I'm converting a Ford T5 transmission to a slave cylinder. I need to drill two holes in the clutch fork. They aren't going through the face of the fork, like the stock holes. They're going through the top and bottom flanges (that stiffen the fork), so I can drop in a clevis pin.
I went at it with your standard homeowner 4-amp plug-in drill and various sizes of carbide-tipped bits. I barely dimpled the surface, after much effort.
I thought WTF, and took the bits over to my cheapo drill press set at 600 rpm and punched through 1/4" mild steel stock, no problem.
Getting the clutch fork into the drill press is a major project, since the trans will need to come off the motor. Do I have any alternative? What am I doing wrong?
Is the drill spinning backwards?
Snrub
Reader
11/16/15 12:33 p.m.
Are your drill bits dull (over spun the drill?)? Did you start off with smaller diameter bits? Are you using lubrication? Are you pressing down sufficiently?
Hardened steel is a pain to drill through. Not sure what clutch forks are made of but it is NOT mild. It's closer to spring steel. They crack instead of bending.
Yep, like others have said, lubrication, low RPMs, and pressure. Resist the temptation to spin the E36 M3 out of it.
Umm, "carbide tipped" drill bits? The only carbide tipped bits I've ever used are for masonry. They grind and bludgeon their way through the material. You need a sharp steel bit and cut through the shift fork.
And use a slow speed, burning up bits is a waste of time and money. You should have big flakes or even spirals of material coming off the stock.
Knurled wrote:
Hardened steel is a pain to drill through. Not sure what clutch forks are made of but it is NOT mild. It's closer to spring steel. They crack instead of bending.
This. Been there, done that.
Where'd the drills come from? If it's anything you can buy at a home improvement store, that's problem #1.
I drill everything from balsa to titanium with regular, non-coated high speed steel, stub length, 118 degree drills. They're nothing special, but they are American made drills that a machine shop would buy to do paying work. They're sharp, and I have extras of all the common tap and screw clearance hole sizes.
Consult a speed and feed chart. When drilling hard materials if your RPM is too low and you don't feed aggresively enough you'll dull the drill instantly and it will never cut. Some materials can be drilled dry, WD40 is a superb cutting fluid for aluminum, sulphurized cutting oil on steel and stainless.
Carbide is likely not necessary - if it's super tough you might consider a coated cobalt drill.
Is this for your e36 swap?
I used a kit - this one http://dazecars.com/dazed/test.html
(about halfway down the page)

Then because the CNC slave is too big for the stock master (you don't quite get enough throw), I put the BMW slave onto that bracket by fabbing a simple bracket from angle iron. Worked perfect, and I was able to use stock BMW stuff for the whole clutch hydraulic system. Didn't have to drill the clutch fork at all.
Sorry, not carbide. I meant cobalt. Century brand. 135 degree. Using lightweight oil as a lubricant. Tried starting small but got nothing so I worked up a few sizes, and still not much. Thought maybe I had dulled the bits, but I took them over to the drill press, used my standard low rpm, lightweight oil lube and drilled right through 1/4" mild steel like usual.
I don't know for sure what the T5 forks are made out of. But there are after-market forks for sale, claiming that they're stronger than stock because the after-market forks are "made from heavier 0.165" stamped steel!" Which doesn't sound heavy-duty to me, either.
I have no clue how to get the speed and feed right with just the homer variable speed hand drill or the cheap drill press I have.
I'm tempted to pick up a used fork, and see if I can do better with that in the drill press.
Thanks Robbie - yes, it's that swap project. I wanted a stouter linkage than the DazeCars pushrod-through-the-hole approach. A clevis pin and a Heim joint threaded onto the push rod is the goal. But I may give up and go the through-the-hole route. Do you have any idea what I can use as the nut on the pushrod up against the fork?
I'm using a Miata 7/8" slave because it has the hydraulic line AND the bleeder screw both on the top, pointing up. I welded up my own bracket out of 1" square mild steel tube.
You had to trim the end of the fork to clear the tunnel, right?
P.S. what's that oval plate with the DazeCars bracket used for?
Daze cars also sells a chrome 'bead' that fits the concave part of the fork perfectly - you can see it in their pic there, but that is what I used. Then you just put any nut or two behind it.
I don't remember trimming the fork to clear the tunnel (but that doesn't mean I 100% didn't do it). I really don't think I did though. I remember it being tight, but it all fit. There may have been heat insulation stuff that I pulled out.
I think the oval plate is for the master cylinder side. dazecars makes this mostly for old mustangs, and apparently they need firewall support where you bolt in the master cylinder. Or you need to cut a hole and stuff. or something. all I know is it is for the master cylinder, I didn't use mine.
EDIT: apparently you can buy it separately, but he says it is a ball bearing with a hold drilled through it:

I threaded the shaft a bit on the stock e36 slave with a tap, and then used just the ball and a nut to hold it.
Thanks again Robbie. I think I might get a brass flare tube cap in a suitable size, and drill/tap it for the thread rod.
But first, I'm gonna get the T5 fork into the drill press, WITHOUT taking it out of the transmission. Photos to follow!
ncjay
Dork
11/16/15 9:22 p.m.
O.k. When you say you're using lightweight oil, is that engine oil or something else? Either way you need to be using something designed for drilling, tapping, or cutting operations. The correct cutting fluid will make a world of difference. As far as drill bits available from Lowe's, Home Depot, or just about anything available to the general public, most of them are all crap, not designed for cutting heat treated steel. I've been doing a lot of fabricating with stainless steel lately, and I have found DeWalt titanium bits to be outstanding. Seems like the slower they spin, the better they work. Slow rpms and short plunges are best. You can find them at any of the big chains stores. Beyond that, getting drill bits from a dedicated machine shop supply company is the only other option. There's also the possibility that it could be heat treated to a level that's basically unmachinable. I have some steel hanging around the shop that the best drill bits I have won't put a dent in.
Irwin solid cobalt bits. they demolish hardened metal. Use a clutch, if it grabs, it will shatter.
PM me your address. I have a couple (small) bits I can send you. When I needed new holes to install a swaybar, I ran into the same issue. I got these bits from an aircraft maintenance supplier and they poked through like butter. With a nice pilot hole the rest was easy money.
Cheers!
-Bill
How does one properly sharpen drill bits. I have more than one set of dull cobalt drills.
RossD
UltimaDork
11/17/15 7:31 a.m.
The easiest way to get a new hole in it is by letting me weld on it. 
chiodos
HalfDork
11/17/15 8:47 a.m.
In reply to DeadSkunk:
youtube it, its hard to explain but you need a bench grinder, hold the bit by hand, match the angle and spin in reverse. it takes practice but once you got the hang of it, its an extremely useful skill.
RossD wrote:
The easiest way to get a new hole in it is by letting me weld on it.
Ohmygod! I almost just laughed black coffee out my nose. Me too.
Snrub
Reader
11/17/15 9:10 a.m.
DeadSkunk wrote:
How does one properly sharpen drill bits. I have more than one set of dull cobalt drills.
There is a product called Drill doctor which can sharpen drill bits.
Hungary Bill wrote:
PM me your address. I have a couple (small) bits I can send you. When I needed new holes to install a swaybar, I ran into the same issue. I got these bits from an aircraft maintenance supplier and they poked through like butter. With a nice pilot hole the rest was easy money.
Cheers!
-Bill
Many thanks, sir! PM sent. I promise to mail them back to you as soon as I'm done.
The_Jed
UberDork
11/17/15 10:04 a.m.
chiodos wrote:
In reply to DeadSkunk:
youtube it, its hard to explain but you need a bench grinder, hold the bit by hand, match the angle and spin in reverse. it takes practice but once you got the hang of it, its an extremely useful skill.
I have yet to successfully sharpen a drill bit by hand, the flutes always wind up at slightly different heights which basically turns it into a 1 flute drill and the asymmetrical tool pressure cuts the hole oversize.
At work we have a hand-held arbor that fits into a fixture which you spin and the cam mechanism sweeps it across the grinding wheel(1), it works great. We also have a more automated yet older drill sharpening machine for the larger bits (2) and a smaller, more manual machine where the bit is locked into a small hand held vice and you manually sweep it back and forth across the face of a grinding wheel(3).
1:
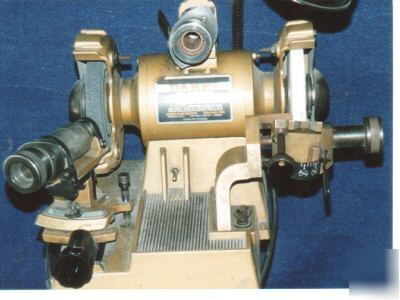
2:

3:
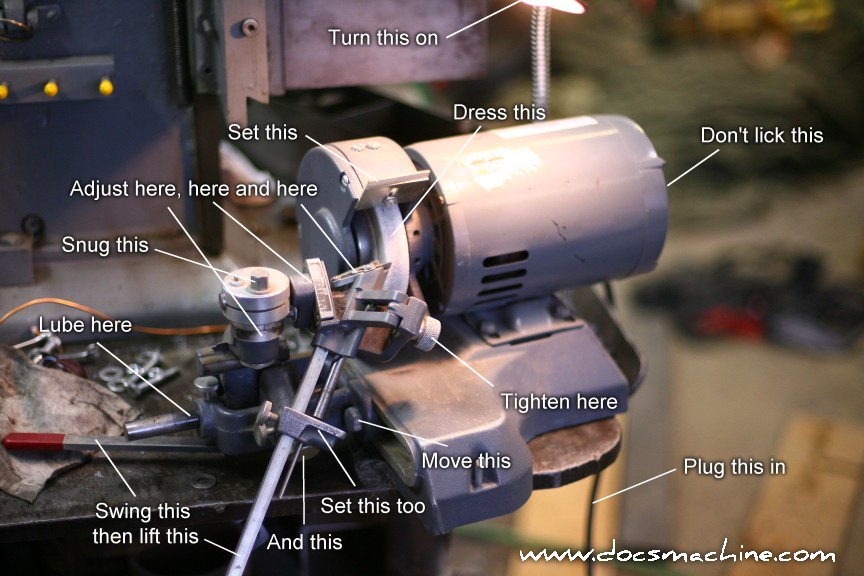
I looked up some carbide tipped and solid carbide drills on McMaster Carr and they were cheaper than I expected from a machinist standpoint but, I wouldn't be able to justify the cost of one for drilling a single hole.
Any time I've had to hand drill hard material with a cobalt or HSS bit the first thing I've done is grab a lid from a spray paint can (or similar), fill it with oil and set it next to my work piece. I drill slowly, sometimes jogging the trigger (do not let the bit bind and stop in the material, think of it like when a drag racer breaks the tires loose in the burnout box then feathers the gas pedal. He/she keeps them spinning but doesn't redline the engine.), for a few seconds then dip the bit in the oil. Lather, rinse, repeat until there's a hole.
Once there's a pilot hole you may be able to use an endmill, should you have access to one and be so inclined. I've done that a time or two, just don't expect the endmill to survive unscathed. 
In reply to Snrub:
I've got a Drill Doctor and it sucks. It leaves the drill flutes at a negative angle and they won't cut. I'll be trying the grinding wheel by hand method after watching more videos.
Thanks gents one and all for your expert advice and guidance. I haven't given up on this yet! I have a 7 amp low speed hand drill on the way; we'll see if that helps out with feed and speed. Also, I'm not kidding about the possibility of getting the fork into the drill press without pulling the transmission. We'll see what develops.