Well, trimming of a sway bars effective date.
Replace both sway bar links with a double ended pneumatic cylinder.
The cylinder body has an air chamber in the middle, when charged with air it pushes on the pistons. One piston is attached to the sway bar, other is attached to strut/control arm.
Charge a 3/4 dia cylinder to 1500psi for 660lbs of force required to compress. Stiff, should function basically like a normal solid end link. Lower the charge to 600psi for 264lbs to compress.
Tie both link cylinders to a common hose so both sides are evenly charged and easier to make pressure adjustments.
Now being a small cylinder, as you compress it, pressure will actually rise and it will stiffen up, but at this point it has already allowed some flex of the actual springs/suspension so it may not truly matter? It will help keep both pistons from crashing into each other too.
There would only ever be one link compressing at a time, on a left turn, the outside link compresses, the inside link will be in extension, so it will just be getting pulled so no air acting on anything.
Where could one get a cylinder like this, preferably a shrader valve in the middle, in the 200-230mm OAL with a 3/4in or so piston?
Thoughts?
Edit: ahh can someone edit the title? Sway bar.
In reply to EastCoastMojo:
Thanks!
Thinking more about it... A single acting cylinder would work fine provided you have a way to get a heim/something attached to the body of the cylinder.
Also no idea if a cylinder exists that can take super high pressures that is small enough to be substituted for a sway bar link or not. Most are rated to 250psi max.
For those pressures you'd probably need to use a small hydraulic cylinder with air. Also note that at lowered pressures there will be a dynamic rate effect, unless you want that.
Kenny_McCormic wrote:
For those pressures you'd probably need to use a small hydraulic cylinder with air. Also note that at lowered pressures there will be a dynamic rate effect, unless you want that.
Yeah that's what I was getting at here:
"Now being a small cylinder, as you compress it, pressure will actually rise and it will stiffen up, but at this point it has already allowed some flex of the actual springs/suspension so it may not truly matter? It will help keep both pistons from crashing into each other too."
The main idea I think would be to be able to "trim" the sway bar's effectiveness quickly and easily. Anywhere from basically nothing(as long as you have plenty of travel to not crash into the ends) to full stiff(effectively a solid link).
I've got 550/450 rates on a Mazda2, no front sway bar right now. It would be nice to have an infinitely tuneable front option to try and balance body roll w/ spring rate. (I think a VERY light front bar would be beneficial)
I think that having it increase in pressure as its flexed wouldn't matter too much, you're effectively softening the bar in the first inch or two of travel.
I first need to find something suitable to build a proof of concept. For cheapish.
Edit: http://www.lstechnologies.ca/
I think hood struts modified with a shrader valve to adjust pressures is exactly what's needed. Losing the oil charge is probably desirable as you don't want the bar to be loaded right after a turn(if it takes time for it to extend back to full length).
They have 270lb gas springs in lengths/sizes reasonable for end link use.
I really don't think scheme would work well enough to justify the weight and complexity. However, may I suggest using small hydraulic cylinders instead of pneumatics. Oil is incompressible, but accumulators could be added into the pressure lines to do the damping.
This is more or less how Lexus does their active variable stabilizer bars, except they put the hydraulic stuff (pretty sure it's all-hydraulic) on one of the chassis mounts. A stabilizer with only one fixed mount does nothing useful, so they only need to alter one side.
how about just ditching the bar, and replacing it with small hydraulic cylinders mounted between each control arm and the frame and linked to each other via a hardline? figure out a way to control the resistance to flow back and forth between the cylinders and you have what amounts to an infinitely adjustable rate sway bar with very few parts. make the cylinders and lines big enough, and you could replace the springs and shocks with this system, as well, which would mean you could also adjust ride height and spring stiffness on the fly.
In reply to novaderrik:
I think you might have just invented a Citroen.
Remember, a (normal) anti-sway bar resists wheels moving opposite (i.e., one wheel in compression and one in rebound). Using air cylinders connected with a hose will resist moving the same way (i.e., both in compression or both in rebound). While cornering, compression of the outside wheel will simply transfer pressure to the inside wheel in rebound, possibly even accentuating body roll. You'd need some way to "reverse" how the cylinders are mounted or plumbed.
If you didn't, you'd have a really cool anti-dive or anti-squat invention. ;-)
I used to have a front anti-sway bar that, rather than having holes drilled for different, adjustable positions, had the end-links connected to a sleeve that slid along the end of the bar, so it was infinitely adjustable. Well, infinitely adjustable in the range defined be the inner and outer ends of the bar. That was a really simple and effective method and it was easy to adjust: just loosen one bolt and slide the sleeve. That did require jacking the car up, though. Maybe you're looking for a wider range of adjustment, too.
In reply to DWNSHFT:
In the idea of novaderrik, yes.
My original idea(replacing the end links with cylinders) would function normally over bumps with both wheels. It would just pivot the sway bar inside the bushings like normal.
So, since both sides of the axle are connected via air hose, what prevents air from moving from one side to the other in a corner?
I.e. you get pressure in both sides via your pump. Then, in a left turn, the right pressure goes up, left pressure goes down, what stops air from moving from one to the other and leaving the sway bar mostly ineffective?
In reply to rcutclif:
It's at full extension. Won't matter.
i made an ommission in my first post: you'd need to plumb it so that the top side of the piston on one side is plumbed to the bottom of the piston on the other side. in my mind's eye, that would cause it to naturally resist rolling forces.. figure out a way to control the rate that the fluid (or air, i guess) flows or how to control the pressure spikes in a linear manner and you have what amounts to an infinitely adjustable anti roll bar.
I think you will find that a cylinder is needed on only 1 side.
Because any modification to effective torsion rate will be effective for the whole bar.
You can see this in modern 'blade' adjustable bars, where the 'blade' mechanism is on just one side.
In reply to novaderrik:
That might potentially work but would work. Though I do want to retain an actual sway bar for a chance at standing up to scrutiny for SCCA STF class.
In reply to erohslc:
It's needed on both sides if using a single acting cylinder(lower weight and complication).
If using a double piston(like I was originally alluding to), you'd need to make sure pressures are identical on both sides of the piston. Technically you'd need more on the side where the shaft rod enters because of lost surface area. So you'd need to charge to say 500psi on the non-rod side, and maybe 600psi on the rod side, and maybe it will center itself in the range of travel. Pretty complicated to make sure that happens. Especially with pressure change from heat, which would probably heat up the non-rod side of the piston faster because higher pressures to start with, plus less chamber capacity. Meaning it will slowly want to contract on it's own, and continue to add preload to your sway bar in one direction.
The difference in chamber capacity will also mean when the piston is being forced to the rod side(extension), it will ramp up in pressure considerably faster than in compression. So you'd have more body roll in one direction than another.
I will need to draw up a diagram to illustrate my idea when static + when turning in either direction....

One other way of finding is you could connect them to a larger air reservoir so pressure doesn't rise as quickly so if will be softer through its action. You can tune the "curve" of how quickly the link effectively becomes "solid." Small or no reservoir means it stiffens up quicker and then starts transmitting full force of the bar itself. Different capacity reservoirs would be much like tuning off-road air shocks by varying the amount of oil vs air in the shock(oil takes up volume so the spring rate ramps up faster when added).
I think your idea could use some improvement, but you're definitely on the right track to a workable concept - sway bar end links that have adjustable stiffness with a pneumatic mechanism.
But now you have to ask yourself how practical this idea is? You'll have to compete with much simpler systems, like cable-actuated rotating blade adjustable sway bars:

And multi-hole/slotted hole adjustable sway bars:
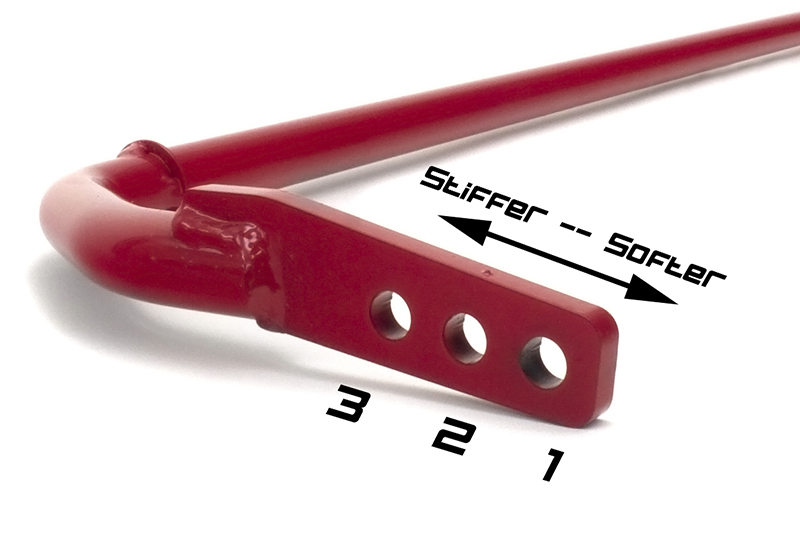

Also your idea, if applied to both axles, is almost as complicated as a full hydraulic FRICS setup which offers a different league of performance:

I have seen this before......
Edit 1:
They change the bars rigidity itself.

Edit2:
Hydraulic actuation.

This isn't the exact one I saw as it had screw actuators. Which God help you if one side gives out and the other goes to the extreme 
Yeah, Hood struts aren't gonna work. That will break very quickly. It needs to be hydraulic as opposed pneumatic unless comfort is what you are going for. Then you are going to add weight and complexity. You could do a screw drive with a position encoder but you better be sure you spec the right screw or else pow! all over but the tow truck.
The_Jed
UberDork
6/14/15 11:29 a.m.
If I were a real fart smeller I could probably fab up a similar pneumatic/hydraulic type system on my Mark VII; a system that would transfer pressure to the side/corner that would compress in the turn while reducing the pressure to the side/corner that would extend. An active air suspension of sorts. I'd assume it might give some strange feedback and take quite a bit of time to adapt to. Tuning it could be a pain. A real time, on board controller would make it less time consuming to tailor the system to the different levels of grip available in given situations.
Interesting idea.
In reply to GameboyRMH:
Thanks for the input! Also make sure to see my last post, we posted about the same time.
I really like the blade style arms. Ever priced those things out? Like $350+ for just the arm! I was originally mulling over these before coming to the conclusion there's no room on my Mazda2 for that. Plus a custom sway bar itself would need made to accept that arm due to multiple bends/etc.
As for bars with multiple holes... If that were an option I'd try it. The problem is I'm fairly sure I need a softer than stock front bar. Nobody aftermarket makes softer than stock. I suppose I could weld tabs to my control arms to change the motion ratio to significantly lower than on the strut, but that's still just a guess.
Pneumatic cylinders are relatively inexpensive. The link posted above builds them custom, and their prices aren't bad. I'd double some of their catalog stuff(which is available with heims on the ends) and estimate $200-250 for a pair built to spec. Plus some hose and shrader valves.
I'm not looking to create active suspension like the McLaren, just something to make a tunable sway bar that adjustments take less than a min.
They share a common valve strictly to keep pressures equal left and right(so heat didn't build in one quicker causing one to increase in pressure faster). And to speed up the adjustment process.
What I think is the really cool thing about substituting the end links with pneumatic cylinders like this, is that you run pressures high enough so the bar doesn't compress them at all for maybe 2in of travel, then the force of the bar overcomes the air pressure some, so it tapers off the bar's effectiveness to not push as much during a longer turn/transition. It would be full stiff for initial direction change like in slaloms.
At least in my head. 
Technically the McLaren's suspension is a passive adjustable system, not an active system. The suspension doesn't adjust to how the car is driving, you just choose a profile which sets the height and various stiffnesses. It does have active yaw control, but that's not really part of the suspension.
You shouldn't weld on a sway bar since it could affect the metal's "springiness," but you could clamp/glue multi-hole adjustable ends onto the stock sway bars.
Looking at your diagram, I think that setup should work assuming that gas can't flow between the two cylinders. If it can then they'll work like a heave spring, which isn't a good thing to have as sway bar links.
In reply to GameboyRMH:
I had to Google heave spring.
I don't think it would be possible to compress both sides... The sway bar itself will simply pivot within the bushings like normal under braking/accel.
Just looking for some clarification. Thanks for the input so far!
You're right that the sway bar would keep the links from working like a heave spring, but they would allow the links to keep your sway bar from doing anything until one side hits the end of its travel. So you'd have a little "dead zone" where it would be like having no sway bar - again assuming that gas can flow between the two sides.