We’ve spent a lot of time discussing welding skills and technique in this magazine, but maybe it’s time to back up and start at the beginning: How do you decide what kind of welder to use in the first place?
Sure, the skills and techniques we’ve covered apply to all types of welding, but we’ve generally assumed that our readers …
Read the rest of the story
In reply to Carl Heideman:
No that I'm an expert by any means (far from it), but here's my $.02:
As it pertains to which of the two is easier to learn on, it seems the common advice is start with MIG if you've never welded before. I had tried both MIG and stick on a handful of occasions in high school shop class before really learning to weld on the school's SAE Formula Hybrid team in college doing TIG.
Starting out with MIG, I feel like the M.O. is basically pull trigger, keep tip in general vicinity of joint. I felt that TIG allowed me to better see how I was manipulating the weld pool, I could control it better due to the slower pace, and I got a better feel for amperages and "feed rates" through being able to manipulate both on the fly. I actually got halfway decent at TIG for a few years and chose that process exclusively even for personal projects, even though I had access to a MIG on campus as well.
ncjay
Dork
9/17/15 4:30 p.m.
The MIG gets used for mild steel only. TIG gets used for anything else, or anything that needs to be real pretty. I've seen some awesome MIG welds in aluminum, but it's a pain changing gas bottles and wire, etc. Hadn't really given it much thought until now, but you can weld everything with a good TIG machine, but the MIG machine is fairly limited.
You can MIG weld aluminum and stainless, it's not limited to mild steel only.
The advantage is that MIG is pretty much a "hot metal glue gun" thanks to the auto-set welders you can buy now.
Heck, even Mikey from OCC can use a mig welder.
Having never "really" welded, I thought I wanted a MIG. I went to Mezzanine's house and realized I really wanted a TIG.
The potential is there with a TIG, even if I'm not quite "there" yet.
My feelings: First a MIG. for tacking, etc. Then a TIG to make beautiful welds with less warping. Stick is valuable as a baby step towards MIG, Gas the same if TIG is the goal.
I guess the catch for Grassroots folks is tacking. Can you hold those header pieces together in the engine bay, and with TIG? Best have both.
TIG is for the race car and things in the machine shop.
MIG is for trailers and cars w/ VIN plates.
The process that's closest to TIG from a learning standpoint is gas welding. Anyone w/ tanks and a torch would do well to get a book and learn how. Every tube fuselage airplane from the beginning of flight to the 60s was most likely gas welded.
kb58
Dork
9/17/15 10:55 p.m.
TIG: artist's brush, precise, fine point, slow, clean
MIG: house painting brush, fast, not so precise, a bit messy
In reply to motomoron:
Pretty much anything that can be TIGed, can be, and historically has been, OA welded. I think the practice really only died out because TIG works out cheaper and safer to operate at any sort of production/shop scale, and probably home as well.
My feelings echo most of what's been said. One thing is that I've never gotten comfortable with the hand amperage control for TIG welders. I much prefer the foot pedal, but when you're climbing all over something, often the pedal doesn't work.
Stick welding is still very valid and used a lot, just not in applications we're likely to be using.
NOHOME
UberDork
9/18/15 5:50 a.m.
I have a MIG and a TIG. TIG used to be the only welder in the shop cause I thought it was more cooler than MIG. Once I bought the Lincoln MIG the TIG has gathered dust and I have done a lot more fabricating.
If you can only have one rig, and old cars are your game, it is possible to get by with only the MIG. It will be quite difficult to get all panels and parts clean enough to TIG. (backside of a long quarter panel seam for example, assuming you CAN get at the back) Then we can talk about out of position welding and working a foot pedal.
If you are running a shop or paying for one's time, a TIG welded quarter panel seam is going to take 3 times or more to than the MIG equivalent.
With TIG, you are constantly sharpening and changing out tungstens either because you dipped the tip or need a different diameter. This will drive you nuts when you start out.
They both weld aluminum but if doing thin sheet, the TIG is the only real option.
Don't let anyone tell you that you can't metal finish MIG welds.
TIG wont tolerate weld-thru primers. This means that lap joins or spot welded joins will be more rust prone.
Neat trick with TIG is you can do a spot weld without drilling the top panel.
TIG is kind of like the parachuting or base jumping of the welding world, very rewarding when done right, while MIG is more like skiing.
Synchrowave 300 and a Millermatic 185. Before I bought the MIG I would TIG everything. I bought the TIG machine before learning. A retired T&D welder taught me the basics, then practice, practice, practice. I bought the MIG new w/ absolutely no experience and learned on my own in my shop. Now the MIG sees 95+% of the work. E36 M3, I don't even wanna stick weld anymore. I still like to play w/ gas welding once in a while, very similar to TIG as said above.
From a learning standpoint I like to tell folks to start w/ a good MIG machine before stick. I've seen newbies get turned off by stick welding w/ the splatter, discipline and fumes. Well, I did catch my pants on fire back in the day. MIG is the Easy Button of welding, builds confidence faster w/ practice and then they're hooked.
Once hooked, TIG is a natural progression to learn if you're really into it.
WilD
HalfDork
9/18/15 8:21 a.m.
I have learned a lot from the article and this thread... thank you all.
My father was a pipefitter and was an expert stick welder as that was what you had to use out in the field. I never got very good at it. I later purchased a MIG welder and used it to fab up many of my car projects. I later purchased a TIG and now will use it 90% of the time for the type of fab projects I do.
If doing a roll cage I use MIG but will use TIG in a few spots that are hard to get to. The nature of MIG is that you are constantly adding filler when ever the trigger is pulled and getting a good weld in these tight places is difficult. The control TIG provides is what I like.
I currently own a newer Lincoln 180 Dual Voltage MIG and a Lincoln Econo TIG. Both are use on a regular basis. I bought the new MIG as I got a good deal and it's much more portable then the old MIG I had and as well as the TIG. Also it operates on 110V or 220V so I can take it to a friends house without worrying if he has 220V in his garage.
If more people could weld steel and solder tube, I think they would enjoy their hobbies more. It's really useful.
I think there are just so many mental barriers, that many people never attempt it.
A decent MIG machine with gas (I entered the fray with a 180 amp Lincoln wired to 220) let me get through a lot of the frustrating things I needed to learn. Like fit-up, clamping, burn-through, torch angles, vision and position. If I had started with TIG, I'm not sure I would have stuck with it.
OTOH, if I had started with an inexpensive flux MIG, I'm not sure -- that might have frustrated me enough to put me off.
Plus if you look around, there are some videos that will show how to make really good, good-looking MIG welds.
I encourage anybody who's thinking about taking the step into welding, to just go get that MIG w/ gas and get started.
I will add a couple of things. I got rid of foot control with my TIG and use finger control and will never go back to depending on my feet 5 feet away from my hand and the weld.
Years ago a gas lens made my TIG welds look 100% better and they are all I use.
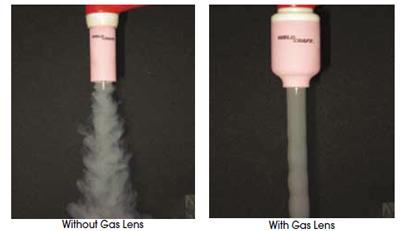
Aluminum is getting to be a toss up between the MIG with a spool gun, and TIG. It generally comes down to how much time a spend getting off the oxide and cleaning preparation. Pretty clean prepared aluminum, the spool gun gets picked most of the time. The TIG gives me cleaning and penetration knobs I don't have on my MIG.
Its puzzling but it (MIG Sgun) seems to keep the heat more consistent down the bead? That give me confidence doing fine or thin work with it. It is certainly 3X faster than TIG'ed. The spool gun "dimes" are not quite as round and there is a bit more splatter breath, but it visually passes my comparison standards.
My MIG is not pulsed, and I am looking at new machines with that that feature.
I don't agree that TIG means less warping.
This pic is typical of results I get with my MIG and spool gun on Aluminum. I use Miller.
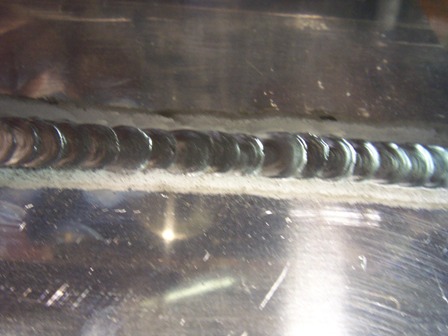
Thanks for the conversation, guys. You've added some great points and I especially like what Gasolene just said.
I want to pick up on his comment about TIG and warp--I agree completely. It a metalurgical fact that when you heat metal and it cools, it shrinks. More heat=more shrink. Apples to apples, TIG welding actually puts more heat into the base metal than MIG and therefore shrinks (more). However, it's a more malleable weld, so it's easier to get it back to its correct shape.
What happens in practice is that TIG welding tends to be more controlled in the hands of a skilled person. This person is usually better at putting the right amount of heat into the weld to make a puddle, but no more. With MIG, it's way too easy to put way too much heat in since you can't usually control the heat on the fly (except by moving the torch faster). Because of the control of the TIG, less heat=less shrink.
The easiest way to see this in action is to look at the heat-affected zone on the welds. The bigger the heat-affected zone, the more shrink (warp) you'll see, every time. Often, a good welder with TIG will have a smaller heat affected zone than an average welder with MIG. But put that same TIG person on the MIG and have it set up just right, the MIG will have a smaller heat-affected zone and less warp.
And Nohome is right, you can metal finish MIG welds. The key, just like TIG, is to have the bare minimum amount of heat to get a good weld, to try to work it as much as possible while the joint is still warm, and do what's left when it's cool. At Eclectic Motorworks, we regularly MIG dogleg and other patch panels into cars and can measure warp with a feeler gauge (.015-.020"). We could fully metal finish them if we wanted to, but at that point they can pretty much be filled with high-build primer.
It's funny, too how we've all agreed that MIG is 3X faster.
In reply to rafe_999:
Do you offer any marine grade equipment? I've been looking to outfit my canoe?
This is turning into an armada
I just got started welding. First I picked up an old stick welder. Attempted to use it for a couple small things, realized it wasn't easy to use and also didn't fit my applications well.
Now I got a Miller MIG welder, and it is so easy to use. I still have a lot of practice to do, but so far it has been incredibly easy to catch on.
I plan to get a TIG welder sometime in the near future for aluminum, but for now the MIG does just fine.
I know this is an older thread but I was happy to see it return to the top.
Has anybody tried one of the new machines from Harbor Freight yet? I have an older Lincoln SP100T MIG... but I'd love to learn to TIG for pretty stainless exhaust and aluminum bits.
TIG is the Zen of the welding world. It requires time and effort to get correct, but once done, is amazingly beautiful. I work in food processing, which means TIG almost exclusively for two very good reasons-
1) Cleanliness- it doesn’t throw sparks and slag everywhere, and the welds themselves are smooth and easy to keep clean on processing equipment.
2) Stainless steel- Stainless is where TIG absolutely shines. The degree of control you get allows a strong weld while maintaining the stainless property of the base metal; incredibly important when things are cleaned daily with harsh chemicals.
NOHOME
UltimaDork
10/26/17 12:18 p.m.
Recon1342 said:
TIG is the Zen of the welding world. It requires time and effort to get correct, but once done, is amazingly beautiful. I work in food processing, which means TIG almost exclusively for two very good reasons-
1) Cleanliness- it doesn’t throw sparks and slag everywhere, and the welds themselves are smooth and easy to keep clean on processing equipment.
2) Stainless steel- Stainless is where TIG absolutely shines. The degree of control you get allows a strong weld while maintaining the stainless property of the base metal; incredibly important when things are cleaned daily with harsh chemicals.
TIG is as clean as you make it. Much of the beautiful smoke-and-spatter free process is bbecause you cleaned the weldment to surgical clean standards before you picked up the torch.
If you really want to shine with stainless, you need to learn about the joys of back-gassing the weld. This is where both the front and rear of the seam have shielding gas delivered to the puddle.
Nowadays, my recommendation to the aspiring motorsports/DIY weldor is to watch Craig's list and ebay for entry level > > NAME BRAND < < MIG machines where the seller is stepping up to a larger or one with more features.
Please refrain from falling into the flux-core trap; even an experienced weldor can't do much better than make bird-poop looking welds. A setup with a regulator and shielding gas is far and away better, and the when set appropriately, the gas lasts a long time (and I'm using smallish 40CF cylinders).
Personally, all my welding machines are BLUE (including the Snap-On/Lenco Spot-II that used to be red is now also powder-coated in Miller colors). But there are good red (Lincoln) and yellow (ESAB) units too. I was actually impressed with a Century (Sam's Club) welder I used for a while too.
A reasonable analogy of MIG vs TIG, is much like the (getting to be...) age-old argument on the S-52 engine versus the S-54**. Both are great I-6 engines, but to be truly happy, you need__at least__one of each!
I am happy.
**However, you'll never hear an S-54 owner belittle the S-52 by saying "it's got all its power down low..." ;)