My Challenge car has a tubular chassis. The floor area is composed of rectangular, square, and round tubes. I'm debating whether to put the sheet metal above the structure and keep the inside smooth and easier to clean, or put it under to have a flat bottom in case I may want to play aero games down the road. What does the hive think, and what are the pros or cons of each?
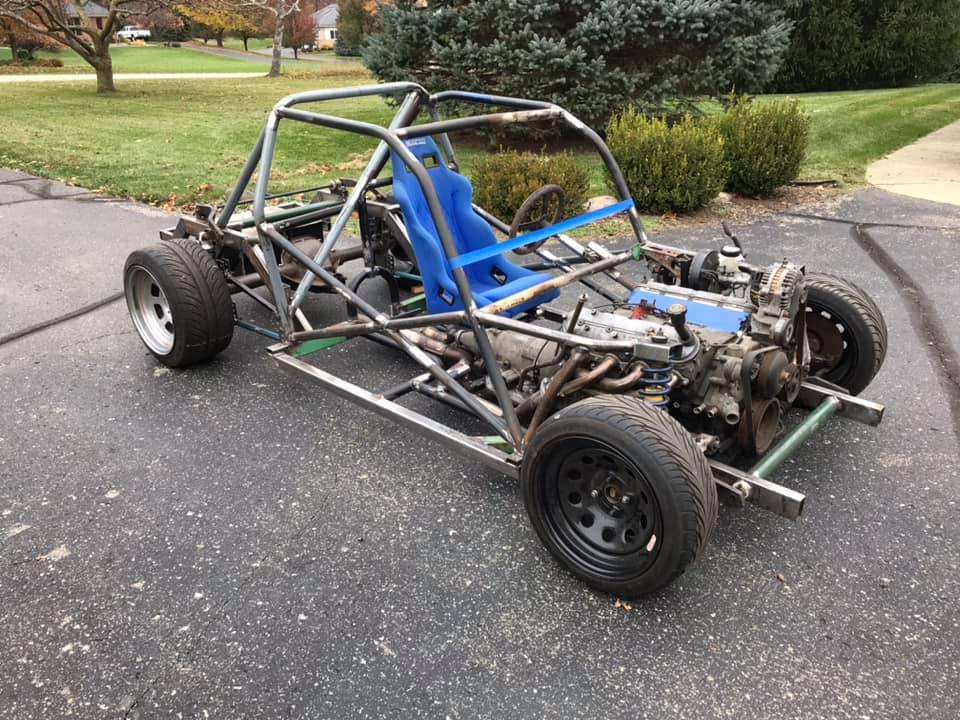
Under the tubes
This give you the most vertical real estate for interior work/installations/seats/drivers. You get the side benefit of smoother underbody.
The cleaning requirement can be sorted the same way production cars are built: a small hole with a grommet. Add a vacuum and you are all set.
Dont forget to put some beads or brakes in the sheet to keep them from oil canning and making a bunch of noise.
I'd go over. You have no roof.
if you want to play aero later you can do that with shaped panels added to the structure assuming you have the ground clearance.
STM317
UberDork
8/5/21 10:47 a.m.
Under. Better aero. Keeps a clean, dry, protected place to run wiring and lines if necessary. If it's too much of a hassle to clean, you can always add a sheet to the top at a later date.
stafford1500 said:
Under the tubes
This give you the most vertical real estate for interior work/installations/seats/drivers. You get the side benefit of smoother underbody.
The cleaning requirement can be sorted the same way production cars are built: a small hole with a grommet. Add a vacuum and you are all set.
Dont forget to put some beads or brakes in the sheet to keep them from oil canning and making a bunch of noise.
This is my preference as well but here's my pros and cons list
Above:
- potentially cleaner looking interior if you run wires, tubing and hoses under the floor
- room under the floor for wires, tubing and hoses
- easier floor installation
Below:
- better aero
- slightly lower CG
- wires, tubing and hoses protected during off track excursion
- more vertical interior room
- easier access to wires, tubing and hoses
I would go over. Looks like a lot of tubes to bang your feet and ankles on. Ankle bone versus chassis tube, hurts very much bad.
I'm up against the same problem right now.
I'm planning to do the real floor underneath, but I will also probably have a false floor above.
For reasons.
Under, as a skidplate more or less. The you can run all yoir lines and wiring inside where its protected.
Not sure aero will help with a 70s Toyota body.....
In reply to Dusterbd13-michael :
I'm hoping aero will help with a 60's Datsun body...
Here is an image to help define my 'reasons'.

In reply to itsarebuild :
It will have a roof, I just posted the picture of the naked chassis so you could see the tubing..
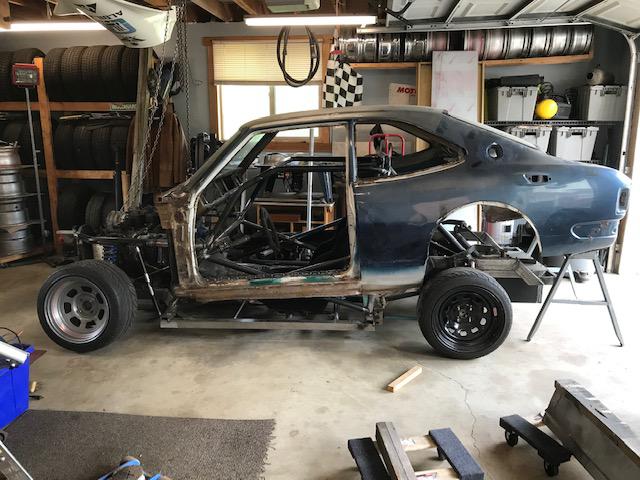
Also note, the bottom side of all the tubes is pretty close to flush, and about 3-3.5" above the ground , so nothing will be going below the tubes. Cables, hoses and wires will either go through the cabin, or through the passenger side 2x2" frame rail. Only other alternative I had thought of was to make a sheet metal channel in the floor so stuff can go below the floor , but above the chassis tubes if the rest of the floor is kept above the tubes.
Edit: I also have to look at the NHRA rules to see what they want for fuel lines, materials and location may affect my decisions.
In reply to stafford1500 :
With the load in the fasteners when underneath. In addition to flush rivets I'd use a good adhesive like 3M's
No matter where the floor is I always try and keep all tubes with fluid in them out of the driver's compartment.
Under. 100%
Clean air flow, stops tubes from getting scratched and corroding, gives more foot room, looks more like racecar... etc.
frenchyd said:
In reply to stafford1500 :
With the load in the fasteners when underneath. In addition to flush rivets I'd use a good adhesive like 3M's
A person could turn the edges of the floor panels up at 90degrees and put the fasteners in shear instead of tension. That would also keep the bottom surface clean of bolt/rivet heads. Modern adhesives are very good, absolutely consider using them, but watch for cost since it is a challenge car.
In reply to stafford1500 :
I was just going to weld (stitch or plug ) the sheet to the tubes and then take a tube of seam sealer to it. What's normal race car practice?
In reply to dean1484 :
Not a bad idea and NHRA may require it for fuel at least. I will have a brake bias valve in the cock pit. Originally the car had braided fuel line inside, too. That will end up separated from me.
DeadSkunk (Warren) said:
In reply to stafford1500 :
I was just going to weld (stitch or plug ) the sheet to the tubes and then take a tube of seam sealer to it. What's normal race car practice?
I think normal race car practice is probably to use aluminum sheet for the floors.
But, would you ever need to remove them? I think I'm going to use a combination of rivets and cap screws to attach mine.
In reply to Robbie (Forum Supporter) :
I've been building to a set of ASSumptions and when you ask a question you always learn something new or different around here, so I'm not sure what I'm doing yet. All the tubing inside the perimeter boxis 0.090x1.75" round, so pretty light. I can readily remove the tack welds and move it, build an entire new structure (but out of 1/8" wall) cheaply. It's all up in the air for a few days until I strip the chassis to complete welding the underside. At that point I need to make up my mind and I'll be committed.
Edit: The sheet steel was free, but I also have a large chunk of free aluminum, too.
I'm planning on using steel floor panels at the bottom of the tubes on my project, cut to fit the shape that the tubes make and stitch welded into place.
Put the floor under the tubes and make it so it bolts to the chassis.
Having now owned three single seat cars, I can tell the one that had bolt on floors was far easier to clean. It also makes it a lot nicer when it comes time to redo the floor pan. Basically the floor is the skid pan.
As for the floor on top; any minor off course excursion may result in dented frame tubes.
With fuel lines in cockpit:
Nascar uses a steel tube (1 inch id or so) to run the lines through. Welded to the firewall and rear pan where the cell is. Keeps them separate from the driver, as well as protecting them from damage while wrenching or ingresa/egress.
Id do that. Probably out of thin wall conduit.
In reply to Dusterbd13-michael :
That would be easy to do, I'll just need big enough for a supply and a return line. Good idea, thanks.
In reply to DeadSkunk (Warren) :
Or two smaller pipes