330 E46 for track use only. Putting E36 manifolds on it, and from there deciding between 3 choices:
A.) Cobble something together myself (I have a 3"in/3" out Magnaflow muffler on the shelf) using a handful of 180* bends cut/clocked to make what I need. Have never done an entire exhaust this way, and figure I'll be into it for $3-400 worth of material when it's said and done. Kind of want to try it to see how bad I do.
A.1) buy BimmerWorld/Magnaflow Y-pipe, fab from there back. That feels easier, but doubles the price.
B.) Drop at muffler shop. Don't want to spend the money at a "fab" shop, so thinking that's $500-700, and isn't great quality, but is definitely easier than me doing it.
C.) Buy the entire BW/Magnaflow Spec E46 Y-pipe/exhaust. $1300+ tax+shipping. Not planning to race this car W2W in next couple of years, so don't need this system for anything other than it works with the E36 headers I plan to use. Have read less than positive comments about fitment, which is not the end of the world for "racecar", but that's a lot of money to spend on something that sounds like it's a decent chance might rub on something.
Appreciate any insight or words of wisdom on the topic. Or if there's an archived GRM "Roll your own exhaust" article, love to read it.
I definitely would not go with a "muffler shop". Pinch bends, crappy welds, poor materials, no thanks.
Personally I don't think I'd want to try to fabricate a Y-pipe for my first time doing a DIY exhaust. Fitting the parts together is important for getting a good weld, and that sounds hard.
So I'd go with A.1 or C.
I have a Bimmerworld exhaust on my E46 M3. The center Magnaflow resonator exploded after a dozen or so days at the track, and the race shop who maintains my car welded in a Borla replacement. Other than that it's been fine.
All are fine options, the choice should be based on your comfort with fabrication vs. handing out stacks of cash.
If you're worried about the fitment of off-the-shelf options and want to try cobbling together something yourself, that way you could be sure of the fitment...or at least you won't have to worry about looking at the OTS exhaust and thinking "I could have built that better myself."
I took option B with my AE92, I dropped the car with headers + downpipe + new mufflers at a midrange exhaust shop (edit: didn't do crush bends but not mandrel, it was an in-between option that makes smooth bends and only slightly reduces the radius, don't remember what it's called). It wasn't cheap but I've been pleased with the results.
My Toyobaru came with a full aftermarket OTS exhaust that I've also been happy with, and considering it came with a nicely priced car it was a pretty good deal 
On multiple cars, I dropped the car off at the muffler shop with the premade mandrel bends and had them cut and weld them into place. The end result came out great and was inexpensive.
I'd recommend some slip fit radius of various degrees (90, 45, 30 deg) in the diameter you want from Summit or something. And get couplings too, for joining non slip fit ends.
That way you can lay it up, tack it, get the fitment and routing done quickly, and then just weld it up.
I've done it a couple times using non-slip fit ends, on my back, trying to mark it, tack it, check it, etc, and it takes lots of needless extra time.
Summit sells entire DIY "generic" kits with various radii and straight sections, might be as cost effective as piece parting it.
So you don't have an option where you live to have a good shop fab up something for you? If you were in SE MI, I would tell you to go to Watson Engineering and let them do it. While there, you can check out all of the race cars they are making ford and maybe even see a prototype being worked on.
All are reasonable. If working with a muffler shop make sure your expectations are clear. I had one do some work on our Bentra and I'm surprised exhaust could even find its way out of the pipe it was so restrictive.
The hardest part of making your own is measuring where to cut the bends. I made some 3d printed pieces to help do that when I last made and exhaust and it was a game changer. I posted them here somewhere, but the idea is simple and you could easily make some of your own. I highly highly suggest doing that before starting, if you go with that route.
I did Option A on my E28 with the car up on jack stands in the garage when I bought a set of headers for it. I'm pretty comfortable with welding and fabrication but space limits the tools on hand so I was mostly using angle grinders to do my cuts and prep. The job definitely took longer than I was expecting it too (a couple of weeks) so if you are going this way make sure to budget enough time.
What I like about the system I put together though is how easy it is to remove to get at other things on the car. A few well place V-bands means once the car is up the in the air the exhaust can be removed up to the headers in a few minutes in chunks that are easy to manage/hang by myself.
Came here to say exactly what adam525i said. I've made several exhausts out of mandrel bends and welded it up myself. A band saw helps, getting a nice cut perfectly perpendicular to the pipe can be a challenge with an angle grinder, and being off just a small amount quickly results in gaps that aren't great to weld.
A single exhaust is a full day in the garage. A dual is a couple solid days. But even the first exhaust I made this way was nicer than any that I ever paid an average-priced shop to make. Obviously you can pay as much as you want to get nice results, just depends on how valuable your time is to you.
I will add one comment to the V band suggestion - get the piloted ones. Makes it a lot easier to get them lined up and not leaking.
Also, weld the pipes and flanges like you're doing sheet metal, careful not to get anything too hot. It's amazing how much a little warping can tweak a system, and how much it can make a flange leak. The first exhaust I did I tacked the whole thing, pulled it off the car, and finish welded the whole thing. It didn't line up all after that, I had to cut and re-weld stuff to account for warping. Now I fully weld each bend as I go, starting at the headers with the muffler hanging in its mounts where I want it to sit at the other end.
Do it yourself. It will be an excellent learning exercise and you'll be able to do the fitup exactly right. You can get inexpensiveish kits to help you do the fitup; in fact, I seem to remember one for sale here not long ago.
You'll definitely want a quality vertical bandsaw. TIG would be the preferred welding process for heat control; don't forget to back-purge your work!
ProDarwin said:
All are reasonable. If working with a muffler shop make sure your expectations are clear. I had one do some work on our Bentra and I'm surprised exhaust could even find its way out of the pipe it was so restrictive.
The hardest part of making your own is measuring where to cut the bends. I made some 3d printed pieces to help do that when I last made and exhaust and it was a game changer. I posted them here somewhere, but the idea is simple and you could easily make some of your own. I highly highly suggest doing that before starting, if you go with that route.
If you use some of the shorter elbows (mandrel bent) from Summit, you just need to figure where in space to put the bends, that's fairly easy.
In the screen shot below, for a 2.5" exhaust I picked 2 of a 30, 45, 90, and 4ft pieces of tubing, plus a y pipe with two 1.875 inlets to one 2.5 outlet, for $285. If you sized up to 3" it goes up a little.
Aluminized tubing except for a couple stainless pieces, so if you go all stainless it goes up a bit more, so the $3-400 figure above is about right.
And I picked stuff with slip fit ends, so you mock it up, twist a little this way, slide a little that way, tack it, and weld the sections side to side in equal amounts, done.
Next exhaust I build, this is how I'm doing it.
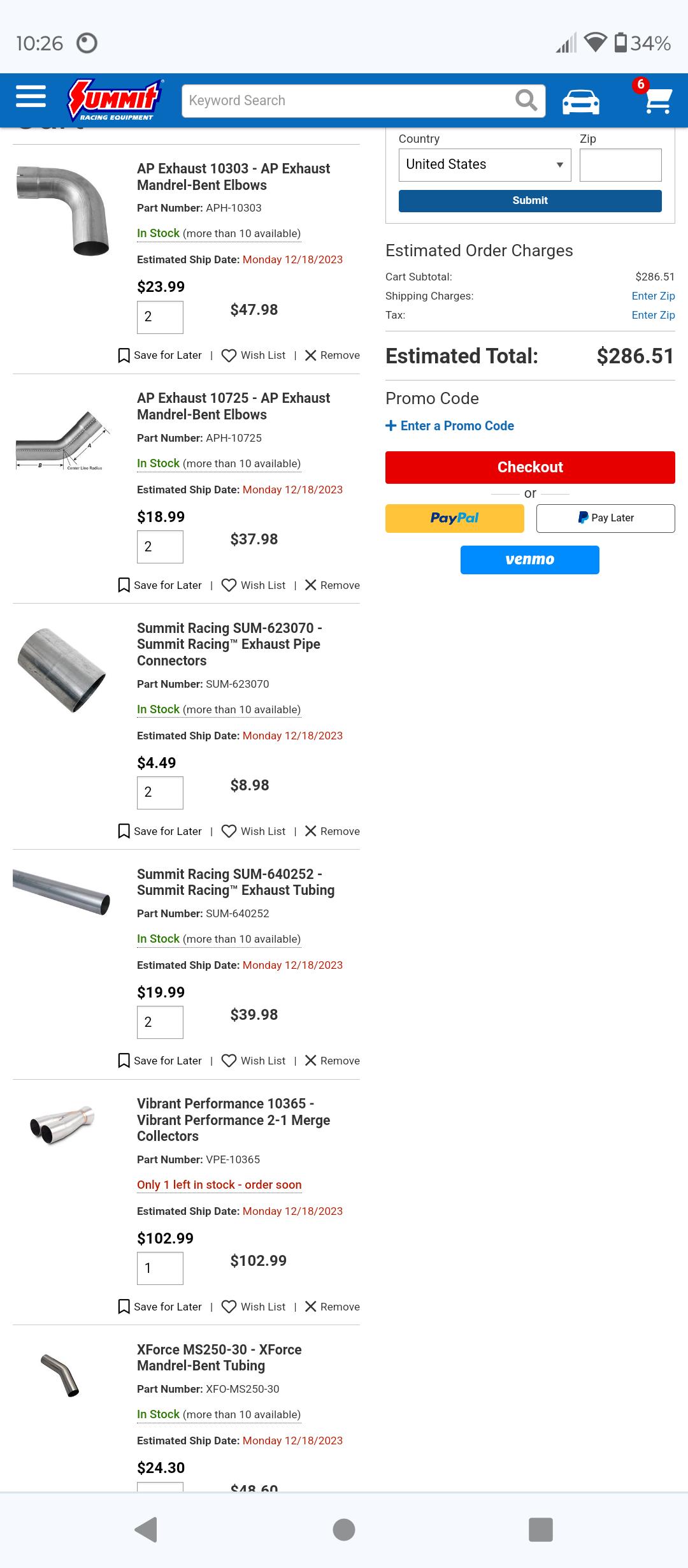
Rodan
UltraDork
12/16/23 8:02 a.m.
Definitely roll your own...
adam525i and GearheadE30 already hit the high points, but I'll just emphasize how nice it is to have the exhaust joints where you want them. Also makes it easy to set up a different muffler setup for noise restricted tracks if necessary.
Also, as noted above, a bandsaw works far better than a cutoff wheel for exhaust stuff. Summit/Jegs are great sources for the materials and almost everything you'll need is pre-made unless you have to fabricate some strange y-connector or something. I prefer the raw piping to aluminized.
Thanks for all the great comments. I looked yesterday and Jegs had a "kit" with like 4 each of various bends and straights. Looked like it was setup to do duals, so if we played it right a buddy and I could split it and end up with most of what we'd need to do two single e46 exhausts. Leaning towards buying the Y-pipe, then fabbing from there.
I have a two post lift, a mig machine and a portaband, but I swear the straighter I try to cut with it, the further it berkeleys off of the line I'm following. It's lived a hard life: spent 4 solid weeks in the hands of a "carpenter" cutting off 1-1/2" diameter threaded tension bars coated in concrete. Might use this as my excuse to buy another.
I'd figured on going with aluminized, unless there's a compelling reason to go with raw?
alfadriver said:
So you don't have an option where you live to have a good shop fab up something for you? If you were in SE MI, I would tell you to go to Watson Engineering and let them do it. While there, you can check out all of the race cars they are making ford and maybe even see a prototype being worked on.
I do. My logic is that I assume the cost of good fab shop would creep up close to BW/Magnaflow option, and I'd rather buy that at that price point so I'd be "legal" for spec E46 should that be a pursuit with this car down the road. I've stuck within the rules as far as getting the MCS setup and a 3.46 diff, so trying to keep my options open to eventually running that class. Plus it just seems like a good recipe for a track 330 e46.
Go pick yourself up an inexpensive bandsaw on CL or FB and spend a few bucks on a good quality metal cutting blade for it. Saws can be bought for $100-150 and a good quality blade for under $50. Most of the saws you will find are for wood and spin too fast for metal cutting, but with a good blade can do a good job.
This is what I meant earlier:
https://grassrootsmotorsports.com/forum/grm/learn-me-exhaust-fabrication/136560/page1/
https://grabcad.com/library/exhaust-bend-sections-1
ProDarwin said:
In use: trying to get the bend right after the header tight to keep the exhaust tucked as high as possible (because rallyx). Last exhaust dipped below the crossmember a bit and got smashed to bits.
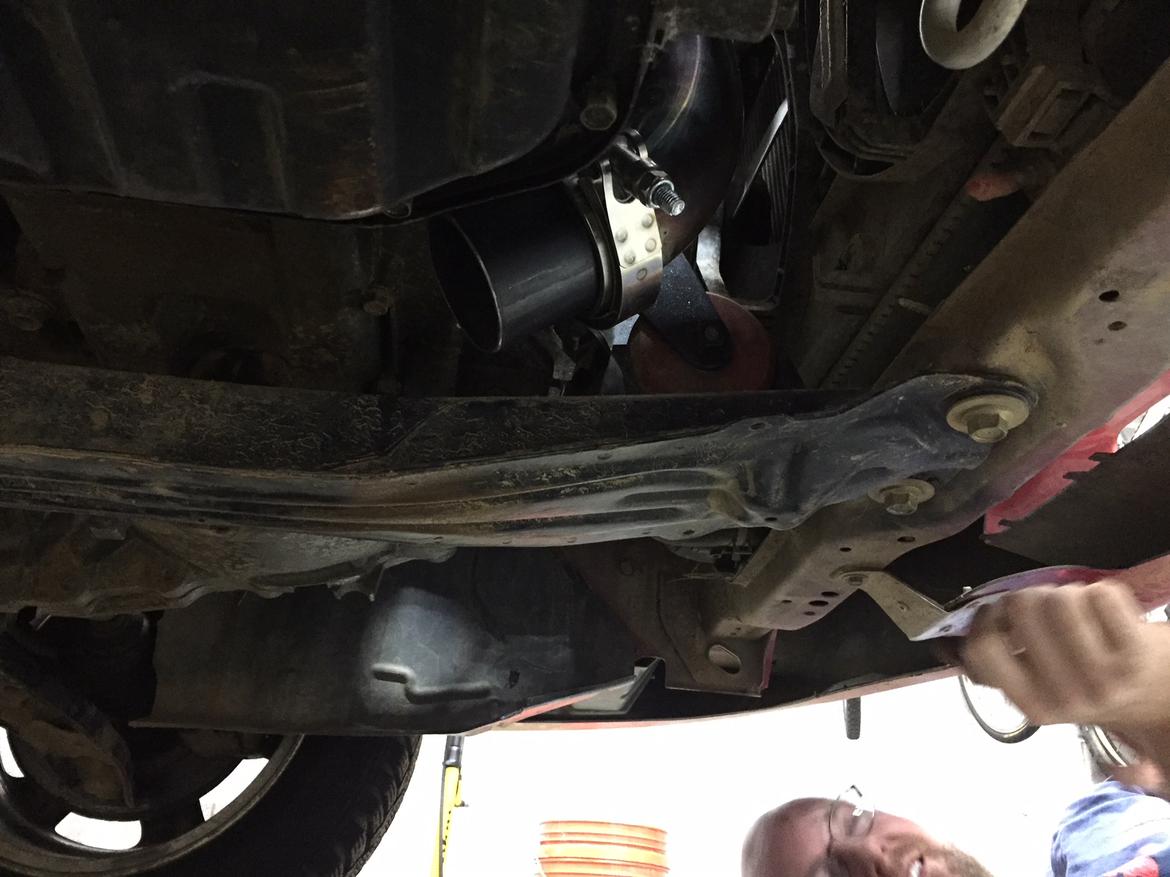
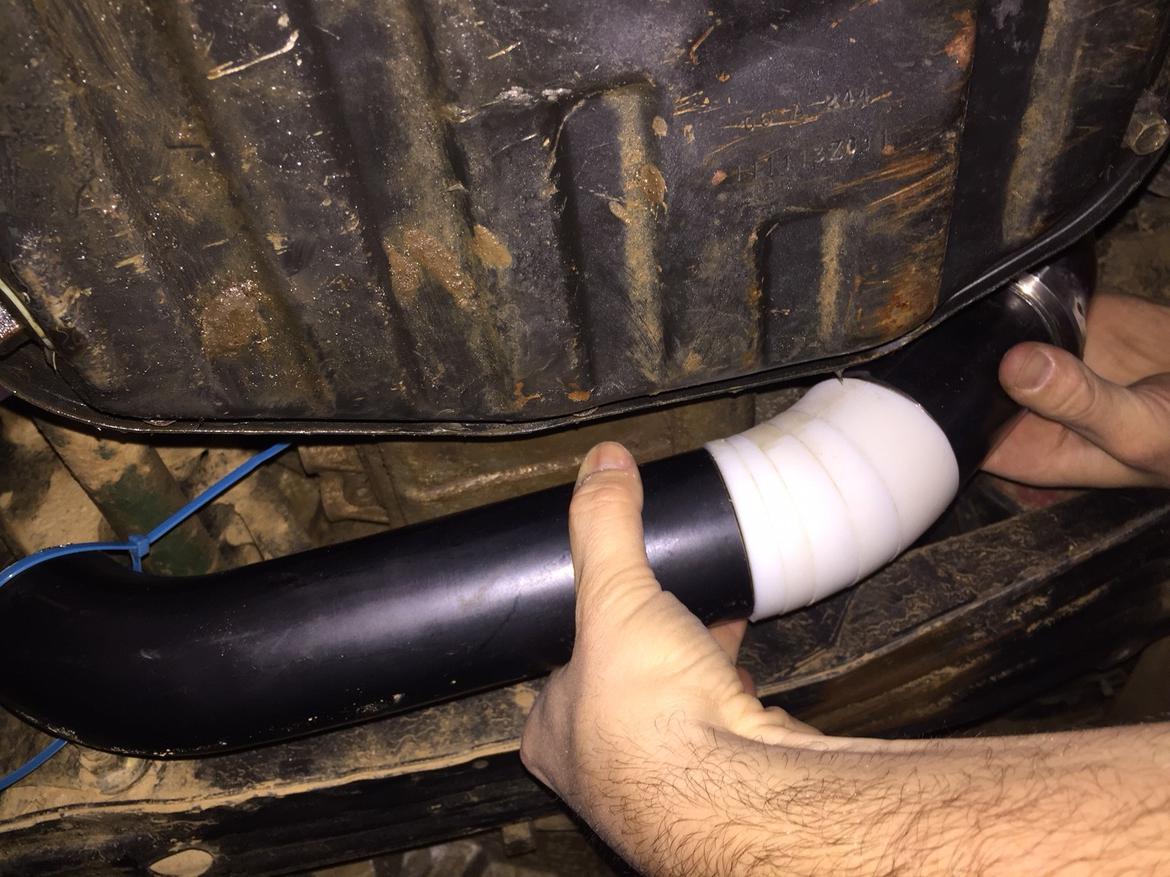
FWIW, I used a cutoff wheel chop saw thing from HF, I didn't have a bandsaw.
I once did the "muffler shop" option and had good luck with a car that needed a large exhaust with pretty tricky routing. Bought mandrel bends and some other bits to them and it worked out really well, and way way cheaper than an off the shelf option. I spent a decent chunk of time calling around though to find a shop that would do it and seemingly do it right.
These days if there's a (track) proven off the shelf system I just use that. More expensive but being able to get it all done in an hour or two is priceless.
Rodan
UltraDork
12/16/23 11:36 a.m.
Spearfishin said:
I have a two post lift, a mig machine and a portaband, but I swear the straighter I try to cut with it, the further it berkeleys off of the line I'm following. It's lived a hard life: spent 4 solid weeks in the hands of a "carpenter" cutting off 1-1/2" diameter threaded tension bars coated in concrete. Might use this as my excuse to buy another.
Take a look at Swag Offroad for tables and vise mounting for portabands. Makes a huge difference in being able to get precise cuts.