My dad bought this compressor. The stock air line lasted less than a year. He had it replaced under warranty. The replacement lasted less than a year. The warranty process at Home Depot was annoying so he bought a new Kobalt compressor at Lowes. The Husky is now mine.
The tank is clean and not rusty. The compressor head works perfectly. The stock air line setup is garbage. Uses this weird o-ring system that destroys itself quickly with use. I have no experience with air compressors and don't know what to replace this with to make it work or if I can change the way it works at all to something better? Or do I just buy another line from Husky and wait for it to self destruct.
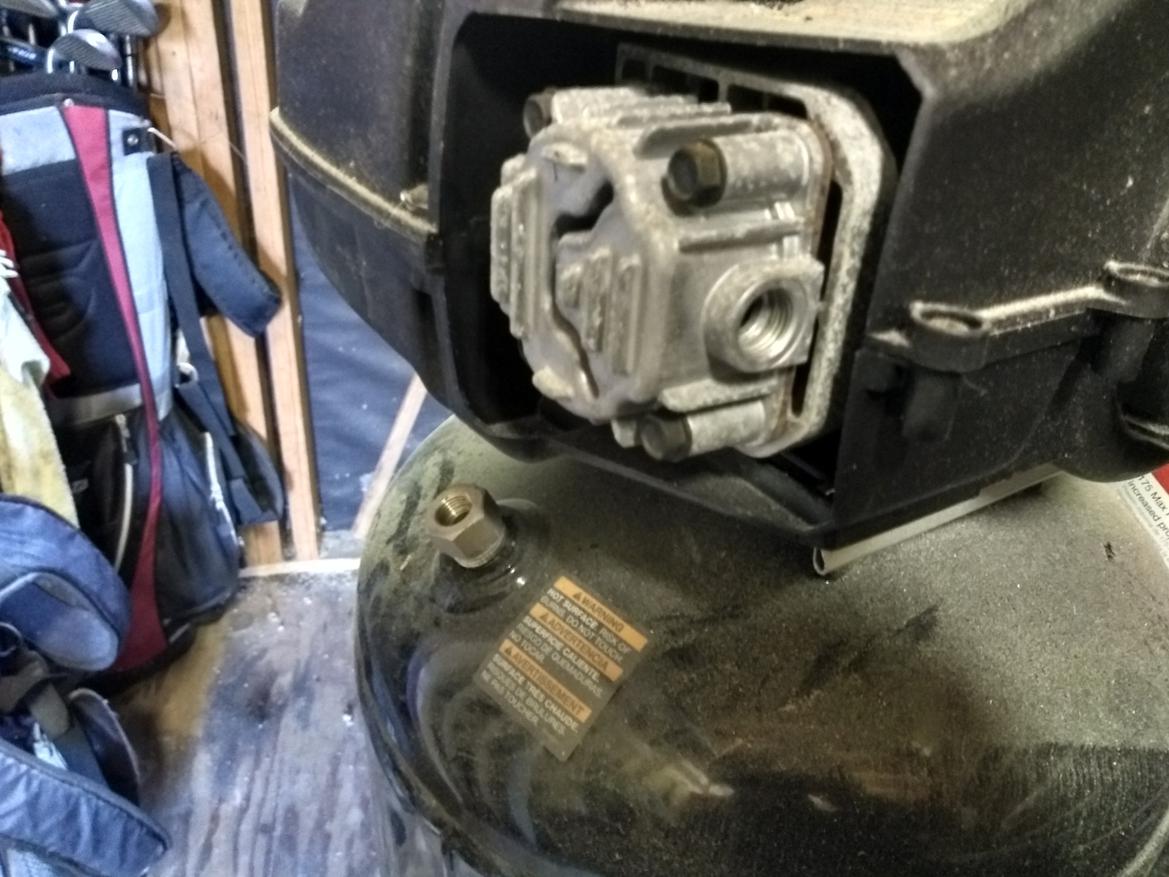
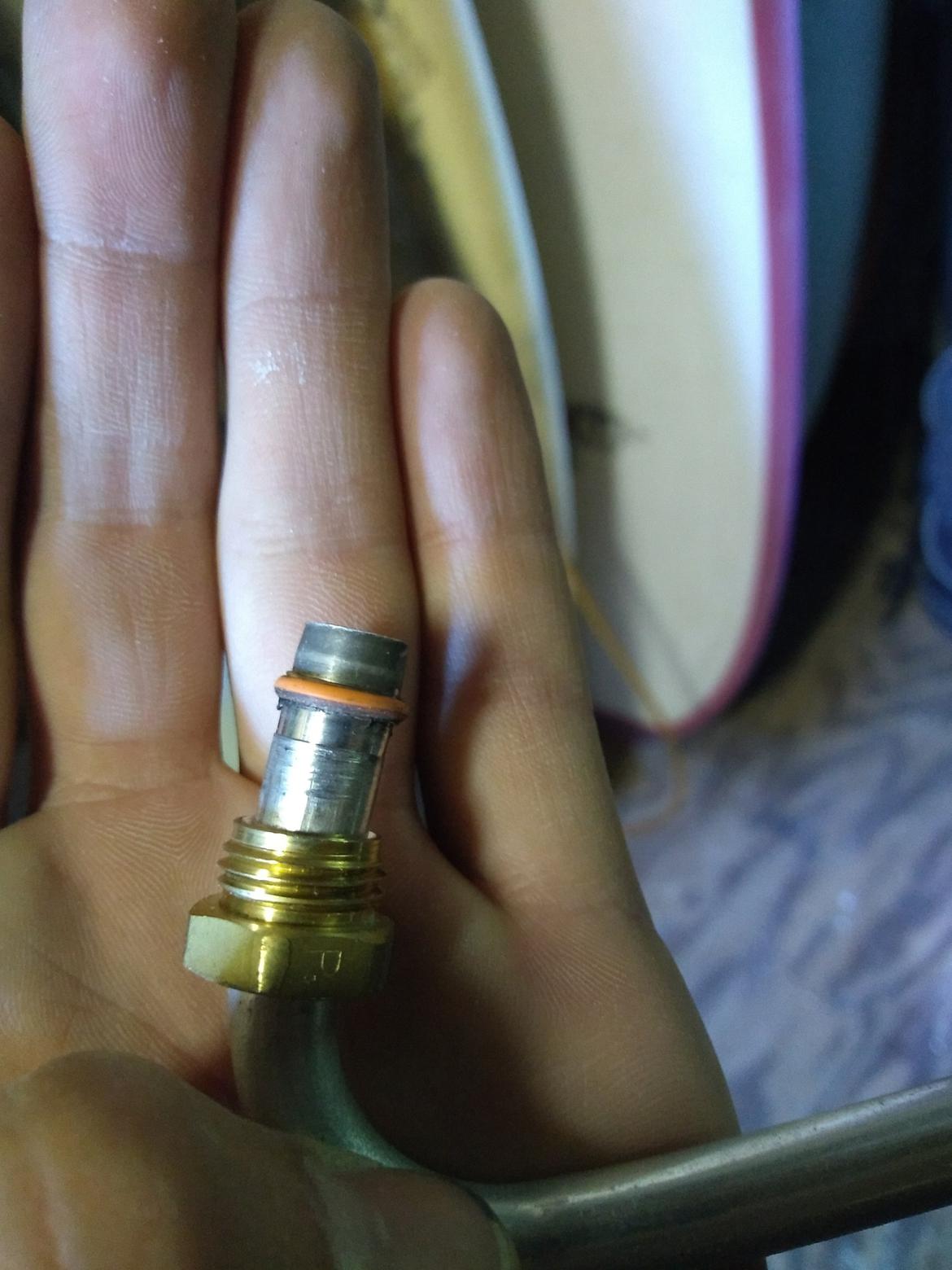
84FSP
UltraDork
5/14/21 7:14 p.m.
I'd hit a hydraulic shop and have them make you up replacement upgraded lines. It will be hilariously cheap and likely made while you wait.
Is it blowing the o-ring or the whole line? If it's just the o-ring, I would try another one, possibly from a hydraulic shop. My cheapo task force is similar but has ferrell's instead of o-rings. Maybe you can adapt to that style.
I fixed my old harbor freight compressor with some fuel line
I would pull the fitting out of the tank and replace it with something else. NPT to inverted flare? Maybe NPT to compression? If the fitting keeps failing, just replace it with your favorite flavor or something different.
Is it blowing out the o-ring (I assume not the line; that would be extreme) at the tank end, or at the head end? Nothing special about compressor lines... just had to be something to hold against what is , for fittings) fairly low pressure.
I see (I think) that the head end has the threads made into the aluminum, so hopefully it's the tank end! Just replace that fitting with just about anything, and I imagine the line itself is aluminum, so can be turned into what ever fitting you decide to use.
wow. That took longer to type, than it would for me to put a new type of fitting on there!
You in NC or out west these days? I've got a friend in fuquay could fix ya right up!
if it's the aluminum head end, I have some answers, as well, but the easy button will be if it's the fitting in the tank end.
im a fan of Swedglok brand fittings- a type of compression fitting. Outrageous expensive at fastenall, but can be found online reasonable
The tank side appears to be easy because it's got the NPT adapter. I don't recognize the fitting on the head to know how I could seal anything to it.
If that's all hardline between the compressor and tank, I think I see why it is failing. The O-ring is on the hardline, not the nut, so vibration pushing and pulling on the junction is working the O-ring.
I'm struggling to figure out what the nut tightens against. Does the O-ring just float on the line? If so, WOW that's a bad idea.
If the nut actually tightens something that holds the hardline in place, I'd cut the line short at both ends and connect the two with rubber hose. If the hardline just floats in there, I'd graunch some NPT threads in the compressor...
The line has a groove cut in it to locate the oring. The only thing holding the hardline in place is the od of the oring against the id of the nut. Horrid design.
What size is the tube?
I wonder if you could stick a flange on it, like quick disconnect on a fuel line has, to hold the O-ring and give something for the nut to tighten against.
I have a feeling it's a lot larger than 3/8", though.
Honsch
Reader
5/15/21 6:05 p.m.
If the nut actually tightens something that holds the hardline in place, I'd cut the line short at both ends and connect the two with rubber hose.
Rubber hose won't last. The air coming directly out of the head will be HOT which is why it was a metal tube from the manufacturer,
Tap the head for pipe and use a proper metal compression fitting. Make sure the tube is supported for damping the vibes.
Honsch said:
If the nut actually tightens something that holds the hardline in place, I'd cut the line short at both ends and connect the two with rubber hose.
Rubber hose won't last. The air coming directly out of the head will be HOT which is why it was a metal tube from the manufacturer,
Erk, good point. Hose is usually only rated to 250F and that'd be pushing it.
Swedglock 3/8 OD tube to 1/4 MNPT
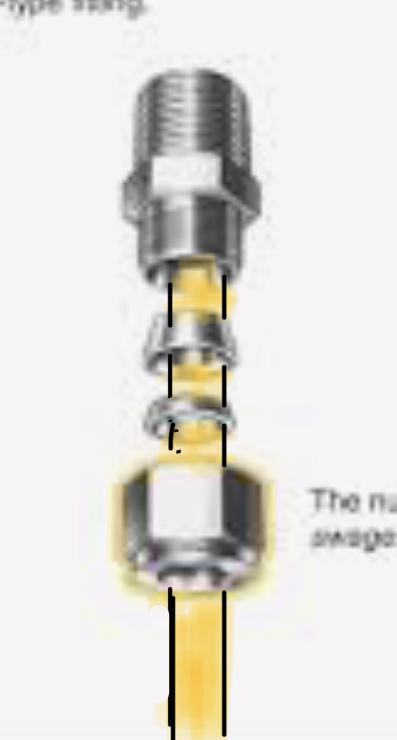
mid only the tank end is leaking, and is either 3/8 or 1/2 inch OD, one of Swedglock's fittings added to that one end will work. Or a fitting style you like. The aluminum head end, as was suggested, tap the hole to whatever pipe thread works, and use a firing in both ends. Then you can add a double loop, for strain reliever and cooling
In reply to buzzboy :
Re: tapping the compressor head in NPT.
What is the OD of the brass nut threads in the 2nd pic of original post? That could determine what tap drill/ NPT tap size if feasible. That is, if you are so inclined to that.
In reply to 03Panther :
+1 on Swagelok fittings as they have a high tolerance for vibration. I’ve had 30+ years experience with that product but I’ve never seen it used with aluminum tube. The fitting material is mainly 316 stainless and I’ve seen it used widely with “poly flow” plastic tubing with typical working pressures up to around 200 psi. It might work with aluminum, I’ve just never seen it.
I spent some time rooting through the bins at Napa. I don't know what these fittings are but they fit the threads (9/16 18th) and seal with an o-ring but they're too long to engage the o-ring. I'm thinking it's a possibility if I cut the threads down?
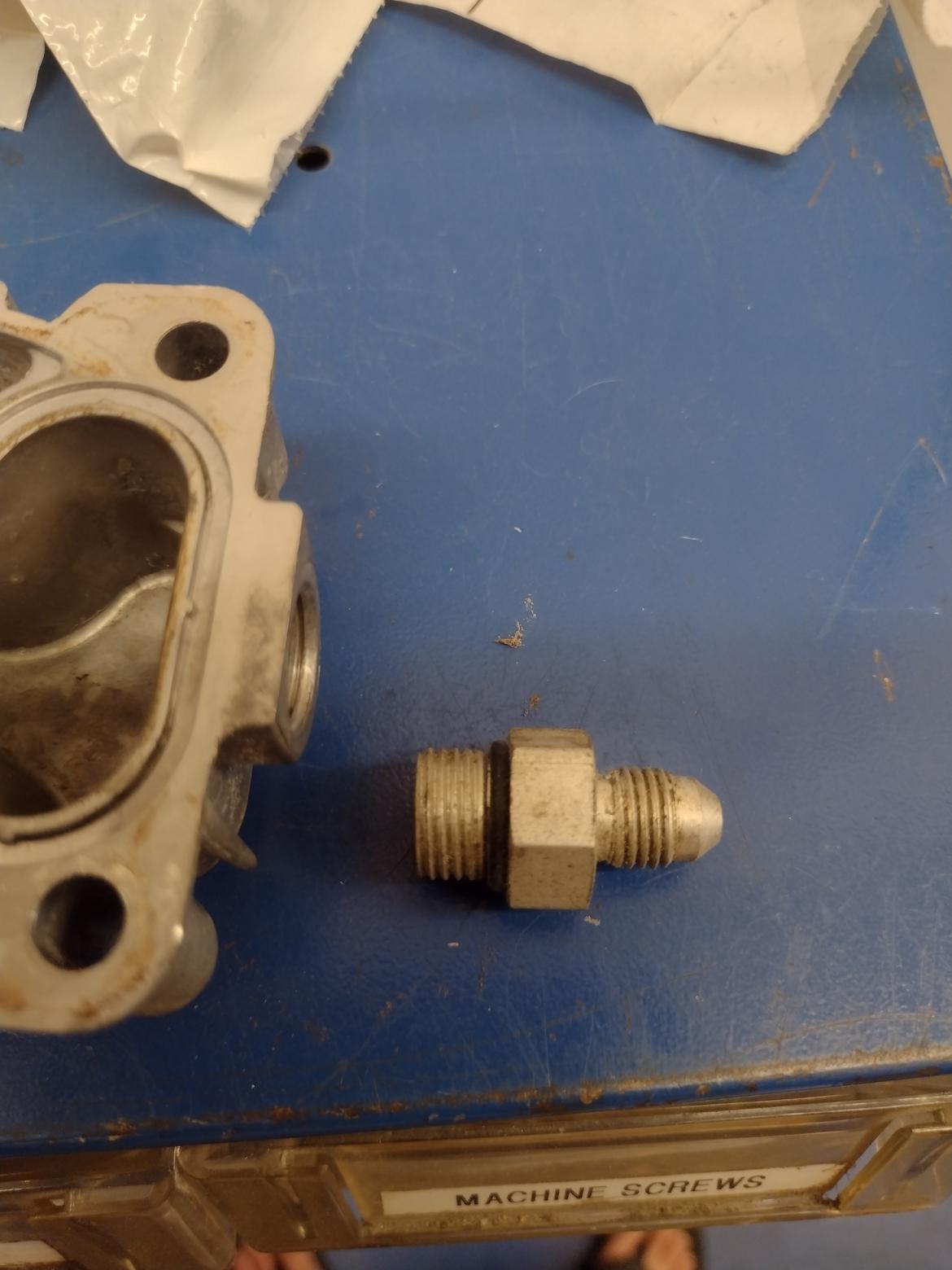
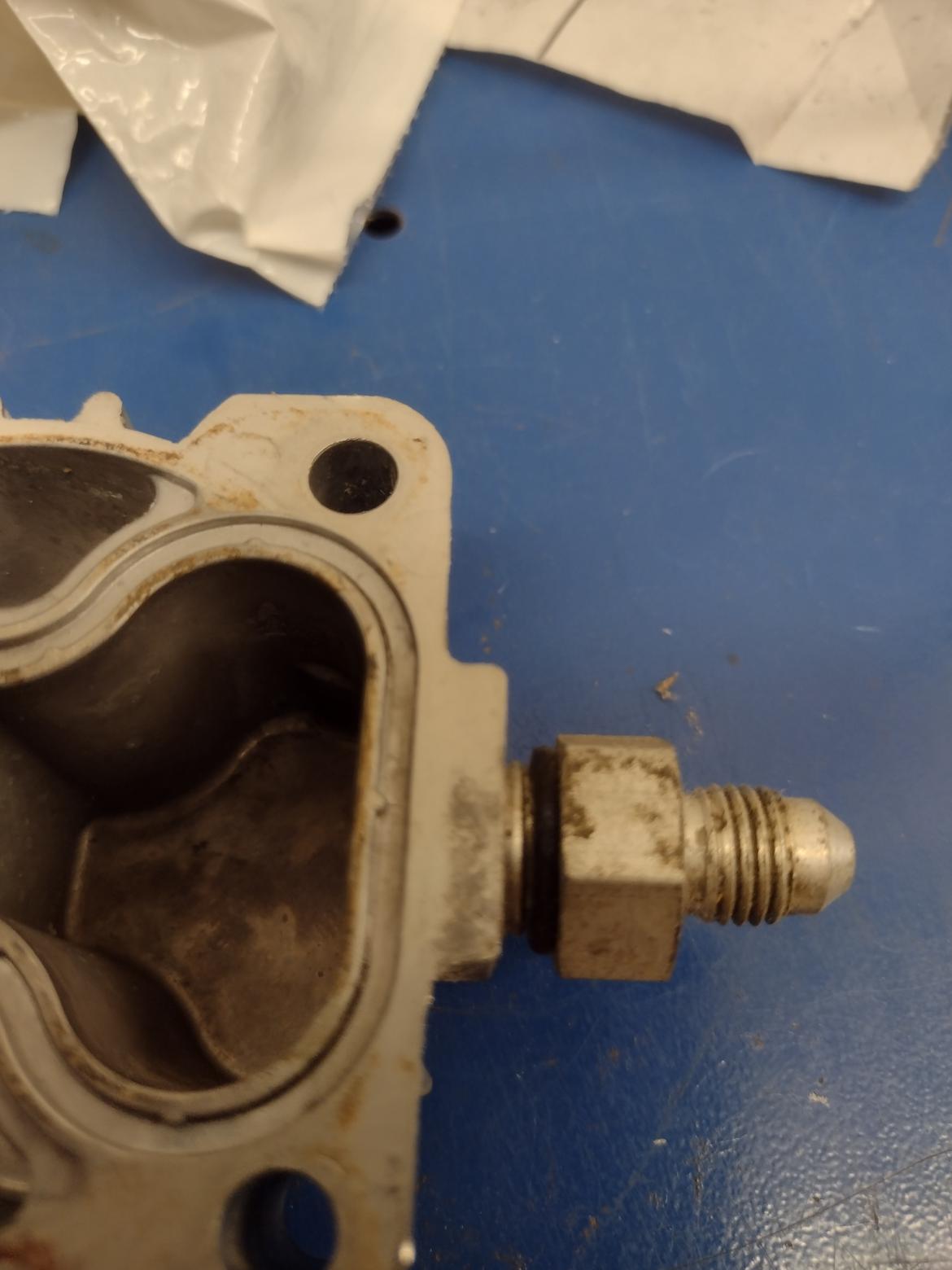
The hydraulic guy at Napa was off today. I might go pick his brain tomorrow
Hell yea, cut the threads. It looks like there's a nice bevel to capture the O-ring.