caseam
New Reader
11/21/24 9:01 a.m.
First off thank you tvs1320 for the .STL files. I had my brother print them off at work for me.
I am still having an INSANELY hard time getting the piston off the end of the ram. I tried being gentle in the beginning without marring the the end of it, but resorted to vice grips, channel locks, and eventually a pipe wrench WITH a MAAP torch. Still ZERO luck.
I was really trying not to damage the U-seals/oil seals as I only need to inpsect/replace the air seal on the inside of the male threaded cap.
This is very unfortunate after spending a small fortune on these and QuickJack/Bendpak being of no help other than "you're going to have to buy new cylinders". I use my QuickJacks maybe 10 times a year.
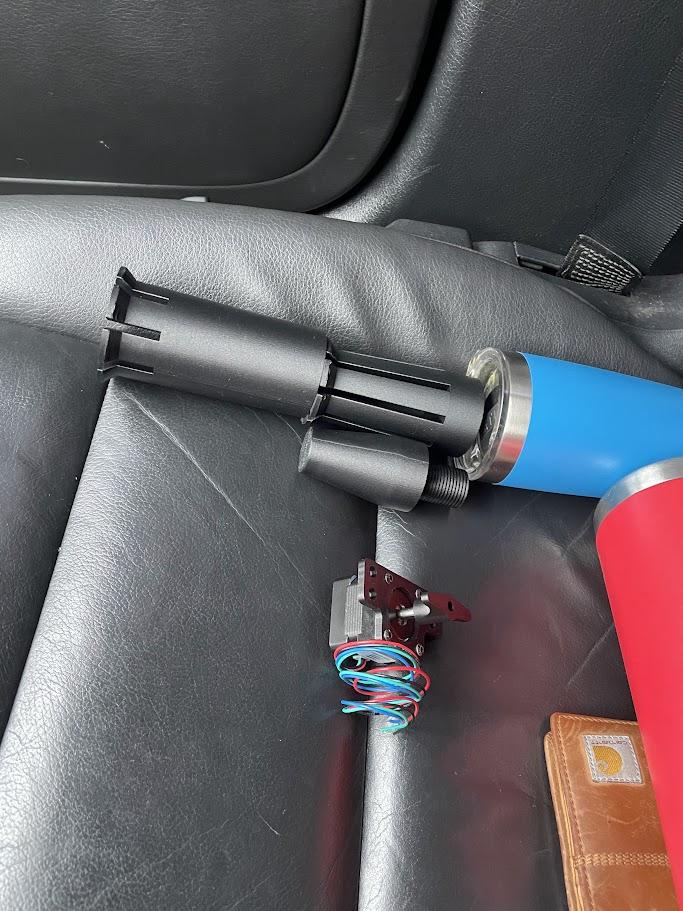
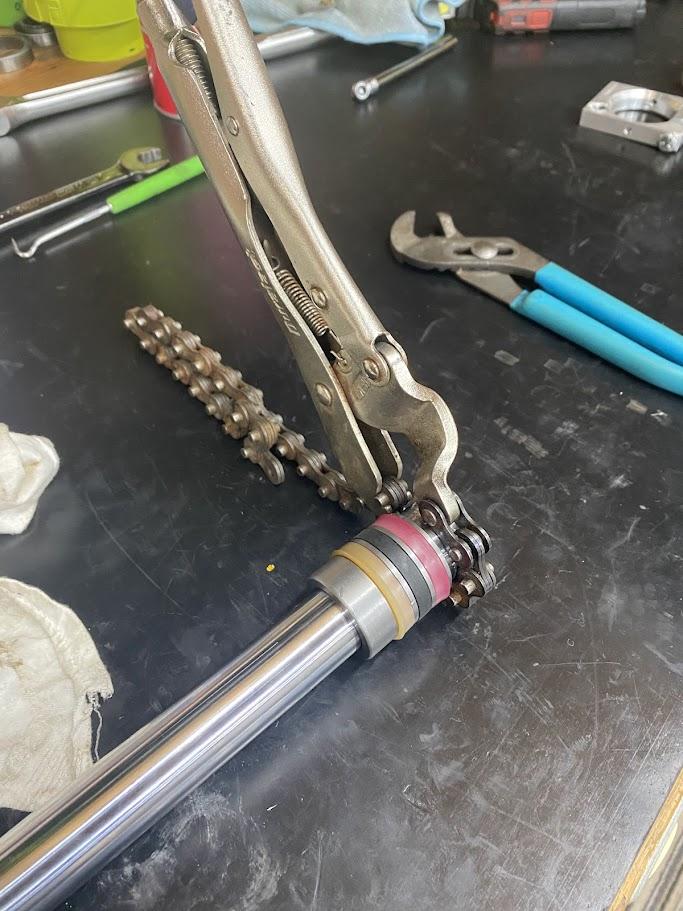
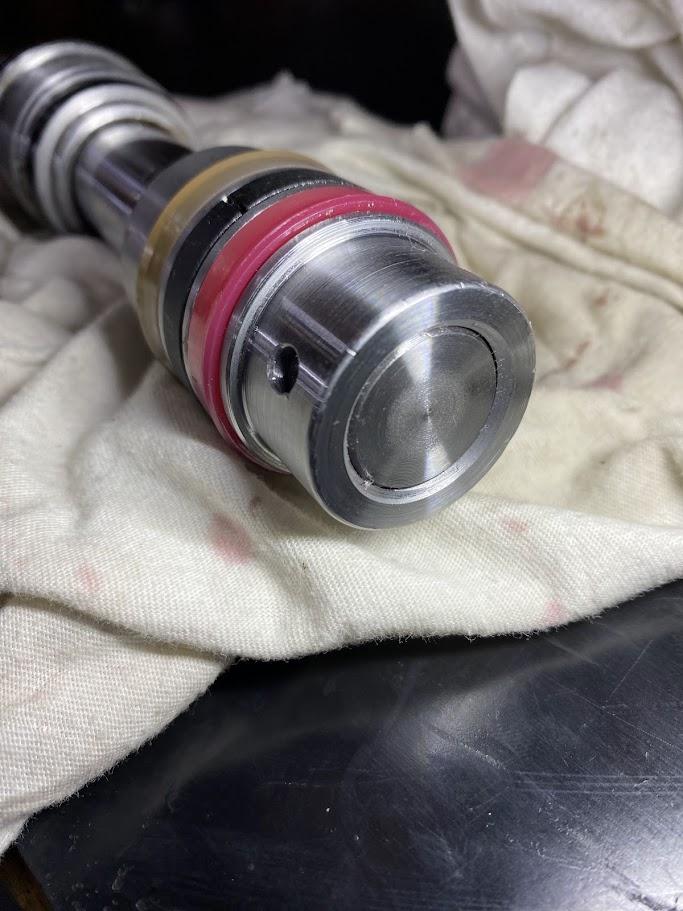
caseam
New Reader
11/22/24 8:03 a.m.
UPDATE:
I got the piston off. The entire thread stack had locktight on it, has to be high strength. It dawned on me to put the ram back into the quickjack frame where I had more leverage and could atleast stand on the frame. After heating up for several minutes it started to turn (I got the other side removed with just some heat and a spanner wrench, did not resort to a pipe wrench or vice grips - thank god).
Anyway, I disassembled everything and sure enough the inside of the cap was filled with rust, pitting, and corrosion (has to be an issue with their chrome plating process, I am almost certain the rams are made from A36 or 1045 steel, not stainless as they are very magnetic (explains the pitting). There are 3 seals inside the cap: 1 wiper, another U-cup seal, and some sort of teflon/PTFE coated split ring bushing. I cleaned the seals thoroughly with brake clean & compressed air, scotch brighted the surfaces, and reassembled everything with standard wheel bearing grease. All went back together great, but when I pressurized the cylinders there was still an air leak.
I disassembled everything again in a quarter of the time originally and replaced the air seal with one from the harbor freight o-ring kit ($8.00). I figured 50 PSI really is not much for an o-ring, alot of other systems are much higher pressure that use standard o-rings. I assembled everything once again, charged with 50 PSI, let it sit overnight, checked again in the morning and no air leaks!
I filmed the whole process and plan to upload a youtube video since there seem to be none out there. Will test this weekend!
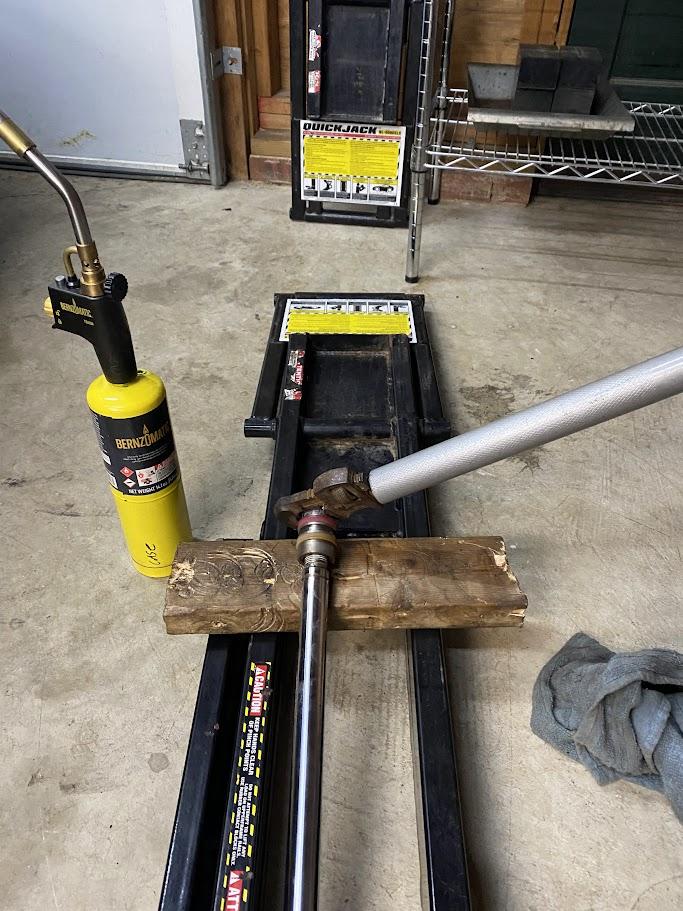
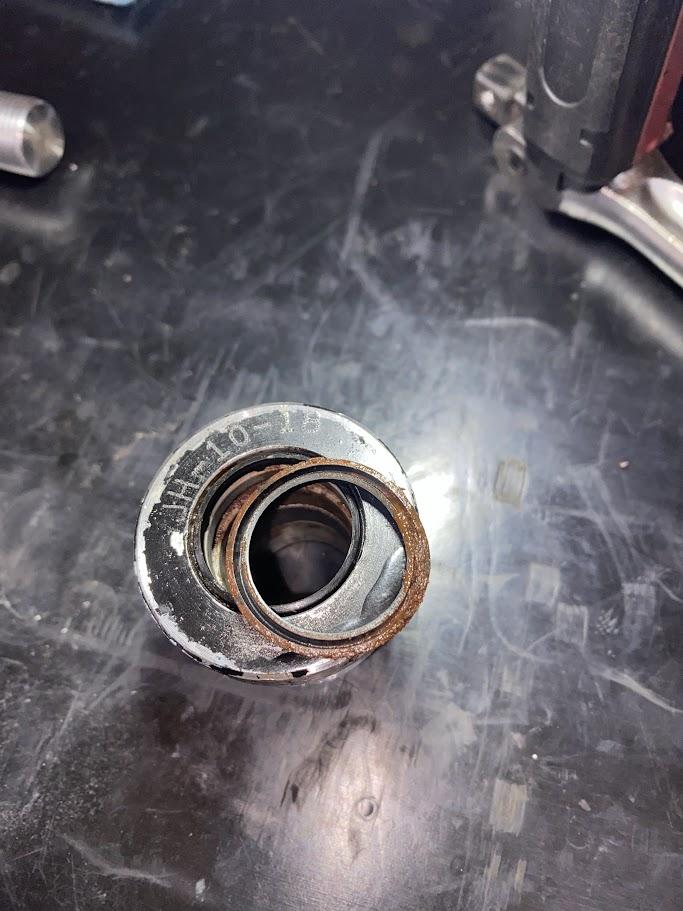
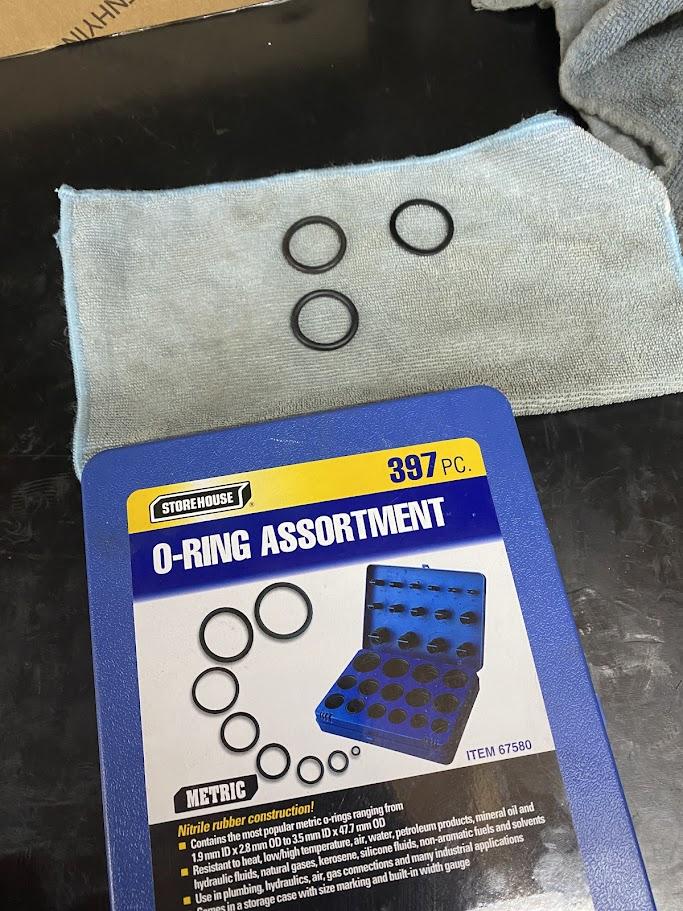
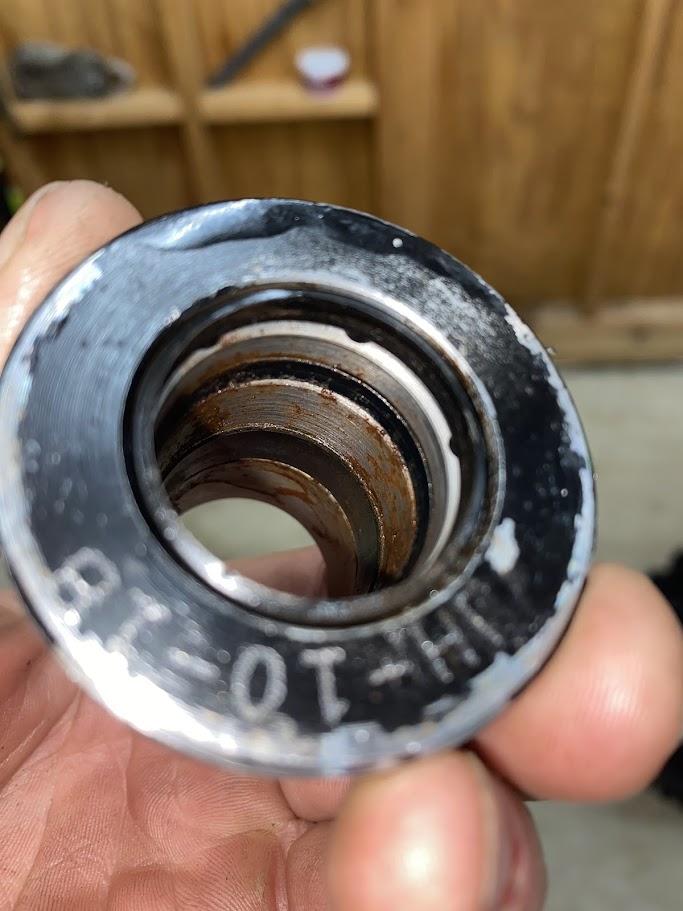
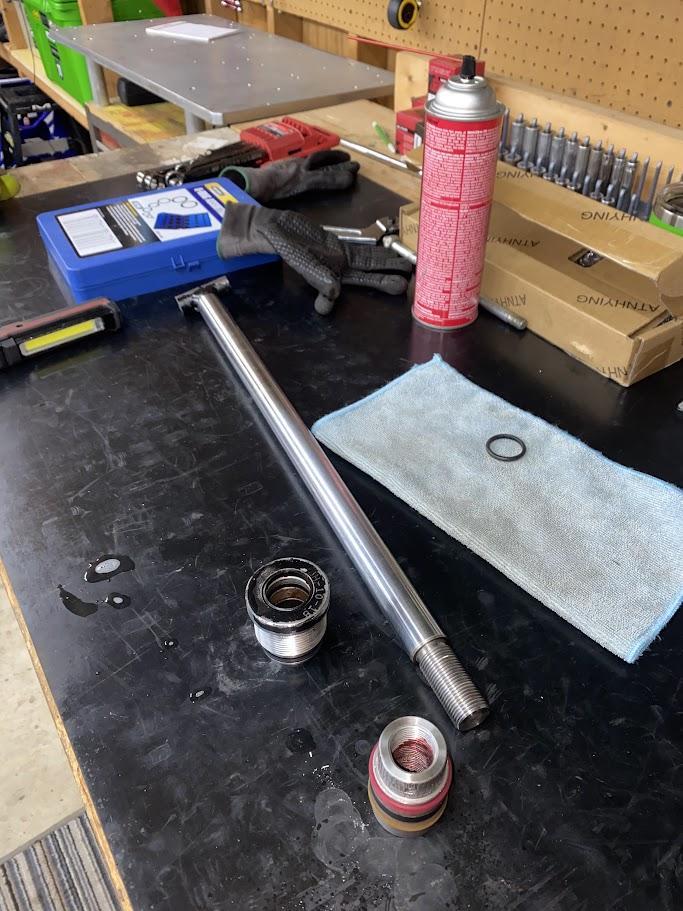
In reply to caseam :
Excellent progress! Good job getting it apart non-destructively.
caseam
New Reader
11/25/24 7:45 a.m.
Got the cylinders back in the frames, bled the lines, and tested them out two times on two separate days and everything worked perfect. Although I did not replace the oil seals, I do have the 3D printed parts for when (if) that time comes. I made a video on the entire process, hope this helps someone in the future.
https://www.youtube.com/watch?v=z9GP8wuQC1o&t=20s