Ready for some more? Well with the weekend here and only one more before race days, it's a mad push to the finish. Thursday night was a washout as I had a conference call (SCCA) that was right in the middle. Friday night however was time to get into what's left of the electrics. A lot of trips to the shop and A.Z. and precious little was accomplished. BUT, today was another story. A set of Moroso switches in a panel and a plastic enclosure from Mcmaster Carr made for a center console with switches for the system. Most are unused yet but I have plans for later. Right now, ignition power and starter are all I need. The feed goes to the I-wire relay box and that feeds the fuel pump, radiator fans, EFI and everything else on the engine.
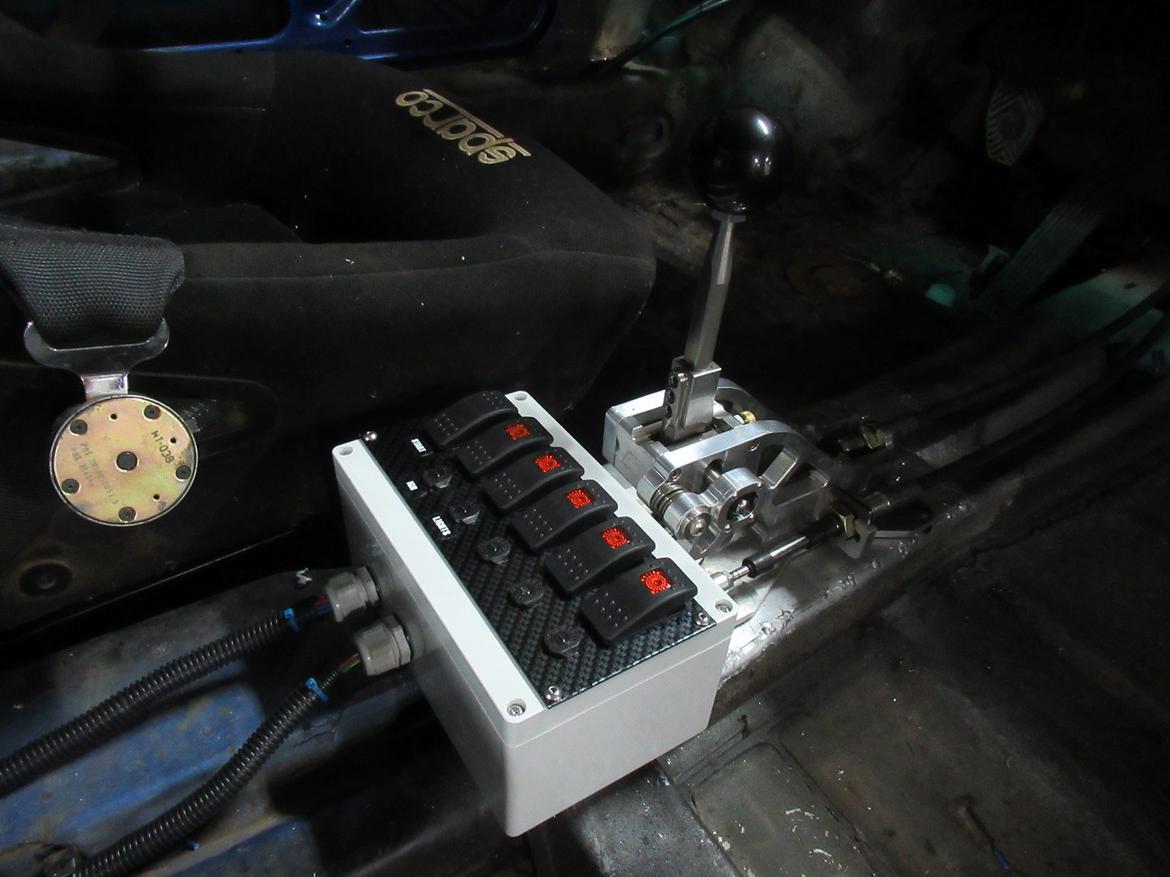
Stopping several times to clean up around the car so I can find tools. Once you waste 20 minutes looking for what you had in your hand 20 seconds ago, it's time to stop, clean and then start again. Looks like the trash pickup right after Christmas.
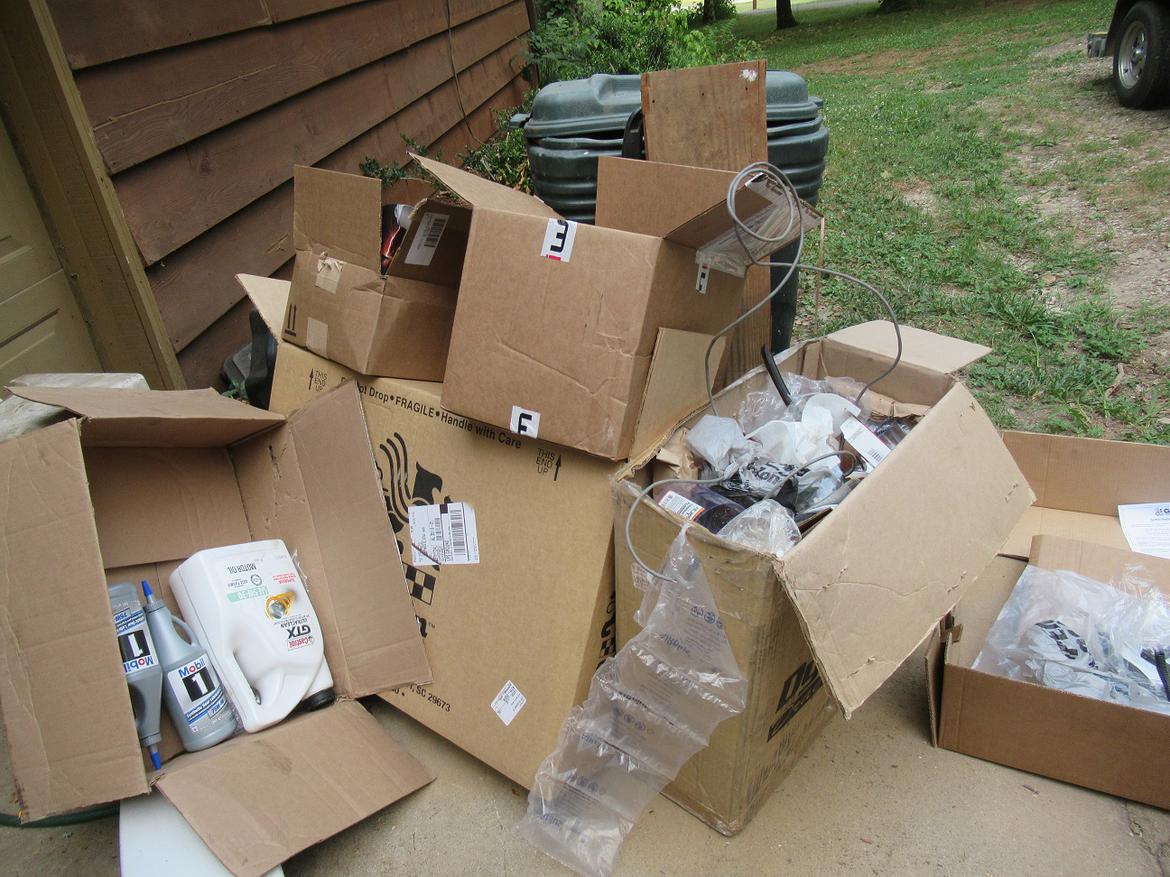
So A big Thanks goes out to Matt Brower for cutting the rust out of the right door, Re welding in new metal and getting it straight and primed. All in just a couple days. He may be doing more on this next week.
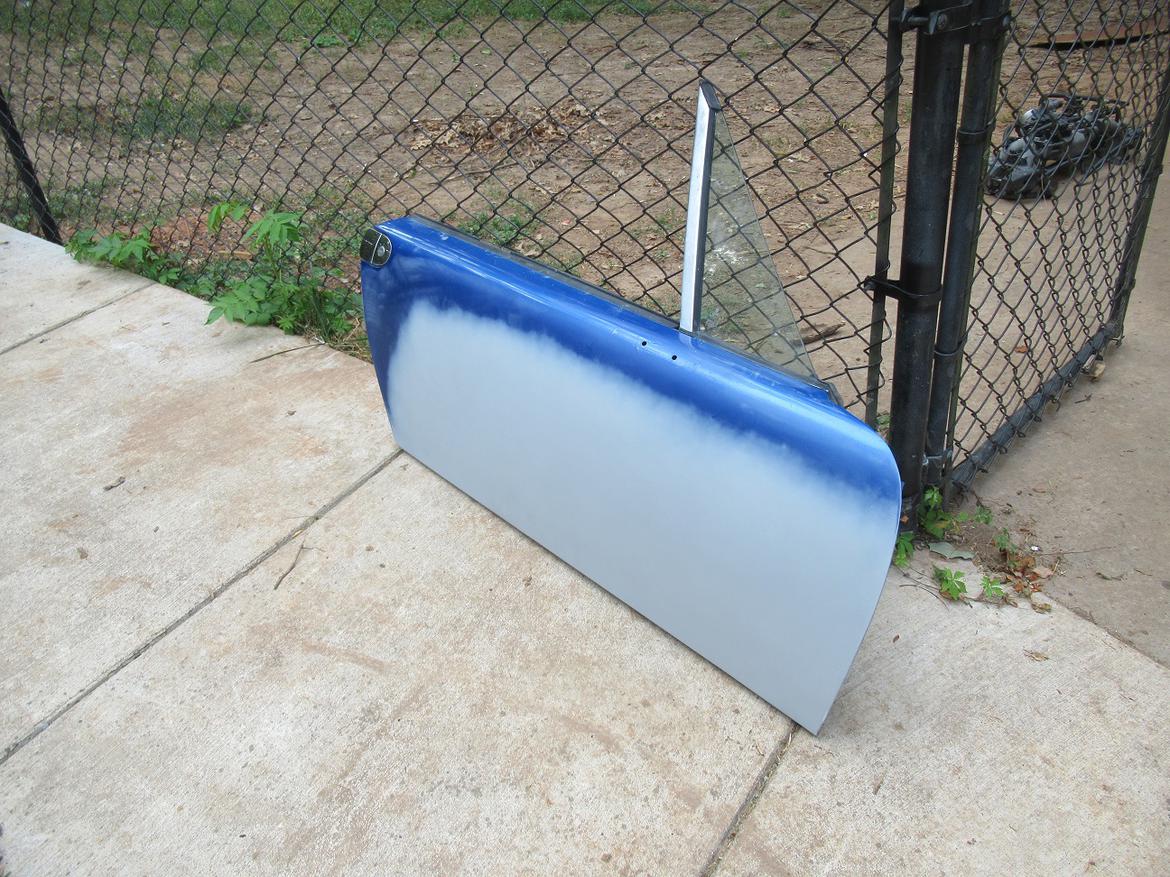
So add oil to the engine and trans, straighten up the wiring a bit, tie things down and connect the fuel pump wires and fuel lines. Check for pressure and leaks. All good. Crank it? Well, yes it turns over but timing seems off and it won't start. Remove and test the crank sensor that came with the motor. Well, TRY to. It was jammed in the engine and would twist but not come out for anything. Pry, pull, cuss. No way. Well it will get a new one anyway cause this ones coming out in pieces before it's done. Yup. Broke the tab, then the whole guts came out leaving the metal cap in the block. I had to crush iy in from the sides and twist the remnants out. It was corroded into the hole. A trip to Huntsville main A.Z. store and I had a new one. Some hole cleanup and anti seize for this puppy. Went in but it made no help. I called Saheed and he's going to go into it Monday. I'll deliver it Sunday evening.
Meanwhile, back at the ranch, keep working. Exhaust right? Well I got a kit of many bends to use as a basis for whatever I'll need.
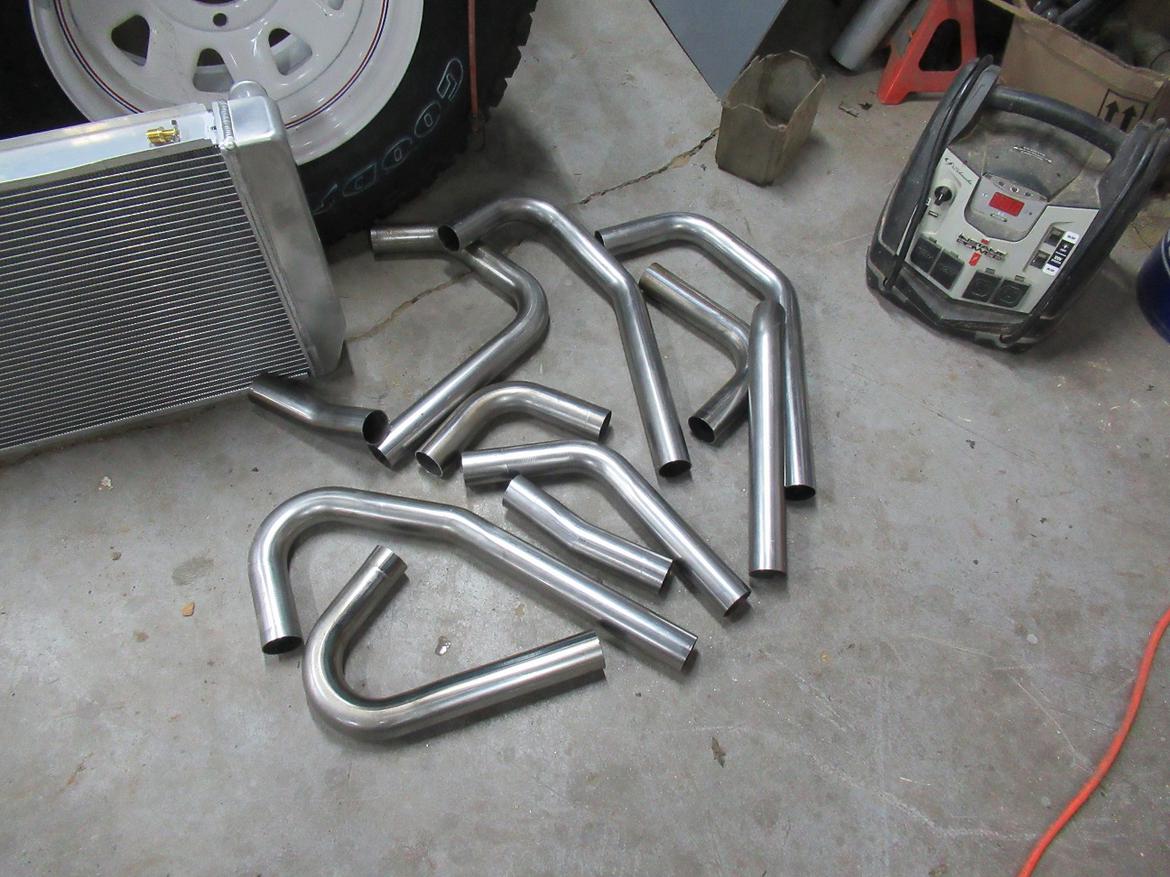
So some work with the trans jack to hold the back half of the Y pipe and then cut, fit and tack it together. Pull it off and weld it up.
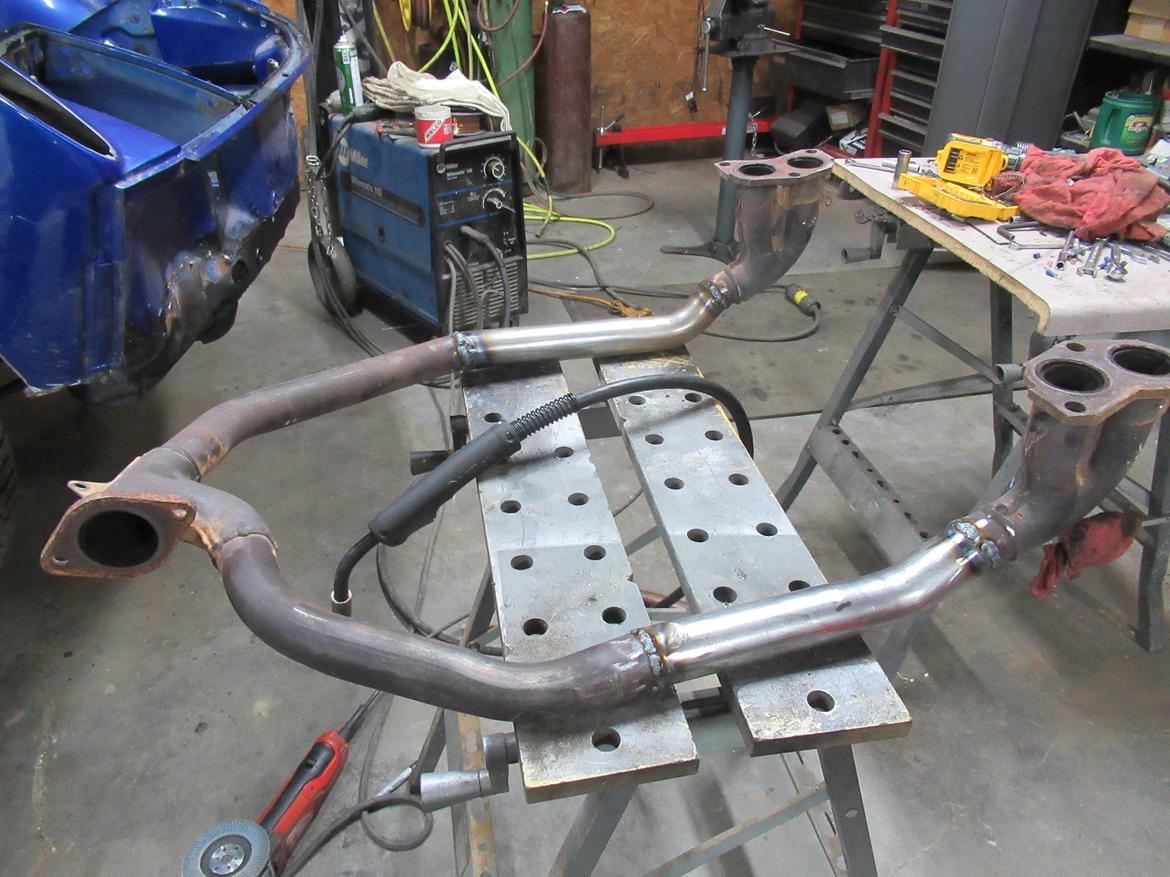
No harm doing the drop-it-on-the -floor test (clumsy) but it stays together so that's a thumbs up. Then add an O2 bung for the sensor. The harness has 2, I-wire said I only need the front one but since I got an extra bung, WTH, put it in there. I can always plug it later but it can't hurt.
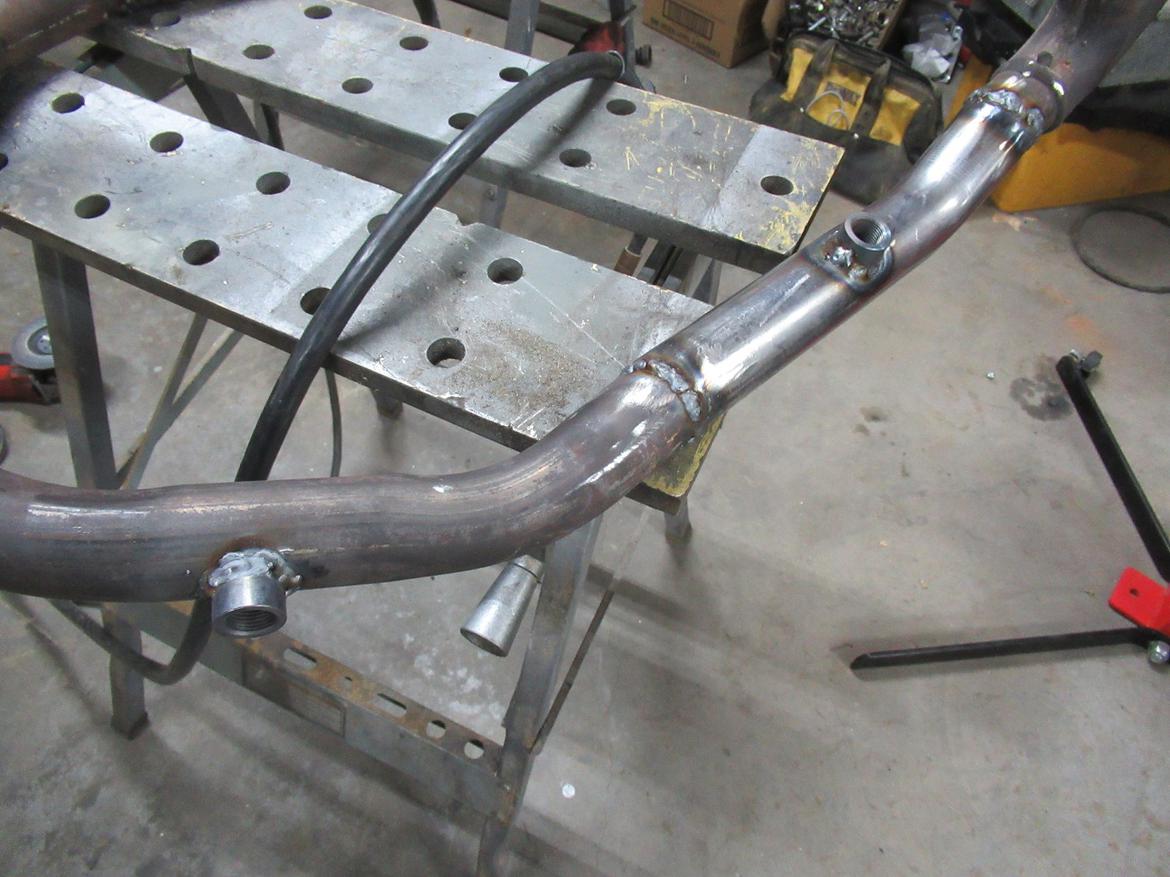
Put it in now for good. A rear hanger for that comes next but first.....
That rear valence in the back is kind of in the way for the right side exhaust planned and it always acts as just a huge mud catcher. It's also going to act as an air dam for the radiator air discharge. Plus it'll look beter gone.
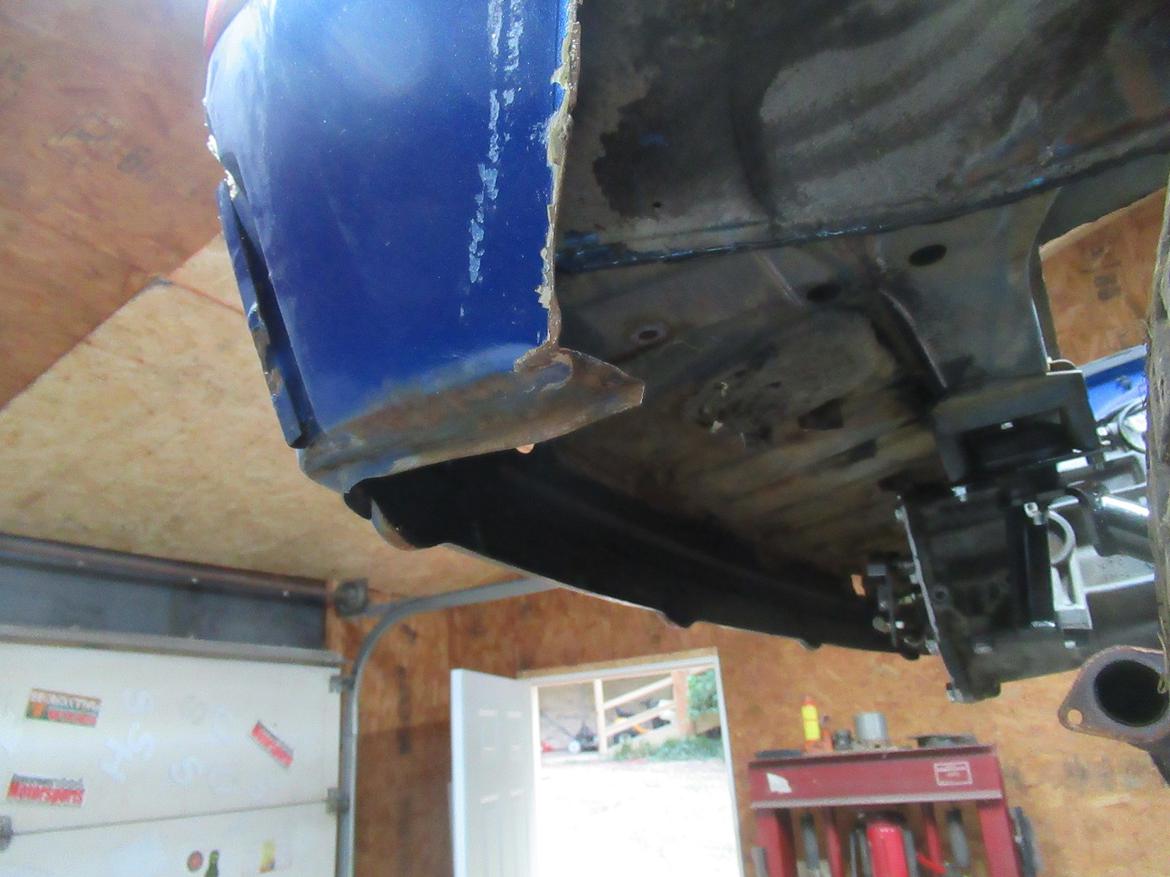
From the back.
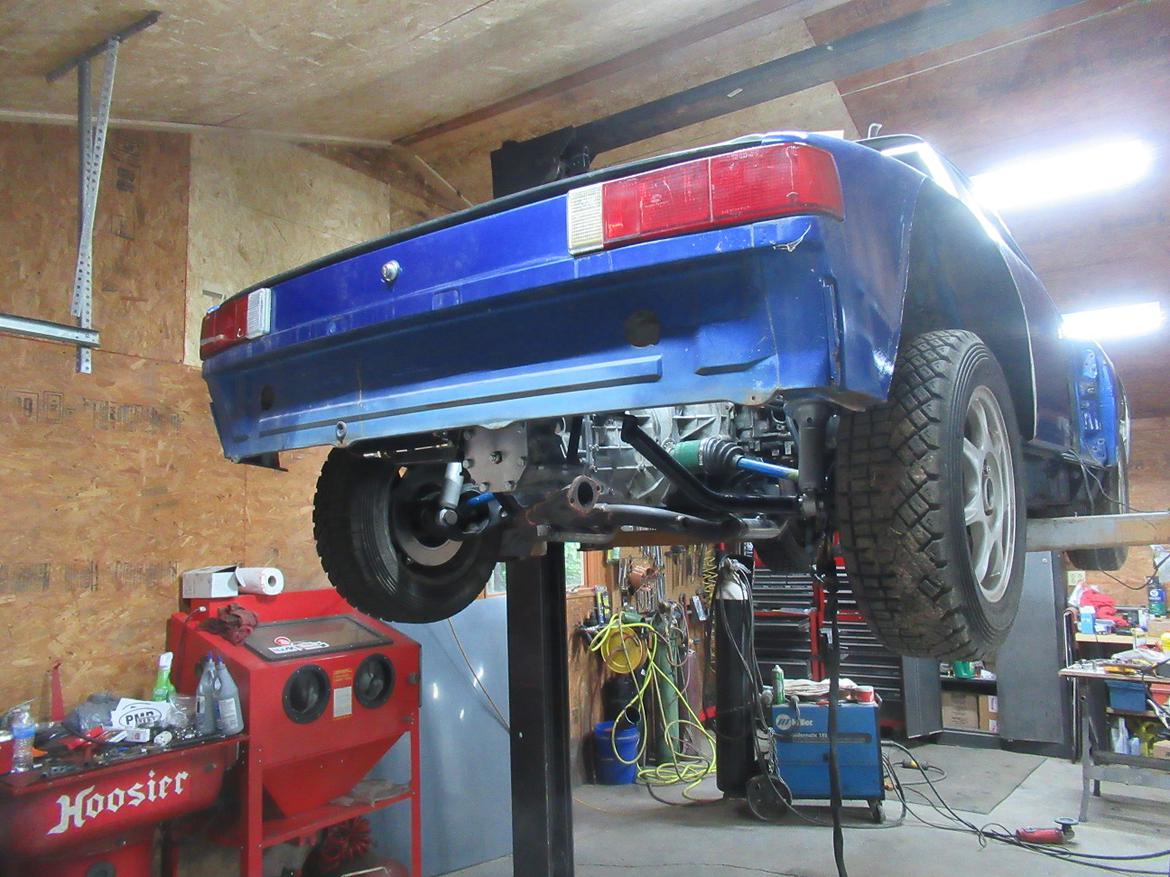
Start about 3/4 inch below the rear floor. Cut out the center and see what we have.
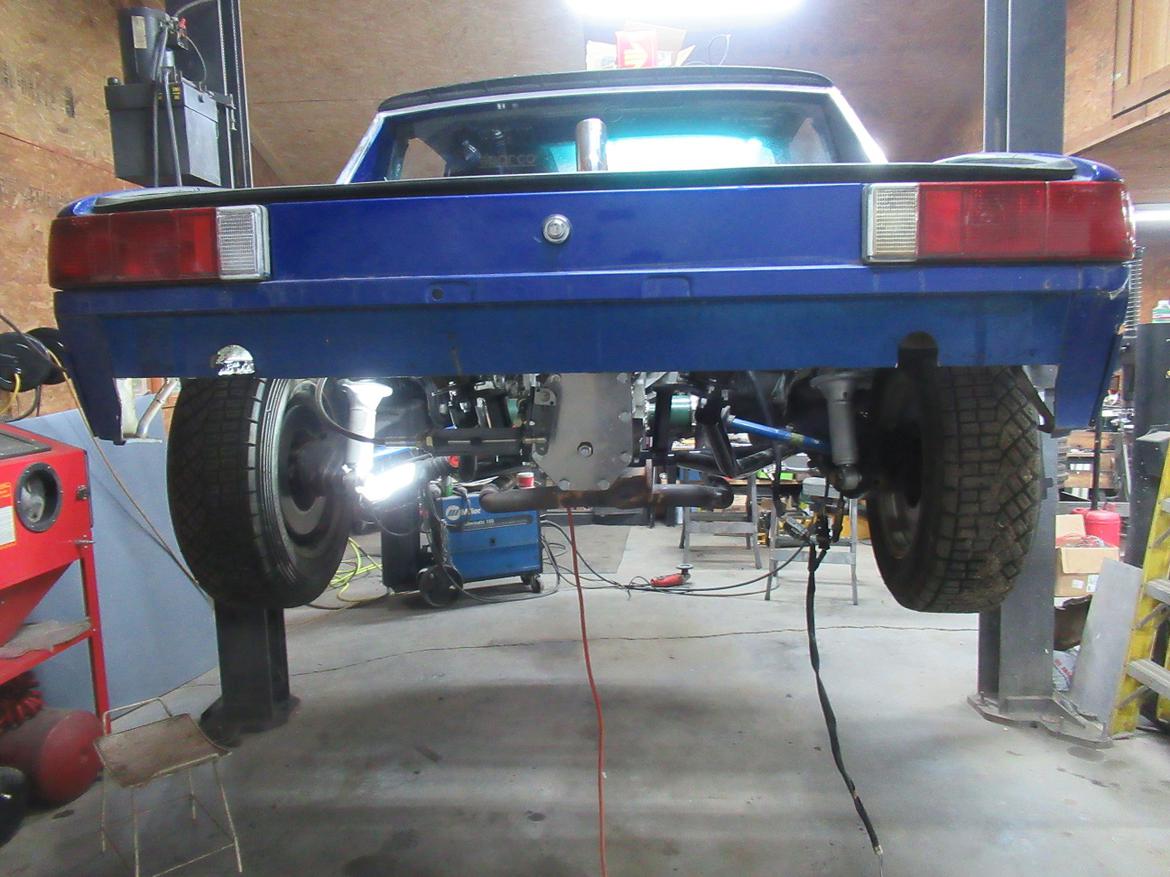
OOOOhhh. I LIKE that. Kind of Can-AM Chaparral look. I still may need to trim around the corners but it's best to cut less and add than to have to replace. Well, next is a run to work to cut out an exhaust flange to mate with the Y pipe. Perhaps first thing in the morning. Then the muffler, hangers and a tip. Oh, and finish installing the O2 sensors and wiring loom.
After that, cooling.