In reply to VWguyBruce:
You have the shade two or three steps too dark. Remember they all have the same UV protection, the darkness is just a brightness thing. Weld arc should appear bright enough that you can easily see your puddle and everything around it.
NOHOME
SuperDork
9/7/14 6:31 a.m.
I seen to recall that if you convert from flux core to gas, you need to reverse the polarity by swapping the ground and torch lead positions. With Gas, the torch will be +DC and the ground clamp will be ground. With Flux core, the torch is the ground and the clamp is the + electrode.
Exhaust weld looks pretty decent. When doing thin stuff, I like to do a series of tack welds, not doing another until the last is no longer glowing through the hood. With practice, you can get the stack of dimes look pretty easily with this method. Use a good bit of heat, middle ground on wire speed, and above all, patience. Welding beads is for thick stuff that is tacked, or clamped in place. I agree with the consensus on the shifter - taper, lots of heat. For the record, I am a certified weldor , and I am humbled by a lot of the skill I see on this site.
BTW, look at a "professional" muffler shop's work some time. You.re doing fine.
Yep, NOHOME, I did swap the leads when I changed over.
Really appreciate the advice everyone. Welding a good bead is really satisfying. Reminds me of surfing, one GOOD wave is worth being out there all day.
Yeah, the exhaust weld looks pretty good and should hold fine. I do have one criticism of it: the upper weld has laid out 'flatter' than the lower weld. That can come from a few different things, one of which is trying to weld from the side or underneath, another is low heat.
Cold weld:
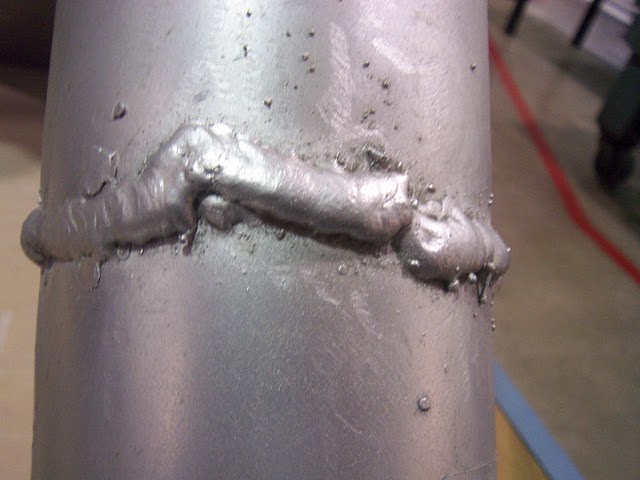
Notice how the bead looks like, no kidding, bird crap? It has no taper on the sides. That's because the base metal and the bead didn't get hot enough to fuse properly so the bead just sits on top. FWIW I recently saw a cold cage weld very similar to this which broke. I looked around the cage, saw a BUNCH of cold welds just like it.
The guy was saying the unibody was bent beyond repair and he was going to scrap the car, whew. I hope his next cage builder puts some more heat into it.
Good MIG on thin stuff:

Notice how the edge of the weld makes a smooth tapered transition into the base metal? That means everything got hot enough and fused.
If your work piece is vertical or upside down, keep in mind that the hot metal acts just like a liquid for a few seconds. That means yes gravity will pull down on your bead and can cause poor fusion. The best way to do it is to position your weld at the top or horizontally always, but of course that's not always practical. The trick is (and this takes practice, I'm still not there yet) to do such a weld in short sections, don't try to run, say, a 2" long bead on a roll cage tube all at once. I once tried that on some 1 3/4 .134 wall tubing, the damn stuff started to DRIP.
And yes tool snobs that was with my sissy little 110v Lincoln. 
Thanks to that lesson I will now limit myself to a 1/2" or so bead, move to the other side of the joint for another 1/2" bead, then move back to the first side. That way the base metal stays pretty hot and my weld bead is less likely to get pulled down by gravity.
Understood. Is there some kind of magic for not having a blob where the continuation bead starts?!? Seems like where I pick up the bead, the welder always gives me a pop pop before the sizzle starts and then it's a blob.
Also should I angle into the seam or does it not matter?
tuna55
UltimaDork
9/7/14 11:28 a.m.
VWguyBruce wrote:
Understood. Is there some kind of magic for not having a blob where the continuation bead starts?!? Seems like where I pick up the bead, the welder always gives me a pop pop before the sizzle starts and then it's a blob.
Also should I angle into the seam or does it not matter?
Are you snipping the wire before starting the weld? Sometimes leaving the leftover blob at the wire end can cause issues in the beginning.
NOHOME
SuperDork
9/7/14 11:57 a.m.
tuna55 wrote:
VWguyBruce wrote:
Understood. Is there some kind of magic for not having a blob where the continuation bead starts?!? Seems like where I pick up the bead, the welder always gives me a pop pop before the sizzle starts and then it's a blob.
Also should I angle into the seam or does it not matter?
Are you snipping the wire before starting the weld? Sometimes leaving the leftover blob at the wire end can cause issues in the beginning.
What Mr Tuna says, plus give the end of the bead a quick swipe with a wire brush.
Yep, snipping each time. Learned that from the magazine.
Wire brush. Got it
Turn the wire feed speed down 'til you get skipping, then dial it back up 'til you get a nice sizzling bacon sound. Point the gun at the thicker material and work the puddle mostly on the thick material with little passes up into the thin.
It wuldn't hurt to pre-heat the ball w/ a propane torch if you're having difficulty getting penetration. But the main thing I see is too much filler. When MIG is perfect, most of the bead is below the surface. Also, go wider so you're not piling a narrow bead up; side to side, advance, side to side.
motomoron is exactly right, spend more time on the thick side of the weld since it's going to require the most heat.
Definitely snip each time, keep spatter off the weld tip and wire brush a bit. Use stainless brushes, the brass ones can contaminate a weld. On preheating, MAPP gets hotter and a quick start torch is a wunnerful thing.
In fact, I have learned to braze well (at least for me) with MAPP and the secret is to have TWO torches; one to keep the work piece hot the other to get the rod etc hot enough to flow. That's how I built the stainless steel adapter for the turbo inlet in the Jensenator; it is 2 .750 OD by about 6" long and has two tubes brazed on it, one for the idle air bypass and one for the crankcase vent system. It was a beeyotch keeping it hot enough!
In reply to Curmudgeon:
It's sort of a fundamental part of MIG welding that it starts out cold, but the wire keeps coming, so you get a blob effect at the start. Makes it difficult to do the weld in short sections. With TIG you can just hold the arc until the base metal gets hot, then add filler; MIG doesn't give you that luxury. There's been lots of good advice here, but there are also tons of videos on youtube that might help you visualize a good weld. You might want to get some scrap metal, different thicknesses, grind it clean to shiny metal, and run some practice beads to get a better feel for it.
Yeah, TIG will get you around that and it makes for beautiful welds. One of these days maybe I can afford one... In the meantime, clipping the wire helps me a lot.
Many thanks again you guys! I'll be welding a lower crossmember/subframe thingy out of 1/8" flat and 1/2" round this week. I'll keep you guys updated. I also grab a pile of scrap for practice next time I'm at the metal supply.
Oh and another thing, one of the guys from work asked if I was running fans in the garage. I run 2 56" ceiling fans and usually a box fan. Thought maybe I was blowing my gas away.
Glad he asked that. Yes, shielding gas will blow away quickly!
In reply to VWguyBruce:
Go to the local scrap yard and grab metal of a couple different thicknesses to play with. Way cheaper than new steel and when you are all done boogerin' it up... sell it back to them.
I have to add if you are welding galvanized steel, well really anything galvanized, make sure you have adequate ventilation. Metal fume fever is not something you want to deal with.
In reply to wearymicrobe:
I always drink milk after welding galvanized steel, that and staying upwind seems to work.
I have a cheap helmet too and I thought it was no good, as I could not see the joint, only the arc. I discovered to my embarrassment that I forgot to remove a protective film on the inside of the helmet. Now I can see everything when I weld and I am getting better because of it.
Spent the day fabbing up a lower cross brace/sub frame dealio for the Metro today. After all the advice many good welds. Some crapola but it's built like a brick E36 M3 house. Thanks again everyone. Very satisfying to complete.
Inspiration.
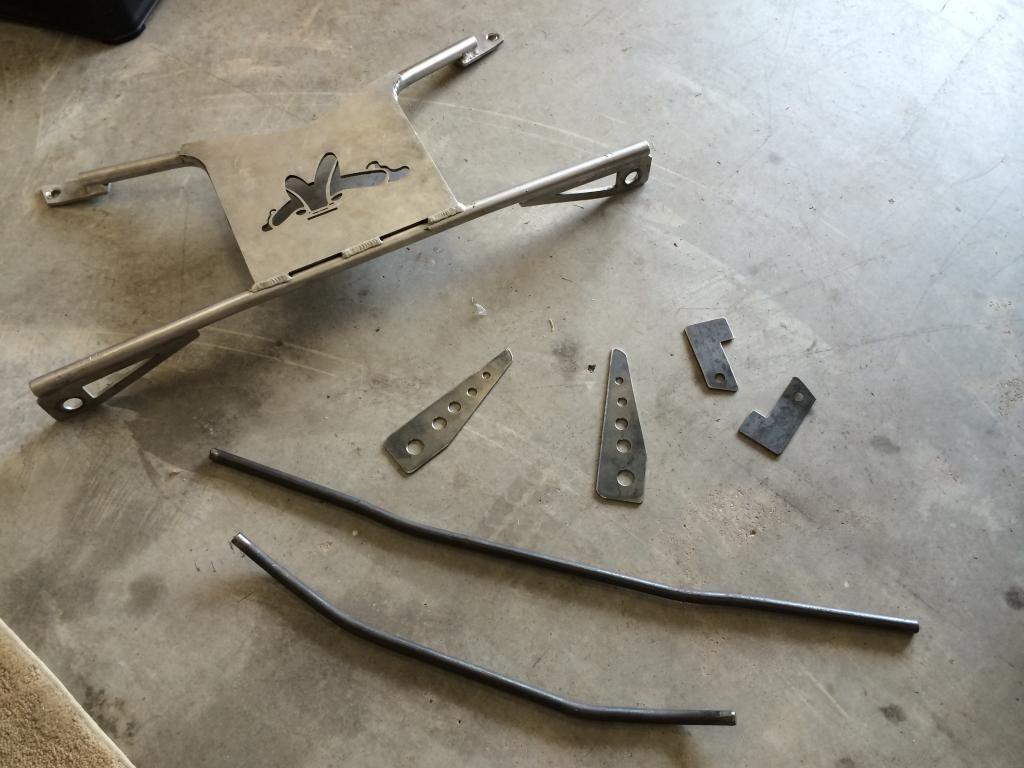
Good one.
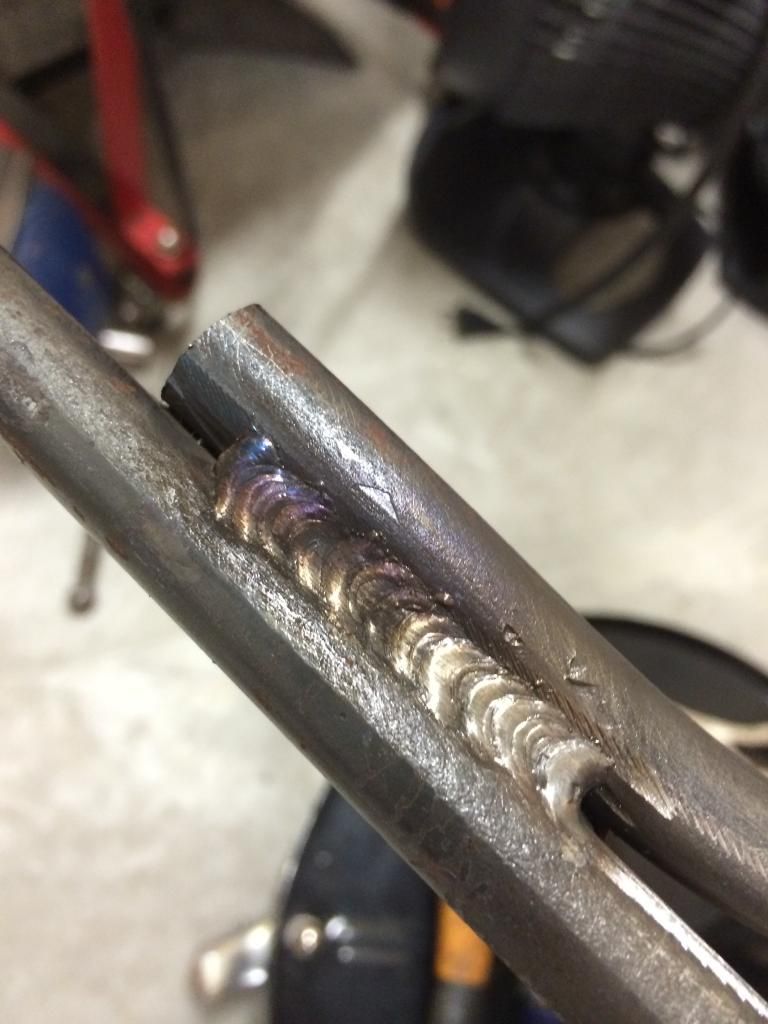
Poopie.
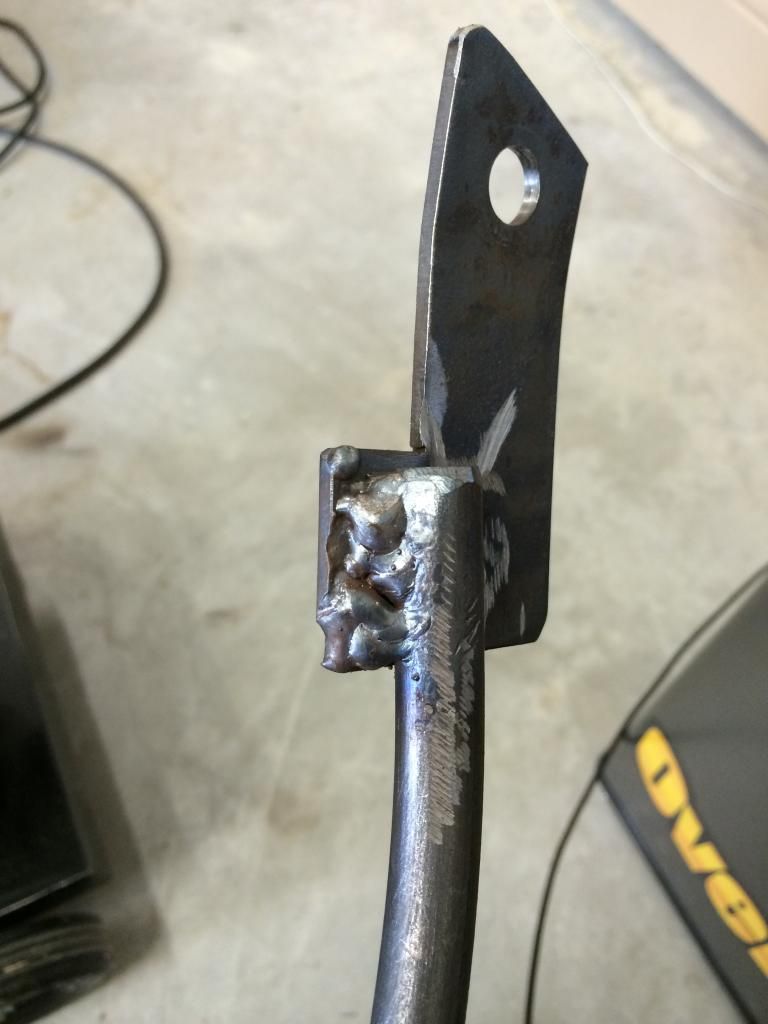
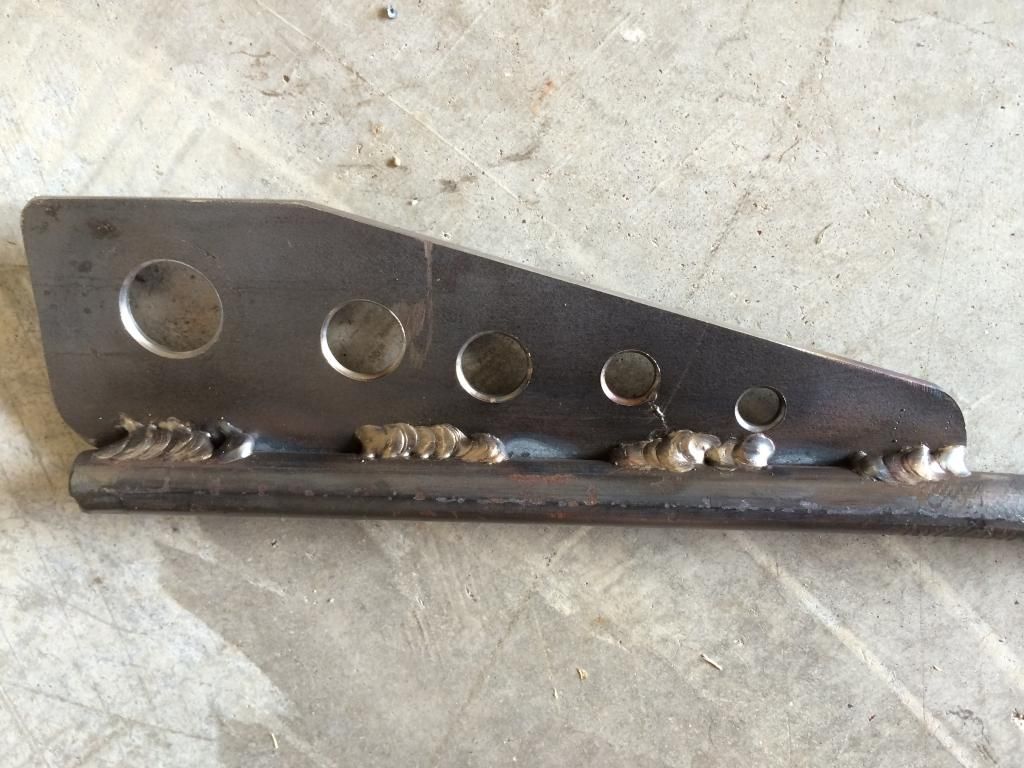
Finished.
