I personally own three sewing machines; a newer Brother that was a donation, a '78 Elna that I grew up learning on, and a Riccar from the 80s that I picked up cheap. All of them are fine machines, but they are all entry-level. The only one of those three that will do denim is the Riccar and it struggles. I recently made all new curtains for the theater with heavy velour and promptly broke all three machines.
In our props storage was an old Singer 31-15 industrial, so I figured it was time to drag it out and see why it was a prop instead of in my shop being used. The answer was basically.... nothing. It was caked with old oil, and the timing was a bit off, but it's lovely.
It's a 1952, manufactured in May, but the 31-15 model began life in 1908. From some research I found that it's set up for leather but has a more traditional feed dog and presserfoot for textiles.
Eventually I'll repaint and put new decals on it, but for now I focused on the desk. 60 grit, 100 grit, and 150 grit cleaned up the maple butcher block. I have two coats of a polyurethane recipe that is equal parts oil poly, tung oil, and mineral spirits. Nice sheen, waterproof, and super at self-leveling.
Then I took off all the chrome bits and hit them with a wire wheel to polish and remove rust.
Finally got to test it today. It works. I would guess with that 1/4hp motor and a #18 needle I could likely sew two rocks together.
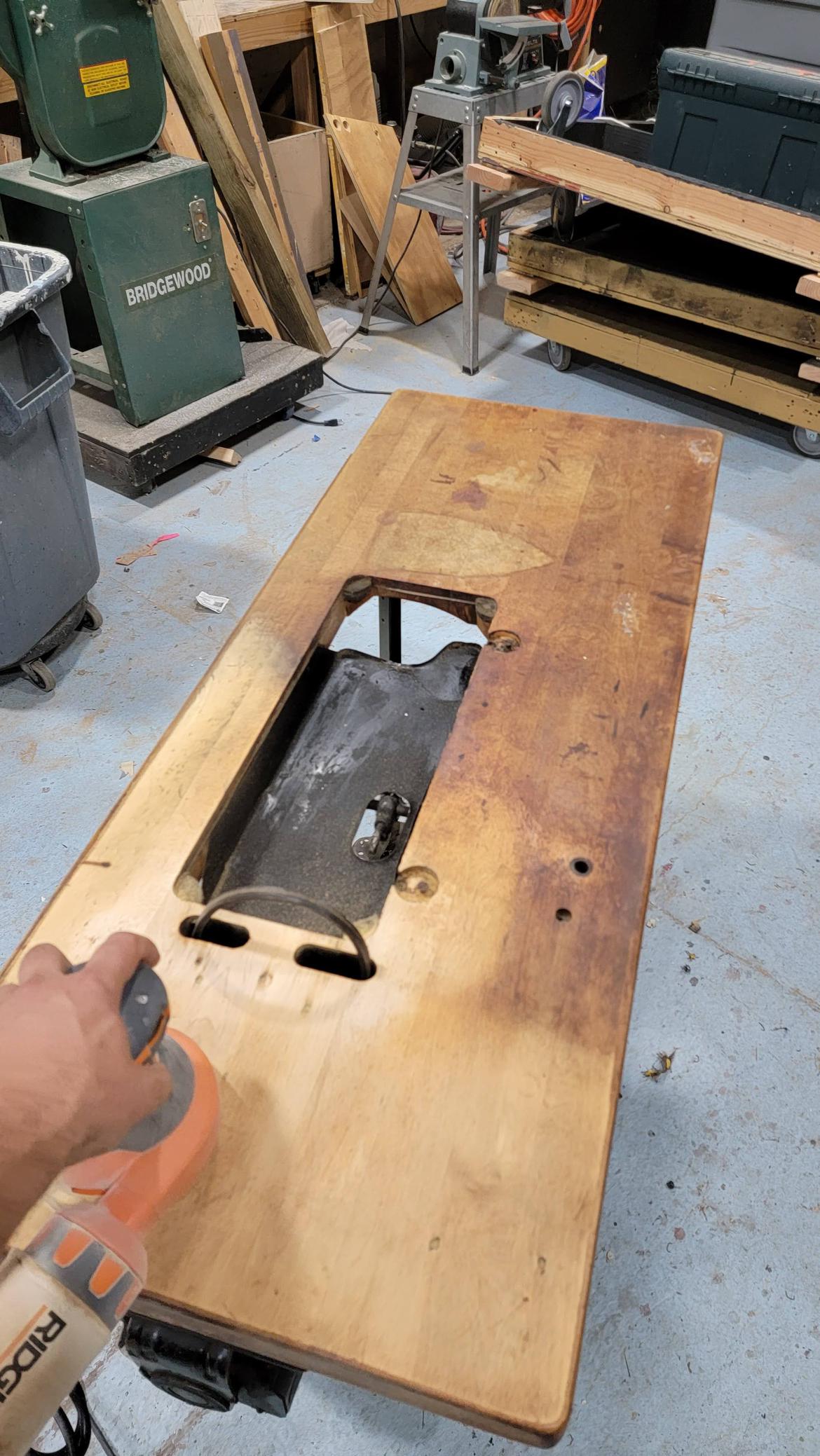
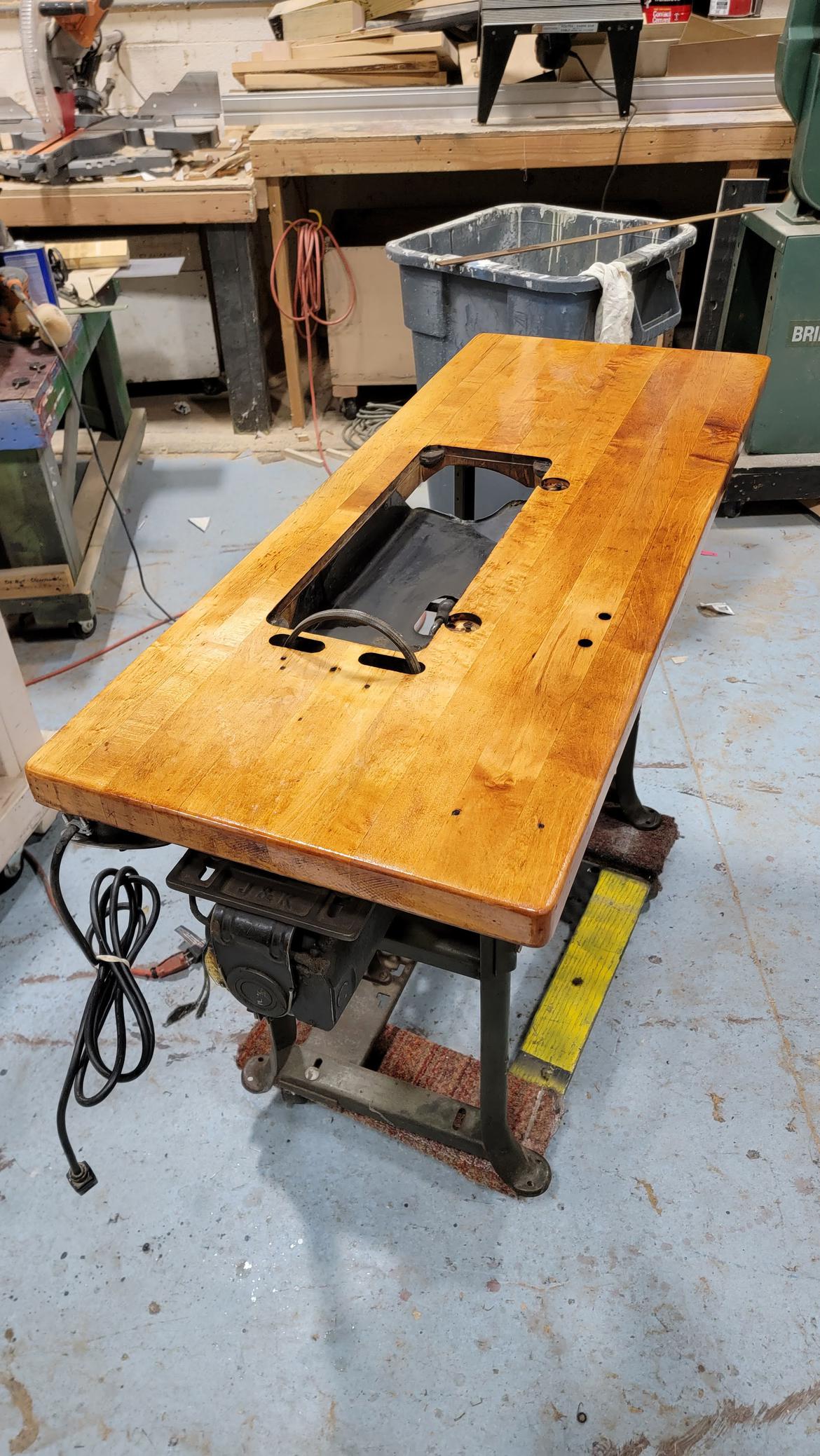
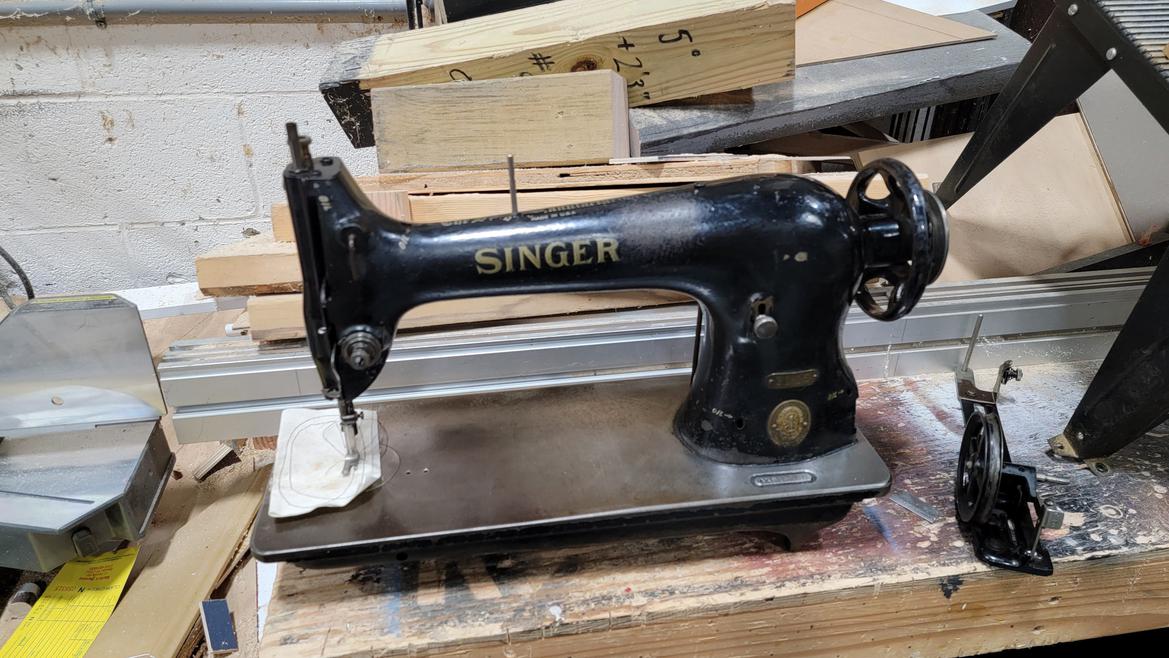
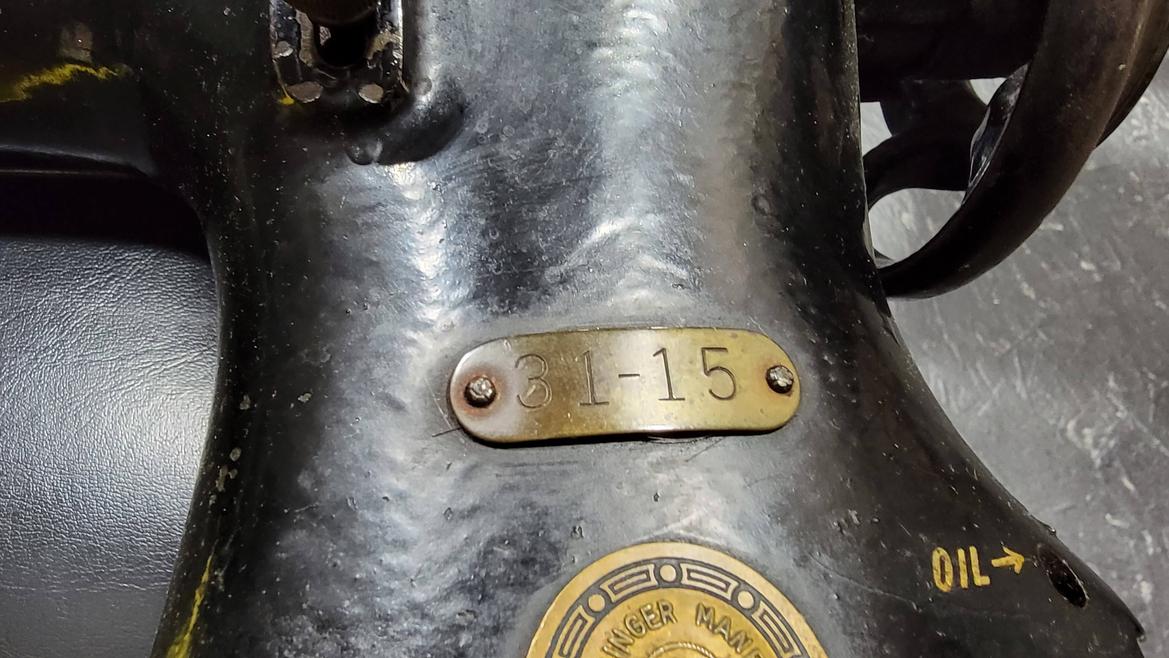
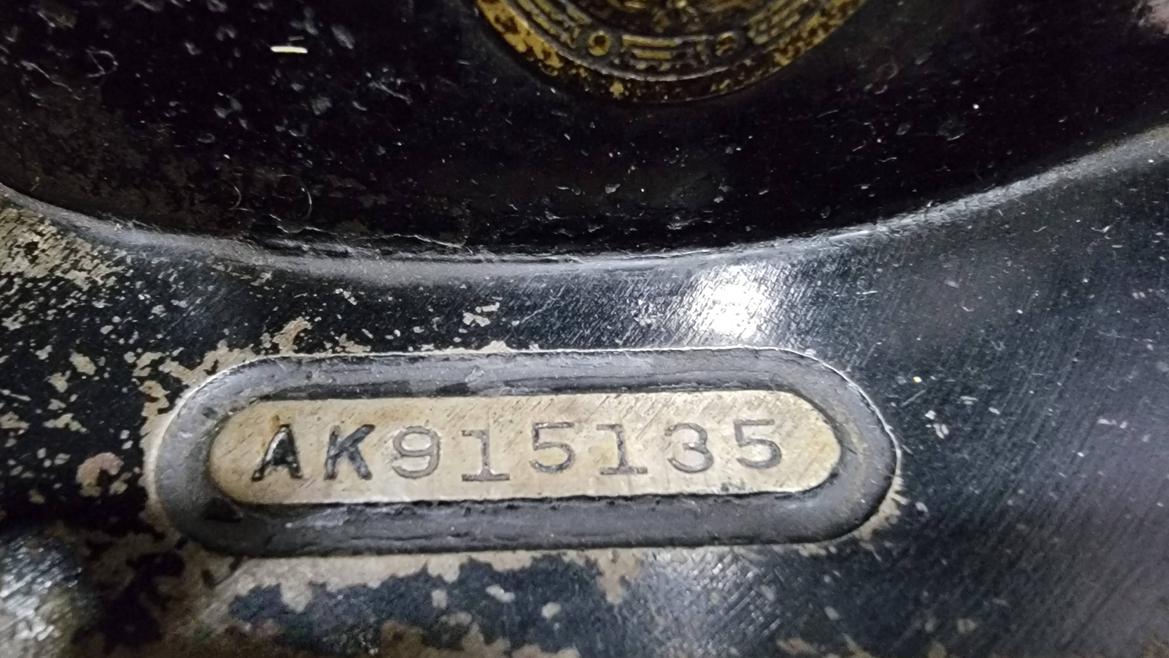
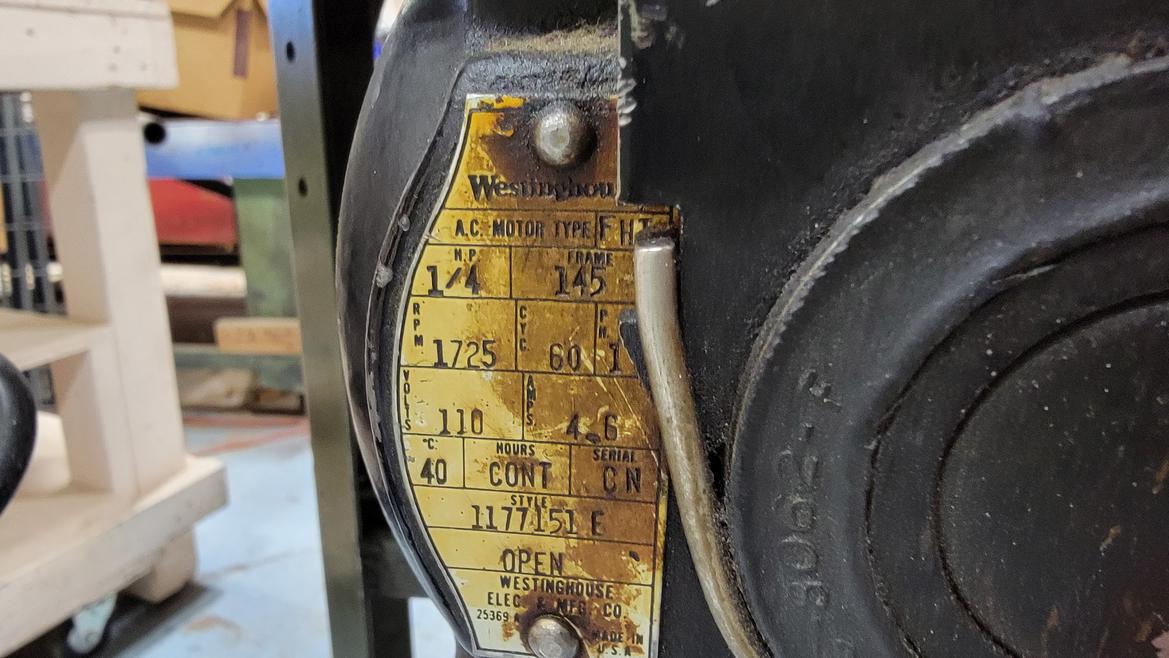
We found a Model 15 in a junk shop for $18, complete with the rounded case. We had it serviced by our local sewing machine guy and I'm working on cleaning up some of the aesthetics as well, including repairing the case. I'm going to modify the foot pedal to use a detachable plug instead of being hardwired (for storage) but it's a pretty solid machine. I'll get some pics to accompany this later.
Old sewing machines are a deep rabbit hole.
I too have an oldie but goodie.
The motor is tired on it and the belt isn't a standard size so the one I have is slightly too big; sometimes I need to help it by hand.
But heck, even just turning the crank manually beats the heck out of sewing with a thimble!
I think this winter I might try to spruce it up a bit.
In-laws have an old singer like that. Not sure the exact model. Someone put a motor on it at some point but a thumb screw will detach the linkage and it can be run from the pedal. I'll try to get a picture next time I'm there.
We used to have a ton of 132s at work but we have cycled them out for more modern machines with easier SPI adjustment, tension, parts supply, etc. But there are still some jobs that require a good 132 and operator.
I have an old Singer embroidery machine , it's at my friends house and he does old jackets ,
The old Singers were made to last forever ,
We got my mother in laws singer similar to that... and several '70s machines needing tuneups from my grandmother and mom. Let a couple ok tables go; kept a nice table with the drop down, and fold over top. The old Singer has a different pin spacing, so I have not gotten it mounted on table yet... we just set it on top the few times we've used it.
I need to get some info off of it, and pic's
Final coat of poly concoction went on today. Now for my patented (not really) baked-on treatment.
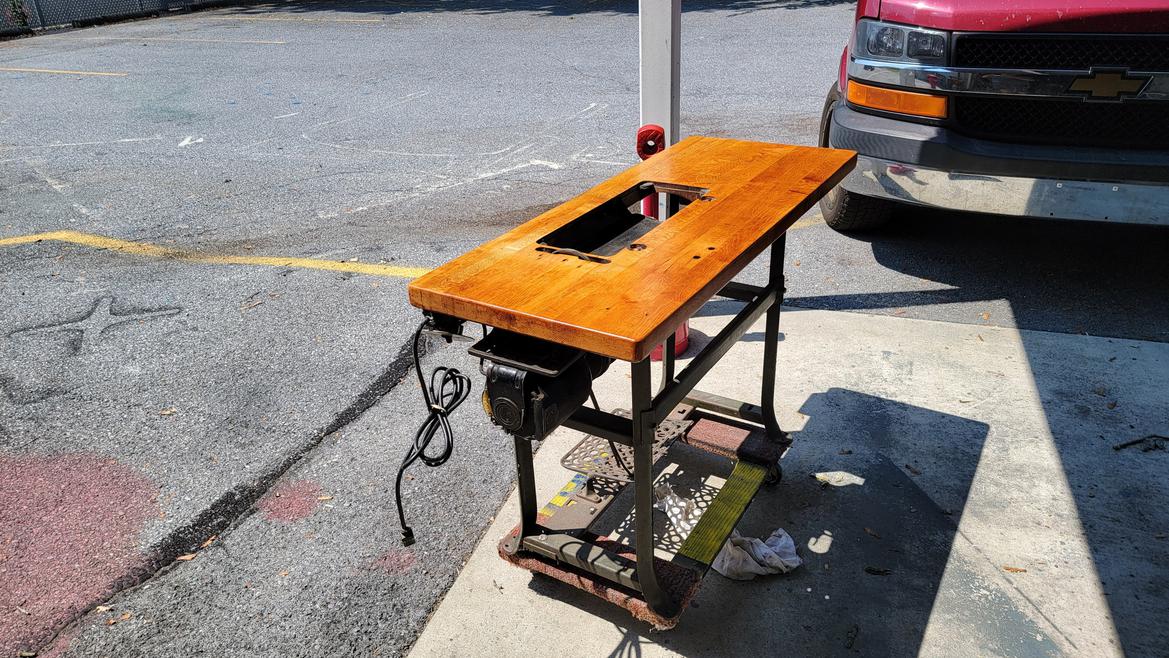
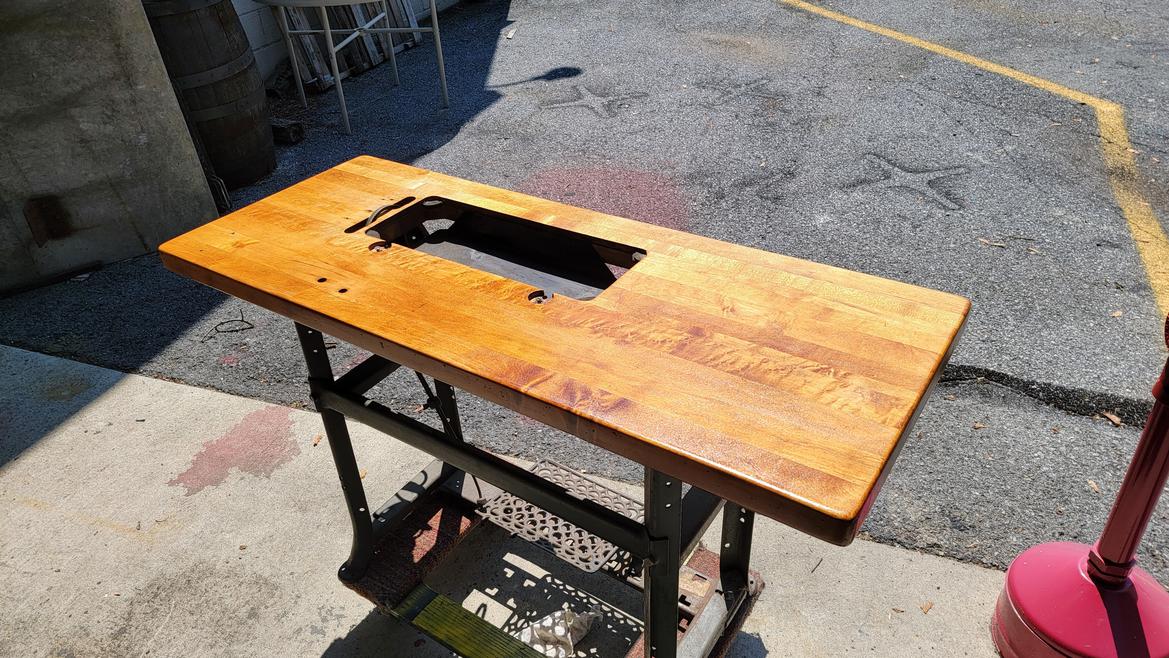
My wife also has a very nice old treadle base, with a solid oak (3/4 thick) top as a pretty table. Fits on well with some of my family's oak stuff from the late 1800s, as well as the newer solid oak entertainment/curio wall unit.
I like your baked on finishing method!
jgrewe
HalfDork
8/24/22 3:45 p.m.
I have your machines older brother, made in Feb of 1921 IIRC. Looks like the exact set up, table and all. From what I've read about them if you can fit the material under the foot it will go through it. The biggest problem is the speed. They are dress maker machines and will run down a seam lightning fast. I think the stitch count/inch is high too.
I don't know anything about sewing except seeing my mom sew for fun growing up. I've always wanted to play around with car interior stuff and looked at how to slow the machines top speed down so I don't perforate myself and bleed all over some expensive fabric.
In reply to jgrewe :
This one has an adjustable stitch spacing. The knob on the front takes it from zero feed up to fast feed/wide stitch. No reverse, so you have to manually secure the start/stop by rolling the flywheel backward.
Not sure how others are set up, but this one has a constant-spinning motor and the old treadle engages a clutch on the pulley. You can regulate the speed with foot pressure on the clutch. Another thing some folks do is to install a potentiometer on the motor to set a slower speed.
My first project will be new fabric for my cot. The old fabric is rotten/ripped so I got some new poly duck/canvas. It's like the fabric you might find on one of those folding lawn chairs, but a little heavier. I'm going to pull the old fabric off to use as a pattern.
jgrewe
HalfDork
8/24/22 3:58 p.m.
I'm going to have to crawl up on the pallet rack and take a look at mine to see if it has that knob.
Mine was given to me years ago by a guy that did a clean out for a family after their 95+ y.o. mother passed. Heck, she might have bought it new,lol. She made dresses her whole life for business then pleasure.
Today's project was electrical. The old cord was asbestos/fabric and had exposed copper. It also had only a two-wire plug. I snagged about 20' of 16/3 SJOOW and fixed that. The wires going to the motor were also equally sketchy, so I finished that run with some 16 ga lamp cord. Total amperage of the whole desk is under 5A, so I don't think I'll burn down anything. I also found a nice desk lamp without a base. There was a pre-existing 9/16" hole in the desk, but the lamp had a 1/2" base = floppy things. Fixed that by boring the hole out to 5/8" and pounding in a wee stub of PEX 1/2" tubing. Press fit into the desk, then the lamp press fit into the PEX. Custom low-friction bushing. Wired that up in the J-box to the hot lead so the lamp can work independently of the switch/motor.
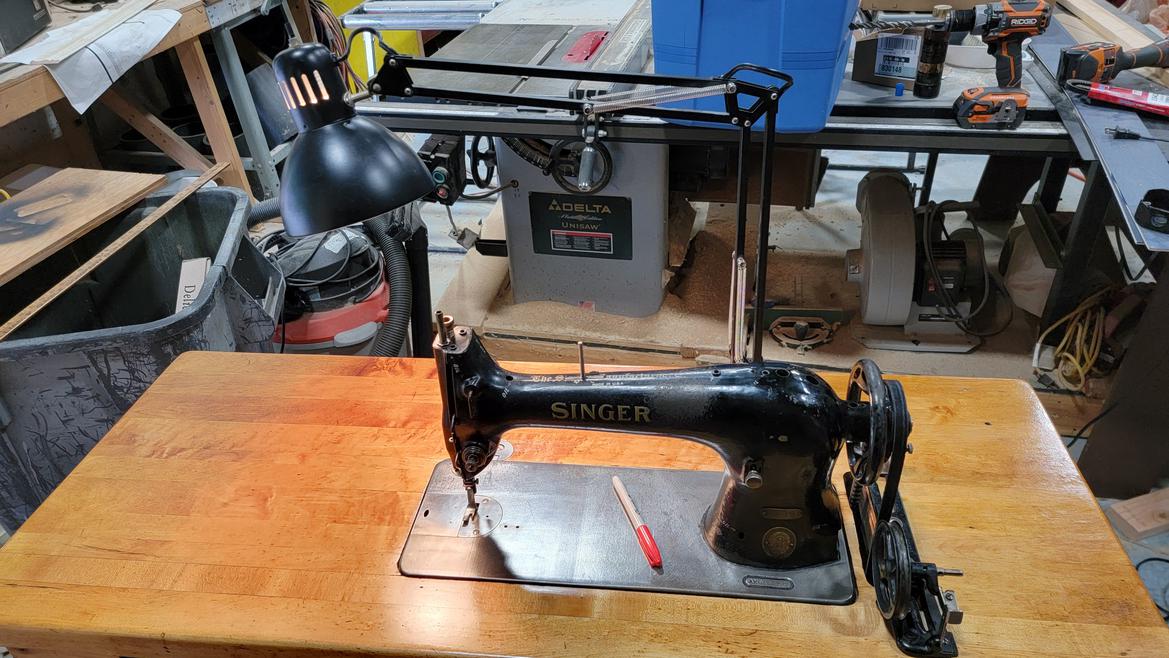
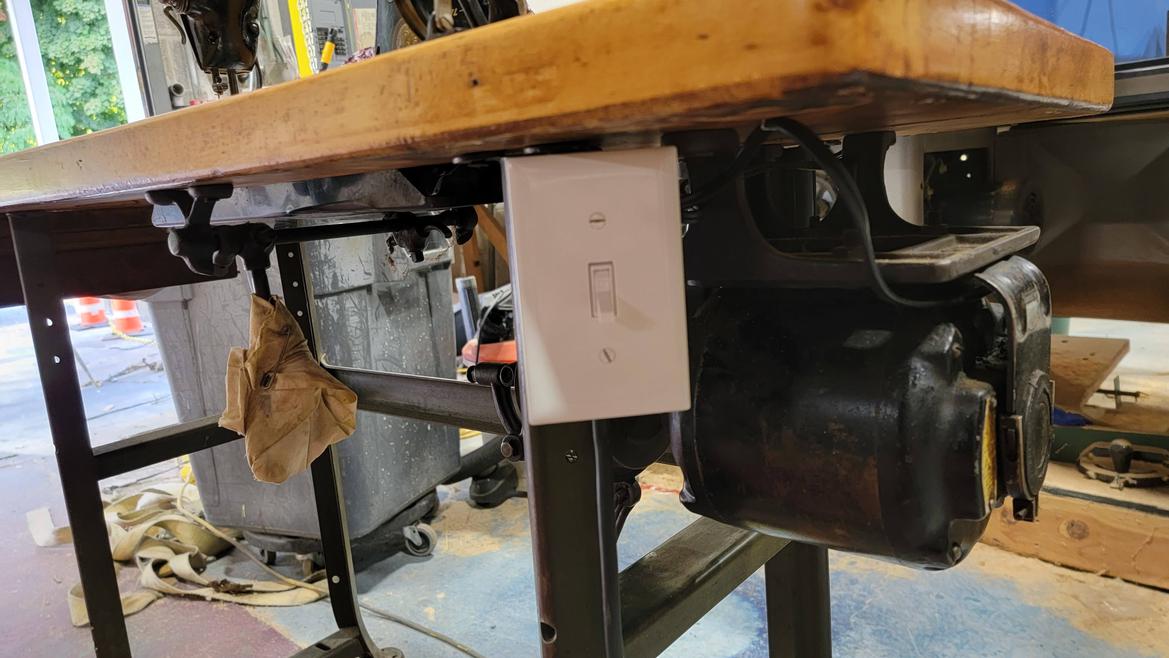
I'm having some doubts about the clutch. (see photo below) The clutch engages using the old treadle. Push the treadle like an accelerator and it pushes the belt pulley against the clutch friction material on the spinning motor. I used the set screws (red circle) to align the pulley parallel with the clutch. The clutch (yellow) engages as you push the treadle (green arrow) and it pushes the pulley to the right (blue arrow)
No matter what I do, I can't get a lot of friction at the clutch. That is to say, no matter how hard I push on the treadle, I can grab the upper pulley and stop it and the motor doesn't seem to slow down. The belt isn't slipping, it just doesn't seem to transfer much torque to the drive pulley. (sidenote - a 15423 belt works nicely)
I suppose I'll try it on some heavy fabric and see if it has enough oomph to go through it, but start maybe thinking about ideas to increase friction. Sand the pressure plate/pulley? Some kind of dressing I can put on it?
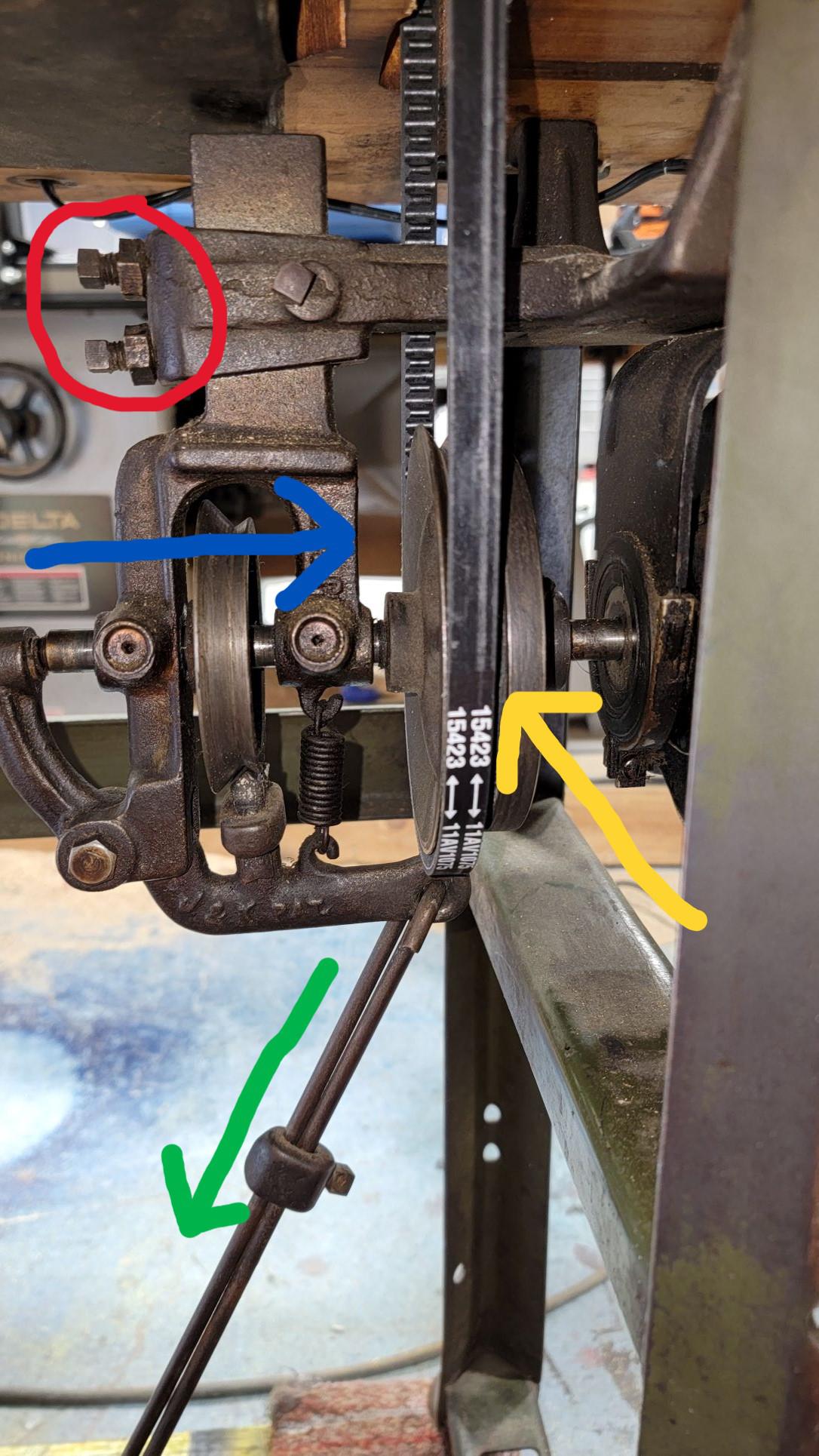
That's probably a street clutch. You need a racing clutch. 
In reply to 1988RedT2 :
Of course. Why didn't I think of that?
Try a lawn and garden belt meant to be clutched / declutched. The green ones.
In reply to wvumtnbkr :
The belt never slips. That is to say, it's not the belt that is the clutch. The belt is under constant tension and the pulley engages against the motor.
In reply to 1988RedT2 :
I can get to all of it if I remove either the pulley/cam assembly or the motor.
My first thought was to pull the motor, spin the pulley with a drill, and lay a 60 grit belt sander on it to knock the glaze off. Might benefit from a palm sander on the clutch material as well.
In reply to Curtis73 (Forum Supporter) :
Worth a try, for sure. Or it might be like some brakes I've seen and there might not be any friction material left at all.
My project is not nearly as old as yours I think, by far. Yet it is cool.
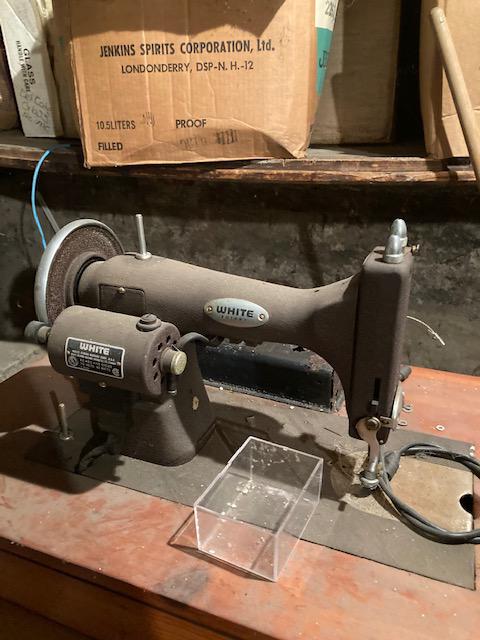
On a childs desk I think:
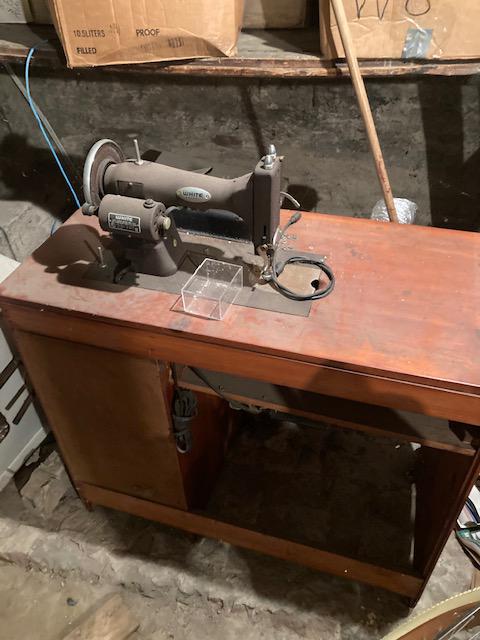
In reply to preach (dudeist priest) :
Sweet. IIRC, the logo suggests 1964 or older. For a while after 1964 they had WCI logos (white consolidated industries) after they acquired Kelvinator, Philco, and a few other companies.
My wife, the daughter of a life-long quilter and sewer, is a sewing machine snob. Her weapon of choice is the Singer 401a. We actually have two of these because she found the second one at a killer price. Made from 1956-1961 the 401a has a cult following as being "the last of the great ones."
https://silverbobbin.com/singer-401a-sewing-machine-history-value-review/
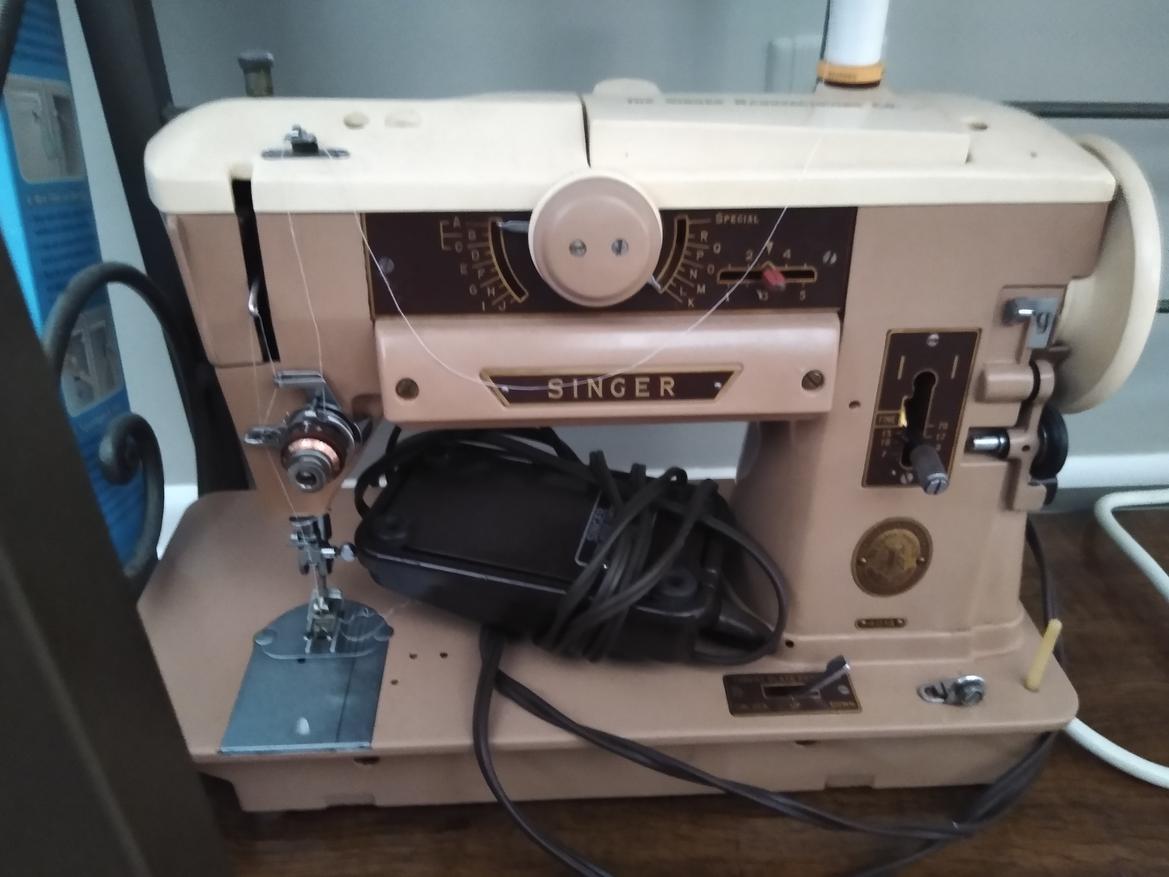
Curtis,
I think you have my Grandmothers old machine. My mom made her own clothes with it, Grandma upholstered furniture. You know between raising 14 kids and many grand children.
In reply to Curtis73 (Forum Supporter) :
Cool to know!