Sorry, that should be Nickel. That's two in two days. I'm going to have to work on my proofreading skills.
The one thing I didn't like about the restoration I did on the 9" South Bend lathe was painting the levers and wheels. I used paint because I couldn't get the cast to shine the way I wanted.

Since I'm doing the 16" SB lathe, I'm thinking about plating the parts. It should be more durable and look better than paint.
Do any of you gents have any experience with nickel plating. Any kits you would recommend?
Arrow plating in ft worth Texas does mail order plating really reasonably. Its the outfit cousin Eddie reccomend.
There was a guy here in town doing stuff with the Eastwood kit. He never got great results.
I know that a lot of the antique outboard guys are constantly trying to get their pre-war parts nickel plated. I'll see what they recommend and get back to you on that.
We use a plating company south of Charlotte for industrial nickle plating parts for work. I can get the contact info, if you are interested. I am planning to try and have them do the bumpers for my widened Spitfire.
What is recommended for preparing parts to send out for plating? Vibratory tumbler to clean them and strip rust?
I know plating reacts better to smooth surfaces than rough ones from my experience.
Arrow told me to degrease, strip paint, and send. Dunno about others.
And im getting black zinc. Other finishes may be different
I use a local company. It is $65 per batch. Not sure of the poundage but a ziploc sandwich baggie is one batch as is two 5 gallon buckets full of metal.
Prep is key. They do not want to work with grubby old stuff. Degrease, media blast or vibratory tumble and or wire wheel and probably another trip through the degreaser. The shinier your parts are when you send them the shinier they will be when they return. Sandblasted parts will have a satin finish.
Every fastener on our restorations is stripped and replated. Customers choice of white zinc (blueish tint), yellow zinc, black zinc or nickel. Nickel being the most popular. Turnaround time of 5 days.
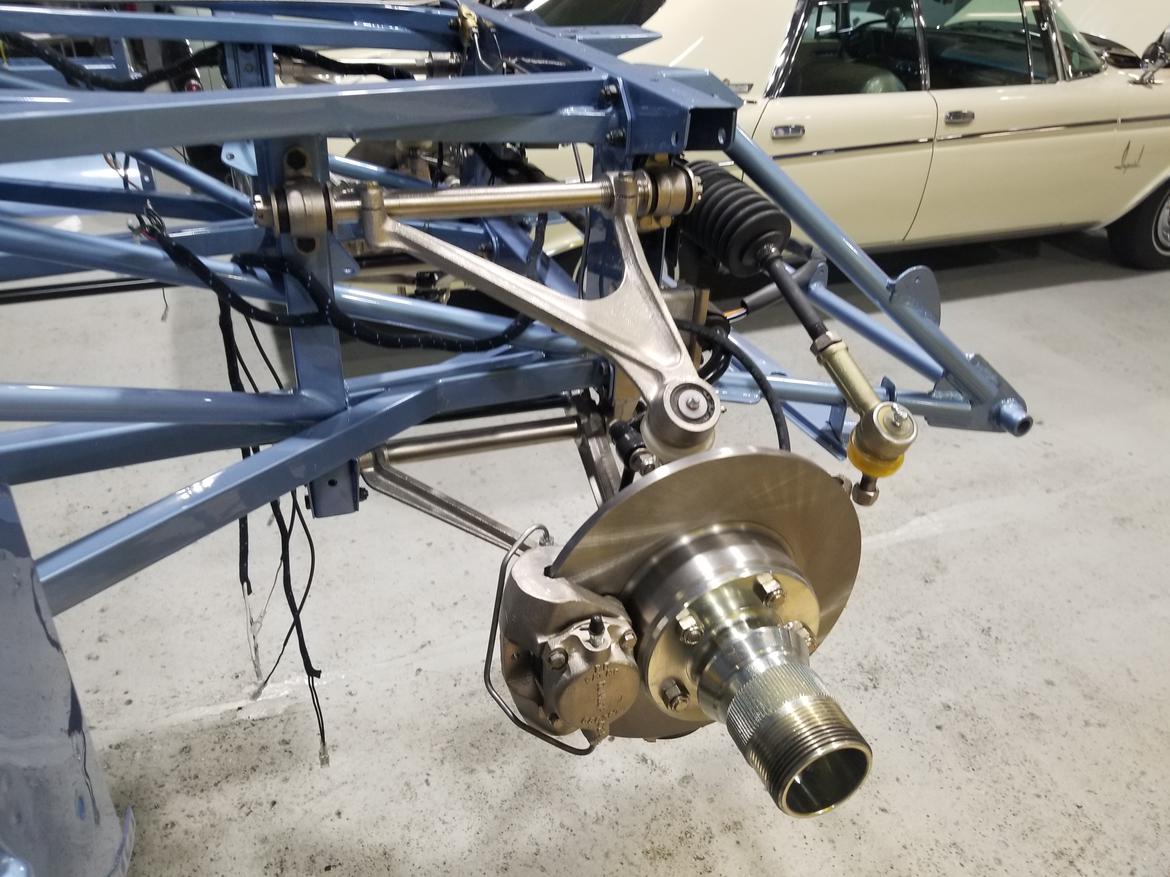
Front corner of an e type next to me showing off its nickel plated arms and calipers
And I guess it is time to clean my camera lens on the phone 
If you are interested in the process of nickel plating, here is a good read. I'm going to have to try this at home.
NICKEL PLATING HANDBOOK
Caswell is kinda the gold standard for home electroplating kits. I have the zinc plating setup and have it working quite well these days.
The power supply is the most expensive part. A battery charger won't work, you need very fine control of amperage to match the surface area being plated
https://www.caswellplating.com/surface.html
I bought our power supply off ebay. It is variable 0-20 volts and up to 30 amps. I have the caswell electrolyte solution in 5 gallon plastic buckets. They manage to get polluted once a year and need to be changed out.
In reply to Trent (Generally supportive dude) :
I have a 1-60 volt 0-30 amp power supply at home already. I basically have everything except the anodes and the solutions and those are pretty cheap.
This guy was bought for reviving Segway batteries.

Awesome!
The other caveat is the electrolyte solution is acidic. Even with lids on the buckets, steel items within a 5 foot radius will start to rust. Make sure you have a place to store them away from your tools and toys.
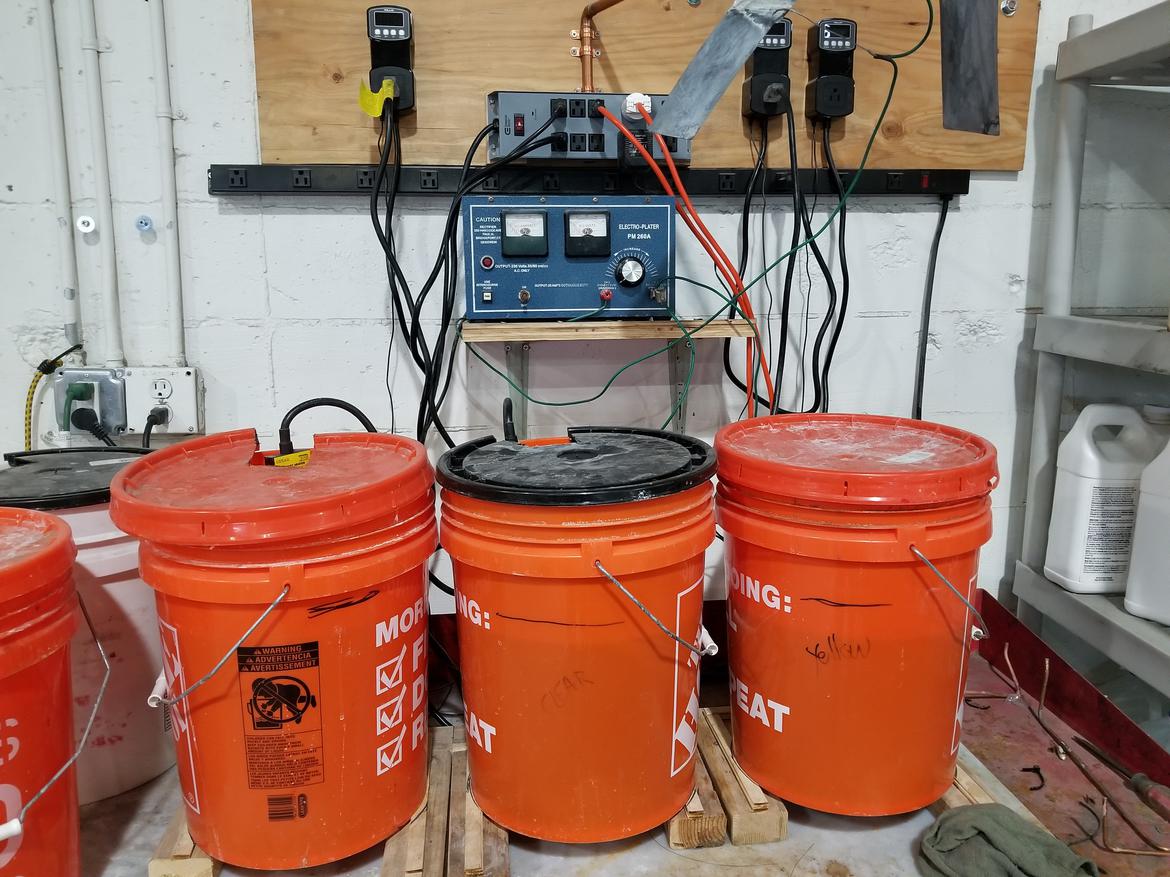
My setup. Bucket of the acid pickle, degreaser, distilled rinse water and the electrolyte. Anode plates are hanging. The plating solution needs to be around 105 degrees so there are bucket heaters on controllers.
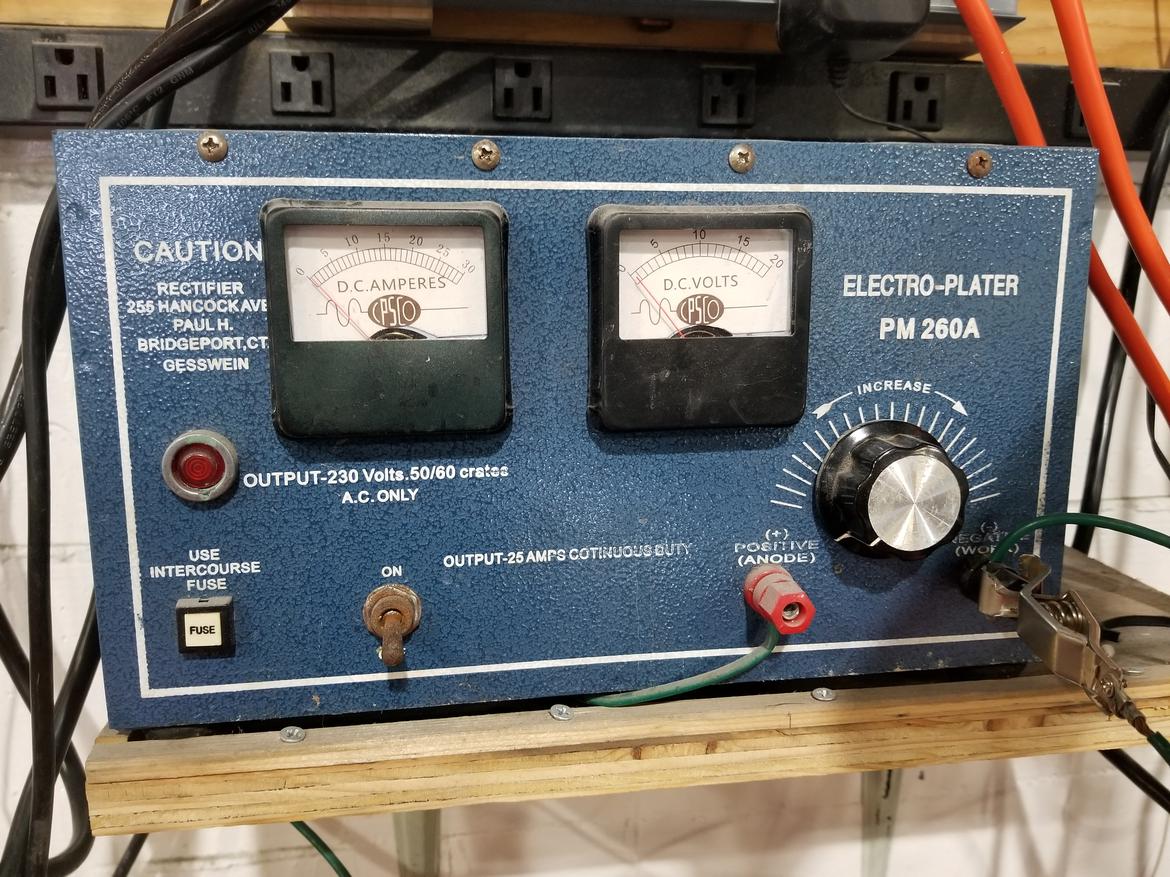
Cheap import power supply
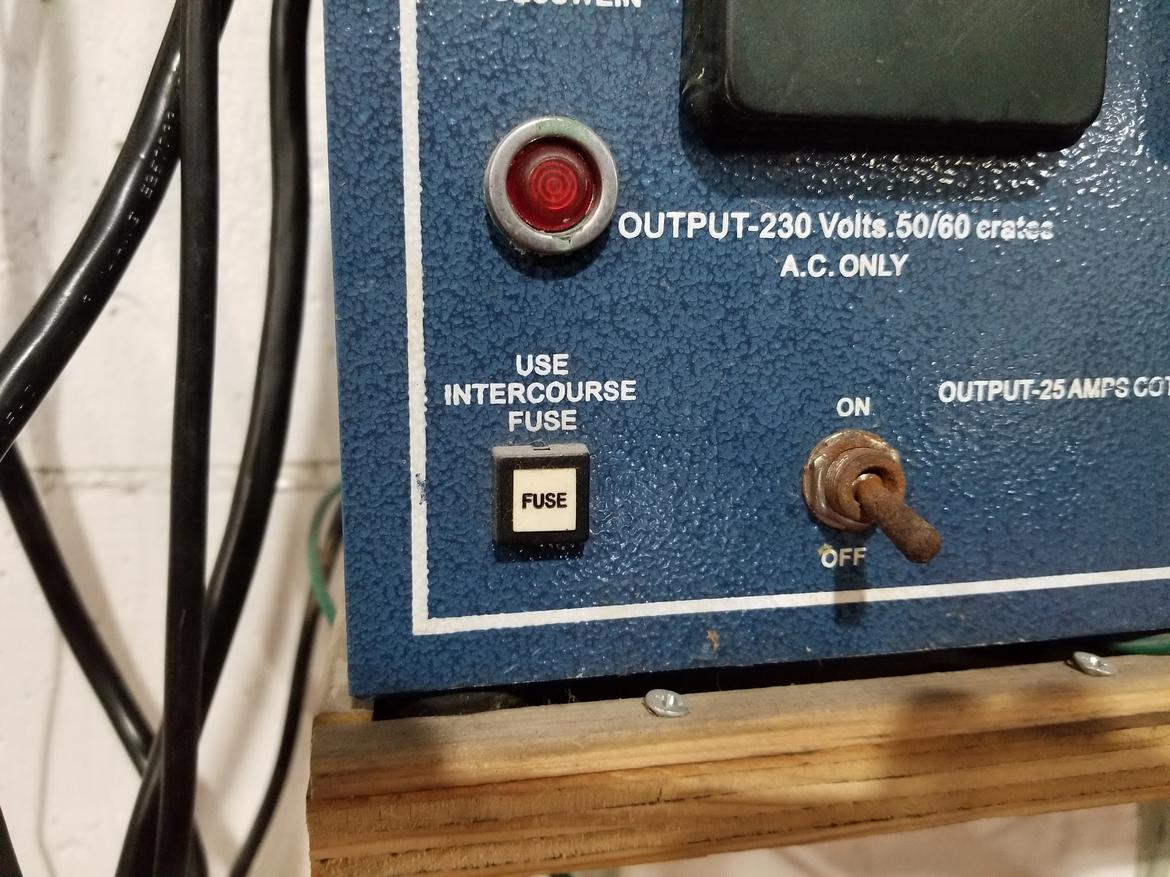
Rust on the chromed switch from acid vapor exposure and a curiously labeled fuse
Jerry
UberDork
5/13/20 11:46 a.m.
I can measure the plating thickness here at work for you, in the millionths of an inch. Or microns if you want to go metric like 98% of the world. XRay Fluorescence baby, and as boring as it sounds. Although my boss has learned to do some zinc, copper, and nickel plating to make our own reference material.
Mr_Asa
Dork
5/13/20 11:48 a.m.
Trent (Generally supportive dude) said:
Caswell is kinda the gold standard for home electroplating kits. I have the zinc plating setup and have it working quite well these days.
The power supply is the most expensive part. A battery charger won't work, you need very fine control of amperage to match the surface area being plated
https://www.caswellplating.com/surface.html
I bought our power supply off ebay. It is variable 0-20 volts and up to 30 amps. I have the caswell electrolyte solution in 5 gallon plastic buckets. They manage to get polluted once a year and need to be changed out.
Yup. Old boat guys like Caswell for their kits at home.
Caswell needs to hire someone to straighten out their website. It's a hot mess.
I've about decided to pass on the kit. There is enough info out there to very easily and cheaply make the solution for nickel. The power supply I already have. The anodes are on their way from Amazon. I should have something up and running in the next week or so. I'll share my results.
Odd question- can Nickel plating replace old chromed pieces, like on the old 50s winga-dinga machines? I've seen the cost of chroming things, and good GOD I don't want that.
In reply to GIRTHQUAKE :
It depends on what look you're going for. Chrome? No, probably not. Chrome has more blue in it for some reason.
Shiny metal? sure, it might do the job
In reply to Mr_Asa :
Yeah, like as a good replacement/alternative kind of thing. I know Nickel has a warmer "sheen" than Chrome but I'm trying to figure out if it's worth it to strip chrome for nickel or to try and re-chrome something.
In reply to GIRTHQUAKE :
IIRC chrome is hella expensive because the chemicals are an EPA nightmare to deal with. Nickel isn't going to be as bright and shiny as chrome.
Chrome is expensive not only because of the regulations on the materials, but because there is so much manual labor in it. 90% of the cost of getting something chromed happens before the chrome. The piece has to be smoothed out by hand then a layer of copper is plated on top of that. The copper is the primer and the filler in the chroming process. The copper layer is smoothed out and likely replated with another copper layer until the part is smooth enough for the final steps. The last layer before the chrome is nickel.
"Take all the labor of a show winning paint job and make it even more difficult because all your materials are metals" level of labor. Chrome shows off imperfections like nothing else.
Nickel plating like we are talking about here will not look like chrome. With a lot of prep it can look like a pistol. With the labor intensive copper process it will be the "warm chrome look" everyone talks about
In reply to CrustyRedXpress (Forum Supporter) :
We fang it.