https://www.youtube.com/embed/EvD9C_0F6II
The ability to fabricate parts opens up a whole new world of potential for working on project cars–but only if you do it right.
Here are five of our favorite fabrication tips and tricks to make your project a success.
Presented by CRC Industries.
Watch more videos
Always file, round corners, and de-sharpen metal edges from cutting. Sure it takes a few minutes, but you'll be glad your piece of metal won't cut you from a razor sharp edge as you install it, or later on when you re-work on the car.
Buy a drill press. You'll be glad you did, in fact you may even say 'Why didn't I buy this sooner'. We've all used the hand drills too many times. Though a drill press takes up space and requires clamps and some setup.
Is one of the tips about checking your work?
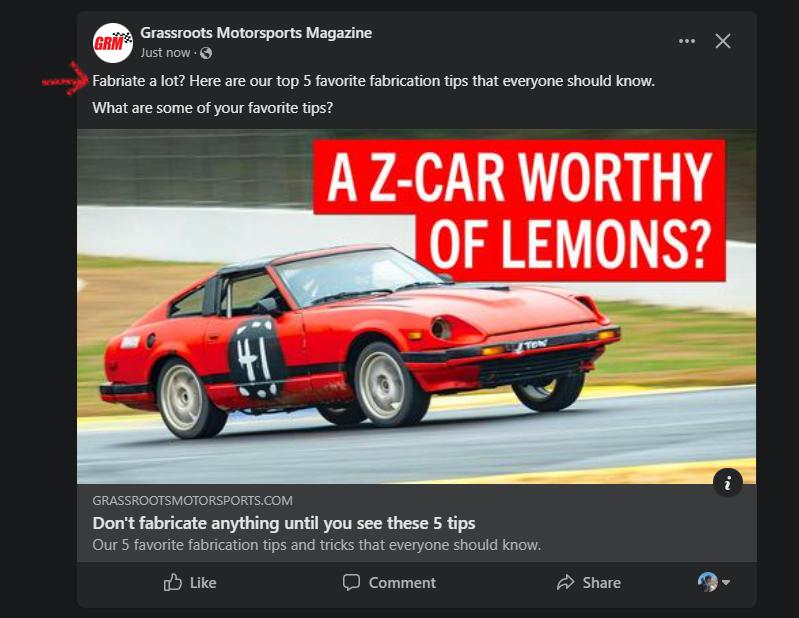
NOHOME
MegaDork
3/2/23 10:08 a.m.
When you fabricate with angle iron, try to finish the part so that it does not look like you made it from angle iron! Radius the edges and drill a few speed-holes. I love my belt sander and drill press for this kind of work.
A countersink bit to put a slight taper on the edge of a drilled hole makes a nicer finish and mayhap a bit of stress relief. If nothing else it takes the burr of the edges.
Learn to think in three dimensions. A piece of square tube can be carved into a finished part without the need to weld if you are clever. The finished part also tends to look more professional.
In reply to ¯\_(ツ)_/¯ :
We're just making sure you're paying attention ;-) Nevertheless, good advice. :-)
i love fabricating. it's no different than anything else...you can keep looking for another 0.01 second, or 0.001 inch.
regarding cutting angle or bar...
with a friction blade, cut as thin a cross section as practical.
with a hacksaw or bandsaw...using HSS...you want at least 3 teeth on the metal. so, 1/8 thick requires 24tpi. if your blade is coarser, rotate the part to get more contact with the teeth.
Carbide teeth will chip off if you cut thin pieces vertically. angle cuts best when the open face is down and the angle is up on a carbide chop saw. check your manual.
as noted, take the time to chamfer and deburr.
a pedestal grinder and pedestal wire wheel are good investments.
for those who started off in wood working, steel requires much more pressure to drill or saw...and low speefs. Higj speed and light pressure will just drag the cutting tips / Edge across the metal, heat it up, and make it dull instantly. the right pressure and speed common steel gives you nice curly-q pieces, with no blue (=overheating). cutting oil...not X oil...cutting oil..will make things easier. your tools will stay sharp longer. Splurge!
a drill press allows high pressure in a straight line. bits break when they bend. drilling by hand requires twisting your wrist to prevent bending the bit.
when get to point where you want to bend (.or un-bend) metal, you need heat. An oxyacetylene torch is your best friend. and rusty or stuck fasteners or parts will never be a problem again.
Evander
New Reader
5/19/24 7:57 p.m.
Mag drill holy cow do annular cutter work well
And or hydraulic hole cutters, this tool seconds for dimple dies