Have a picture. Question to follow.
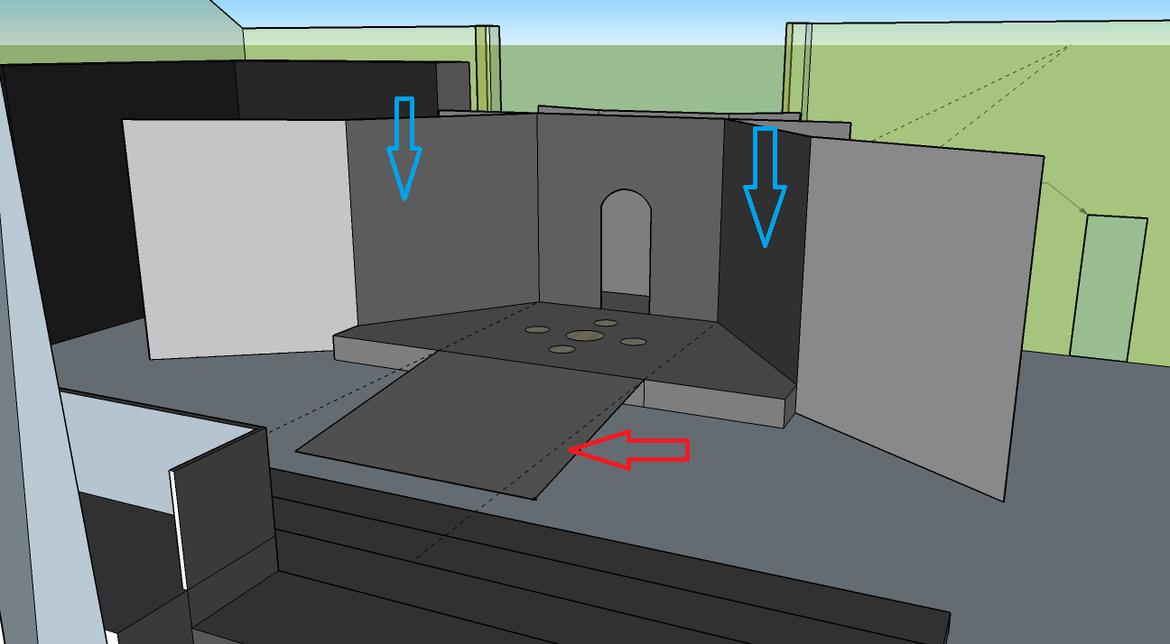
This is the set I'm building. Relax... I have a week and a half before we open.
The ramp indicated by the red arrow folds up, and the two walls indicated by the blue arrows fold in. The whole thing is a cube that opens up to what you see here. The ramp wall is 12' wide and 11' long/tall. Up to 7 people walk on it, although I don't think they're ever on it at the same time.
My first thought was to use some aluminum I-beam extrusions I have. I have 4 that could span the 11', so I would put them at 0, 4, 8, and 12' as stringers/studs. Then in between I was planning on several 1-by spans between the aluminum, skin it with luan, and fill the cavities with 2 lb urethane foam. Unfortunately, that will cost about $600 in foam.
Enter idea #2. Have another picture:
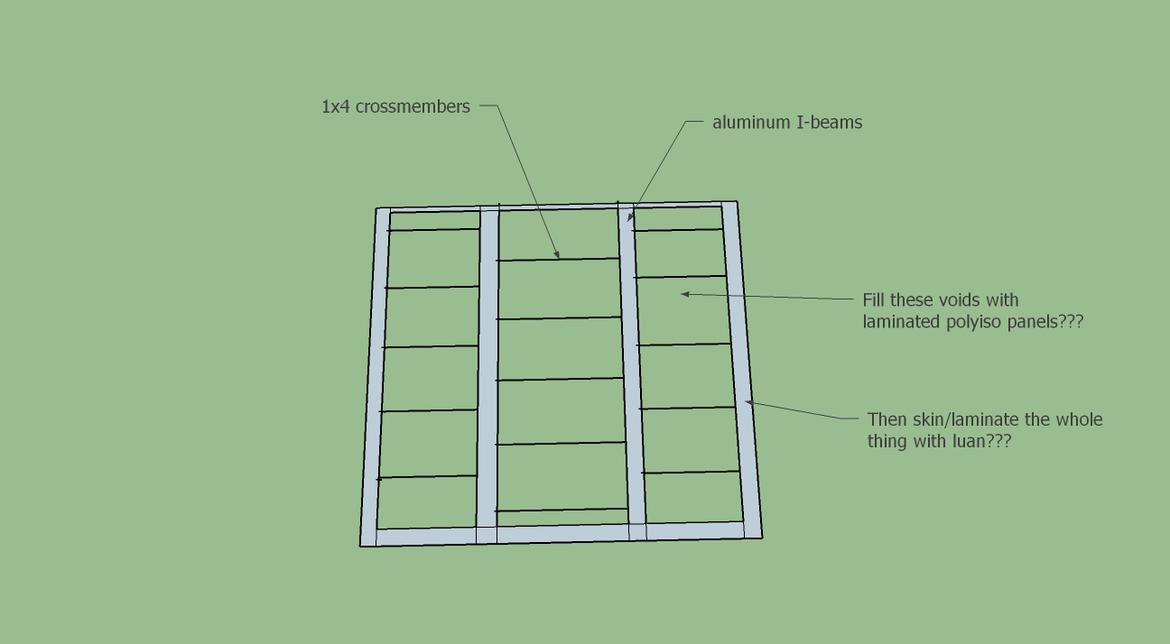
I need to make this thing rigid enough to hold some people, but light enough that two people can fold it down/up. Is there some sort of adhesive I can use to laminate some polyiso insulation sheets together, then use that same adhesive to make a stress-skin platform by laminating luan onto it?
I know epoxy would work, but we'd be spending as much or more on epoxy as we would the expanding foam.
mtn
MegaDork
2/19/20 2:52 p.m.
I'm no help, but my first thought was this:
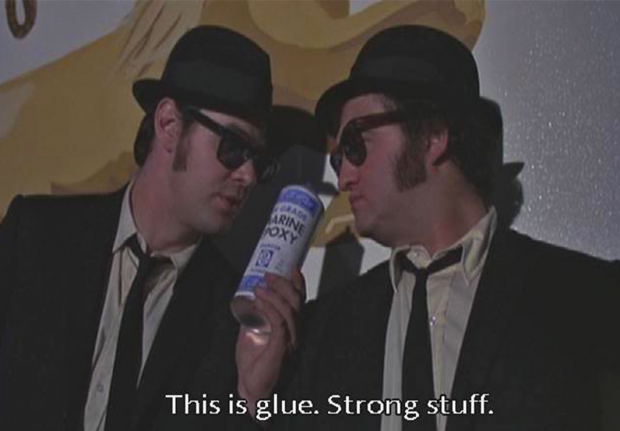
Hasbro
SuperDork
2/19/20 3:27 p.m.
I have to ask, does it need to span the entire length? Removable braces underneath?
It does need to span the length. If I can't engineer it, I might be able to convince the designer/director to add a knee wall half way.
Spanning it isn't really my issue. It's getting a means of supporting in between so I can use a lighter subfloor. 140 sf of 3/4 ply is just heavy, regardless of how light I make the frame.
In reply to Curtis73 :
Build the whole thing out of coroplast? If you make enough ribs from it to span between your spars I think it'll be strong enough. Though you'd need to add some grip tape to the surface for traction.
And miss out on actors falling on their asses? That's beyond my pay grade.
Mndsm
MegaDork
2/20/20 8:31 a.m.
mtn said:
I'm no help, but my first thought was this:
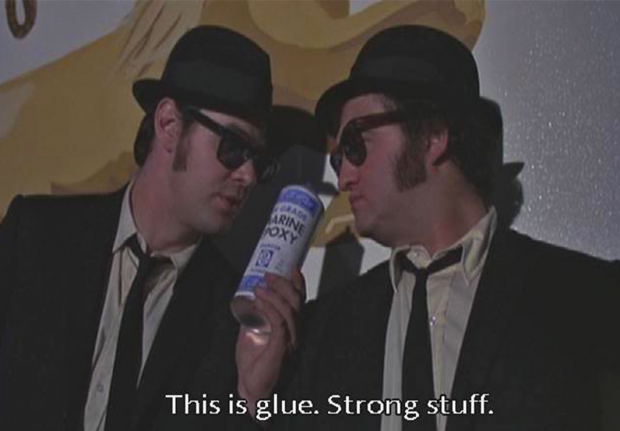
First time I've ever read that can. He's not lying. Marine epoxy is the jam.
Laminating sheets together, I would think a contact cement would be plenty strong enough. You would probably need a stress skin of some sort on the bottom of the floor. Having the foam in tension may cause it to crack.
Agreed. The plan is (referencing the photos above) is for the ramp to begin in the up position which completes the cube, so the outside/bottom will need a proper skin anyway.
So here is my latest idea:
I awoke the other night with visions of where I can source more aluminum I-beam. Then it hit me. Extension ladders. I was able to source 3 extension ladders; two for free, one for $40 because it was missing the feet (which I don't need anyway).
They are approximately 16" wide, so if I use 5 ladder sections laid flat as wide stringers, that will leave 4 voids about 16" wide. In those voids, I can use some of my existing aluminum I-beam as cross pieces "welded" in (note the quotes... I am no good at welding aluminum) Then in the 16" widths, I can buy 3" polyisocyanurate insulation panels. This would eliminate the need for laminating individual 1" panels together. Granted, not quite as strong maybe, but easier, and far cheaper because of using less adhesive.
When I say "welded" I mean some of that weird aluminum brazing E36 M3 they advertise on TV. It won't be actually structural, just holding the aluminum in place.
Then, contact cement and luan skins both sides.
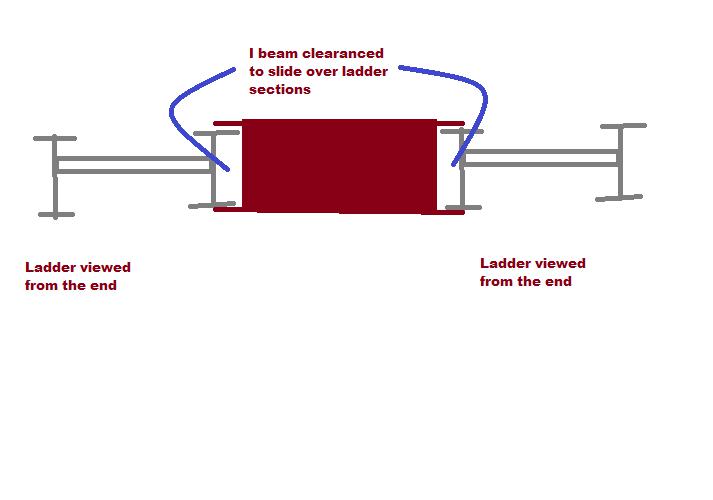
Mndsm said:
mtn said:
I'm no help, but my first thought was this:
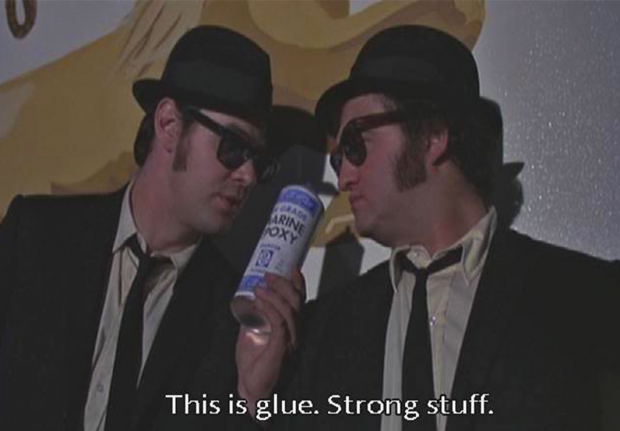
First time I've ever read that can. He's not lying. Marine epoxy is the jam.
I have a gallon of West Systems marine epoxy. Not a cost-effective solution. If I had a 16' x 16' vacuum bag, I'd try it.
The nice thing about contact cement is that once you have a good bond, it's bonded. Epoxy needs to be held in place while it cures.