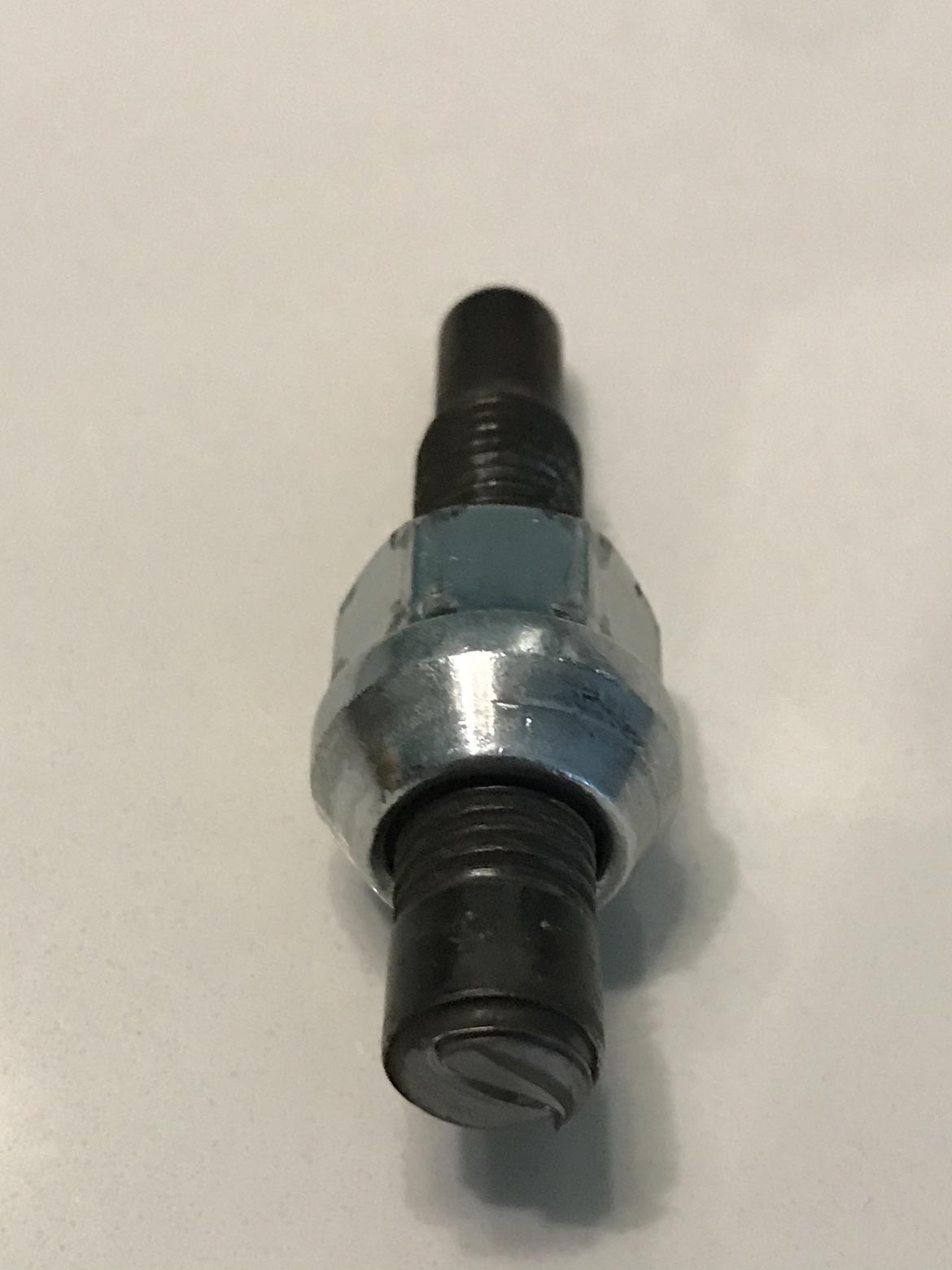
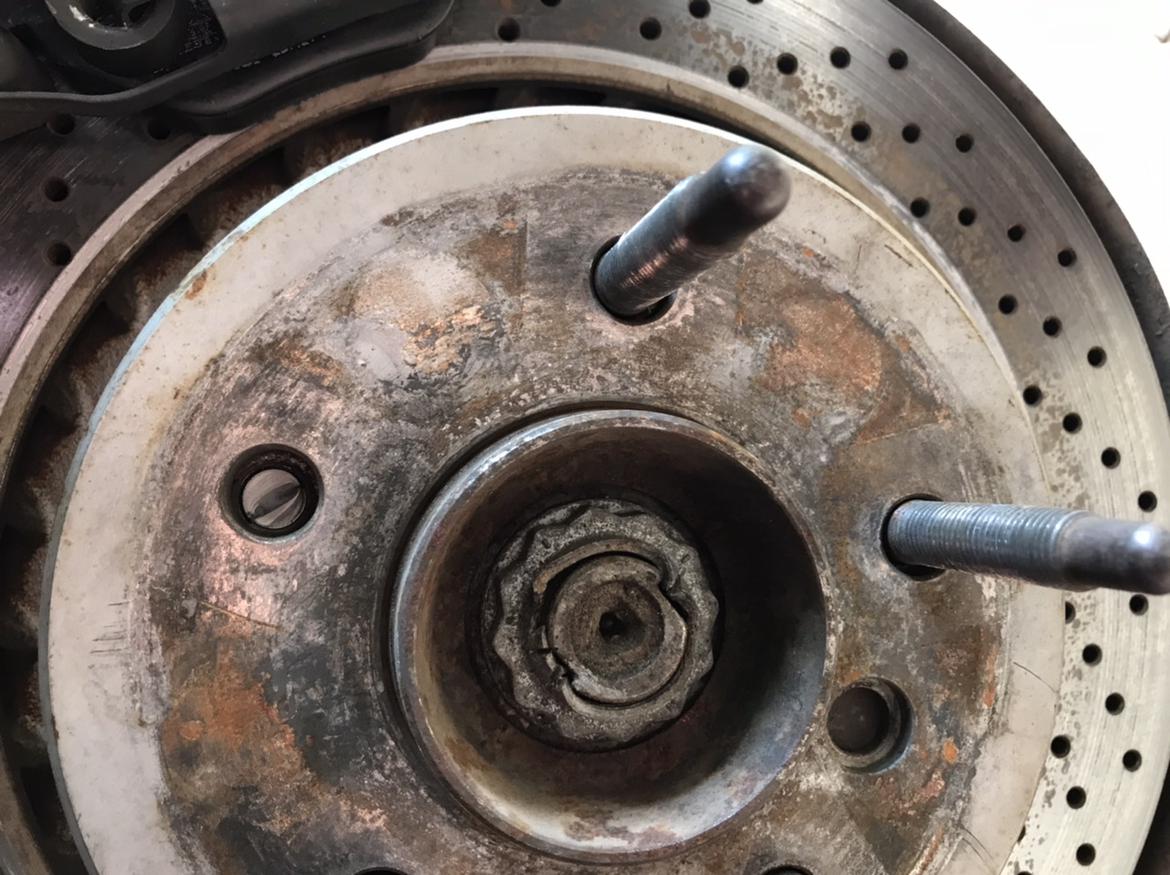
Snapped a wheel stud on my E36 earlier today and looking for some help. The remainder of the stud is below the surface of the rotor top hat upper left. I've never had to remove a broken fastener of any kind. I'd estimate there isn't more than a half inch of fastener remaining the hub.
Guessing the right way to proceed is to center punch it, drill out the center with a bit about half the diameter of the stud and then use an extractor. Any recommendations on fluted or square extractors?
Also, a sharp eye will notice that the stud that broke has a rounded head. I'm going to need to remove all of the studs on the rear and they all have that rounded head which offers me no easy way to back them out. Guessing I'm going to need to use two nuts that trap each other?
All tips and advice appreciated as I've got a track day scheduled in 9 days so anxious to get the car all buttoned up.
How did you break the stud? I presume the nut locked up, and the stud broke while you were twisting. If that's the case, the remains are going to be locked in that hub either by falling, or with red loctite.
There isn't a head on the inside of the hub, right?
Stud broke while I was tightening the lug nut by hand with a socket. I'd bet there is Loctite on the threads and I've had good success using a heat gun or torch before to release Loctite.
No head on the inside of the hub. These are 90mm aftermarket studs that can accommodate wheel spacers.
Did it snap when tightening or loosening? If tightening, the remains may not be that tight. If it is loctited in place, you will need to use heat to get it back out, or drill it out almost entirely (risky).
The big thing to remember is scope. You are going to attempt to buy new tools, learn how to use the new tools (and get good practice with swear words because extracting sucks) and risk damaging a part that you can replace, with new bearings, with a lifetime warranty, for $65 from fcpeuro. Is it truly worth trying to fix rather than just replace the wear item?
If you want extractors, get left hand drill bits, also. Personally, I have only ever tries to extract high quality bolts (studs included) and they are usually hard enough that extractors don't want to grab them at all. Pulling out a stainless fastener is easy, Grade 8 (or metric equiv.) is another story. Left hand bits and center punches work the best for me, so far.
In reply to matthewmcl (Forum Supporter) :
That's a solid point. I may just be better off getting two new rear hub assemblies and paying a local garage to replace them. Because I definitely don't have the tools or experience needed to do the hub replacement myself.
Sorry, it looks like $65 was about $20 to low, but still not too bad. If you want studs, then look at having your hubs put in by a machine shop that can drill the hubs for press in studs.
Yep a bit more expensive and the rear hubs don't come as an assembly with bearings already pressed in. So about $350 all in on parts for both rear hubs and bearings plus probably another 300-450 in labor. Not to mention the $135 for new wheel studs.
I think I'll try my hand at removing the damn stud before breaking down and shelling out $700+ for the complete rear hub and bearings refresh.
Worse case scenario I guess is that I'll end up taking my E46 M3 to the first track day instead of my E36.
Assuming loctite: Propane/mapp torch to get good local heat on the broken stud when you want it to move. You want a bit more than 400 degrees to melt the loctite. With the rotor off, it looks like you should be able to hit the ridge of the broken stud with a center punch. That can spin it around. You are not tightened against anything, so with the loctite soft it won't take very much to spin.
If you're already willing to buy a new part ,a hub ,by all means try to remove it what's the worst that happens?
Yeah I'm going to give it go. Worse case I learn something.
I'd still practice on a piece of scrap first. Even a bolt through a board with a couple of nuts on the thread side. See if you can drill the bolt with out buggering the nuts.
If you can do that three times in a row you're probably alright to drill out your stud
To clarify, try hitting off center with the center punch, not to prep for drilling, but to spin the stud.
matthewmcl (Forum Supporter) said:
To clarify, try hitting off center with the center punch, not to prep for drilling, but to spin the stud.
What he said, although I've had good results with a small cold chisel to engage the broken stud. Tap it out by using the chisel to carefully rotate out the stud. Specs for loosening red loctite are heating it to 450* F for ten minutes. Propane torch will handily do that.
Another thing often worth trying is an impact screwdriver with a flathead tip in it. Looks like you've already got a bit of a groove that the tool may be able to bite and spin if the piece isn't that tight to begin with. If not, i use a small cutoff wheel on a dremel to make a slot for the screwdriver to work with.

But if none of that is possible i end up drilling, which sucks.
In the old days , a hammer and punch did the job.
In reply to iceracer :
If the stud weren't threaded into the hub then yes, I suspect that would be all that is needed. In this case I'd like to save the threads and hub.
trumant (Forum Supporter) said:
In reply to iceracer :
If the stud weren't threaded into the hub then yes, I suspect that would be all that is needed. In this case I'd like to save the threads and hub.
Hammer and punch to unscrew the stud and save the threads (or screw it out the other side if there is room and that is easier). It's like loosening a wingnut with a hammer.
Thankfully I have some punches on order. When they get here on Tuesday I'll give it a good dose of heat with my butane torch to defeat the red Loctite and then give it the beans with the hammer and punch.
I would use an extractor or ezout as a last resort as they usually break and you likely won't be able to drill it out. You'd probably have to drill tiny holes around it and try to break it out or have it removed by a shop.
It might just be me, but I'd rather change the hub myself than try to get that stud out. That looks like a world of frustration. Plus, you can replace it with a hub with press in studs so that next time replacing the broken one is easy.
Thank you all for the words of wisdom!
My cutting oil, reverse drill bits, punches and fluted extractors arrived a day early so I had some time to get down to business after work today.
Started by heating with my torch for 4-5 minutes until the stud was visibly smoking. After heating tried the punch and hammer on the small lip formed by the shear. After about 15 whacks I finally saw some small regular movement that indicated the Loctite problem has been defeated. However the hammer and punch approach was making little progress and was actually slowly destroying the lip on the face of the stud.
Phase two of my battle plan was to use my Dremel with a conical cutting bit to team out a cone shaped hollow in the face of the stud.
Phase three was punch to center reverse drill bit, cutting oil for lube and then slow and steady with the cordless drill. About five minutes of intermittent drilling and lubrication and I punched through the back of the stud.
Phase four, bang in fluted extractor and a slow twist brought very positive movement and ultimate victory!
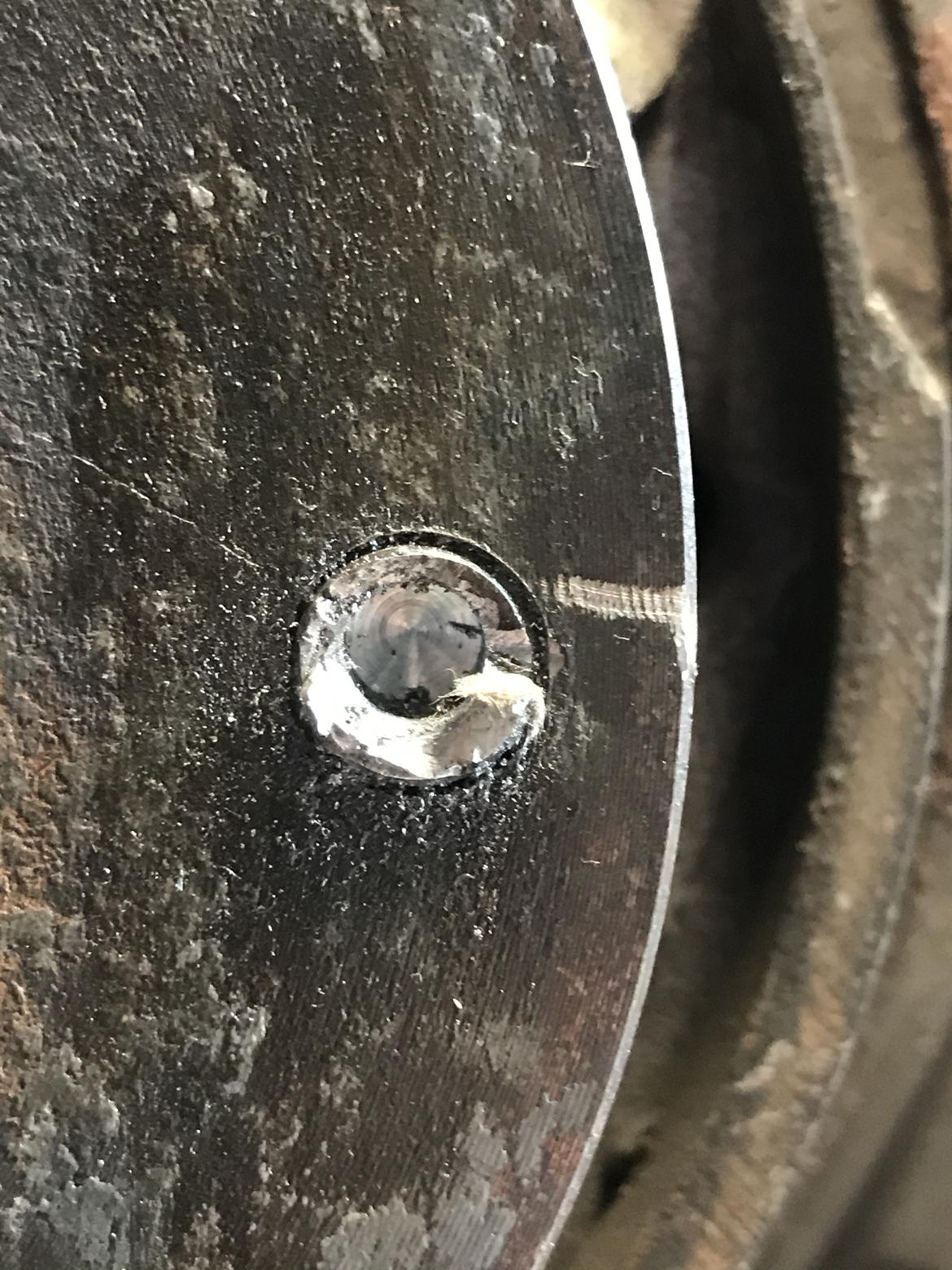
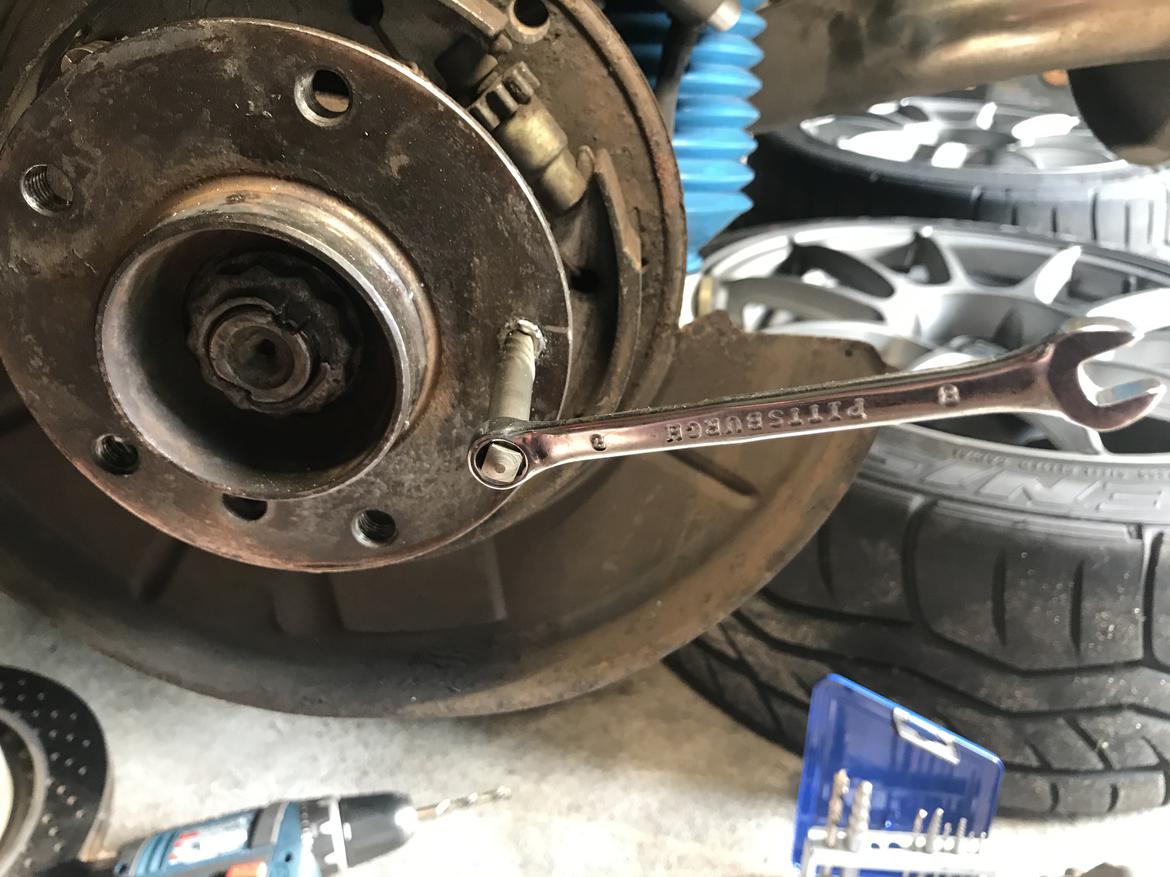
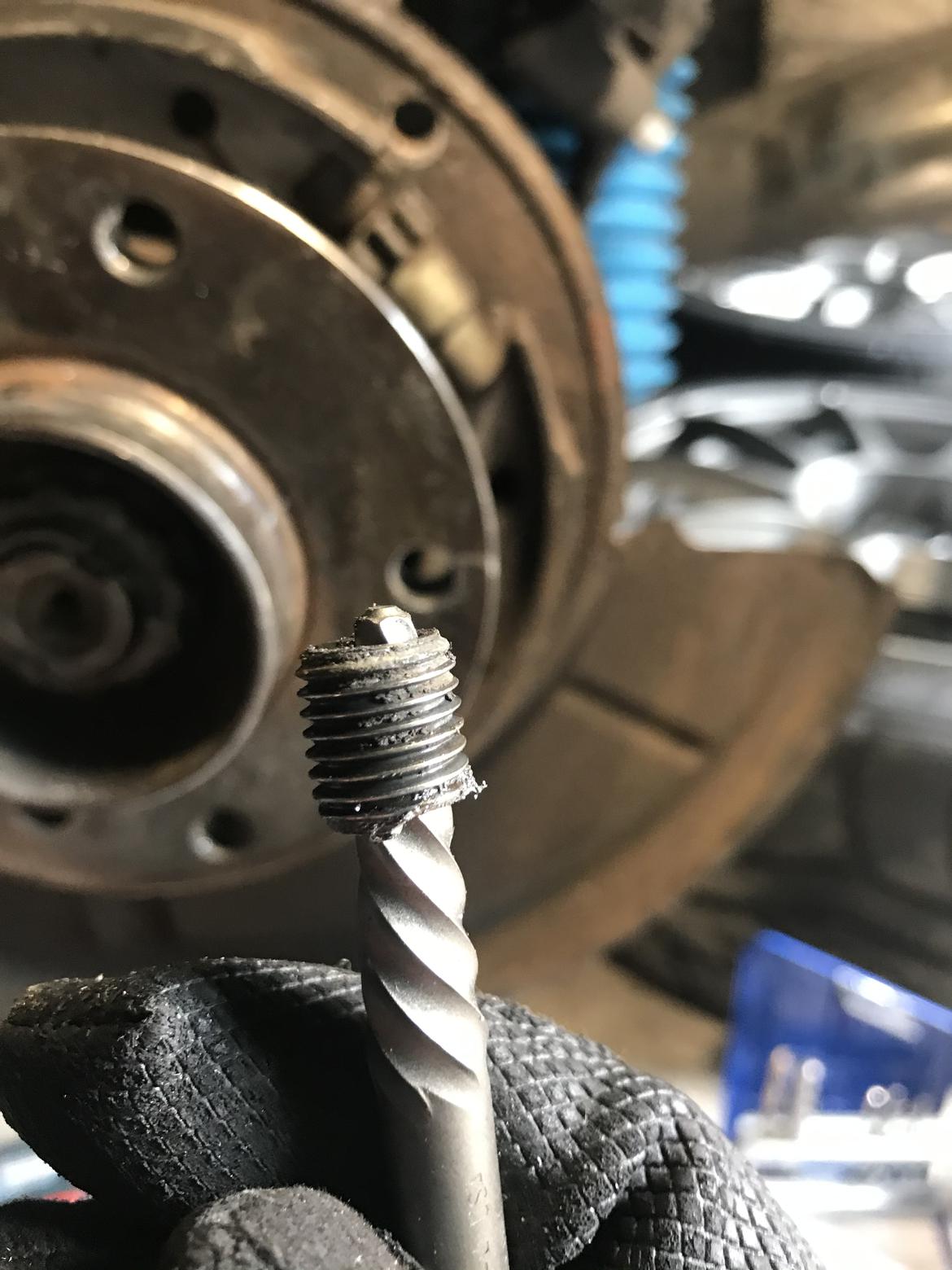
So happy I was able to remove it, save the hub and learn some new techniques.
I know it may seem like a small thing but working through these kinds of speed bumps with the help of you all here is really building my skills and experience and giving me confidence to at least try to tackle things I wouldn't have even considered previously.
That's fantastic! But that kind of success on your first try is going to spoil ya rotten.
But you did approach it in a logical manner, and patience wins the day.
Removing a broken bolt might be the most sweat inducing automotive thing imaginable.
By the way, if you do end up blowing up an EZ Out, a carbide bit in a Dremel tool works well to hog out the extractor. Ask me how I know.