Rather than slog through a blow-by-blow of every nut, bolt and weld joint of this nearly 2-year-long ordeal (which might be therapeutic, but might also induce a bit of tedium...), the goal is to outline steps of significance, and areas where I diverged from Volvo's original design intent. Here we go.
While relatively solid, as 50 year old cars go, as you might imagine there was still some non-trivial amount of corrosion to contend with. As 50 year old cars bought for LeMons sums of money tend to go. Stuff like the driver's floor, underbody/ unibody structure, and trunk floor all needed some care. In the case of the latter, since the goal for this was to create a racecar, the OEM gas tank was pitched in the recycling bin, and the trunkfloor completely redone for a fuel cell. After removing the cruddy, leaky, stinky old tank (which protrudes through the trunk floor in a totally unsafe way, like many cars of this period), I cut out the majority of the trunk floor.
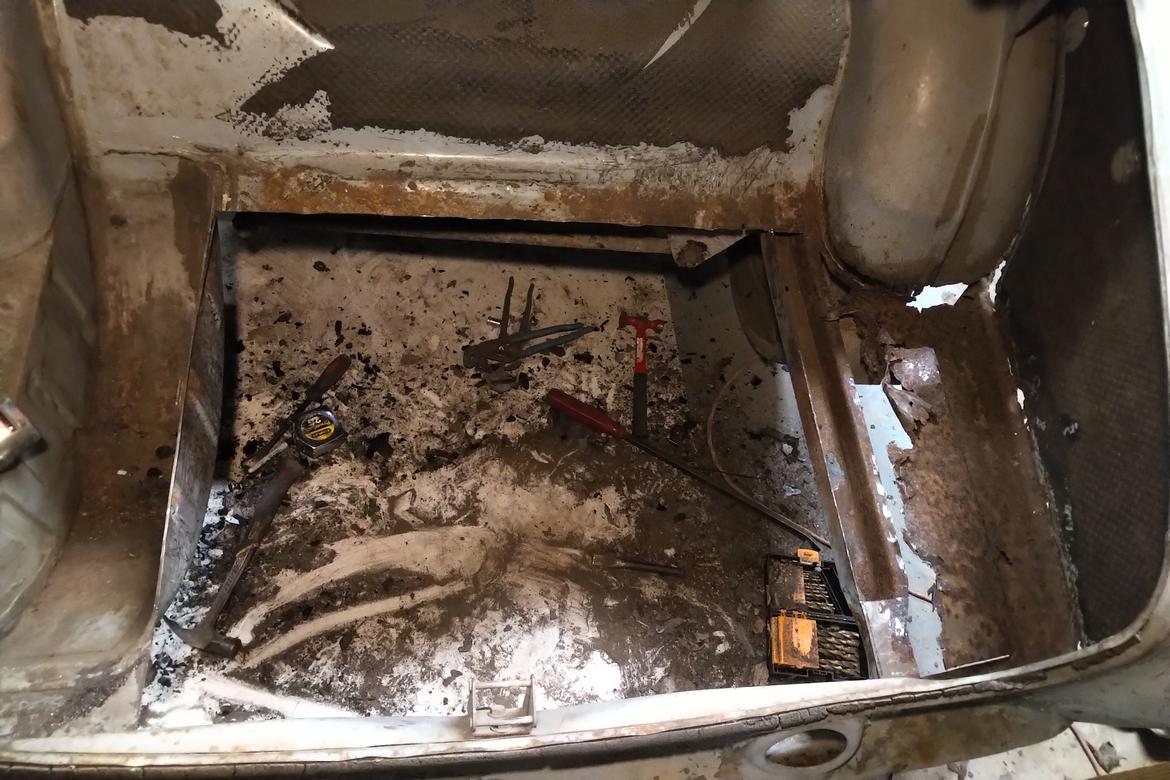
My shop is what I would call "moderately equipped", in that it possesses most of the tools one might desire to perform most tasks. The key modifier being "most", and the key concept being "perform". What that all boils down to is that the ideal tools to perform tasks as expediently and well as possible do not, in fact, always exist. Like, for example, metal bending and forming. Where a "well-equipped" shop would contain breaks and shears and English Wheels and all other manner of expensive and real-estate consuming apparatus, in my 18' x 27' lair those are replaced with:
1) A multipurpose steel workbench, quite heavy
2) Clamps, vice grips, mallets, and other instruments of general use.
In my defense, such tools are generally used to somewhat acceptable effect:
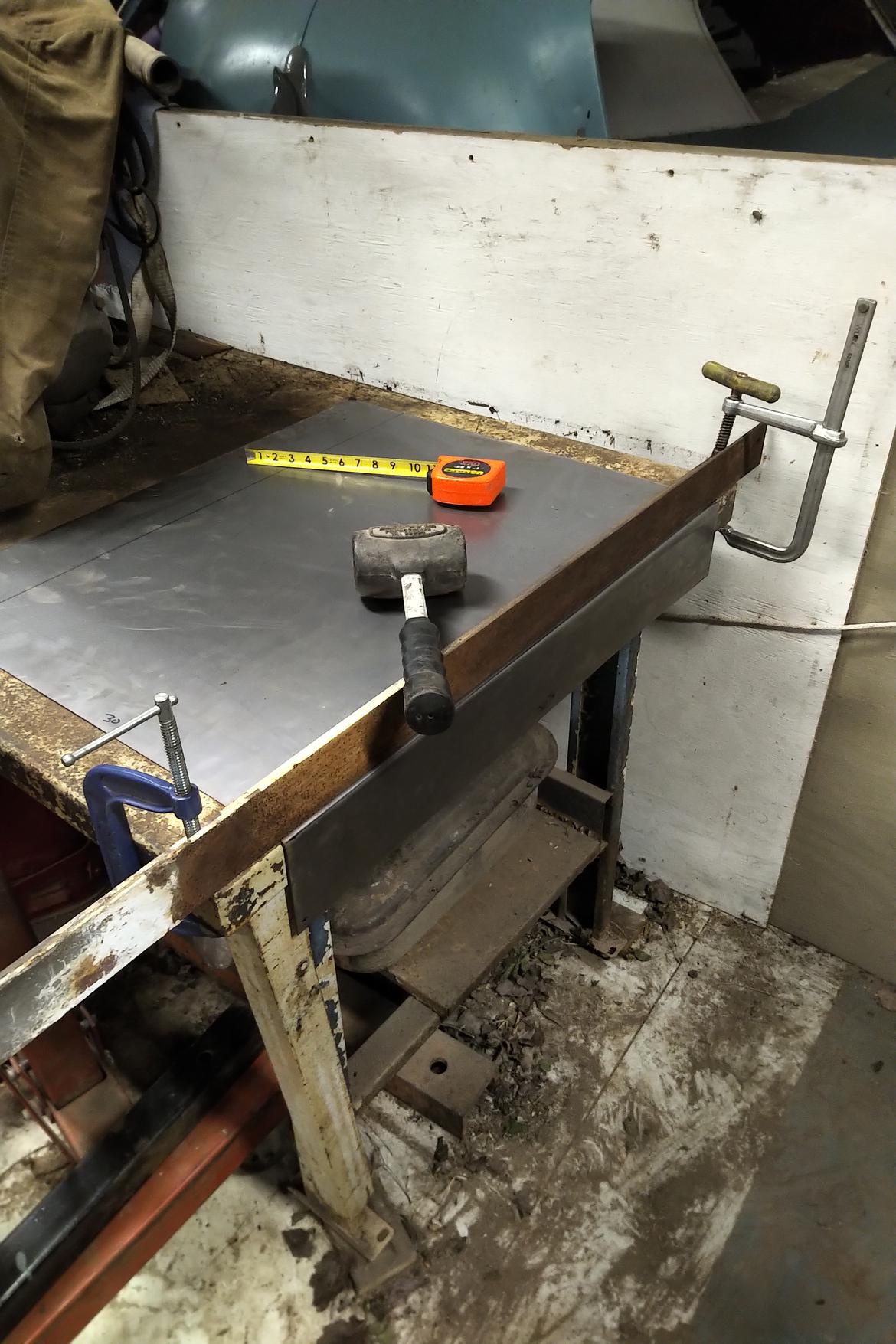
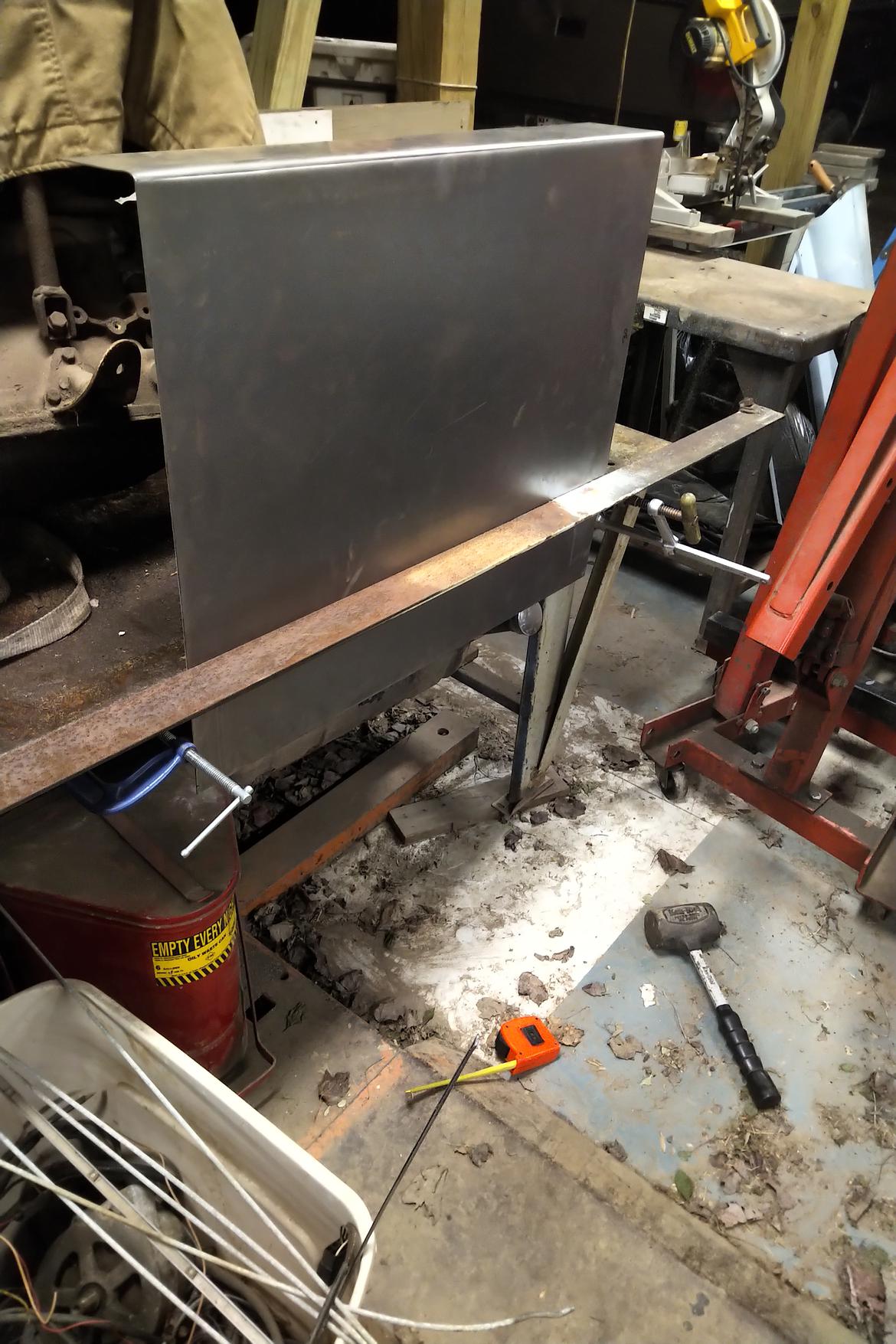
That giant steel workbench (It measures approximately 3' x 6') was salvaged from a place I used to work at, for the princely sum of twenty dollars. Angle iron makes a great break clamp.
Plenty of measuring, bending, cutting and tack-welding yielded encouraging results:
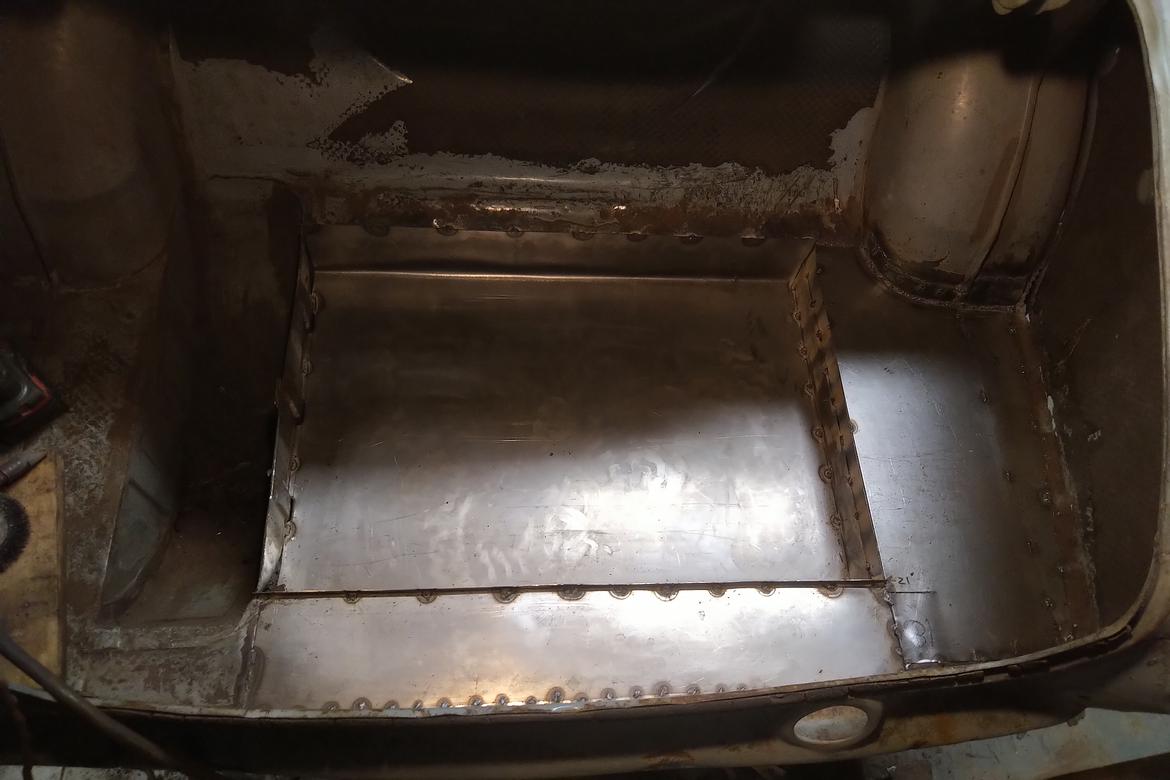
The trunk floor is dropped down about 4" where the fuel cell will ultimately sit, thus lowering the center of gravity of the tank and providing enough area to fit a tank with more volume than stock (good for endurance racing, where fuel stops are a time wasting annoyance). It also provides a significant level of protection over the stock fuel bomb. The eagle-eyed observer will note that I took the time to correct all the little bits of rust perforation here, including the edges of the wheel wells and the sides of the trunk floor. I also drilled out the spot welds and removed the brace for the trunklid catch; it was badly mangled and will be replaced with better reinforcing and trunk latch mounting.