Torque = Force applied X Lever Arm length. Correct?
I have nuts on a short bolt hidden and tough to get to, you have to slip the fixture on with a few threads showing, put on all 6 or 8 nuts and tighten them to pull the fixture in. Imagine torquing a flywheel from the throwout bearing hole in the flywheel. Like that. You can only get an open end wrench on it.
So, if I welded an open end wrench to a 1/2" drive socket and put the socket on a torque wrench, the lever arm changes.
Lets say the torque wrench is 12" long (easier math), I add the open end wrench socket thingie and now it's 15" long
1 ft. lb. = 12 in.lb. If the requirement is say 15 ft. lbs, that would be 180 in.lb. Making a 3" extension makes the arm 15". 15 X 15 = 225 in.lb.
BUT, the measurement is taken at 12", not 15". Wrong? Incorrect reading?
What if I made a 15" long open end wrench and use a scale, like the ones used to weigh fish, and tug until it shows 180 lbs.?
Logical?
WWGRMD?
Rats, can someone spel chick the Title?
In reply to 914Driver :
180 in-lbs of torque applied through a 15" lever (as measured from the center of the fastener) comes to 12lbs of pressure at the end of the lever.
Or in shadetree terms, "snug".
Getting all the bolts torqued to the same value is more important than the actual value.
A little booklet I have,"Tips on Torque" shows a couple example of adapters. With a torque wrench 19" lever length,a 19" adapter , multiply by 2.
A 9 1/2" adapter, multiply by 1 1/2.
So maybe you can work out something from that.
If you make the arm 90*from the torque wrench there is no math involved.
Have the formula for this in my A&P book and basic aircraft maintenance manual at work. Have to look it up Monday.
180 lbs on a 15" open end wrench is 2700 in-lbs.
180 in-lbs from a 15" lever arm requires a 12lb load on the end.
But really I'm not sure you are explaining the question well. Once you extend your lever arm to 15", 12" should not factor in anywhere
I think you are saying you are essentially using a crows foot on a torque wrench?
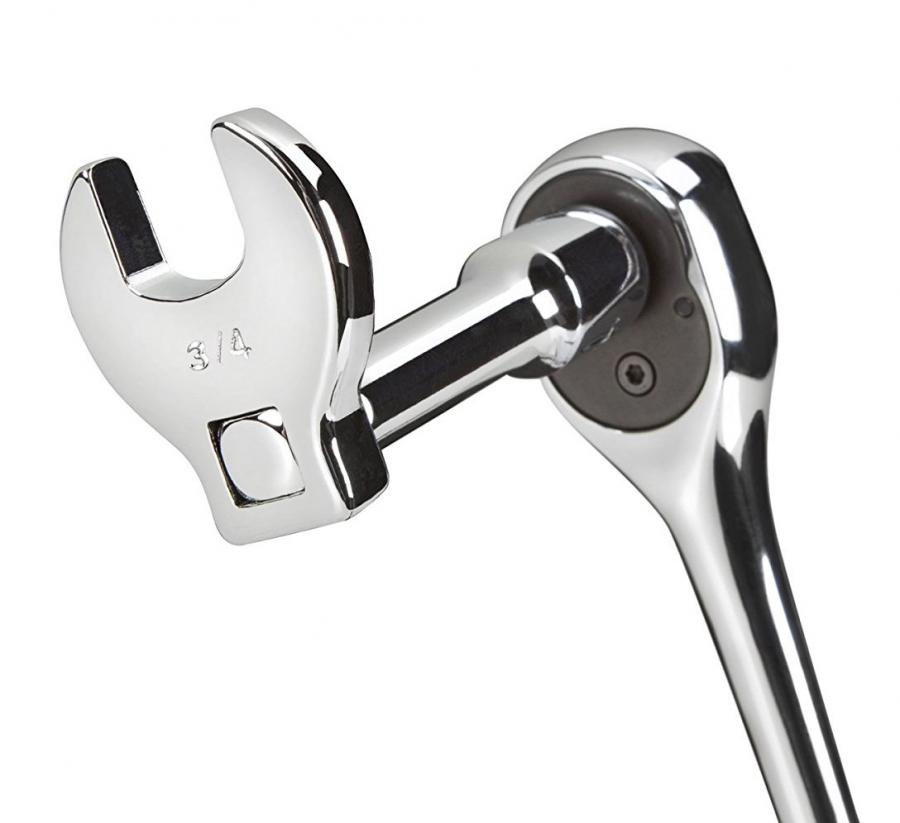
All the math so far is about adding distance to the handle end, not the bolt end. I actually think you might need to increase the torque reading you tighten too. But I could also see the Crowfoot not making a lick of difference.
In practice I'd be willing to negate the effects of the Crowfoot and just shoot for the specified torque setting.
iceracer said:
A little booklet I have,"Tips on Torque" shows a couple example of adapters. With a torque wrench 19" lever length,a 19" adapter , multiply by 2.
A 9 1/2" adapter, multiply by 1 1/2.
So maybe you can work out something from that.
Had to read this a few times but I think this is the right solution. If you add 25% (3 on 12), then you need to add 25% to the torque wrench setting. 15 ft lbs goes to 18.75 ft lbs.
I think he's saying that he is welding a socket onto a 15" end wrench, then sticking the torque wrench into the socket like this:
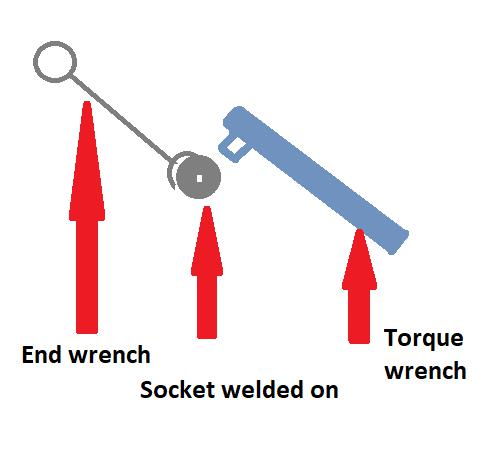
If that is the case, you need to reduce your setting on the torque wrench by the factor of how much longer you have made the lever by adding the wrench. In your case, the torque wrench is 12" and the end wrench is 3". Since you are adding 25% more length, you would subtract 25% to get the new setting. So, if you needed 100 in-lb before, you would now set the wrench to 75 in-lb. When the wrench clicks at 75 in-lbs, the nut is seeing 100.
Even easier math. 12" torque wrench and 12" end wrench. Cut the number in half. 50 in-lb setting would generate 100 in-lbs at the nut when it clicks.
Also I should point out... it doesn't matter how long you make the lever of the torque wrench. If you slip on a 4' piece of pipe, the wrench will still click where the setting is on the dial. It only reduces the amount of effort you put into it.
If you have a 12" torque wrench and add an additional 12" worth of lever on the handle end, then set it to 100 ft-lbs, it will click when the socket reaches 100 ft-lbs, buy you'll only have to apply 50 lbs of force on the lever.
The difficult part of this theoretical experiment is that the torque wrench is no longer measuring the torque at the bolt. It is measuring the torque on a joint somewhere in the lever arm.
So: bolt - distance A - torque wrench pivot - distance B - point where force is applied.
In you example above, distance A is 3 inches, distance B is 12, and required torque at the bolt is 15 ft lbs.
The total length of your new tool is 15 inches, so if that were one solid wrench that would require 12 lbs pull (as stated above).
And thats about all I got before I start guessing.
Robbie said:
iceracer said:
A little booklet I have,"Tips on Torque" shows a couple example of adapters. With a torque wrench 19" lever length,a 19" adapter , multiply by 2.
A 9 1/2" adapter, multiply by 1 1/2.
So maybe you can work out something from that.
Had to read this a few times but I think this is the right solution. If you add 25% (3 on 12), then you need to add 25% to the torque wrench setting. 15 ft lbs goes to 18.75 ft lbs.
Not unless we're not talking about the same thing. The wrench will click at the set torque. Period. Doesn't matter if you add three miles of extension on the handle end. It only changes the force you have to exert to get it to click at the desired setting. The torque wrench clicks when it reaches the set amount of torque because it is relative to the center of the ratchet. It doesn't matter what you do downstream of that toward the handle.
If we're talking about like I pictured above (with my super-dandy drawing skills), then you need to reduce the setting on the wrench by the amount you've added relative to the original length.
Robbie said:
The difficult part of this theoretical experiment is that the torque wrench is no longer measuring the torque at the bolt. It is measuring the torque on a joint somewhere in the lever arm.
So: bolt - distance A - torque wrench pivot - distance B - point where force is applied.
In you example above, distance A is 3 inches, distance B is 12, and required torque at the bolt is 15 ft lbs.
The total length of your new tool is 15 inches, so if that were one solid wrench that would require 12 lbs pull (as stated above).
And thats about all I got before I start guessing.
Exactly my point... so with your numbers, he has to set the torque wrench at 12 ft-lbs in order to get 15 ft-lbs at the nut.
And I should clarify... I'm talking about when the torque wrench clicks which is unrelated to where you grab the handle. Grabbing the handle halfway between the end and the bolt just means your hand will have to exert twice the force to get it to click.... but it will still click at the set torque.
In reply to Curtis :
I agree that the torque wrench will always click at the selected setting (which is ft lbs, not just lbs - which is why adding a cheater bar makes it easier but doesn't change the setting).
But in the Crowfoot case, the torque wrench is no longer measuring torque at the nut, it is now measuring torque at some point along the length of the tool.
Curtis said:
Robbie said:
The difficult part of this theoretical experiment is that the torque wrench is no longer measuring the torque at the bolt. It is measuring the torque on a joint somewhere in the lever arm.
So: bolt - distance A - torque wrench pivot - distance B - point where force is applied.
In you example above, distance A is 3 inches, distance B is 12, and required torque at the bolt is 15 ft lbs.
The total length of your new tool is 15 inches, so if that were one solid wrench that would require 12 lbs pull (as stated above).
And thats about all I got before I start guessing.
Exactly my point... so with your numbers, he has to set the torque wrench at 12 ft-lbs in order to get 15 ft-lbs at the nut.
And I should clarify... I'm talking about when the torque wrench clicks which is unrelated to where you grab the handle. Grabbing the handle halfway between the end and the bolt just means your hand will have to exert twice the force to get it to click.... but it will still click at the set torque.
And you may very well be correct, but I don't like the edge case here of making the Crowfoot extension significantly longer than the torque wrench. It would mean that a very small torque setting on the wrench equals a large torque at the bolt, and that feels opposite to me of what should happen.
Take a look at this other dandy-tastic drawing.
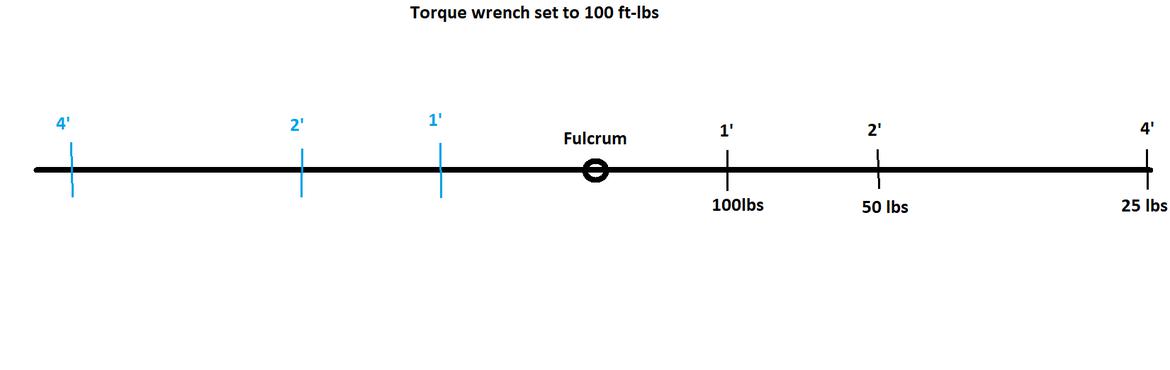
To the right of the fulcrum, let's imagine you have a 4' long torque wrench set to click at 100 ft lbs. The black labels show you the amount of force you would have to apply in order for it to click.
On the left (the blue labels), that is more like the example of my first superific drawing where you weld a socket to an end wrench and extend the wrench PAST the fulcrum. In this case you are fooling the torque wrench.
So on this above represented lever, the physics remain the same. You are still trying to target (in my example) 100 ft-lbs, so you need to exert less force to get it. Since you are now measuring the torque in the middle of the lever instead of at the end, you have to reduce the setting proportional to the length you add because you're measuring it AFTER you've added mechanical advantage. In the above drawing, if you added a 4' end wrench to a 4' torque wrench, you would set the torque wrench to 50 ft-lbs, you would apply 12.5 lbs of force to the handle, and it will click when the nut reaches 100 ft-lbs.
This is how I calibrate my torque wrenches, and actually it is why most torque wrenches have either a little flare and divot at the end or a little ring. It's because those spots are known distances. In the case of my 1/4" torque wrench, I have a little split ring on the end because that ring is attached exactly 12" from the center of the drive. I can calibrate it by setting it to 12 in-lbs, putting it on a nut, and hanging a 1-lb weight on that ring to see if it clicks. My 1/2" torque wrench has this (red arrow) on it because that smaller circumference is exactly 24" from the center of the drive. So I can set it to 50, put it on a nut, and hang 25 lbs to see if it clicks.
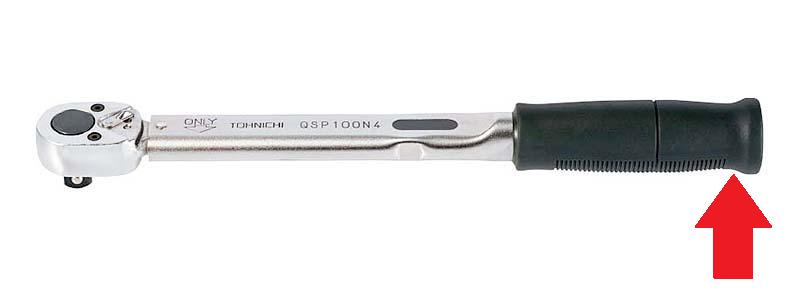
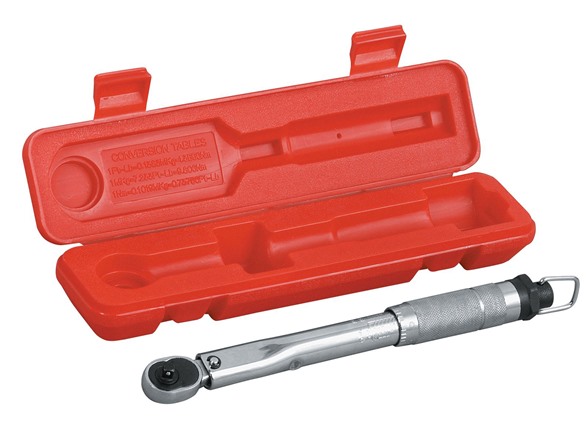
Come to think of it, this would be pretty easy to test.
Set it up with a bolt and nut. Choose a low target for the fastener... like for a 3/8" nut and bolt, maybe set it to 30 ft-lbs. Tighten it until it clicks. Then set it up where you add 50% more length between the torque wrench head and the nut and leave it set to 30 ft-lbs. Tighten it more until it clicks. Then remove the nut with just the torque wrench. It will click at 30 but not move. Keep raising the setting until starts moving before a click. My guess is it will be around 45-50 ft-lbs because you added 50% more mechanical advantage AFTER the measuring part.
It would be 45 mathematically, but I say 45-50 because you may have sticktion to overcome to get it moving.
Another idea. With the crowsfoot like you pictured above, he could at least get close to his target if he positioned the crowsfoot more perpendicular or even pointed backwards a little to the handle. it would still alter his mechanical advantage, but at least it wouldn't be adding or subtracting a couple inches.
Curtis said:
Come to think of it, this would be pretty easy to test.
Set it up with a bolt and nut. Choose a low target for the fastener... like for a 3/8" nut and bolt, maybe set it to 30 ft-lbs. Tighten it until it clicks. Then set it up where you add 50% more length between the torque wrench head and the nut and leave it set to 30 ft-lbs. Tighten it more until it clicks. Then remove the nut with just the torque wrench. It will click at 30 but not move. Keep raising the setting until starts moving before a click. My guess is it will be around 45-50 ft-lbs because you added 50% more mechanical advantage AFTER the measuring part.
It would be 45 mathematically, but I say 45-50 because you may have sticktion to overcome to get it moving.
This is a good test.And really you just need a crows foot or something to know if you change the distance a little, does the torque applied to the bolt go up or down (or does it not change!)
Really the only thing I'm still struggling with here is the idea of putting a 12 foot "end wrench" on an inlb torque wrench and torquing something to 100 ftlbs without breaking the inlb wrench.
ShawnG
PowerDork
7/6/19 10:15 p.m.
I have a slide-rule in my work toolbox for exactly this.
Or, you could just go here: https://www.engineersedge.com/manufacturing_spec/calculator/torque_adapter_extension.htm
Or, you can just put the adapter 90 degrees to the torque wrench and have zero correction.
PS for those too lazy to follow the links it confirms Curtis as well as many other prior posters.
ShawnG
PowerDork
7/6/19 10:29 p.m.
I'm going to tell all of you something I tell my apprentice.
Go buy these for your toolboxes:

Lots of companies sell them, not just Lee Valley.
They have charts, tables and formulas for what the O.P. was asking and tons more stuff.