275nart
New Reader
1/18/18 12:50 p.m.
I plan to experiment with an X pipe and without one. The jag firing order is the same as modern v12 ferraris and other high end supercars. This is a near perfect sound to me- certainly a lot of that is intake noise from the webers.
https://youtu.be/0vDqzXcGUIE
Really hard to get this
https://youtu.be/LMNc7LBlWyw
In reply to 275nart :
Go to AJ6 performance to find answer to the question you posed. These guys are really knowledgeable about the V12. Read the bio of the founder.
Medchin
New Reader
1/22/18 11:31 a.m.
In reply to 275nart :
Not planning to make the car any longer, but I do plan to make it wider. The pipe dream is to cut everything from the firewall forward out of the car, build new frame rails that run the length of the car, replacing the rear subframe with new metal in the same step. Then the IFS for the aftermarket support and tunability, 9 inch in the rear to handle the 351 I have for it. Alas all of that is like 2-3 projects down the line. Too many bad ideas, not enough time or money to go around.
Medchin said:
Fantastic thread. My Swedish proclivity it coming out in full force.
Your "body and frame" design, mustang II front suspension, T5, and Ford rear axle is EXACTLY the recipe I'm thinking for my 242 way in the future... however not a V12. Knew it was a proven formula, glad to see equally or more insane people exist in this world with the same serial skill collecting.
I need to shorten my axle about the same you did, I'm curious if anyone has had it done by a specialty shop? Do you mind spilling the beans on how much that costs? I have a 9" for my car with the theory it's way more axle than I'll ever need to make that a part that never needs upgrade so I don't mind spending a little bit to have it done right.
Anyways, look forward to how this goes! If I ever get my 242 build going I will be sure to mention you in beginning so your ears burn and you can come check it out. 
Look into the Moser weld in axle tube ends. They eliminate the c-clip axles and convert it to the 9 inch style press fit axles. Get the small bearing model ends and an explorer rear axle assembly and you can retain the big explorer disc brakes and make it any width you want and jet get a pair of cut to fit axles. You can also get the axles drilled with a 5x108 pattern if you want to keep the stock bolt pattern. I am in the process of building one for my 2J powered 93 960 and then one for my friends 2J powered 79 242.
275nart
New Reader
2/22/18 9:08 a.m.
I took the car to a friend's shop who does roll cages and traded him some welding work for this. We bent and tacked some 1 5/8" down bars to connect the A pillars to the frame rails. It's surprising how much this changes the look of the car at it's current state. Even though these bars will not likely be seen once the body is on I'm pleased with the design, clearance, and finished look. It also gives me something to build the radiator and bumper support from- I'm thinking I may make that removable so the engine is easier to remove and install later. I will be finishing the welds on the down bars soon and will seal up and epoxy prime the front end, firewall and floors. There's a little surface rust starting to develop, especially after transporting the car in this humidity, and I want to nip that in the bud before it gets out of control.




Hey, fairly new to the forum (or at least when it comes to posting). Great build you have here! I'd like to apologize in advance for not reading the entire thread, but I thought that maybe I could lend a hand if you haven't already started making the body.
As for how I can help: I work with industrial 3D scanners (check out http://www.gom.com) and could easily scan a scale model of a 275 GTB if you have one that you wouldn't mind lending out temporarily. The model can be scaled up and then cut into sections which can then be print and used as stencils or cut out with a CNC router.
Just DM me if I can help at all.
275nart
New Reader
3/2/18 5:48 p.m.
I'll send you an email. You could definitely help! I am local (Fort Mill) too
It was very difficult to find this model BTW!

WillHoonForFood said:
Hey, fairly new to the forum (or at least when it comes to posting). Great build you have here! I'd like to apologize in advance for not reading the entire thread, but I thought that maybe I could lend a hand if you haven't already started making the body.
As for how I can help: I work with industrial 3D scanners (check out http://www.gom.com) and could easily scan a scale model of a 275 GTB if you have one that you wouldn't mind lending out temporarily. The model can be scaled up and then cut into sections which can then be print and used as stencils or cut out with a CNC router.
Just DM me if I can help at all.
In reply to 275nart :
Oh nice! I'm located near UNC Charlotte, so maybe 40-ish minutes north. That would be a pretty simple scan but I'll be sure to be careful with the model! Email would work much better since I'm still not sure how to access the messaging on GRM... If it even exists.
pres589
PowerDork
6/19/18 1:38 p.m.
Bump for updates? Been a while since this thread got some love.
NOHOME
UltimaDork
6/19/18 9:55 p.m.
was wondering where you got to with the project.
Every time I walk by, I kind of chuckle over the antics that hat to take place to get the door skins from your car on to the door frames of the Molvo.
Pete
275nart
New Reader
6/25/18 11:13 a.m.
It has been a bit since any update! I have done a few things here and there but have been on a slight hiatus. I buttoned up the trans tunnel and cut down the doors (skins went to Pete for his Molvo) and fitted up the door frames to see what I'm working with. I need to do some more trimming and then I can start fabricating the jambs. There are tons of little holes here and there in the floor needing to be welded off, seam sealed, and primed. That's all the stuff I'm dreading so I've been putting it off.
In other news willhoonforfood came by and is helping me out a ton by scanning the scale model for me. I need to check back with him and see where that's going! But what he showed me he can do with scanning parts is beyond cool.
NOHOME said:
was wondering where you got to with the project.
Every time I walk by, I kind of chuckle over the antics that hat to take place to get the door skins from your car on to the door frames of the Molvo.
Pete
Did you use them both Pete? It looks like the passenger side worked out really nicely for you.
275nart
New Reader
6/25/18 11:38 a.m.

Rough idea how it's coming along. Since the photo I took in the garage is a lot wider angle than the one I superimposed on top it sort of goofs up the proportions
NOHOME
UltimaDork
6/25/18 1:18 p.m.
In reply to 275nart :
Just the PS one. I already had done a ton of work on the DS and while it might have a full skim of mud, it was looking real good and I am too lazy to go back!
If I find a worthy recipient for the DS I will pay it forward.
Pete
275nart
New Reader
6/27/18 11:19 a.m.
I know the feeling. I hope someone else needs it!
NOHOME said:
In reply to 275nart :
Just the PS one. I already had done a ton of work on the DS and while it might have a full skim of mud, it was looking real good and I am too lazy to go back!
If I find a worthy recipient for the DS I will pay it forward.
Pete
Quick insight into what I do: I'm an application engineer for an industrial 3D scanning manufacturer. We manufacture both structured light scanners and x-ray CT scanners (that's my baby). The setup I used for this scan is our entry level scanner. It's simple to setup and scan...
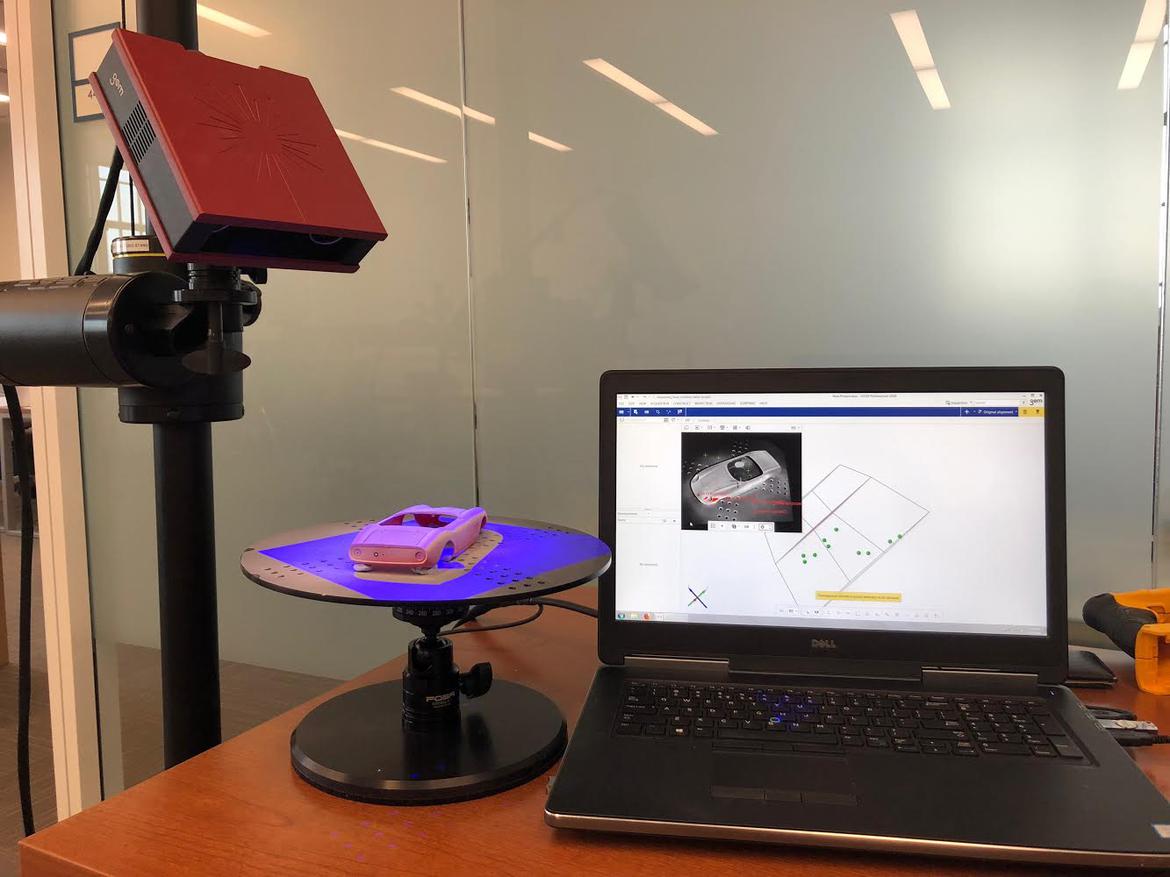
This picture just looks cool. We use blue light in our projectors since most indoor lighting doesn't cause interference. The projectors project light patterns onto the object, and the 2 triangulated cameras take a picture. After a bunch of math, a point cloud is created and is turned into a super accurate surface... Pretty trick stuff.
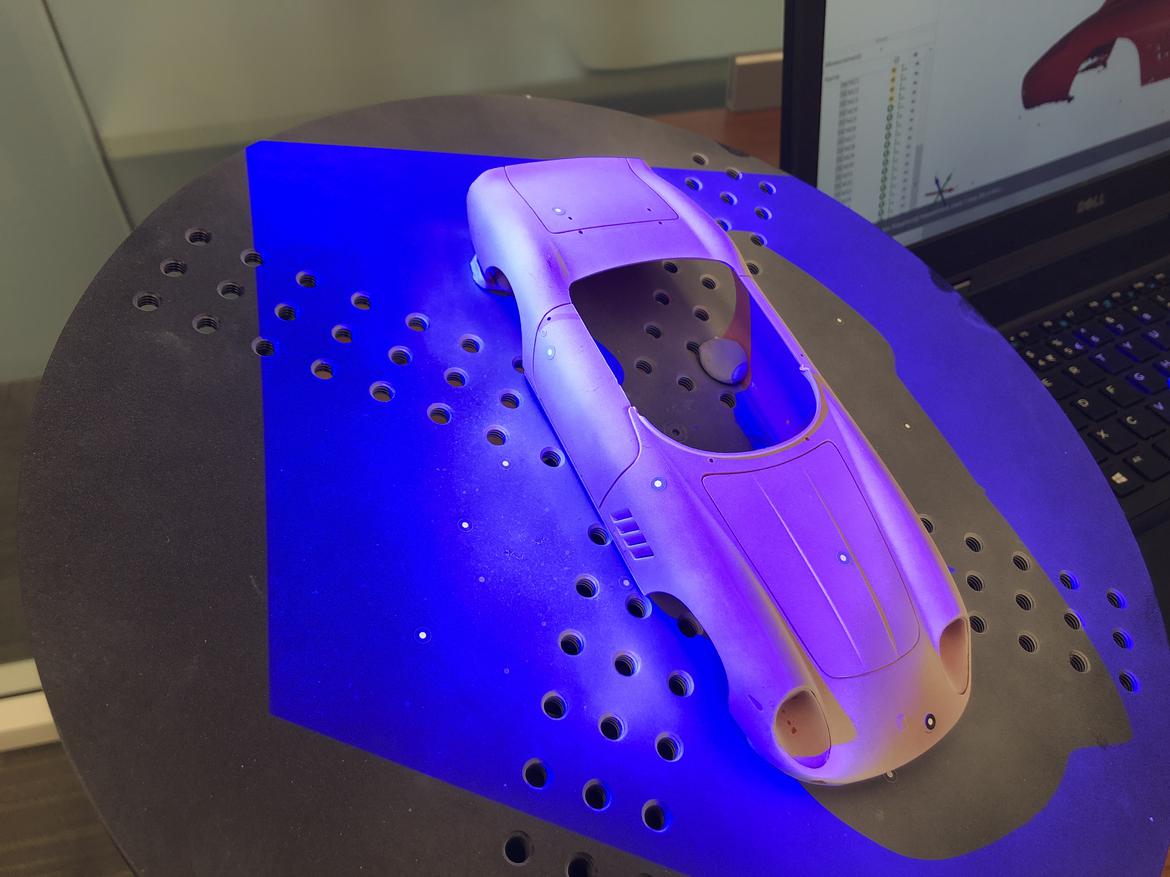
This is the final mesh that's created.
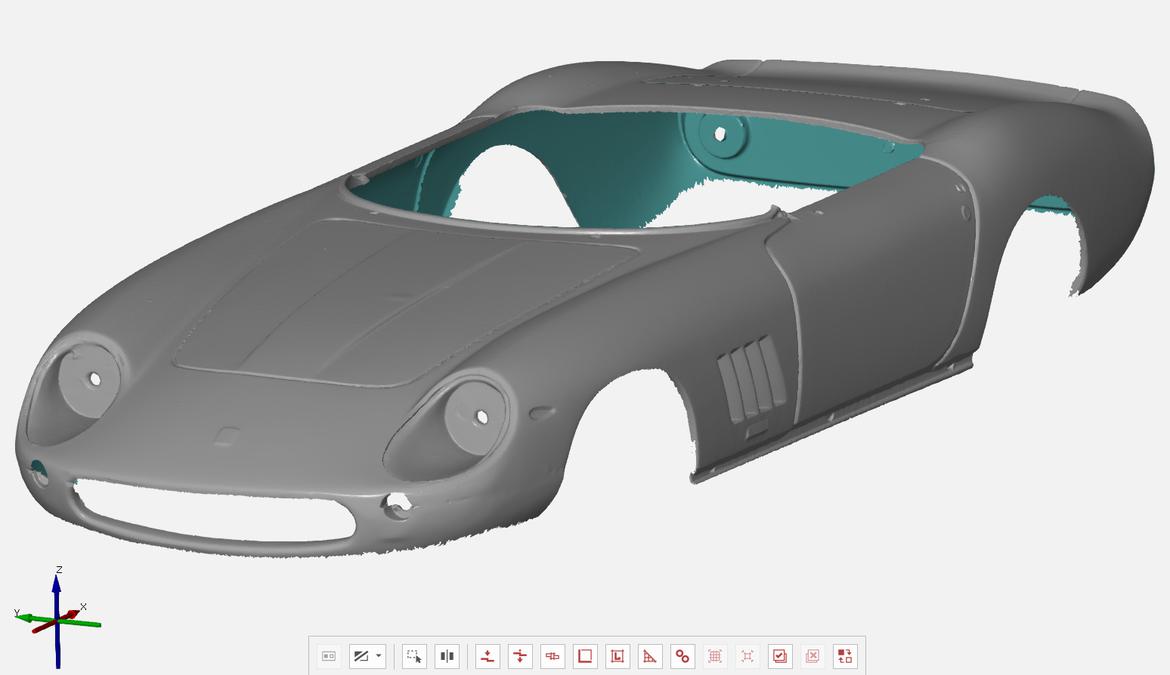
I think this is kind of cool. It's basically all of the triangles that are created from the point cloud.
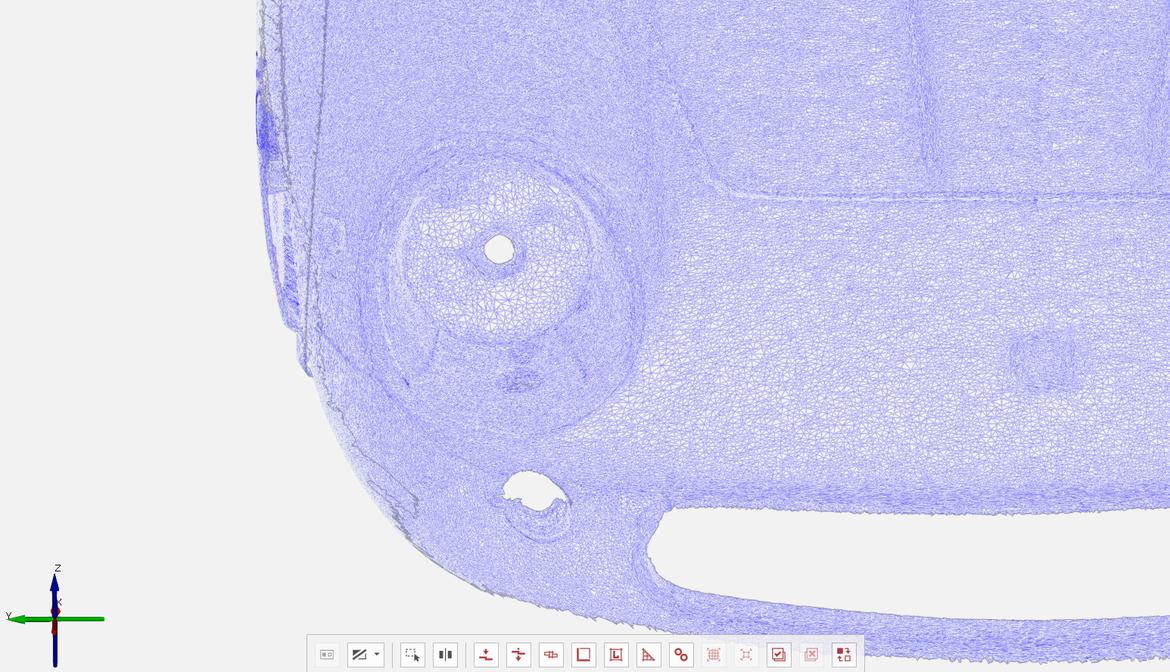
Wow, impressive in ambition and scale!
275nart
New Reader
8/23/18 9:31 a.m.
Jon has done an awesome job with the scan. Honestly a lot of it goes over my head so I'm hoping I can translate the 3d model/ slice it into 2d sections and build the wire buck from. I have a few ideas for that- either using a projector and tracing, CNC cutting cardboard, or printing each section on drafting paper.
This is a very nice example of what I'm shooting for to build the body off of.

NOHOME
UltimaDork
8/23/18 9:50 a.m.
Why a wire buck? I would expect that with digital models in hand, it would be easy to create the lateral and longitudinal slices that could be cut out on a water jet for a traditional wooden buck?
Pete
275nart
New Reader
8/23/18 11:28 a.m.
NOHOME said:
Why a wire buck? I would expect that with digital models in hand, it would be easy to create the lateral and longitudinal slices that could be cut out on a water jet for a traditional wooden buck?
Pete
Pete,
A wire buck will be nice because I can fix it to the car (if you can even call it a car at this point) and make minor adjustments where needed. I don't have the space in my workshop to have a buck separate from the car. There's a corvette in there right now too.
No matter how good digital tools are, there's no substitute for seeing the parts in the metal.
You might want to split that .stl down the middle and mirror the better half. There is a good chance of the plastic model being a little asymmetrical.
ATOS Core? Those are neat. We have a compact scan 5mp I love using. Some days I wish we had sprung for the triplescan though.
I can't wait to see how this body turns out. One day I want to build my own large format 3 axis router so I can machine big blocks of foam from scans like that.
275nart
New Reader
8/23/18 12:27 p.m.
In reply to mblommel :
You'd have to ask willhoonforfood. This is totally out of my wheelhouse. He already suggested splitting and mirroring it and I think that's the best route to go although some of these real ferraris were off up to an inch or more per side!
Keith Tanner said:
No matter how good digital tools are, there's no substitute for seeing the parts in the metal.
Thank you for the encouragement? I guess?
Oh, definitely encouragement. I've moved designs from the digital realm to the real, and then made adjustments once I actually saw it. I think you're doing just the right thing.
Plus those wireframe models look so cool.