oldtin
UberDork
9/1/15 11:52 a.m.
I need the aluminum piece below - triumph tr4 fan eliminator (takes about 8lbs of steel off the nose of the crank.

but not the $73 price tag.
Round bar in the right diameter (3.5") - not finding any pieces under about 6" long. Don't have a big lathe, so what about cutting out a 3 3/4" piece of flat plate with a hole saw? Other ideas? Of course cost of plate & hole saw and bolts is around $50. Other ideas? Anyone have a scrap 3.5" x .5 aluminum disk laying around?
Cut plate with jigsaw?
I think you should be able to make this work with simple tools. It seems to be a pretty loose tolerance part.
Balance will matter to some extent, that thing is bolted to the front of your crank.
Does it have to be metal? It would be easy to make out of UHMW plastic. Heck, you could probably get it made for you for about $40 at your local plastic shop. I don't know what's bolted to what under there.
Rough cut plate to generally round, but bigger od. Put bolt and nut through the center. Mount in drill press and turn down to final od with files.
oldtin
UberDork
9/1/15 12:15 p.m.
The stock pulley consists of a two-piece pulley, a long steel fan extension and my long crank bolt has a funky shoulder to fit the fan extension and a profiled/notched head for the hand-crank starter. additionally, a steel fan is bolted to the end of the snout. The replacement material needs to be tough enough to hold the pulley together around 7,000 rpm. Inside of the pulley is notched for a woodruff key on the crank nose.
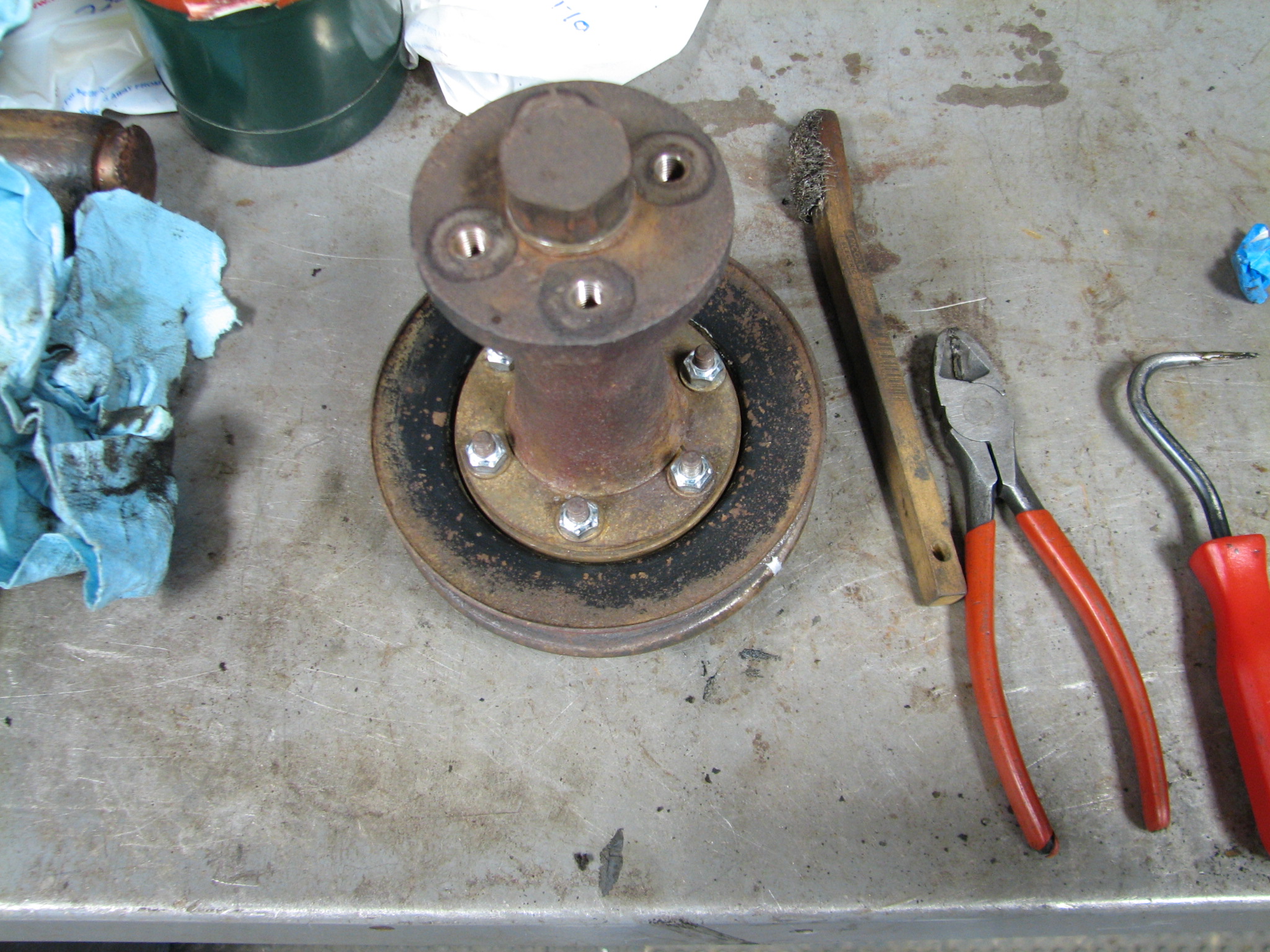
oldtin
UberDork
9/1/15 12:19 p.m.
In reply to Dusterbd13:
That's sort of what I'm thinking. Finished diameter is about 3.5" Using a 3 3/4 hole saw would get me pretty close.
T.J.
UltimaDork
9/1/15 12:31 p.m.
I like a project, but unless you have a chunk of aluminum sitting around already, I'd be tempted to just spend the $37 and buy the already made part and support Patton Machine or whomever you are buying it from.
What is teh bolt pattern? is it possible to get a wheel spacer that would work?
What about cutting the stock piece down?
That's what I'm thinking. Cut the stock one down and get a welder.
I also agree that it's worth rewarding someone else for their time and expertise, especially on a 7000 rpm part.
Opti
HalfDork
9/1/15 1:05 p.m.
Obvious choice is cut the stock fan extension
oldtin
UberDork
9/1/15 1:10 p.m.
Not a fan of cutting the stock bit. Cast iron and the center is hollow, so it would still need the center welded and drilled.
Get that pitch wrong and kiss that belt life bye-bye
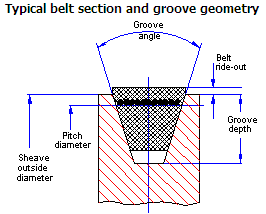
What about modifying something like this?

I've got one that the keyway failed on that's been riding around in the back of my truck for a few years waiting on me to recycle some aluminum. Yours if you want it.
EDIT: outer dia is roughly 4.5, 3.5 inside the "bell"? open area inside the pulley.
T.J. wrote:
I like a project, but unless you have a chunk of aluminum sitting around already, I'd be tempted to just spend the $73 and buy the already made part and support Patton Machine or whomever you are buying it from.
Keith Tanner wrote:
I also agree that it's worth rewarding someone else for their time and expertise, especially on a 7000 rpm part.
I'm guessing you're building an engine, yes? You're probably not doing it on the cheap, no?
Keith Tanner wrote:
Balance will matter to some extent, that thing is bolted to the front of your crank.
Like TJ, I'm all for DIY, but why risk your investment - both time and money - with something you've hacked together, when someone else has already created a reasonably priced solution?
If I understand this correctly, why not just use a shorter center bolt, eliminate the disk, and use 6 shorter bolts with washers to hold the pulley together? Surely ARP makes something strong enough. Or find a crank pulley with the same ID (inside dimension) key dimension and OD (outside dimension).
Cut to Length Aluminum Disks
2021 in 3.75 x 1/2" is $14.
$73 doesn't sound all that bad,especially if you wind up needing to DIY it more than once to get it right.
If you had you already had a lathe and chunks of scrap aluminum sitting around, the calculation could work the other way, but it sounds like you don't.
For reference, I paid a good bit more than that to have a steel flywheel machined down to a lighter weight and rebalanced, fairly simple machine work.
What does machine work cost to rework the bottom end once the out of round home made part beats the bearings flat? Spinny bits are where I pay someone else.
oldtin
UberDork
9/2/15 12:29 a.m.
Where's your GRM spirit?
. Keep in mind the home brew part is about 8oz and 3.5" in diameter replacing about 6lbs of metal that's about 12" in diameter. When a piston departs from the block it will probably be from something else imho
What's your time worth?
It's been 12 hours just thinking about how to make the damn thing.
Hit up the local machinist/welding and machine shop. That's small cheese
Dietcoke wrote:
Hit up the local machinist/welding and machine shop. That's small cheese
Bring that picture to a machine shop with a case of beer (I don't drink but this has worked for me in the past).
That part needs to be balanced. See what a machine shop would charge you to make something similar on a lathe...it might be more though.