Okay, VFD enclosure is DONE.
One note: I didn't install a fan yet. I left room for one, but I've heard plenty of anecdotes that VFDs don't actually get that warm, and that mine will likely be fine in this large of an enclosure. I'll monitor its temperature and add a fan if it gets warm, but I'd really prefer to not have a chip blower aimed at my electronics.
Sloppy paint job with leftover paint after I was done booger welding:
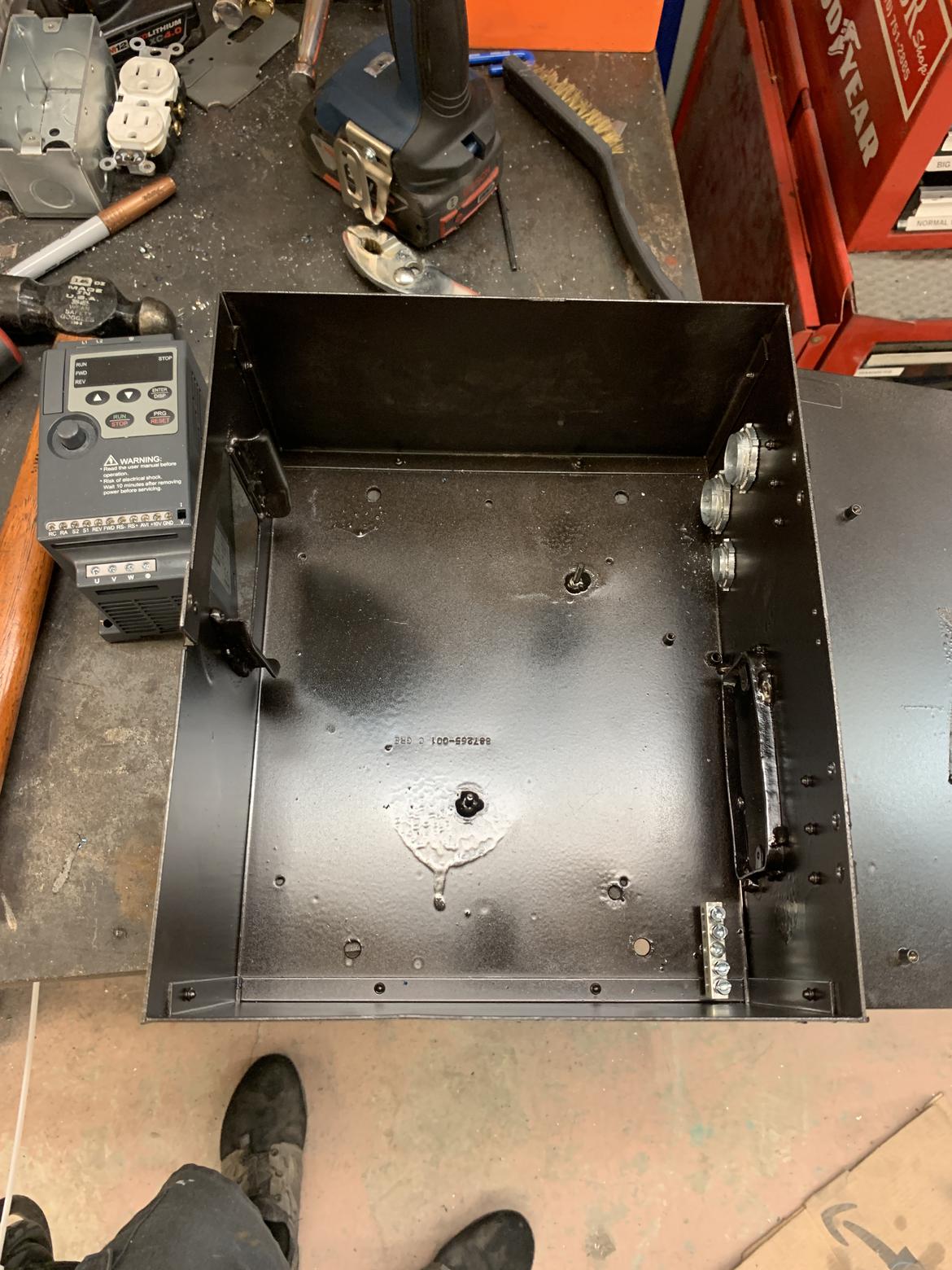
Add a little wiring...
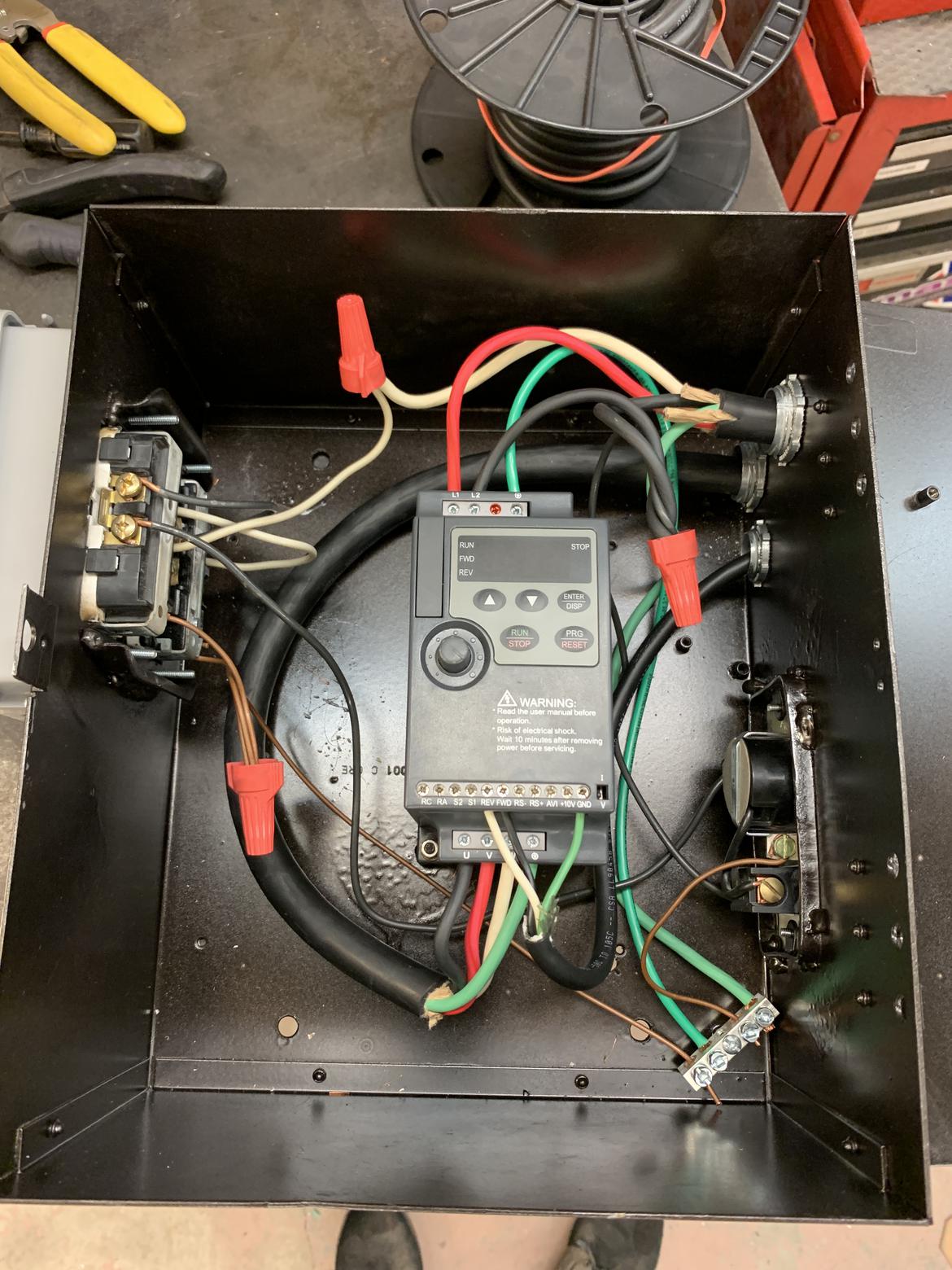
And done!
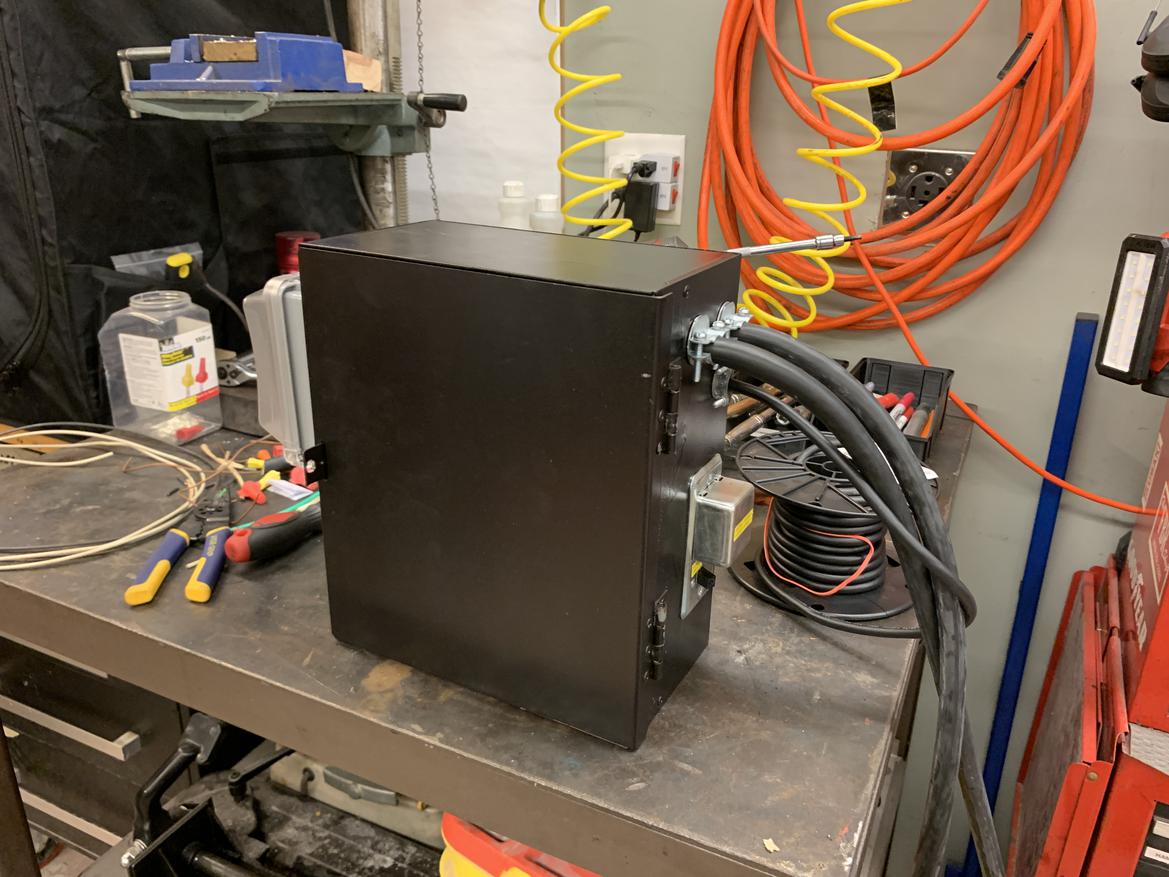
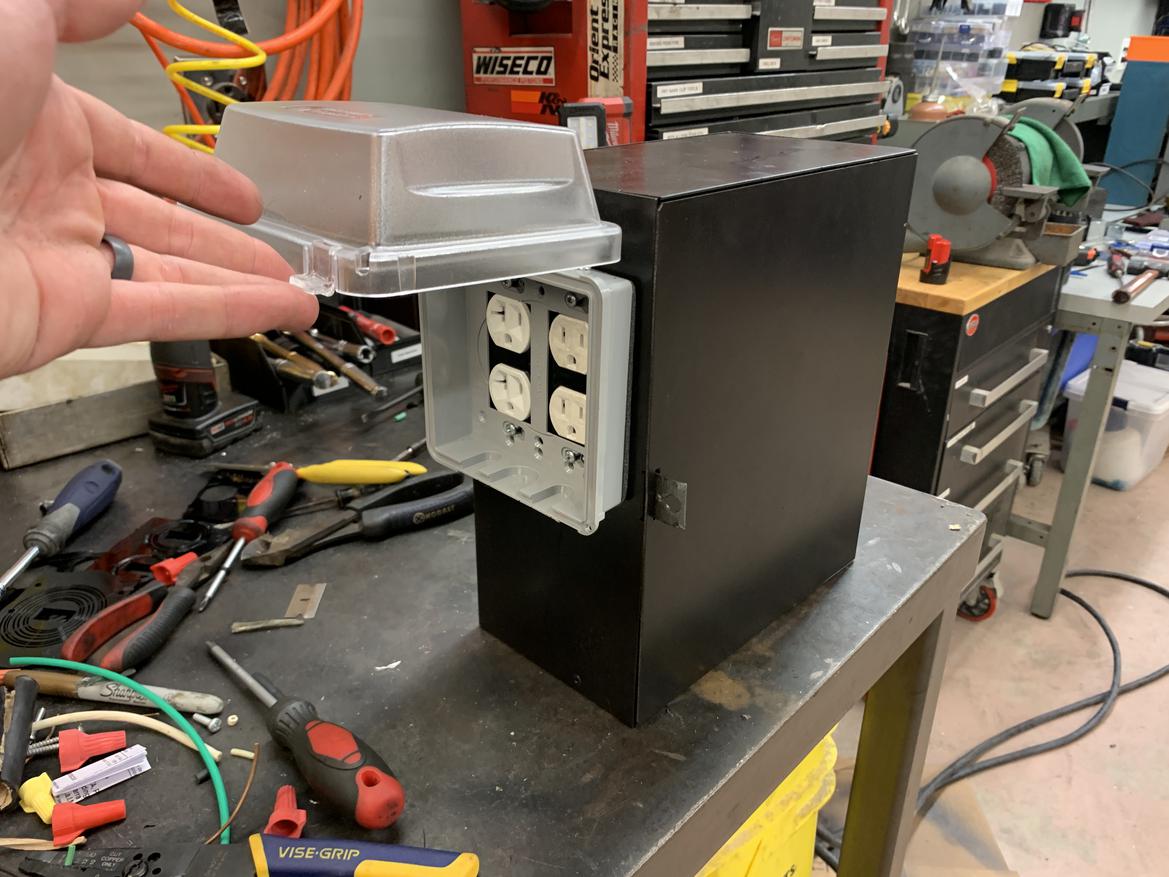
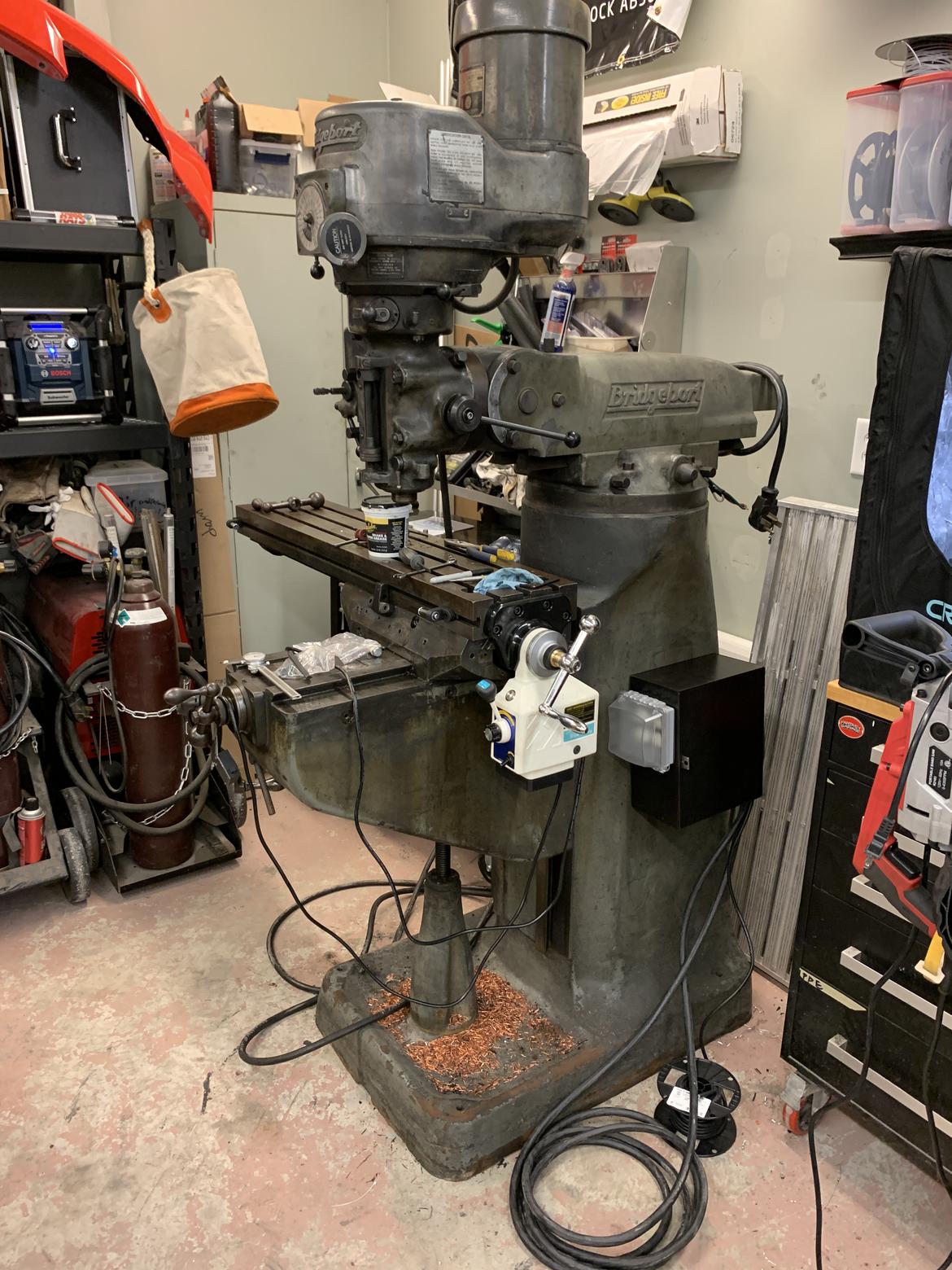
I called it a night at this point. Tomorrow if all goes well I'll put the plug on, wire the motor and wire the low-voltage control circuit.
Okay, the wiring is officially done!
I extended the ram and rotated the head 90 degrees to put the wiring entrance as far away from the VFD enclosure as it should ever be:
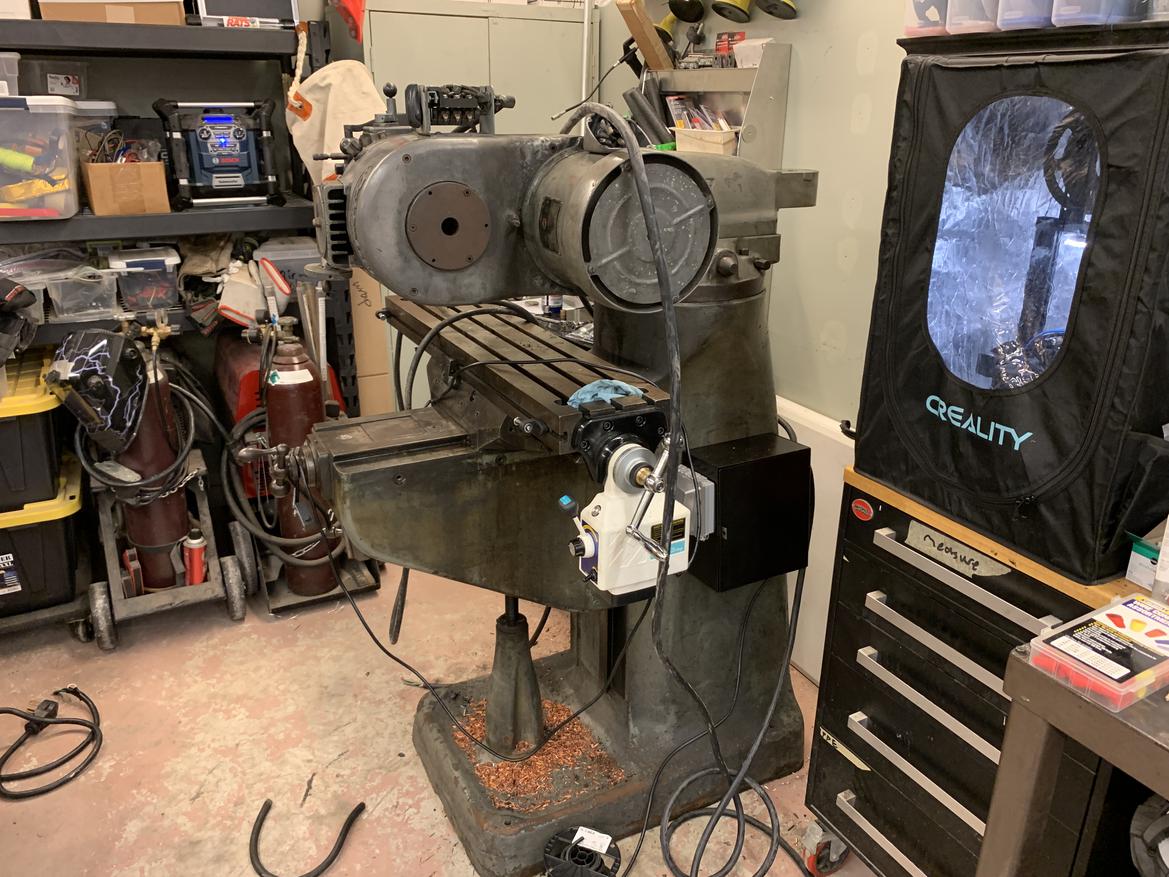
Then I cut the power and signal cables to length and hooked them up.
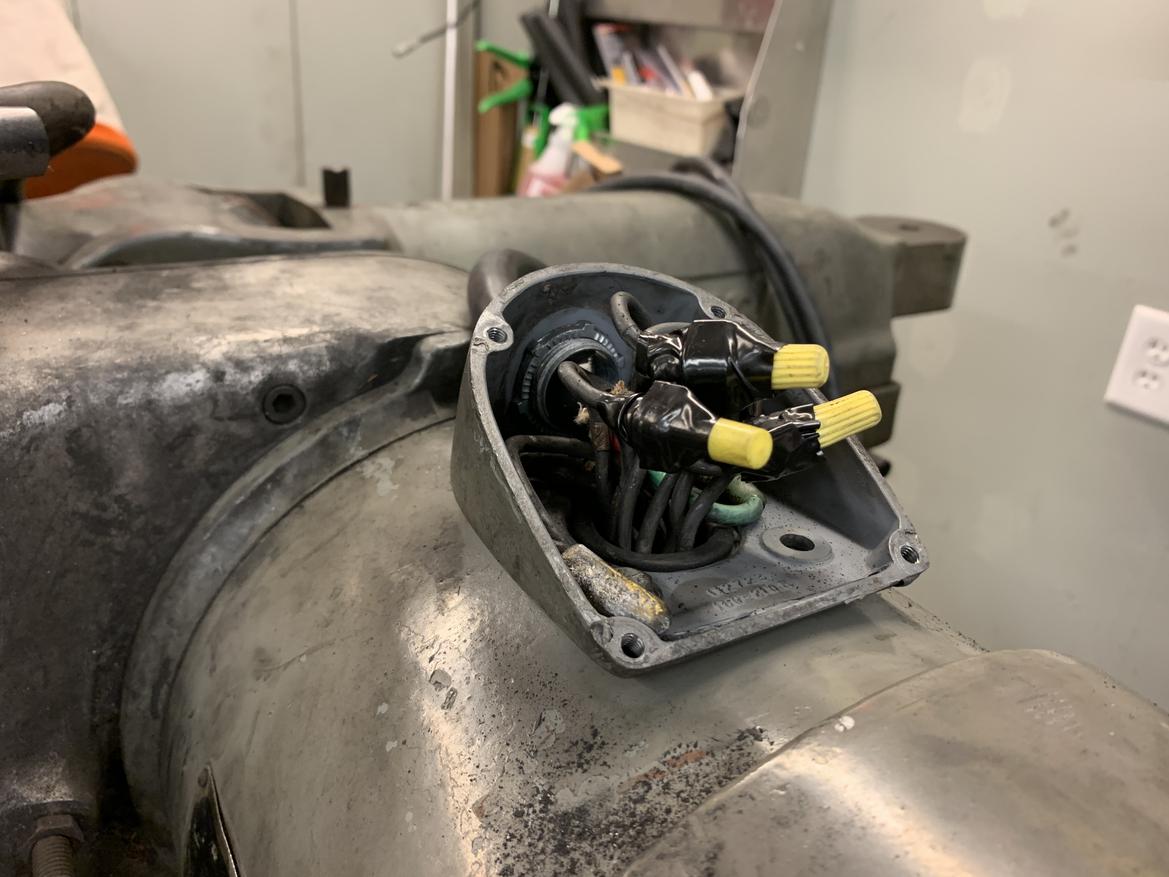
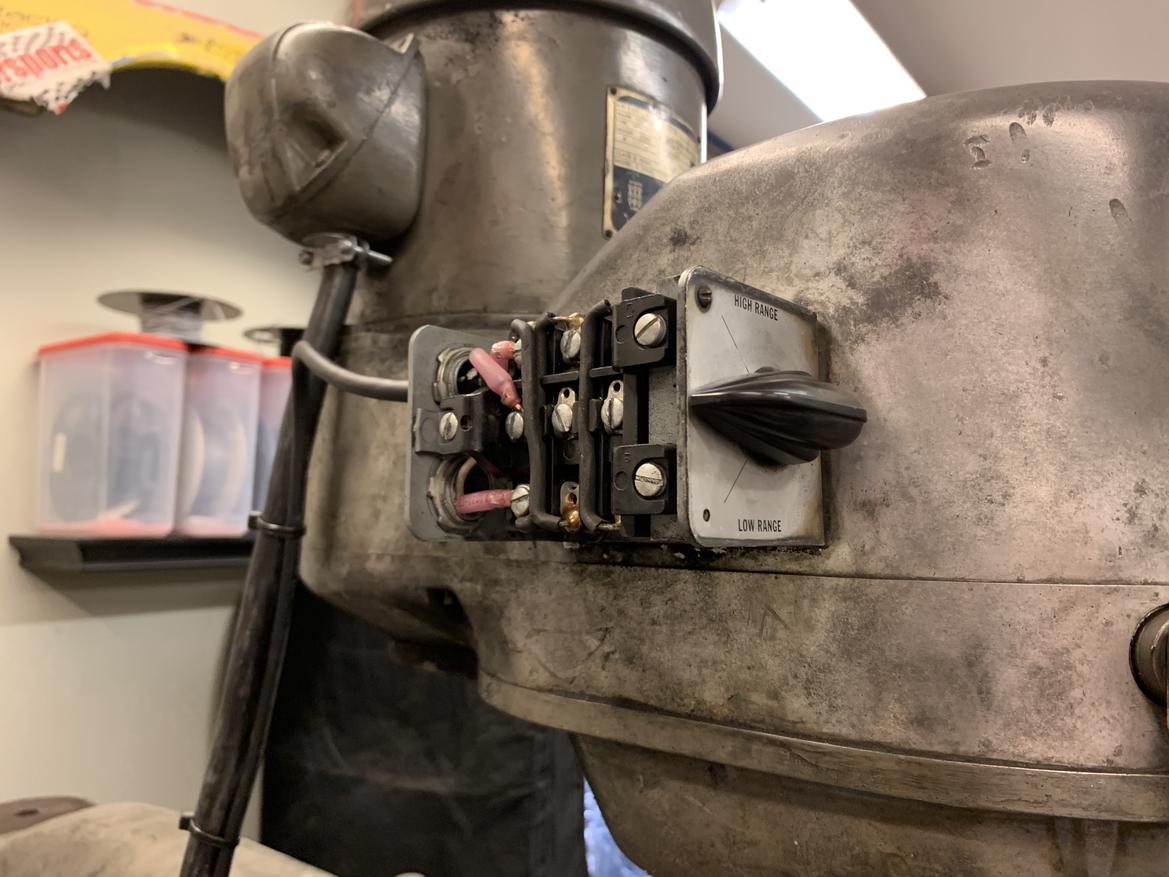
I'm really glad I was able to keep the factory on-off switch, as it's super cool and super intuitive. It now controls on/off/forward/reverse.
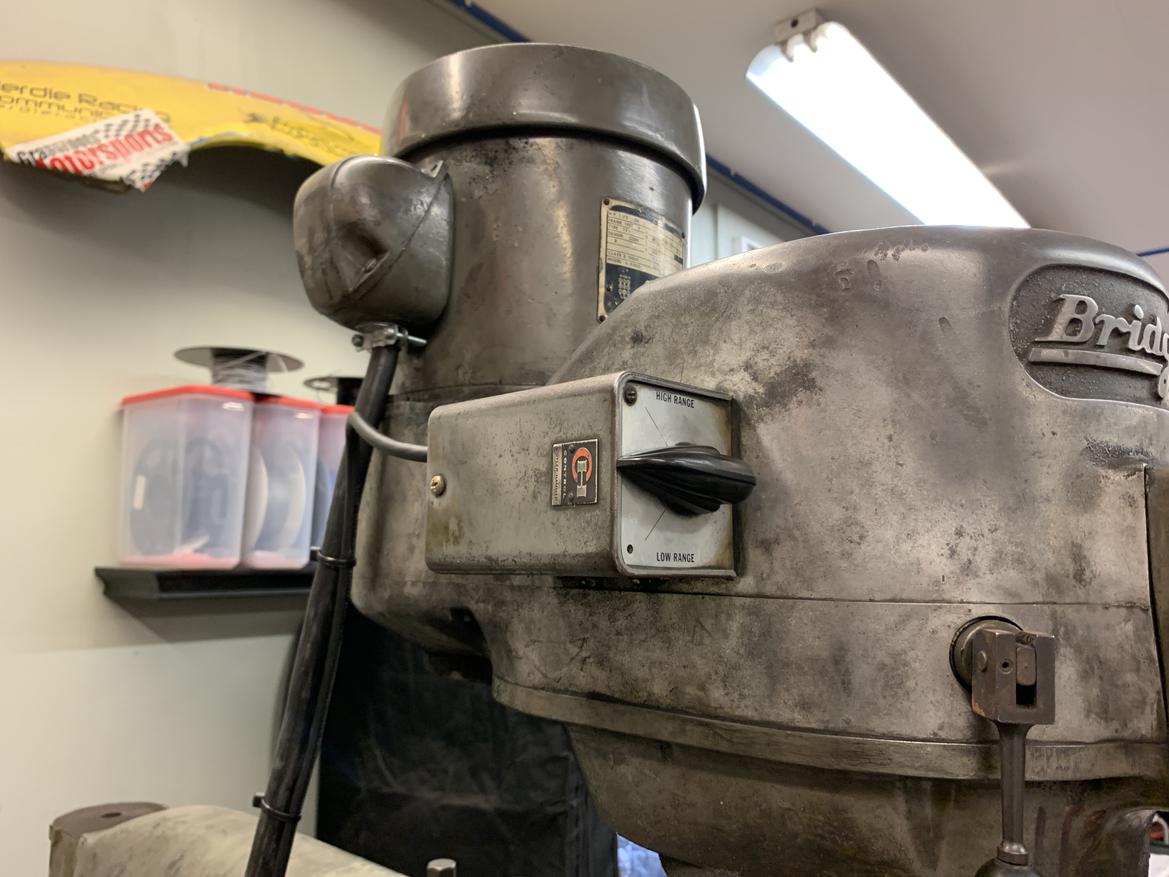
Ta-dah!
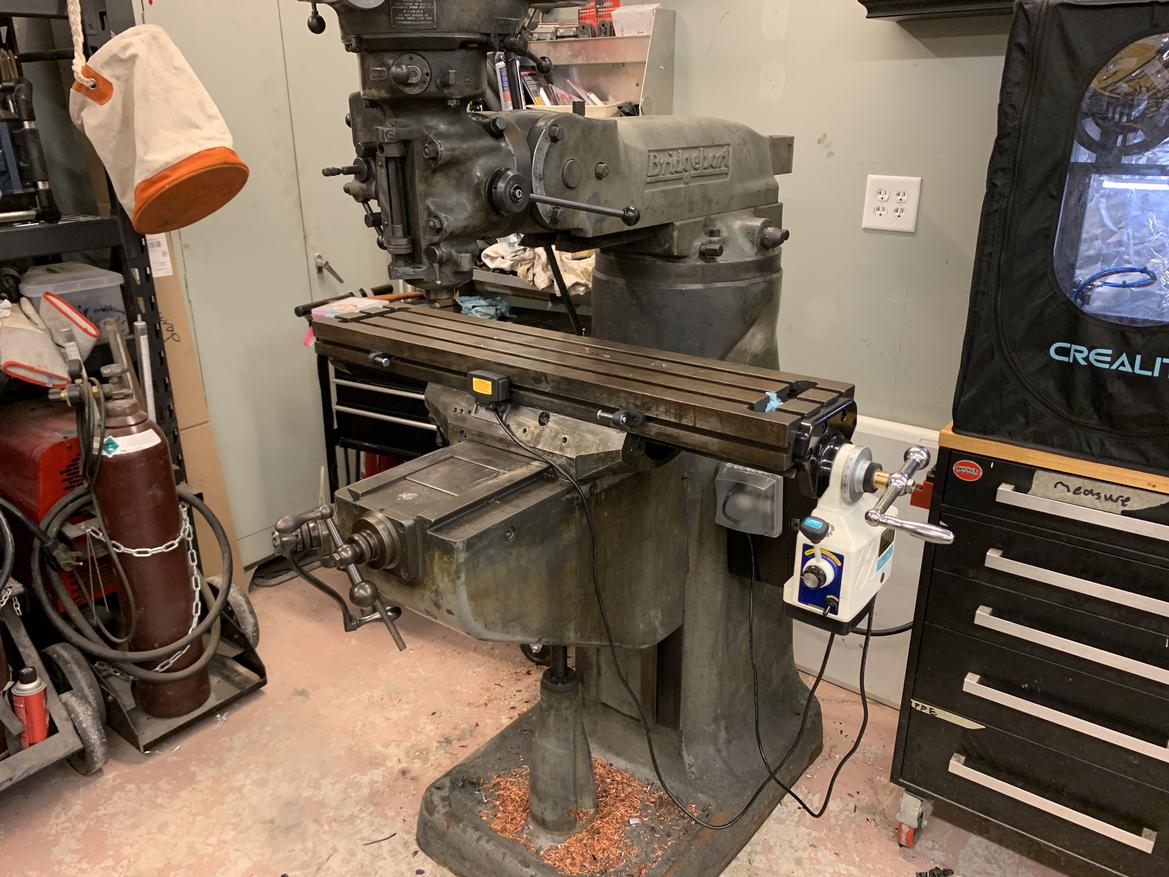
Super cool seeing this thing come back to life
If you need to add a cooling fan, standard industrial practice is the fan pulling air through a filtered vent port across the electrical/electronics not blowing chips in to the cabinet.
Tom Suddard said:
I haven't made much progress in the past few days, but I can still post a quick update:
Since I need to mill the wrench flats onto the bolt I'm making, I've started building an enclosure for the mill's VFD. Why not just leave it exposed? Simple: 230V power and hands/chips/coolant don't mix. I need to put the VFD in an enclosure that will protect it from metal shavings and oil as I'm running the mill.
First step: Go to Skycraft Surplus. This place is an institution for people who build stuff, and well worth the hour drive to Winter Park (we needed to go to Ikea anyway). They don't have military surplus, rather it's all surplus electronics parts and widgets and such. Need a 380V-5V transformer? They have it. 50 lb. block of 7075 aluminum? Those are towards the back of the store. Three NASA panel switches in various colors? Check the used switch aisle, probably next to the emergency stop parts. And feel free to stop by the test bench, where you can poke and prod your finds with an adjustable power supply to make sure they're working on your way out of the store.
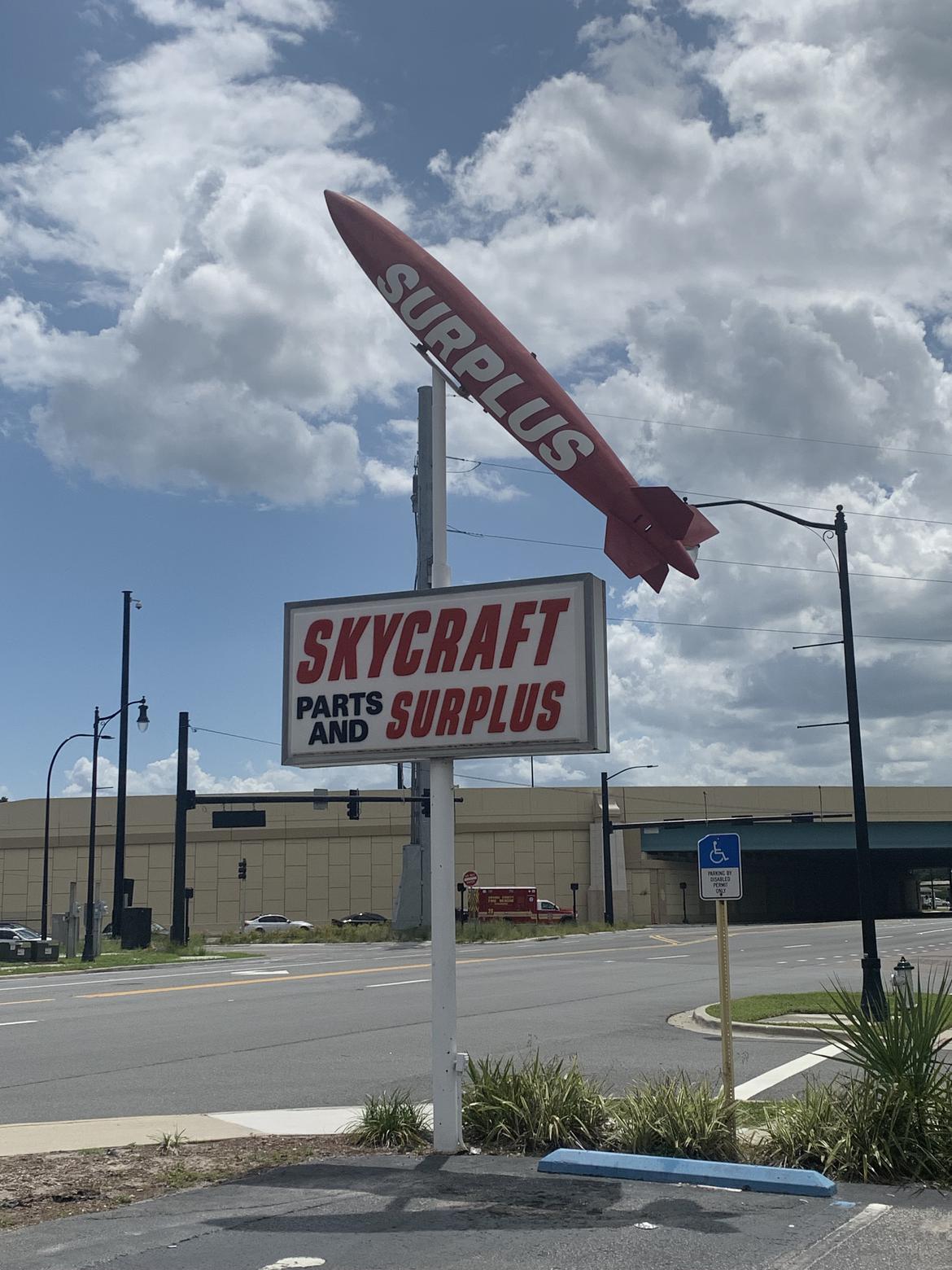
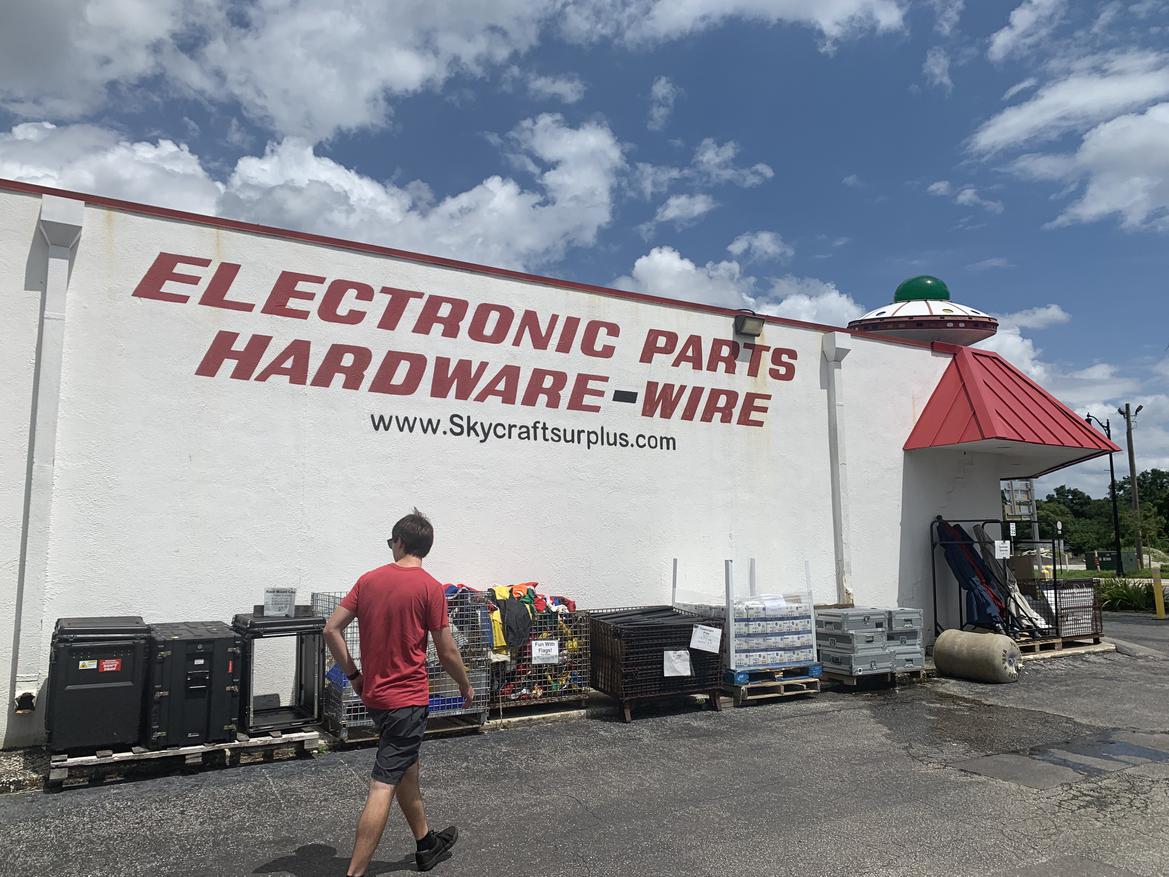
Success! Nicole snapped this photo of me choosing fans for an old control box I found. 
Skycraft FTW !!!
I moved to Orlando from Miami in 1989 to finish school, and quickly discovered Skycraft.
Sometimes I would just go in and wander every aisle.
The grease (actually oil) fittings got here, which meant I could lubricate the ways and then mill the flats on the funny nut I'm making for the X axis. So close to finished!
First, though, I needed an oil gun. I ordered one from ICAI, but it was plastic and immediately shattered when it fell off the bench (oops). $20 wasted.
Instead, I bought a cheap grease gun and soldered the end closed. Success! (And it doesn't leak).
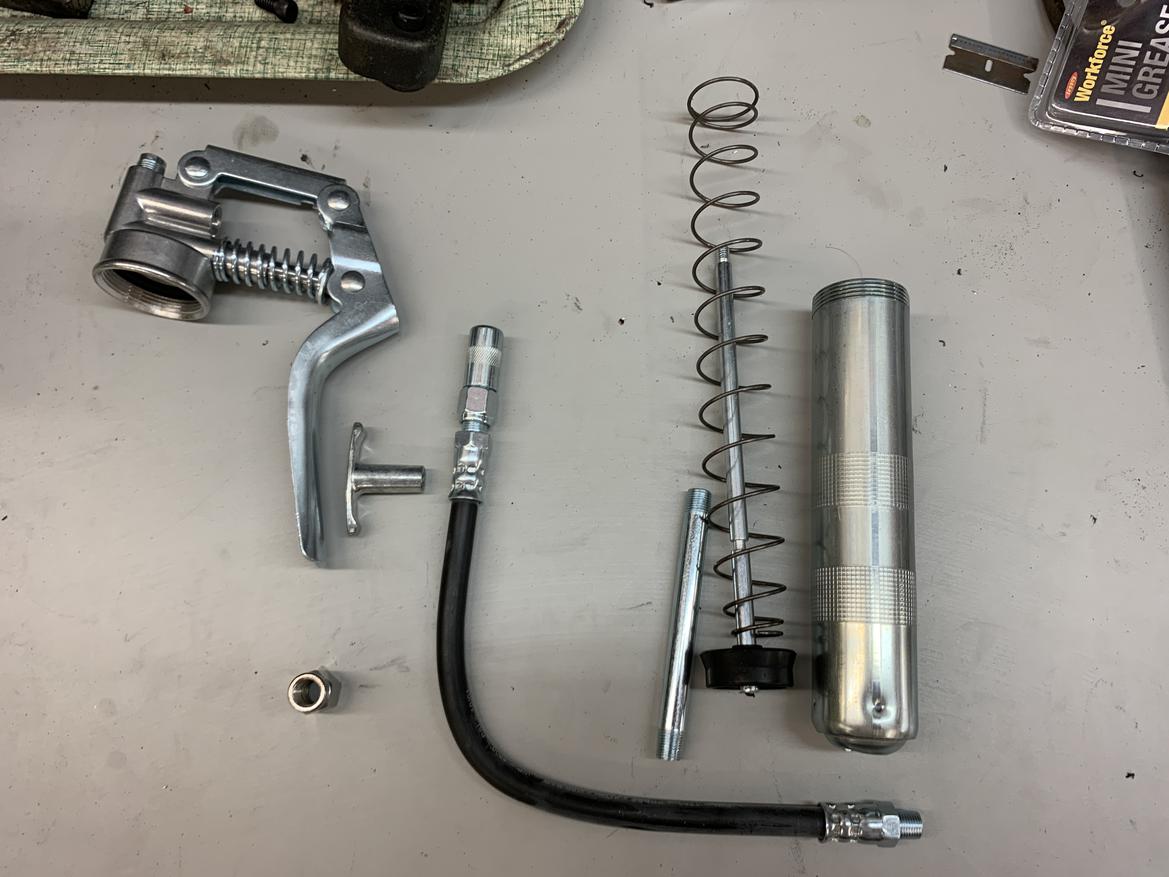
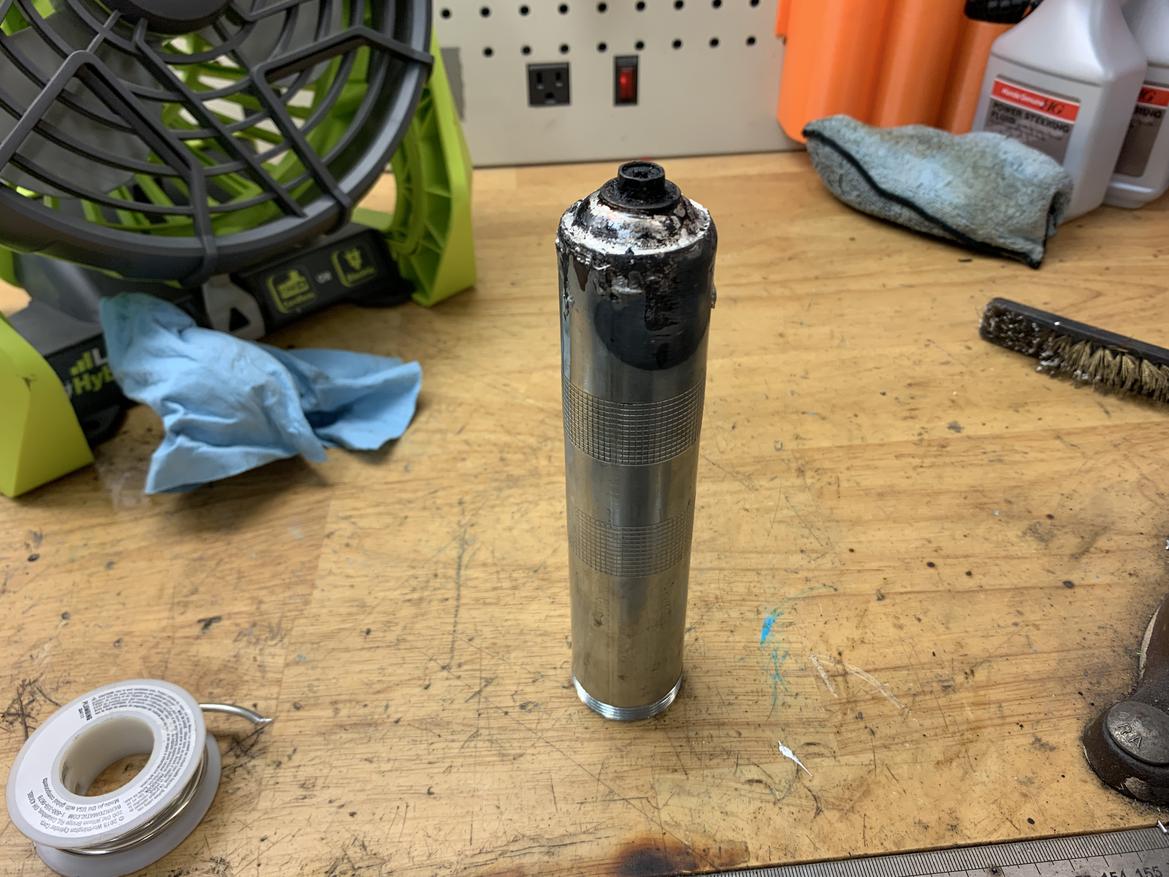
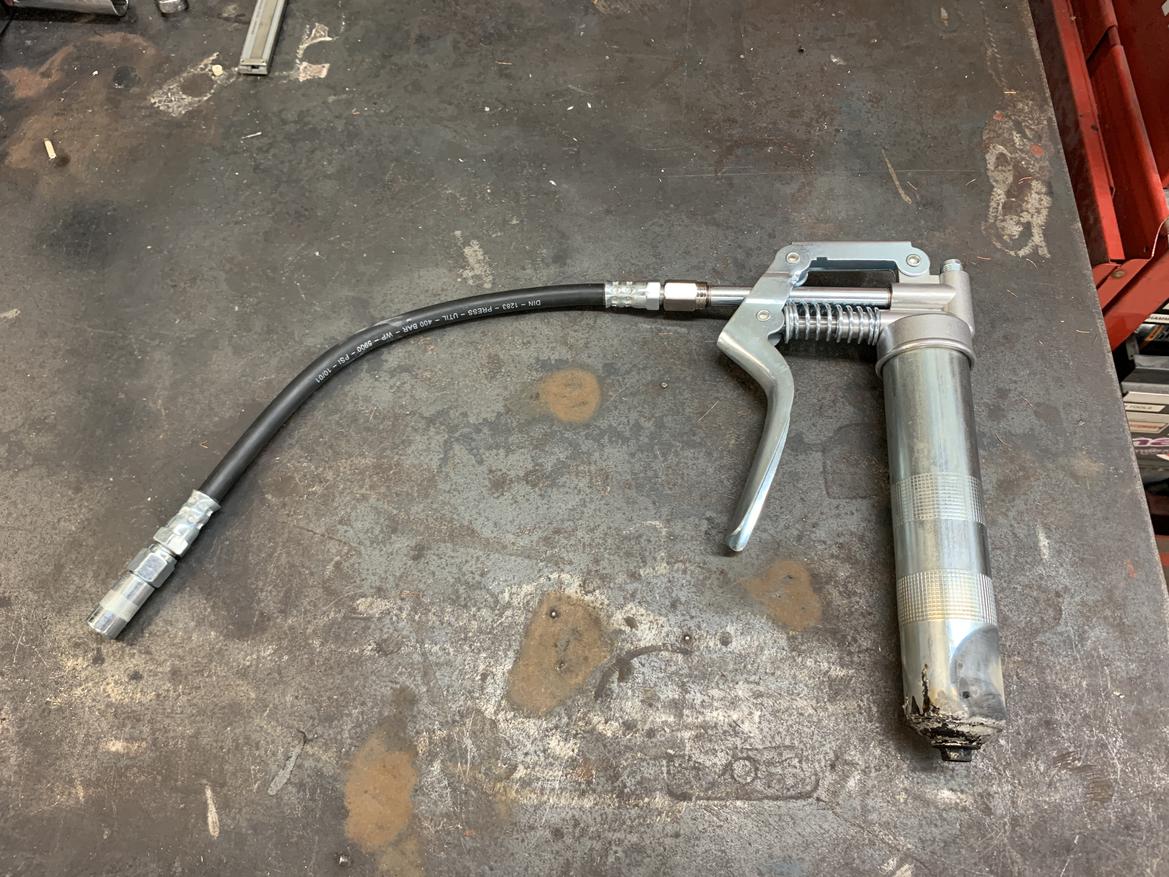
It was finally time to mill stuff!
Wait, the drawbar won't thread into the collet far enough to tighten down?!?!?!
Back to the lathe... Google told me I'm missing the spacer/washer that goes between the drawbar and the spindle.
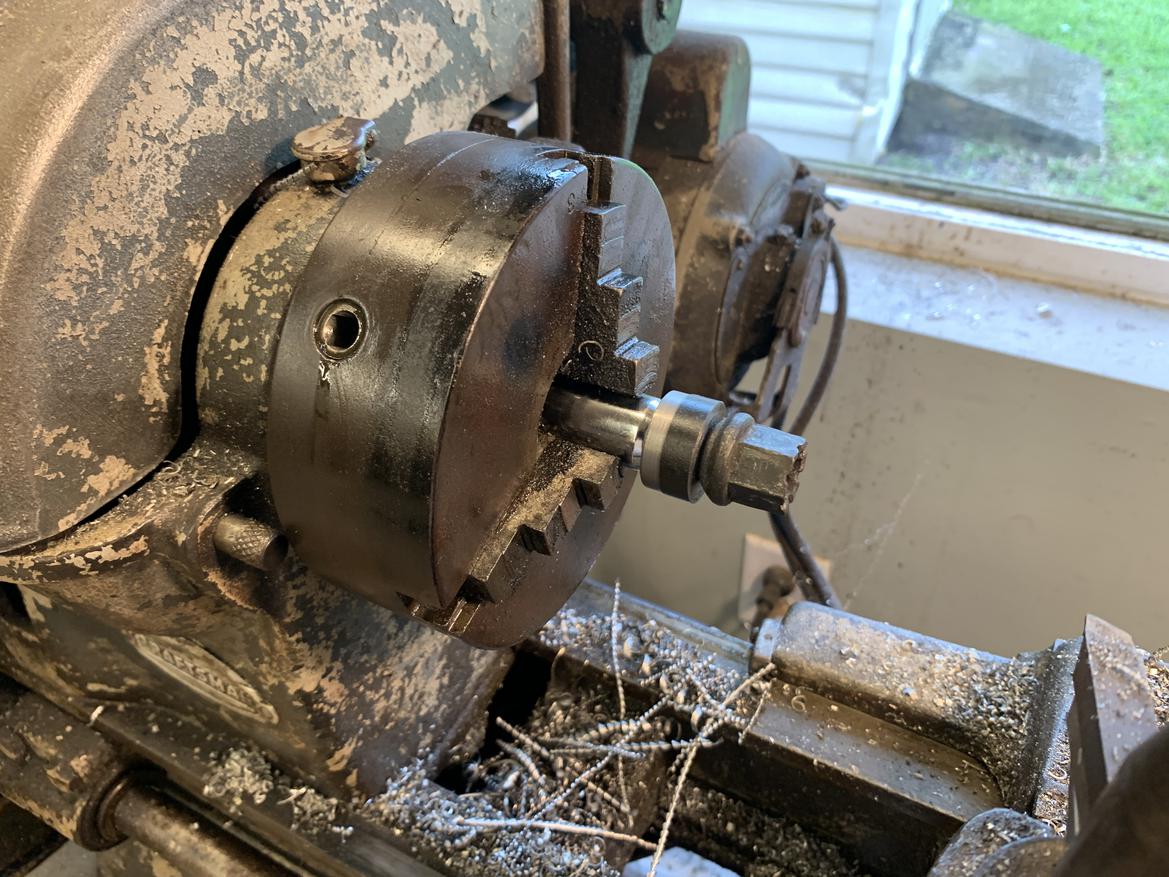
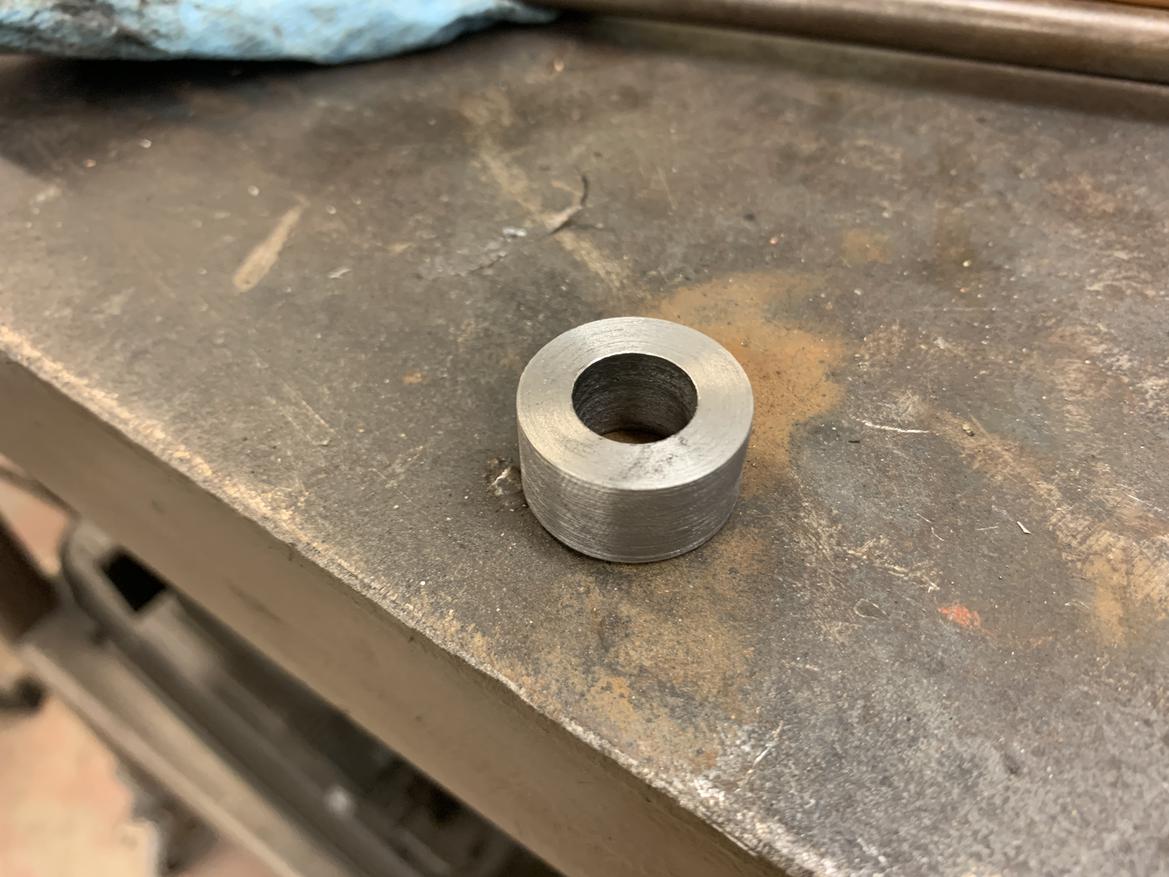
Okay, now we can mill!! I quickly/sloppily squared the machine and vise, then went to work making my round part into a 3/4" flanged nut.
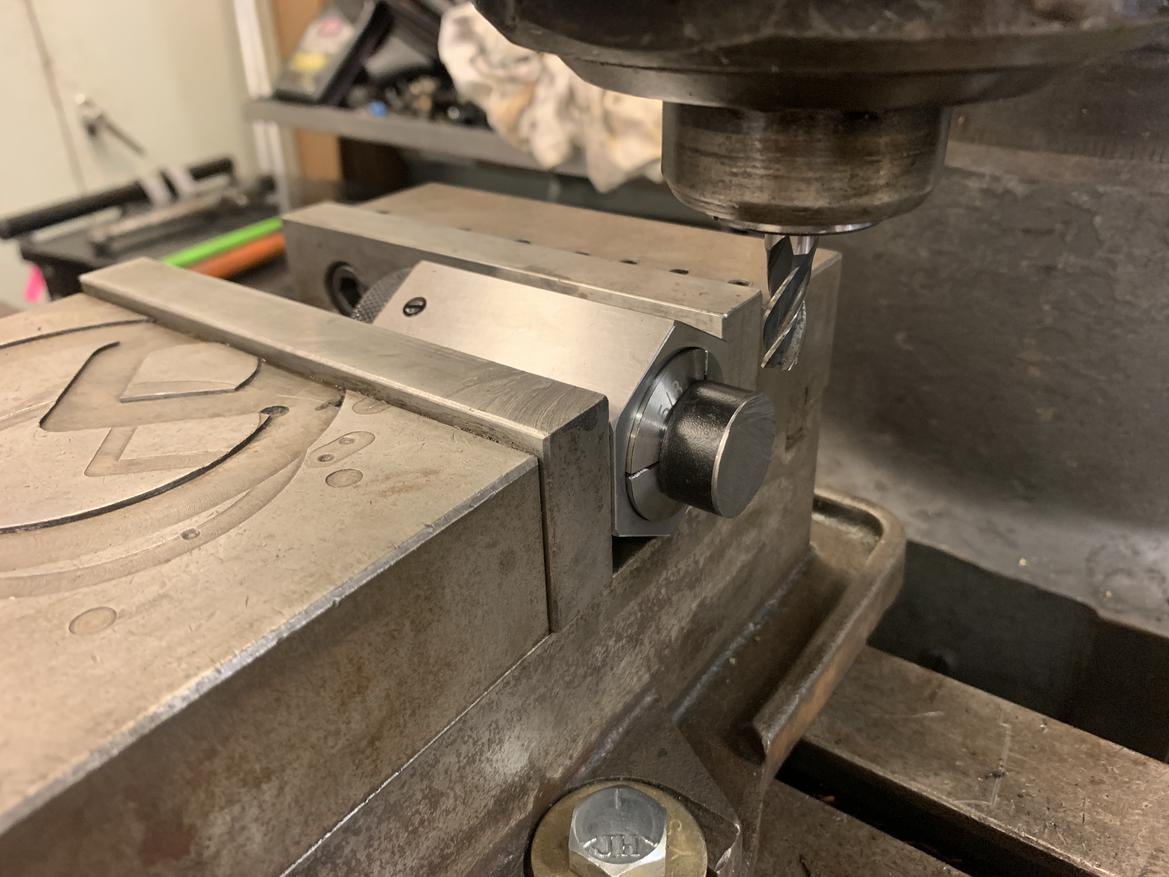
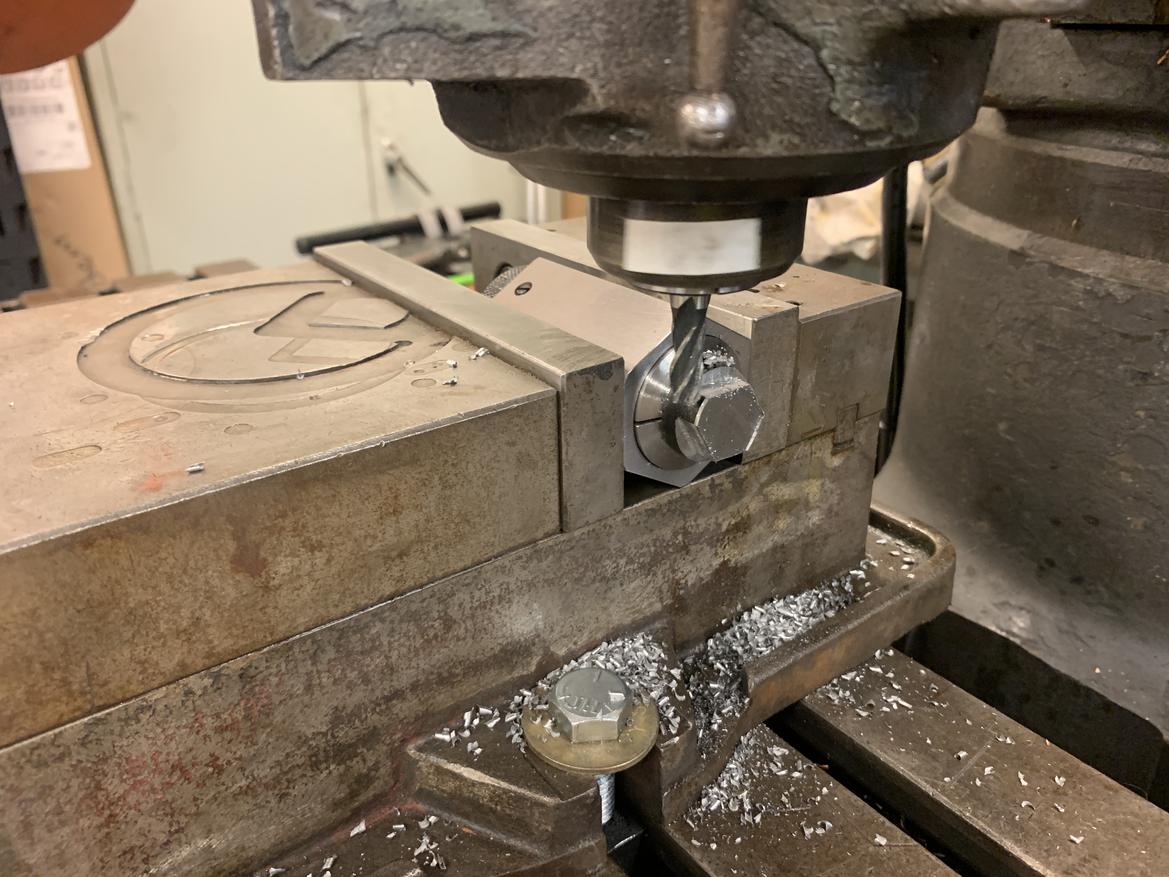
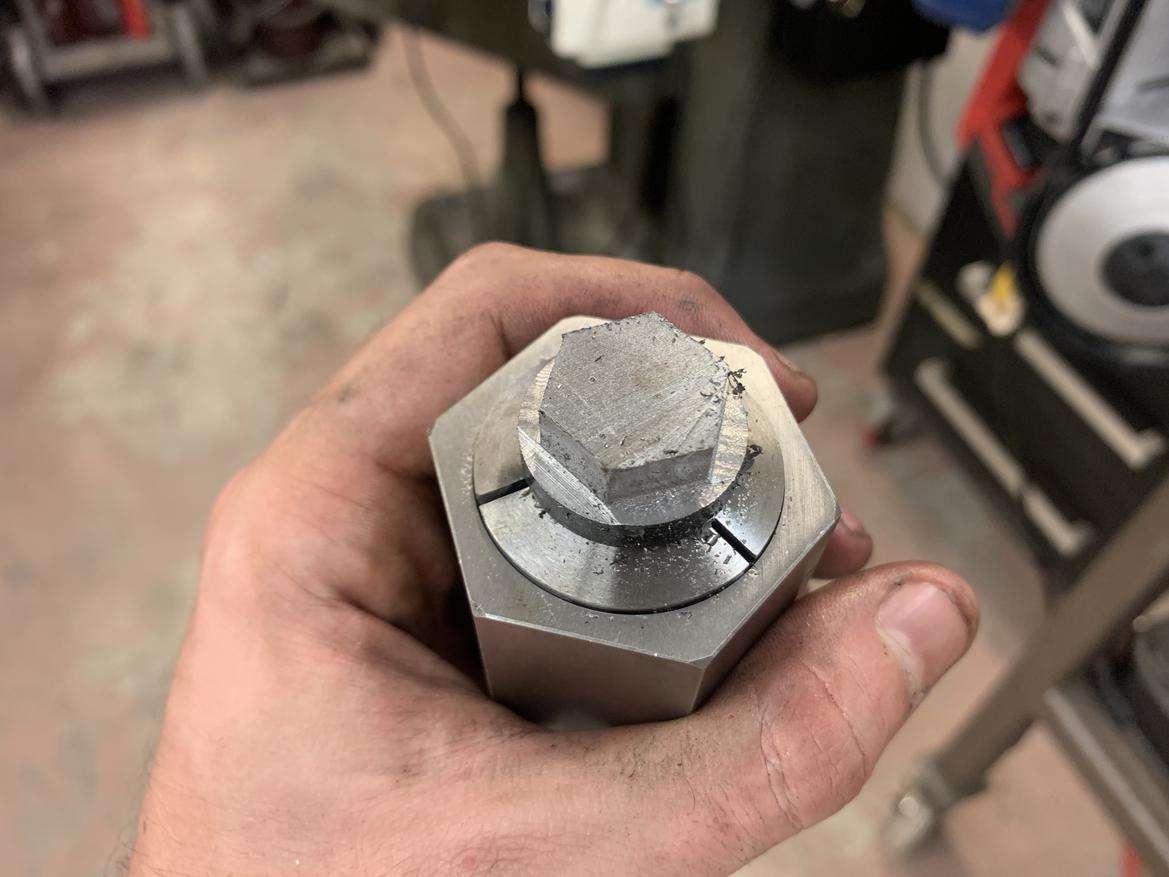
Aaaaaaaaand TIME! It took me a month, but I've made a thing with my Bridgeport mill!
Great job on the vfd enclosure.
Woohoo, chips!
Mr_Asa
PowerDork
8/7/21 8:41 p.m.
That's how you make a hex on a mill. Nice.
ShawnG
UltimaDork
8/7/21 10:18 p.m.
Mr_Asa said:
That's how you make a hex on a mill. Nice.
Rotary table on it's side with a chuck and indexing plates does the trick too.
CHIIIIIPS!
Expressed as units of initial purchase price, what did it take to get to this point?
Here is a VIDEO of us moving a mill out of an old garage and up a series of steps. Hilarious.
Hey Tom, just a thought here from an ex-machinist, and this may have been suggested already (haven't read the whole thread thru), but you may want to, if you can, turn the mill slightly on an angle. This would allow you to work on longer pieces without taking up more footprint. In our machine shop, all machinery was angled in relation to the walls to allow this.
Keith Tanner said:
CHIIIIIPS!
Expressed as units of initial purchase price, what did it take to get to this point?
I need to go back and total everything up, but right now I think I'm somewhere around $500 in tooling and $1000 in machine transport/repair/upgrade costs.
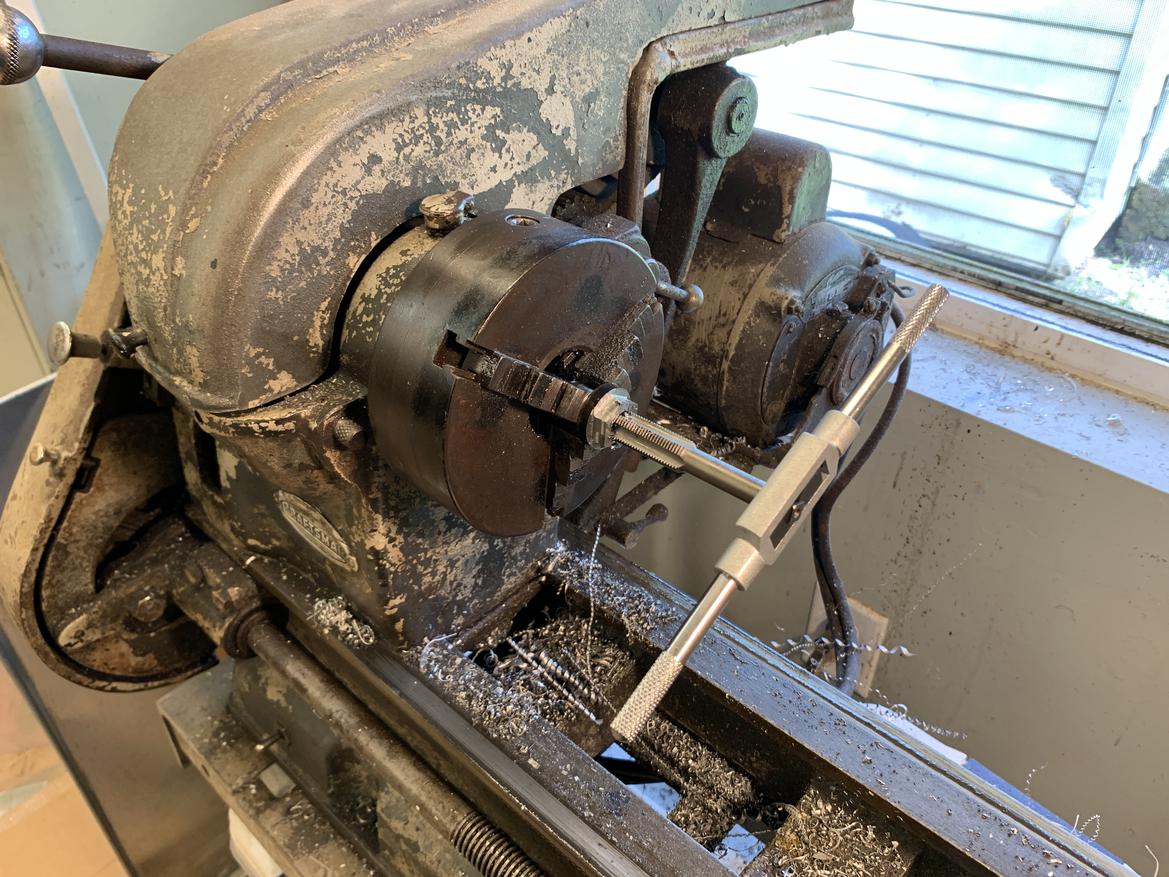
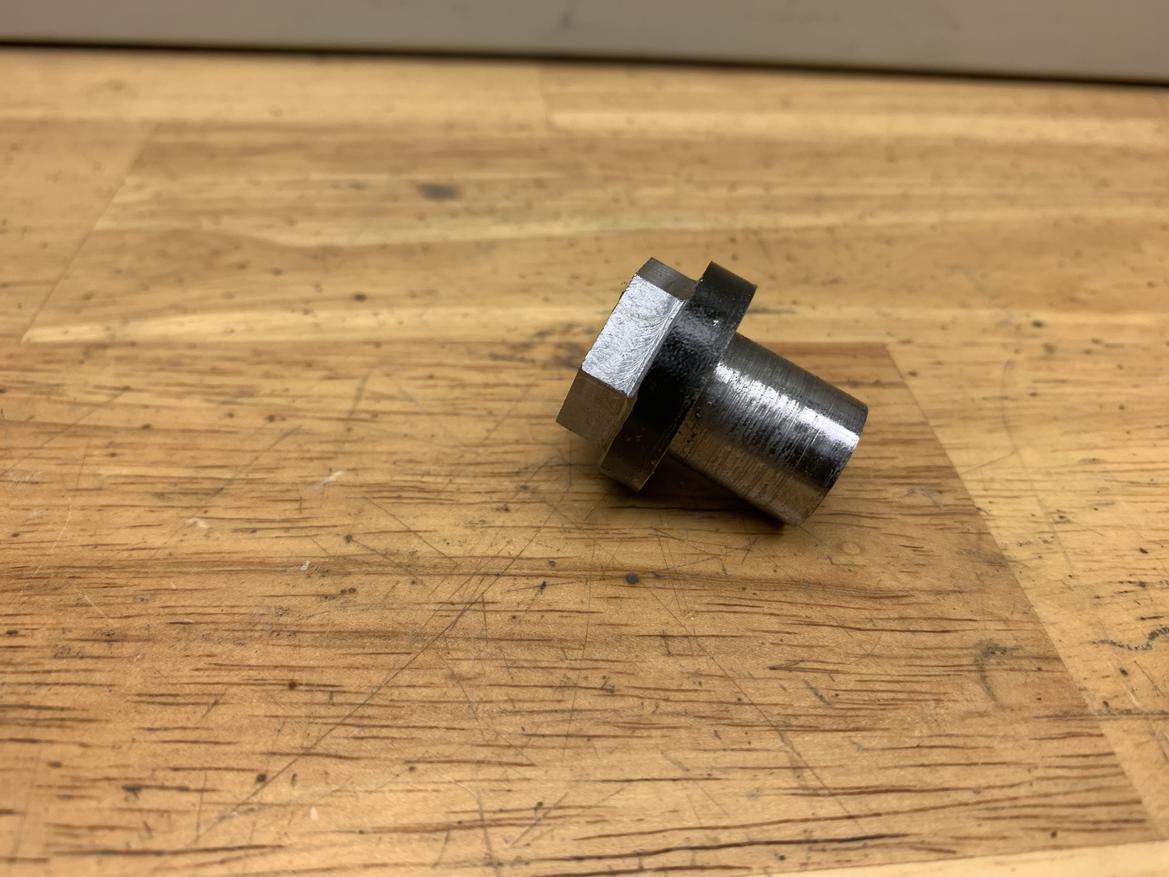
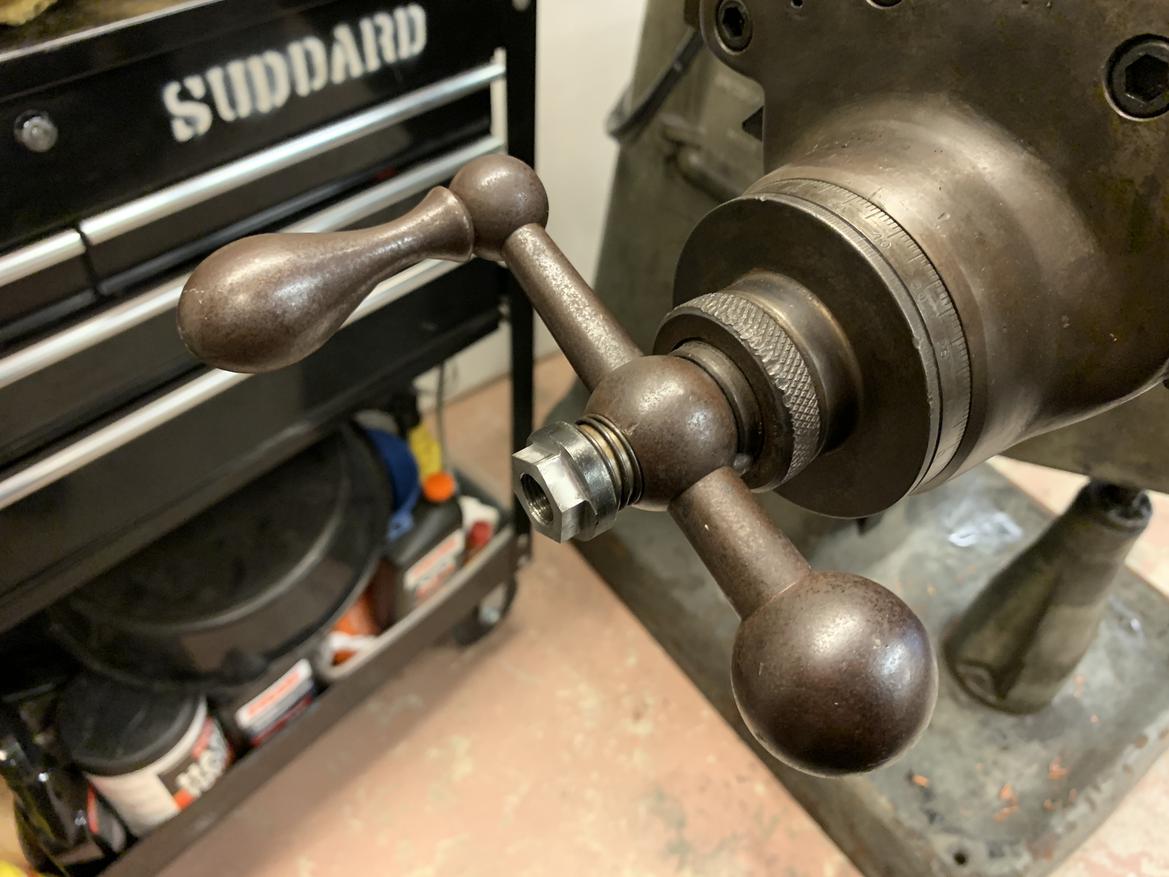
And here's the weird nut finished and installed. Success!
Tom Suddard said:
Keith Tanner said:
CHIIIIIPS!
Expressed as units of initial purchase price, what did it take to get to this point?
I need to go back and total everything up, but right now I think I'm somewhere around $500 in tooling and $1000 in machine transport/repair/upgrade costs.
So that would be 0.75 Initial Purchase Units to get to First Chips. It would be really interesting to get an idea of where the crossover is between buying a cheap one and fixing it vs the old car rule of "get the best you can afford". I know yours is upgraded from how it left the factory now, but if we take power feed as a requirement - would it have been worth buying a more expensive one, or are the speed bumps you encountered ones that you'd expect with any used Bridgeport?
Keith Tanner said:
Tom Suddard said:
Keith Tanner said:
CHIIIIIPS!
Expressed as units of initial purchase price, what did it take to get to this point?
I need to go back and total everything up, but right now I think I'm somewhere around $500 in tooling and $1000 in machine transport/repair/upgrade costs.
So that would be 0.75 Initial Purchase Units to get to First Chips. It would be really interesting to get an idea of where the crossover is between buying a cheap one and fixing it vs the old car rule of "get the best you can afford". I know yours is upgraded from how it left the factory now, but if we take power feed as a requirement - would it have been worth buying a more expensive one, or are the speed bumps you encountered ones that you'd expect with any used Bridgeport?
So, I haven't done an exhaustive study but based on the half dozen or so machine tool purchases I've been involved in Tom's experience is pretty typical. If you want/need precise ways then you need to step up to a more expensive (and probably newer) machine but every used machine I've been involved with needed some, sort of expensive repair before being serviceable. I suspect that's because the looming repair is what prompts the previous owners to get rid of the machine in the first place.
Tom is just getting started with the tooling costs and I'd anticipate that they'll soon outstrip the current total investment.
Yeah, new machines were off the table; they're not even close price-wise.
After fixing this one up, I'm at about the same money as if I'd bought a "ready to run" one elsewhere and gotten a good deal. So I'd call it a wash; every single one of these will need some repair, just like a used car, so I'm content with the path I took.
The cool part about this process, though, is I replaced the most common wear item on one of these, so it's probably a better machine now than an equivalently priced used one that didn't need a new leadscrew would have been. Think of it like buying a car with flat tires vs. buying a car with 10-year-old tires that hold air. They both need replacement, but the flat tires saved me some money on the purchase price.
Oh, and it's worth mentioning that owning a lathe saved me somewhere between $100 and $1000 depending on how you'd make the power feed and table handle fit without the ability to make spacers/adapters.
Seems like you lucked out and got a pretty good used machine. Not too worn out or beat up. The problems you found could be fixed with simple replacements.
Sometimes these old machines have serious problems - like worn out spindles or badly-rocking bed ways. Things that cost a huge amount of money to fix properly. And those are jobs that you can't usually do at a hobby level. It's even worse if you buy a machine that is old and no longer supported. Bridgeports are generally pretty easy to fix up. I've had old machines that haven't been supported in decades, and you often have to fab your own replacement parts for them. Getting an accurate machine can be very difficult.
Checked the mail today for a nice surprise; more stuff showed up! Thanks a ton 914Driver; I swear you're psychic since you always know what tools I'm missing!
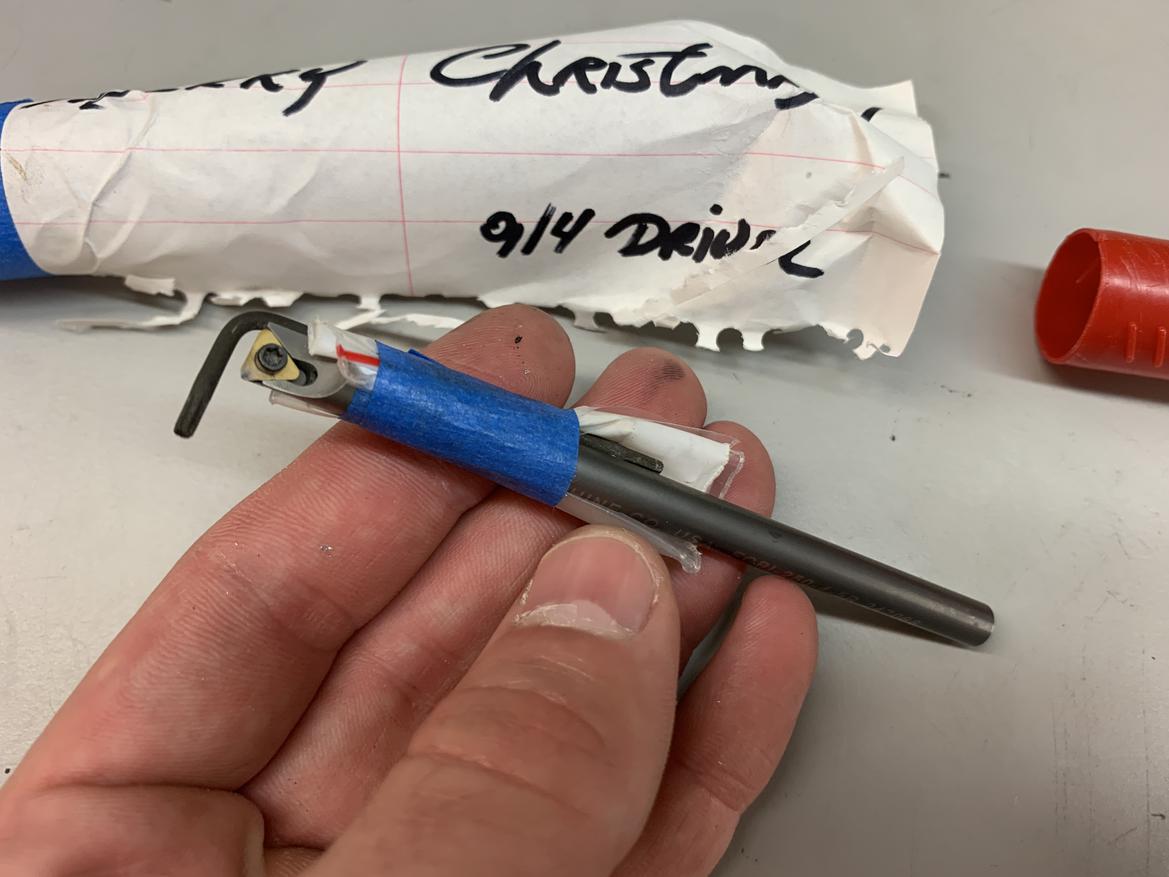
You're welcome, don't see myself using it again. BTW, the tapping photo above; if you put a live center in the tailstock and push it into the hole at the top of the tap it will ensure the threads are going in straight.
Dan
In reply to 914Driver :
Ah, that's a good tip. Thank you!
To everybody who said "Once you have mill you'll wonder how you ever lived without one!"
Well, you weren't wrong. This thing has already churned out a Bugeye Sprite lowering kit (details whenever I find some photos).
I also got a text from a friend yesterday:
"Hey, could you make me an axle?"
"Uhhhhh, I've never done that before. But sure! I saw it on YouTube once."
Axle creation coming soon....