I am looking for a way to ditch the leaf springs with the least amount of cutting on the tub of my Falcon. To wit I have been leaning heavily towards truck arms. I mean if it is good enough for nascar it ought to be fine for a daily cruiser.

The drawbacks would be a change in pinion angle over suspension range. But in real life with my lowered car, actual suspension movement is under 2" anyway.
What I have figured out is that the trailing arms need to be flexible. That kinda bashes my dreams of 2" square tube and johnny joints onto the rocks. Short of purchasing pre-made units how would one fabricate a pair of arms that would have the necessary stiffness but allows torsional twisting?
What do I need to know?
This forum of any should know better than that.
It's not "Good enough for NASCAR"
It's "What is required by the rulebook"
NASCAR just proves that you can make anything work if you throw cubic dollars at the problem.
That being said, they will work fine for a daily driver.
The factory units are two pieces of "C" shaped steel, welded together like this )( but not a continuous weld.
Perhaps a single section of commercially available C channel will give the flex required.
Or have a steel supplier replicate the C sections from 1/8" flat steel and a press brake. Then you just cut, weld and fit.
What about a radius arm set-up like the front of old solid axle Fords?
Truck arms will be tough to package in a small car with a unibody. You are going to have to put in a crossmember by the tranny mount for the front mounting point and cut and raise the floor over the arms so the have room to travel. If you are worried about cutting up the car there have to be easier ways to go. You could probably come up with a fairly compact three link that will take less up less space. Either way unless it was a serious track car I doubt you would see a big improvement over the leaf spring set up.
Isn't the (minimal amount of) torsional rotation supplied by the bushings be them rubber or urethane? Or in a more flexible application such as an off-road vehicle, supplied by a moveable joint ie: Johnny Joint?
Ignore the pinion angle change. Millions of cars were made with torque arms, which have just as much pinion angle change over suspension travel.
Heck, if you put a camera down there and saw how much pinion angle change there was under your car with its leaf springs, under normal conditions, you may be shocked.
Wally wrote:
You could probably come up with a fairly compact three link that will take less up less space.
I was thinking the same thing, no need for flex this way and you could control the pinion angle.
RossD
PowerDork
10/14/14 7:49 a.m.
SN95, MN-12, or even XR4Ti IRS and go back to 4 bolt wheels all the way around.
It seems to me that the Truck arms would need a lot of underbody clearnace in Jounce. You're obviously not affraid or and very capable at fabrication. why not as other have suggested fab wither a 3 or 4 link or possibly a traditional torque arm. All proven to work very well.
Mustang torque arm

Escort 4 link

3 Link

There's tons of info out on the web on all versions. I bet you could buy an aftermarket Mustang torque arm and make it work.
But having said all that. Why do you want to get rid of the leaf springs? I think your car is more of a DD and cruiser than any kind of race or autocross toy. Leaf springs can be made to work really well. Why not look at different leaves in the rate / height you want. Go for stiffer front bushings for location and add a Watts link for lateral control. Even a panhard rod works pretty well as the theoretical scrub really isn't that much of an issue in practice, especially if you only have a couple of inches of travel.
I agree with not ditching the leaves. They are compact, require no re-engineering, and can be made to work well. Personally, if you are going to go through all the trouble to building a whole new rear suspension for you car, you should just go IRS from a Jag or a Vette like the hot rodders do
A Falcon is a Mustang as least as far as the suspension design is so since there are thousands of early Mustangs running on the road I don't see why a major change is required. If you just have to change something then a parallel 3 link with a panhard bar is what I would do. Two lower forward links replace the leaf springs, an center upper link, (Shelby used dual uppers), a panhard bar to locate the rear end, and coil over shocks to hold up the rear of the body.
Replace the panhard bar with a Watts link and you have what worked quite well on 80's & 90's Trans Am race cars, and is still used today!
My reasoning for upgrading is thus. The Falcon is equipped with the narrow early spring packs mounted as far out by the wheels as they could be located. This makes tire clearance a real issue. Even with under a hundred horsepower axle wrap is an problem because of the lowering blocks and narrow springs. If I get on the throttle hard trying to pull out into traffic I am greeted with wheel hop and the wonderful feeling of the differential bouncing off the pinion snubber. And before it is mentioned, because of the blocks there is no room for traction bars.
I spoke with a local spring shop about getting my leafs rearched and adding a leaf or two and the cost was quite a bit higher than I had anticipated. Plus that does nothing for my clearance issues.
My initial thoughts were to swap to the wider mustang springs mounted further inboard. Aftermarket is strong here but it would actually be quite a bit of work.
I didn't realize truck arms needed to be so long. I was envisioning them only about 28" forward of the axle, not up by the transmission. This is the kind of thing I needed to know. I was picturing the crossmember mounted between the rear sub frame rails just forward of where the leafs mounted.
With that giant 8.8 pumpkin back there I do not have room for a three link above the diff. Not without raising the trunk floor.
A 4 link is obvious but I was again trying to cut down on major tub modification
Another option that has been rolling around in my head is the Alfa Romeo "T" bar rear. Pretty much just a 3 link but the upper link is mounted lower and also is triangulated and stiff enough that a panhard rod isn't needed.

At this point I am just bench building/day dreaming and looking for ideas.
That Alfa T-bar setup looks like a good option. Although with the amount of fabbing involved you should also consider an IRS swap.
They have been installed in unibody cars. This is a Hot Rods to Hell kit for an early Nova. 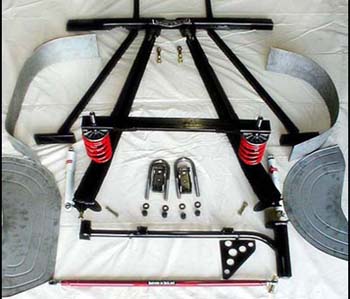
Here is a kit installed in a first gen Camaro
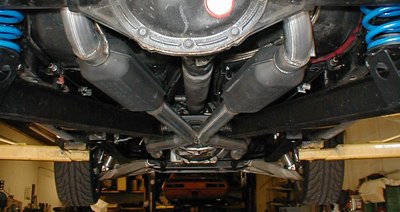
Exhaust routing is also a huge issue with truck arms.
http://www.suspension.com/Must-IRS.htm

Should be doable on a budget with some decent fab experience. Quick change rear end optional :) Of course with the newer Thunderbird IRS as an option along with CTS/GTO, Miata or 2nd Gen RX-7's available at the local yards as a nearly complete dropout you shouldn't have a problem finding one that can be adapted to your needs.
Another thought would be a modified 3-link:

turboswede wrote:
2nd Gen RX-7's
Been on my radar for a while. The width of the 2G RX7 rear is perfect for my car as is the bolt pattern. I think a subframe could be fabricated that would allow it to pretty much bolt into the leaf mounts. But that is more than a weekend project. And I have yet to find a complete rear end setup.
3 link with a Watt's link.
There's another Alfa setup employed with some of their DeDion rear suspensions.
It uses long rigid arms (truck arms) to a single central pivot located under the driveshaft.
Watt's linkage takes care of lateral location.
I have several good pictures and technical drawings, but on a prior computer.
In your case, the DeDion is replaced with the rear axle housing (both are rigid members),
unless you wanted to attempt a DeDion solution.
The central pivot could be a large Heim Joint, a standard Ball joint, or even a urethane bushing.
It could be located as far forward as the under trans UJ.
Because the training arms are rigid, they essentially form a large triangle with the rear axle.
For body/chassis clearance the arms can be 'bent' or offset a bit in the side plan view rather than straight.
In fact, the whole member could be designed as a T shaped rigid spaceframe structure, with portion from
front pivot narrow enough to partially enclose the driveshaft and fit in the tunnel, until the rear where
it would spread out to connect to the axle.
Would of course need to handle the bending loads from suspension as well as drive torque and braking torque in the housing.
Lateral location is your choice, Watt's, Panhard, or even a 'sliding block' (modern ball bushings are a tough and inexpensive off the shelf solution).
This offers a simple, lightweight, rugged solution that introduces minimal rear KPI changes vs suspension movement, zero camber change, camber preset (bent/machined housing ala Herb Adams Trans-Am Tempest), no tub surgery,
AND NO LEAF SPRINGS.
Carter
Ditchdigger wrote:
That Alfa system is similar to the early Jaguar C types and early Mk I Lotus Cortinas in that it uses the 3rd link to handle the lateral loads as well. In all cases it puts tremendous strain on the single pivot point of the 'A' (or 'T') arm. The biggest drawback though, other than the loads being put through a single point, is that the arm also dictates the roll center, which for the Alfa and the Jag were very high. Much lower and more manageable for the Cortina. Note both the JAg and the Lotus Cortina soon reverted to more traditional rear suspensions due to issues with the handling (Jag) or fragility (Lotus Cortina)
Early C type 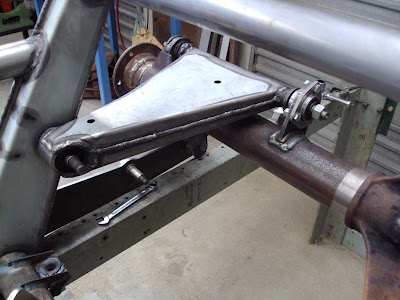
Lotus Cortina (arly cars top left, later cars lower right)

Richard Petty once said he preferred the leaf springs of the Dodges/Plymouths to the coil spring truck arm.
Leafy
Reader
10/14/14 12:03 p.m.
no room aove the diff to run the 3rd link why not flip it over? You can make the kinematics exactly the same with it flipped. You could also do the math about running the 3rd link off center. Sure this would cause the axle to steer one way or the other as it moved in 2 wheel bump but it might be a small enough number that you dont give a E36 M3 in the suspension range you care about.
Quoting this pic from your build thread.
Ditchdigger wrote:
Something new
Stepping up to 17's allows more backspace so I can fit a bit wider tire. Went from 185 to 215 up front.
Is there another pic from a lower angle? It looks like there is room outside of the current rear tire? If so is the current narrow leaf spring an issue, can you move your wheels out with the same location? While I grant you leaf springs aren't as cheap as coils, I have to think that at the end of the day with the knowledge base here you could find some other car to donate it's leaf springs, maybe like this:
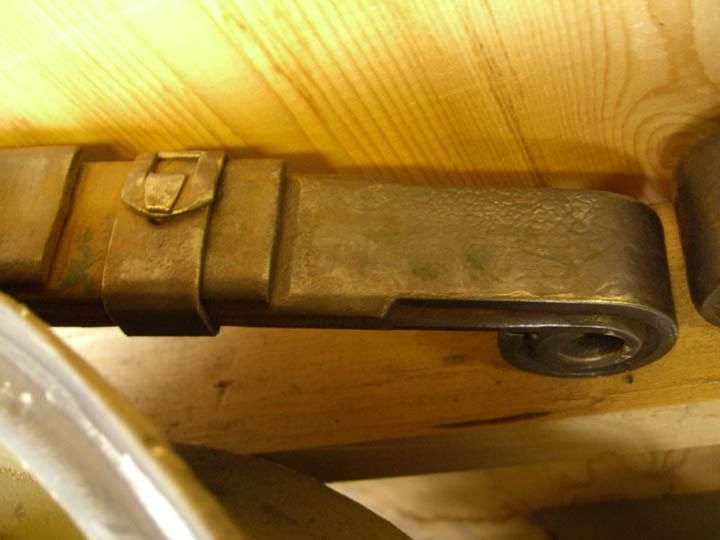
Start with a wider spring and cut down the width at the mount.
Then add a panhard and call it good?
Am I making sense or do I come across as talking out of my ass? If the later I'll try again.
Chris_V
UltraDork
10/14/14 1:21 p.m.
You want tire clearance for a lowered Falcon? Mini tubs and move the springs inboard of the frame rails with a cheap weld in kit. It's pretty common and allows for 275s in the back easily.
http://www.tffn.net/phpBB3/viewforum.php?f=11&sid=0b7057f2b989c4ea05bca88202e14557
http://www.tffn.net/phpBB3/viewtopic.php?f=11&t=29659&p=218734&hilit=chuckbizkits#p218734
The Crites restorations kit is $169 and moves the springs inboard for lots of clearance.
Chris_V wrote:
You want tire clearance for a lowered Falcon? Mini tubs and move the springs inboard of the frame rails with a cheap weld in kit. It's pretty common and allows for 275s in the back easily.
http://www.tffn.net/phpBB3/viewforum.php?f=11&sid=0b7057f2b989c4ea05bca88202e14557
http://www.tffn.net/phpBB3/viewtopic.php?f=11&t=29659&p=218734&hilit=chuckbizkits#p218734
The Crites restorations kit is $169 and moves the springs inboard for lots of clearance.
Those sites require registration to view the threads.
I'd avoid moving the springs in board as much as you can. In board doesn't affect straight bump motion as in drag launches or speed bumps, but the further in board yo move a spring, you effectivley reduce it's rate in roll. So if you move them in, you either need to have higher rate springs to keep the roll resistance the same and ruin your ride, or you up the rate to keep the correct roll resistance and end up with a harsh ride in double wheel bumps.
Bloody physics, always a sodding trade off!