Alright!
I put together a setup on my surface plate this evening to measure the valve rocker ratio. Let's talk about it.
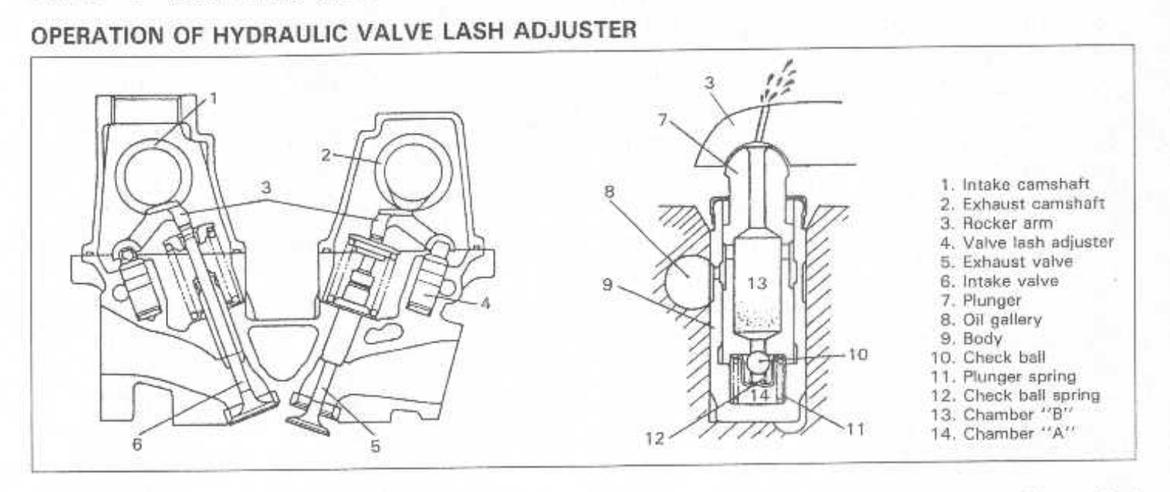
Here's a snip from the factory service manual. You can see that the lash adjuster and valve sit in parallel bores in the cylinder head. Also, when the valve is closed the tips are nearly level.
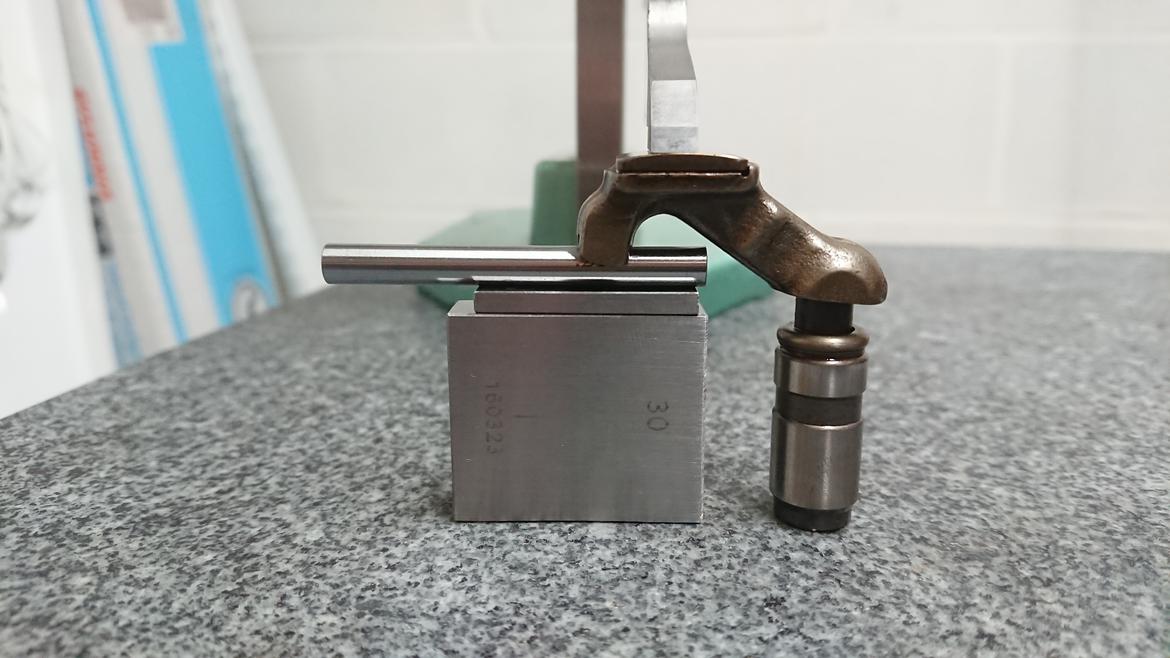
On the right is the lash adjuster. On the left are a stack up of gage blocks. My gage blocks are wider than the round pad that the valve rests on, so I'm using a 5.5 mm gage pin. The pad is round in profile, so this creates a point contact.
I lower the height gage down onto the cam pad. The pad is round, so this creates a line contact. With the lash adjuster resting flat, the whole configuration is well constrained. I read the height gage, rinse, and repeat. As the height of the gage stack changes the highest point on the cam pad moves from one side to the other. You can see this by where the line contact of the height gage is on the cam pad. At the smallest amount of valve lift the highest point is closest to the valve side. At the largest amount of valve lift the highest point of contact is closest to the valve adjuster.
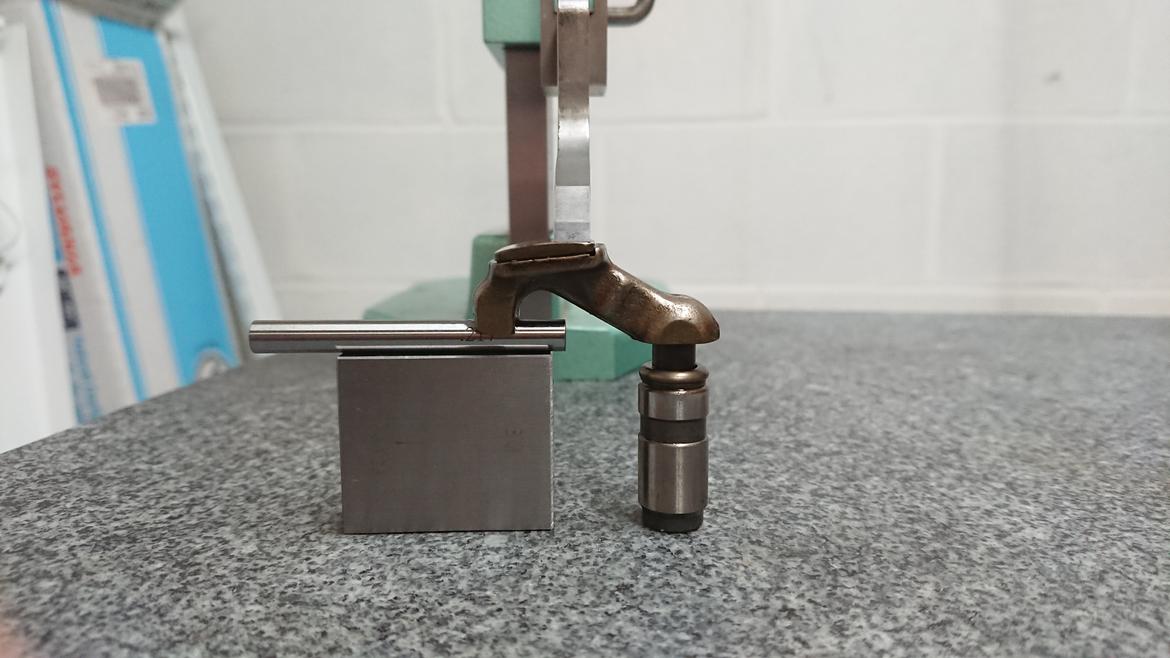
This means that the valve lift ratio is smallest at lower lifts and highest at larger lifts. I calculated the rocker ratio by finding the difference in height gage readings. At lowest valve lift the rocker ratio is very nearly 1:1. At highest valve lift the ratio is nearly 2:1.
The camshaft has a 26 mm base circle and is 30 mm nose-to-heel. That's 4 mm of cam lift, which seems tiny, but it's 8 mm of valve lift! That's better!
Would we be able to do better?
The way that the camshafts fit in the cam box means that the the cam lobes must fit through the bearing journals:
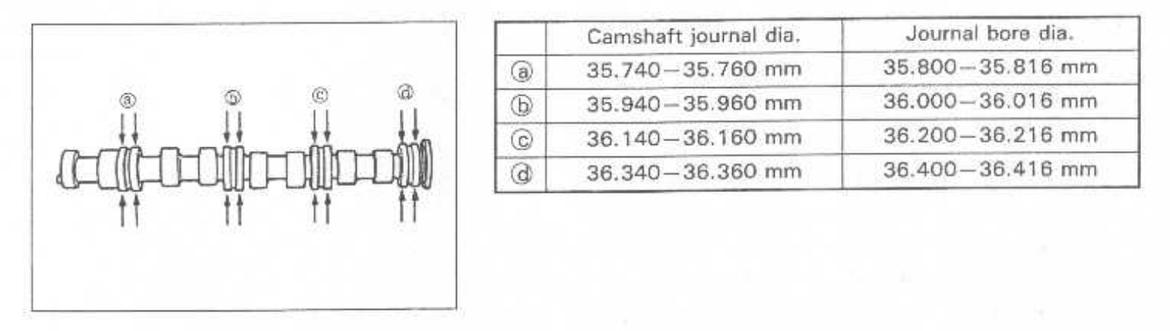
The lobes to the left of journal bore b must fit through b. That bore is 36 mm in diameter at its smallest. 36/2 = 16. We can have a cam lobe with a nose radius of 16 mm. If we keep the same base circle of 26 mm we have a nose-to-heel dimension of 31 mm. 31 - 26 is 5 mm. That'd be 10 mm of valve lift. We can gain 2 mm of valve lift if we can weld the cam lobes, keeping the base circle the same! If we can reduce the base circle we could go even bigger!
I would need to find the limit of the lash adjuster to know how small I can make the base circle.
Next on the list of tasks is measuring cam lift and valve lift. This will confirm my rocker ratio measurements and help determine what my next cam profile will be. Then I can shop around with cam grinders to see who can help me weld up and grind a set of camshafts.
I'm also considering cutting up a lash adjuster to see about replacing the hydraulic action with some kind of internal shim setup.