Enyar
Dork
11/11/15 8:27 a.m.
Both the toilet and the toilet shut off valve were leaking so yesterday I watched a couple youtube videos and decided I had the skills to be a apprentice plumber. The valve isn't in the most accessible location which made removing the old valve and cutting off the old brass ring a bunch of fun. Dremel made easy work of the old brass ring after I wasn't getting the right angle with the hacksaw.The new valve went on pretty easily but I'm afraid to keep tightening it as it's pretty damn tight. Unfortunately it leaks about a 1/4 solo cup a night....I believe because I didn't clean the old copper pipe well enough. The pipe has a little buildup from over the years so I think a light sanding should clean it up. I also was fooled into thinking this new 1/4 turn valve was all metal but I now realize the lever is plastic.
I'm going to make another attempt at replacement with a new valve that has a metal handle. I also did some reading on sharkbite valves which seems like the way to go.
Any tips to make sure this goes a little more smoothly? Also, if I wanted to move the copper pipe up a few inches, so I just need to cut out the drywall, cut the pipe at the 90 elbow and extent the pipe/add a new 90? This pipe is too low which causes some issues with the tile/flange. I'll be replacing toilets shortly so that would be the time to give that a try.
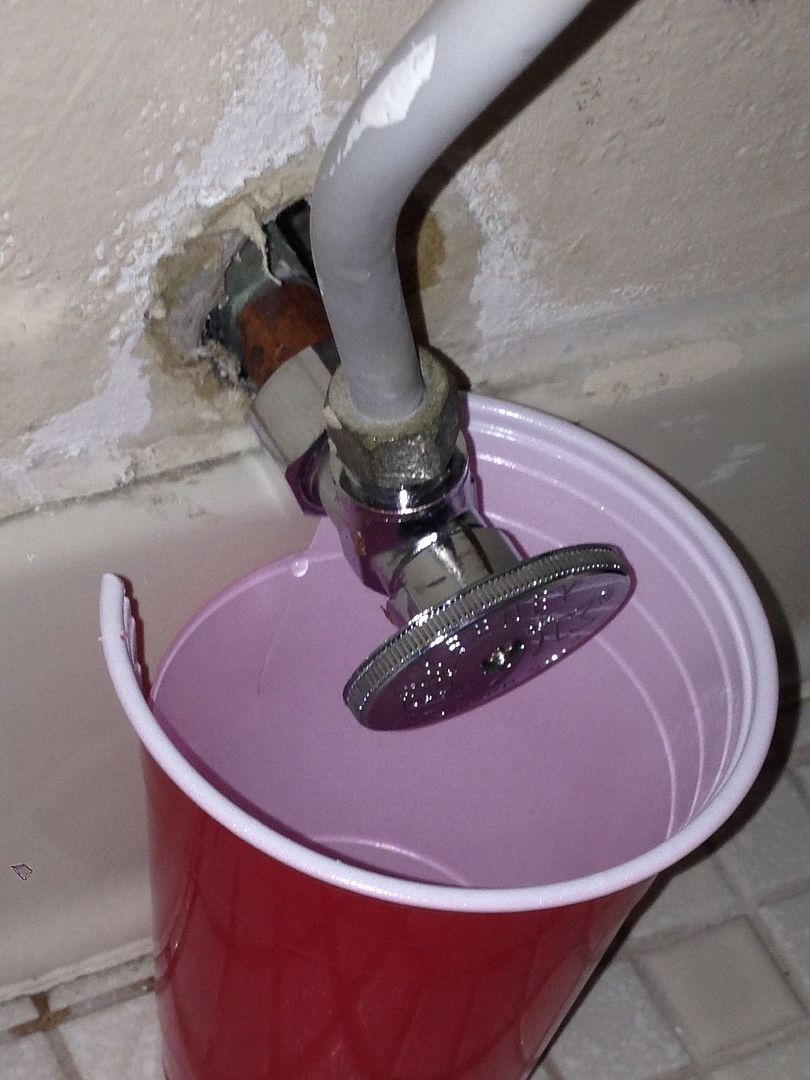
I have used the shark its stuff successfully for a repair I could properly solder at the time of the fix (to much water around the area) but I definitely wouldn't use that inside a wall cavity. If you are good at soldering joints you can do this job, but be sure you can do it first. Your previous post indicating that you used a hacksaw and didn't use an Emory cloth to clean the pipe suggests you may want to read up on how to do this and what tools are required before you try. A leak inside a wall is no good.
did you use teflon tape on the threads? I would undo it and add that if you didn't.
Sharkbites work great as long as you sand the cut end of the pipe and push them ALL the way on.
Ian F
MegaDork
11/11/15 8:46 a.m.
If you have access to the pipe in the basement, I'd replace the stub-out from the wall. It doesn't look like you have enough pipe left to make a good connection.
Press the "easy button" and replace the entire valve and hose assembly with one of these: http://www.homedepot.com/p/BrassCraft-1-2-in-Nominal-Push-Connect-x-1-2-in-FIP-x-20-in-Brass-SpeediOne-Braided-Connector-and-Valve-G2PS19B200HX-F/205395457
Prep it correctly and Sharkbite is amazing. Soldered joints are great if done correctly but if you mistakenly make a "cold joint" it can fail and crest a flood. Using a Sharkbite connection is much more forgiving of less skilled installation.
Just prep it better. Emory cloth till it shines.
Enyar
Dork
11/11/15 9:06 a.m.
I think prep was my issue. Water was still flowing everywhere and I was running out of towels/dinner was ready. We just moved here so I wasn't certain I could find the emery cloth in the garage so today I'll pick some up and try again.
I read that teflon tape was a big no no in these compression fittings so that's not on there.
I've never soldered anything other than electrical connections. I wouldnt use the sharkbite inside the wall, only to replace the valve shown above. What I would want to solder is the copper pipe inside the wall to raise the horizontal pipe up a few inches so it's not interfering with the tile (which will be getting replaced soon). Maybe I'll buy some copper pipe to practice on before I go start cutting up the drywall.
Ian F
MegaDork
11/11/15 9:17 a.m.
Personally, I like to avoid joints in the wall entirely, soldered or otherwise. Of course, I say that after burying a berk-load of PEX joints in the walls and ceilings of my ex's house when I re-did much of her plumbing. Sometimes it's unavoidable.
Anyway - you didn't say - do you have access to where the pipe branches off? I mention it because the fitting inside the wall doesn't look great either. Which often means the pipe below is in poor condition. Unfortunately, I speak from experience here - there's a reason I re-did much of the plumbing - it had corroded to the point where I couldn't get the pipes clean enough to solder well. It was a mess. I soooo look forward to doing this again in my house (Not).
Having sweated more pipes than someone who is not a plumber should have, I will pass on what I have learned.
- The pipe can never be too clean. If it's an old pipe, it needs to be cleaned up till it shines like new, then apply some flux to get prep the copper for the solder.
- Any water left in the pipe is your enemy. Shove some white bread into the pipe to soak up all the left over water, it'll just dissolve once you turn the water back on.
- Get a piece of metal flashing or even some aluminum foil doubled up and stuck between the pipe and the wall or stud if it's close to one. Helps keep you from burning them up with the torch as you try and get the correct angle on the pipe to sweat it.
That's pretty much it. Just heat the pipe and let the solder flow into the joint, it's pretty cool when it works like it should.
Everything t25torx just said. Also, if you do go with soldering buy a MAPP gas torch instead of propane. Much hotter.
And the trick is to heat it more than you think you need to. The flame around the copper will start to turn green when it's hot enough, this is a good bit hotter than the solder melting temp.
Enyar
Dork
11/11/15 9:36 a.m.
Great tips everyone.
I've illustrated what I imagine it looks like behind the drywall.The light green is the tile where the valve is just too close too. In theory I would cut, solder a 3-5 inch upright piece of pipe, then solder the 90* elbow and then add the new sharkbite shut off valve on the end of the horizontal piece.
Make sense? Good idea?
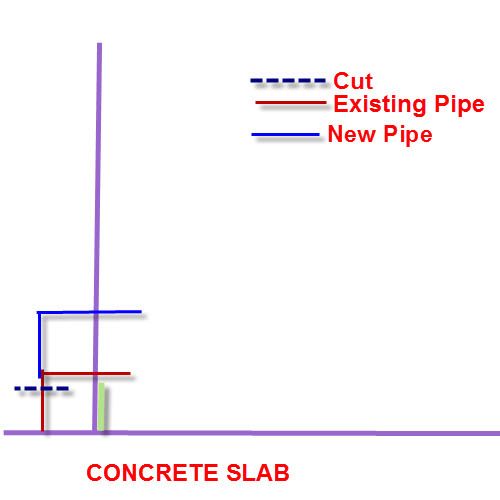
Ixnay on torch fire unless you're a pro. +10 on the sharkbite fittings.
I think the Teflon tape suggestion is for the threaded joint(s) on the flex hose.
Solder the new union, the vertical stub, the new 90 and the horizontal pipe in your garage (before it's in the wall and hard to reach). Then you'll only have one more joint to sweat down near the floor, and in the wall. And you'll have a few joints worth of practice.
Lastly - Don't berkeley it up, it'll be a lot tougher if you have to bust the slab...
Enyar
Dork
11/11/15 2:11 p.m.
OHSCrifle wrote:
I think the Teflon tape suggestion is for the threaded joint(s) on the flex hose.
Solder the new union, the vertical stub, the new 90 and the horizontal pipe in your garage (before it's in the wall and hard to reach). Then you'll only have one more joint to sweat down near the floor, and in the wall. And you'll have a few joints worth of practice.
Lastly - Don't berkeley it up, it'll be a lot tougher if you have to bust the slab...
Ah I see. The hose/toilet is just there for show. I have the valve turned off because this toilet isn't even bolted down and it runs. I only replaced the valve because the old one wouldn't turn off completely.
I'll have to look into the soldering and see if it's for me. Definitely a skill I want to learn but I also want to minimize flooding.
I used the sharkbites under my upstairs sink after it sprung a leak and we couldnt find a reasonably priced copper line faucet so i had to convert it to the hose style. Tubing cutter cuts the line much cleaner then a hacksaw. Cleaned the pipe with 1500 grit sandpaper. It helped that i had a guy with years of plumbing experience watching over my shoulder.
Ian F
MegaDork
11/11/15 2:30 p.m.
Agree about the tubing cutter - You'll need one to cut the pipe accurately in the wall. I have three of them... By the time I finished my ex's house, I had a large canvas bag full of plumbing tools...
Ian F wrote:
Agree about the tubing cutter - You'll need one to cut the pipe accurately in the wall. I have three of them... By the time I finished my ex's house, I had a large canvas bag full of plumbing tools...
Ain't it funny how that happens? I have 2 pipe cutters, 2 pipe wrenches, 2 drain snakes, and a propane torch. This isn't even my part time job.
t25torx wrote:
Ian F wrote:
Agree about the tubing cutter - You'll need one to cut the pipe accurately in the wall. I have three of them... By the time I finished my ex's house, I had a large canvas bag full of plumbing tools...
Ain't it funny how that happens? I have 2 pipe cutters, 2 pipe wrenches, 2 drain snakes, and a propane torch. This isn't even my part time job.
QFT
I'll see your drain snakes and raise you 5 nail guns! And I'm a locksmith.
Tighten compression fitting until it stops leaking or the nut cracks. Unless the pipe was crusty or nicked it should seal.
Crank that nut down. For future reference dont bother cutting off old nut/ferrule if tight like that, just compare depth of old and new valves, trim back copper end if too long, and pop new valve on the old nut.
Teflon tape is ONLY to be used on pipe thread. It does nothing on compression since the threads don't do any sealing.
I agree. Turn off your water supply and crank the nut tight. You can go pretty tight with them. Turn the water back on and see if that fixed it. If not, you aren't humped, just turn off the water, remove the whole thing, and re-prep. Always go around the copper, never go... uh... like you were alone with porn. You want the scuffs to go around the copper, not longitudinally. Otherwise the grooves can be channels that can leak.
If you end up removing the valve for reprep, you can often re-use the compression ring. If you can't, they sell them individually at hardware stores. No need to buy the whole valve again.
Quarter-turn valves are fantastic because they are a ball valve instead of a gate like multi-turn valves. Gates get gunky and in 6 years when you need to replace the toilet, chances are the valve won't close. Ball valves don't get gunky like that.
If you want to solder it, let me know. I have some tips. Not because I'm a good plumber, just because I've done it with some tips that a plumber gave me.
But honestly... a compression fitting is not weak, easy to replace, and a no brainer. I refitted my whole house with compression 1/4 turns and they are lovely.
Hal
SuperDork
11/11/15 9:32 p.m.
OHSCrifle wrote: Solder the new union, the vertical stub, the new 90 and the horizontal pipe in your garage (before it's in the wall and hard to reach). Then you'll only have one more joint to sweat down near the floor, and in the wall. And you'll have a few joints worth of practice.
Add to this: DO NOT cut the vertical pipe! Just heat up the 90 and pull it off the vertical pipe. That way you will have a pre-tinned end for the union to go on. Will make getting a good solder joint much easier.
Wow, as a master plumber, all I can saw is wow. There is so much bad information on this thread. Always always solder clean pipe and fittings that has plenty of flux. Never overheat. You want it just hot enough to melt the solder and then pull the flame away. Hit it again in little bursts if you the solder stops flowing. If your a novice, add a little extra solder. If your a pro, 1/2" of solder for 1/2" joint. 3/4 for a 3/4 and so on. Let the joint cool before you touch it. If there is water in there, then you didn't do a good enough job draining down the whole house. Compression joints need clean pipe as well. Any burr, out of round pipe, or solder blob will prevent the ring from squishing around the pipe and seal. You need to crank those things down real hard. Harder than one would think. If it keeps dripping, keep cranking. They suck and thats why we don't use them. Shark bites work pretty good as long as there is a clean edge on the pipe and it doesn't mess up the O ring.
NO TEFLON TAPE! Those are compression fittings. Teflon tape is for pipe threads, you don't have any there. Teflon tape is more likely to screw things up with a compression fitting.
All joints need clean pipes. So yes, if you just shove a ring down a dirty pipe, it's likely to leak.
Compression fittings usually work 1 time.
Compression fittings are frequently pretty durn hard to get off the pipe after they've been compressed. Especially if the pipe has been slightly squeezed under the compression ring. You've barely enough stub pipe there now.
Soldering isn't nearly as hard as people make it out to be. Though I do understand if you simply don't want to do it.
That valve and feed pipe to the toilet are pretty restrictive, which makes the toilet tank slow to fill. If you want fast refills for more rapid flushing, use non-toilet specific valves and lines. In a house with many people, the difference can be appreciable.
Enyar
Dork
11/12/15 8:09 a.m.
Thanks for the help everyone! The good news is the leak pretty much stopped. I'm getting about a penny size little blob after 24 hours. I' still plan on removing it and replacing it with a valve with a metal handle.When that happens I'll be sure to clean with emory cloth around the pipes. That will hold me over until I do some research regarding soldering/raising the vertical pipe.
Be on the lookout for future threads because I have big plans and I need the GRM hive to walk me through it.
I have found that compression fittings will sometimes leak like you observed and then slowly stop after a few days. When I get a leak like this I protect the area from the water, as you did, and then wait for a few days and then recheck. I would tighten the fitting a bit more and you should be good.