My challenge car has a solid rear axle and leaf springs. Originally, I was planning on keeping them for the initial build, but now thinking it'd be easier to just improve it from the get go. My engine donor is a Trailblazer, with a 4 link and panhard bar. Been doing a lot of reading, both old threads here, on the web in general, and my old copy of How To Make Your Car Handle(which doesn't really have anything for this comparison), and it seems like for autocross, a 3 link would be favored over a 4 link, but I am curious as too how much. The 4 link would presumably be a bit better for the drags, but 2005-2014 Mustangs seem to do well with a 3 link, so I probably should not overemphasize that. Especially with some caveats for budget/time/fabrication capabilities.
Here's what I would be starting with:
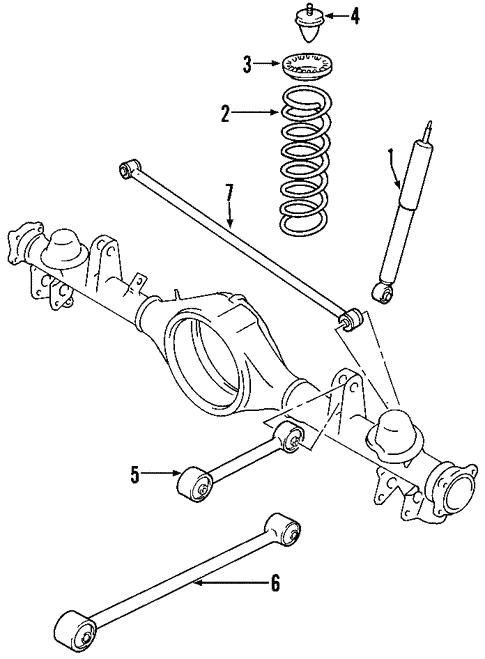
The upper arm is shorter than the lower, but I think it might be exaggerated in the the picture. I'll know better when the truck is in my possession. However, I should be able to lengthen the bars and make them adjustable fairly easily and cheaply, so I may be able to get them set at equal length, if needed. If I were to go to three link, I think I would keep the lower trailing arms, and would have to weld a bracket to the differential (cast iron?, probably not easy with my equipment/skill level) or fab up a bracket that mounts to some of the bolt holes for the diff cover.
Things of note:
- The four trailing arms are parallel(ish), but are not in the same plane.
- Due to budget, there's a good chance everything will use rubber bushings rather than heim joints. To me, this is the big question mark that makes me wonder if the three link will not be much of an improvement, due to the center link resisting flex too much.
- Springs/shocks may be non-adjustable, or at least only having a few mounting holes at the upper perch. Depends if I can fit coilovers/adjustable shocks into the budget.
- Both the challenge autocross lot, and my "home" lot are not the smoothest in the world, so whichever setup can be made to handle rough surfaces better would be ideal.
- If I go to the trouble of building a bolt on bracket for a three link, maybe it would make sense to also set up a watts link instead of the panhard bar.
- I do not have a mill or lathe, pretty much all fab is done with an angle grinder, bench grinder, and a very janky drill press.
Any opinions on which way to go? Also, any other books or websites I should be reading for more info?
Watching due to similar yet different project interests. Don't have much real world personal experience so I won't comment further as I want to help keep signal up and noise down in your thread.
Driven5
PowerDork
10/24/24 1:11 p.m.
While there would be some difference in how the axle tubes deform under load, 3 link and 4 link geometry works the same for drags. Also note that all link bushings get twisted similarly in roll, not just the 3 link upper.
The main constraint for a 3 link is it can force a rather short upper link and extra care has to go into reinforcing the upper link chassis mount to not tear out under acceleration.
From a fab standpoint, offsetting the upper link to the passenger side helps balance the torque reaction. So you could weld the bracket to the axle tube next to the center section and still be just fine or better.
The main constraint of a (non-triangulated) 4 link is that it is by nature over-constrained. Even with full sphericals this can be largely mitigated by having the upper and lower links non-parallel in side view, converging a little closer (3/8-3/4 in/ft) on the chassis end than axle end. Rubber bushing (stock arms) largely makes it irrelevant too though.
Assuming the odd bolt pattern isn't a concern for reusing this axle, I'd say go with whichever is the cheapest, easiest, and fastest to package with decent geometry. Either way, I suspect you'll need to fab some new brackets for it.
If I go four link, I am hoping to stick with the brackets on the rear axle. No matter what, I will need to fab new frame brackets.
I did quite a lot of reading when I was ready to change from the leaf spring suspension in my '64 Ford F100 restomod/pro-touring build. I decided that I would never be a good enough driver to be able to tell the difference between a triangulated 4-link and a 3-link. This video helped me make that decision:https://youtu.be/Pq5LjV4lnV0?si=Hb-AAlGYngfswVd1
One advantage with my truck is that I have lots of room to work with and I can take the bed off to access the rear suspension. In the end I went with a parallel 4-link kit with a Panhard rod and coilovers from No Limit Engineering, primarily because of the adjustability of this kit and the reputation of the builder.
For a Challenge car, I'd go with whatever system fit the easiest/ best and build in as much adjustability as you can.
buzzboy
UltraDork
10/24/24 2:05 p.m.
I've seen plenty of rockcrawler builds with a 3 link where the link is offset to one side of the differential. I don't feel like I see it as much in the onroad builds. Not sure why.
except for the shock mounts, that looks like the rear axle from a fiat 124 spider (original, not the Fiata). It's a very good design.
I changed my AE86 from its unequal length 4 bar to an equal length 3 bar and adjustable height(both ends) panhard bar.
Worked very well,no axle hop on launch and put power down from the turbo'd 4ag with less drifty drifty lol.
Lighter and probably less work to build.
I'm wondering how short the 3rd link in a traditional 3-link suspension can be (so, not a torque arm) in relation to the lower pair of links. Like, can it be 1/2 as long and still "work well" or can it be shorter etc etc. Is there a rule of thumb?
To the OP, if you've got the factory Trailblazer 4-link setup, I wonder if making the springs stiff enough to not allow a lot of motion will negate the potential negatives of going with that configuration vs. something more optimal, making this "optimal enough".
In reply to pres589 (djronnebaum) :
i don't have a measurement, but i've seen pictures of the 3rd link on the S197 mustangs and it looks pretty short (~6-8"). And from what i understand they handle pretty well
In reply to budget_bandit :
Agreed, but if we're building something and cutting a bit of the floor is acceptable, how far should one go? I have a smaller car in mind that came with leaf springs in the rear and would like to change that whole situation for something better.
Probably smarter than using some rule of thumb as a general guide would be to get the rear target vehicle and take some measurements of things that would be harder to change and then use math and such to put together a plan for that specific application.
Quick update to this one, now that I have the Trailblazer in my possession. The upper trailing arms are actually considerably shorter then the lowers. Once it is out and able to be mocked up under the S10, I'll have to see if it makes more sense to lengthen them, or try to fab up a bracket to convert to three link.
"Torque arm" he shouted into the void
Pete. (l33t FS) said:
"Torque arm" he shouted into the void
Since I have to convert the transmission from 4WD to RWD, I suppose snagging the tailshaft casing from an F-body is an option.
In reply to eastsideTim :
i wouldn't. just build a mount on the trans crossmember and don't route all that force into the tailshaft
eastsideTim said:
Pete. (l33t FS) said:
"Torque arm" he shouted into the void
Since I have to convert the transmission from 4WD to RWD, I suppose snagging the tailshaft casing from an F-body is an option.
It would be much easier to just mount a torque arm to the trans crossmember. And better for the transmission.
Sounds like I have another suspension design rabbit hole to wander down.
There's also this style torque arm which allows articulation, also serves as a driveline loop. It's anchored to the top of the trans tunnel with large dia rubber bushings, basically machined hockey pucks...
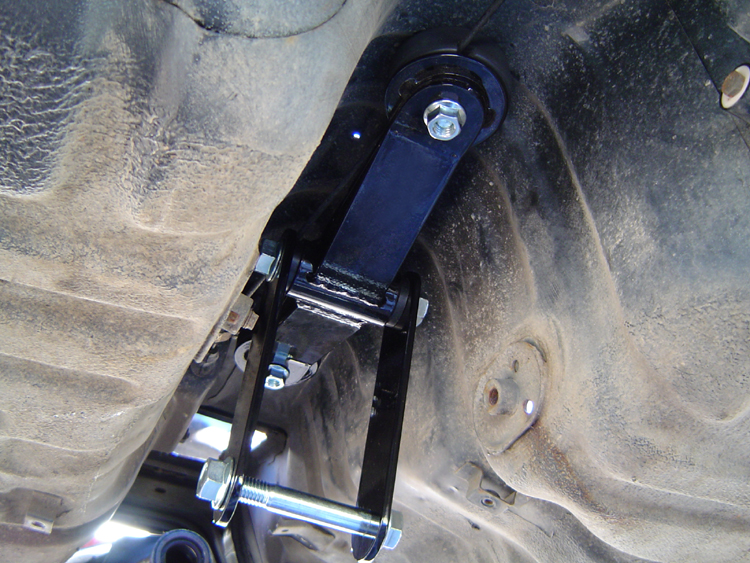

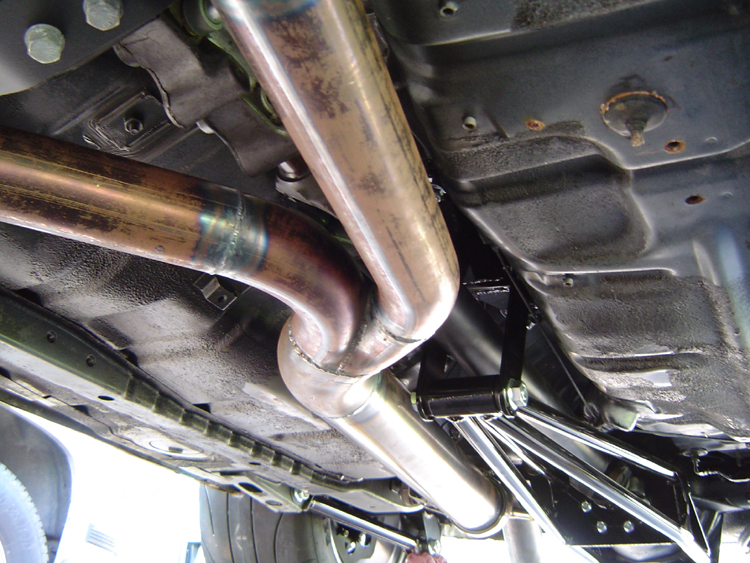

Grant