I have this 130hp BMW bike engine with no purpose. Then I found a sand rail thing on FB with a VW beetle transmission. The clutch on the BMW is on the centerline of the block, but with the transmission bolted up, the driveshaft exits 6" right of center. I don't want to put all the weight on the left to make the shaft on center and the 18" shaft probably won't make that steep angle.
Question is, what now? I could probably make up a short shaft to marry up the BMW crank with the VW input spline but I no longer have access to the machines required to make a plate with both bolt patters. Bolt the engine and the transmission separately to the frame with a Guibo to reduce flex and vibration?
I haven't verified yet is the BMW crank and driveshaft rotate in the same direction when in gear, I like the BMW 6 spd., but using the VW trans will give me reverse.
Thoughts, suggestions, know any jokes?
Sand Rail - Vee thing.

BMW KJ-1200rs without transmission:

I won't go under oath, but I think it was driveshaftspecialists I used when I needed a custom driveshaft for my S52 swap in my E30.
slip shaft axles and shift the trans to one side?
Let's assume for a minute that the engine and trans weigh the same (which I know they don't). If you move the trans 3" to the right and the engine 3" to the left, you haven't shifted any weight. What you have done is made the axles move in different arcs than the suspension since one is longer and one is shorter. So maybe use splined slip (look to tractor PTO shafts) for the axles so they can change length as the suspension moves.
My first thought was to move the driver a few inches left or right, but looking at that cage, that ain't happenin.
This one is more common these days... it's a tube that slips over another tube instead of splines, but it allows for variable length, and uses pretty commonly-available u-joints.
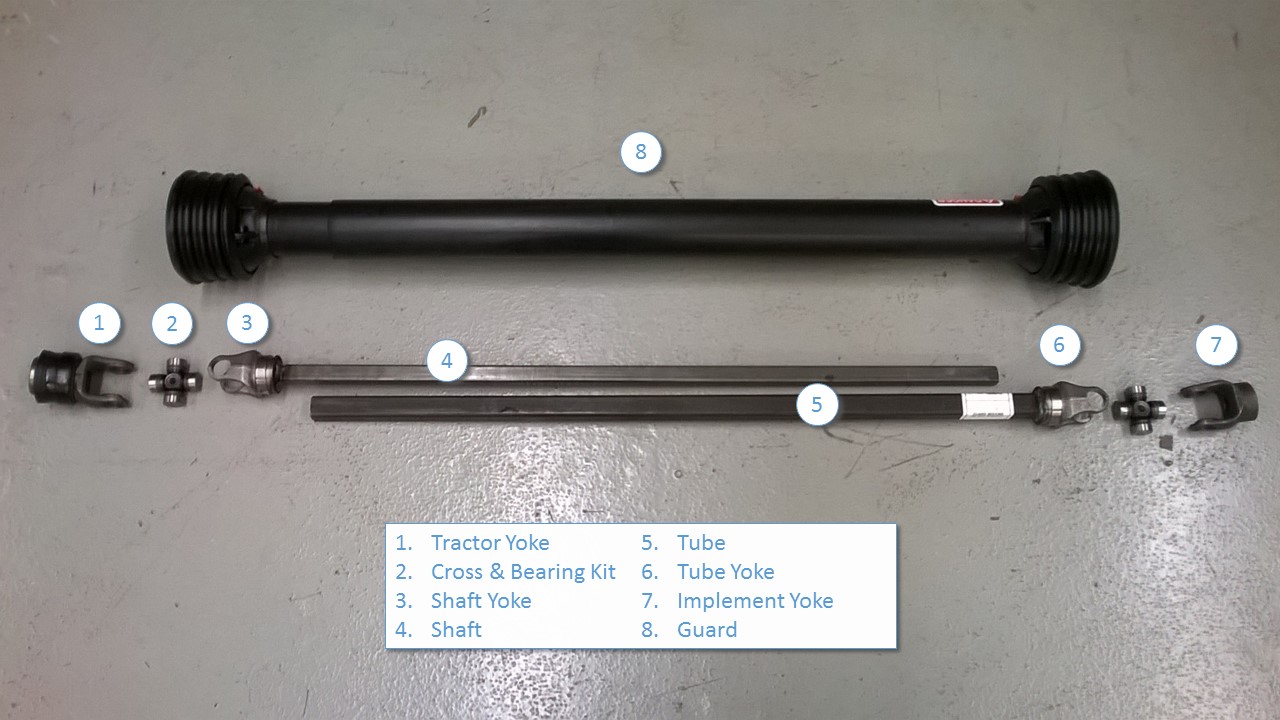
Hmmmmm...... Check my math:
Assume engine & tranny mounted on the CL. Turn the engine driveshaft inboard until it face the trans input shaft; turn the transmission outboard until it faces the driveshaft. Using the 18" driveshaft, when they are lined up CL to CL, each has moved 9.5 degrees. Sine= O/H or 0.16666666. Inverse Sine of that is 9.5*.
Now the engine-trans are lined up and each U Joint at the transaxle output is dealing with half of the 9.5* or 4.75 degrees.
I"d be tempted to get the shafts aligned and use a Lovejoy coupling.
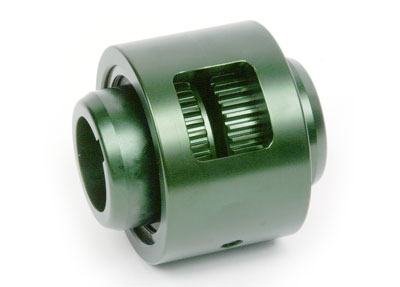
The next option would be a couple of CV joints and a short driveshaft. Then you could offset the engine and with the CV joints, angles aren't very important.
Thanks Toy, never thought of a CV !! 47 - 50 degrees of flex, you bet. I would certainly box in the rear half of the frame into the roll cage better, but that would come with the engine mount system.

I just recently learned how awesome these engines are with the centered clutch and divorceable trans.
Perfect for this kinda swap to mount to a transaxle that shifts like a normal car and has reverse.
I like the CV idea, but need to keep it short. Long shaft at high rotation speeds (motorcycle engine speeds) is a recipe for harmonic issues.
In reply to Robbie (Forum Supporter) :
There is a formula for driveshaft diameter vs speed and length. There are also some online calculators. The driveshaft for the Ecotech swapped B210 I built needed to be 3.5" in diameter to avoid critical speed failure. It used Solstice CV joints on both ends and worked perfectly.
https://spicerparts.com/calculators/critical-speed-rpm-calculator


Would balancing the shaft help?
In reply to 914Driver :
I didn't balance mine. I put it in the air and spun it about 3500 rpms. It didn't vibrate so I sent it. It has about 24 hours of track time so far without failure.
In reply to Toyman! :
Yes I agree just use the calculator.
Main differences here are that a, your driveshaft is at engine speed (higher than regular car driveshaft speed in all gears except OD), and b engine speed on a MC engine can be much higher than a car engine.
So instead of screwing it up and only getting a vibration while in top gear at 45-55 mph you get a vibration at pretty much all speeds in all gears.
I am no driveshaft engineer, but I think cvs also really help vs u joints.
I can't imagine having the shaft speeding up and slowing down rotationally helps with vibration.
I don't see a big downside to the engine laying over. Just make sure everything else is on the other side.
What would the weight offset be if the engine is offset so that the half shafts are equal? Just add lead weight to the light side? This is for using the BMW transmission with the VW transaxle? Still using the VW swing axles?
Google tells me the transmission weighs 90 lbs. Off set to starboard 6" would not be horrible, but would one shaft 6" longer and the other 6" shorter effect geometry?
Robbie (Forum Supporter) said:
I am no driveshaft engineer, but I think cvs also really help vs u joints.
I can't imagine having the shaft speeding up and slowing down rotationally helps with vibration.
This is very noticeable in my RX-7 when U joint angles get over 2 degrees. There is a noticeable shudder in the drivetrain when under light load, such as driving at 70-75mph. There is about one meter of driveshaft that has to accelerate and decelerate twice per revolution, and when under LIGHT load, the inertia of the driveshaft overcomes the inertia of the pinion gear and the transmission's mainshaft and everything buzzes horribly. It also eats transmissions. It's okay when going uphill, but when on flat ground or going downhill, have to slow down to 62-65mph or so.
I see the harmonic damper that Mazda fit to Miata pinion flanges and think "YES! Yes I want one of those!"
Corvettes, for one, (944's as well I think) have long driveshafts attached to the engines...
7k rpm +. I've heard of guys with 8.5k redlines and no talk about issues. They are a pretty straight shot though, just using guibos.
Robbie with the challenge Datsun roadster just turned his rear end and engine to deal with this same issue. Hasn't been tested yet to my knowledge but in theory it should be fine.
as suggested already, maybe this would solve?
In reply to jfryjfry :
No Guibos on 944s or Corvettes. The driveshaft is a straight shaft running in a series of bearings in the torque tube. This helps curtail resonances that would otherwise cause the shaft to whip around like a jumprope.
I forget what Corvettes did, 944s had a much maligned rubber-damped clutch disk but the transmission end clamped the shaft straight to the trans's input shaft.
Tempests, on the other hand, were WEIRD. They had a "rope drive" driveshaft between the engine and trans that was NOT straight, it was curved by design for floor clearance and resonance negation. It also could twist by something like 3/4 of a turn!

(The engine was, indeed, half a 389. Different bellhousing pattern from the V8s. And for 194ci they were amazingly slow)
In reply to Pete. (l33t FS) :
C6 at least has rubber guibos and they and the 944 have long driveshafts turning engine speed.
the only point was that long driveshafts turning engine speed has been done and could be an option.