This is gonna be a great project. What does the stock DC motor have in terms of cooling? Maybe you can add some passive heatsinks and ducting that will help keep the motor cool from airflow as you feed it more juice.
I'm sure you can get some cheap Peltier coolers off eBay.
wvumtnbkr wrote:
The wheelbase is too short for Lemons I believe.
Just attach the back of one to the front of the other. Double the wheelbase, and now you technically have 4WD. If you went back to back you could even have four-wheel steering to make it an unstoppable, undrivable suicide booth on track.
bluej
Dork
10/24/13 3:33 p.m.
These are like the lemons/challenge version of the f&f jump cars
jpnovak
New Reader
10/24/13 3:46 p.m.
You should bolt the two back to back and make the wheel base longer. It would also be bi-directional and dual motor powered.
Nashco
UberDork
10/24/13 4:12 p.m.
Anybody who thinks electric motors have a place at the $20xx must be a lunatic. 
I'm curious to see what you are using for batteries, voltage, and controller...with enough attention to detail, you might crack into the 20s!
You're a real glutton for punishment working with that chassis, but who am I to judge? I wish you the best of luck just the same, of course!
ssswitch wrote:
This is gonna be a great project. What does the stock DC motor have in terms of cooling? Maybe you can add some passive heatsinks and ducting that will help keep the motor cool from airflow as you feed it more juice.
Cooling? It's only going to be running for a minute at a time, why bother?
Bryce
Today's update:
This morning Spinout007/MrLee came over and spent an ungodly amount of time removing brake master cylinders that had rusty bolts blocking rusty bolts and cotter pins disintegrating everywhere but where they needed to actually come out. Now we have props to bring to the parts store when tell them we want them to look in the real parts book with dimensions and specifications instead of vehicle names:
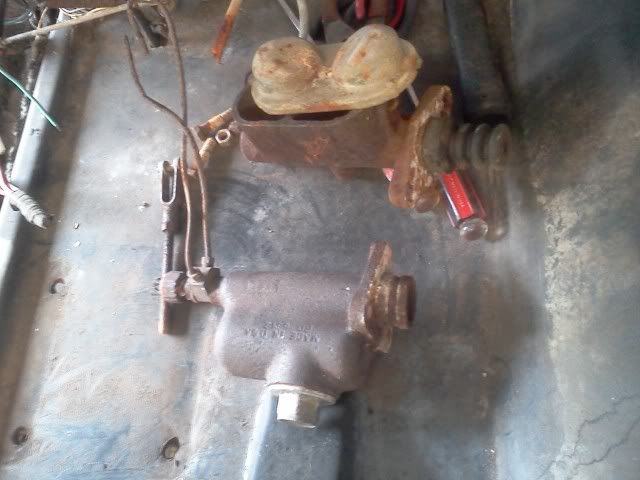
While he was fighting nearly 40 year old rust and bad engineering I stripped the orange cars body panels.
Ewwww, they're naked!
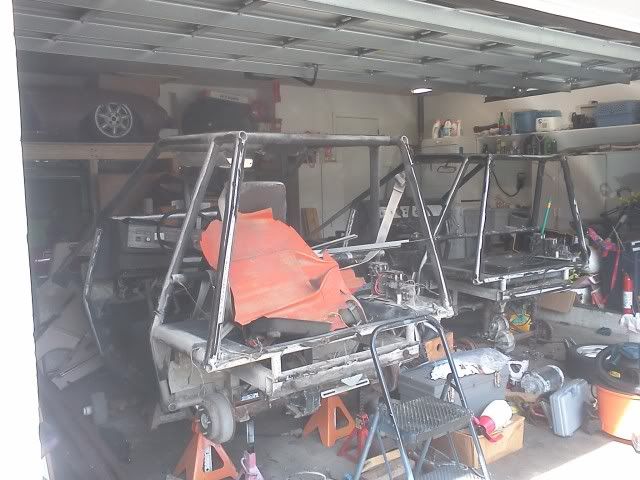
After that Mr. Lee assembled the Harbor Freight High Performance Leaf Spring Re-Arching Tool:
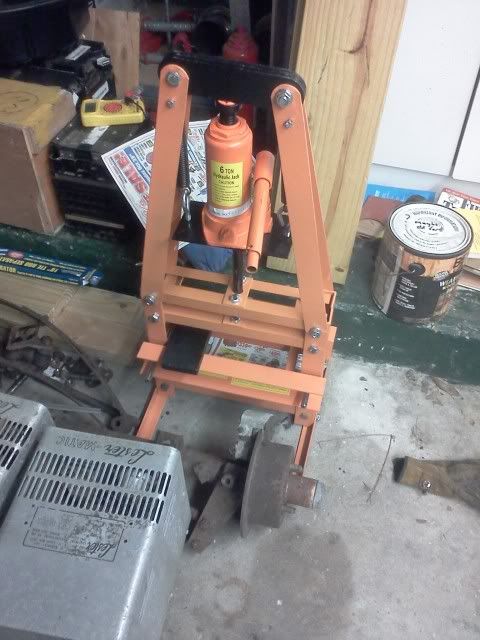
All the suspension is off. All the bodies are off. All the brakes are ready to start rebuilding and the motors are dismounted. Hopefully most of the future updates will be about assembly.
The master cylinders were absolutely stupid. Almost 2 hours to remove 5 bolts 4 lines and 2 pins. 
SVreX
MegaDork
10/26/13 9:23 a.m.
MrJoshua wrote:
All the suspension is off. All the bodies are off. All the brakes are ready to start rebuilding and the motors are dismounted.
So, you have essentially removed the car from the car, right? 
Have you thought about using some Ski's instead of leafsprings? I know they probably aren't common down there but some cross country ski's or downhill skis could be used in addition the the stock leaf springs to raise the rate significantly.
tuna55
PowerDork
10/28/13 9:36 p.m.
MrJoshua wrote:
wvumtnbkr wrote:
2 motors 1 car?
Seriously considered.
Something to think about since electric cars have so much trouble with transmissions. The Leaf accelerates very quickly 0-30 and even decently 0-45 but very little from there on. If I grafted an overrun clutch on to the output shaft, and ran a second motor at a much lower numerical gear ratio, the second motor could extend that acceleration a bit beyond the RPM range of the first motor and the overrun clutch would ensure the first motor doesn't become a generator. An automatic transmission could be a great donor of these clutches.
Too many days since an update.
Unlike an ICE powered car the power in an electric car comes from the batteries and the controller, not the motor. The Batteries determine the available power and the controller determines how much of that power you can force through the poor motor. The motors job is to survive and determine where in the rpm range you get your power.
In my car I have a decent amount of battery. I am using an American built government subsidized battery recalled, recycled for scrap, sold to Chinese vendors shipped to China, resold to silly American and shipped back to America battery (all for less than the American battery maker would sell it to Americans
). The car will be powered by an A123 28s3p battery module. It is ~90 volts nominal and 60 amp hours. In "I don't care about money or fire" land it is capable of 2541 amps at 44.8 volts or ~153 hp. The reality is I will be limited by by the controller and motor/drivetrain.
Two A123 modules side by side:
The Controller will either be an Open Revolt open source motor controller or a DIY really stupid idea that really really want to do but I am trying really hard to convince myself I have little enough sense to do it.
The 'Open Source controller is nice and cheap as far as the EV world is concerned. The issue is overall power availability. 144 Volts and 500 Amps is 77,000 watts. 77,000 watts divided by 746 (hp conversion) is only 103hp. 103hp sounds great in my tiny car but I have other problems.
In the EV world Amps determine torque and motor size determines how much torque you get per Amp. In a series DC motor torque is a square of diameter and single multiple of length. Tiny little motors like mine are better at rpm's. The 500 Amp limit of my controller limits me to about 50ft/lbs of torque. That sounds fine for a 800lb car but being direct drive I only have one gear. I will be nearly doubling the stock Volts so my top speed should be quite a bit higher, but I am counting on weight loss to to improve acceleration.
The Motor: The motor is a tiny, 50lb, tiny brushed motor rated at 3.5hp continuous. When pushed hard the motor had a tendency to melt the brush leads. That was partially due to the fact that the motor was totally sealed with no airflow and partially due to the fact that it had tiny brush leads and crappy brushes. Not long ago an EV enthusiast from a large brush manufacturing company showed up on the DIY EV forums willing to make better brushes for people who wanted more from their DC motors. I found online references to this company making stuff for CitiCars and contacted the company. Man they were helpful. They supplied me with a brush setup that should allow my tiny motor to withstand way more abuse than the stock GE brushes can handle. They not only supplied the brushes for an obscure motor, but I received multiple unsolicited personal phone calls offering advice on every aspect of my oddball project. I was pleasantly shocked.
If it is ever a market you are in Helwig Carbon is incredible.
bluej
Dork
10/28/13 10:16 p.m.
isn't 103hp in one of these like a 230hp miata, power:weight wise?
bluej wrote:
isn't 103hp in one of these like a 230hp miata, power:weight wise?
My above post had "ghost post" midway through. Unfortunately my 103hp is more like 50hp.
I have multiple A123 batteries and other batteries of many different nominal voltages sitting around so I needed a charger that would accommodate multiple voltages and fit my cheap mindset. On recommendations from another forum I bought a 100 Volt 10 amp power supply. The power supply was great until early one Sunday morning I tried to finish a tricky charge of a persnickety module I had shut down at 12:45 AM because I couldn't stay awake to watch it anymore. In my half awake state I hooked the leads to the back module (which was sitting opposite of the front module) and let the smoke out of my power supply. Being cheap it had no reverse polarity protection. Fortunately the parts are cheap. Unfortunately I have another project on top of my limited schedule. 
Last night and tonight I/we "Re-Arched" the rear springs. Basically this moves the spring in relation to the mounting hole and you end up with 3/4" to 1" lowering of the axle.
You start with the main leaf with all the helper springs removed and trace the curve onto a flat surface:
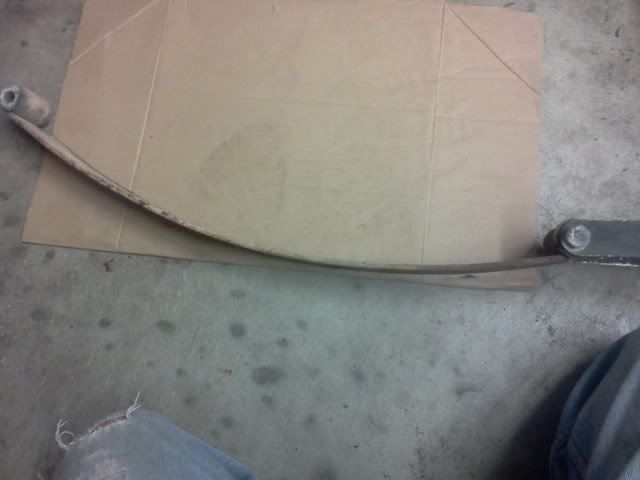
Then you make marks every 1" and go to work reversing the curve with your press:
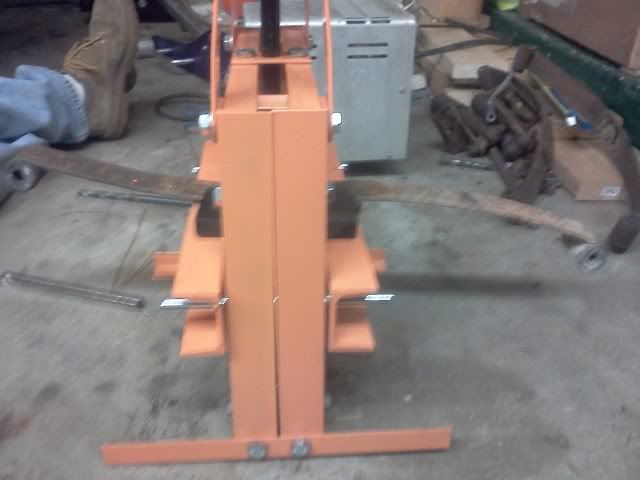
I will use homemade lowering blocks to lower it the rest of the way in the rear.
Nashco
UberDork
10/29/13 12:55 a.m.
Lithium...I'm excited and scared at the same time. Dare I ask...what are you using for a BMS? Funny that you've got some (scrapped versions) of the worlds best batteries with one of the worst motors to use it. Oh well, I foresee a forced upgrade in your future.
I'm curious to see how the stance turns out, yo.
Bryce
Nashco wrote:
Lithium...I'm excited and scared at the same time. Dare I ask...what are you using for a BMS? Funny that you've got some (scrapped versions) of the worlds best batteries with one of the worst motors to use it. Oh well, I foresee a forced upgrade in your future.
I'm curious to see how the stance turns out, yo.
Bryce
Uh oh, you just set me up for the debate on AC vs. DC and the BMS/top balance/bottom balance debate. 8)
MrJoshua wrote:
I was pleasantly shocked.
Comedic genius, I tell ya'… 
Whoa nice score on the A123 cells. Some of the best batteries out there, certainly the best value.
youngfg
New Reader
10/29/13 12:46 p.m.
I had a Commuta Car I fixed up a few years ago, and sold.
I don't know how fast you plan on making your car go, but in a stock Commuta car 37mph is exciting/ scary. I couldn't imagine going 55 mph in one.
After I sold the car, the new owner commissioned me to, upgrade the brakes, and the motor controller.
I installed four wheel disc brakes with Willwood calipers, and an Alltrax controller.
The rear wheel bearing setup is scary, they use tapered bearing and have nothing for cornering thrust force other than the bearing cage rubbing against the bearing retainer. You should look into fixing that if you plan on autcrosssing yours

Nashco
UberDork
10/29/13 12:59 p.m.
MrJoshua wrote:
Nashco wrote:
Lithium...I'm excited and scared at the same time. Dare I ask...what are you using for a BMS? Funny that you've got some (scrapped versions) of the worlds best batteries with one of the worst motors to use it. Oh well, I foresee a forced upgrade in your future.
I'm curious to see how the stance turns out, yo.
Bryce
Uh oh, you just set me up for the debate on AC vs. DC and the BMS/top balance/bottom balance debate. 8)
Well, AC motors and a real BMS are clearly the superior technical solutions...but you're on a budget and you're new at this, so you've got to start somewhere. I don't think there's debate to the technical superiority, and you're doing what you're doing without any debate.
That's why I'm excited and scared at the same time. I know quite well what the A123 batteries expect, and some of these Chinese un-scrapped versions even come with the BMS attached (but of course it's not open source on how to use this BMS to its potential). Some of them, especially cheapest ones like you'd use on the $20xx, are just a bunch of cell assemblies with a few less-healthy ones in the strings. When you've got a few less-healthy ones in there and they're all welded together, it makes for a pretty unstable situation if you're not using a BMS to at least monitor these low cells and warn you (or shut things down). Note that any automotive battery OEM is not using a "top balance" or "bottom balance" in normal use, they balance batteries in a much more sophisticated manner to extend battery life in typical usage profiles. You'll read a lot of hogwash by guys experimenting on the internets and trying to save money with top/bottom balancing, this is certainly not considered in industry. With lithium and no BMS (not even basic monitoring) you can have some very bad stuff happen. With proper monitoring, you might hurt a cell but at least won't have anything dangerous happen.
BE CAREFUL!!!
Just trying to help you protect your safety and investment with my hard learned lessons. Not that I know anything about failed batteries in a $20xx competitor or trying to balance cost, performance, and reliability with high voltage batteries.
From your comment, I'm guessing you're trying to get away without a BMS, which is risky. If it's purely used for monitoring to alert you of abnormal conditions for safety reasons, this is cheap and fairly easy and well documented in the DIY EV world.
Oh yeah, while I'm wearing my high voltage safety hat, please make sure you've got isolation monitoring, an inertia switch, contactors, and a properly sized fuse in the system. There are lots of info/rules that NHRA provides for the EV safety requirements, in case you didn't already know, which I used in my build.
I'm trying to be helpful and keep you and others around the car safe, hope you don't think I'm just doggin' ya. If you have any questions or need parts, please let me know. I'm happy to help and I've got most of the mentioned safety parts to provide if you don't already have them sourced.
Bryce
Bryce. Mine are living the OEM style above 20 percent below 80 percent charmed life. Each cell group voltage was monitored before, during, and after charging an each stayed within .01 Volts of each other. I am the BMS and will likely be seen crawling around the car with a multimeter before and after every run. NEDRA outlines the NHRA EV specific safety regs and I will be following those to the letter.
In reply to Nashco: Bryce, Does that mean you are coming to the challenge? Cool! There is one part I don't think I have around: an inertia switch. What did you use in yours? I keep remembering that my Land Rover had one but I think all the electrons would just refuse to come out of the battery if I put a Lucas switch in the safety circuit.
BTW-in most cases I've seen the OEM's treat their batteries very very poorly. I need to read up on how Nissan is handling it with the Leaf.
In reply to youngfg:
Do you have any more information about your brake upgrade? We are damn near the point of giving up on the stock crap and using all Miata parts all around, but I am open to suggestions.