Hey All,
I've finally gotten a bottle for my MIG welder. Well, argon does not a welder make. 
After a failed "easy" Civic short shifter swap on my Metro I decided to cut and flip the ball on the stock shifter. Like this:
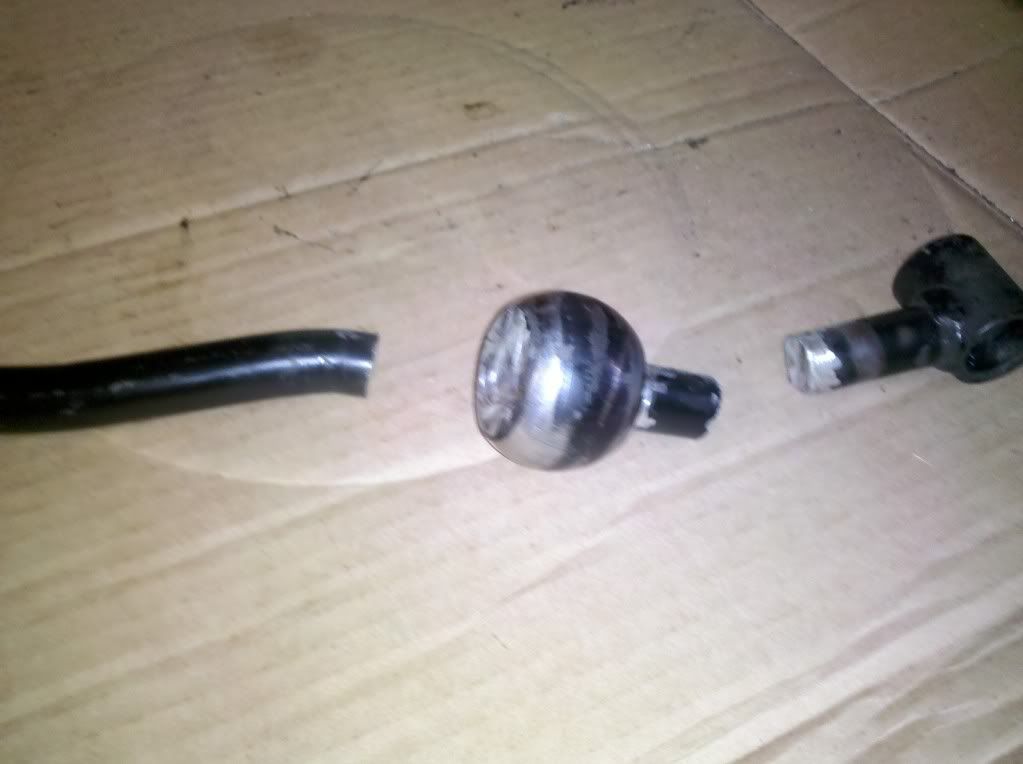
My bottom weld is strong like bull. The top half I broke off after a few pulls of the shifter.
I'm using a Handy MIG 101 Manufactured for Lincoln. I think the same unit is just branded Lincoln now. It's on a 15A circuit that should give me 65A out @ 16V, 15% Duty Cycle. I bought WA Alloy .030 wire and the argon the welding supply gave me. Welder has high/low heat range and min/max fine adjust. I welded it on High Heat and fine adjust to min, wire speed was on 4. Made my cut just like the pic but I barely got any penetration after seeing the break.
Do I need to shape the parts different? I have the tapered shield tip on should I used the squared off tip? Any help is appreciated.
Bruce
A 110V welder is rated for a max material thickness of 1/8" to 3/16" and you are trying to weld to what looks like a 1" solid steel ball. It simply won't have enough power to penetrate into that. You could try preheating the ball with a propane torch to gain a bit, but it really is a case of wrong tool for the job.
Preheat the ball end, shape the end of the shaft to a taper. and start filling it in with the welder. That is about the only way I can see it happening.
Do you have the polarity correct? If you had it set up for flux wire welding, that uses a reverse polarity as compared to gas welding. My Italian HF MIG has a picture inside for gas or no gas for the connections. Also, I would make sure to grind out a channel that you can fill in with weld.
I'm a rank amateur.
I run 80/20 argon/co2. Good advice above. Bevel and clean the cut before welding, high heat, and maybe up the feed speed. You should get a nice bacon frying sound when you weld.
I have a Lincoln 135 which is 120V Mig. Thick metal needs to be preheated to get the proper weld penetration. MAPP or propane with a turbo head will generally do a decent job of preheating.
old_
Reader
8/10/14 1:06 p.m.
For sure you need to heavily bevel and make multiple passes.
Shouldn't be using straight argon, and like others said, bevel it
Switching to straight CO2 will get more heat into the material you are welding at the cost of an uglier weld but it is still beyond the limits of a small welder.
Can you drill into the ball and slip the shaft in 1/2" or more? Then a good preheat and weld a bead around it on your highest setting.
A decent mechanical connection will go a long way to making this work. You have a long lever and the joint is right at the fulcrum so it needs to be strong.
If I had to do this with the welder you have I wouldn't weld it at all. I would actually drill and tap the ball end, thread the shaft with a die and screw it in with red loctite.
Thanks guys, understand, heat my ball before I go at it.
Bevel and multiple passes.
Should I go around the joint with my weld or vertically up and down the shaft? Man, there's no way to ask that without setting myself up.
They gave me a bottle of 75/25. Guy was knowledgeable and helped me based on the work I was doing. I didnt tell him about the shifter which was a departure from the plan.
Leads were swapped for gas wire. Welder supply guy told me that when he sold me the wire.
Thanks!
I may wait until tomorrow and use the drill press at work to do like Ditchdigger suggested. I would still like a bit of angel on the shifter since I roll with the seat pretty far back.
Weld around the perimeter of your shaft. 
Well, damn. I guess this means I have to disassemble three shifters (Jensen, Jensenator and Abomination) that I have been using for a while 'cuz obviously 110v won't do da trick.
Oh, and let's not forget 6? or is it 8? inner tie rods along with some other stuff I can't recall at the moment.
Cut the stuff apart, bevel it. You want points touching in the middle. Use a magnet to hold them aligned, then burn the points together. Now work your way around, welding with the length of the stick not around it. You want to have the weld stick up or be 'proud' of the shaft, as the Limeys would say. Between passes, wire brush the E36 M3 out of the workpiece.
Then use a bench grinder to roughly level things out, the final smoothing works best with a die grinder and Roloc discs. 120 grit leaves a nice slick finish. Degrease and paint, reinstall, done.
NOHOME
SuperDork
8/10/14 8:14 p.m.
You need to bevel this like you were welding two pencils tip to tip. MIG does not have the penetration of a TIG. 110 will work fine, crank it on full and use as slow a wire feed as possible.
You need to turn the wire speed down and the amps up, go slow and dump lots of heat into it. Because its not structural it shouldn't need to be beveled unless you don't have clearance for a bead.
Bevel the parts and make multiple passes. Make certain that your gas flow is correct. Too much gas flow can create tubulence and allow atmospheric contamination leading to poor welds. Too little gas can do the same thing. A multipass rated wire will help but is not absolutely necessary on this type of job.
tuna55
UltimaDork
8/12/14 9:49 a.m.
As Pilot said, be sure your gas flow is correct. I also want to stress that while beveling to a point and welding a bazillion passes will ensure maximum penetration, it is not a requirement. It needs to be stronger than the shifter lever. I would bevel the first 1/4"-1/2" maybe and do that.
Also, as others have said, it should sizzle if you have the heat/speed combo about right. Make sure it's good and clean too, and don't die by using the wrong brake cleaner to do it.
http://www.lincolnelectric.com/assets/global/Products/Consumable_MIGGMAWWires-SuperArc-SuperArcL-56/c4200.pdf
The Lincoln Electric site has some very good educational material. The link above is to their GMAW (MIG) guide. I hope that it helps.
As Tuna states, a 1/4" bevel should be plenty.
Thanks for all the tips. I'm still trying to get to the welding, we've had company for the last week and my boy is having his tonsils removed today.
As for gas flow, I only have a single gauge with the valve only the bottle. It was what my buddy was using before he sold it to me. Should I get a new regulator?
Grind a taper the end of the shaft where you want to weld to the ball to make a groove. Tack it in 3 places. Turn the heat all the way up point the wire into the ball (thicker material) as you push it - then move it side to side to fill the groove. Let it cool. Now do the same around on the shaft working back toward the ball until you have the original shaft diameter.
So... basically two passes where you direct the heat into the part and lap the weld material together. Find some similar round stock to practice butt welding two tapers together first to get the wire speed right or you will goober it up with way too much material.
A "more better" way would be to drill the ball and insert a stud (drill into the side too and plug weld it or just thread it into the ball) then use a sleeve of tubing slipped over both to join the shaft to the stud.
Mr Snorklewacker's advice is good.
I don't think that you need a new regulator. You should have 2 gauges on your regulator. A gauge to show the pressure in the tank and a gauge (flow meter) to set the cubic feet per hour. 25-30 cfh is a good place to start. Pages 12 and 28 in the Lincoln GMAW guide give some good information on gas types, how they affect the weld and gas flow. Straight argon gives deep penetration but can have excessive undercut. The next time you get gas try 75/25 (75% argon 25% carbon dioxide)
admc58
Reader
8/14/14 5:55 p.m.
I had to drop to a smaller wire to get enough heat to weld larger materials. It made a huge difference in weld penetration.
Well, after several attempts again yesterday with a torch, with more taper and all bits being super clean I failed to get ANY penetration. Hey, I tried. If I had been working on this thing at an hourly rate, I'd have been deep in the hole. I took it to a buddy and for the cost of 6 pack it was done. Way too much time spent for a shifter.
I'm gonna have someone with more experience take a look at my setup. If it all checks out I'm gonna just start practicing until I can get a good weld going the majority of the time.
I am wondering if there is an issue with your setup. I have a Lincoln 140 110volt units and it has all the heat I need to weld together 1/2" plate. Proper prep is key and having a plan of attach is also critical to welding large pieces but with some practice it becomes simple.
Just as others have said bevel the joint and make multiple passes. I have welded up new control arms for expeditions using the OE bushing mounts welded to new tube steel that replaces the OE stamped things that rust out to nothing. uupper and lower) and a host of other suspension things. THe real key is to get that sizzling bacon sound AND I have found that you need more heat and slower wire speed than you think with larger pieces at the start but as you get in to it you can turn up the wire speed a little as you put heat in to the item you are welding.
Lastly once you start to "get it" you can tell when a weld is going wrong with in a second or three and make the needed corections.
The biggest thing that I try and explain to others when welding is that you can see the penetration of the weld occurring almost instantly. You see the item being welded start to melt and this melted metal combines with the melted filler rod / welding wire. If you see this you are doing it rite. If you are just laying molten metal on top of the parts you are welding together sticking them together like you would be if you were using epoxy it will be a very week weld. Another way to explain it is the puddle that is created by the heat or arc should be %50 created by melting of the material you are welding and %50 created by the melting of the filler wire. This is the hardest thing to learn about welding and it is effected by wire speed and heat but it is equally "controlled" buy the arc distance how far you hold the filler wire from the weld and by how fast you move your hand along the weld. This is where the skill in welding is and why everyone can not just pick up a welder and weld and it is also why a welder set to one wire speed and one heat setting probably will not be optimal for another person welding the same thing.
IT took me 5 minutes to learn how to stick metal together with a welder it took MANY MANY hours to learn how to weld metal with my welder.
Thanks to all and I'm continuing to apply everything you guys have said. I've read thru all the posts multiple times.
I have had an inch or two if success this week and that alone makes me want to keep on truckin'. Here is tonight's weld. Chrome eBay resonator to 14ga aluminized pipe that's been on the car for who knows how long. Didn't get ANY good sizzle until I pulled it off the car and ground the joint down. Then I think I had feed too high and me too slow. Then there were times that I felt the opposite. Either way I'm using max heat, max fine to get my sizzle. Please take a look and let me have your criticism.
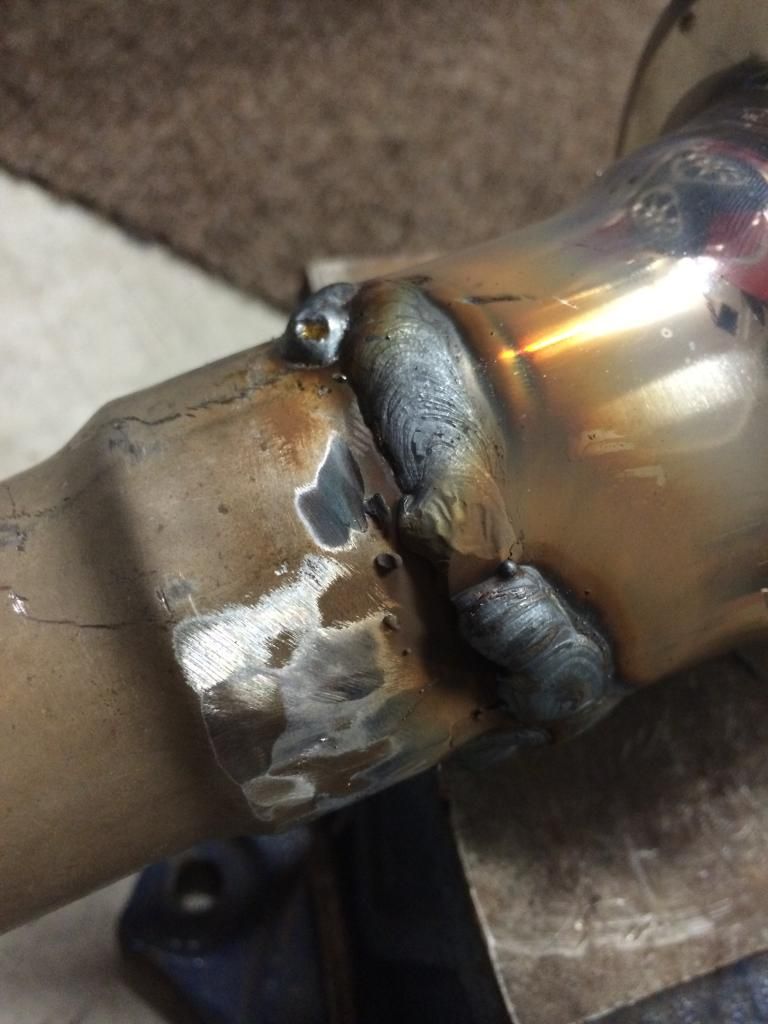
Also, do I do little circles, figure 8's or the ol' back and forth?!? Just curious how you guys manage the puddle.
I also think my cheap Northern Tool welding helmet isn't working quite right. I can't see anything but the weld. I'm having to guess where the joint is. Next purchase helmet!