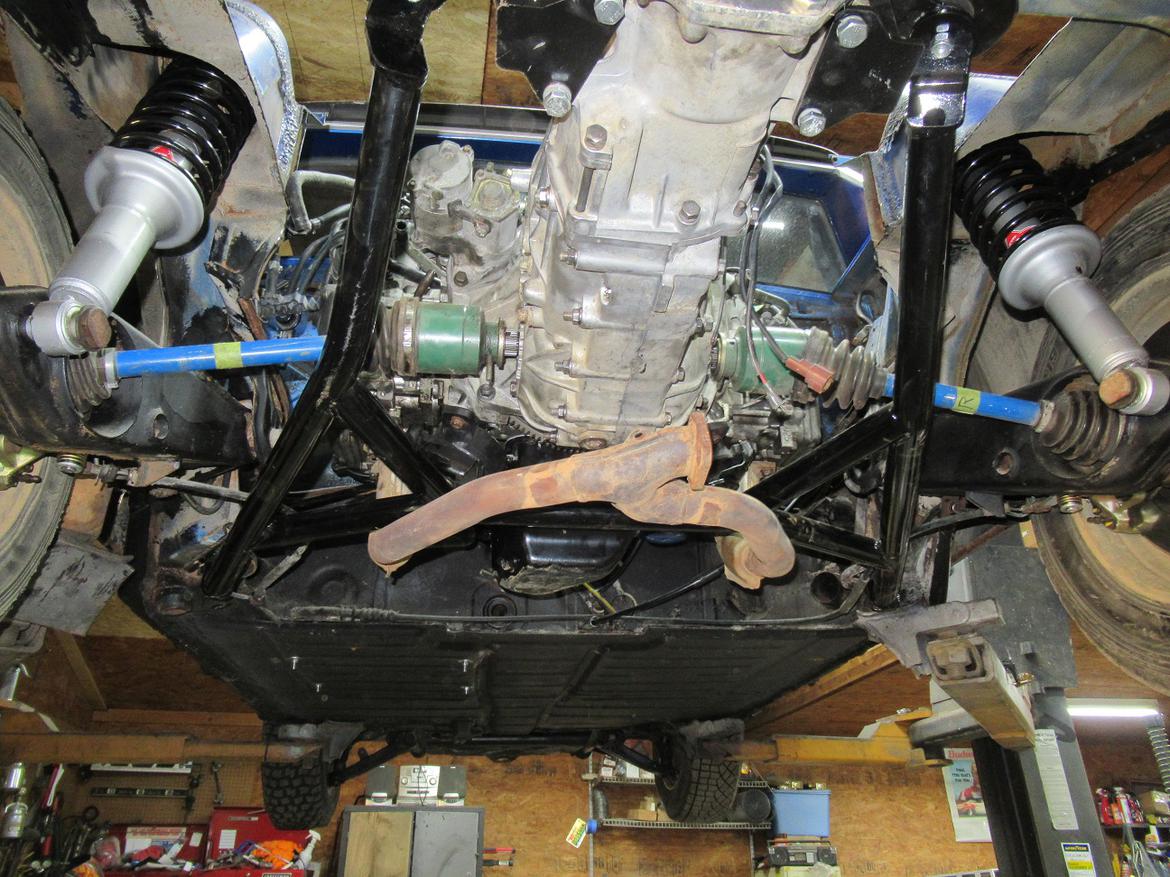
OK, problem, it hits the cradle before the bolts get tight.
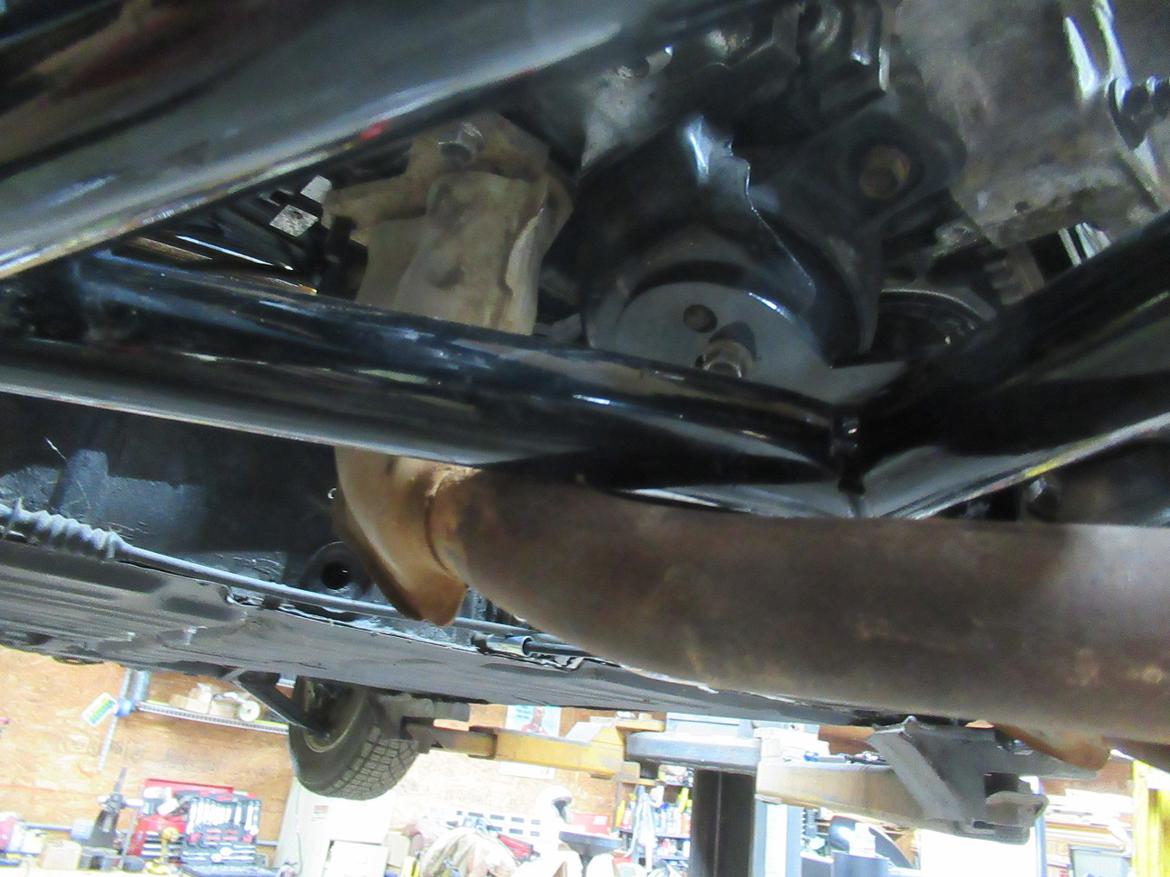
That will require some new pipe(s). Perhaps duals and forget about the crossover or do an H pipe. Cutting away the Y looks like this. It's fixable without restriction. I am not super happy about the pipes below the frame as they could get damaged, but the oil pans is already down there.
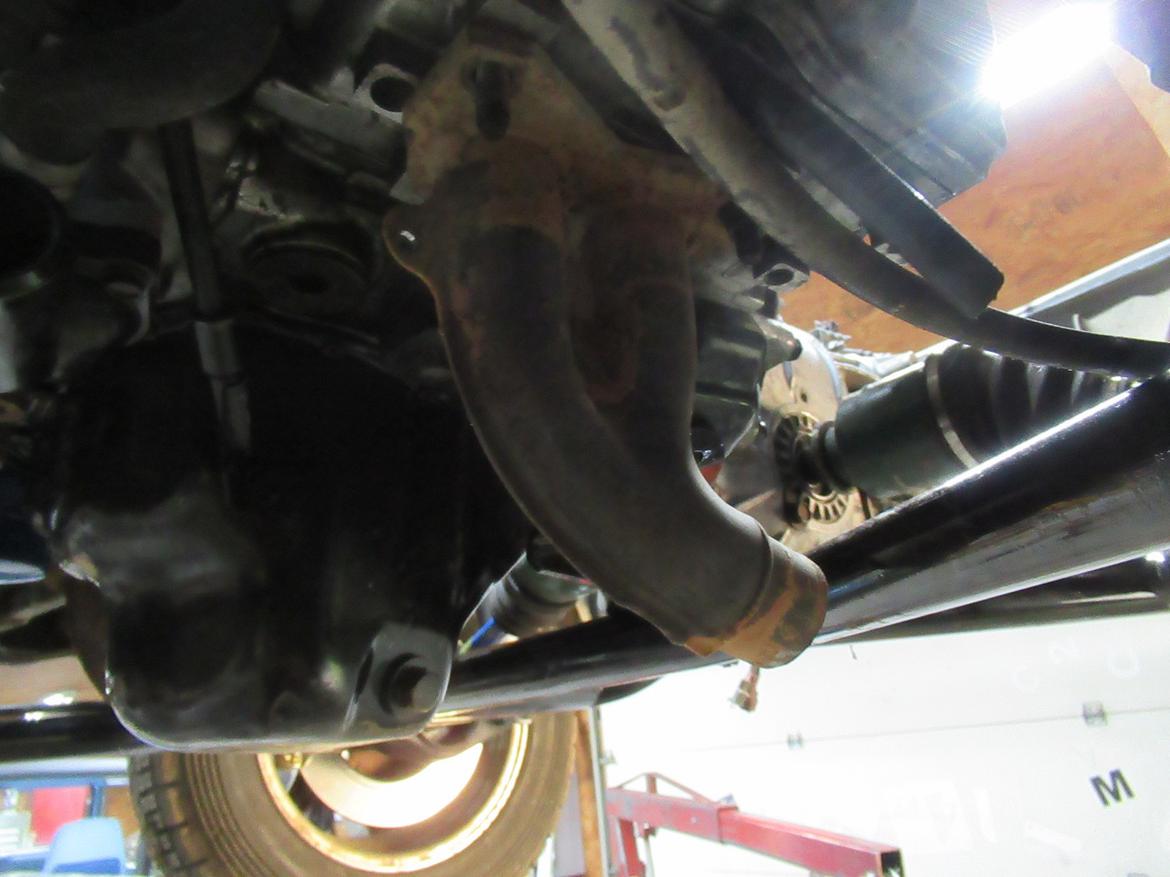
The next item turned out to be a huge win. The half shafts supplied with the swap kit had the wrong outer joints. They were larger and did not fit the 914-2.0 outer hubs. I knew about this already and assumed that I would have to fabricate new ones using Subie and Porsche shafts splicing them. That;s a couple days work with machining and welding. On a hunch, I thought "maybe the splines on the shafts are the same". Lets disasseble and check. Sure enough they were indeed the same. So all I had to do was disassmble both shaft sets and swap the outer joint assemblies. YEA.
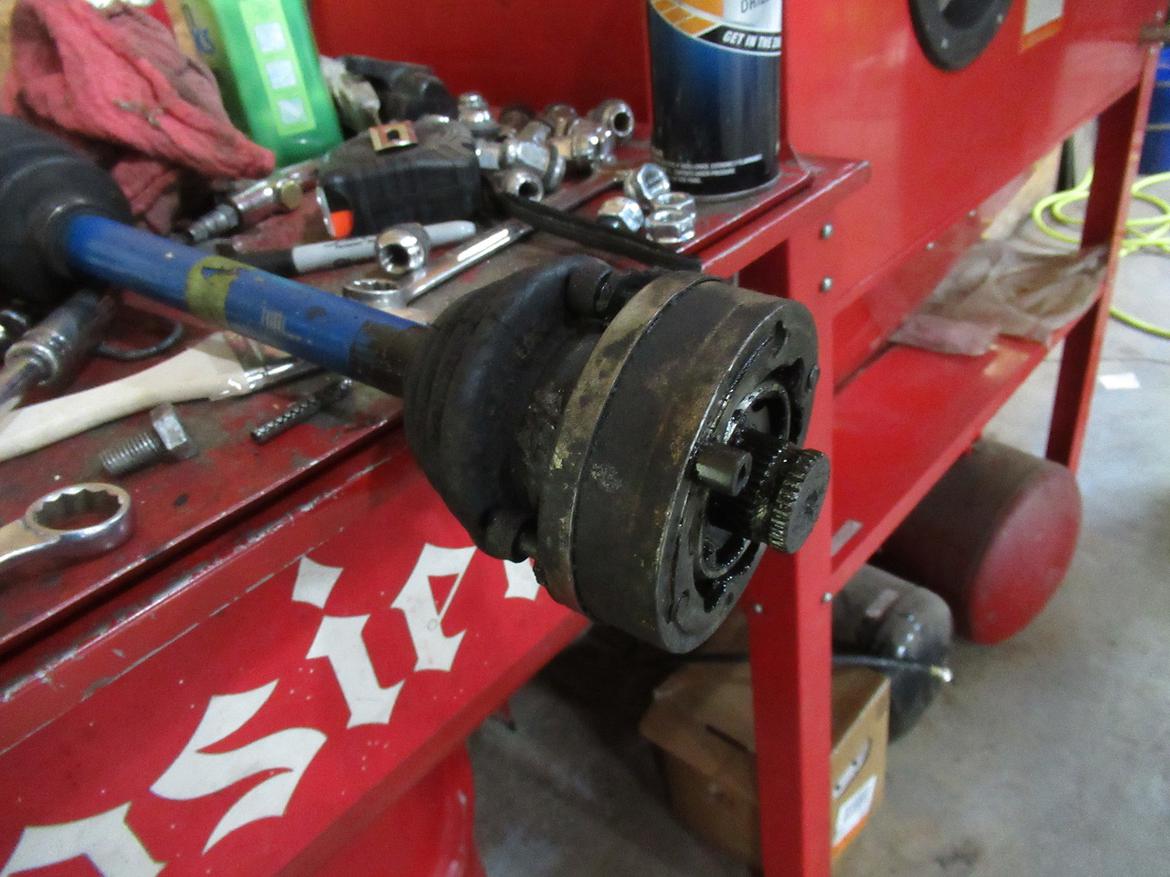
Some cleanup and grease and they'll be just right.
Another item showed up. After putting all the parts on the car for a ride height check, it's not good. The front compressed about 2" but the rear? Nothing. That's good for weight saving but not for handling. New springs will be required asap. Meanwhile, what rate? Well to figure that out we need to know just what we have. Time for the scales. Any guesses overall? Well, here...
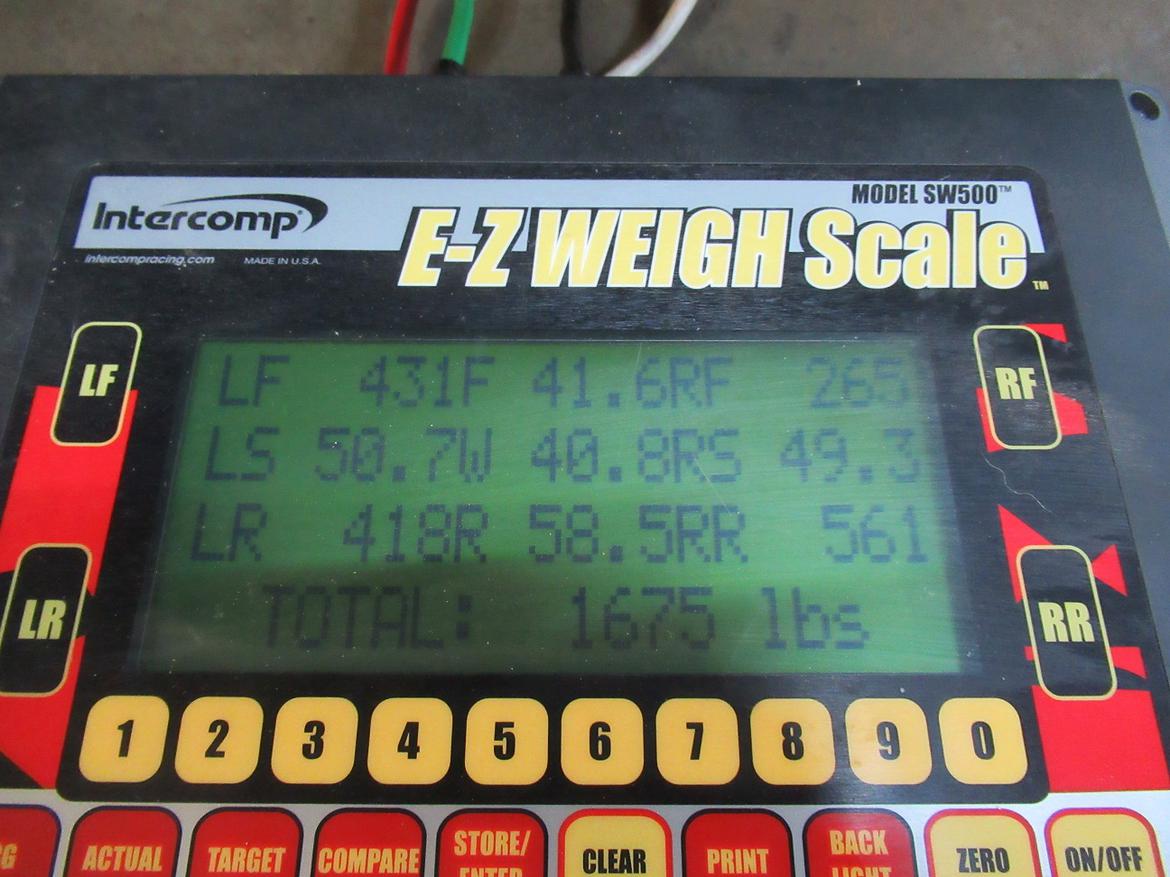
Now my floor is FAR from flat so the L/R balance is way off but the overall is good and the F/R is in the ballpark. I still have to add an aluminum radiator, water, light battery, wiring harness, ECU, exhaust and a few minor details. I also have a bit more metal trimming on the body. Target is 1850#. Lets see how close I get later.
There's still more this weekend. Why not? A whole extra day to crush knuckles.
So the next issue is installing the shifter. I had figured that the cable shifter system from Factory 5 would go down the middle around the engine and back to the rear of the transaxle. Well, I was wrong. When I finally unpacked the cables and checked out the 818 build sheet, I see that these things are LONG. They run the shifter cables forward thru the firewall (yeah, the trans is at the back) and then down the side and around the rear wheel and finally end up at the far back. This is actually a good thing. It avoids all the hot parts.
With all that in mind, I had to run the cables down the drivers side. But where? Ah, remember that the 914 is air cooled? Remember that they ran the heater air thru ducts from chambers around the exhaust system? Yes, these run thru tubes in the rockers that enter at the firewall (rear) and exit at the kick panel. Nice. It does have a bend at the back that is tricky but the front is another story. The front has a fairly sharp bend tha the cables will not like. So I cut the top of the rocker open and the used a hole saw to make 2 holes in the tube, sawzall a slot and the cables come out the top by the kick panel.
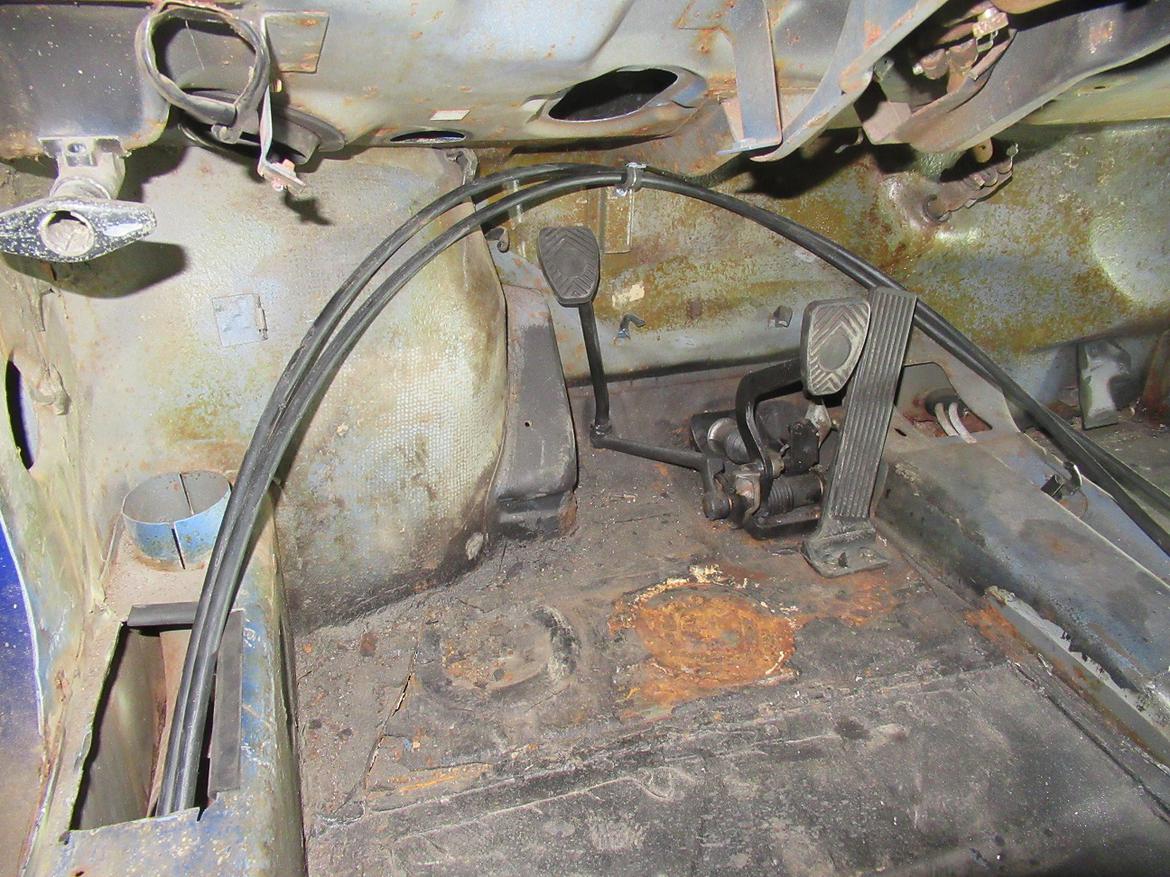
Adding some edge guard to the holes protects the cables. The some rubber lined adel clamps to keep them out the pedals. Not to mount the shifter properly. The top of the center console area has lots of holes for Porsche stuff. # of the 4 for the shifter fall over these holes. So I need a flat mounting plate.
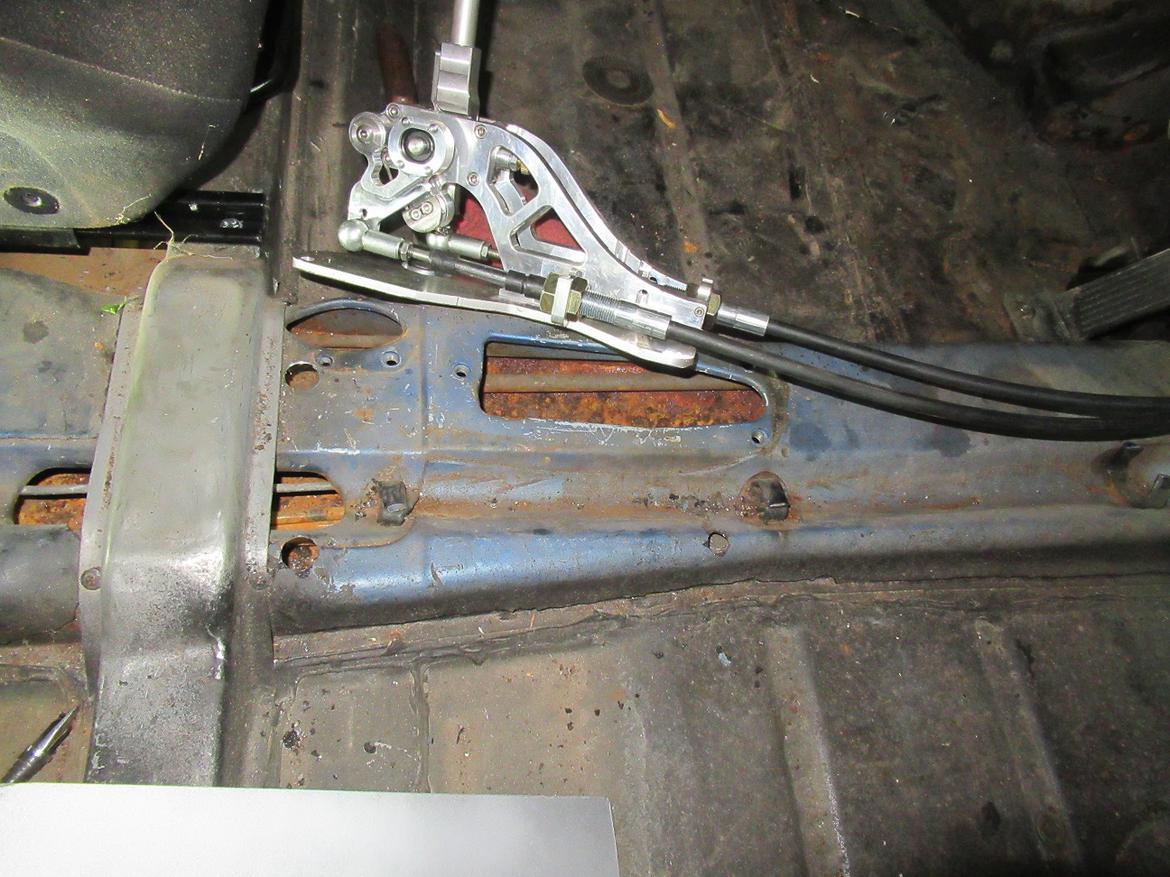
The first thing is that there is a lot of sound deadener on there. I can't weld to that. I know that some people go nuts digging out every vestage of that stuff just because it weighs "something". With the time required to dig all that out and my schedule, I can get to that later. Right now, it's fab time. Just remove whats in the way. A quick CNC plasma plate of 16 ga (see how many times this comes in handy?) and I got what I need, The weld it in. Yes, I did weld spray the back to reduce rust.
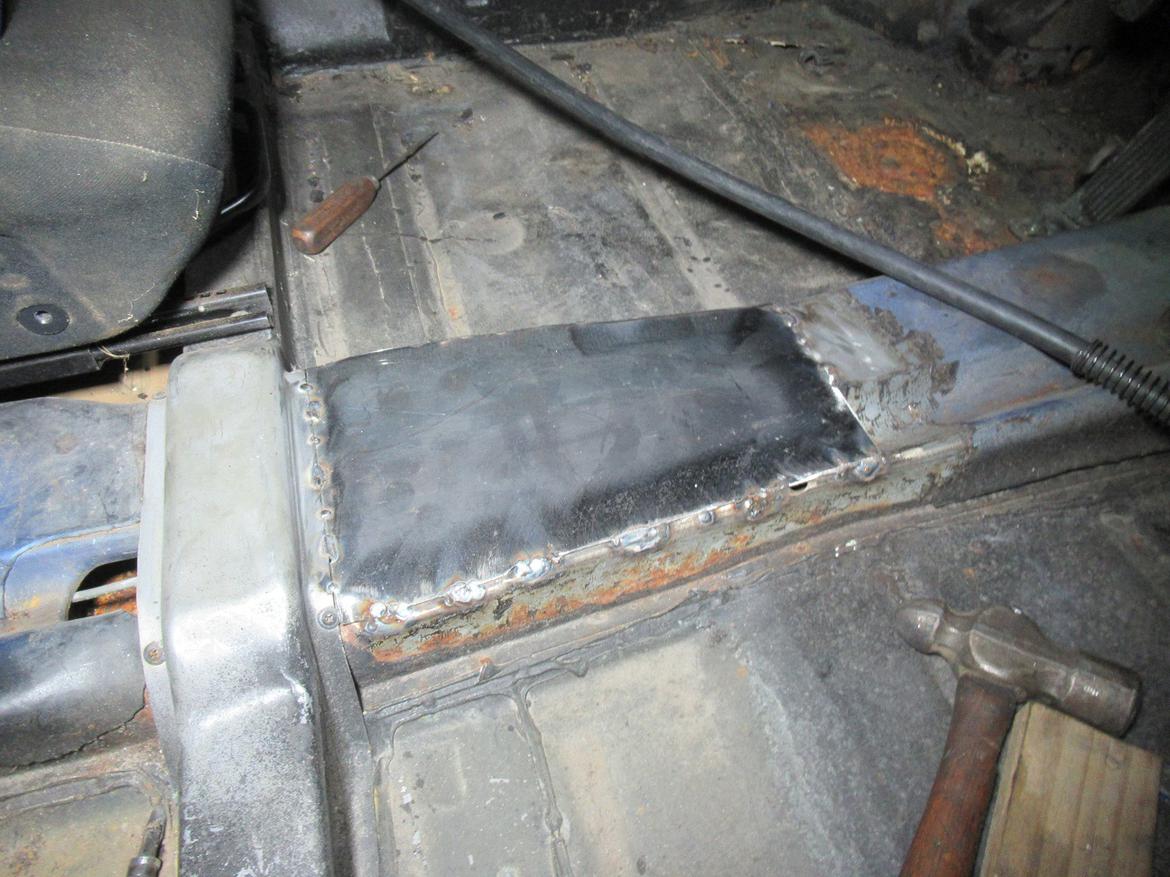
Some self etch primer so I can mark the holes. Then out comes the Nut-serts. 1/4" matches the plate.
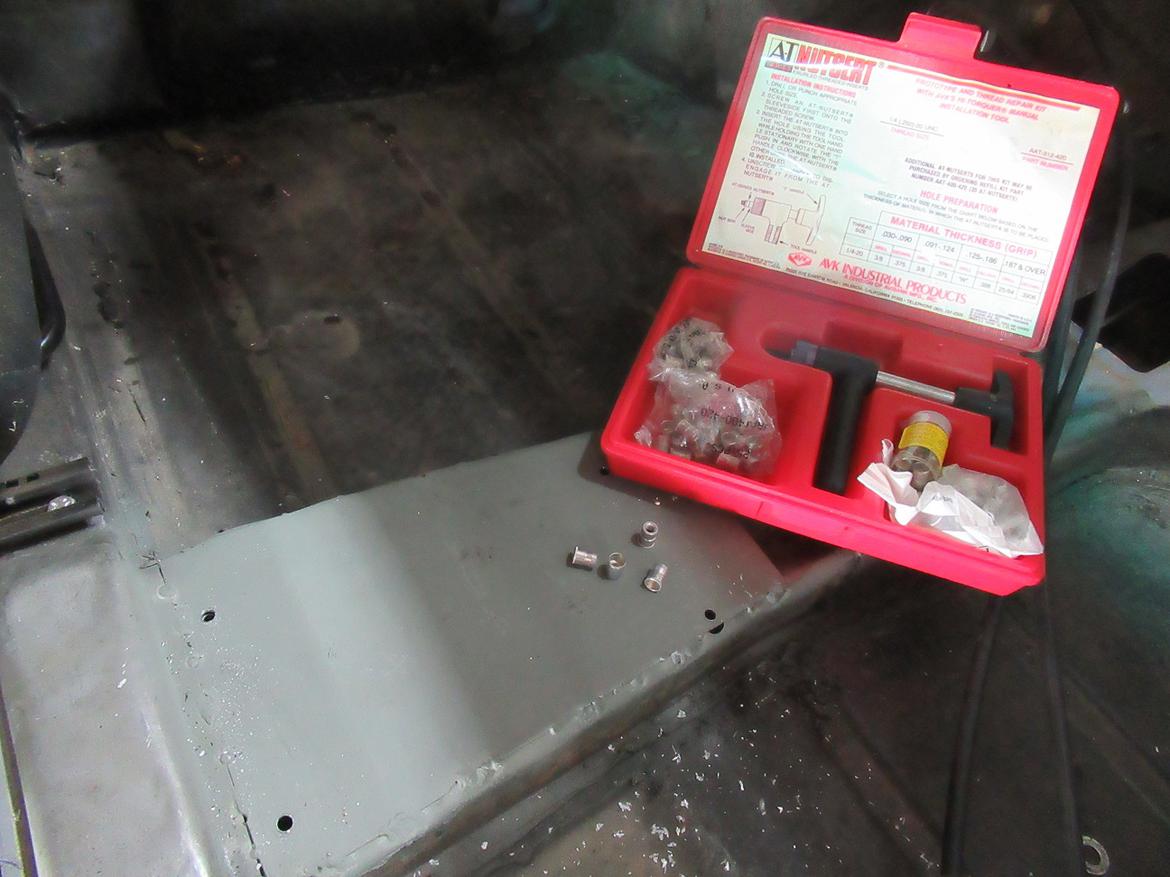
Little things just always add up. The bolts for the shifter plate were button head and sis not sit flat, so a countersink and some flat heads..
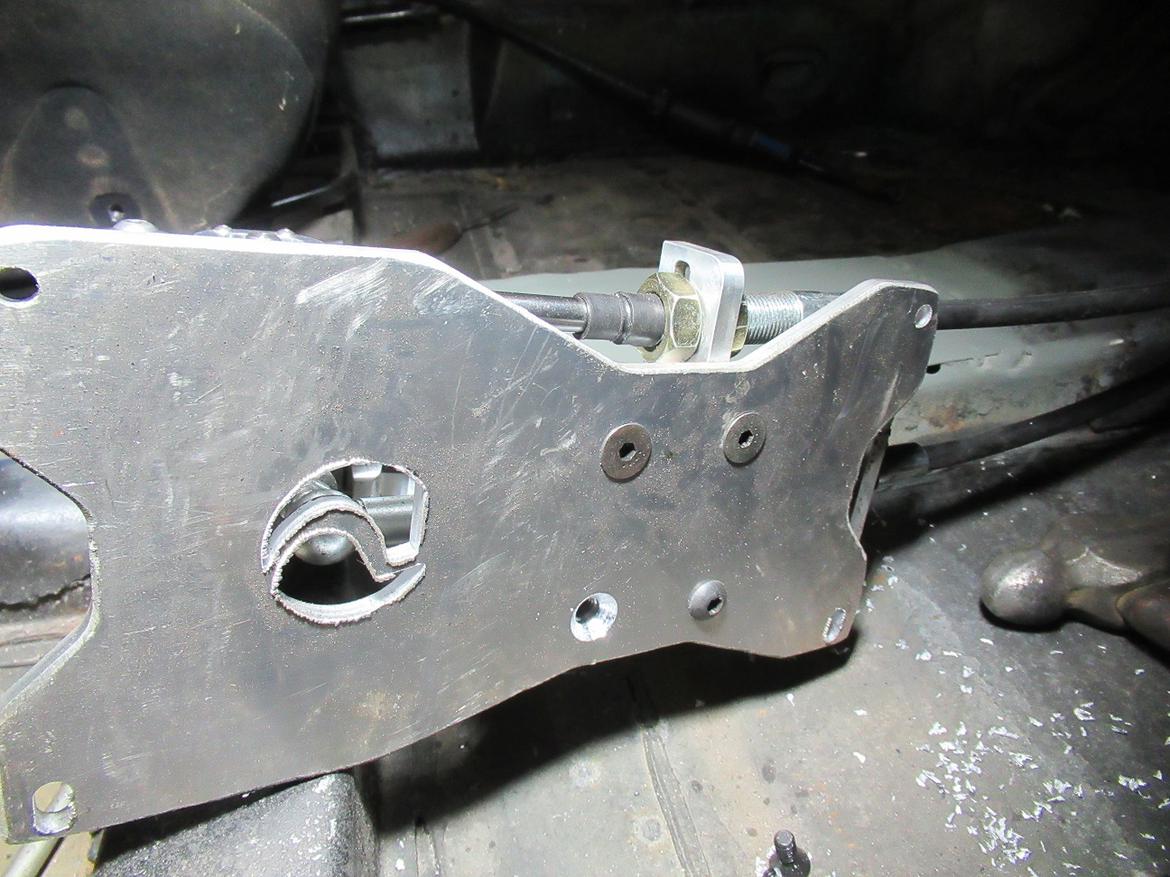
Now bolt it all in and adjust the cables and Hell yeah, we got a sorking shifter! Tight but it works.
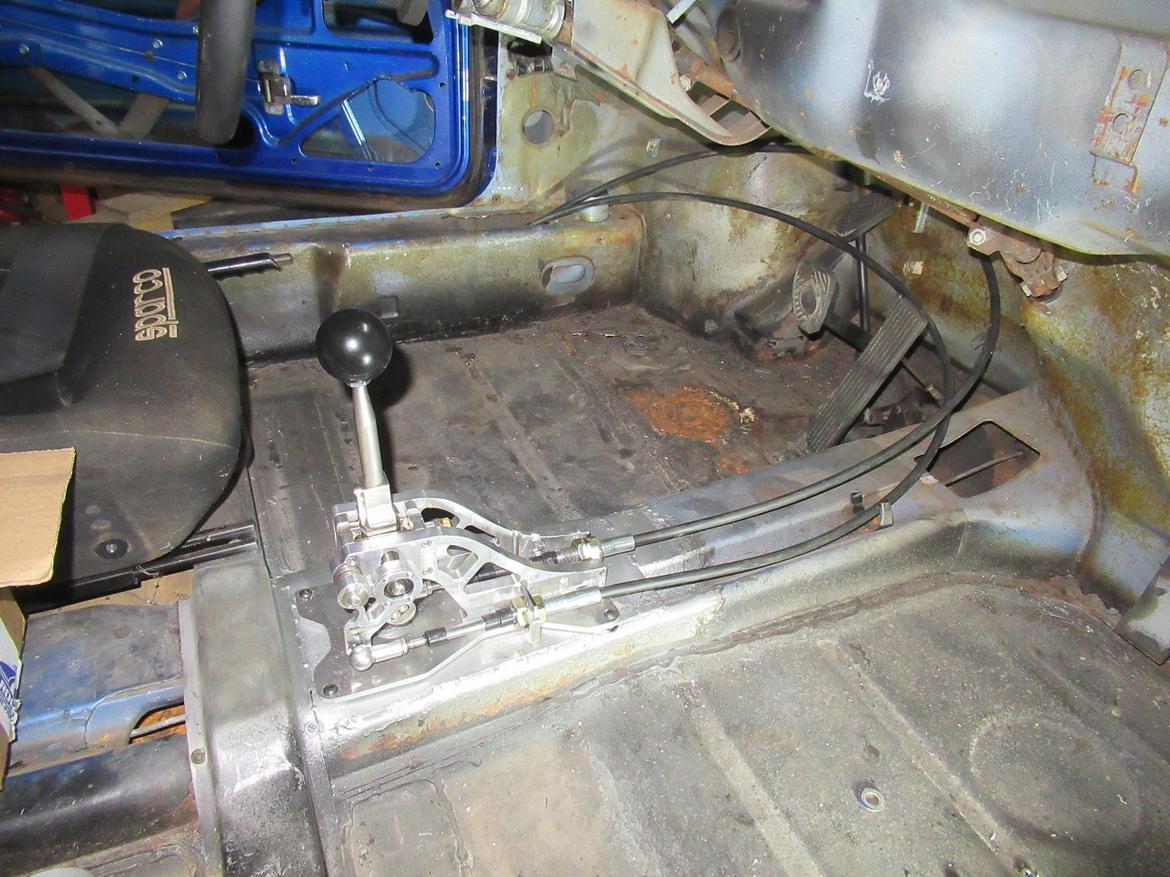
Here's the trans parts. Well one view anyway.
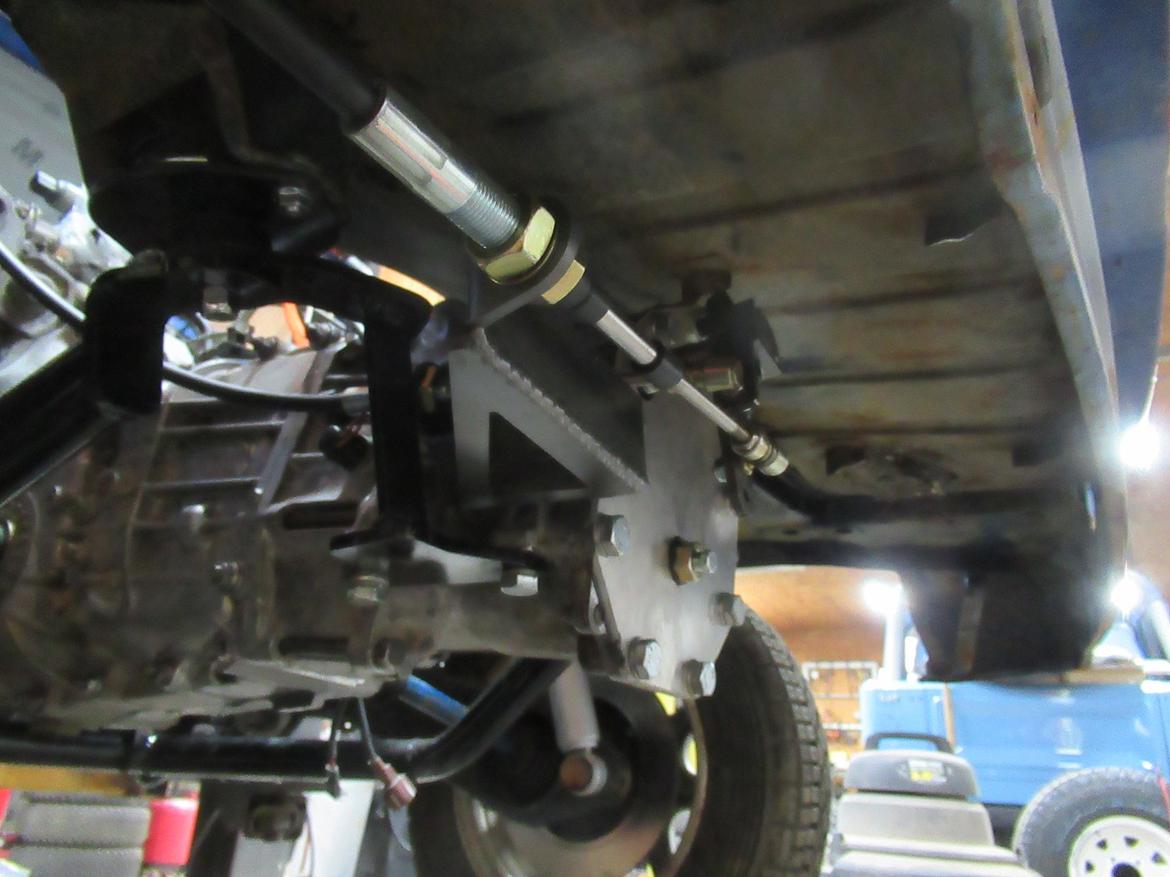
The half shafts were final installed, the throttle cable looks almost ready to use but the clutch cable is going to be a real issue.
I went after the rear spring problem next. No compression at all with the car sitting on them. These springs don't look all that big but they were LONG. I took them back out. Installed length is 12-3/4". Free length is 18"!!!. That's a lot of compression. Since the springs sit out behind the rear axles they have an even greater leverage advantage. The pivot to axle is 12". The pivot to shock mount is 17". Spring rate on my press looks like 75 lb/in. So compressing that the preload is 431 lbs. At the axle, that is equivalent to (17/12 * 431)= 610 pounds. And the car has only about 500 pounds per side on it (remember the scales?). So the preload is over 100 pounds more than the car per side. No wonder. Even adding my paltry 160 pounds to the back (divided by 2 cause both sides) didn't compress anything.
The spring rate isn't bad but that preload is killing it. They would never have worked well in that car unless it was a 6 cylinder with all the heavy bumpers and such. So the answer was to simply shorten the springs. Removing 2-1/4 turns and flattening 1/2 turn put it about right. Total travel is 6 inches on the shocks so I'll have 2" extension and 4" compression.
OK a bit more progress. The electrical is underway as the harness arrived from iwire. There were some missing sensors and I also needed the O2 sensor harness. Man, they use a lot of wires for O2 sensors. Anyway, a phone call and a trip back to Persad and I got what I needed. So last night I was able to bolt in the ECU, relay/fuse box, route the harness and install the engine harness. It still needs dress up but it's a good start.
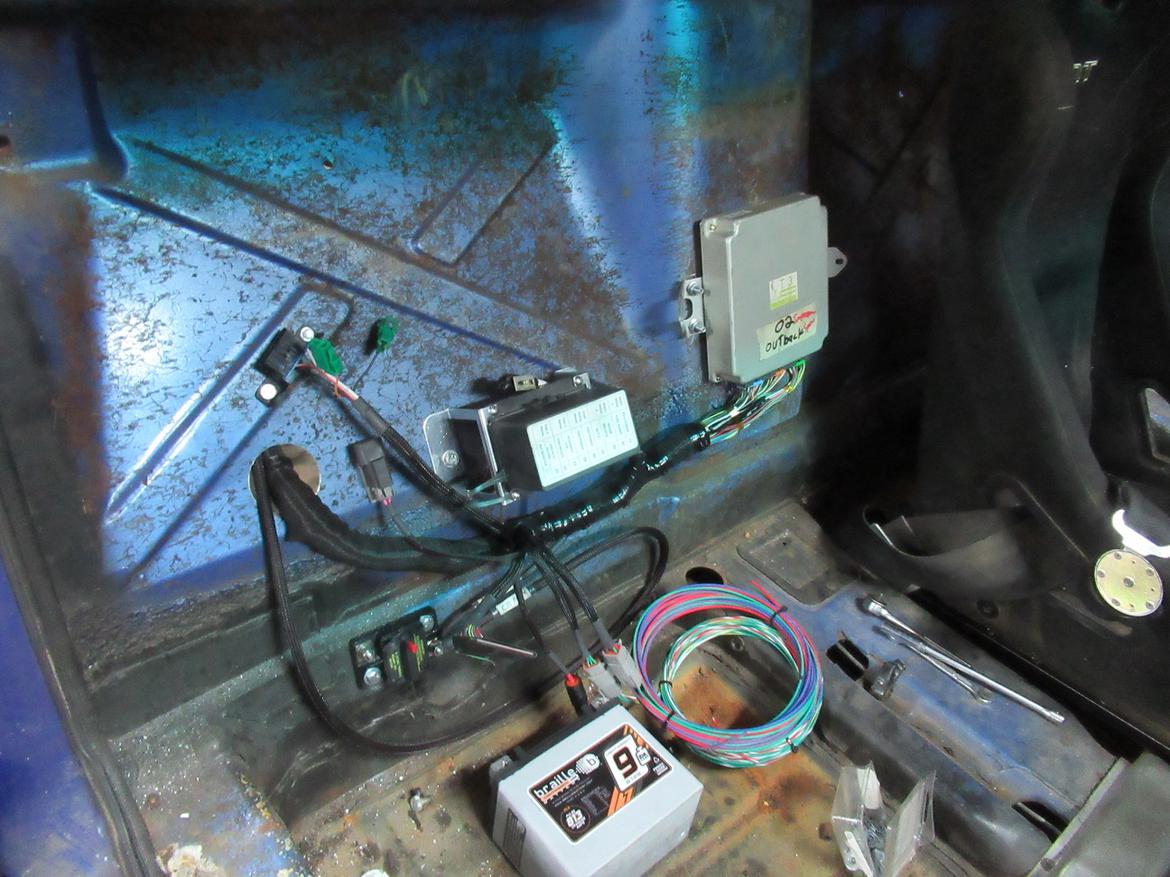
The extra wires in the bundles are for the radiator fans, fuel pump and warning lights.
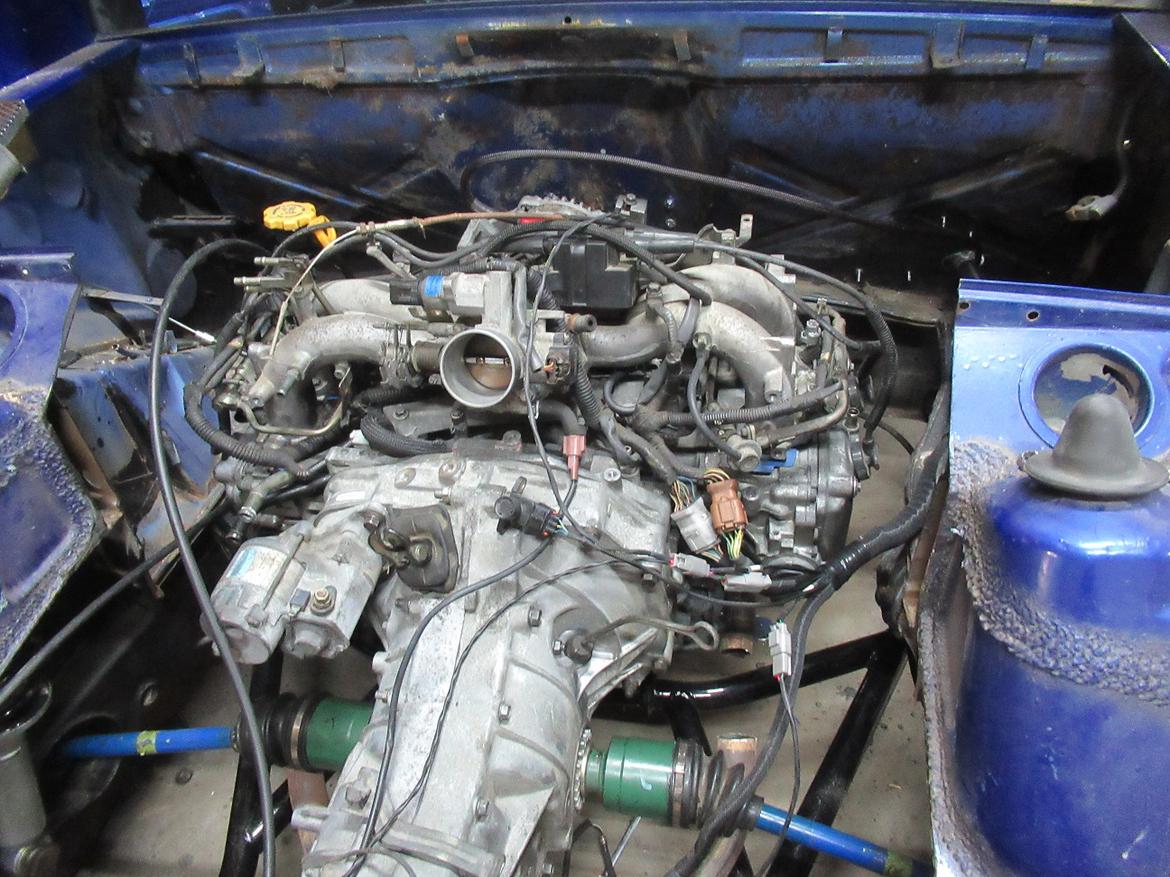
So tie wraps, adel clamps and some protective sleeve and it will look a lot better. I hope to start it this weekend. Fuel pump, fuel lines, battery cables and some oil and I think it will fire up. Then exhaust and cooling are next.
Wow, you're really screaming along on this! At this rate, it seems reasonable that you'd have this ready to go for the June Rallycross National Challenge
This thing really kicks ass. Does it get some structure to tie the rear strut towers together after the engine work is done?