I'm not understanding this picture.
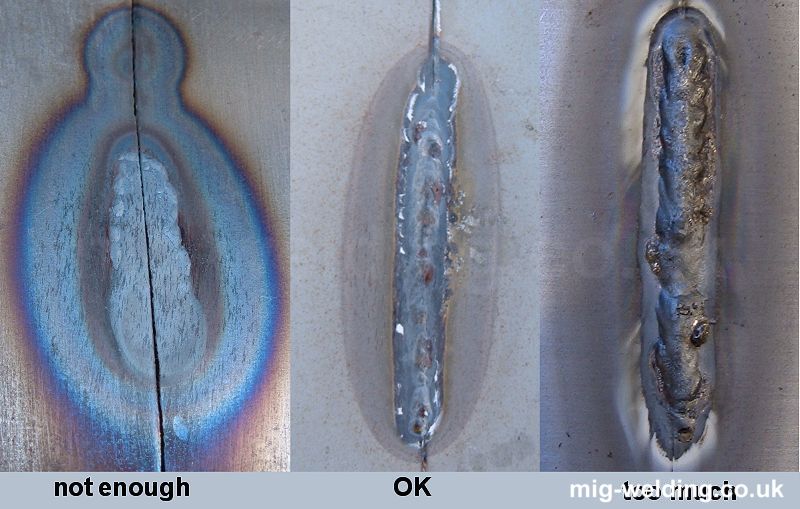
If that's the backside how do you get a bead there? Only thing I can think is you've totally melted both sides and used the filter to build it up. Wouldn't that give you blow out? I think I've been laying it on thicker with later welds but I'll have to look at them tonight after I get off work.
You've got it, you're totally melting the two together. It won't blow out done correctly, the molten metal freezes back up before then. I'd suggest bumping the heat up until you start blowing through so you can see what that looks like, you develop an eye for it after a while. You can see the puddle, right? Too dark of a mask will really screw you up.
Exactly... it is VERY EASY to use a MIG to make pretty welds that just sit on top of the metal. You need to melt the parent material!
Of course 90% of what I weld is weak thin crap where blowing through is a huge problem, so any time I get to weld something nice, I generally spend a few weld-inches reacquainting myself before I go to town.
I've only welded with flux core a couple times but one thing that stuck with me was the first time I used it, the person with me who was more familiar said you have to "push the weld in" compared to using a shielding gas. Somehow that made perfect sense and my welds improved.
OK I'll look at the later one from last night and then see if I can improve tonight. Thanks guys.
Well the best ones from last night still didn't go all the way through. Unfortunately I'm already at the highest current setting. Going to a faster feed just resulted in a tripped breaker. I tried laying a thicker bead and you can see a slight difference on the back side but still nothing like a complete melt there. Would wider side to side help? Am I just at the limits of my machine and circuit breaker? Is laying down a weld down the back side a solution for now?
If you are not getting enough penetration, it's time for a prepared weld. Grind the edge of what you are welding before.
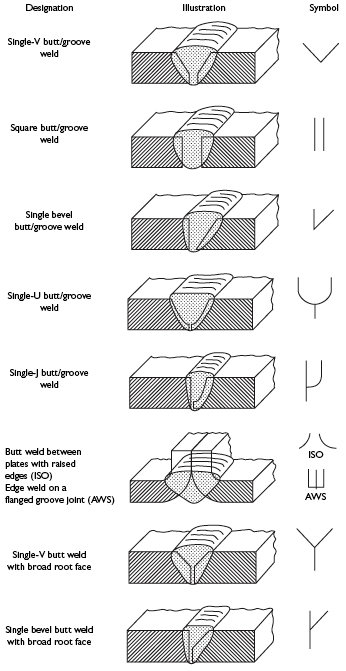
I think I'll have to try the single bevel since all of this is two pieces 90 degree to each other. Won't be free again to work on it until Wednesday night but I might spend that cutting pieces so that I can weld it all up Friday.
Tripped breaker? Insufficient wiring (and thus, power to the welder) will make things difficult.
What welder are you working with? The 120 volt machines really need a 20 amp circuit, EDIT: and heavy duty extension cords, like 10 gauge or better
BrokenYugo wrote:
Tripped breaker? Insufficient wiring (and thus, power to the welder) will make things difficult.
What welder are you working with? The 120 volt machines really need a 20 amp circuit, EDIT: and heavy duty extension cords, like 10 gauge or better
Yea I know but I'm fighting what I have. Tonight I was running off a 14 gauge cord and a 15 amp circuit. I upgraded from what I was running Saturday cord wise. I just looked and I can move to a 20 amp circuit but I'm dealing with a 1953 house here. Permanent solution is a dedicated outdoor circuit to within 20 feet of where I'm working. Don't think that'll happen by Saturday. I'm using a Lincoln Pro-Mig 140.
SVreX wrote:
Hmmm... 
Don't know what you're talking about.
Get a better extension cord. You can use a long one (50-100 ft) if it's 10 gauge, 12 gauge up to 50 ft.
If you can dedicate a circuit to the welder then you can usually use a higher amperage circuit breaker than the normal NEC rules allow.
You haven't reached the limits of your welder yet, just the breaker that its plugged into right now. You should be able to do 3/16-1/4" in one pass on a 140A machine. You've reached the internal limit when the internal breaker on the machine pops for duty cycle
http://www.codebookcity.com/codearticles/nec/necarticle630.htm
SVreX
MegaDork
1/31/16 8:57 p.m.
eebasist wrote:
If you can dedicate a circuit to the welder then you can usually use a higher amperage circuit breaker than the normal NEC rules allow.
Sure, if you want to collect on your fire insurance.
Maybe we should use the alternative NEC rules, instead of the normal ones?? 

Breakers are sized based on load and wire size. Upping the breaker size will not help the wire size at all. It's not just some dumbass rule.
In reply to SVreX:
Welders carry a different set of rules for Ampacity its section 630.11 instead of the normal table 310. Only if you use a dedicated circuit
This is due to duty cylce of the equipment. NEC 630.11 allows for a 0.45 derating for welders under 20% duty cycle
As long as you pay attention to the welder's duty cycle.
I used to have a nice welder, a little 110 rig but it was damned good. Bluebird? Something. Then I loaned it out to my service manager, who was repairing his car and needed to do some other things. When I got it back, it was fried. He didn't care about paying attention to the rated duty cycle, which was pretty low at the highest settings.
Of course, I found this out AFTER I left that job. Oh well.
Don49
Dork
2/1/16 7:35 a.m.
As was pointed out, a better extension cord is needed. It drastically affects the voltage supplied to the welder. I had a fellow who worked for me trying to use a similar welder with a 14 gauge extension with poor results and when I had him switch it to my 10 gauge extension it was like a different welder.
SVreX
MegaDork
2/1/16 8:24 p.m.
eebasist wrote:
In reply to SVreX:
Welders carry a different set of rules for Ampacity its section 630.11 instead of the normal table 310. Only if you use a dedicated circuit
This is due to duty cylce of the equipment. NEC 630.11 allows for a 0.45 derating for welders under 20% duty cycle
Yes, I understand.
That's a little different information than your first post which essentially said, "Stick a bigger breaker in", with no consideration of duty cycle, or percentage derating, or wire size, or actual amerage draw.
Since we don't know the 1eff value on the rating plate of the machine, I think it would be a little hard to do the duty cycle calculations. 
In reply to SVreX:
http://www.lincolnelectric.com/assets/global/Products/k2480-1/e726.pdf
Never once did I advise just how high of a breaker is applicable with the alternate NEC rules for welders, only that it is possible and allowable for a dedicated circuit
Well we busted some ass this week. I even brought in my quality control expert. He had his knee high boots, welding shirt and his own helmet.
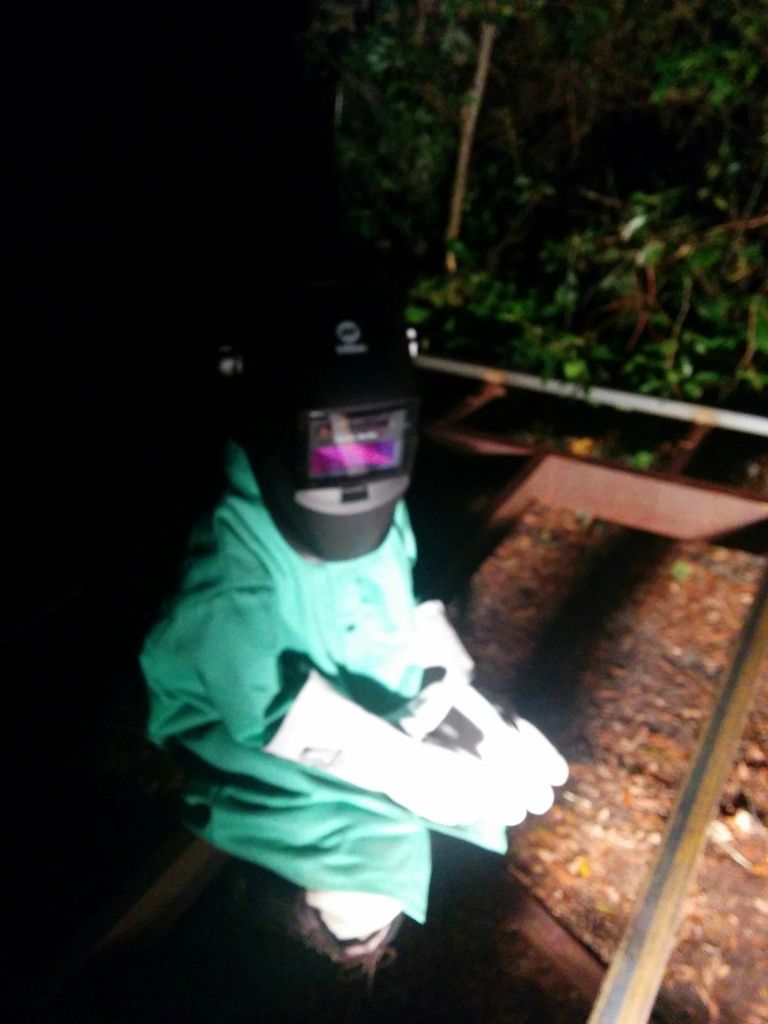
Unfortunately it came down to I berkeleyed up my wood buying at home depot. I came up four pieces short and of course they're right where a car's tires would sit. I'm going to blame it on the cute girl on the wood aisle when I was loading up my cart.
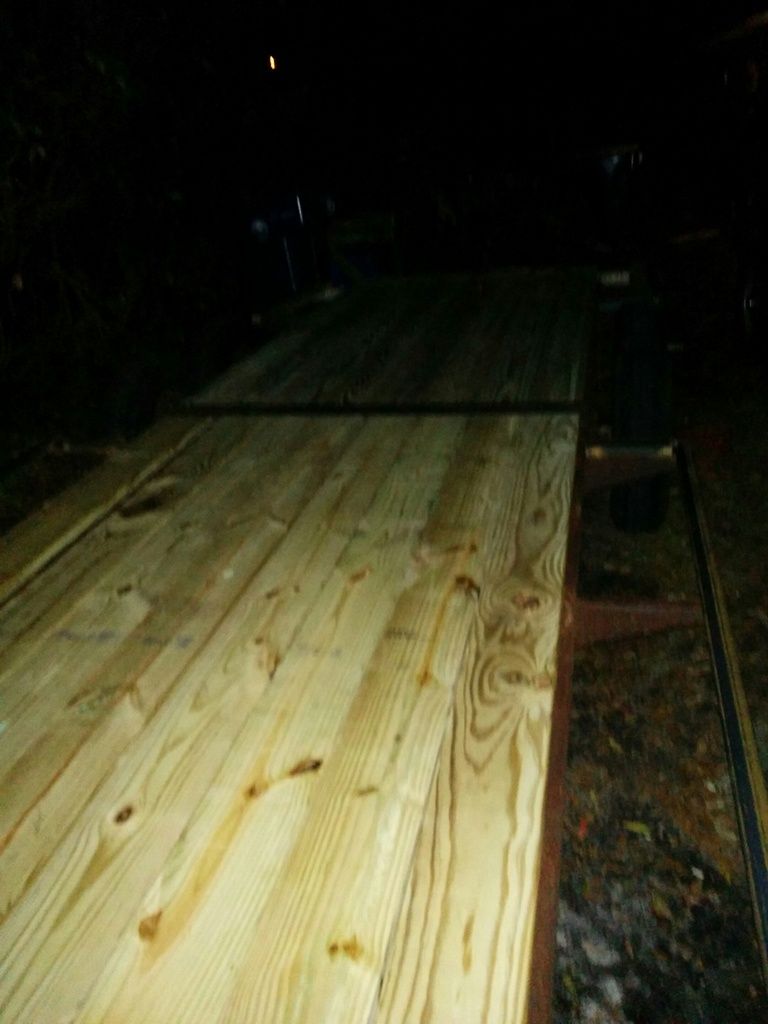
So the new toy pickup is delayed a couple of weeks but I have more time to do things the way I want them.
SVreX
MegaDork
2/6/16 12:49 p.m.
I should have thought this through better ...
...we could have easily finished the wood off at my place today.
Oh well! See you in a couple weeks.
Honestly I think it's for the best. I was cutting corners not safety wise but what I really how I wanted to build the trailer. Now I have time to at least do some basic things like paint the bare metal. It's the simple things in life.
Ummm. You could have left wood out of the middle of the trailer...
As for the welding part, do you have a gas powered generator you can use to power the welder? Just a thought.
Two good points. On the wood I wanted a full deck. It just looks better plus resell is higher/easier. I'll also use it for more than car hauling. I do have a gas generator that could power the welder no problem. Part of the problem though is I actually care about my neighbors. It's bad enough that I can't park anymore cars in my front yard but I also have been making a lot of noise the last two weeks. I knocked off most nights at 9 just in consideration. I really didn't want to be running a generator the whole time.
OK got it painted gloss black.
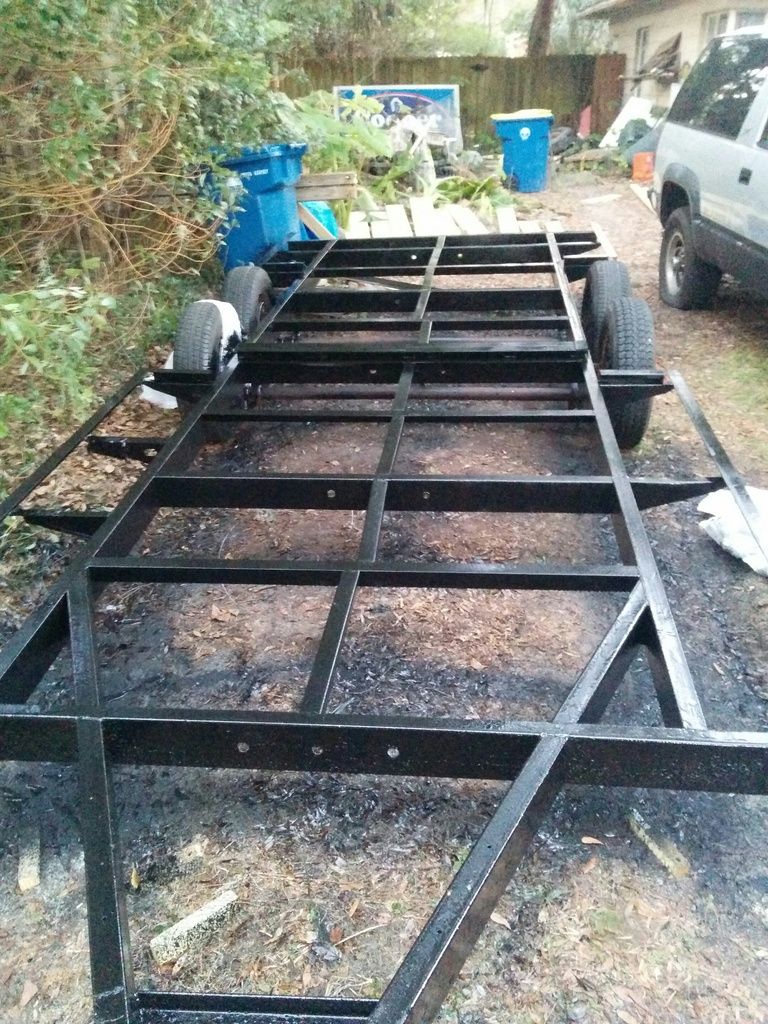
Used 50/50 Rustoleum and acetone. Could have gone thinner but one gallon of paint did it. Sprayed it on with this cause I really hate painting.
