TLDR: Which bowl of poop?
Here’s a headscratcher that’s only interesting because I’m trying to pick between e36M3tty options.
I need to drop the exhaust on my daily, which has been in place since 2004. All weekend I tried heat/PB blaster/candle wax, and got nothing but a garage and house full of chemical fumes (plus pissed off wife) and one snapped off stud. I’ve now accepted that the copper flange nuts are fully rust welded in place. As I see it, i can:
1. Use a dremel to cut the nuts off, and clean up the threads with a die. I’d be careful, but accept I might screw up some stud threads, and have to drill that stud out. Figure 20 - 30 minutes for each of 3 nuts, plus 2 hours to drill the already broken one plus the additional one I screw up. It’s 35-40F in my unheated garage.
2. Cut to the chase, say Berk It and bust off the studs intentionally by going gorilla with a breaker bar, then drill out the studs. Figure an hour each for 4 studs, plus penalty time for cursing and broken drill bits. Cold garage.
3. Swallow pride and take it to a shop. Figure $300? I’d want to take it to a shop, not a muffler place, since I’d guess their default move would be to hit ‘em with an air chisel and a hammer, the vibrations of which are supposedly bad for the cats, which are integral to the exhaust manifold. (Lots of purported “wisdom” on this on the e46 forums, seems dumb to risk it being true.)
4. Punt, and wait until spring to do the work, taking the risk that the partially failed rubber guibo doesn’t fail completely and cause more damage when the driveshaft flops around.
Any advice?
Dremel to remove the remaining nuts is probably a good choice. You should be able to remove enough material to split the nut, so you will only cut a groove in the threads, at worst. Drilling exhaust studs can be a real nasty job.

This is better than no heat at all. (If you have one.)
With just a little damage you can re-use the studs, they need not be perfect. A .045" wizz wheel slot the length of the thread on one side will still be useable. The next guy is in trouble though, and it might be you. Does the Guibo have a centering pin like an Alfa, or is it able to swing free like a Lotus Elan axle? Only if it is centered I would run it long.
02Pilot
SuperDork
12/17/18 8:59 a.m.
Dremel ~90% of the way through the nuts, heat, then impact wrench.
Can’t speak to cats but impacts and air chisels in the vicinity will mess up o2 sensors.
exhaust work sucks balls. however, when i had to drop the system from my E60, i went to Harbor Freight and got two very valuable tools for the job:
- a 6" extension thingie (yes that's the technical term) for hex drive tools like screwshooter bits etc. Link: hex bit extension
- EDIT: I actually used a 12" hex drive extension thingie as seen here
- a set of small-diameter drill bits with the hex drive thingie (yay, another technical term) on the shank. Link: hex drive drill bits
you'll also want/need a long center-punch (i used my belt sander to put a point on a drift punch type of thing), and maybe a long cold chisel for splitting the nut after you drill through it. IIRC i just used my pointed drift punch to smack the nut after drilling through it as shown below. when you start, the exposed threads may look like ass. don't worry about them. the threads that were protected by the nuts will hold just fine with new OE nuts. i also used OE gasket and have been leak-free since doing this job maybe 18 months / 30k miles ago.
procedure (see sweet diagram below):
1. center punch so drill bit doesn't walk
2. drill (maybe use multiple bits to achieve max dia)
3. split
4. remove
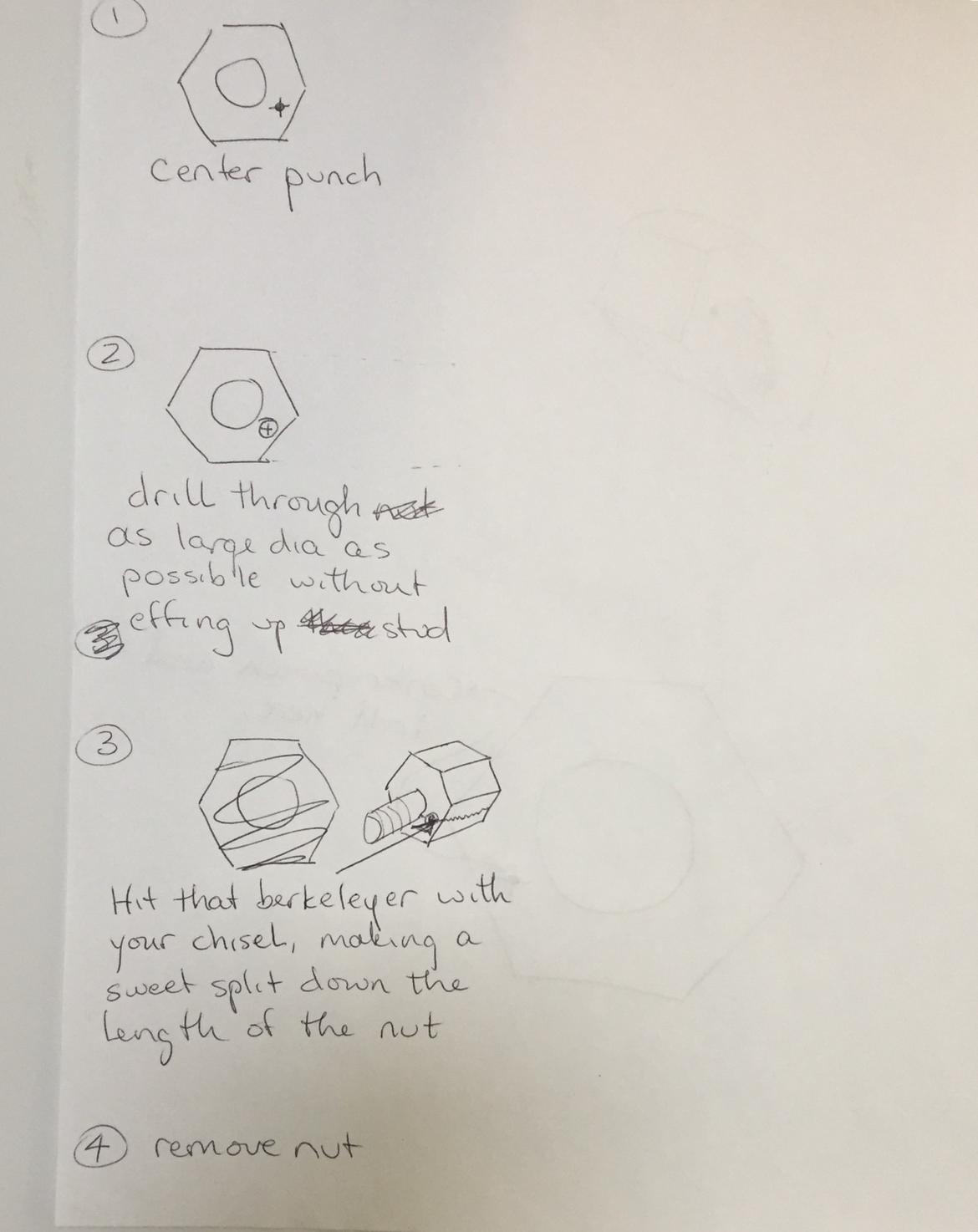
(4) might require using the chisel / drift punch to initiate rotation of the nut, as it may still be stuck to the stud. see below. YMMV, YOLO, etc, but it worked for me. *minor confession: i had the car on a hoist, which made it a lot easier, but i think it's still doable on your back under the car as long as it's secure on jackstands. the better your drill job, the less hammering required.
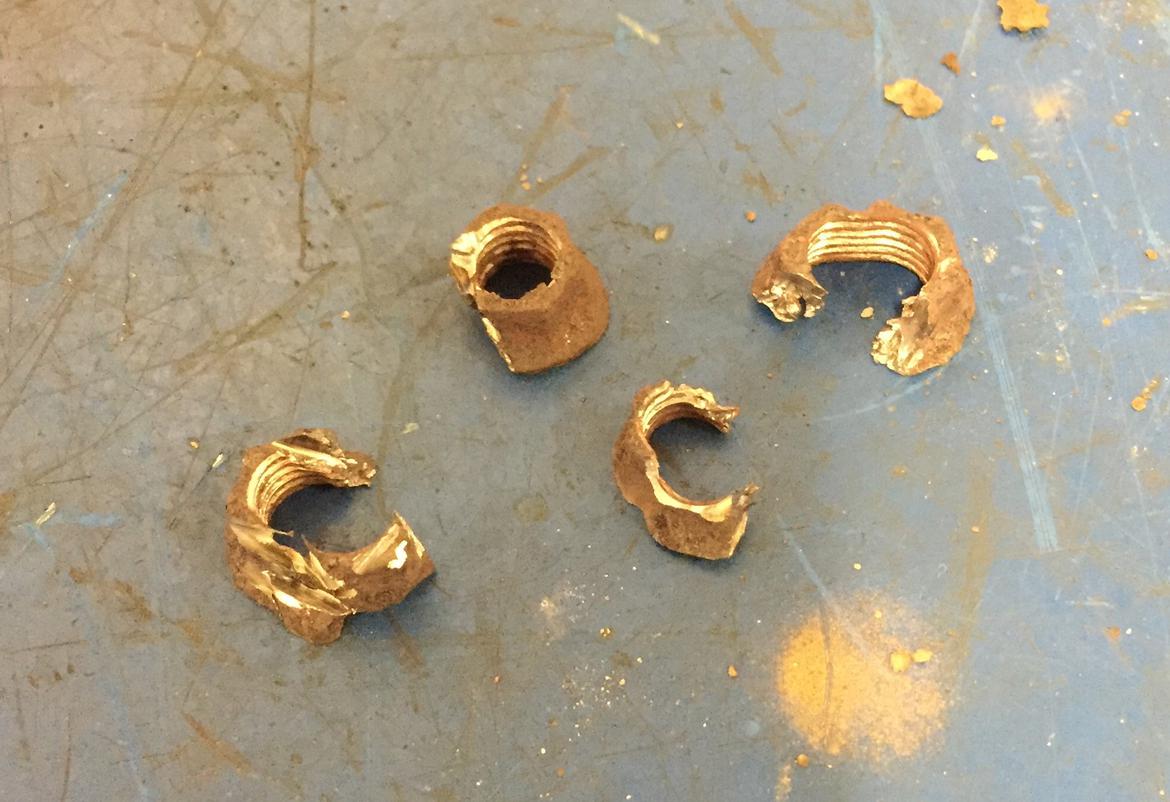
edit: from the above pic it is obvious that i used the death-wheel to slice through the two nuts i could access with said death-wheel. but the two that i drilled and split are clear evidence that drilling and splitting as i described is a valid process that would work on all four.
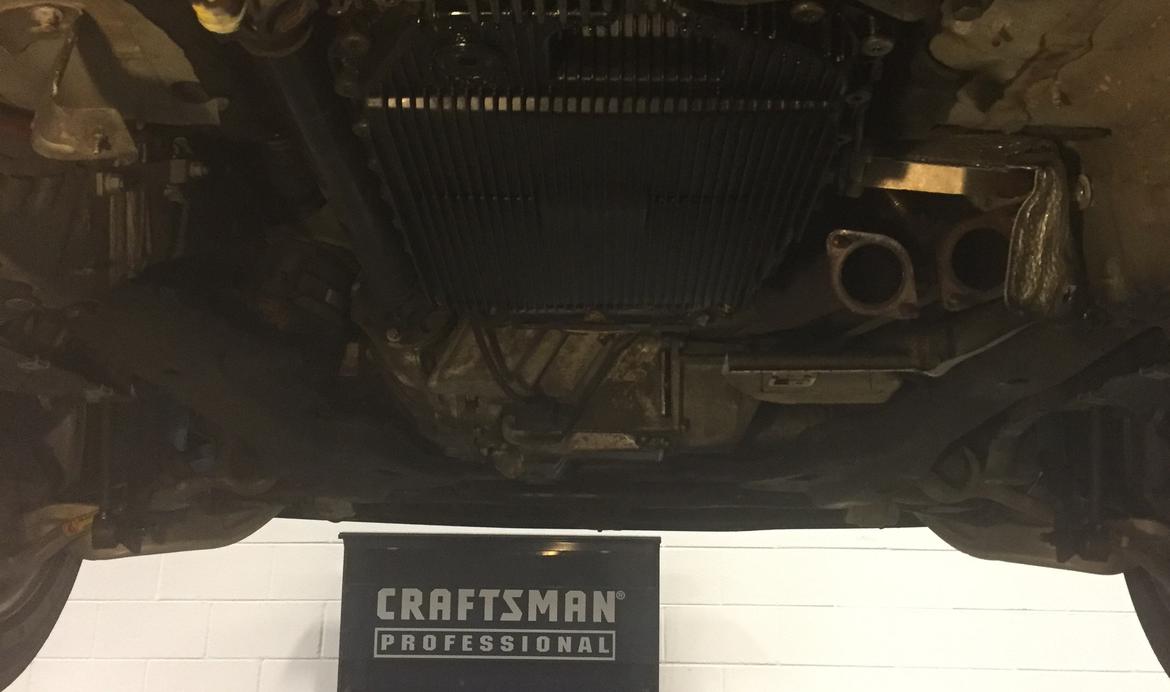
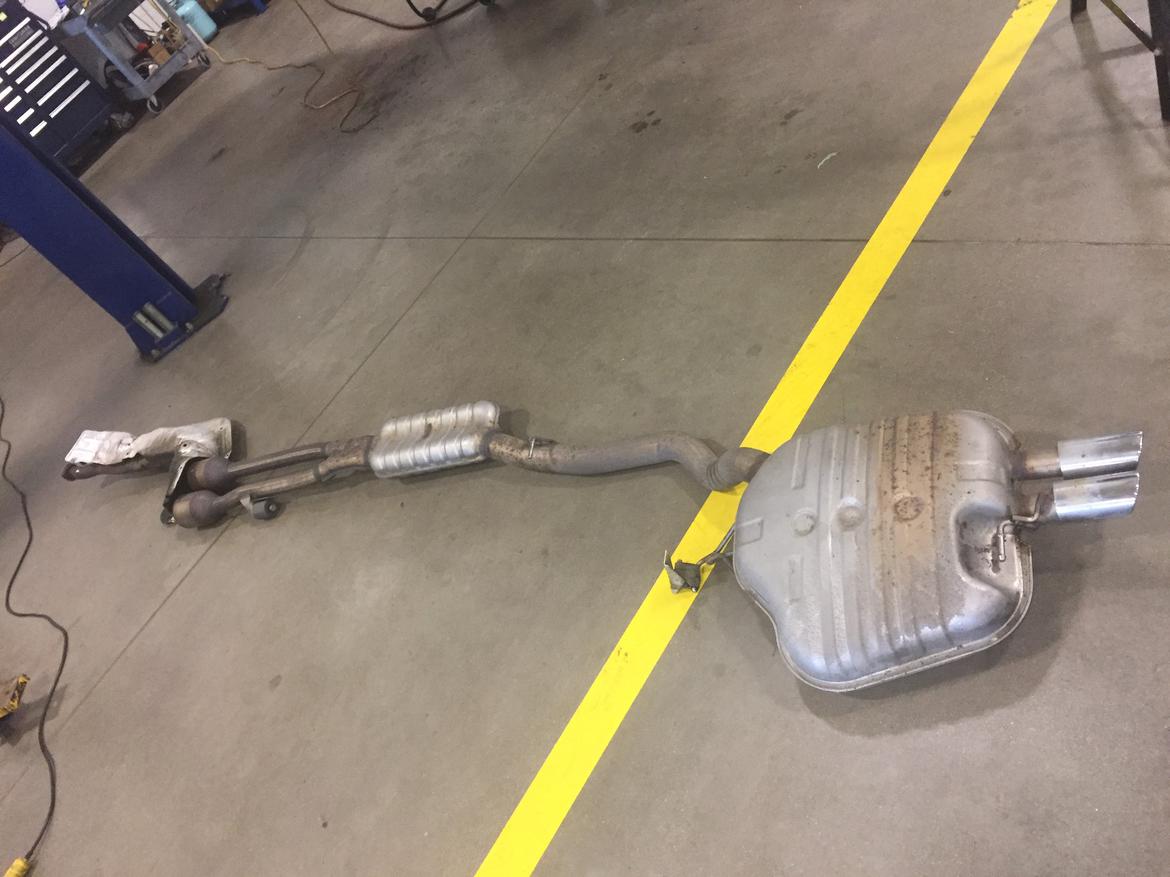
I usually go with the last option...
Sawzall that entire bitch off and start over.
fanfoy
Dork
12/17/18 2:01 p.m.
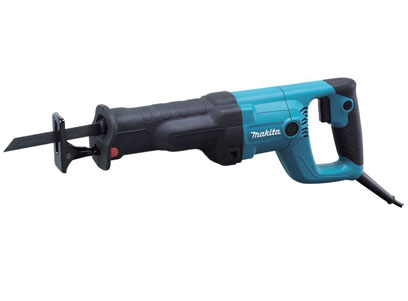
Apply in liberal doses. Trying to save an exhaust system on a rust bell car is an exercise in futility
Mini-ductor if you do not like open flame (but Oxy acetelyne is the best).
Without heat, you are going to break the fasteners...sorry...so plan accordingly.
If you can be without the car for two months or so (and it is inside and warm), you could just continue with penetrants...but remember Kroil is the best.
\
I think #1 and #2 are the most reasonable options. I've done both myself, it's a game time decision once you're in there and see how things go.
I've drilled out studs before and it wasn't as bad as I had feared. Good drill, good bits, cutting oil, and patience all go a long way towards a good outcome.
Brotus7
HalfDork
12/18/18 8:46 p.m.
Can you get at it with a torch? The Bernzomatic oxymap posted above is the ticket if you're comfortable with it. In the very least, I'd give that a shot prior to committing to any of the 3 options.
There is an inductive heater tool that heats up the nut to red hot.
This loosens the threads so it will come lose.....
Maybe one of the smarter guys here can figure out a DIY build
Here is all I have to say about this....
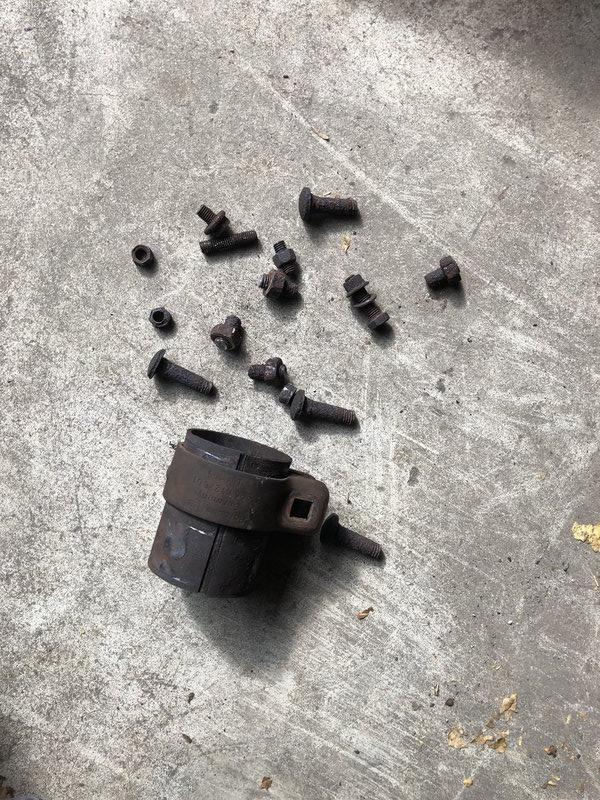
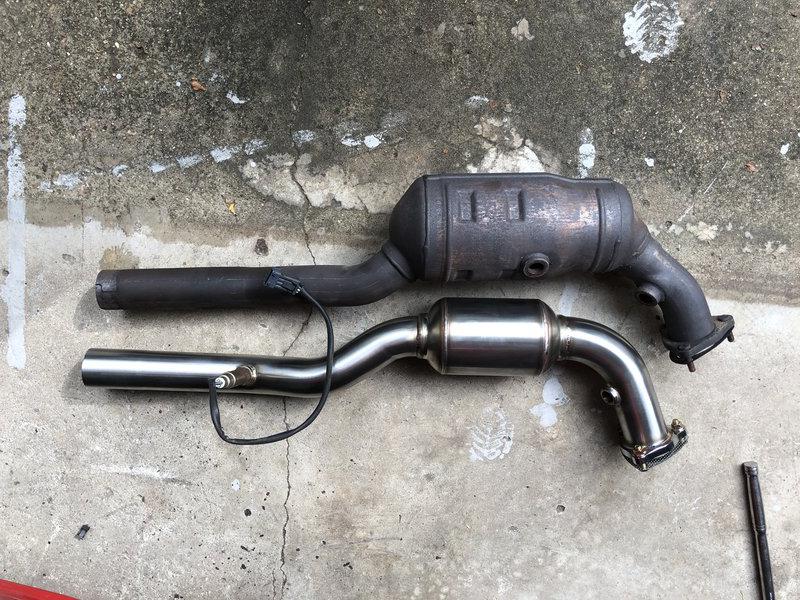
all these posts and not a single mention of the lowly Nut Splitter?
The "mini-ductor" is the inductive heating tool.
joeg1982 said:
The "mini-ductor" is the inductive heating tool.
Bolt Buster seems to be the best one on Amazon
In reply to californiamilleghia :
Just went and looked.....DANG those things are pricey 
I'll probably just continue my old fashioned ways.
Dave M
Reader
12/19/18 8:32 a.m.
In reply to KyAllroad (Jeremy) :
Do you guys know if these things can be rented? Because $400 is a lot for the occasional bolt removal.
44Dwarf
UberDork
12/19/18 8:41 a.m.
If you have a ARC or TIG welder you can make your own inductor coil.
Me I'd bit the bullet cut the nut/ studs off flush with the manifold remove manifold then heat the head area up wack the end of the stud with a hammer and extract the cut off stud. then replace the studs with SS units Metric screw an tool these guys will set you up. There kit for modular ford motors is great.