Many of you on here are actual car builders, with actual talent, with decent tools at your disposal and a good support system.
Not all of these describe me.
Probably closer to none.
In the spring time my garage will be cleared and two vehicles will be spending an extreme amount of time occupying the space.
If everything goes correctly the plan will involve installing two subframes under a vehicle with a unibody. It is my plan to use 2x3 .125" to build a rudimentary frame that ties the subframes and us cut into and welded to the vehicle.
Now for the real question.
If you were going to undertake this with more rudimentary tools, say a 220v stick welder, 6013, 6018 and 70** material (I have some questionable 7011 but I'm open to suggestions) would you feel confident that it would be okay?
I'm not going to BS here, I've only started welding in any manner over the last 8 months. I'm confident but no expert.
What I'm building is essentially full length subframe connectors and bolting the subframes to them.
Should I borrow a welder or pay for someone with skills instead?
I would buy a MIG welder. You can stick weld it. It can be fine. For heavy gauge stuff it will work.
But inevitably you will want to weld thinner stuff together. You will need to do some welding on the unibody. It is possible to stick weld sheet metal. But the metal glue gun is SOOOO much better at it.
Yes it will cost a bit to get setup. Even the cheapest worthwile MIGs are ~$300 (Eastwood 135A) then you need to get a bottle which at my LWS is about $150 for the first one.
I bought a Hobart Handler 180 (Current model is the 190 and is $700). Since then my stick welder hasn't even been turned on.
TL:DR you can do what you want. But you will be happier learning to MIG, If you can borrow a 220V MIG machine do that. That's bestest.
Tie the subframes together with the tubing and then bolt both to the unibody. Weld the tube sections to the unibody as they'll be stiffeners, not a chassis. Your welding is probably good enough. If not you and I can battle it out at the Challenge for the "Most Spectacular Failure" trophy.
Edit: Get a MIG welder, or even a fluxcore welder, trying to stick weld the sheet metal unibody to the tubing will be a PITA.
Come to think of it. I have a Craftsman 110V MIG that I have no use for. It has a baby bottle and gas meter. It likes all the amps or the wire feed slows down but it works.
I'll get out some 1/8" plate next time I'm in the garage and See how it does on that thickness.
If it's passable a deal can be arranged where you can use the Craftsman or take ownership of it.
In reply to DeadSkunk (Warren) :
Really is the plan.
I do have a flux core as well.
2022 brother.
If I were starting over on my project there are a couple things I would focus on. One would be how to hold the car so the parts that need to be cut can be cut without the body warping and the tubes that need to go in wouldn't need to be in the places I am holding up the car. (in my case holding the body by the leafspring mount I would like to tie the frame into). The other is the position of the main rails. I am running mine essentially as full length subframe connecters like you mentioned (down the center of the floor), however it is worth considering running the rails down the rockers. This is how alot of the aftermarket chassis builders do it and it helps with foot space in the passenger compartment (and under the pedals). You should probably take any advice from me with a few grains of salt because my project is still on jack stands :) I'm looking forward to learning by following along.
"Confident that it would be ok..." ???
Whats the worst that can happen? A weld break, and the car is only capable of driving like it does right now??
I think you need to go to the garage and get to work!
nocones said:
Come to think of it. I have a Craftsman 110V MIG that I have no use for. It has a baby bottle and gas meter. It likes all the amps or the wire feed slows down but it works.
I'll get out some 1/8" plate next time I'm in the garage and See how it does on that thickness.
If it's passable a deal can be arranged where you can use the Craftsman or take ownership of it.
You'll find that preheating the thicker plates will make welding with a 110 machine easier to get good penetration. You can use a bernz o matic propane type torch. A better nozzle with trigger tip start will be worth the extra few bucks if John takes the welder to use because he'll have a lot of welding to do. Wire feed may speed up with frequent use.
Weld breaks at the front allowing the subframe connector to drop, it hits the track launching the car into a quasiflying mode. But I'm sure that won't happen.
In reply to Stampie (FS) :
Hanger safety wire. But if I lacked confidence in my welds to that extent, I wouldn't do it.
The point was the vehicle structure will not be compromised regardless of what he does, so he should try.
In reply to SVreX (Forum Supporter) :
Wrong !!! Zip ties are the answer.
In reply to QuasiMofo (John Brown) Forum Supporter :
The question really is do you want to? Welding upside down is nasty work. You can't just weld it, first the area to be welded has to be free of dirt grease undercoating paint and seam sealer. Can you say grinder, wire brush, propane torch, etc? All of that stuff falling down on you your clothes, your hair, and your face, ( especially the eyes )
If it's up on Jackstands you'll be working inches away from all that. A hoist you can stand out of the way and hopefully not get it too bad. Maybe. Sorta. Hopefully.
Now comes cutting and fitting. Uh, look that floor is not level or smooth. So her's a dip, here's groves, etc etc etc. and you can't forget trivial stuff like exhaust systems, wiring, and fuel lines. Oh, and if street driven, parking brake cables.
How are you going to deal with weld splatter? You know what's right above where you will be welding? Yep, carpeting and upholstery. Don't want a flaming mess? It's all gotta come out.
I take it this means the car is going to become a dedicated race car?
In reply to DeadSkunk (Warren) :
You win!
John- another +1 for a MIG welder.
Also- watch a lot of videos- know what it should sound like, and how the welds should look like when you are done. I'm betting you will temporarily weld the structure together before final welding- so there should be scraps to practice- which I would cut up to make sure you are getting the penetration.
Cleanliness is next to Godliness.
Nothing wrong with fear and being nervous- that will make sure you are paying attention.
In reply to frenchyd :
The new car will be empty empty before I start. Sound deadening and all.
It will be on a build table. Elevated about four feet at the rockers. Enough room for a fat guy and a couple tools.
Rotisserie? It will make your life SO MUCH easier. Depending on the type of car and weight, it may be worth figuring out a way to flip it over, build some sort of stand and work on it upside down.
OK I finally got out to give the little craftsman a try at some metals.
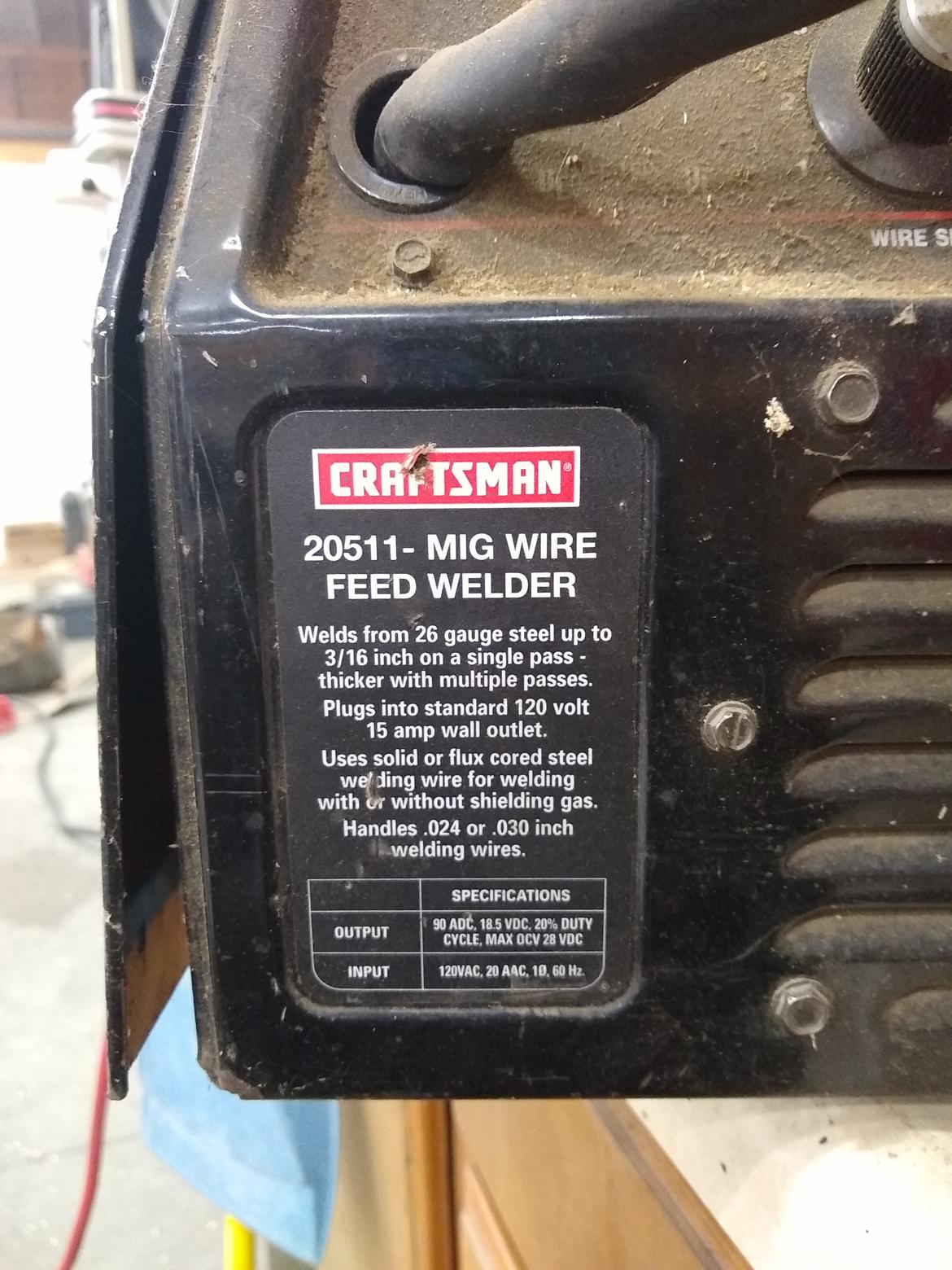
Report: I don't have any welding gas for this welder so everything was flux core wire.
Apologize for the overall weld appearances, these are literally the first 6 beads I've put out with this machine in 20 years.
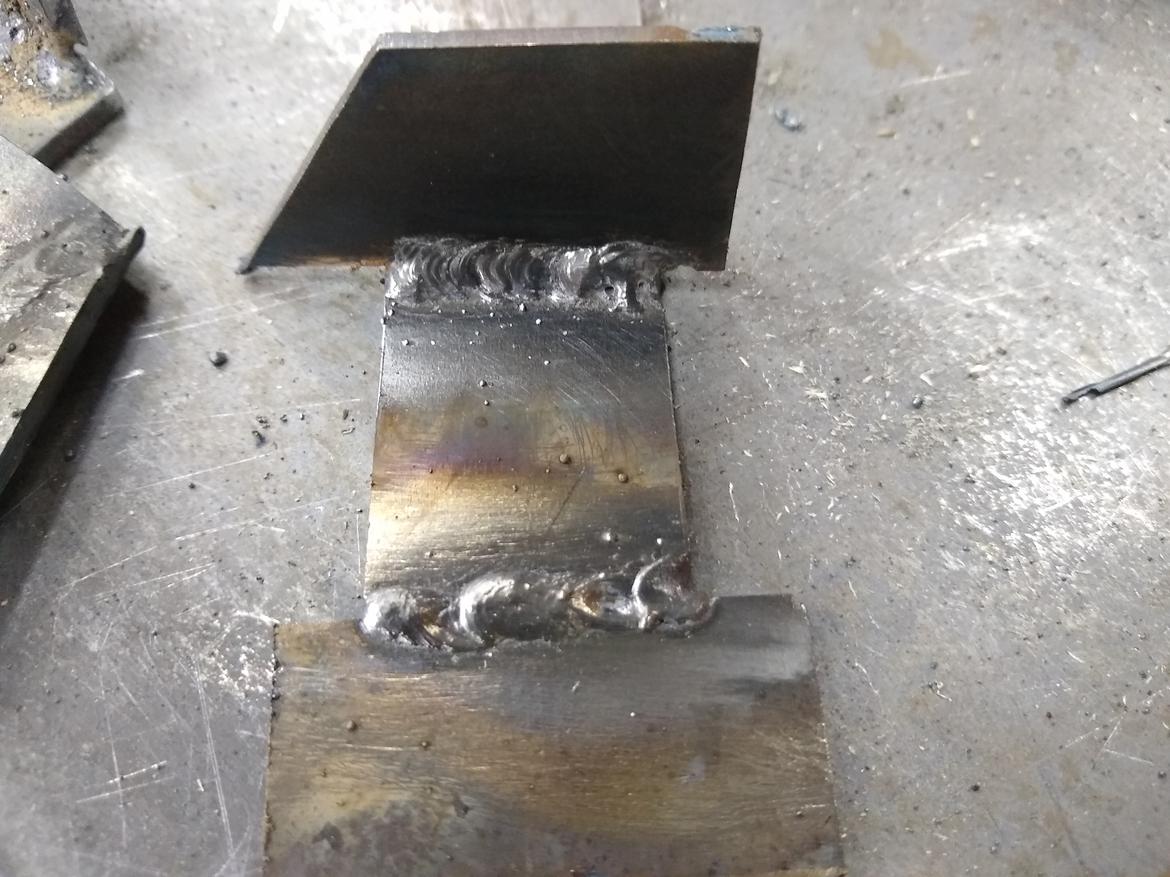
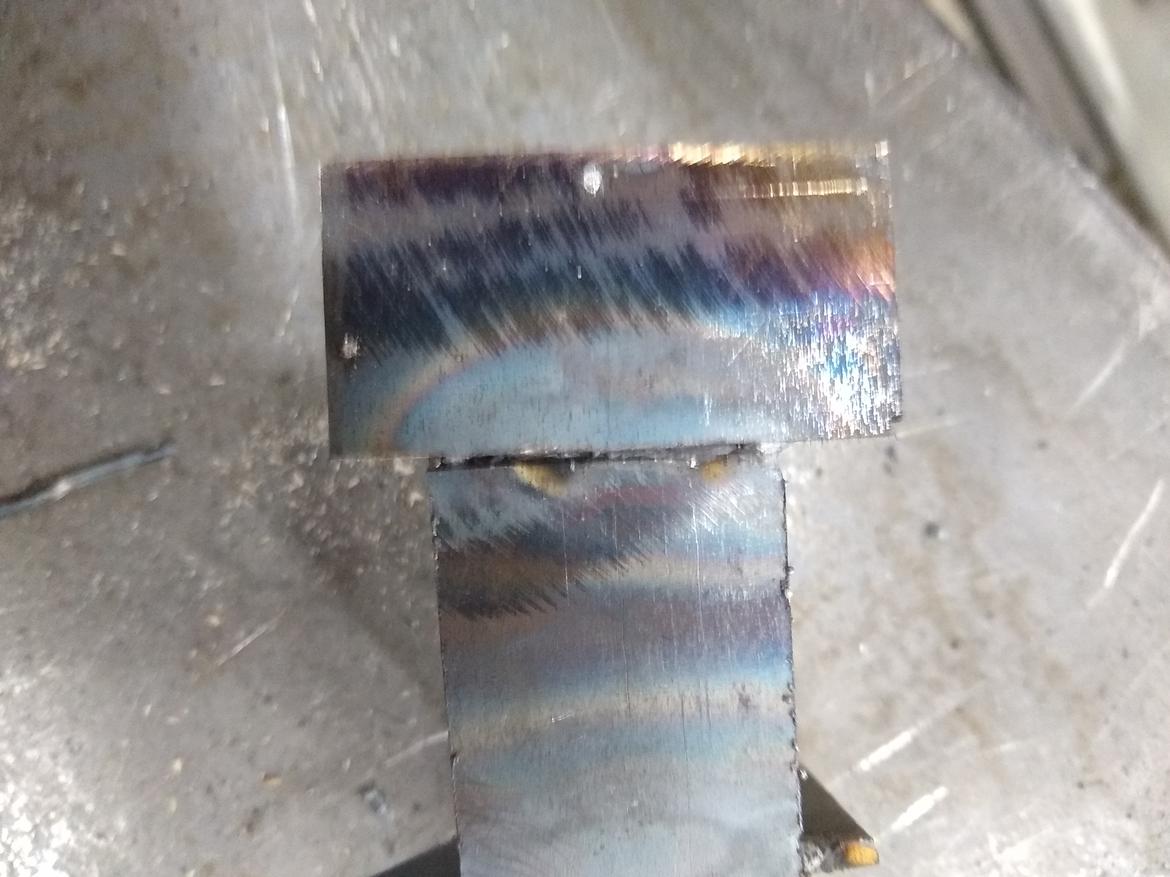
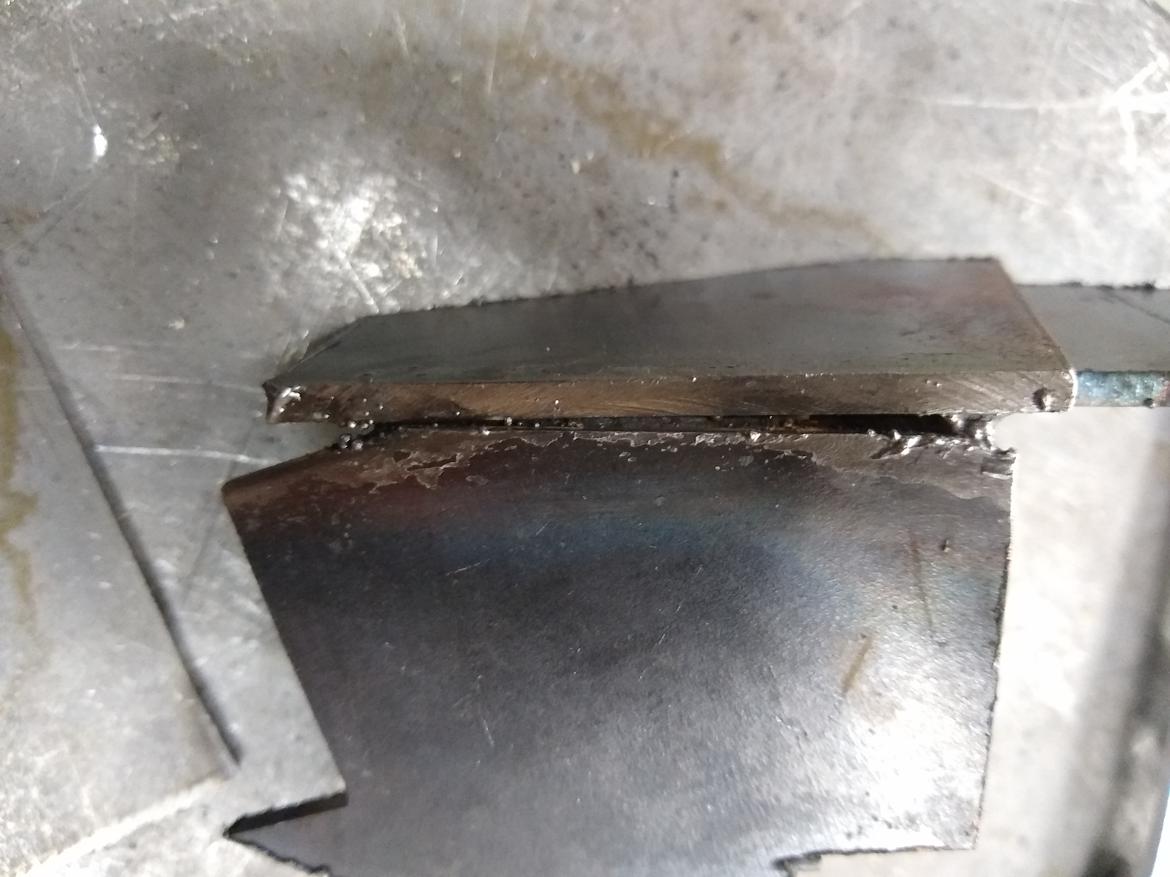
.090/thinner. Decent welds with only cleaned metal (NO fillets or chamfers). I would use this machine for welding these materials.
Lap (left) butt(right) in 10Ga
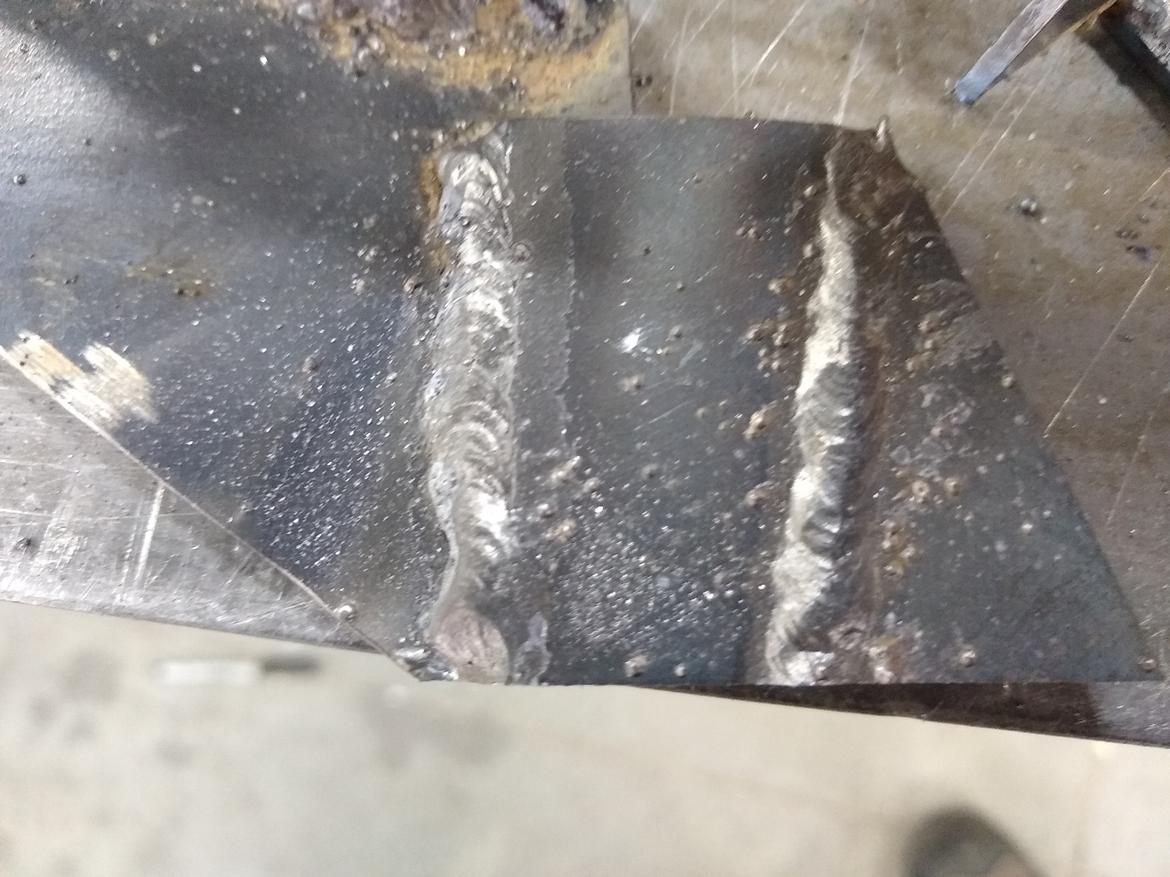
Up to .10 GA (.1345) passable welds. Decent penetration required chamfer ~1/2 through the metal. Overlap weld I'm not sure how deep into the base metal it got but it does look like it can handle pushing a puddle into this thickness.
The machine claims it can do up to 3/16 in 1 pass. I doubt it. Whenever my Dad would weld he used this machine for anything thinner then 1/8" and then busted out the stick welder for thicker stuff. That said he was pretty handy with a stick welder.
If you are interested Message me. It can be part of the deal for that thing I'm acquiring from you.
*fabricating intensifies*
In reply to gumby (Forum Supporter) :
It is QuasiNoShow so maybe we'll see welds when AC finishes his Corvair.
In reply to gumby (Forum Supporter) :
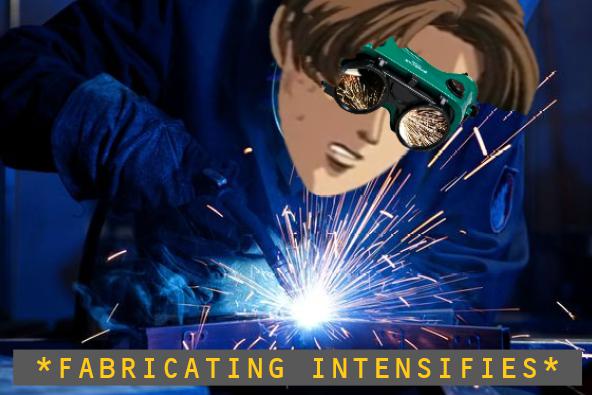