In reply to RichardSIA :
Yeah you're on the wrong website to complain about politics (and concrete for that matter, maybe there's a QAnon for people who hate BiG C0ncR33t?). Now, complain about the price of IMS bearing replacement kits....bingo!
Anyway, like svrex said, I'm sure you can find a way to make something work out, even if it's not your original plan. And let the hoorays continue!
Have not given up yet, but now looking into ways to avoid the ^%#! county and concrete guys altogether. 
Now considering five 40' containers side by side with the interior walls cut out. Less than $20K and could be basically assembled in a few days. Since I am "Rural" containers are not regulated, yet! 
Portable buildings do not have the regulations of Structures and it does not get much more portable than shipping containers.
$20K is less than the cost of concrete alone for even a small conventional building. So my total cost should be about half. Need to use "Hi-Cap" containers in order to have sufficient ceiling height after insulation.
I have to agree that this fall-back plan has a lot downside, but going conventional is just too bleeding expensive! I already increased my loan amount $10K but that hardly makes any difference except increasing my monthly payments. That "Extra" $10K is now intended to allow me to complete at least one car build quickly!
This idea should also have less impact on future property taxes and I really do not care anymore what it does for value of a property that I do not expect to ever sell so long as I live. I will be paying off the loan for the next twenty years, if I live that long. Cannot just sell and relocate as in this area that would require another $150K+ that is never going to be available.
More research to be done.
slefain
PowerDork
10/26/20 10:03 a.m.
In reply to RichardSIA :
That's just insane enough to possibly work. Looks like you just clamp them side-by-side with these:
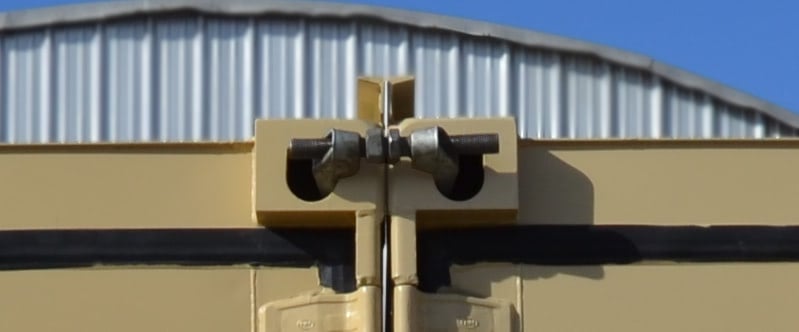
The tiny house "movement" can provide some advice here- even though shippin containers are supposedly all similar sizes they most certainly are not so you need to find multiples of them that are the same manufacturer. I think the phrase was "single use" or "one way"; there's tons of things like medical equipment that go across the seas where the potential of spillage keeps them from being re-used easily.
You'll also have to check heights. Containers seem tall at first, until you start putting in celings and floors.
Dave M (Forum Supporter) said:
In reply to RichardSIA :
Yeah you're on the wrong website to complain about politics (and concrete for that matter, maybe there's a QAnon for people who hate BiG C0ncR33t?). Now, complain about the price of IMS bearing replacement kits....bingo!
drink the corpse grade quicklime to kill the rona
(THE GIRTHQUAKE WAS BANNED FOR THIS POST)
Low conventional unit height is why I am looking at the more expensive but 12" taller "Hi-Cap" type.
Will be making some calls later today.
Also looking into how to fill the gaps and get the floor level across joints.
It looks like the loan may finally happen this month. 
It's now clear that I will not be putting up any sort of conventional building. Varied state and county mandated fees are just ridiculous at around $4K+. That is 10%+ of my previous $40K max budget! So now the county will get nothing, just desserts for their greed and heavy handed "Oversight".
I will be putting up a glorified Tent instead. Not a Wal-Mart tent, a $9,000.00 - $12,000.00 tent with a fifteen year guarantee. Since it is not a "Structure" and does not require a foundation, no permits, no 50% increase in property tax, much cheaper concrete work. In fifteen years I expect to be beyond caring if it still stands.
Savings are enough that I hope to be able to get two 30x60. One with a $10,000.00 concrete floor as the shop and a second with just DG or Pavers for storage.
Since I've begun collecting "Old age" aches and pains faster than cars, I've decided to scale back the shop expense as much as possible. The money saved will go to COMPLETING some projects! So by around Feb.-Mar. I should be posting actual progress pics. Have to get these done while I may still drive them.
What is the name of the tent company? I've seen some really cool tent structures. A local zoo has one, that has stood up to some harsh winters. I'm sure you also looked at quonset hut designs.
ClearSpan, American made! 30'x40' for about $8,850.00 plus more to get a steel roll-up door at one end.
U.S. made long lasting fabric workshops They can build just about anything you can pay for. I'm looking at mostly standard and in stock.
Not getting the super trick thirty year fabric as it gets too expensive. The fifteen to twenty-five year fabric will do OK for my use. They have a LOT of products, I am getting one of their smallest units. These guys do whole stadiums and giant AG grow-houses.
Quonset huts have the same hurdles as any other building. The secret of fabric is that it is not a "Building" so MUCH less expensive in many ways.
Wow, those look great. The one here in maine is used as a butterfly enclosure. It is really solid. I looked on clear span and didn't see it. I know they did a testimonial on the manufacturers website. I'll try and track it down. We are trying to figure out what to do with our soon empty nest. We have thought of building, and of course the correct garage would be in the build. There is a house not far from here that has a garage the same size as the house. I think they have their priorities in order. If I were to build a house now I'd have picture windows or larger into the garage so I could gaze at the cars while I had breakfast. That makes it sound like I have a collection that is worthy of gazing, I do, but just to me.
Those are nice, and inexpensive.
I had a shop in a Quonset hut once. My reservation with anything that shape is that it is really annoying not having vertical walls at the sides. Hard to put any kind of workbench, shelving, etc.
If the curve comes down to the ground (like those shown), the floorspace is effectively 30% less than the footprint, because you can't use the edges. They are only good for collecting dust and clutter.
In reply to SVreX (Forum Supporter) :
I am at the spot where I would really, really like a lift. I have to find out how thick my garage concrete is so I can contemplate a max jax. I have looked at the portable one post lift and would consider that. I would have to re-engineer part of the garage ceiling, I am just wondering if I could get used to a one post.
Watching this thread is interesting for me. We have garages here with wood floors that are solid and years old. I have had some quotes on expanding my garage out back, and was shocked. I would be doing much of the work myself. I am still going to look into this. I feel for anyone trying to get around local coding, etc. We had a new septic put in our yard, I had them redo the plans for the garage expansion. First world problems for sure, but I would love some type of lift. Plus I am originally from Rhode Island, so it would be nice to just say, "quonset" all the time.
I agree that the curve may be a PITA, my plan is to use the lowest space for storage, probably heavy items like engines and transmissions. They have to go somewhere and lifting them on to rack shelving is not easy.
I will have a detailed discussion with the manufacturer Rep. on Monday.
What about the Quonset hut design where you put it on walls? I know that changes the budget, but probably cheaper that other designs. I’m always thinking of snow loads. The Quonset hut would shed it easily.
Putting it on walls means I am creating a "Structure" again, so no longer a Tent and all the hassle and expense I am trying to avoid comes back into play.
I could mount it to two containers but that adds another almost $8K to the expense which would prevent my getting two units for 2400' of total space. I can assure you, 2400' is NOT all that large and only 1200' is too small.
hey I'm following along here.....thank you for what you've provided so far peace out
In reply to Karacticus :
These look interesting but do they insulate them or are they just cold?
In reply to triumph7 :
They are using them for warehouse space-- pretty sure the answer is they are cold!

Insulation is an option item.
Along with ducting, real roll-up doors, man doors, pretty much anything you want and can afford. I would prefer a truss type but the cost goes up quickly.
Plan to get into details and exact cost with the salesman in the morning.
jgrewe
Reader
12/7/20 12:18 a.m.
I had one of them at my tool rental company for storage. It was put up under the same conditions as you are running into with the city. We had it on a slab, but we also sold concrete so... It survived about 15 years of Florida weather including hurricanes. It had one end closed and about 1/3 from the top closed in on the other end. The only thing you have to look out for is anything rubbing against the material as it breathes a little with wind changes.
Someone calls the city on us and the Building inspector shows up. We said, "Not a permanent structure, no permit needed, leave us alone"
Now looks like a 30x48 for the shop and 30x40 for storage.
Will cost a little more than the single 30x72 but much easier to arrange on the property without having to give up my view out back.
Concrete floor only for the workshop makes it semi-affordable.
Still looks to be a little north of $30K all done. But would have been over $50K for a conventional steel building. 
Trying to retain some working capitol to complete a build or two quickly.
Reality bites!
In reality it looks like I am going to end up with only one 30x48 "Tent" for now and a plan of getting another later. It will at least have a full concrete floor and keep the wind/rain/snow out. I may also get a 40' container for secure storage of the non-essential clutter.
This is the only way I may avoid the counties several ha$$les including a 50% property tax increase, and six months of delay for "Permits"!
Going this route seems the only way to retain enough cash to be certain I may complete at least one build ASAP. It's to be the Buick/Dio Tipo with a target completion of early May. I really wanted a steel building but that is just impossible.
Sent the big check to Farmtek today. Pulled cash out of the bank for the concrete floor deposit.
Getting two tents, 30'x48' and 30'x40'. Only the 30'x48' will get a concrete floor. I end up with over 2,600' of space for around $35K and no property tax increase or "Fee's", inspections, etc.
Concrete will be finished and fully cured by the time the tents show up in about a month. Assembly of 2 -3 days each.
Now the big pain will be actually moving out of the current rented space. ENCO MIll, Lathe, steel top build table, cars, engines,..........
Great news! I'm glad you've found a way forward and are making it happen.
Handed over $5,350 deposit this morning. For that I now have a string perimeter for the concrete. Just looking at that string the slab and structure look they will be REALLY small! 2,640' is NOT big.
Spent the rest of the day moving "Stuff" out of the way as the concrete guy needs room to work around the slab site so that he may more easily level and put down Base.