I'm going to have a car up in the air for a while, and would rather have it higher up that jackstands can safely place it, not to mention I'd like to have the suspension loaded at times.
I am thinking of building some modular wheel cribbing, so I can go with more than one height as needed. I thought about buying the race ramps set as they are nice, but that's a ton of money for something that will spend most of its time piled in a corner. For about $125 in materials, here's what I've come up with. I'm going to use 4x4 lumber longitudinally, and 2x4s as cross pieces. For the top piece, I'll use 2x6s so their will be very little gap in the center for the wheel/tire. I'll use the 2x4 cross pieces to lock each layer to the next (they could slide sideways, but I kind of doubt it). Does this look strong and safe enough for pretty much anything 2 tons and under?
Quick drawing, sorry for the crudeness:
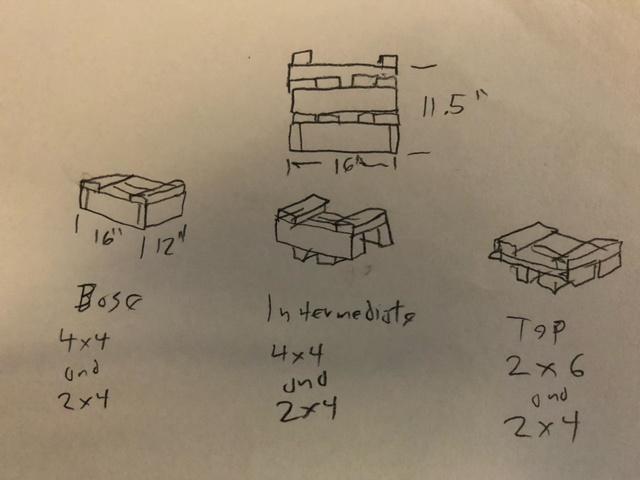
I figure if I want a lower lift, I can skip the intermediate piece. If I want a higher lift, I can build another set of intermediate pieces. Another advantage of going modular is being able to reset how much the jack is lifting the car.
I approve. I did similar but not modular. And I have all-thread in the corners. My only comment about yours is the base. If you have them on edge just figure out a way to ensure the corners don't blow out. Maybe use some hurricane brackets?
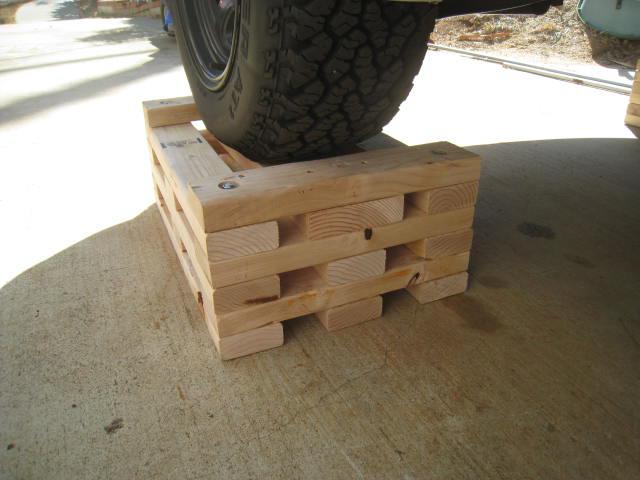
In reply to Sparkydog :
I dont think they are "on edge", they are 4x4s drawn disproportionally.
In reply to Vajingo :
Overkill. I didn't want future me crushed to death if the wood dried out, then split, then the deck screws loosened up, then I decided to use them for something sketchy and they got a side load somehow and wanted to card deck on me.
I dont k ow whether using 4x4s is the right move. Less pieces but they will be heavier, I am torn.
In reply to Slippery :
2x are cheaper to replace (assuming the cost of lumber ends up surpassing gold)
I think you'd find 4X 4's are too thick. Each time you want to lift one end of the vehicle to install crib sections you may have to allow for full droop of the wheels PLUS the thickness of the crib. Also, if you're using a typical floor jack the roll required to raise the vehicle high enough for 4 X 4 sections will come into play.
I use wheel cribs a lot, and for many other tasks as well. Here's a link to a thread explaining how I make them, just scroll down. https://grassrootsmotorsports.com/forum/grm/married-do-not-try-this/27721/page9/
By using cribs made with 2 X 4's you don't have to lift the vehicle as much each time you go up a crib. This keeps the roll to a minimum as a floor jack swings through it's arch. When you're first getting the vehicle up in the air a few cribs it doesn't matter but if you try to raise the car a lot for each crib if say using 4 X 4 cribs it gets sketchy when one end of the car is already on cribs.
In reply to NOT A TA :
Do you end up having any concerns about yours sliding forward/backward on each other, or do you do anything to temporarily keep them locked together? I'm a little afraid of them sliding off if the vehicle wants to roll.
The 4x4s are probably overkill, but with lumber prices being what they are right now, they provide more lift per dollar than 2x4s. Heck, I was checking prices last night, and pressure treated was pretty close in price to normal boards. If I stick with the interlocking design, maybe I'll still make the bases 4x4 and intermediate pieces 2x4.
I found two of these at a shop going out of business sale. I made two more
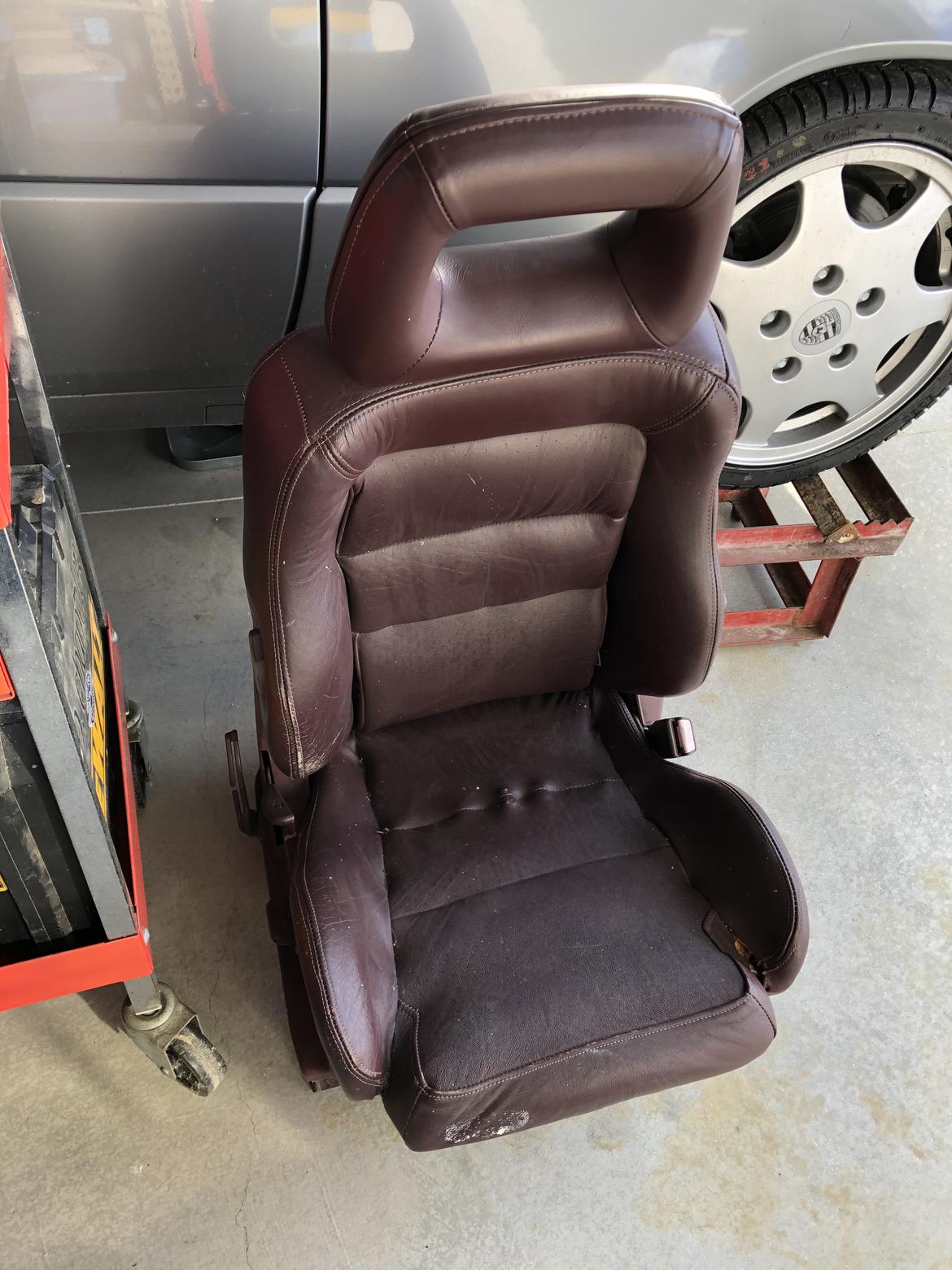
Sorry for the crap pic but the bar can sit at an of the notches raising or lowering the height.
On mine I plan on making the tops totally flat. Then I can do wheel alignments whilst aerial
In reply to chandler :
Considering what the price of wood has been driven up to, I think those are a viable option. Can you get us a better picture, so we can flagrantly copy it?
03Panther said:
In reply to chandler :
Considering what the price of wood has been driven up to, I think those are a viable option. Can you get us a better picture, so we can flagrantly copy it?
As requested
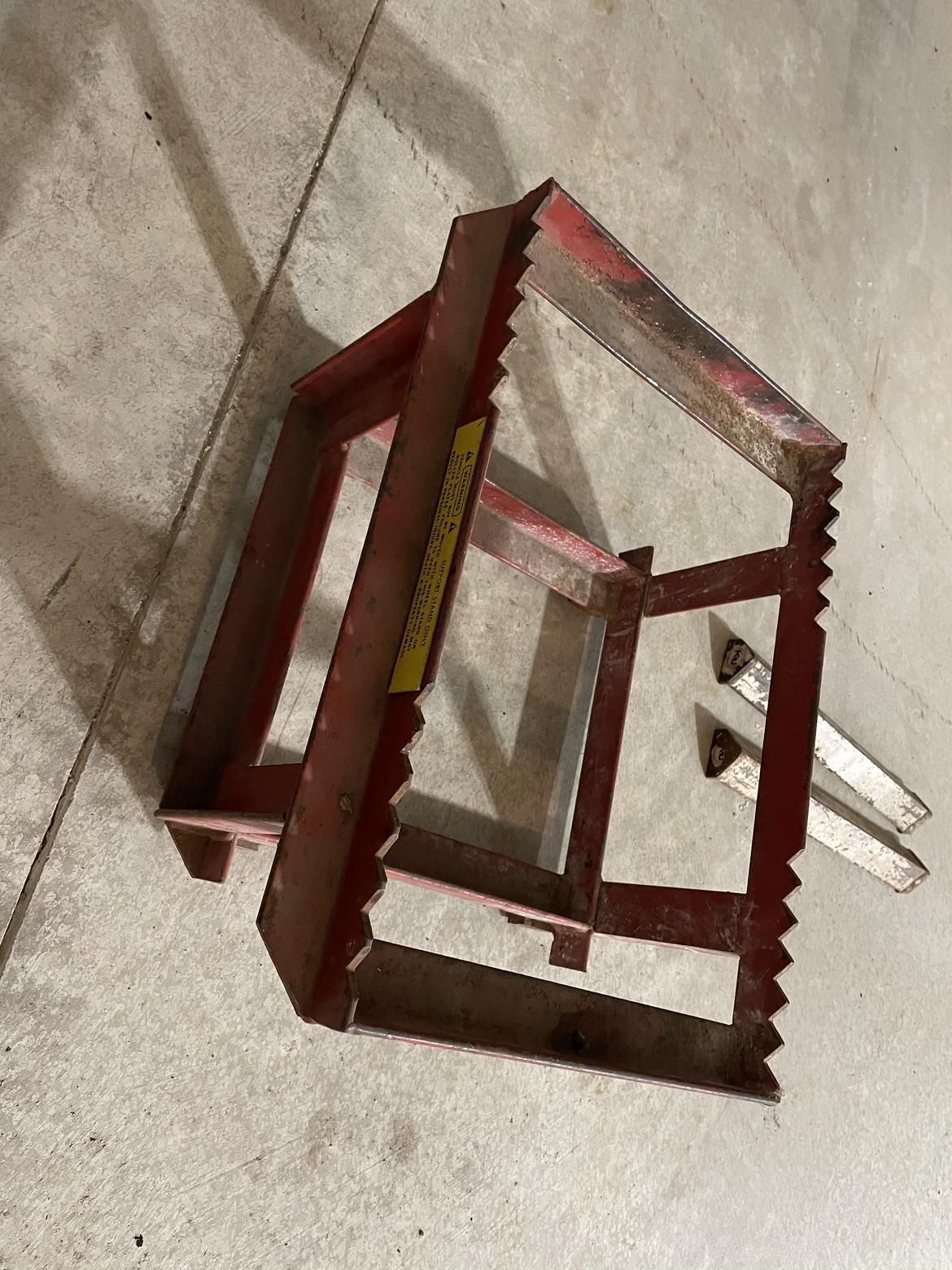
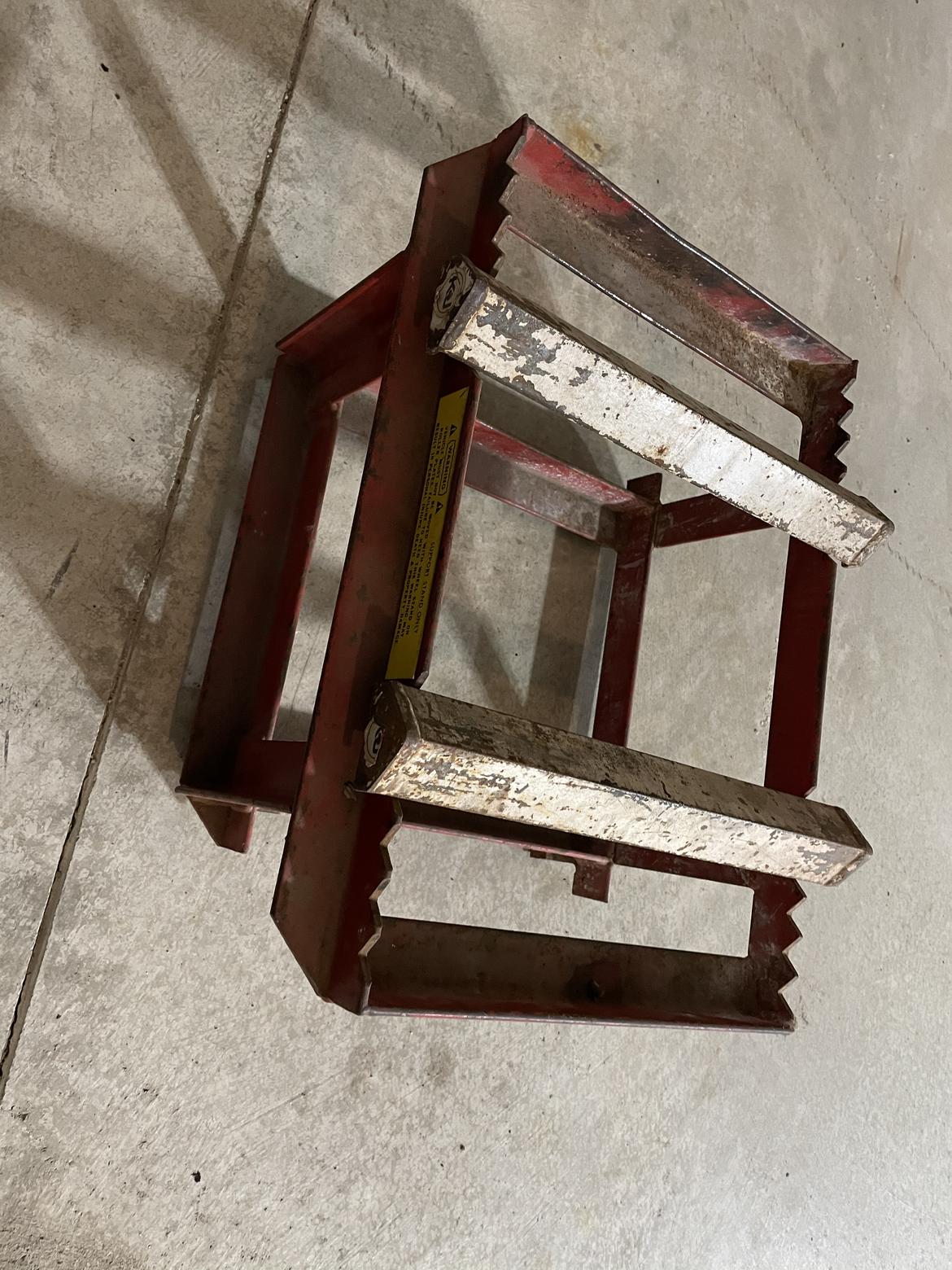
they have 1x1 capped feet so they sit pretty evenly all of the time as well.
chandler said:
03Panther said:
In reply to chandler :
Considering what the price of wood has been driven up to, I think those are a viable option. Can you get us a better picture, so we can flagrantly copy it?
As requested
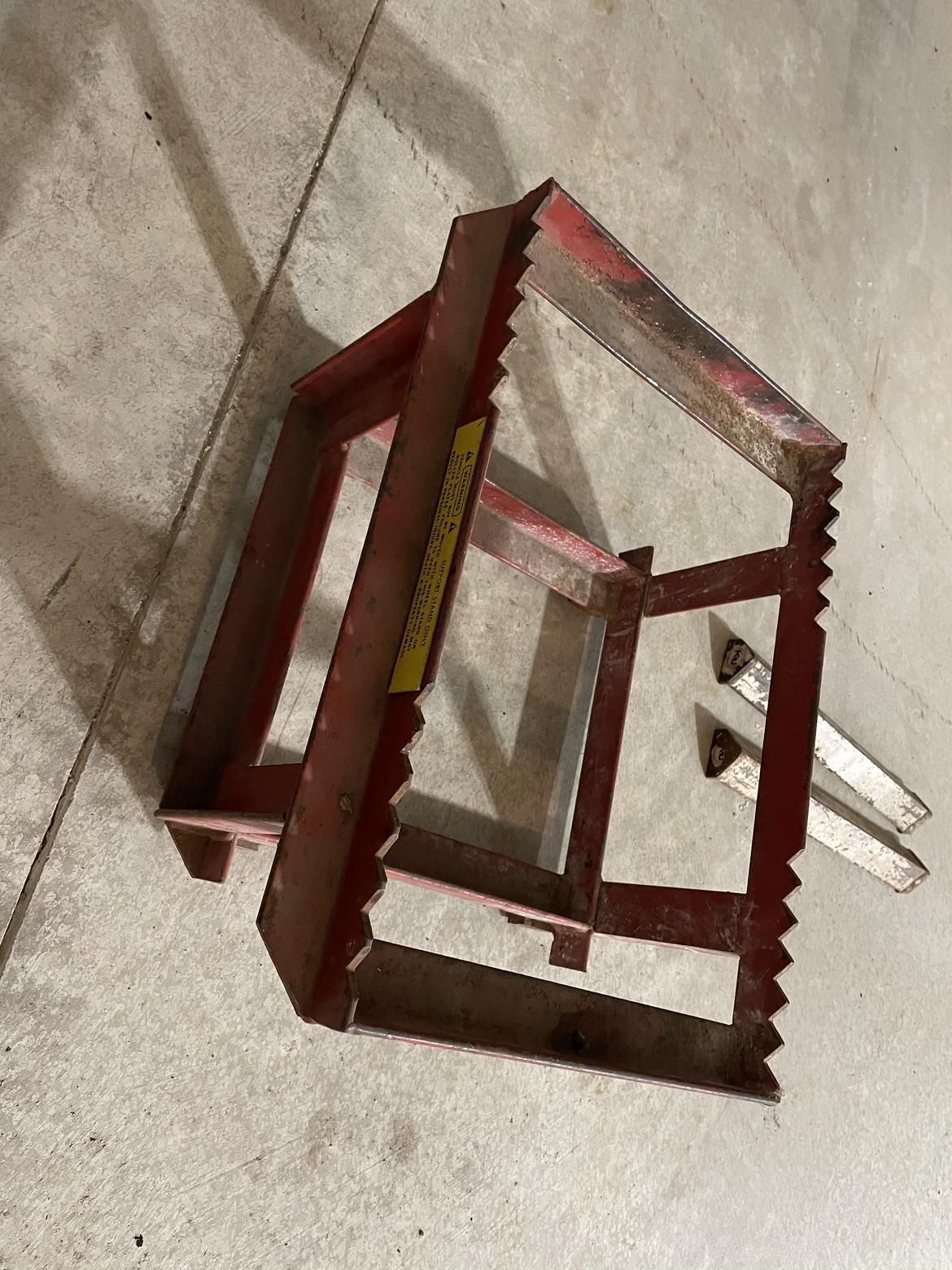
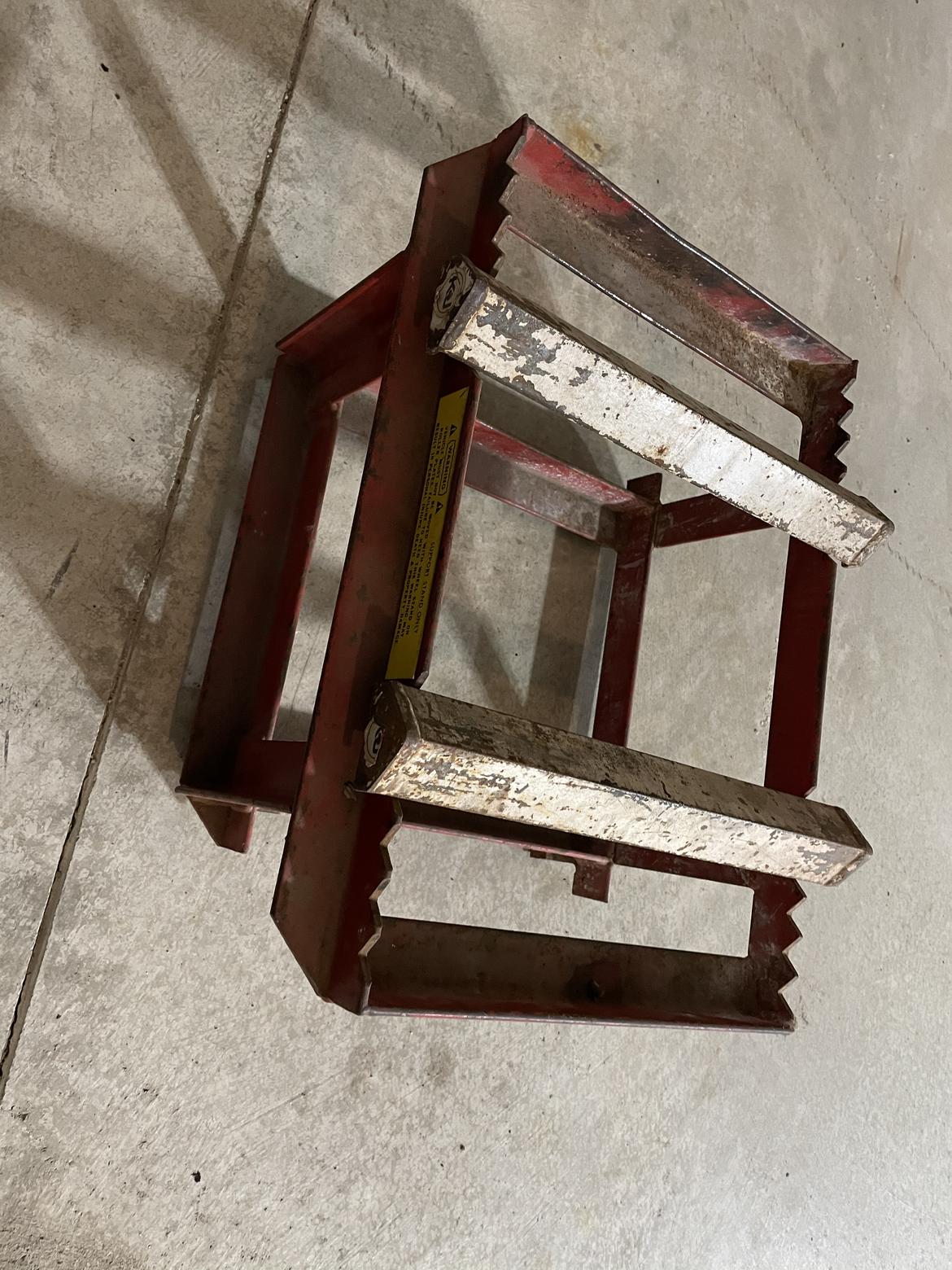
they have 1x1 capped feet so they sit pretty evenly all of the time as well.
I would weld in some x bracing in to those.
Don't think so, it's welded on all corners with full overlap. When I made mine I had my engineer draw it up and the shear was 22,000#s.
I'm Not an engineer, and that was 15 years ago so I couldn't tell you but that number has always stuck in my head.
I missed the post with pictures, till just now. Thanks. I have most of what I need for them already around. I can tack 'em well enough to have someone that can actually weld finish them for me!
No pictures yet, but I used 4x4 pressure treated lumber with 1x10s as a platform on the base piece, then 2x4s across at the ends to keep the car from rolling. Made them 12" x 18", and with the 2x4s blocking at the end, they seem perfect for a 26" tall tire, but should do fine for smaller and larger diameters. This gives the base piece a lift of 4.25". The intermediate and top pieces will each increase the height by 3". I'm using 2x3s to help lock each piece together so it can only slide backwards and forwards by about 1/4" if the car gets bumped hard, though I suspect once the weight of the car is on them, they aren't going anywhere. Will take pictures once assembly is finished.
I used 2x4s and deck screws to get my E46 3+ feet in the air, no issues. I've resused them many, many times since then.
Tyler H (Forum Supporter) said:
I used 2x4s and deck screws to get my E46 3+ feet in the air, no issues. I've resused them many, many times since then.
The next question from me is how did you get the e46 wheels 3ft in the air to get the cribs under the tires?!?!?
chandler said:
Don't think so, it's welded on all corners with full overlap. When I made mine I had my engineer draw it up and the shear was 22,000#s.
Those may take 11 tons of vertical load (that your engineer friend may be calling sheer) but I bet any significant horizontal loading with weight on them will end badly. If you give me the angle iron size I may just model that in my Autodesk software and see what loads it can take in the horizontal plain. Or just give it to my structural engineer and have him analyze it. I still say it needs x bracing but the math would tell us for sure.
I assisted in the investigation into KC Hyatt disaster in the beginning of my professional life and because of what I saw I have a bent towards being conservative with my designs. I keep three of the bolts from that suspended walkway on my desk to remind me to not be a dumb ass when I design things.
Here's the "final" product. My ramps take the car up to 6.5" off the ground. These should be 10.25", and I can build more intermediate pieces if I need to, maybe after lumber prices come out of the stratosphere. Let me know if you see any dangerous design flaws.
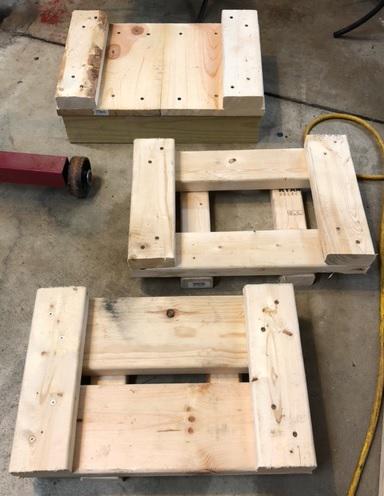
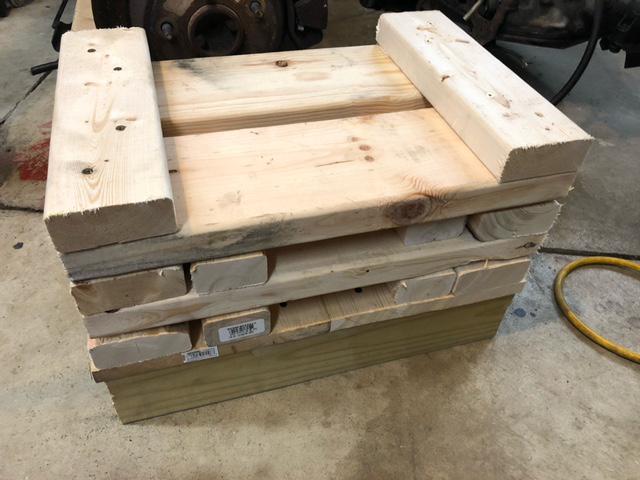