My GoogleFoo and associated carbon fiber mold making links aren't providing any help with this question: Is there a covering I can apply to a porous surface to seal it up to make a mold from? The part I have is something I want to keep and not destroy in making my transfer mold. It is also porous and the surface texture does not lend itself to directly applied mold releases. I was thinking about food service sized saran wrap or packaging wrap and doing a few layers, but that doesn't seem to lend itself to being removed from the resultant mold. I also can't remake this part in a different material either due to its shape and size.
Any help or thoughts?
BAMF
Reader
5/6/12 9:14 a.m.
What kind of surface is this? I've heard of people putting a thin layer of molten wax on things and smoothing them out. Then again, depending on what the original is, hot wax may not pass the removal test.
oldtin
SuperDork
5/6/12 10:53 a.m.
brushable latex? probably would need to build up a couple of layers.
You can use a couple of layers of masking tape to keep fiberglass resin from getting through. Do each layer in apposing directions. You may have small lines from the tape, but should keep it safe. YMMV, test on small piece first.
No ideas on chemical reactivity, but PlastiDip may be easily removable, depending on how porous the surface is.
Hal
Dork
5/6/12 11:23 a.m.
You might try the plastic wrap and then coat it with mold release. That would protect the fiberboard and still provide the release.
I would try it on a sample first to make sure the plastic wrap and mold release don't interact adversely.
Molds are commonly made of cheap polyester resin with a layer or 2 of cloth to follow details and the bulk of the thickness and mechanical strength coming from a bunch of mat and roving. If your "plug" isn't a beautifully polished/painted/buffed object, you'll need to do that to the mold anyway - so...
Cover it with neatly fitted pieces of release ply? Cut the pieces to fit, lightly spray the backs w/ 3M 77, let it dry, then press them into place. Overlap them by 1/2" to an 1".
Lay up the first to layers of cloth and resin carefully, then pile on the mat/roving and resin.
Once it's cured hard, pop the plug out sand the whole thing, skim it with filler, sand it, skim, sand, skim...shoot it w/ hi-build primer, block it back.
Do you have the composites book by Forbes Aird and the West System book by the Gougeon Bros? If not, order them up.
What you want is POLYFLEX, it's the stuff that Dentists use to make molds of your teeth. Comes in a five gallon pail, it's a blue gel that you just scoop into a plastic bowl and microwave for a few minutes, until it melts down into a brush-able liquid.
Use a brush or squeegee, covers everything VERY smoothly, stays put for as long as you want, plus you can peal it off and reuse it time and time again. Nothing affects it.
In addition to being a perfect coating for mold making, this stuff is also GREAT for making molds themselves, of anything. Emblems, horn buttons, dash knobs, trim rings, anything. Rather than heating it into a liquid, just soften it to something like butter and spread it over anything at all, creates a mold in seconds. Use it and toss it back into the tub with the rest and use it again.
Luck,TC
In reply to Ranger50:
OK. We used to use butcher's wax, you know, the stuff folks wax floors with. We'd use it to seal plaster plugs and such when pulling direct molds or when making negative molds from plaster fixtures. Use a little alcohol to make it more fluid and brush it on, or warm it up (careful, it will burn!). It will wash off with alcohol, but it's tough to get out of the pores. I learned reproductive mold making techniques from the master mold makers at the Metropolitan Museum of Art. We bought butchers wax by the case.
With helper(s), lay industrial sized piece of 'saran wrap' over the piece, folding and sealing the excess under the edges. Try to avoid any punctures or tears. Can use a hair dryer to shrink and adhere the edges.
Run a small rubber/vinyl tube under the wrap at an edge, taping as needed to seal, then apply vac to shrink the wrap to the inner surface.
Use a soft brush to eliminate wrinkles/folds, starting in the center and working out towards the edges.
Once the wrap is in place and smooth, apply the release and plug material of your choice (some excellent suggestions so far), remembering to add reinforcement to help maintain the desired plug mold shape, and perhaps a handle to help manipulate it easily.
Once the plug material has set, remove the vac, remove the plug mold, remove the wrap, and your original is unharmed.
We make a lot of temp molds here at work. We lay-up vinlyester resin fiberglass resin on them (either by hand or chop spray).
We use a lot of packing tape to cover them. Also shrink wrap/packing tape combos. You can use mold release wax on top of that.
I used aluminum foil and packing tape on my foam mold, followed by wax.
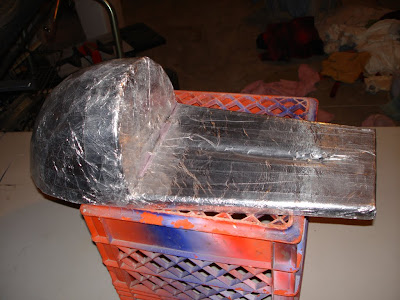