The victim, err patient, is my RX-7. It has MS2/Extra on a 3.57 board, and an AEM X-series wideband gauge/controller.
I bought it thinking I could do a CAN connection, not realizing that you need MS3 to speak AEM. Oh well!
My specific issue is that, with the engine running, the gauge and the reported input to the MS are different, usually by .3 of a ratio but sometimes .5. (Gauge reads 12.5, readout on TunerStudio is 13.0, for instance) There seems to be a skew towards the lean end, where 22 on the gauge reads 17 to the MS unit.
Now, the FUN part. With the engine off, the readings are the same. Sometimes. Other times the skew is there all the time.
MS and gauge are powered up by the same power source (an auxiliary fuse box) and are grounded to the same point on the engine. I was doing some testing for another issue thought I was having and found a lot of charging system ripple, so I used a 10 gauge wire and a beefy relay to connect the fuse box directly to the battery positive. Changing the ground would best be done with an entirely new wiring harness so I'm trying avoid that. Either way the power and ground are literally the same source, so there shouldn't be any voltage differences at play.
Any ideas before I drop coin on an MS3Pro and a set of ID injectors and a bunch of other things?
Any way to log the A/F meter w/o the MS? Just the voltage.
If it's not a voltage error, it could be the AEM sending out different data....
Can you calibrate the guage? I've never used AEM but my Innovate WBG's had a procedure to calibrate them in free air.
In reply to alfadriver (Forum Supporter) :
Not in any meaningful way, sadly. I have a 2 channel digital scope but no way to correlate its data to MS.
In reply to ShinnyGroove (Forum Supporter) :
The discrepancy is variable, though. That's like aligning a car with bad bushings.
On the X series make sure you have the brown to SIGNAL GROUND or whatever wire you use for your dedicated signal connection to the ECU (should only be 1 wire but early harnesses weren't labeled as such)
Check the calibration you are using in tools>AFR the X series volts/afr is different than some of the other AEM output
If both those check out, use the AEM software to put out set voltages at all AFR (basically flatten the cal curve) and measure the voltage on the MS wire and check for offset. If there is some, use this offset to build your new AFR offset (i.e. if output is 1v and you receive .8v use that as your min reading, if output 4.5v and you recieve 4.3v use that as max, etc)
In reply to Paul_VR6 (Forum Supporter) :
According the info I have, all "ground" pins are on the same ground plane.
2008 Me used an RS Autosport harness. 2020 Me has no berking clue what he did, but be probably did everything by the book after seeing people have lots of issues due to being inventive with grounding or wiring.
Paul summarized it pretty well - make sure the brown wire is grounded to the MS and the black wire is grounded elsewhere, usually the battery or head. How exactly do you have your sensors grounded?
I've never used an AEM wideband, but if it offers separate signal and power ground you definitely want to use them. The square wave feeding the heater will introduce a ton of noise.
If you've got any electronics skill, it shouldn't be too hard to set up an Arduino to receive the AEM format CAN and send it back out in the format that the MS3 understands. Maybe $40 worth of hardware and a couple pages of C code.
In reply to MadScientistMatt :
2008 Me is not answering his phone
Without pulling everything apart to access the wiring harness, I assume all sensors that did not have a specific return to the computer are all grounded at the same bolt on the engine as the MS's main ground. (Which, I recall, was six wires that very soon out of the DB37 joined into one heavy gauge wire)
Yes, I know this is no longer accepted practice. I never felt like tearing the engine and interior apart to redo the wiring, and it always worked before.
In reply to codrus (Forum Supporter) :
I'm a hardware hack, not software. For that amount of effort, I'd just as soon contribute to the economy and buy new hardware.
But that also entails pulling apart the engine bay and interior....
Had two epiphanies.
One, the car was wired per the diagrams for a 1.01 board, which is what I'd started with. There wasn't a separate ground plane for sensors.
Two, I'm making it a lot more difficult than it needs to be. The Big Fat Ground Wire coming from the five main ground pins is grounded at the engine, and all of the sensor grounds also go to that same bolt. All I'd need to do would be to cut the Big Fat Ground Wire near the computer and isolate the underhood grounds from the engine. Big Fat Ground Wire in the harness goes to sensor ground on the computer, and the other end goes to the battery. Should be simple and no fishing a bunch of wires through and taping them to pre-existing looms.
...and I see that the five pins on a 1.01/2.0 board are 7-11 and they are 15-19 on the 3.57 board. Huh. Well, this is going to be interesting. How does it even work at all?
Pete. (l33t FS) said:
How does it even work at all?
As someone who has made a career out of swearing at computers for a living for 30+ years, that's pretty much the conclusion every time.
It's at this point that Pete entered berkeleyit mode.
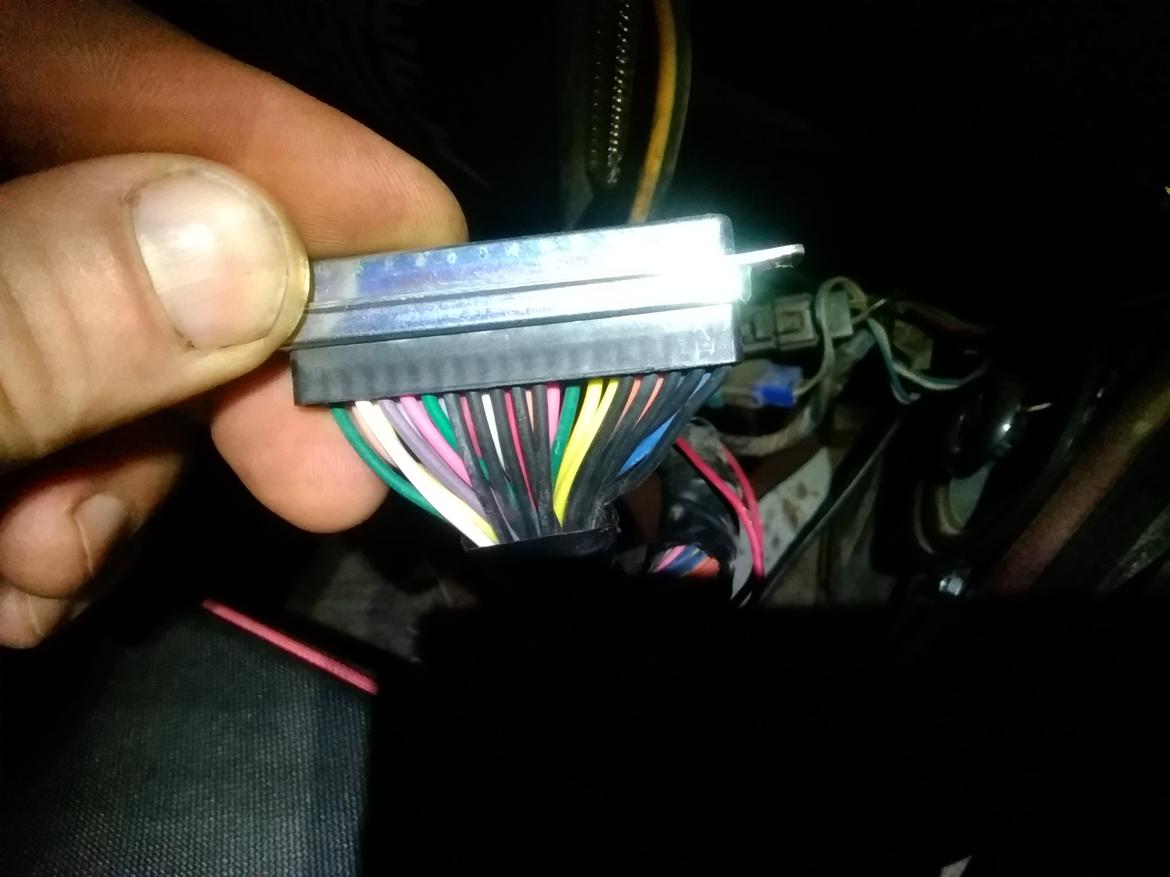
All ten are populated by ground. Well, that makes it cross compatible, I suppose. Now, let's see what pin 3.57 uses for sensor ground.

Pin 7, okay... and crank sensor will go to pin 2 when I put the 36-2-2-2 wheel on for sequential injection.
...uh, pins 1 and 2 are empty. And I don't see how one could remove/add pins without being destructive.
Yay.....
Well, that didn't help the wideband discrepancy any. Key on engine off with an engine that had not been running, the guage was reading 24.8 and the MS was reading 18.7. Tweaked the curve so the MS read 24.8 (had to set it to something like 4v=22.6:1) and started the engine with the MAP sensor unplugged. Rich city. Even with the engine off the gauge was hanging out around 12:1, so I tweaked the lower end to match (had to set it to like 1v=5:1). Ran the engine "normally" and the middle of the range was crazy-bad. So I gave up and set it to the standard X-series settings. (1v=9.7, 4v=16.8)
Need to put it together and get outta here, will deal with it more tomorrow.
Pins 1, 2, and 7 through 19 all go to the same point; any of them can be used for sensor ground. Our current harness has one wire that's black with a white stripe for this purpose. Or you could add a wire with one of these kits.
https://www.diyautotune.com/product/ms-harness-extra-wire-kit/
In reply to MadScientistMatt :
So, you are confirming my original suspicion that there's no point in grounding sensors direct to computer? If they are all otherwise grounded to the same point. (Aside from any potential voltage drops across the actual wire, I suppose)
To be honest, I'd rather go with a Pro box when it comes time to read a crank sensor. The sensor input seems to be a lot more robust. Plus, I'd also like to use a GM style MAF.
Pete. (l33t FS) said:
In reply to MadScientistMatt :
So, you are confirming my original suspicion that there's no point in grounding sensors direct to computer? If they are all otherwise grounded to the same point. (Aside from any potential voltage drops across the actual wire, I suppose)
Not really, The ground wires from the ECU to block carry enough current that there's enough voltage drop to affect the readings. You will get more accuracy from grounding to the ECU.