I'm starting a Challenge car and it needs inner and outer rocker panels replaced. I need to cut and bend the sheet steel to shape. Any suggestions on how to do this at home in the garage without a shear and a brake. I can probably cut the sheet with 4" discs on my right angle grinder, but the bending will be the problem I think.
NOHOME
SuperDork
6/19/14 6:56 a.m.
How long are the sections and how deep are the bends?
The short anwer is to clamp the shee between two pieces of angle using a vice.
If the bend is long, then perhaps you will need to drill a hole through the middle of the angles and sheet so that the middle bit stays tight. especially if it is a ddp bend where you cant get a clamp in the middle of the work.
What gauge are you working with?
If you have the angle stock, its not too hard to use a third piece and make a half decent brake using a couple of hinges. Dont be afraid of having to drill a few holes in your sheet metal to hold the whole sandwich together, easy enough to weld those up later.
If you have a press, you can make a simple set of V blocks and feed the tin and sideways.
Or the next time you are in town, you can bring it here and use the shear and brake!
I bought a cheap sheet metal brake, it's very close to being reinforced bed frame rails welded together. You could make your own.
But I think the answer you are looking for is a very straight 4x4 piece of wood (or strong straight metal table edge) a bed frame rail, some hammers, and a bunch of clamps. Clamp the sheet metal between the rail the hard place, and bend by hand or hammer. A Little At A Time, bend by hand at first.
(Also a lot of hot rodder and circle track guys have suprisingly large brakes in their garages, so make friends.)
I've bent long sections by the spin_out method. A dead blow hammer is your friend here, along with some serious C clamps. As far as cutting it, there are large (4 or 4 1/2") cutting wheels that will fit a side grinder that work pretty well but it is noisy as hell and will tire you out. Advice: if you have to make a short lip, say 3/4" tall, do the bend before the cut. You'd be surprised how hard it is to bend that short a lip in 20 gauge sheet.
Like they said - you can mimic a brake pretty easily with some angle iron and clamps. Don't forget a little heat! A propane torch, or even working outside on a sunny day, will soften it up and help with the bending. You'll probably be using 18 to 20ga, so this will work well for you.
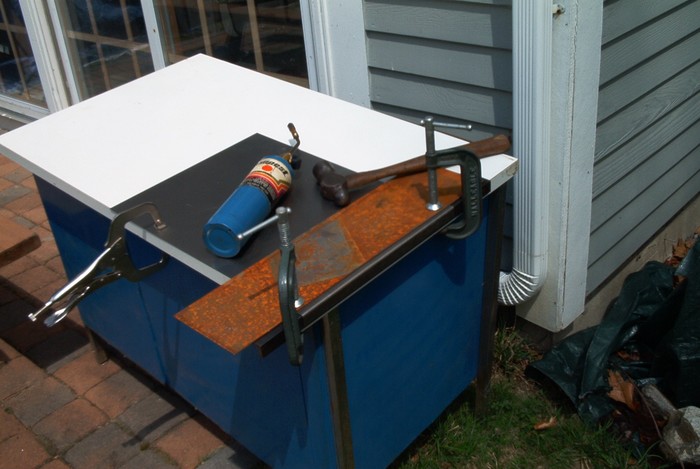
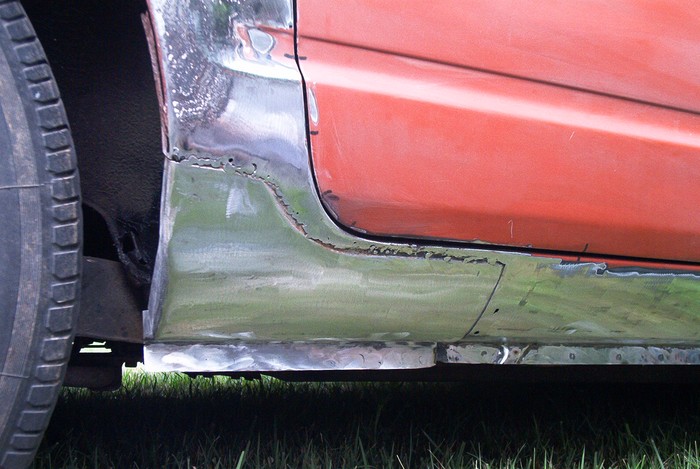
In reply to NOHOME:
IF I had access to a really large brake, like the one in my old place of employment, I'd make a single section that would go from the front fender all the way to the rear wheel well. That's just shy of 5 feet. The door opening section would be shorter at 42". I could make shorter sections and butt weld them together. There would need to be a Z bend in both the inner and outer sills. These would require two bends, in opposite directions about 3/4" apart. I'm thinking I can make the whole thing in two pieces, an inner sill and the outer sill.
I wonder if I could do the bends by using some heavier angle sections , or solid square bar as a V block and squeeze it with large C-clamps.
In reply to Curmudgeon:
The flange where the inner and outer sections are welded together is about 3/4" on both pieces, so I'll remember to bend them first, then cut.
In reply to mikeatrpi:
Not sure what gauge the steel will be. It may depend on what gauge the manufacturer makes a fridge from.
Getting read to do something similar myself. Making a replacement metal mount for my Opel GT fuse block. Clamp between two 2X4 right at the bend point and use another 2X4 clamped as the brake part to bend over. I'm using my wooden work bench, metal and a 2X4 clamped together to hold it steady while bending 16-gage metal about 45 degrees.
I use my shop press and sandwich the sheet between two pieces of angle iron for making 90s in longer or thicker stuff. You can do a radius by using cut tubing and angle iron too.
For making a lip or bend on smaller stuff I use these:

google for straight seaming plier
DeadSkunk wrote:
I wonder if I could do the bends by using some heavier angle sections , or solid square bar as a V block and squeeze it with large C-clamps.
Yes this will work, but you will not get as crisp an edge as you would by bending it over the outside of a piece of angle.
If the sheetmetal is thin, slip it between the hinges of a steel door and it's frame, then close the door...
Giant Purple Snorklewacker wrote:
I use my shop press and sandwich the sheet between two pieces of angle iron for making 90s in longer or thicker stuff. You can do a radius by using cut tubing and angle iron too.
For making a lip or bend on smaller stuff I use these:
google for straight seaming plier
I have a pair of those, they are excellent for aluminum.
A block of wood and a mallet can work wonders.
iceracer wrote:
A block of wood and a mallet can work wonders.
It's what the old Italian panelbeaters used ...
NOHOME
SuperDork
6/20/14 7:47 a.m.
erohslc wrote:
iceracer wrote:
A block of wood and a mallet can work wonders.
It's what the old Italian panelbeaters used ...
Not so much to bend metal but to put a crown or "shape" into the tin. A stump with a bowl in it can be used to stretch or shrink metal, making it arguably more useful than an English wheel and a hell of a lot cheaper.
NOHOME wrote:
erohslc wrote:
iceracer wrote:
A block of wood and a mallet can work wonders.
It's what the old Italian panelbeaters used ...
Not so much to bend metal but to put a crown or "shape" into the tin. A stump with a bowl in it can be used to stretch or shrink metal, making it arguably more useful than an English wheel and a hell of a lot cheaper.]
But somewhat more difficult to move around ... ;)
Had a nice stump I picked up from local tree service working in the neighborhood. Was letting it dry and working on shaping the bowl. Came home from work one day and dad had split it up for firewood. Can't win around here. 
NOHOME
SuperDork
6/20/14 1:09 p.m.
erohslc wrote:
NOHOME wrote:
erohslc wrote:
iceracer wrote:
A block of wood and a mallet can work wonders.
It's what the old Italian panelbeaters used ...
Not so much to bend metal but to put a crown or "shape" into the tin. A stump with a bowl in it can be used to stretch or shrink metal, making it arguably more useful than an English wheel and a hell of a lot cheaper.]
But somewhat more difficult to move around ... ;)
I actually have an English wheel in the shop..I could argue against your point!