I have neither talent nor the access to a proper TIG welder. I am looking for alternatives to bond various bends of aluminum piping for a new intercooler project I'm starting on the FD. Does anyone have any experience with this stuff?
http://www.alumiweld.com/
I'm curious if it will hold 10-30 psi of boost and whether it is easy to create a proper air-tight seal? Assuming two equal lengths of 2.75" OD pipe were bonded together, how much shear do you think it could take before failing?
Thanks!
Matt D.
30 psi on a 2.75" pipe is going to give about 178 lbs of force trying to blow those pipes apart, and it won't be in shear. Fun.
Never tried the stuff, so no direct feedback from me. I'd start by contacting the manufacturer.
Do you have access to a MIG that can be set up for aluminum welding? Do you know someone who can weld aluminum? Or can you do it in steel?
oldtin
SuperDork
7/11/12 6:11 p.m.
alumiweld test
bottom line - these guys say it pretty much works - don't use it for structural bits - what's even better harbor freight version works too ($5 vs $50)
Keith wrote:
30 psi on a 2.75" pipe is going to give about 178 lbs of force trying to blow those pipes apart, and it won't be in shear. Fun.
Never tried the stuff, so no direct feedback from me. I'd start by contacting the manufacturer.
Do you have access to a MIG that can be set up for aluminum welding? Do you know someone who can weld aluminum? Or can you do it in steel?
I asked about shear because some of the weight of the intercooler is supported by the pipes themselves.
I have a flux core MIG welder so that won't fly :( I don't know anyone who can TIG weld locally. I thought about doing it in steel but didn't want my pipes rusting from the inside so I purchased aluminum bends.
oldtin wrote:
alumiweld test
bottom line - these guys say it pretty much works - don't use it for structural bits - what's even better harbor freight version works too ($5 vs $50)
Thanks for the link. I may give it a shot with some scrap pieces of pipe and see how strong it is. At least the buy-in is low vs a TIG welder ;)
Vigo
SuperDork
7/11/12 6:42 p.m.
I used HF alumiweld to stick a plate on the end of this intercooler tank and 'accidentally' gave it the full beans of 110psi shop pressure. It didnt blow off or distort..

I think it's perfectly strong for holding pipes together. Getting the heat right is the hard part.. You need mapp gas as a MINIMUM and something hotter would be better, but on the other hand it's pretty easy to just blow away thin aluminum if you use too much. It'll take some fiddly time to get it right. In the end you might go through enough money in chemical heat to make you wish you'd paid someone to weld it with electrical heat, but that's not to say you shouldn't try!
Vigo wrote:
I used HF alumiweld to stick a plate on the end of this intercooler tank and 'accidentally' gave it the full beans of 110psi shop pressure. It didnt blow off or distort..
Dang, that's good to know. Impressive.
vazbmw
Reader
7/11/12 8:24 p.m.
In reply to Armitage:
I don't know about the product that is linked in the thread, but I do know you can weld aluminum with a torch. I had an instructor that showed us how to do it, although I have never done it on my own. I am sure there are some sources on the net that explain, but before TIG folks welded aircraft in that manner. Basically he carborized the weld area to protect the weld pool, then started welding. He welding to beer cans together. He was highly skilled, but he made the point that it can be done to thin wall metal:
How to:
http://www.howtodothings.com/home-garden/how-to-gas-weld-aluminum
I used it for the EDIS pickup for my 924. It's heck for stout.
Seems to work best when the stuff is clean. The trouble with large items is that you have to get everything up to temp at the same time, keep it hot while you apply the alumaweld, then cool it off while not moving it.
Basically think of it like soldering on a large scale.
I think I would consider my intercooler mounting options a bit more carefully if you are using the pipes to support the I/C. Anything mounted on the pipes will fail eventually, aluminum doesnt have much resistance to repeated vibration. There has to be somewhere to weld a few tabs onto the IC and bolt it (with rubber isolators a-la OEM) to something more solid.
Pipes for piping, brackets for supporting.
That being said a friend of mine build a several-hundred-more-than-stock-horsepower Mirage 4G63T swap and JB Welded his first IC pipes together. They held.
I just realized I do have experience with this stuff. We used it to (finally) fix the rad on my Locost after an "experienced" TIG welder did his best to destroy it. Never had a problem but it sure was ugly when we were done. I'd forgotten all about that.
I agree with the above, though. Find some way to support the IC if you can.
I tried to use the HF stuff to attach a flange to the top of a radiator core. Unfortunately the radiator pulled away the heat so bad i could hardly get the stuff to melt, but at the same time the torch was blowing through the angle aluminum I was using for a flange. The stuff that did stick to the radiator wasn't coming off unless I hit it with a grinder. I may try it again for some intercooler pipes. It might be a little easier without a huge heat sink pulling the heat out.
Raze
SuperDork
7/12/12 6:55 a.m.
Armitage wrote:
I have neither talent nor the access to a proper TIG welder. I am looking for alternatives to bond various bends of aluminum piping for a new intercooler project I'm starting on the FD. Does anyone have any experience with this stuff?
http://www.alumiweld.com/
I'm curious if it will hold 10-30 psi of boost and whether it is easy to create a proper air-tight seal? Assuming two equal lengths of 2.75" OD pipe were bonded together, how much shear do you think it could take before failing?
Thanks!
Matt D.
We coupled our metal 2.5" intercooler piping to our 2.25" intercooler inlet/outlet on the XR4 that sees over 30psi of boost by welding a bead around each end of the intercooler pipe with a stick welder (cheap at harbor freight), and used NAPA Tractor Trailer stick heater hose (working temps like 200+ deg F at 90 psi) secured with t-bolt clamps. We ruptured silicone that was supposed to be up to the task, and we'd pop off without the beads. Switching to the stick heater hose and running a bead fixed our problems...
WhiteLX wrote:
I tried to use the HF stuff to attach a flange to the top of a radiator core. Unfortunately the radiator pulled away the heat so bad i could hardly get the stuff to melt, but at the same time the torch was blowing through the angle aluminum I was using for a flange. The stuff that did stick to the radiator wasn't coming off unless I hit it with a grinder. I may try it again for some intercooler pipes. It might be a little easier without a huge heat sink pulling the heat out.
You might try heating the whole radiator to 450° in the oven first (dont tell SWMBO
). Youll have to handle the thing with gloves, but Id imagine youre doing that anyway. Should help keep the heat in the radiator more even.
Way back in the Dark Ages, there was a paste containing solder which you spread on the crack, wires etc then you lit it. It would basically solder itself that way. I have not seen the stuff in years, though.
Curmudgeon wrote:
Way back in the Dark Ages, there was a paste containing solder which you spread on the crack, wires etc then you lit it. It would basically solder itself that way. I have not seen the stuff in years, though.
Not sure for aluminum, but that stuff totally still exists. It's used in the production of fuel rails these days- mostly made from stainless. I don't know how to get it for a non-commercial level, though.
yes- all modern fuel rails are soldered. including the 2100psi gas direct injection ones.
Thanks guys, I may give it a shot and report back. When I say some of the weight of the I/C is supported by the pipes I don't mean a lot. The I/C sits on a cross-bar and is captured in the front by a duct. The pipes hold it in place against the duct plus they have to support any side loading under hard cornering (which is why I asked about shear). If I had to ability to TIG weld aluminum, I'd add brackets/tabs to the I/C :)
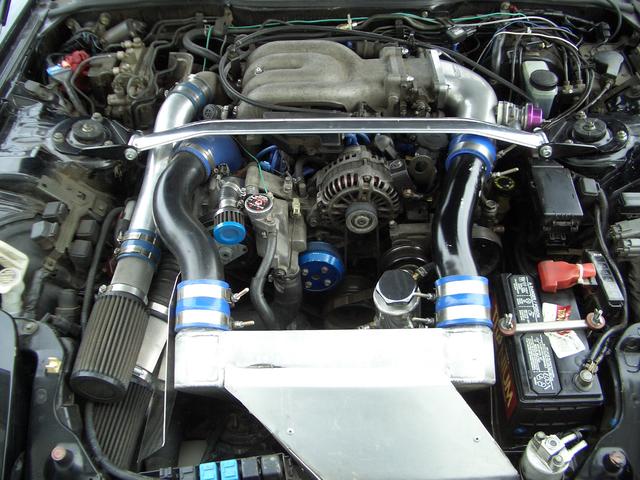
Well, use the Alumaweld to add brackets to the IC and have one less thing to worry about.
Also a radiator shop could add brackets as well, probably for fairly cheap. Rough up some brackets and take it on down.
alfadriver wrote:
Curmudgeon wrote:
Way back in the Dark Ages, there was a paste containing solder which you spread on the crack, wires etc then you lit it. It would basically solder itself that way. I have not seen the stuff in years, though.
Not sure for aluminum, but that stuff totally still exists. It's used in the production of fuel rails these days- mostly made from stainless. I don't know how to get it for a non-commercial level, though.
yes- all modern fuel rails are soldered. including the 2100psi gas direct injection ones.
IIRC isn't that how bicycle frames are brazed?
Curmudgeon wrote:
IIRC isn't that how bicycle frames are brazed?
Oxy/acetylene and filler rod.
On youtube.
Does seem like most framebuilders are generous with the flux, though.
alfadriver wrote:
Curmudgeon wrote:
Way back in the Dark Ages, there was a paste containing solder which you spread on the crack, wires etc then you lit it. It would basically solder itself that way. I have not seen the stuff in years, though.
Not sure for aluminum, but that stuff totally still exists. It's used in the production of fuel rails these days- mostly made from stainless. I don't know how to get it for a non-commercial level, though.
yes- all modern fuel rails are soldered. including the 2100psi gas direct injection ones.
Any idea what the stuff is called? Sounds neat.
i wonder if i can use this stuff on some pot metalish stuff.
got a broken window guide piece in my neon that looks like aluminum pot metal. replacements are not avilible. and finding an unbroken one is like finding a winning lottery ticket in the trashcan and the courts letting you keep it.
m4ff3w wrote:
alfadriver wrote:
Curmudgeon wrote:
Way back in the Dark Ages, there was a paste containing solder which you spread on the crack, wires etc then you lit it. It would basically solder itself that way. I have not seen the stuff in years, though.
Not sure for aluminum, but that stuff totally still exists. It's used in the production of fuel rails these days- mostly made from stainless. I don't know how to get it for a non-commercial level, though.
yes- all modern fuel rails are soldered. including the 2100psi gas direct injection ones.
Any idea what the stuff is called? Sounds neat.
No, I've just seen the process of making rails.
I do understand that solder that is called "silver solder" is supposed to be the bees knees, though. Friends of mine have used it, and really like using it. I'll talk with my fabricator guy Monday, and see if he has insight of what it's called.
In my pre-TIG and MIG days I tried the magical pot metal rods and generally made puddles of the parts I was trying to fix.
I know I'm always bloviating about "doing it right" - but for stuff like this, you've got to know someone who knows someone with a TIG who's a benevolent gearhead who keeps the beer stocked w/ jobs like this.
My TIG-MIG-lathe-mill make as much beer as they do parts...
Silver solder, BTW, is not for AL. It's the perfect thing for close fitting steel parts, or sticking dissimilar metals together, ie - copper to steel to bronze.
I picked some up at H.F. this weekend. The only result I have so far is that a propane torch isn't hot enough. Going to pick up a bottle of MAPP substitute tomorrow.