I'm starting to build my Challenge car and the front suspension will be upper and lower A-arms. The shocks have a total stroke of just over 4 inches. Where should I set the static ride height? Half extension/half compression? One third extension/two thirds compression ? For reference the A-arms are Miata ,and although the shocks aren't Miata they are very similar in overall length and stroke.
Well you could run no springs and strap it down and it wouldn't matter or run like 2k# ones and it wouldn't matter...
In reply to DeadSkunk (Warren) :
Is the weight going to be similar to a Miata? What about spring rates, motion ratio, etc.? Also, what's your swaybar situation?
Going from the presumption that your car will be Miata-like in these regards, and that you have sufficiently high enough spring rates, you really don't need more than a couple inches of travel in either bump or droop at the wheel for the Challenge autox site.
Since more bad things happen when you bottom a shock in compression, and presuming you'll have bump stops installed, I'd go for around 2.5" bump/1.5" rebound(at the shock) travel.
I like the shocks short enough that when the chassis puts a divot in the ground, the shocks still haven't bottomed yet.
And I also like the shocks as long as I can, without the springs coming loose (or falling out) at full droop.
I like zero pre-load on the springs at full droop.
This usually gives me maybe 1/3 travel in bump, and 2/3 travel in droop, though I don't really purpose for a ratio, it's just where it tends to end up. Personally I think having a lot of droop travel is good.
There are, however, lots of opinions on this.
Compression is more important than droop in a pavement vehicle. You'll probably end up trying to get as much bump travel as possible, then package the longest shock shaft you can and there's your droop.
In reply to Pete Gossett (Forum Supporter) :
I don't know where the weight will end up, but I HOPE to be at Miata weight, or less. Spring rate will be 600-650 range and sway bar can be up to 26mm thick, just because I have a 26mm that I fabbed up for the 2017 Challenge Miata, $14 budget hit. The Corollla also came with a front sway bar that's in play because zero budget hit.
In reply to SkinnyG (Forum Supporter) :
I never thought about having the chassis grounding itself before the shock bottoms out. I'll have to figure out where mine will end up. I'm starting with approximately 4" of clearance with a Miata front suspension sitting at stock height, less if the suspension is lowered at all. The lowest point on the car will be the chassis rails.
At full droop I expect the springs will come off the perch. There'll be no preload on them at all.
Edit: Front motion ratio seems to be 0.68, so having 2.75" of compression available at the shock should put the chassis really close to the ground, depending on what I do with bump stops.
In reply to Keith Tanner :
I'll have to figure out when the chassis hits (to Skinny's point) and see how much of the stroke that uses up. The whole suspension is Miata components except for the shocks, which are close to Miata dimensions. I'm using these particular shocks because they were $10 Bilsteins and valved for 475-550 pound springs in their original vehicle. I'll probably run some cut down Miata bump stops, too.
Edit: I just measured the Challenge shocks and a set of Miata Bilstein Sport shocks. The Challenge shocks are 3/8" shorter in the body and have about 3/8" longer stroke. I haven't tried, but I have very little doubt that they would bolt right into a Miata with nothing more than enlarging the lower bolt hole in the A-arm a little.
Having the ground act as a bumpstop is not a great idea. I got my Targa Miata pretty darn close to that point, and I have the damaged diff protection to show it. Leads to some discontinuities in handling. You want your travel limits to be via bumpstops, and full engagement should be just before you reach a hard limit such as control arms hitting the subframe.
So, my procedue (as used on the MG and I use a variant when starting development on a new chassis): assemble the suspension without springs or shocks but with a tire. Lift the suspension until something makes contact with something. In the front, don't forget to turn the wheel from lock to lock. If that thing in contact can be moved, look at moving it (roll fender, etc). Once you're at the point where you're running into a fixed limit (angle of ball joints, unavoidable contact with something), you're at max bump. Now set your upper shock mounting plane as high as possible so you can package as long a shock as possible. Put as much shaft into the shock body as possible. In Miataesque geometry, this is more of a factor in the rear than the front. Every Miata rear shock packs as much shaft as possible. The fronts have a bit of unused space, typically.
With those rates and with the packaging constraints of the Miata front upper control arm, you're going to have springs loose at full droop.
In reply to Keith Tanner :
OK. That makes sense to me. As for the rear. it's a live axle, so if I manage to scrape the differential I'll have already had some pretty big other issue. There's a trophy for Most Spectacular Failure.
Since I can create all kinds of clearance for the front suspension will the upper ball joint be the limiting factor for upwards travel before the shock bottoms out?
tr8todd
SuperDork
4/23/20 9:24 a.m.
You want to try and keep the travel in the middle of the stroke. Start by setting them up at 30% and limit travel to 70%. You can stretch that a little, but don't go past 20 and 80. If you find you have to have more travel than that, then you picked the wrong shock.
Sounds like it.∆
To control droop, you could try limiting straps. You could make different lenghts to preload the suspension if desired, and take them off for the drags. Maybe use old seatbelts or tie down straps to make them? Seems better than chain or cables as they with stretch a little.
In reply to Gearheadotaku (Forum Supporter) :
I'm not worried about droop on the front. The Challenge Miata and my ITB VWs would all have the springs come off the perches at full droop. I wire the springs to the upper perch to keep them from flopping all over and the coilover sleeve on the shock body will behave like a guide. Ideally I'd stumble across some tender springs for Challenge money, but that's very unlikely.
You don't really need to worry about limiting droop on an independent suspension. Once the spring unloads, it's unsprung weight vs damping and you never have enough time for the shock to extend very far. With a live axle, you can get one end forcing the other one down but this is more of a maximum articulation offroad situation.
And you should be able to use 100% of the shock's extension. I don't think Bilsteins are damaged by using 100% compression either, but you really want the bumpstop to take that hit for handling purposes anyhow.
As for ball joints - watch the upper and lower as well as the tie rods. I suspect they'll all limit out about the same time (it's fascinating to put a well-designed factory suspension to full bump and discover all sorts of little tweaks that only come in to play at this point) but ignore one at your peril. You may also want to watch your ground clearance :)
I agree, differential clearance may not be a prime concern of yours! You're basically building the same setup as my MG then.
For entertainment value. I take a picture every time I do this because there's a certain demographic that goes nuts.
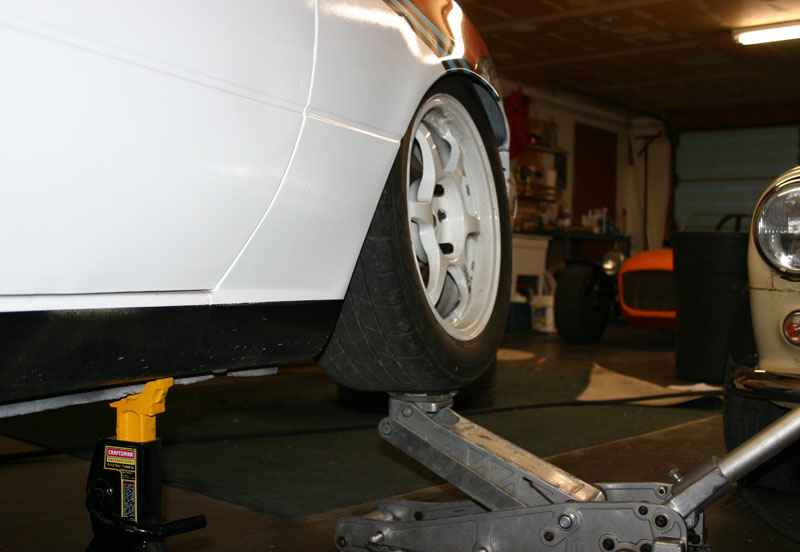
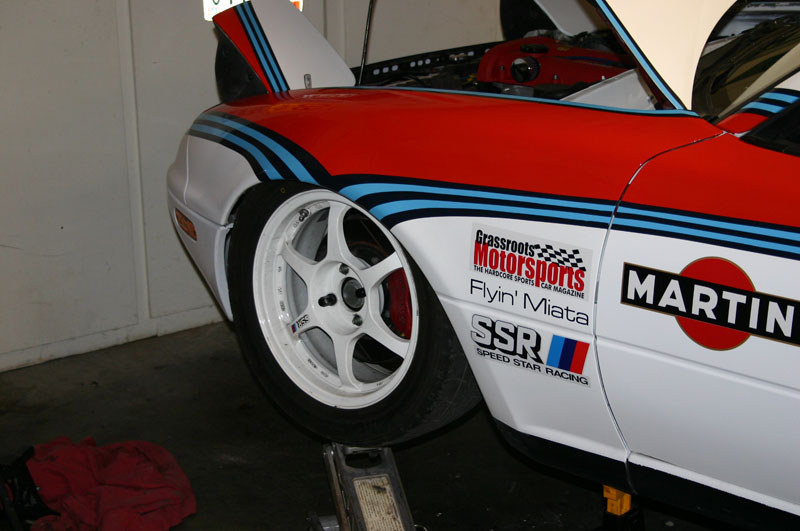
Apparently I don't do it with the MG...
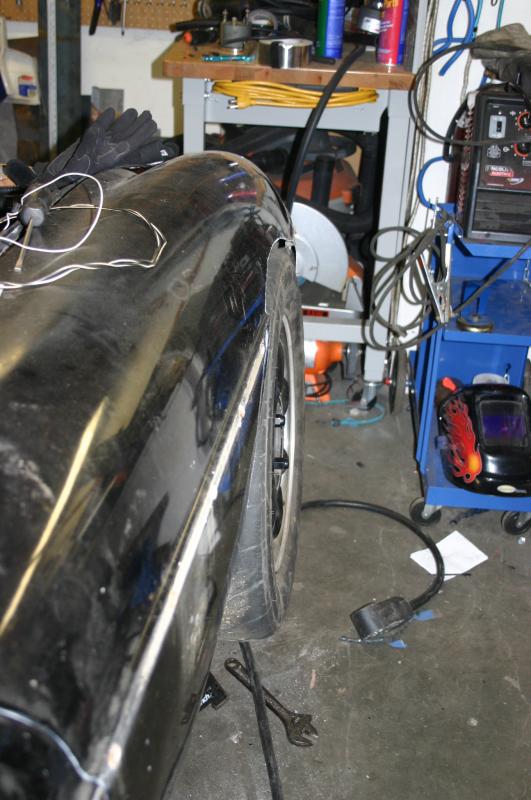

Driven5
UltraDork
4/23/20 10:38 a.m.
In reply to DeadSkunk (Warren) :
Are you confined by the positional relationship between the suspension and the upper shock mount, as would be on an existing chassis, or do you have the freedom to set them wherever you want/need them to be? It sounds like the latter, but I wanted to be sure as this would affect my approach.
Note: I'm not using the ground as a bumpstop.
I'm making sure I have enough travel that I COULD hit the ground with the chassis - and then I add bumpstops so that it doesn't.
I like enough droop travel that I'm not picking a driven wheel off the ground in roll, or some unusual movement. I'm with you, Keith - I want lots of bump travel, but not at the cost of droop; I want both.
On my '61 C10 (my current project), I used off-the-shelf C10 shocks so I could always get a replacement at any auto parts store.
I let the front suspension hang in full droop, stopped by droop stops on the upper a-arm, and tacked the shock mounts in place (that way I can easily remove a full-extended shock without having to compress it, if I ever have to replace it).
Then I set the frame on the ground at full bump, crossmember on the floor, and made sure the shocks weren't bottomed. Then I put long enough bumpstops in to keep it off the ground.
In the rear, I made sure at full bump the shocks were not bottomed, then added bumpstops. Droop is going to end up where droop ends up.
In reply to Driven5 :
I'm using Miata suspension components in a home built tubular chassis, so there isn't much latitude to move stuff around. The inclination of the shock might have some leeway, but nothing else.
In reply to SkinnyG (Forum Supporter) :
Given what you guys have said, I believe my chassis would hit the ground before the shocks bottom out without any bump stops. With bump stops it won't, but I'll be checking as I fab up mounts and assemble the suspension bits to the chassis. I'll basically have the same range of motion as a Miata, but the chassis rails are closer to the ground to begin with.
Driven5
UltraDork
4/23/20 12:39 p.m.
So if the upper mount height from the lower lower control arm mounting point is already fixed at a pre-determined distance, then that limits your options a bit more than I was thinking the question implied. However, remember that with the exception of contacting the stops, your shocks don't care where they are in their travel...So neither should you. Generally speaking, your selection of ride rates and travel constraints will determine your minimum amount of static shock extension not the other way around. The main caveat to this being if there is not enough available shock travel in bump and/or droop when the suspension/chassis is at an acceptable ride height.
The numbers provided so far (>600 lb springs, .68 motion ratio, and <Miata weight), and assuming a ~50/50 weight distribution. Biased to the conservative side, you're looking at a natural frequency of somewhere in the 2.33Hz range. This translates to a 1.8" at the wheel (<1.25" at the shock) of natural static compression, which is becomes the inherent functional droop travel. I personally would then target having that much free travel available from ride height in bump from the static position as well, especially if trying to minimize bumpstop usage.
Then the selected bumpstop length to prevent mechanical contact (assuming <2.75") added to the free bump travel length becomes the shock extension at the minimum functional ride height.
In reply to Driven5 :
Really, the only thing I can vary is the height from the A-arm pivot to the upper shock mount and then adjust the spring perch to get whatever ride height. All I'm mulling over is how much droop to leave and maximize the compression. I could even put a bump stop on the upper A-arm to prevent the shock from bottoming if that left a bit more compression stroke , or just cut the bump stop on the shaft down to some minimum length. I need to get everything mocked up and run it through the full range of motion before finalizing the location of the upper mounts. I may just fab up a dummy shock at some predetermined fixed length to replicate the ride height with an arbitrary amount of droop. Lots of good input in this thread for me to play with.
Driven5
UltraDork
4/23/20 5:40 p.m.
If you can vary the height of the lower pivot to the upper mount, I would be looking to set it such that the springs fully unload at full shock droop from your intended ride height, but not much beyond that. This will prevent having unnecessarily wasted shock travel at ride height.