I am working on the mounts for my challenge car, trying to learn about getting the transmission in the right spot in regards to the rear diff.
challenge car is IRS (Mercedes 190e), I am reading about pinion offset and getting all confused.
Basically can I have the transmission and the rear differential not totally in a straight line? Or will this cause bad vibes?
The transmission is a slip yoke if that matters at all.
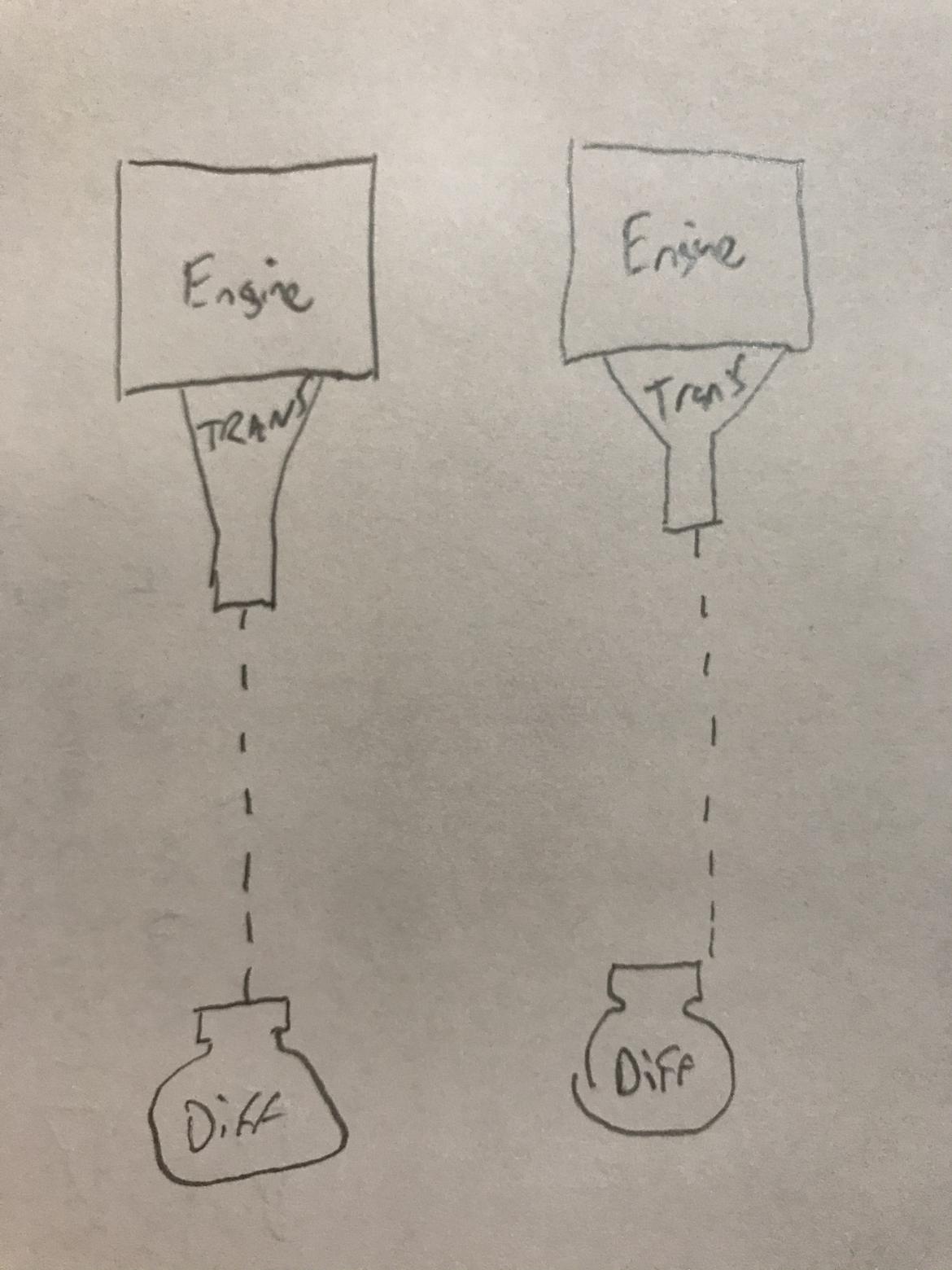
That is what I mean by not a straight line, I read something about creating vibrations, then something else where they should be offset to lube the needle bearings or something like that
As long as the angle on both ends of the drive shaft is the same you should be fine.
Ideally any angle should be less than 3 degrees or u joint life will be shortened.
Basically angle 1 needs to be equal to angle 2.

In reply to Toyman01 (Moderately Supportive Dude) :
Thanks I need to study up on it more i guess
So it is more up/down issue than a left right issue?
In reply to Somebeach (Forum Supporter) :
Doesn't matter if it's up and down or left and right or even any combination of the two, as long as the transmission output shaft and the differential input shaft are parallel.
Edited for clarity.
Toyman01 (Moderately Supportive Dude) said:
Basically angle 1 needs to be equal to angle 2.

Hmmmmm..........I'm going to have a problem with this in my Challenge Corolla, I think. Currently the engine sits in the chassis with a 3 degree slope down toward the rear. That puts the transmission yoke about 3 inches below the rear axle pinion. I'll be exceeding the 3 degree U-joint angle unless I raise the rear of the transmission up, at least to parallel to the road. The devil is always in the details.
In reply to DeadSkunk (Warren) :
I wouldn't worry too much about it in a Challenge car. 3 degrees is for optimal u joint life. You need to survive two days of drag passes and autocross runs. If it eats a u joint every 5000 miles it doesn't really matter. My Samurai eats a rear joint every year or two but I don't drive it enough to care.
The other option is a double cardan joint on one end. They will handle some pretty raunchy angles without vibration.

The driveshaft in the B210 was less than ideal so I used CV joints on it.
Edit to say: You don't want extreme angles when you dump the clutch for a drag pass. It will pop a joint. I also wouldn't use extreme angles in a track car. I would also consider a driveshaft hoop if the front joint is close to your legs or seat. I have seen driveshafts come through the floorboard of a track car with enough force to fold an aluminum race seat and trap the driver. Better safe than sorry.
In reply to Toyman01 (Moderately Supportive Dude) :
I've got a safety loop already and it would be the drags that concern me about too much U-joint angle. Putting the crankshaft center line level would make it all close to a straight shot. Rear is four linked with Heim joints, so the pinion angle shouldn't change a lot from static position, just the amount induced from any squat at launch. I just hadn't given any thought at all to pinion angles before this thread, I was focused on a low center of gravity and used the standard 3 degree crank slope, although Corvettes apparently install the engines level.
Toyman01 (Moderately Supportive Dude) said:
The other option is a double cardan joint on one end. They will handle some pretty raunchy angles without vibration.

Slight derailment based on that drawing. I understand how the double cardan fixes the vibration issue on that driveshaft, but what about the rear u-joint? Aren't you supposed to run a u-joint with some angle so it spins the caps and lubricates properly?
In reply to buzzboy :
From my reading, that's the old school of thought. Done to keep the grease in the joint happy. Modern lubes have apparently eliminated that necessity.
Toyman01 (Moderately Supportive Dude) said:
In reply to Somebeach (Forum Supporter) :
Doesn't matter if it's up and down or left and right or even any combination of the two, as long as the transmission output shaft and the differential input shaft are parallel.
Edited for clarity.
Correct. It doesn't matter what plane it's on - up down/left right. As long as the output of the transmission and the pinion yoke are parallel, that's what matters. Care should be taken with measurements. You don't want to go more than about 4 degrees or you'll get vibes and put extra wear on the U-joints.
Toyman01 (Moderately Supportive Dude) said:
In reply to buzzboy :
From my reading, that's the old school of thought. Done to keep the grease in the joint happy. Modern lubes have apparently eliminated that necessity.
I like to keep at least 1 degree in it, but there is an emerging theory that things inside those joints are pretty violent. We think of them as this smooth bearing that only spins a couple degrees, but in reality things are pretty violent in there when it's spinning 3000 rpms.
In a live axle, you also have constant suspension articulation to move things around. I would also expect enough chassis/bushing flex in an IRS to keep things moving from time to time.
Thanks for all the great info. I am understanding better now.
Is there a good way to measure for this when you don't have a drive shaft yet?
I have one of those magnet angle finders. But I am not sure how to come up with of it is parallel or not.
If they are the same numbers, they are parallel.
You could run a length of masking tape from trans to pinion to estimate operating angle (measure angle of "driveshaft" with angle of "driveline component".
Once I measure the angles and make sure they're kosher, I just measure between the trans and pinion. Then measure floor to output and floor to pinion, subtract to find the difference. That gets you two sides of the triangle which is all you need. It won't be perfect, but close enough for ballpark which is all you need.
Soh Cah Toa for the angles. Or cheat and use a triangle calculator app.
In reply to Curtis73 (Forum Supporter) :
Thanks for all the help I went out with my angle finder and this is what I can up with. Seems ok right?
rear diff
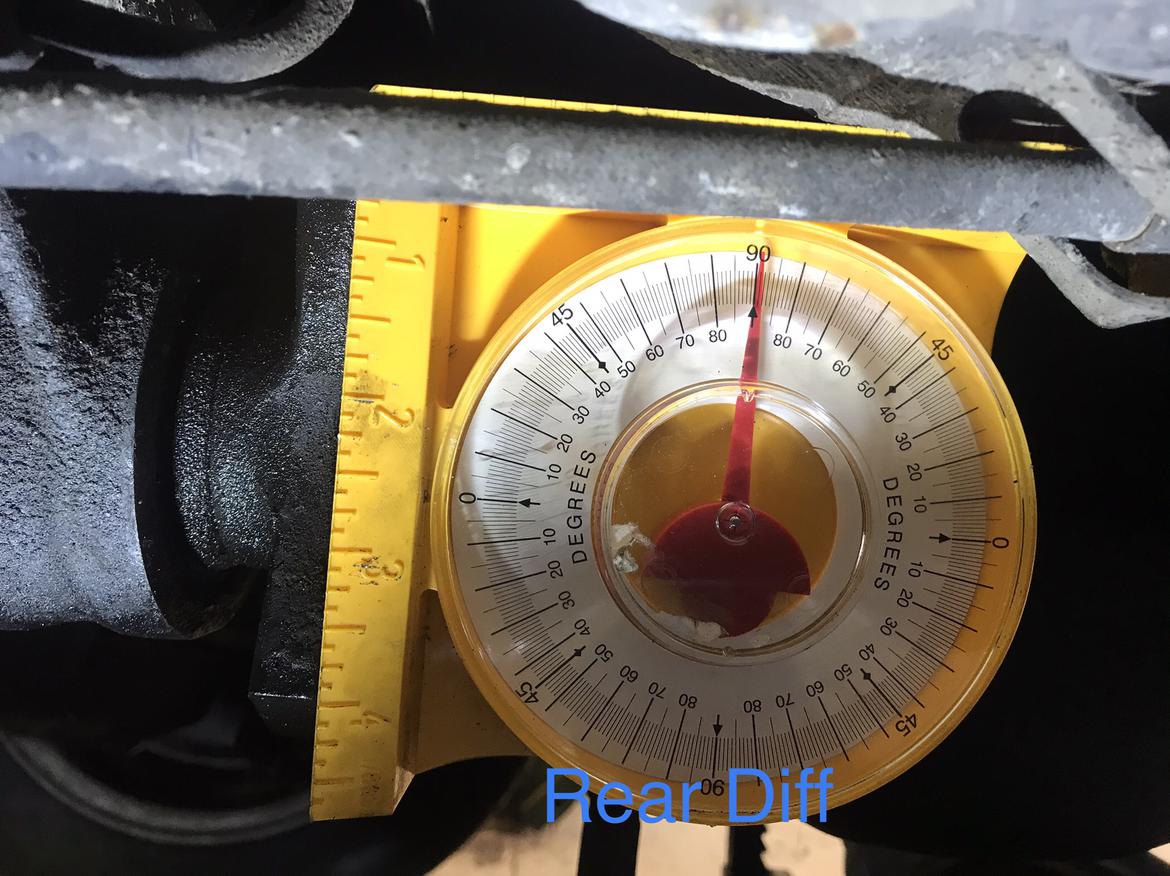
trans out put shaft
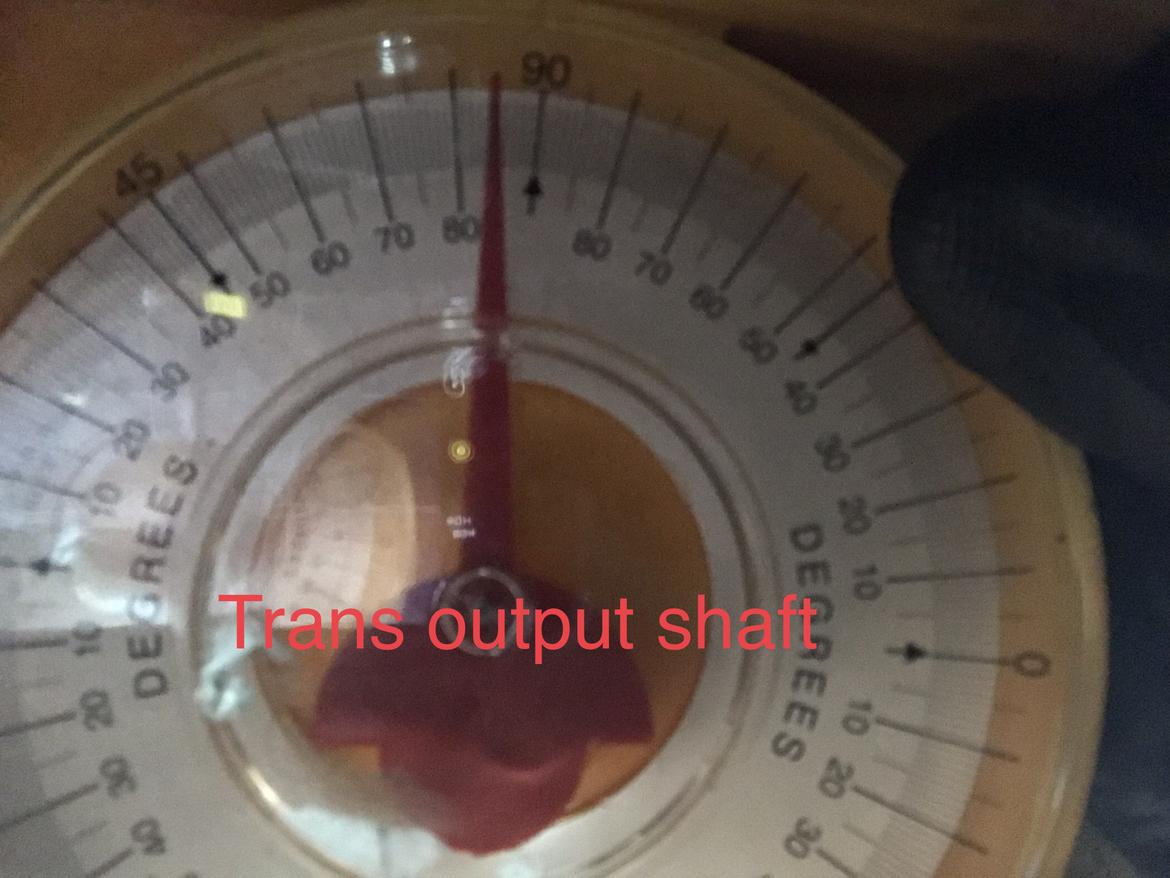
thanks for everyone's help.
You can go to the Spicer website and bone up. When you have off set plus slope they are two different calculations.
In reply to Toyman01 (Moderately Supportive Dude) :
I had a vehicle that consistently seems to prove this false. Pretty much a straight shot at ride height, and would consistently eat the joints. Upon inspection, they would have sharply defined grooves worn in matching the location of each roller element, specifically on the drive side of the cross shaft. I never really got around to fixing it and just replaced the joint every year or so.
Somebeach (Forum Supporter) said:
Thanks for all the help I went out with my angle finder and this is what I can up with. Seems ok right?
So the pinion is pointing "up" at 1°, and the trans is pointing "down" at about 5°?
Are you on leaf springs?
In reply to SkinnyG (Forum Supporter) :
Pinion up at 1degree, and the trans down about 4. Is how I was reading it. It was kinda hard to get a picture in the tunnel.
It is a independent rear suspension, with coil springs.
How long will the driveshaft be? (ballpark)
You'll need to shim up the trans and/or shim up the rear diff so that they match and are parallel/opposite. The one you move will depend on the resulting angle of the driveshaft. If it's a short driveshaft and the diff sits 5" lower than the trans, then shimming up the trans will probably take you outside the comfy angle at the u-joints.
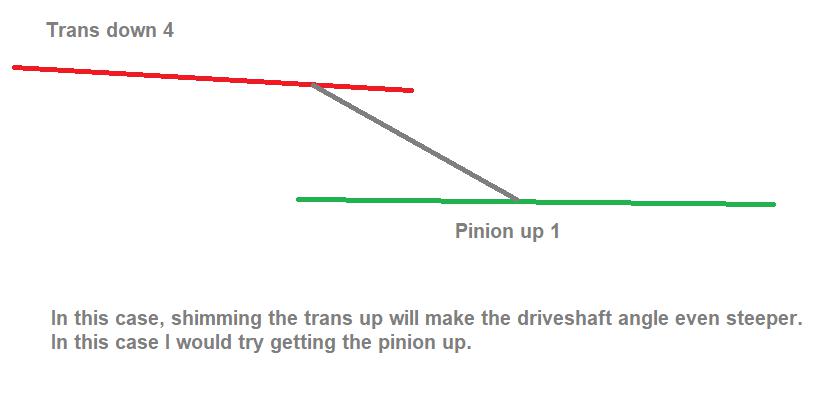
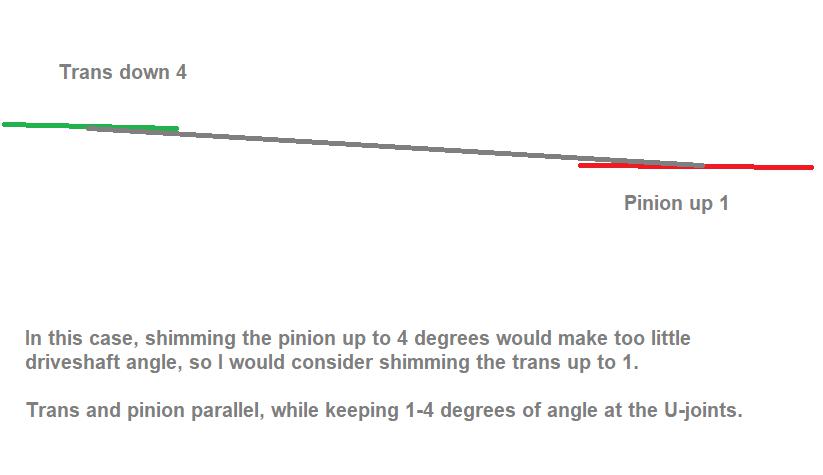
In reply to Curtis73 (Forum Supporter) :
Drive shaft total distance will be about 53".
Thanks for explaining that to me.
I was thinking that the angles of the trans and diff just needed to be with in 2-5 degrees of each other, but really these need to be equal (parallel) and then the drop if any from trans to the diff will create the angles in the u joints?
Exactly. Trans and pinion need to make parallel lines, so the same angle down at the trans as you have up on the pinion. If the trans points down at 4 degrees and the pinion points 1 up, you're off by 3 degrees.
That's where the heights come into play. If they are vastly different heights and a short driveshaft (like in a lifted jeep) the U-joint angles would be severe, so you would likely have to do a little of both to lessen the U joint angle. In something like a Cadillac where the pinion is about the same height as the trans and you have a long driveshaft, it's a little easier.
Let me know the heights of each from the floor - floor to output shaft and floor to pinion shaft and I'll use that and a little math to get you close.
In reply to Curtis73 (Forum Supporter) :
Thanks. I was going to get these measurements then I realized is the car supposed to be on the ground for all these measurements? I was thinking maybe because of being IRS it didn't matter,but does it?