The commute attack car that is newly barchetta’d needs a 2-3” windshield to fulfill my vision and maybe to make it aerodynamically nice to drive. Whats the hot setup? I was thinking I’d fabricate a holder that slides into the roll over hoop remnant on either side of the dash and pins into place (like I’m doing with the original windshield frame with dowels). Then with a channel across the bottom made from aluminum.
What source do you guys use, and what’s the hot setup for moldable (it’s going to have curvature) and safe, etc.?
Learn me. 

this is what I’m trying to do. I always drool over this setup when I see them at vintage festival. So sweet. Surely some idiot passenger will open the door without flipping up the little doohickeys that join the side windows to the windscreen at the top, but berk it, I can fix whatever damage they do.
I'm the Jag on the pole in the corner I used both polycarbonate for the first one that lasted about a decade. And plexiglass for the rest of them. The plexiglass last 1&1/2 times longer than the polycarbonate and cast less than 1/2 as much.
I will echo frenchy on this, and explain my experiences. Polycarbonate is much more impact resistant, but the down side is that it scratches very easily. It gets hazy the first time you wipe it gently. Acrylic is less than 1/2 the cost and still adequite with regard to impacts. You do not "mold" either one. If you look closely at the Ferrari you posted you can see that all curvature is in a single plane. Make a cardboard template, trace it onto flat sheet, cut n install. Below are pictures of several that I have made, all from flat sheet.
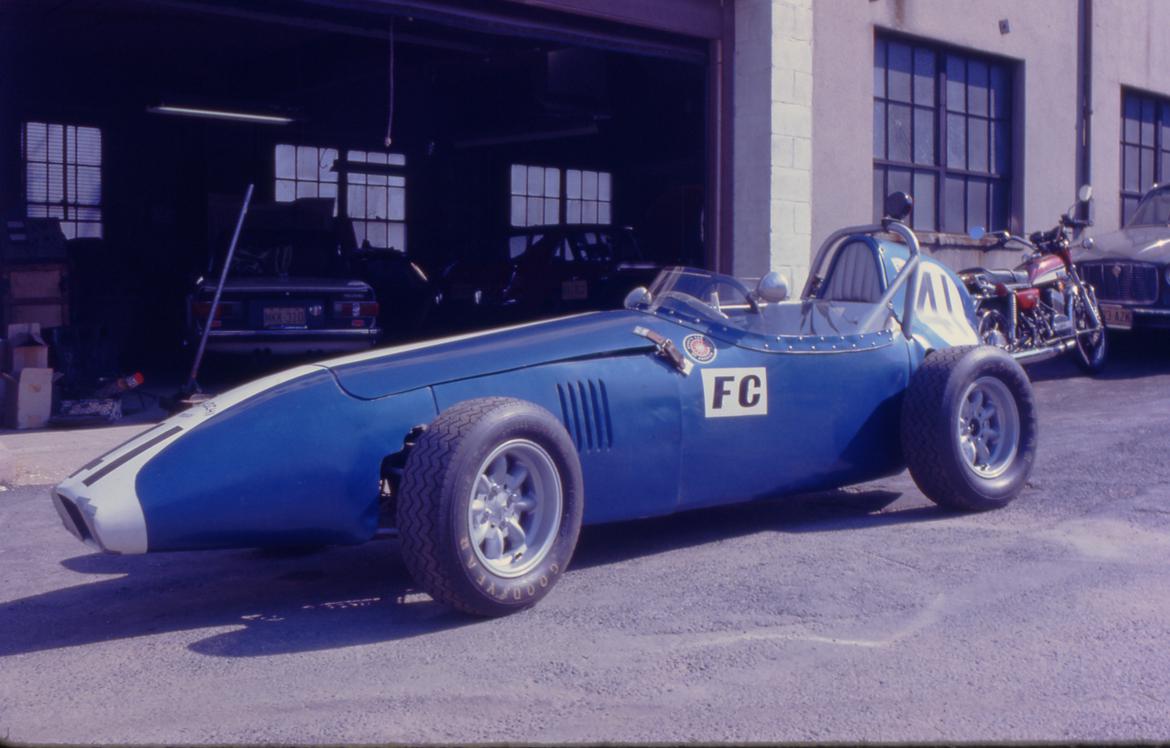
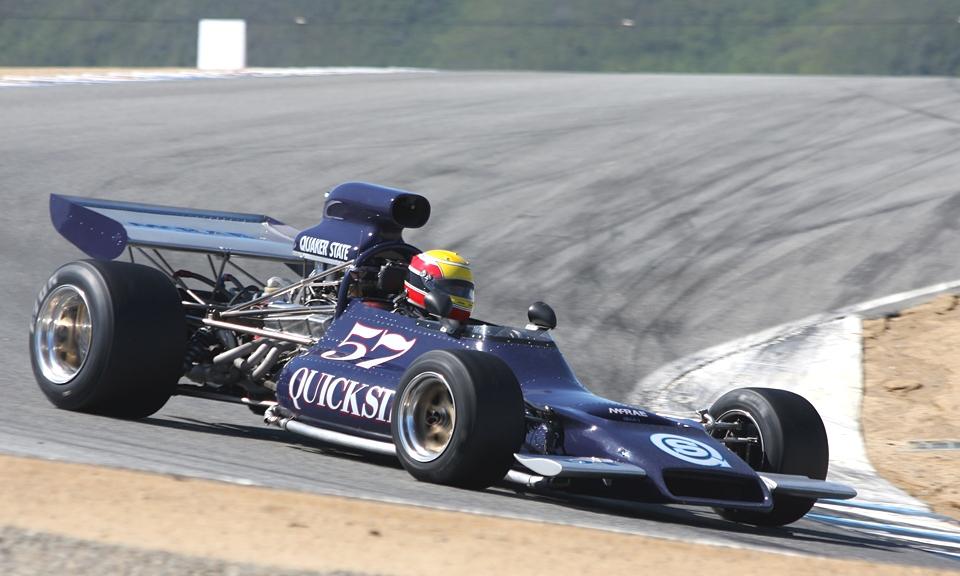
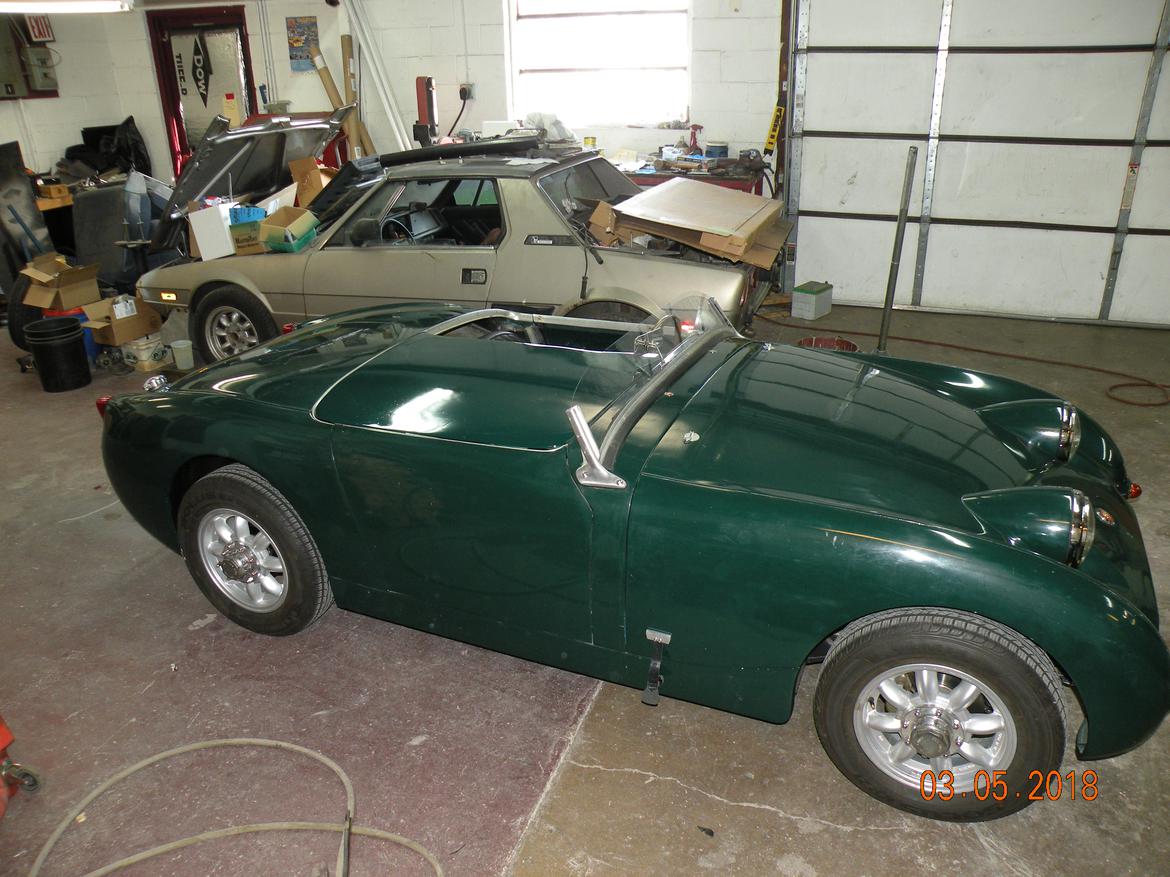
kb58
SuperDork
4/14/20 8:09 a.m.
Be aware that polycarbonate ("Lexan") expands a lot with temperature... think like 1/8" over 4 feet or so. Point being, drill oversized mounting holes to allow it to move around.
Agree they look awesome, but that's about as far as it goes. I remember finding a 3"-long 1/2" diameter bolt IN my headlight after a trackday session. Imagine hitting that with you helmet, or sunglasses if on the street. Just sayin'
kb58 said:
Be aware that polycarbonate ("Lexan") expands a lot with temperature... think like 1/8" over 4 feet or so. Point being, drill oversized mounting holes to allow it to move around.
Agree they look awesome, but that's about as far as it goes. I remember finding a 3"-long 1/2" diameter bolt IN my headlight after a trackday session. Imagine hitting that with you helmet, or sunglasses if on the street. Just sayin'
yes this is important. I had a 100 degree temp swing between 2 races and the cold events it likes to crack around the rivets, dont use rivets. use rivnuts or weld nuts and have the hole oversized on the lexan and use flanged hardware to install it.
Carbon (Forum Supporter) said:
The commute attack car that is newly barchetta’d needs a 2-3” windshield to fulfill my vision and maybe to make it aerodynamically nice to drive. Whats the hot setup? I was thinking I’d fabricate a holder that slides into the roll over hoop remnant on either side of the dash and pins into place (like I’m doing with the original windshield frame with dowels). Then with a channel across the bottom made from aluminum.
What source do you guys use, and what’s the hot setup for moldable (it’s going to have curvature) and safe, etc.?
I have just finished doing what you are planning. The moldable part is not strictly required for most windshield shapes. The material (Lexan/polycarbonate) will take quite a bit of shape before heat is needed. I did use heat to try and bend the ends of my windscreen at the dash ends. It did not go quite as planned, but some of that is due to the material spec I went with. I used a hard-coated Lexan, which helps to reduce the likelihood of getting scratched. Also, I used 1/4" material and it will take some very significant heat (from both sides) to get a clean heated bend. The hard-coating on my material reacted to the heat before it was soft enough to bend cleanly and I wound up with some crazing in the corners. I did try cold bending some samples and would do that in the future.
kb58 mentioned the expansion and that is a real concern, so do oversize any mounting holes and allow the system to expand contract. Mine has a line of foam at the front and rear of the mounting channel and is only pinned at the ends (with over-sized holes). Frenchy and Turner both noted that acrylic is harder (less prone to scratching) but it is more brittle and when it fails it makes shards. Lexan/polycarbonate bends/tears so is a better option for impact resistance.
Turner did mention that the easy answer is a flat pattern and that is the way I approached it as well. I made a cardboard windscreen shape and transferred that to the plastic. Treat most of the fabrication of the windscreen like you were working with wood and you will get good results. As far as source locations, try any local metal supply house and if they don't carry plastics ask them who might. Since the material is sold in sheets you are going to wind up buying more than you need for a single 3" tall windscreen. Make the first one with your pattern and when you are happy with it, edit your template and cut out a few extra blanks for future use. I got my material from StockcarSteel, but they are local to me and supply lots of race teams with materials. A 4ft*8ft*1/4" sheet was ~$300. I got several blanks and quite a bit of leftover material from a single sheet.
I will post pictures of my windscreen mounting details later today.