Been a while. Floor is trimmed, hammered, trimmed some more, and the edges cleaned.
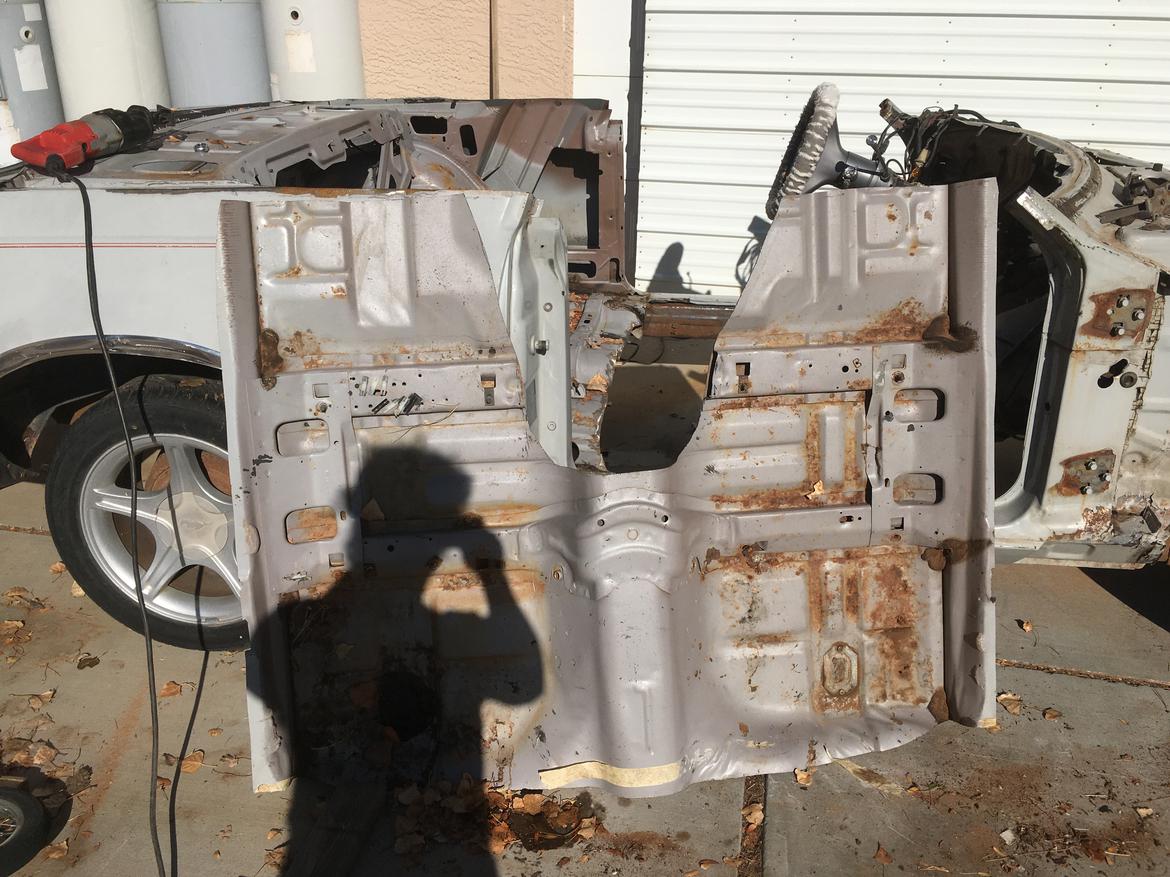
More hammering and grinding and it's welded back where it came from
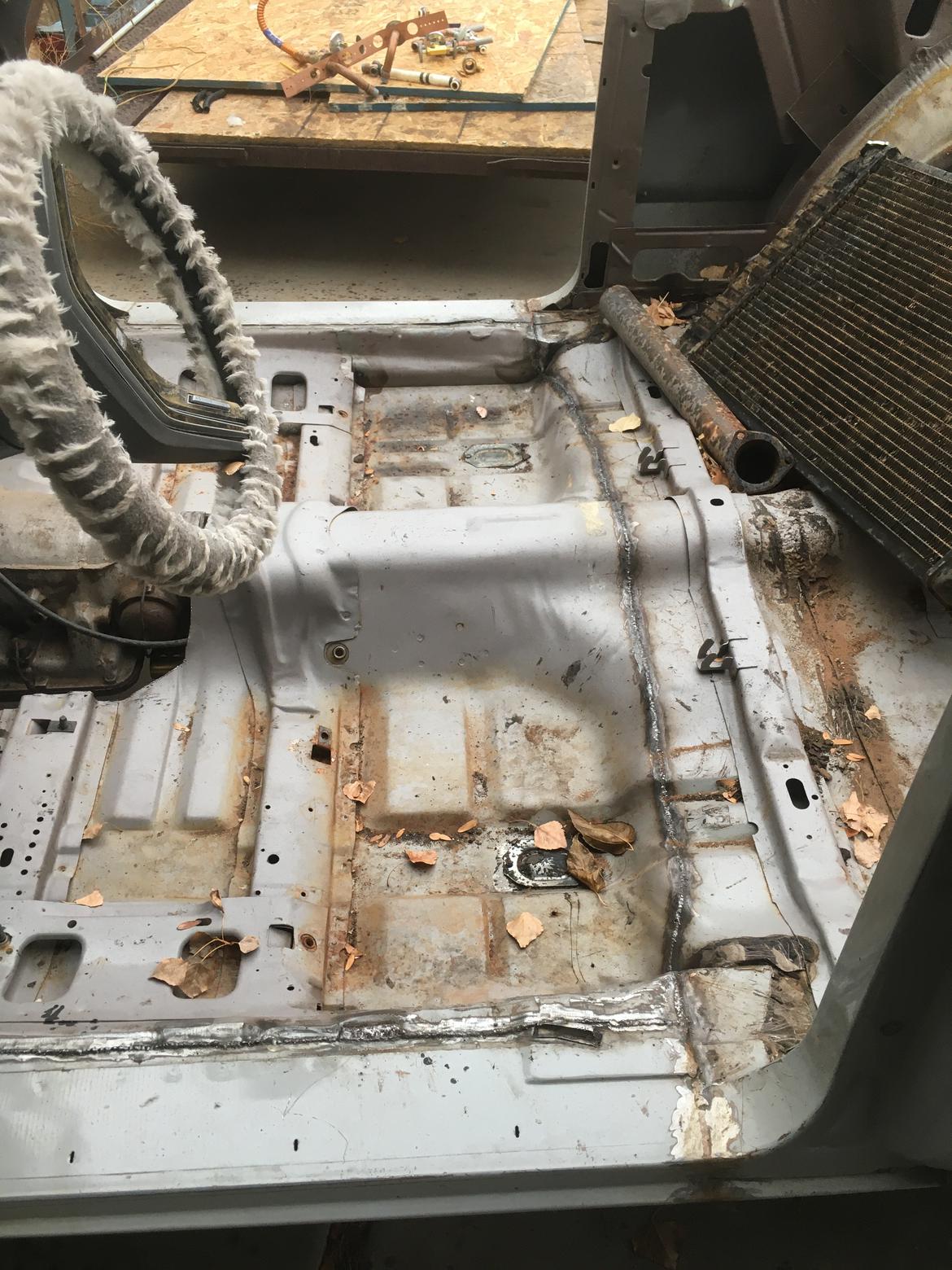
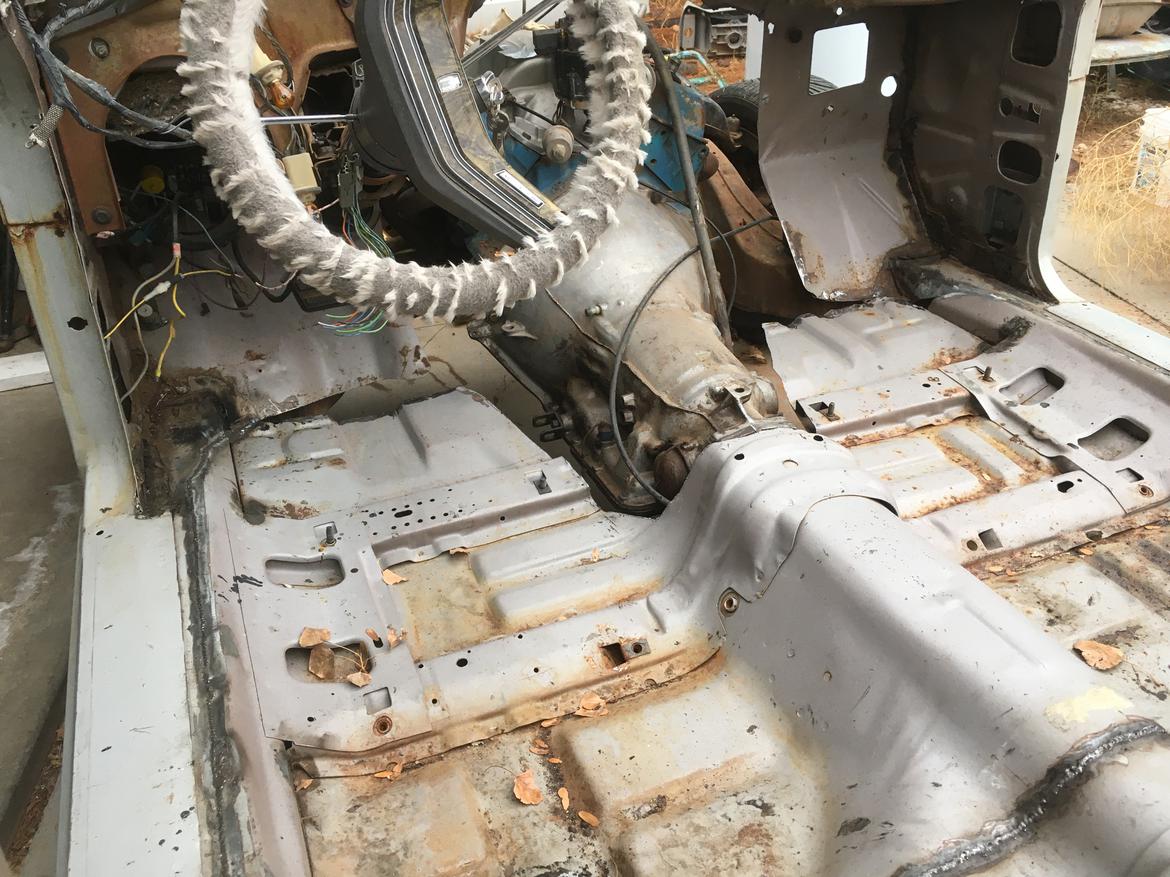
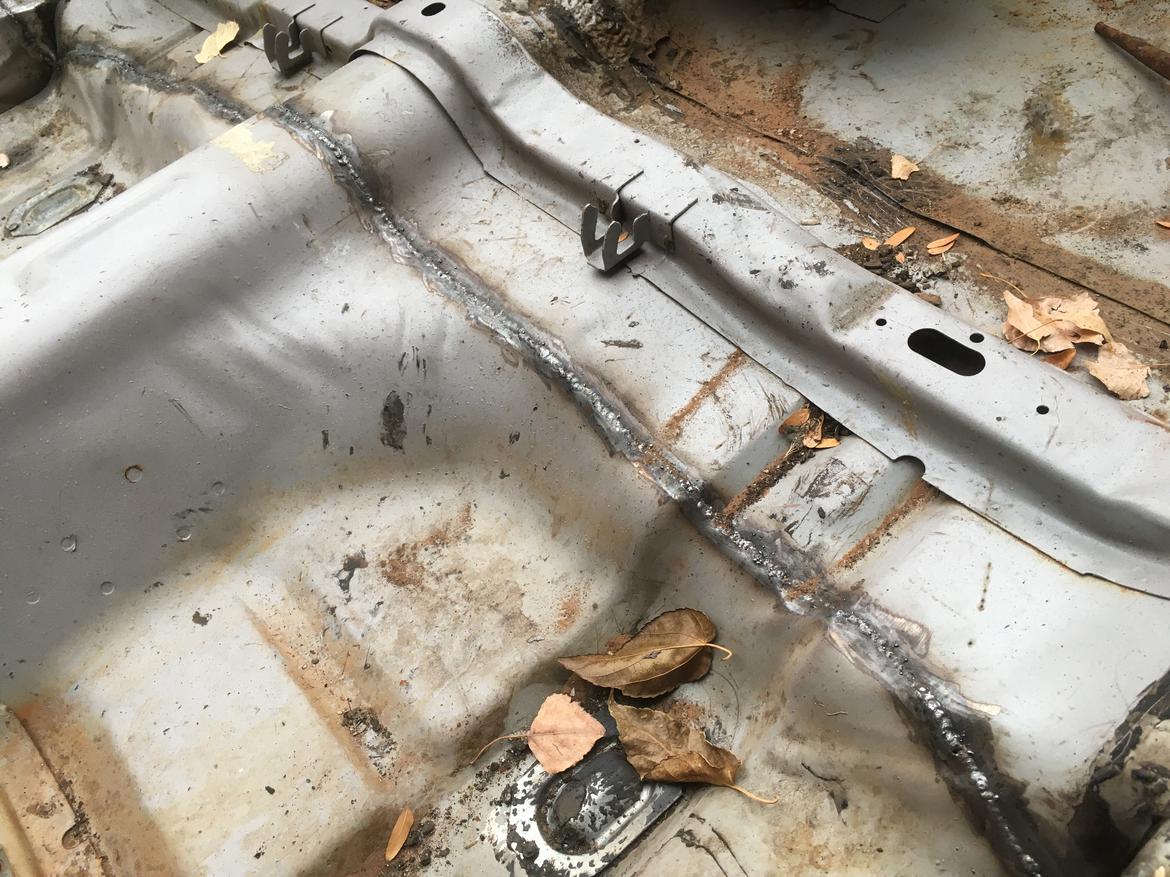
excuse the boogers. Some of the positions I got into while welding were less than ideal. Gotta patch up the foot wells and make a firewall/doghouse. Weather went from 60 to snowing so I'm gonna go get lunch and call it a day.
Progress. October is coming fast.
Decided to actually chop the roof. There's a first for everything.
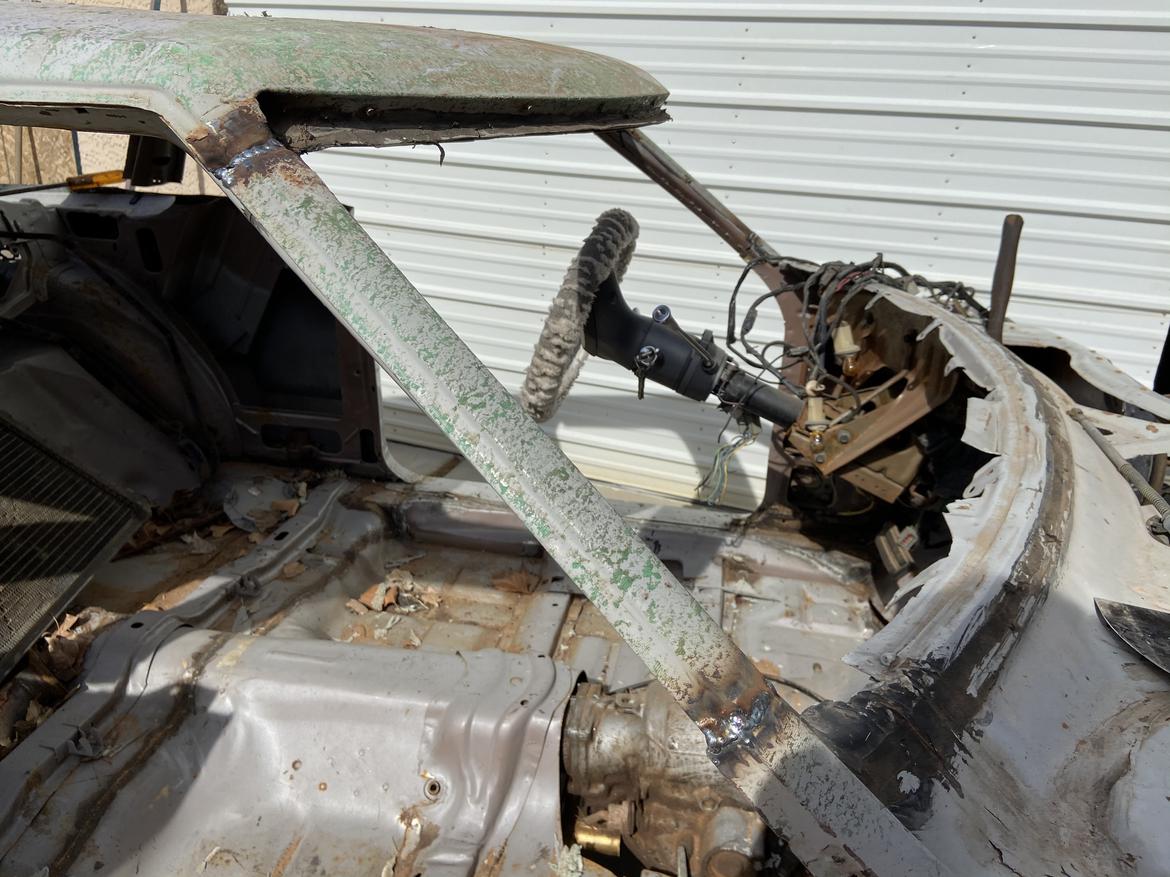
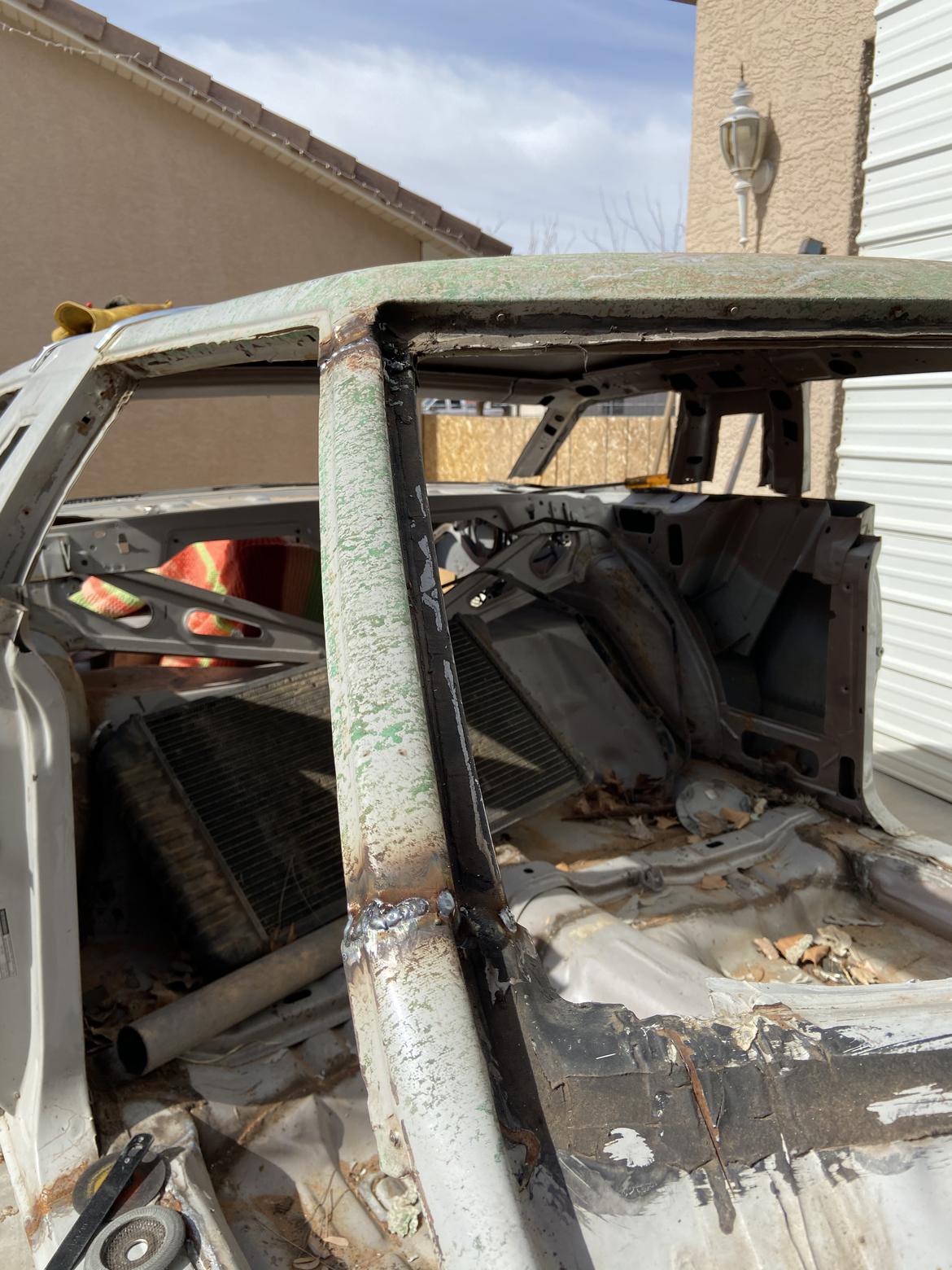
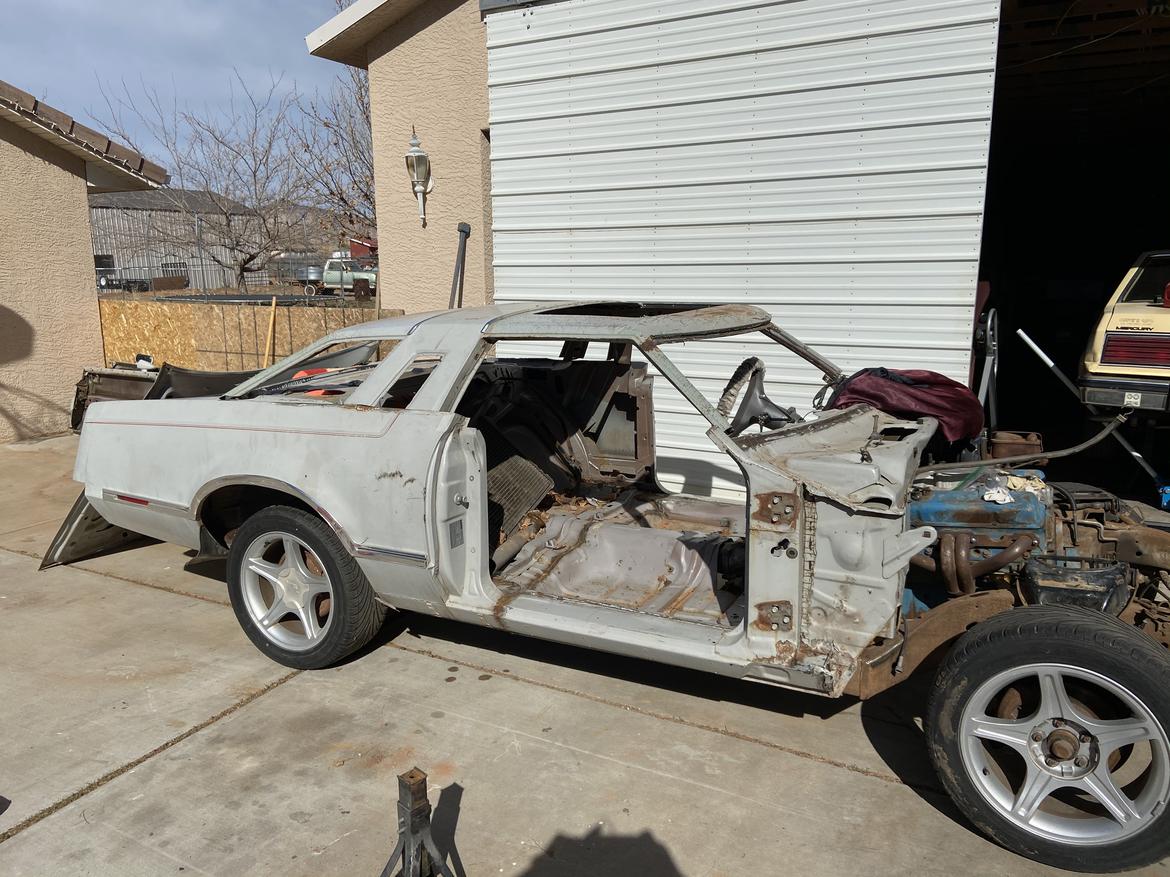
gonna do something different with the b-pillar
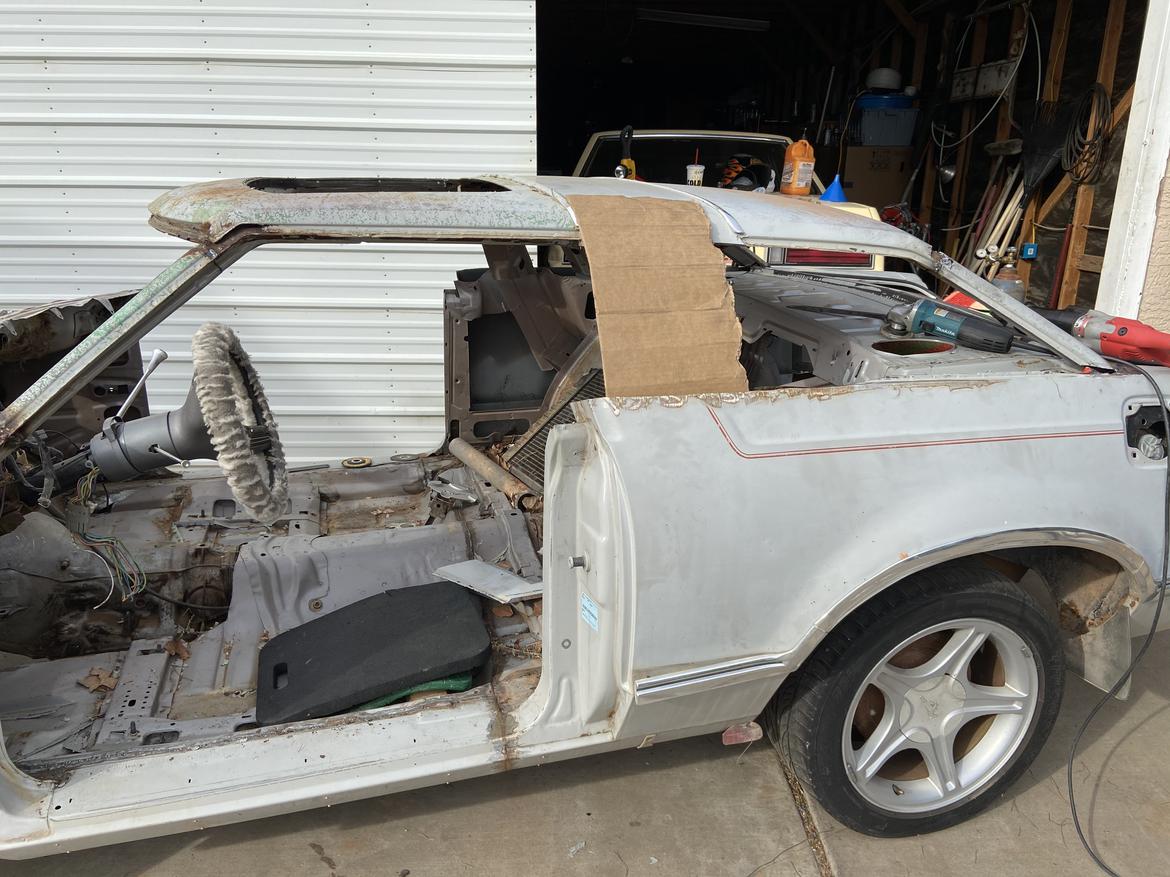
The back looks good
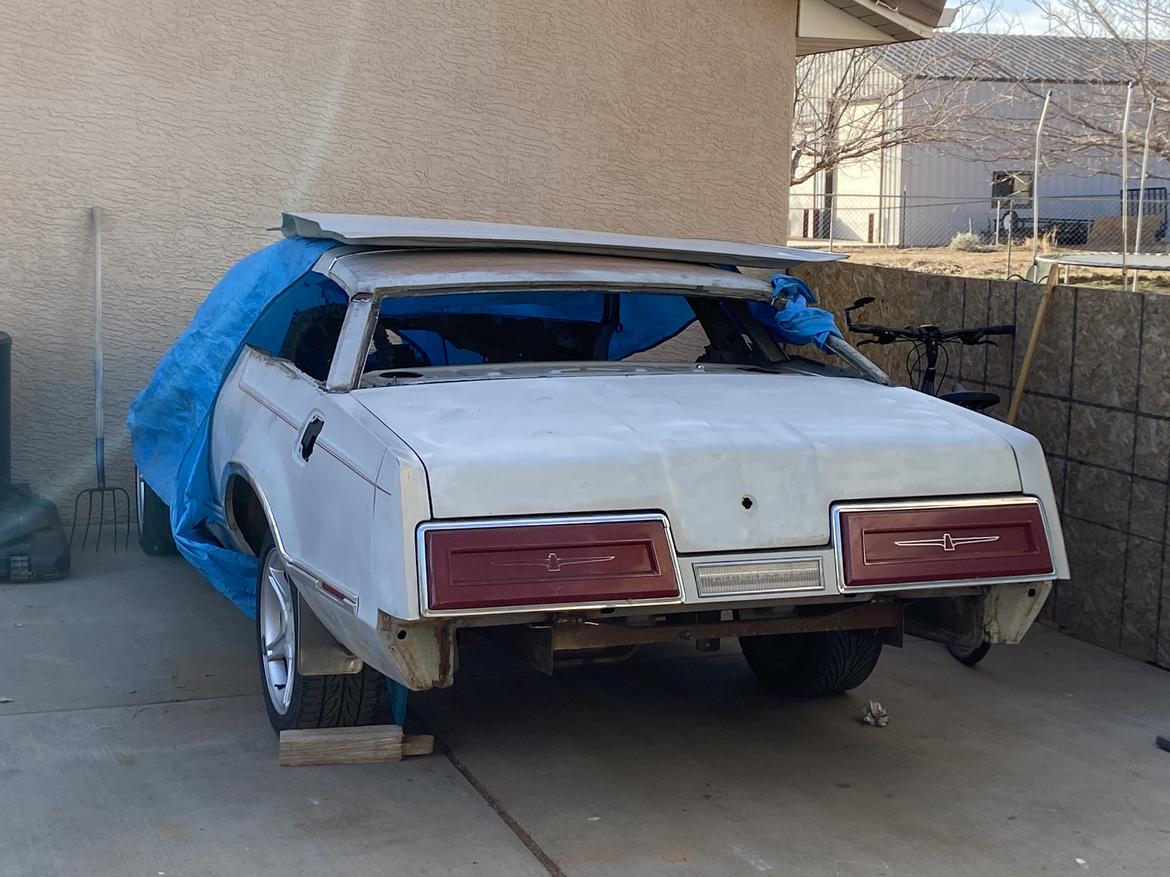
also I learned that Ford used lead to smooth body lines over seams. Also learned that lead will not mig
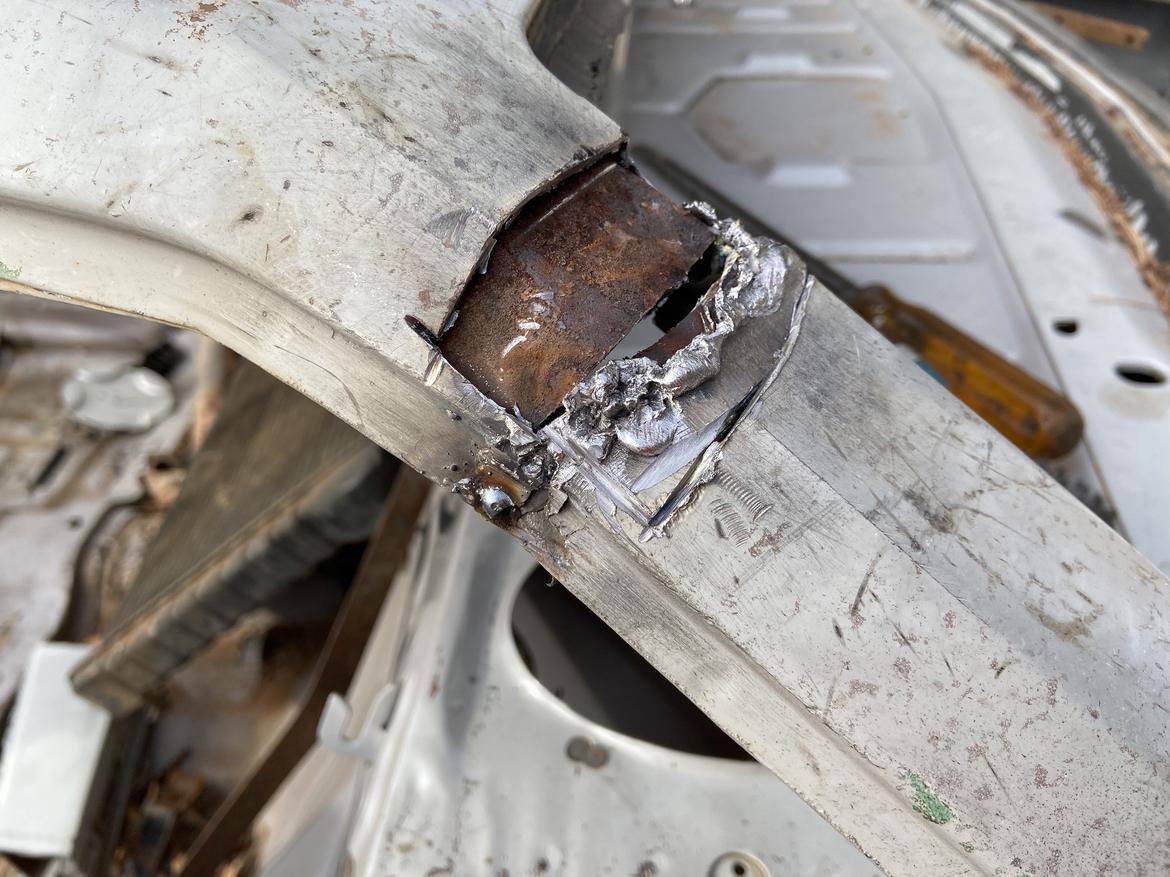
hopefully more next week.
In reply to barefootskater :
I learned that lesson with mopar quarters
In reply to Dusterbd13-michael :
It was weird. Tack here, just great. Move the thing half an inch, won't tack. Check the ground, check the gas, try again. Melts like lead, grinding makes no sparks, cut the piece off and it is soft and heavy. Learned something new I guess. Just means more patches I have to make later. Lots of welding still to do. Might have to put a whole roll of wire in the budget.
These are the kind of builds that made my join this forum. Awesome work. I can't wait to see how it turns out!
barefootskater said:
In reply to Dusterbd13-michael :
It was weird. Tack here, just great. Move the thing half an inch, won't tack. Check the ground, check the gas, try again. Melts like lead, grinding makes no sparks, cut the piece off and it is soft and heavy. Learned something new I guess. Just means more patches I have to make later. Lots of welding still to do. Might have to put a whole roll of wire in the budget.
I generally put a whole roll in budget. Amc was two rolls....
In reply to V6Buicks :
Thanks. But we're just a couple hacks with no real plan.
In this picture we have 4 possible challengers. All under budget and all needing some work.
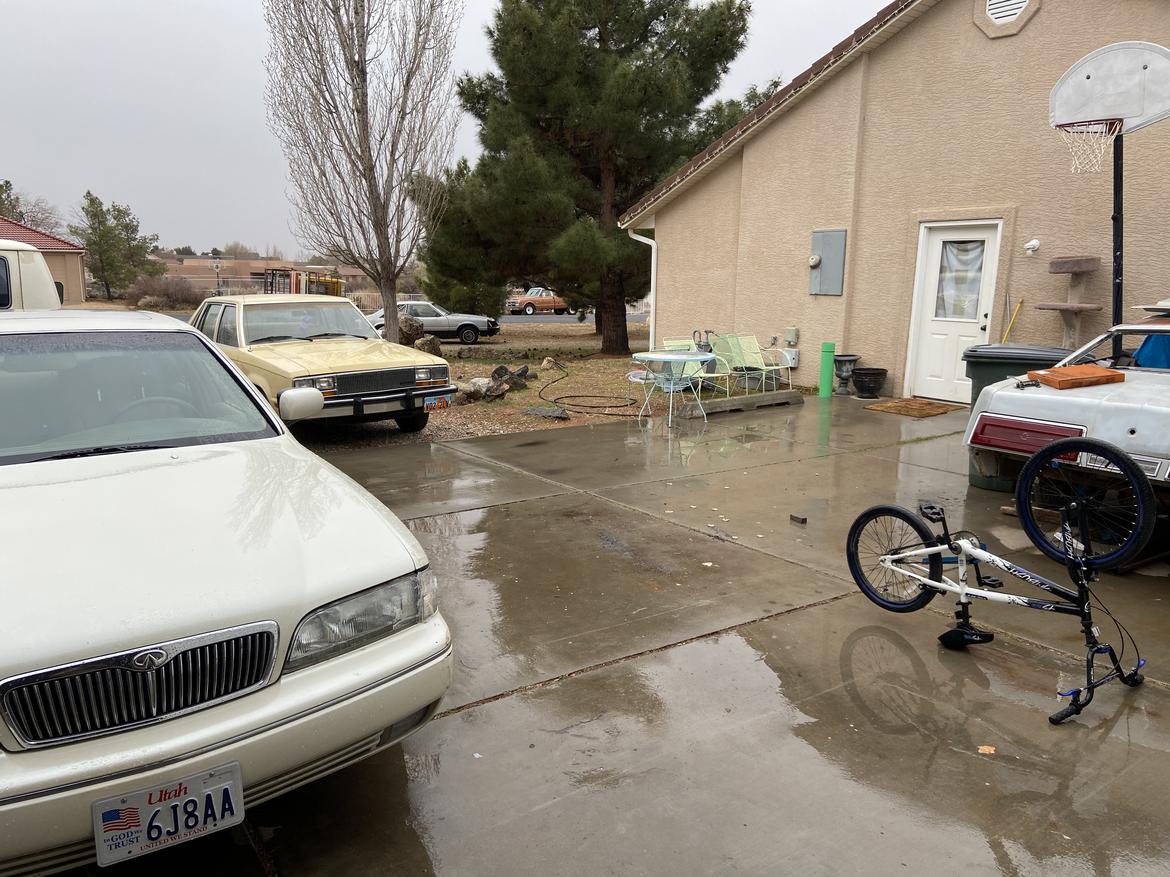
the count is two fox fords, Q45, Funderbird.
Living the life here.
If you have a few minutes spend a few minutes working on the race car, or so I hear. No pictures to show for it, but the drivers door is now cut and stitched and on the car.
Also I changed the oil and put a few quarts of fresh fluid in the trans of the 5 because tomorrow is road trip.
Firewall or front clip next. Haven't decided. Also need to pull the TH350 so we can swap it for a manual in a couple weeks. Much to do yet.
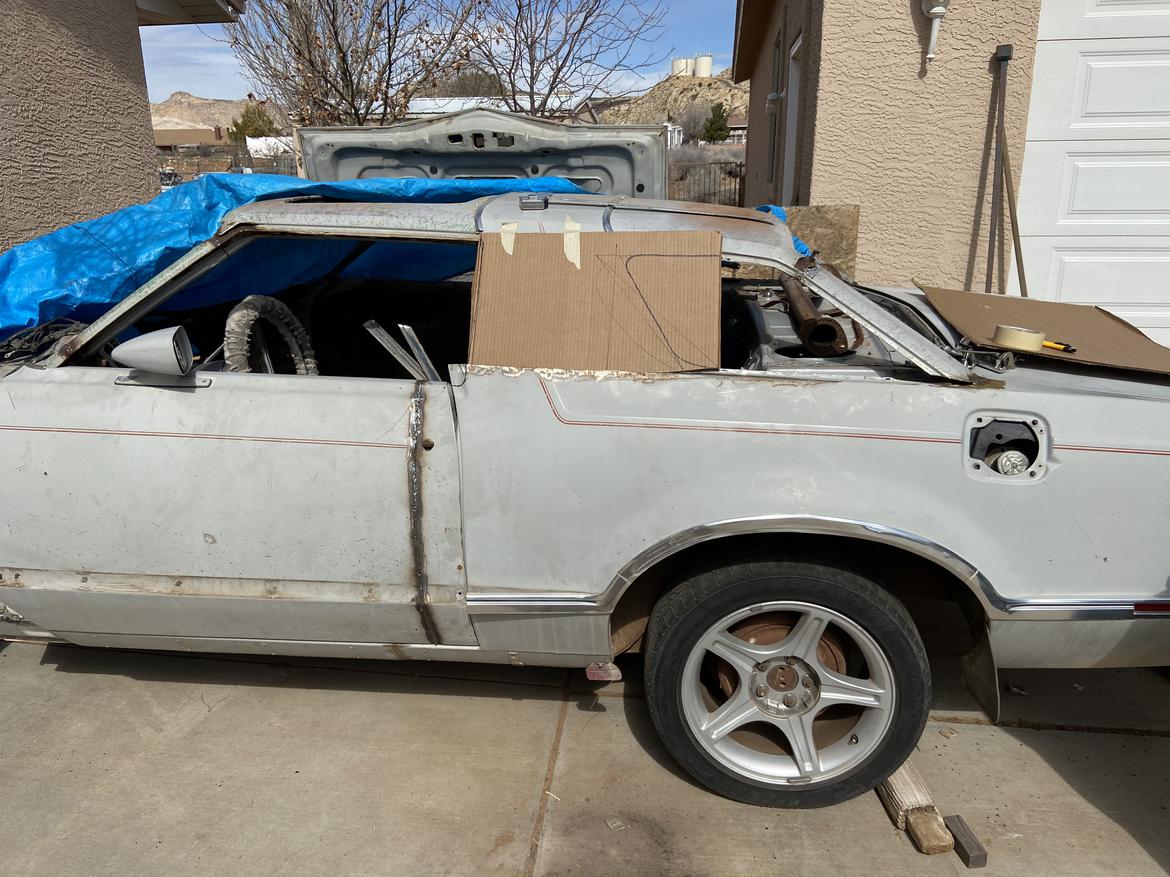
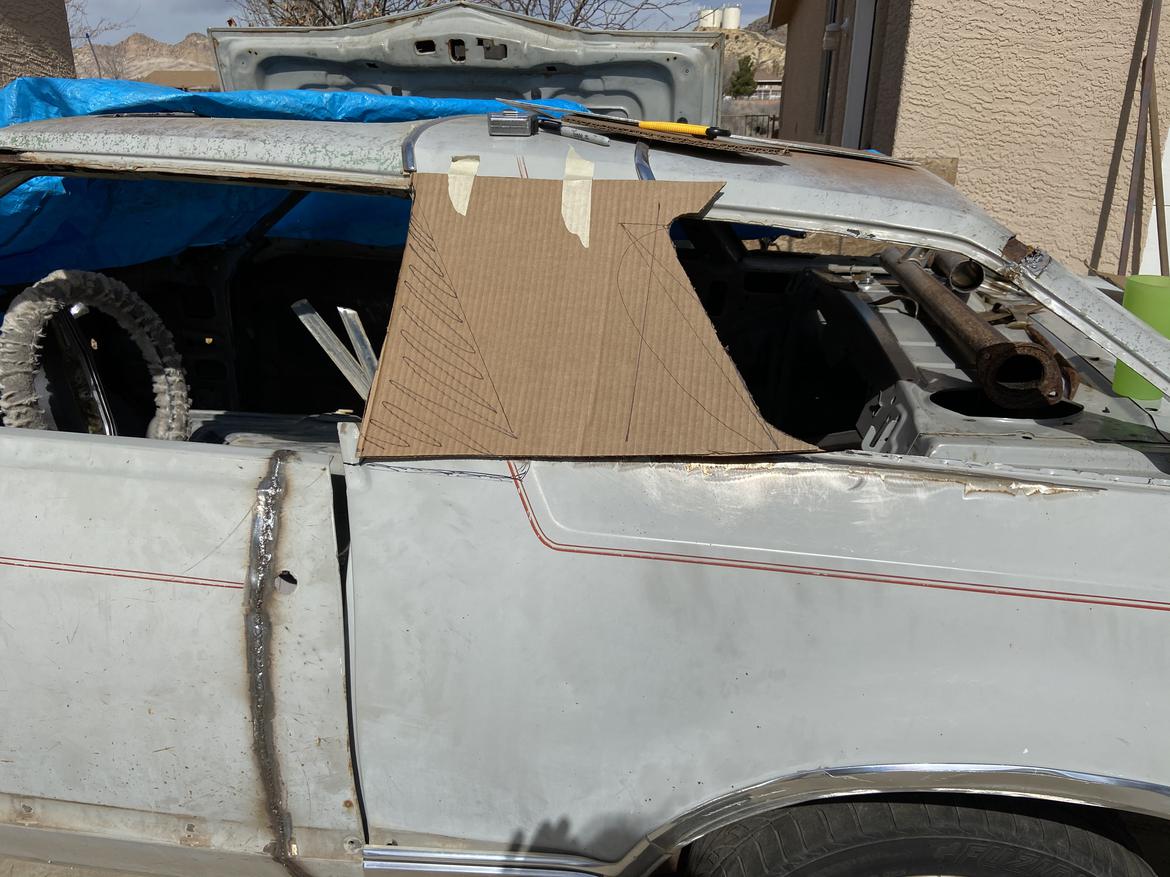
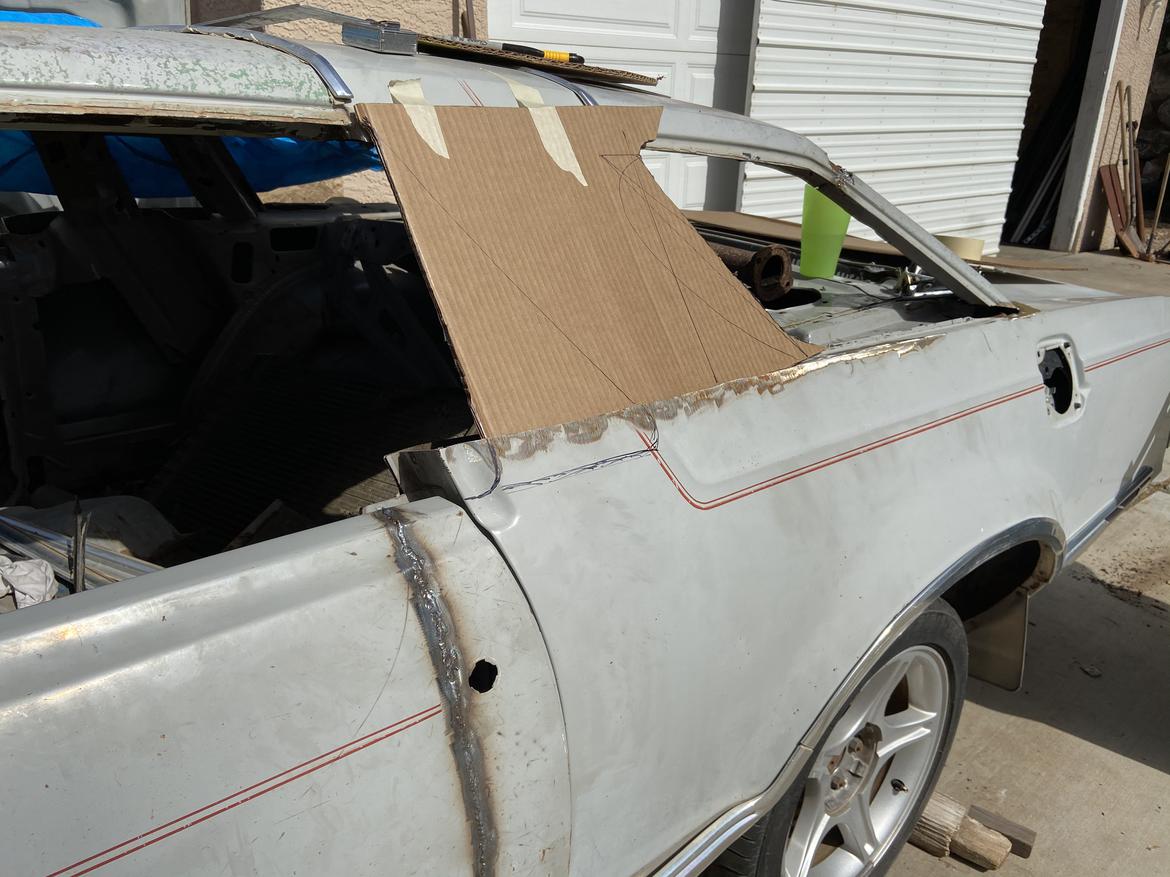
cant decide to leave the front edge vertical or slant it back...
Less metal is less weight. 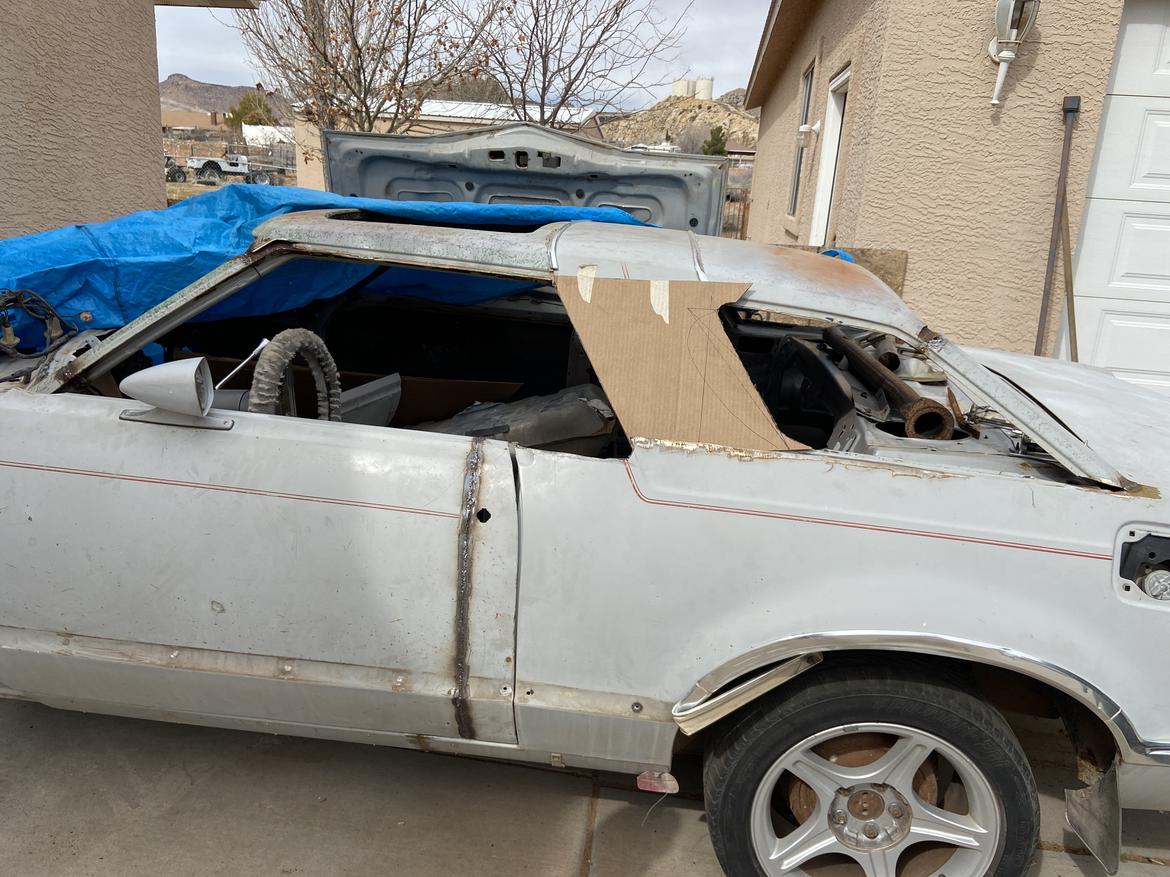
Official vroom noises
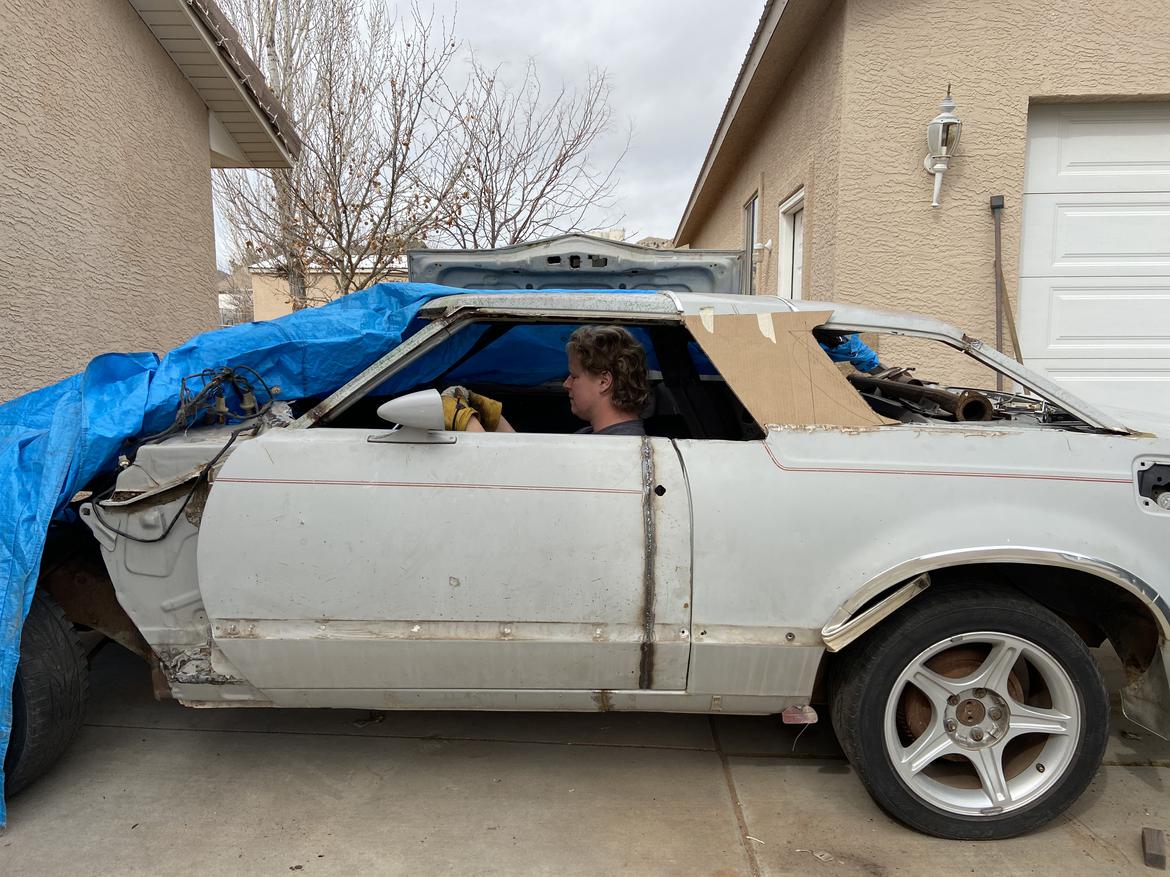
*edit. Tilt steering ftw, thanks Henry.
barefootskater said:
Less metal is less weight. 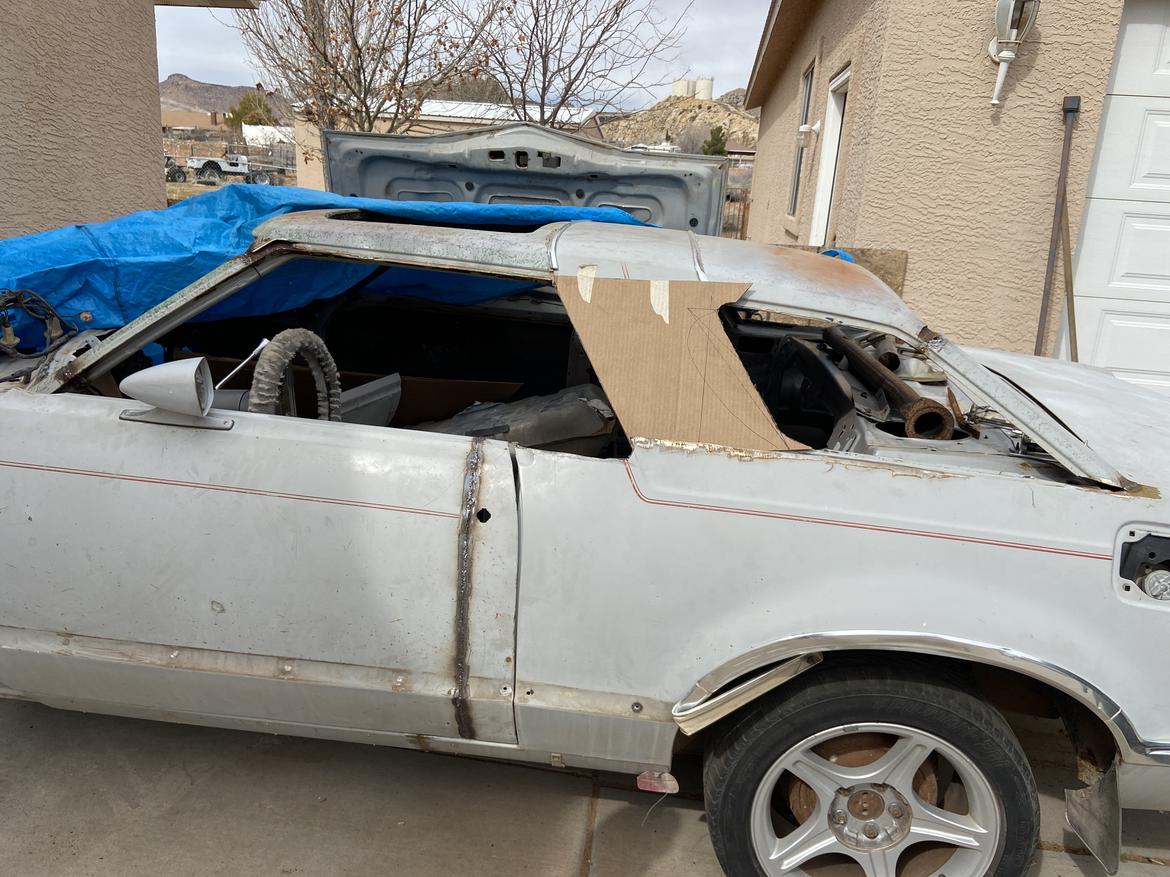
Thats metal as berkeley. Keep on keeping on!
Dusterbd13-michael said:
Thats metal as berkeley. Keep on keeping on!
So you're saying less metal is more metal?
barefootskater said:
Dusterbd13-michael said:
Thats metal as berkeley. Keep on keeping on!
So you're saying less metal is more metal?
In this case, yes. Chopped, sectioned, shortened...
400, oh 400. I spent $85 on an edelbrock performer rpm which has a square bore so it'd need my $5 square/spread adapter. The carb is a Quadrajet and will remain such. I also spent $75 on an edelbrock torker 2 single plane which is spread bore. Or I have the stock cast manifold which was on the 400. I bought a full gasket set for the thing because it was cheaper than buying the intake and oil pan gaskets separately. So I have head gaskets that are already included in budget whether I use them or not. I have evidence this motor was rebuilt and therefor have no idea on cam specs or compression. I'm hesitant to pull the heads because time is tight and it's a rabbit hole. So here's my options:
$90- Performer rpm/adapter (tall combo, would require some hood surgery) as that is easily the best intake for the application. Adapter may do more harm than good.
$75- Torker 2, wrong intake for our rpm range, but cheaper than option 1 and possibly better than stock. Also it is polished so it looks the coolest. 1/3 of the competition is presentation after all.
$0- stock cast intake. Heavy, not great but carbide bits are budget neutral and I like fiddling.
option 3 would be mostly an excuse for me to do some porting. The heads would come off and if clean them up too. But where do I stop? A little more compression is relatively cheap at that point. And reseating and backfacing the valves is free-ish. Port matching obviously.
decisions decisions and time is quietly running away.
Torker and send it. Cant score if it done show up.
And if anyone balks at our sheet metal being free, I present:
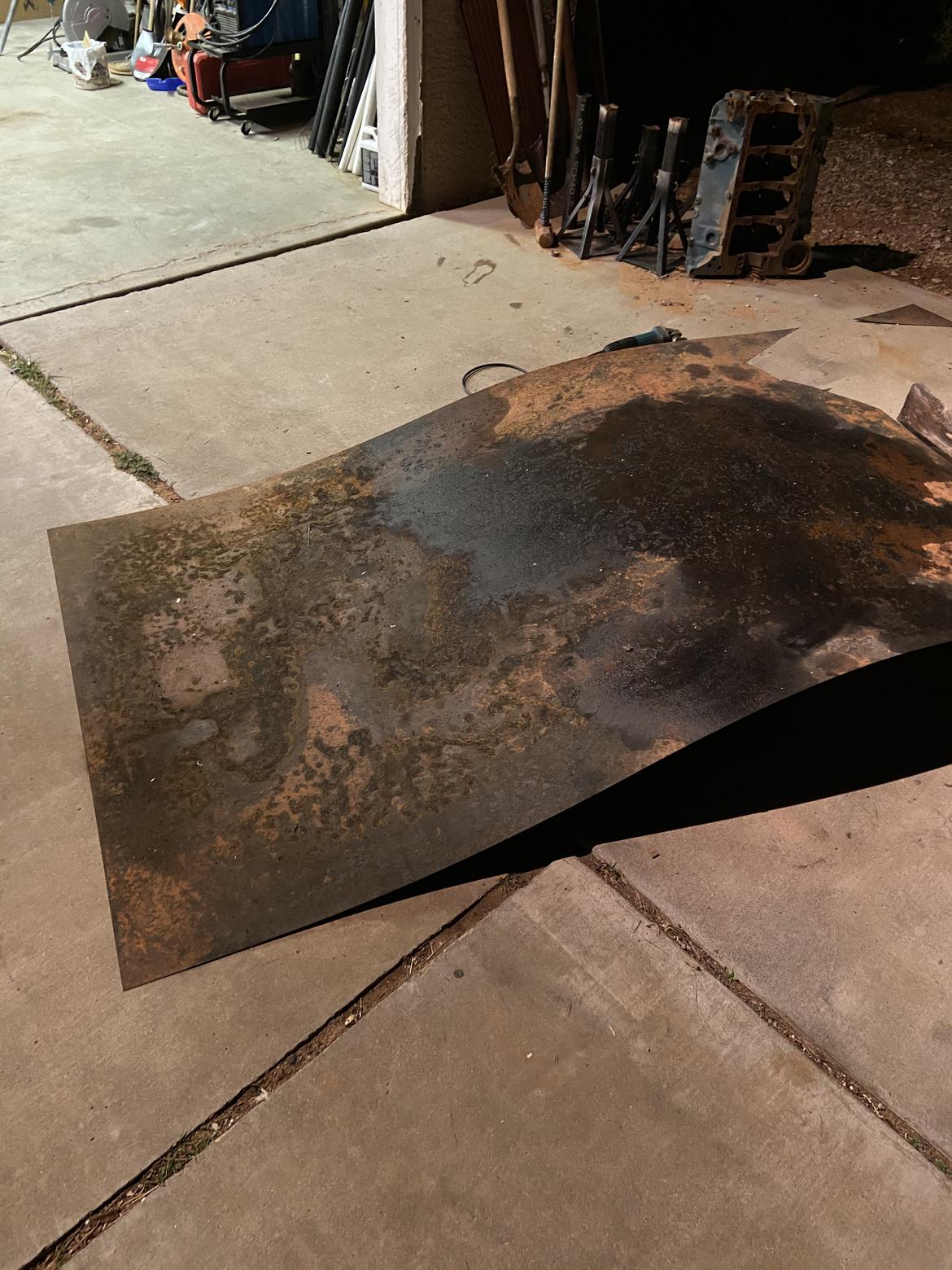
When you need a brake:
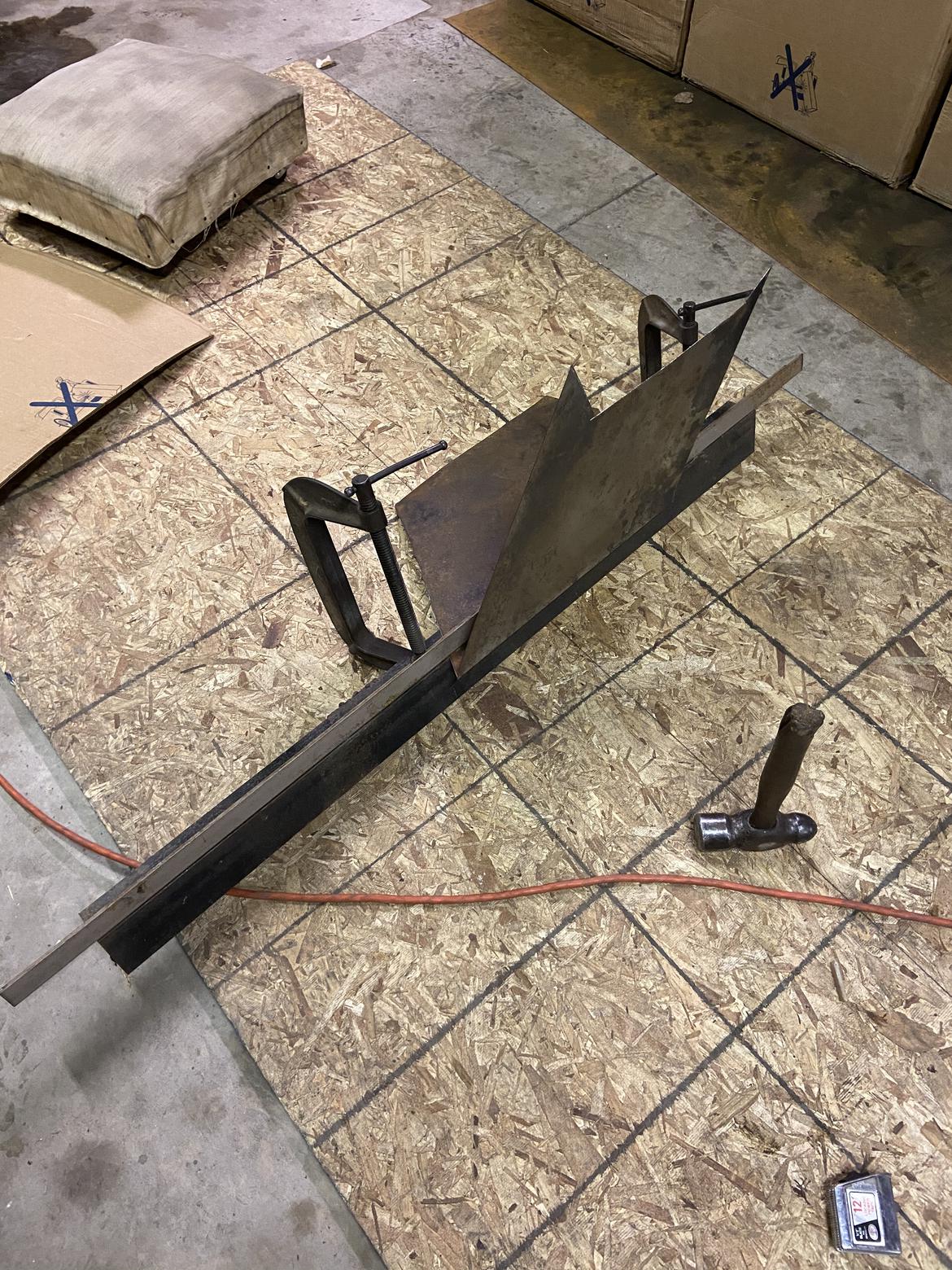
And I present, B-pillar. From scratch:
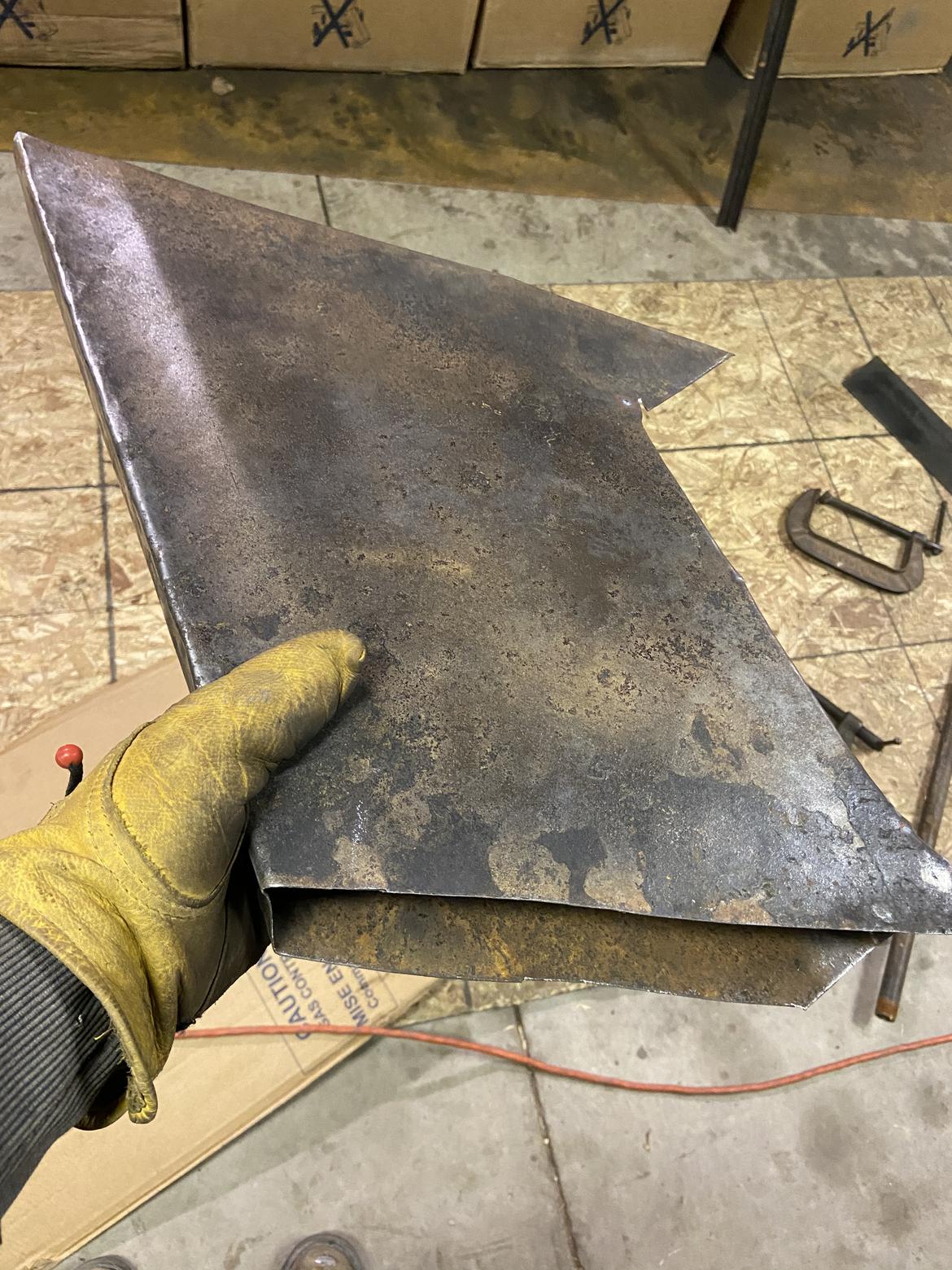
in situ:
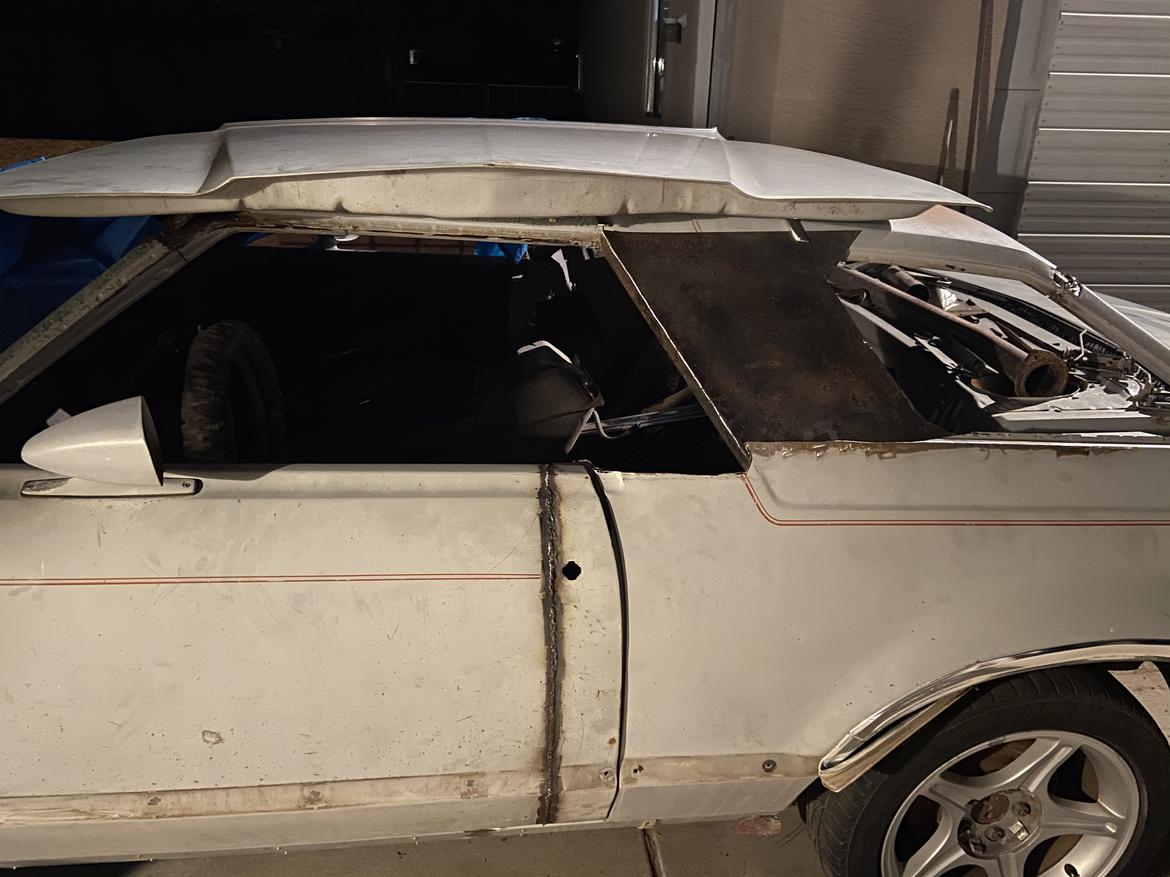
Dusterbd13-michael said:
Torker and send it. Cant score if it done show up.
"Torker and send it."
sounds like something you'd hear from a shady uncle. Not that that is a bad thing. And it would pair well with the "bottom of the page" camshafts that dad keeps trying to talk me into.
So one vote for the Torker. Anyone else have an opinion?
Colored and scribed 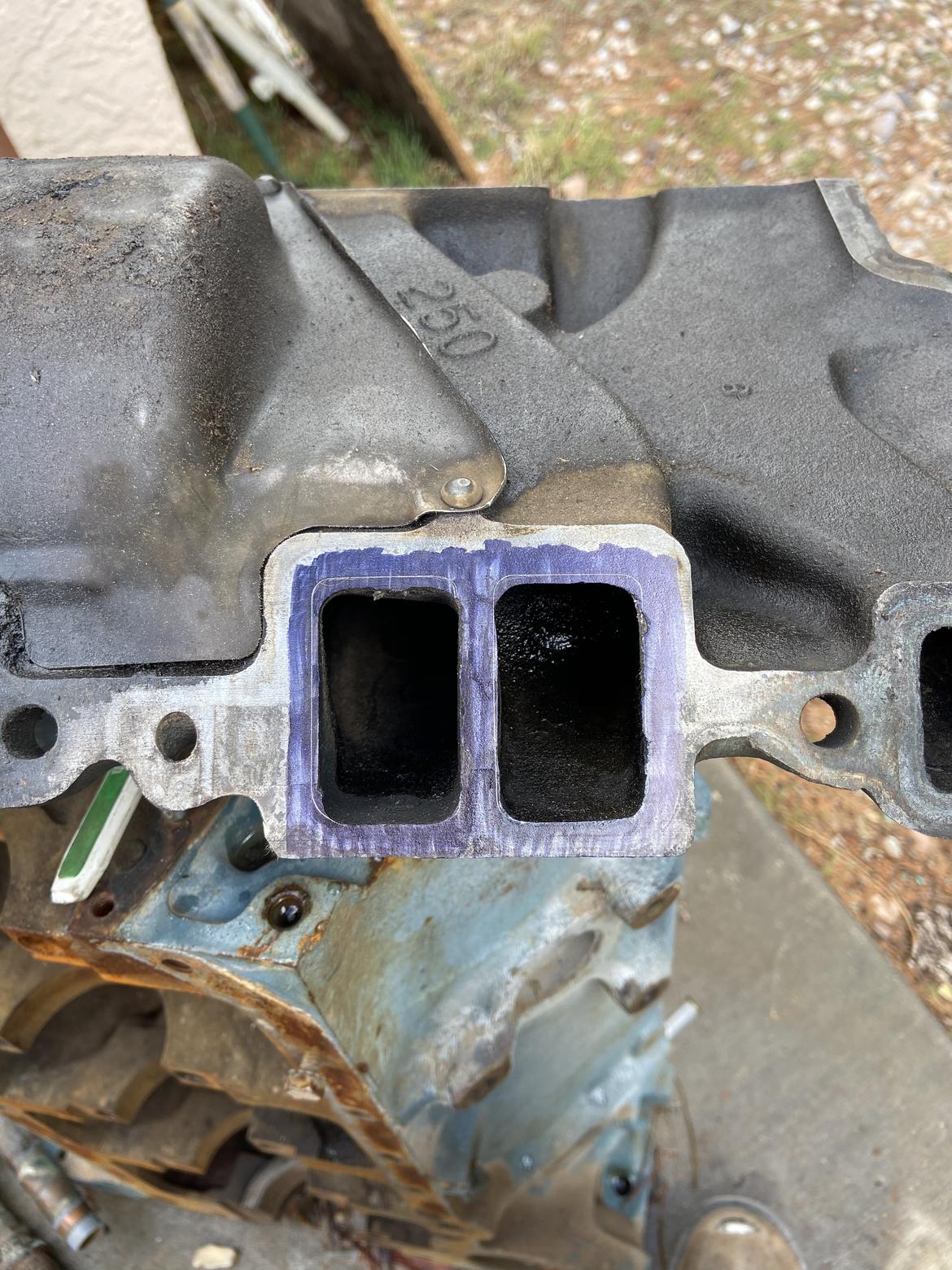
Edges found and blending started. 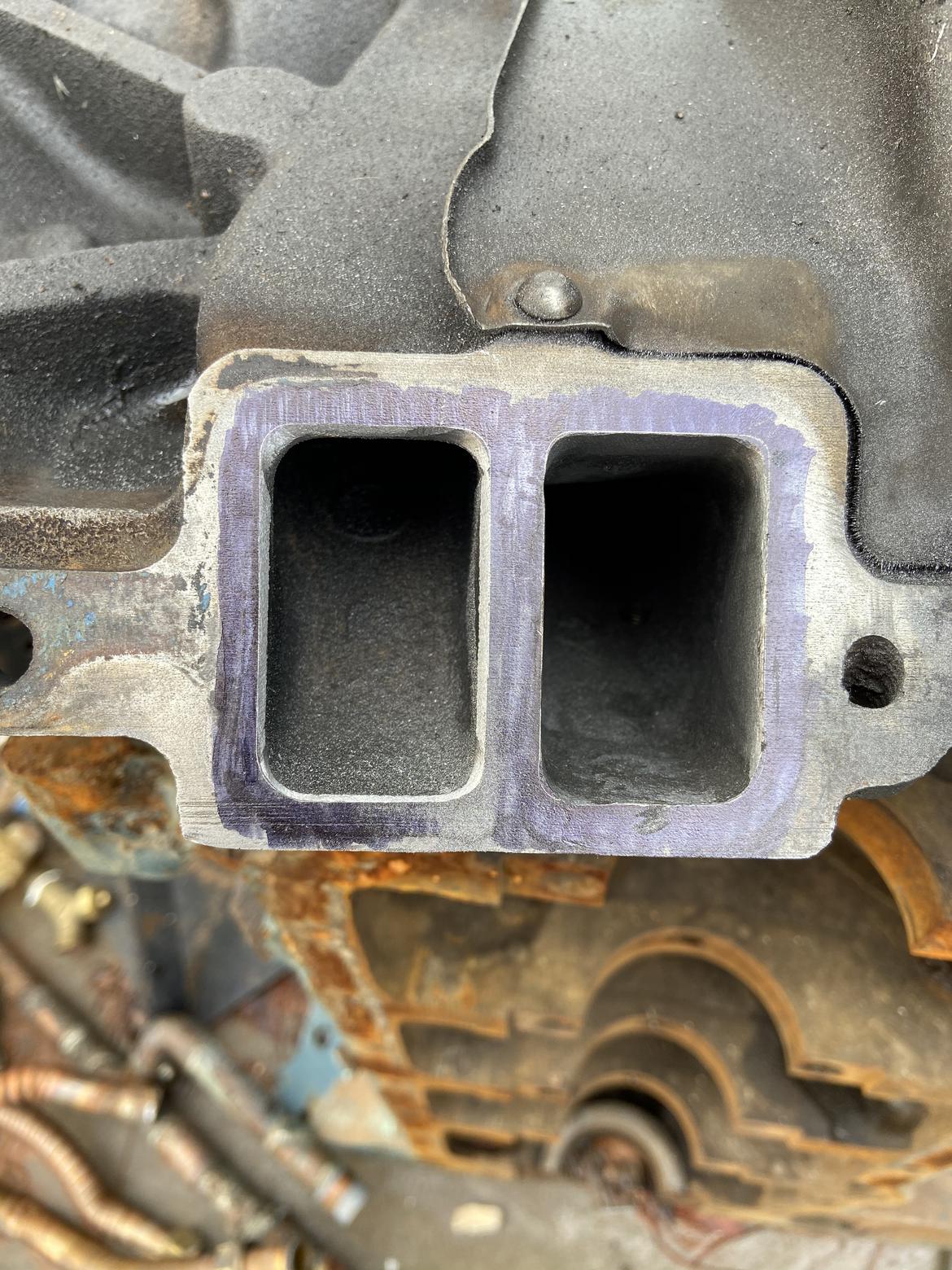
blend blend blend
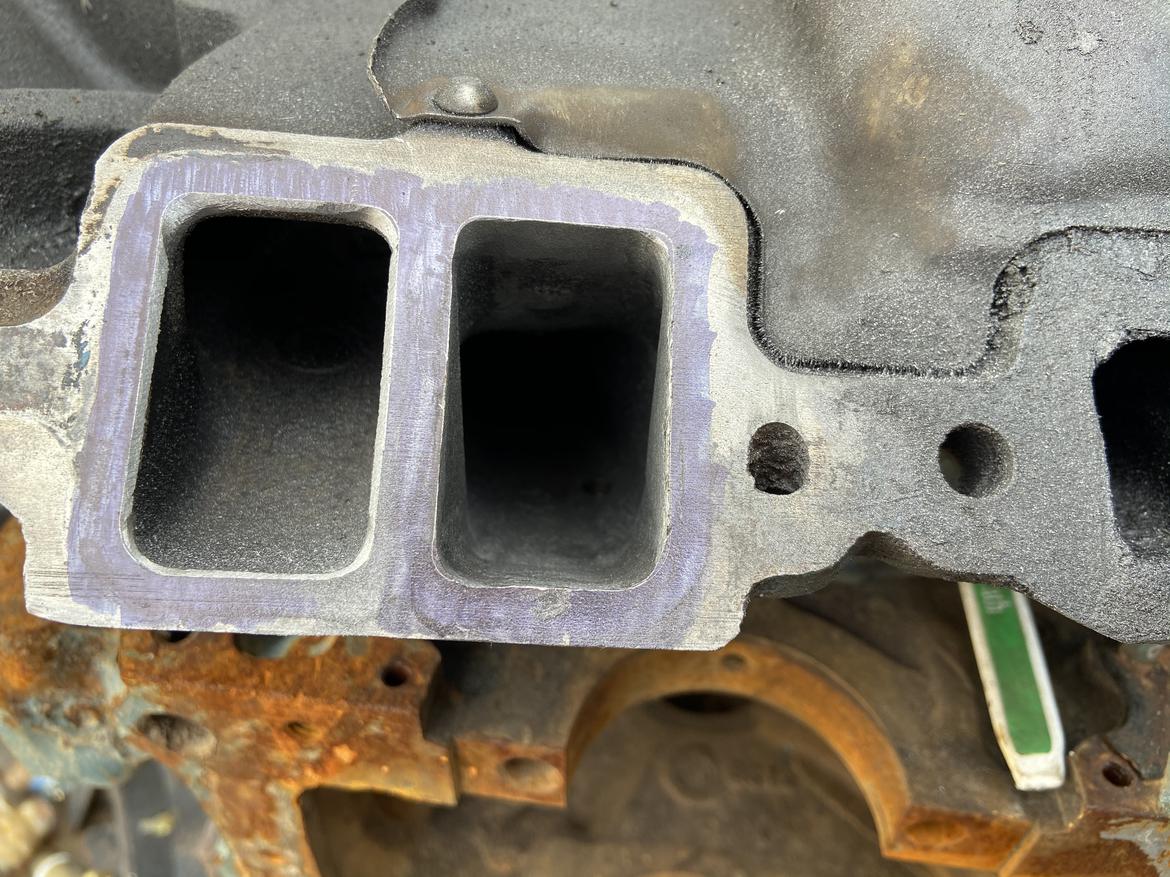
it's not super exciting. But it's progress.